A must-see for injection molders! The advanced mould equipment and technology of those precision mould factories
2020-04-28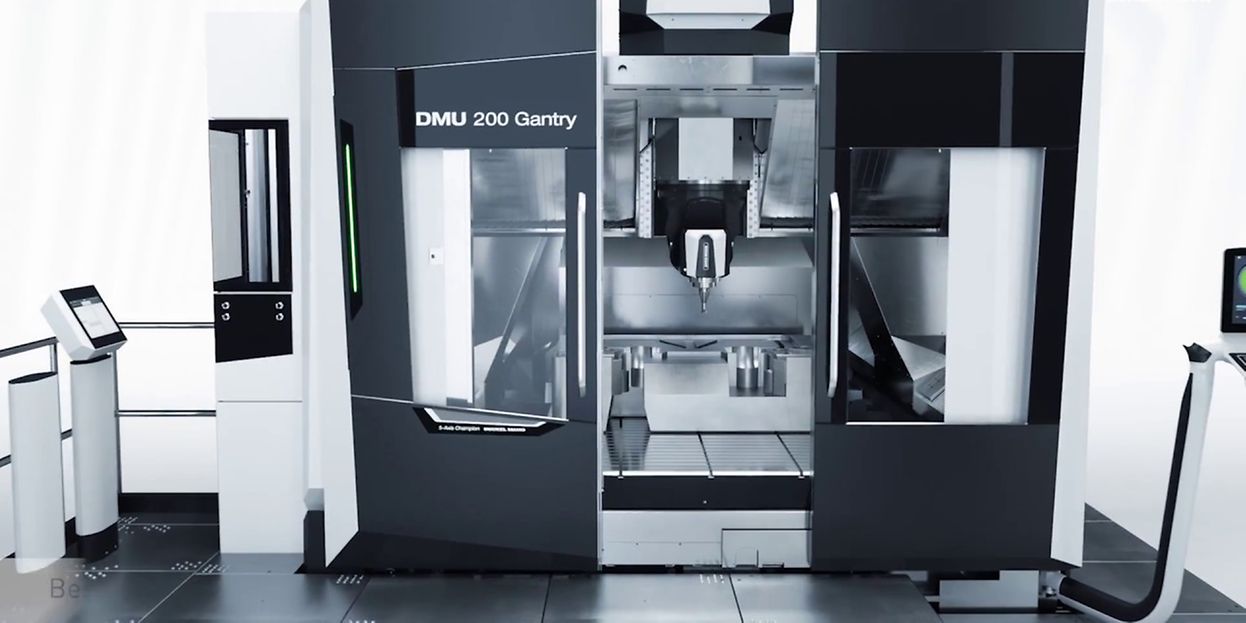
The manufacturing of precision molds cannot be done without that advanced machining equipment. The main processes of tool making are CNC milling, jogging wire cutting, EDM, grinding, turning, measuring, automation, etc. This article introduces the advanced equipment and technology of these processes.
It can be said that the rapid development of the plastic mould manufacturing industry is mainly due to the innovation of CNC milling technology. From traditional general milling machines, to three-axis machining centers, to today's five-axis high-speed milling, the machining of even the most complex three-dimensional parts is almost a reality, and the hardness of the material is no longer a limitation. The main cavities and faces of plastic molds are finished by CNC milling.
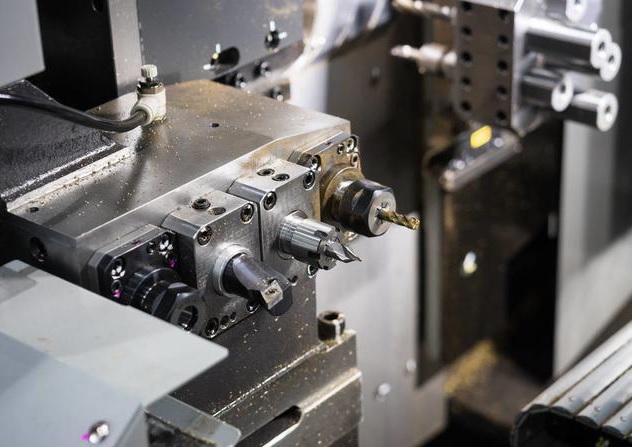
High-speed milling uses small diameter end mills (typical tools are integral carbide ball end mills, end mills and corrugated end mills), high rotational speeds (up to 40,000 rpm on the spindle), small cycle feeds, resulting in a significant increase in production efficiency and a stable accuracy of 5 μm; at the same time, due to the low milling force, the workpiece thermal deformation is reduced, the depth of milling is smaller and the feed is faster (linear motors, up to 80 m/min fast travel speed, up to 2 g acceleration), and the surface finish is Ra<0.15 μm. High-speed milling can process hardened die steel parts up to 60 HRC, so high-speed milling allows cutting after heat treatment, making the die manufacturing process greatly simplified.
