A simple way to figure out the mold high-speed cutting process!
2020-04-06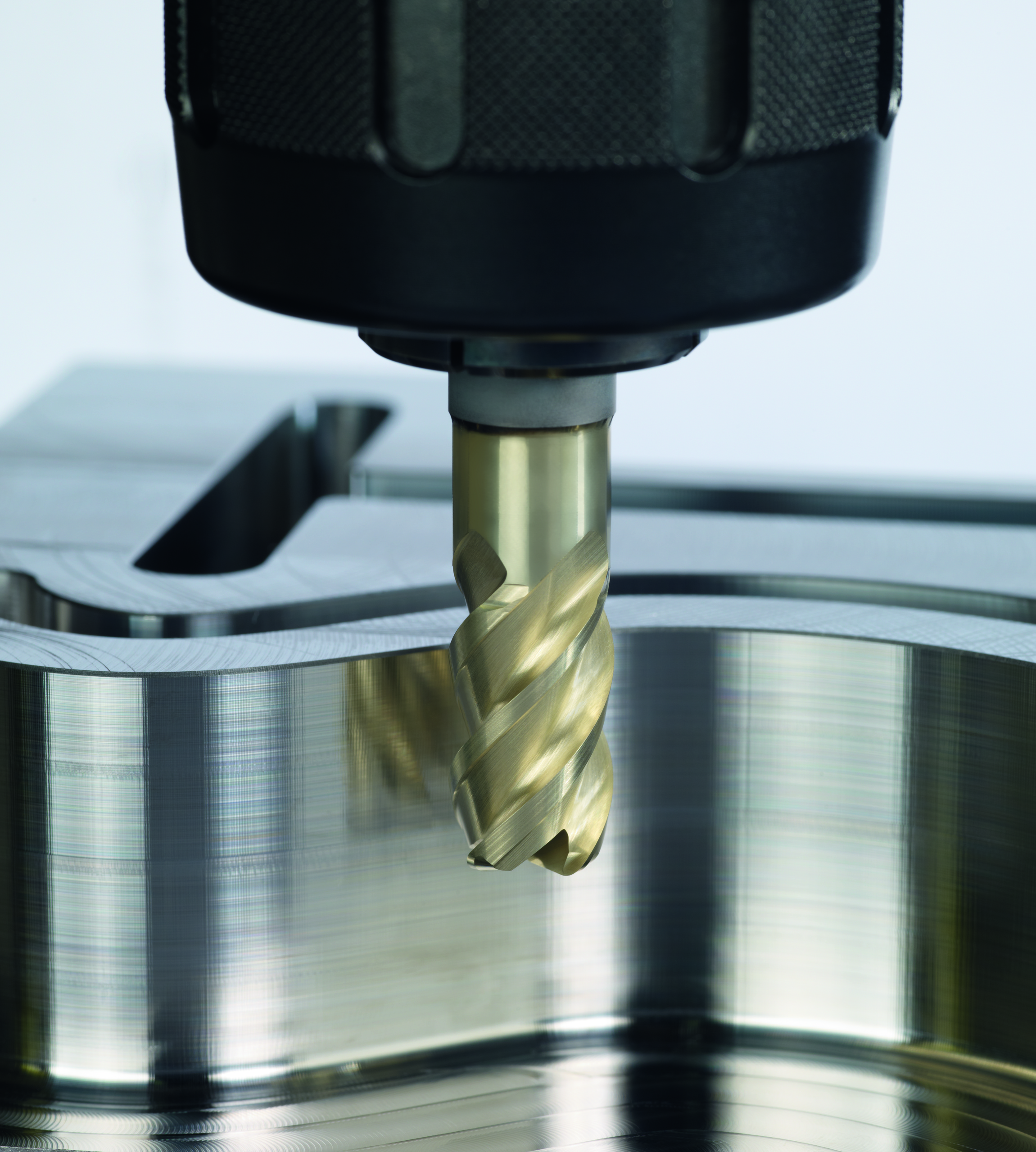
As the aesthetic and functional requirements of the products become higher and higher, the design of the internal structure of the products becomes more and more complex, and the shape of the mold design becomes more complex, the proportion of free-form surfaces is increasing, and the corresponding mold structure is also more complex. All these have put forward higher requirements for mold processing technology, high-speed processing technology has been increasingly applied to the processing and manufacturing of mold cavities.
The cutting speed and feed rate have been greatly improved compared to traditional cutting, and the cutting mechanism is different. High speed cutting makes an intrinsic leap in machining, the metal cutting rate per unit power increases by 30% to 40%, the cutting force decreases by 30%, the cutting life of tungsten steel end mills increases by 70%, the cutting heat left in the workpiece is greatly reduced, and the low-order cutting vibrations almost disappear.
In the machining process of high-hardened hardened steel parts (HRC45~HRC65), the use of high-speed cutting can replace part of the EDM machining and grinding and polishing process, thus avoiding the manufacture of electrodes and time-consuming electrical processing, greatly reducing the amount of grinding and polishing of the clamps. High-speed milling is also possible for some thin-walled molded workpieces that are increasingly in demand in the market, and on high-speed milling CNC machining centers, the mold can be clamped in a single pass for multi-step machining.
Support components such as the bed of a high-speed cutting tool machine should have good dynamic and static stiffness, thermal stiffness and optimal damping characteristics. Some machine tool companies also add polymer concrete with high damping properties to the base to increase its vibration resistance and thermal stability, which not only ensures the machine's accuracy and stability, but also prevents the tungsten carbide cutter from vibrating during cutting. The closed bed design, the overall casting of the bed, the symmetrical bed structure and the dense reinforcement are also important measures to improve the stability of the machine tools.
The spindle performance of a high-speed machine is an important condition for high-speed machining. The spindle speed range of high speed cutting machine is 10,000~100,000m/min, the spindle power is more than 15kW, the axial clearance between the shank and the spindle is not more than 0.005mm, and the spindle is required to have fast ascending speed and fast stopping speed at the specified position (i.e. very high angular increase/decrease speed), so the high speed spindle is often used in liquid hydrostatic bearing type, aerostatic bearing type, hot pressed silicon nitride (Si3N4) ceramic bearing magnetic suspension bearing type. Lubrication is mostly by oil and gas lubrication, spray lubrication and other techniques. Spindle cooling is generally water-cooled or air-cooled inside the spindle.
To meet the needs of high-speed machining of molds, the drive system of high-speed machining machines shall have the following characteristics.
(1) High feed rate. Studies have shown that for small diameter tungsten carbide cutters, increased rotational speed and per tooth feed are beneficial in reducing tungsten carbide cutter wear. The current commonly used feed speed range of 20~30m/min, such as the use of large-profile ball screw drive, feed speed up to 60m/min; the use of straight-line motors can make the feed speed up to 120m/min.
(2) High acceleration. The high speed processing of 3D complex surface contours requires a drive system with good acceleration characteristics, which requires the provision of a high-speed feed drive (fast forward speed of about 40m/min, 3D contour processing speed of 10m/min), capable of providing 0.4m/s2 to 10m/s2 of acceleration and deceleration.
Most machine tool manufacturers use full closed-loop position servo-controlled small-circuit, large, high quality ball screws or large-circuit multihead screws.
Advanced CNC system is the key factor to ensure the quality and efficiency of high speed machining of complex curved surfaces of molds, the basic requirements of the CNC system for high speed machining of molds are.
(1) High-speed digital control loops, including: 32-bit or 64-bit parallel processors and hard drives over 1.5Gb.
(2) Forward feedback control of speed and acceleration; Jerk control of digital drive systems.
(3) Advanced interpolation methods to obtain good surface quality, precise dimensions and high geometric accuracy.
(4) Requires a large-capacity buffer register that allows multiple program segments to be read and checked in advance so that measures such as changing the feed rate can be taken in a timely manner to avoid overcutting when the shape (curvature) of the surface being processed changes.
(5) Error compensation functions, including thermal error compensation, quadrant error compensation, measurement system error compensation due to heat generation of motors, spindles, etc. In addition, high speed cutting of dies requires high data transfer speed.
(6) Traditional data interfaces, such as RS232 serial port, have a transfer speed of 19.2kb, while many advanced machining centers have adopted Ethernet for data transfer at speeds up to 200kb.
High-speed machining with coated carbide tungsten carbide end mills, at high speed and temperature without cutting fluid, cutting efficiency is higher. This is because: the milling spindle rotates at a high speed, and the cutting fluid has to overcome a very high centrifugal force to reach the cutting zone; even if it overcomes the centrifugal force to enter the cutting zone, it may evaporate immediately due to the high temperature of the cutting zone, with little or no cooling effect; at the same time, the cutting fluid will cause the temperature of the tungsten cutting edge to change drastically, which will easily lead to cracking, so oil/air cooling and lubrication of the dry cutting method is used. This way the cutting area is quickly blown away with high-pressure gas, which carries away a lot of cutting heat, while the atomized lubricant forms an extremely thin microscopic protective film on the cutting edge of the tungsten carbide cutter and the surface of the workpiece, effectively extending the life of the tungsten carbide cutter and improving the surface quality of the parts.
Due to the influence of centrifugal forces and vibrations during high-speed machining, the tungsten steel milling cutters are required to have high geometric accuracy and clamping repeatability as well as high rigidity and safety reliability of high-speed dynamic balance. Due to the high centrifugal force and vibration during high speed machining, the traditional 7:24 taper shank system shows obvious deficiencies such as insufficient rigidity, low repeat accuracy and unstable axial dimension during high speed cutting. At present, HSK high-speed toolholders and the hot expansion, cold shrinkage and fastening type of toolholders are the most popular ones. The shank is generally tapered and in contact with the spindle endface at the same time, which is more rigid, but the tungsten end mills are less replaceable. Since this type of heating system is more expensive, it is sufficient to use HSK type knife shank system in the initial stage. When the number of high-speed tool machines in an enterprise is more than 3, it is more appropriate to use the hot expansion, cold shrinkage and fastening type of toolholders.
Tungsten carbide end mills are one of the most active and important factors in high-speed machining, which directly affects machining efficiency, manufacturing costs and product accuracy. Tungsten carbide end mills are subjected to high temperature, high pressure, friction, impact and vibration loads during high-speed machining. The technology of high speed cutting tungsten and steel milling cutters is developing rapidly, with more applications such as diamond (PCD), cubic boron nitride (CBN), ceramic tungsten and steel milling cutters, coated carbide, (carbon) titanium nitride carbide TIC(N), etc.
Carbide is the most common material used for cutting tungsten steel end mills for machining cast iron and alloy steel. Carbide tungsten carbide cutters have good abrasion resistance, but are less hard than cubic boron nitride and ceramics. In order to improve the hardness and surface finish, tungsten steel end mills are coated with titanium nitride (TiN), aluminum titanium nitride (TiALN) and other materials. Coating technology has enabled the development of coatings from single coats to multi-layer, multi-coated materials, and has become one of the key technologies to improve high-speed cutting capabilities. Carbide inserts with diameters from 10 to 40 mm and titanium carbide coating can process materials with a Rockwell hardness of less than 42, while titanium nitride coated tungsten mills can process materials with a Rockwell hardness of 42 and higher.
For high-speed steel cutting, tungsten carbide end mills should be made of carbide P with high thermal and fatigue strength, coated carbide, cubic boron nitride (CBN) and CBN composite tungsten carbide end mills (WBN), etc. For cutting cast iron, fine grain Class K carbide should be used for roughing, and composite silicon nitride ceramics or polycrystalline cubic boron nitride (PCNB) composite tungsten steel cutters should be used for finishing.
For precision machining of non-ferrous or non-metallic materials, use polycrystalline diamond PCD or CVD diamond-coated tungsten steel cutters. When selecting cutting parameters, for round inserts and ball end mills, attention should be paid to the concept of effective diameter. Carbide cutters for high-speed milling should be manufactured to a dynamic balance design. The front angle of the tungsten cutter is smaller and the rear angle is slightly larger than the front angle of a conventional tungsten cutter. The main and secondary cutting edge joint should be rounded or angled to increase the angle of the tip to prevent heat wear on the tip. The length of the cutting edge near the tip and the material volume of the tungsten cutter should be increased to improve the rigidity of the tungsten cutter. The overhang of the tungsten steel end mills is as short as possible and the central toughness of the cutter body is good under conditions that guarantee safety and meet machining requirements. The shank is thicker in diameter than the tungsten carbide end mills and the connecting shank is inverted tapered to increase its rigidity. Leave a coolant hole in the center of the carbide end mill and the carbide end mill system as much as possible. Ball end mills should consider the effective cutting length and the cutting edge should be as short as possible. Two helix-grooved ball end mills are usually used for roughing and milling complex surfaces, while four helix-grooved ball end mills are usually used for finishing complex surfaces.
High-speed machining includes roughing and residual roughing for the purpose of removing residuals, as well as semi-finishing, finishing and mirror finishing for the purpose of obtaining high quality machined surfaces and fine structures.
The main goal of tool roughing is to pursue material removal rates per unit of time and to prepare the geometric profile of the workpiece for semi-finishing. The process solution for roughing in high-speed machining is a combination of high cutting speed, high feed rate and small cutting volume.
Contour machining is a common machining method used in many CAM software. The more commonly used is the spiral and Z-axis contour methods, that is, only one feed in the machining area, without lifting the tool to generate a continuous smooth tungsten end mill path, the feed and retract method is circular in and out. The characteristic of the spiral equal height method is that there is no movement of the knife path between the equal height, which can avoid the frequent lifting of the knife, the effect of the feed on the surface quality of the parts and unnecessary wear and tear of the mechanical equipment. Separate treatment of steep and flat areas, calculation of suitable contours and areas suitable for the use of similar 3D offsets, and the use of spirals to generate optimized carbide end mill paths with little tool lift for better surface quality.
In high-speed machining, it is necessary to adopt the circular cut-in and cut-out connection methods, as well as the circular transition at the corners, to avoid sudden changes in the direction of feed of the tungsten carbide end mills, and to prohibit the use of direct down tool connection method, so as to avoid burying the tungsten carbide end mills into the workpiece. When machining the mold cavity, you should avoid the vertical insertion of carbide end mills into the workpiece and adopt the tilting down tooling method (common tilting angle is 20°~30°).
When machining the core of the mold, the tool should be cut from the outside of the workpiece first and then horizontally into the workpiece as much as possible. Tungsten carbide milling cutters should be used as much as possible to cut in and out of the workpiece by inclined type (or circular arc type) to avoid vertical cutting in and out. Climbing cutting reduces cutting heat, reduces tungsten cutter stress and machining hardening, and improves machining quality.
The main goal of semi-finishing of molds is to make the workpiece profile shape flat and the surface finish balance even, which is especially important for tool steel molds because it will affect the change of the cutting layer area of tungsten steel end mills during finishing and the change of the tungsten steel end mill load, which will affect the stability of the cutting process and the finish surface quality.
Roughing is based on the volume model and finishing is based on the face model. The previously developed CAD/CAM system is discontinuous in its geometric description of the parts. Since there is no intermediate information describing the model after roughing and before finishing, the distribution of the remaining machining residuals on the roughing surface and the maximum remaining machining residuals are unknown. Therefore, the semi-finishing strategy should be optimized to ensure a uniform residual machining balance on the workpiece surface after semi-finishing. The optimization process includes the calculation of the profile after roughing, the calculation of the maximum remaining machining allowance, the determination of the maximum allowable machining allowance, the calculation of the trajectory of the core during semi-finishing, etc. for the area of the profile where the remaining machining allowance is greater than the maximum allowable machining allowance (e.g., areas with a transition radius smaller than the radius of the roughing tungsten cutter such as recesses and corners).
Most of the existing CAD/CAM software for high-speed machining of molds is equipped with residual machining analysis function, and can adopt reasonable semi-finishing strategy according to the size and distribution of residual machining residual.
The high-speed finishing strategy for dies depends on the point of contact of the tungsten cutter with the workpiece, which varies with the surface slope of the machined surface and the effective radius of the tungsten cutter. For complex surface machining of a combination of surfaces, continuous machining should be performed in a single process whenever possible, rather than machining each surface separately to reduce the number of tool lifts and tool downs. However, due to the variation in surface slope during machining, if only the amount of side milling (Step over) of the machining is defined, it can result in uneven actual steps on surfaces with different slopes, thus affecting machining quality.
In general, the radius of curvature of a finished surface should be greater than 1.5 times the radius of the tungsten carbide cutter to avoid sudden changes in the direction of feed. In the high-speed finishing of the mold, in each cut in and out of the workpiece, the change of the feed direction should be as far as possible to adopt a circular or curved transfer, avoid the use of straight transfer to maintain the smoothness of the cutting process.
High-speed finishing strategies include strategies such as three-dimensional bias, contouring and optimal contouring, and spiral contouring. These strategies ensure a smooth and stable cutting process, ensuring that the material on the workpiece can be cut quickly to obtain a highly accurate and smooth cutting surface.
The basic requirement of finishing is to obtain a high precision, smooth surface quality of the part, and to easily achieve the machining of fine areas, such as small rounded corners, grooves, etc. For many shapes, the most effective strategy for finishing is to use a three-dimensional spiral strategy. The use of this strategy avoids the frequent directional changes that can occur with parallel and offset finishing strategies, thereby increasing machining speed and reducing tungsten mill wear.
This strategy generates a continuous smooth tungsten end mill path with little tool lifting. This machining technology combines the advantages of spiral machining and contour machining strategies, with a more stable load on tungsten end mills and fewer tool lifts, shortening machining time and reducing the chance of tungsten end mill tool damage. It also improves the quality of the finished surface and minimizes the need for hand sanding after finishing. A combination of isometric finishing methods for steep areas and three-dimensional isometric finishing methods for flat areas is required in many scenarios.
The choice of machining method and the programming strategy to be used are key when using CAM systems for CNC programming of high-speed machining, in addition to the selection of tungsten steel cutters and machining parameters according to specific conditions. An accomplished programmer using a CAD/CAM workstation should also be a qualified design and craftsman with a proper understanding of the geometry of the parts, knowledge and concepts of the ideal process arrangement and rational tungsten mill trajectory design.
High-speed milling operations are placing increasing demands on CNC programming systems, and expensive high-speed machining equipment is placing greater demands on software safety and effectiveness. In addition to high speed cutting tools and high speed cutting tungsten cutters, it is also important to have the right CAM programming software. An excellent high-speed CAM programming system should have high computing speed, strong interpolation function, automatic overcutting and processing capability, automatic toolholder and clamp interference check, feed rate optimization, track monitoring function, tungsten milling tool track editing and optimization function and machining residual analysis function, etc. High-speed cutting programming should firstly pay attention to the safety and effectiveness of the machining method; secondly, do everything possible to ensure smooth and smooth trajectory of the carbide end mills, which will directly affect the machining quality and the life of parts such as the spindle of the tooling machine; finally, make the carbide end mills as evenly loaded as possible, which will directly affect the life of the carbide end mills.
With very small feeds and depths of cut for high-speed machining, the NC program is much larger than for conventional CNC machining, requiring faster software calculations to save time in editing and optimizing the tungsten milling tool track.
High-speed machining is carried out at nearly 10 times the cutting speed of conventional machining, and if overcutting occurs, it will have disastrous consequences for the tooling machine, products and tungsten carbide end mills, so the CAM system is required to have the capability of automatic overcutting prevention and automatic toolholder and clamp interference check and bypass function. The system automatically prompts for the minimum length of the clamped carbide cutter and automatically performs an interference check of the carbide cutter.
In order to ensure maximum cutting efficiency and safety during high-speed machining, the CAM system should be able to automatically optimize the feed rate according to the size of the instantaneous machining residuals, edit and optimize the tungsten milling tool track, analyze the machining residuals and monitor the machining track to ensure the stability of the force state of high-speed machining tungsten milling tools and improve the service life of tungsten milling tools.
Due to the stringent requirements of high-speed machining processes, overcut protection is even more important, so it takes more time to simulate and check the NC instruction. In general, high-speed machining takes much longer than normal machining programming times. In order to ensure adequate utilization of the high-speed processing equipment, more CAM staff is required. Existing CAM software such as hyperMILL, PowerMILL, MasterCAM, UnigraphicsNX, etc. all provide a high speed milling tungsten tool tracing strategy with relevant features.
High speed cutting technology is mainly used in the automotive industry and mold industry, especially in the machining of complex curved surfaces, the workpiece itself or the rigidity of the tungsten carbide end mill system, etc. The high efficiency and high quality are highly appreciated.
The cutting speed and feed rate have been greatly improved compared to traditional cutting, and the cutting mechanism is different. High speed cutting makes an intrinsic leap in machining, the metal cutting rate per unit power increases by 30% to 40%, the cutting force decreases by 30%, the cutting life of tungsten steel end mills increases by 70%, the cutting heat left in the workpiece is greatly reduced, and the low-order cutting vibrations almost disappear.
In the machining process of high-hardened hardened steel parts (HRC45~HRC65), the use of high-speed cutting can replace part of the EDM machining and grinding and polishing process, thus avoiding the manufacture of electrodes and time-consuming electrical processing, greatly reducing the amount of grinding and polishing of the clamps. High-speed milling is also possible for some thin-walled molded workpieces that are increasingly in demand in the market, and on high-speed milling CNC machining centers, the mold can be clamped in a single pass for multi-step machining.
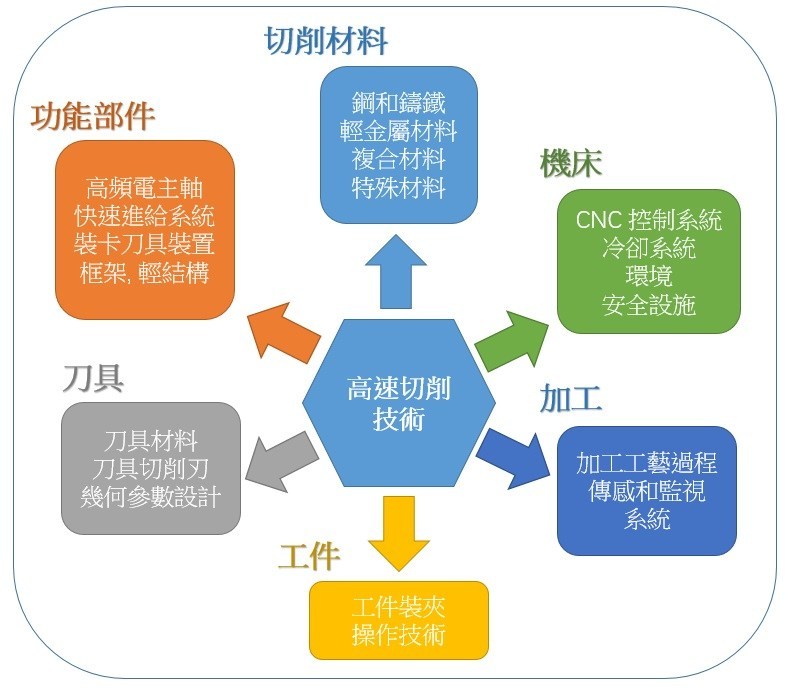
I. High-speed milling and machining tool machines
1. Highly stable tool machine support components
Support components such as the bed of a high-speed cutting tool machine should have good dynamic and static stiffness, thermal stiffness and optimal damping characteristics. Some machine tool companies also add polymer concrete with high damping properties to the base to increase its vibration resistance and thermal stability, which not only ensures the machine's accuracy and stability, but also prevents the tungsten carbide cutter from vibrating during cutting. The closed bed design, the overall casting of the bed, the symmetrical bed structure and the dense reinforcement are also important measures to improve the stability of the machine tools.
2. Machine tools spindle
The spindle performance of a high-speed machine is an important condition for high-speed machining. The spindle speed range of high speed cutting machine is 10,000~100,000m/min, the spindle power is more than 15kW, the axial clearance between the shank and the spindle is not more than 0.005mm, and the spindle is required to have fast ascending speed and fast stopping speed at the specified position (i.e. very high angular increase/decrease speed), so the high speed spindle is often used in liquid hydrostatic bearing type, aerostatic bearing type, hot pressed silicon nitride (Si3N4) ceramic bearing magnetic suspension bearing type. Lubrication is mostly by oil and gas lubrication, spray lubrication and other techniques. Spindle cooling is generally water-cooled or air-cooled inside the spindle.
3. Tool drive system
To meet the needs of high-speed machining of molds, the drive system of high-speed machining machines shall have the following characteristics.(1) High feed rate. Studies have shown that for small diameter tungsten carbide cutters, increased rotational speed and per tooth feed are beneficial in reducing tungsten carbide cutter wear. The current commonly used feed speed range of 20~30m/min, such as the use of large-profile ball screw drive, feed speed up to 60m/min; the use of straight-line motors can make the feed speed up to 120m/min.
(2) High acceleration. The high speed processing of 3D complex surface contours requires a drive system with good acceleration characteristics, which requires the provision of a high-speed feed drive (fast forward speed of about 40m/min, 3D contour processing speed of 10m/min), capable of providing 0.4m/s2 to 10m/s2 of acceleration and deceleration.
Most machine tool manufacturers use full closed-loop position servo-controlled small-circuit, large, high quality ball screws or large-circuit multihead screws.
4. Digital control systems
Advanced CNC system is the key factor to ensure the quality and efficiency of high speed machining of complex curved surfaces of molds, the basic requirements of the CNC system for high speed machining of molds are.(1) High-speed digital control loops, including: 32-bit or 64-bit parallel processors and hard drives over 1.5Gb.
(2) Forward feedback control of speed and acceleration; Jerk control of digital drive systems.
(3) Advanced interpolation methods to obtain good surface quality, precise dimensions and high geometric accuracy.
(4) Requires a large-capacity buffer register that allows multiple program segments to be read and checked in advance so that measures such as changing the feed rate can be taken in a timely manner to avoid overcutting when the shape (curvature) of the surface being processed changes.
(5) Error compensation functions, including thermal error compensation, quadrant error compensation, measurement system error compensation due to heat generation of motors, spindles, etc. In addition, high speed cutting of dies requires high data transfer speed.
(6) Traditional data interfaces, such as RS232 serial port, have a transfer speed of 19.2kb, while many advanced machining centers have adopted Ethernet for data transfer at speeds up to 200kb.
5. Cool and lubricate
High-speed machining with coated carbide tungsten carbide end mills, at high speed and temperature without cutting fluid, cutting efficiency is higher. This is because: the milling spindle rotates at a high speed, and the cutting fluid has to overcome a very high centrifugal force to reach the cutting zone; even if it overcomes the centrifugal force to enter the cutting zone, it may evaporate immediately due to the high temperature of the cutting zone, with little or no cooling effect; at the same time, the cutting fluid will cause the temperature of the tungsten cutting edge to change drastically, which will easily lead to cracking, so oil/air cooling and lubrication of the dry cutting method is used. This way the cutting area is quickly blown away with high-pressure gas, which carries away a lot of cutting heat, while the atomized lubricant forms an extremely thin microscopic protective film on the cutting edge of the tungsten carbide cutter and the surface of the workpiece, effectively extending the life of the tungsten carbide cutter and improving the surface quality of the parts.
II. High speed cutting shanks and tungsten steel end mills
Due to the influence of centrifugal forces and vibrations during high-speed machining, the tungsten steel milling cutters are required to have high geometric accuracy and clamping repeatability as well as high rigidity and safety reliability of high-speed dynamic balance. Due to the high centrifugal force and vibration during high speed machining, the traditional 7:24 taper shank system shows obvious deficiencies such as insufficient rigidity, low repeat accuracy and unstable axial dimension during high speed cutting. At present, HSK high-speed toolholders and the hot expansion, cold shrinkage and fastening type of toolholders are the most popular ones. The shank is generally tapered and in contact with the spindle endface at the same time, which is more rigid, but the tungsten end mills are less replaceable. Since this type of heating system is more expensive, it is sufficient to use HSK type knife shank system in the initial stage. When the number of high-speed tool machines in an enterprise is more than 3, it is more appropriate to use the hot expansion, cold shrinkage and fastening type of toolholders.
Tungsten carbide end mills are one of the most active and important factors in high-speed machining, which directly affects machining efficiency, manufacturing costs and product accuracy. Tungsten carbide end mills are subjected to high temperature, high pressure, friction, impact and vibration loads during high-speed machining. The technology of high speed cutting tungsten and steel milling cutters is developing rapidly, with more applications such as diamond (PCD), cubic boron nitride (CBN), ceramic tungsten and steel milling cutters, coated carbide, (carbon) titanium nitride carbide TIC(N), etc.
Carbide is the most common material used for cutting tungsten steel end mills for machining cast iron and alloy steel. Carbide tungsten carbide cutters have good abrasion resistance, but are less hard than cubic boron nitride and ceramics. In order to improve the hardness and surface finish, tungsten steel end mills are coated with titanium nitride (TiN), aluminum titanium nitride (TiALN) and other materials. Coating technology has enabled the development of coatings from single coats to multi-layer, multi-coated materials, and has become one of the key technologies to improve high-speed cutting capabilities. Carbide inserts with diameters from 10 to 40 mm and titanium carbide coating can process materials with a Rockwell hardness of less than 42, while titanium nitride coated tungsten mills can process materials with a Rockwell hardness of 42 and higher.
For high-speed steel cutting, tungsten carbide end mills should be made of carbide P with high thermal and fatigue strength, coated carbide, cubic boron nitride (CBN) and CBN composite tungsten carbide end mills (WBN), etc. For cutting cast iron, fine grain Class K carbide should be used for roughing, and composite silicon nitride ceramics or polycrystalline cubic boron nitride (PCNB) composite tungsten steel cutters should be used for finishing.
For precision machining of non-ferrous or non-metallic materials, use polycrystalline diamond PCD or CVD diamond-coated tungsten steel cutters. When selecting cutting parameters, for round inserts and ball end mills, attention should be paid to the concept of effective diameter. Carbide cutters for high-speed milling should be manufactured to a dynamic balance design. The front angle of the tungsten cutter is smaller and the rear angle is slightly larger than the front angle of a conventional tungsten cutter. The main and secondary cutting edge joint should be rounded or angled to increase the angle of the tip to prevent heat wear on the tip. The length of the cutting edge near the tip and the material volume of the tungsten cutter should be increased to improve the rigidity of the tungsten cutter. The overhang of the tungsten steel end mills is as short as possible and the central toughness of the cutter body is good under conditions that guarantee safety and meet machining requirements. The shank is thicker in diameter than the tungsten carbide end mills and the connecting shank is inverted tapered to increase its rigidity. Leave a coolant hole in the center of the carbide end mill and the carbide end mill system as much as possible. Ball end mills should consider the effective cutting length and the cutting edge should be as short as possible. Two helix-grooved ball end mills are usually used for roughing and milling complex surfaces, while four helix-grooved ball end mills are usually used for finishing complex surfaces.
III. High-speed mold processing technology and strategy
High-speed machining includes roughing and residual roughing for the purpose of removing residuals, as well as semi-finishing, finishing and mirror finishing for the purpose of obtaining high quality machined surfaces and fine structures.
1. Roughing
The main goal of tool roughing is to pursue material removal rates per unit of time and to prepare the geometric profile of the workpiece for semi-finishing. The process solution for roughing in high-speed machining is a combination of high cutting speed, high feed rate and small cutting volume.Contour machining is a common machining method used in many CAM software. The more commonly used is the spiral and Z-axis contour methods, that is, only one feed in the machining area, without lifting the tool to generate a continuous smooth tungsten end mill path, the feed and retract method is circular in and out. The characteristic of the spiral equal height method is that there is no movement of the knife path between the equal height, which can avoid the frequent lifting of the knife, the effect of the feed on the surface quality of the parts and unnecessary wear and tear of the mechanical equipment. Separate treatment of steep and flat areas, calculation of suitable contours and areas suitable for the use of similar 3D offsets, and the use of spirals to generate optimized carbide end mill paths with little tool lift for better surface quality.
In high-speed machining, it is necessary to adopt the circular cut-in and cut-out connection methods, as well as the circular transition at the corners, to avoid sudden changes in the direction of feed of the tungsten carbide end mills, and to prohibit the use of direct down tool connection method, so as to avoid burying the tungsten carbide end mills into the workpiece. When machining the mold cavity, you should avoid the vertical insertion of carbide end mills into the workpiece and adopt the tilting down tooling method (common tilting angle is 20°~30°).
When machining the core of the mold, the tool should be cut from the outside of the workpiece first and then horizontally into the workpiece as much as possible. Tungsten carbide milling cutters should be used as much as possible to cut in and out of the workpiece by inclined type (or circular arc type) to avoid vertical cutting in and out. Climbing cutting reduces cutting heat, reduces tungsten cutter stress and machining hardening, and improves machining quality.
2. Semi-finishing
The main goal of semi-finishing of molds is to make the workpiece profile shape flat and the surface finish balance even, which is especially important for tool steel molds because it will affect the change of the cutting layer area of tungsten steel end mills during finishing and the change of the tungsten steel end mill load, which will affect the stability of the cutting process and the finish surface quality.Roughing is based on the volume model and finishing is based on the face model. The previously developed CAD/CAM system is discontinuous in its geometric description of the parts. Since there is no intermediate information describing the model after roughing and before finishing, the distribution of the remaining machining residuals on the roughing surface and the maximum remaining machining residuals are unknown. Therefore, the semi-finishing strategy should be optimized to ensure a uniform residual machining balance on the workpiece surface after semi-finishing. The optimization process includes the calculation of the profile after roughing, the calculation of the maximum remaining machining allowance, the determination of the maximum allowable machining allowance, the calculation of the trajectory of the core during semi-finishing, etc. for the area of the profile where the remaining machining allowance is greater than the maximum allowable machining allowance (e.g., areas with a transition radius smaller than the radius of the roughing tungsten cutter such as recesses and corners).
Most of the existing CAD/CAM software for high-speed machining of molds is equipped with residual machining analysis function, and can adopt reasonable semi-finishing strategy according to the size and distribution of residual machining residual.
3. Finishing
The high-speed finishing strategy for dies depends on the point of contact of the tungsten cutter with the workpiece, which varies with the surface slope of the machined surface and the effective radius of the tungsten cutter. For complex surface machining of a combination of surfaces, continuous machining should be performed in a single process whenever possible, rather than machining each surface separately to reduce the number of tool lifts and tool downs. However, due to the variation in surface slope during machining, if only the amount of side milling (Step over) of the machining is defined, it can result in uneven actual steps on surfaces with different slopes, thus affecting machining quality.In general, the radius of curvature of a finished surface should be greater than 1.5 times the radius of the tungsten carbide cutter to avoid sudden changes in the direction of feed. In the high-speed finishing of the mold, in each cut in and out of the workpiece, the change of the feed direction should be as far as possible to adopt a circular or curved transfer, avoid the use of straight transfer to maintain the smoothness of the cutting process.
High-speed finishing strategies include strategies such as three-dimensional bias, contouring and optimal contouring, and spiral contouring. These strategies ensure a smooth and stable cutting process, ensuring that the material on the workpiece can be cut quickly to obtain a highly accurate and smooth cutting surface.
The basic requirement of finishing is to obtain a high precision, smooth surface quality of the part, and to easily achieve the machining of fine areas, such as small rounded corners, grooves, etc. For many shapes, the most effective strategy for finishing is to use a three-dimensional spiral strategy. The use of this strategy avoids the frequent directional changes that can occur with parallel and offset finishing strategies, thereby increasing machining speed and reducing tungsten mill wear.
This strategy generates a continuous smooth tungsten end mill path with little tool lifting. This machining technology combines the advantages of spiral machining and contour machining strategies, with a more stable load on tungsten end mills and fewer tool lifts, shortening machining time and reducing the chance of tungsten end mill tool damage. It also improves the quality of the finished surface and minimizes the need for hand sanding after finishing. A combination of isometric finishing methods for steep areas and three-dimensional isometric finishing methods for flat areas is required in many scenarios.
The choice of machining method and the programming strategy to be used are key when using CAM systems for CNC programming of high-speed machining, in addition to the selection of tungsten steel cutters and machining parameters according to specific conditions. An accomplished programmer using a CAD/CAM workstation should also be a qualified design and craftsman with a proper understanding of the geometry of the parts, knowledge and concepts of the ideal process arrangement and rational tungsten mill trajectory design.
IV. High-speed cutting CNC programming
High-speed milling operations are placing increasing demands on CNC programming systems, and expensive high-speed machining equipment is placing greater demands on software safety and effectiveness. In addition to high speed cutting tools and high speed cutting tungsten cutters, it is also important to have the right CAM programming software. An excellent high-speed CAM programming system should have high computing speed, strong interpolation function, automatic overcutting and processing capability, automatic toolholder and clamp interference check, feed rate optimization, track monitoring function, tungsten milling tool track editing and optimization function and machining residual analysis function, etc. High-speed cutting programming should firstly pay attention to the safety and effectiveness of the machining method; secondly, do everything possible to ensure smooth and smooth trajectory of the carbide end mills, which will directly affect the machining quality and the life of parts such as the spindle of the tooling machine; finally, make the carbide end mills as evenly loaded as possible, which will directly affect the life of the carbide end mills.
1. The CAM system should have a high computational programming speed
With very small feeds and depths of cut for high-speed machining, the NC program is much larger than for conventional CNC machining, requiring faster software calculations to save time in editing and optimizing the tungsten milling tool track.
2. Full automatic overcut handling and automatic toolholder interference inspection capability
High-speed machining is carried out at nearly 10 times the cutting speed of conventional machining, and if overcutting occurs, it will have disastrous consequences for the tooling machine, products and tungsten carbide end mills, so the CAM system is required to have the capability of automatic overcutting prevention and automatic toolholder and clamp interference check and bypass function. The system automatically prompts for the minimum length of the clamped carbide cutter and automatically performs an interference check of the carbide cutter.
3. Abundant trajectory strategy for high speed cutting tungsten steel end mills
In order to ensure maximum cutting efficiency and safety during high-speed machining, the CAM system should be able to automatically optimize the feed rate according to the size of the instantaneous machining residuals, edit and optimize the tungsten milling tool track, analyze the machining residuals and monitor the machining track to ensure the stability of the force state of high-speed machining tungsten milling tools and improve the service life of tungsten milling tools.Due to the stringent requirements of high-speed machining processes, overcut protection is even more important, so it takes more time to simulate and check the NC instruction. In general, high-speed machining takes much longer than normal machining programming times. In order to ensure adequate utilization of the high-speed processing equipment, more CAM staff is required. Existing CAM software such as hyperMILL, PowerMILL, MasterCAM, UnigraphicsNX, etc. all provide a high speed milling tungsten tool tracing strategy with relevant features.
High speed cutting technology is mainly used in the automotive industry and mold industry, especially in the machining of complex curved surfaces, the workpiece itself or the rigidity of the tungsten carbide end mill system, etc. The high efficiency and high quality are highly appreciated.