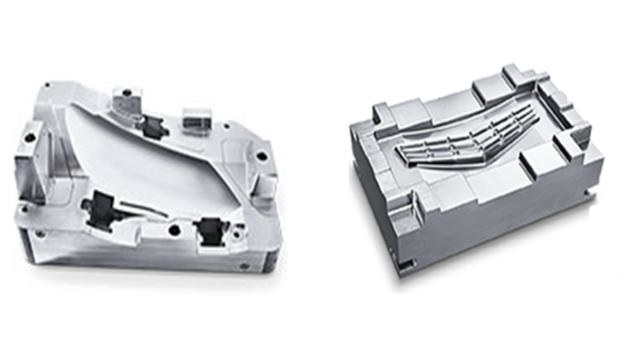
Advanced foreign manufacturers of CNC milling equipment include GF Machining Solutions (Switzerland), DMG (Germany), Hammer (Germany), Makino (Japan), Rhodes (Germany), OPS (Germany), Chiron (Germany), Index (Germany), Yamazaki Mazak (Japan), Big Nestle (Japan), Haas (USA), etc.
Low speed wire machining is mainly used for the machining of 2D and 3D straight grain parts such as stamping dies, plastic dies, powder metallurgy dies, etc. The largest proportion of them is the machining of press dies, the press die, die retaining plate, concave die and unloading plate and other precision hole machining, low speed wire cutting is indispensable key technology. In injection mould manufacturing, common applications include machining of inlay holes, ejector holes, beveled ejector holes, cavity clearing angles and sliders.
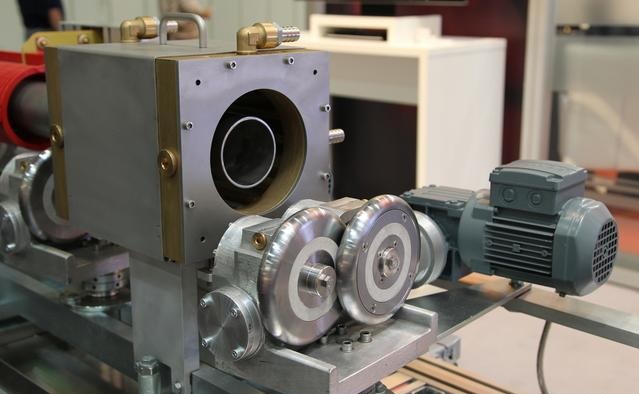
Low speed wire machining is a high-precision machining method, high-end tool machine can achieve less than 3μm machining accuracy, surface roughness up to Ra0.05μm, at present can achieve automatic wire-threading cutting of 0.02~0.03mm electrode wire, practical cutting efficiency up to 200mm 2/min or so.
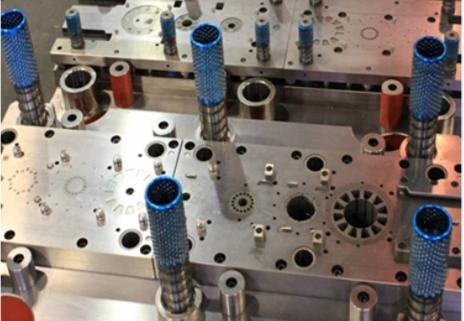
Advanced foreign manufacturers of low speed wire machining equipment include Swiss GF Machining Solutions, Japanese Mitsubishi, Western Japan, Japanese Sodick, Japanese Makino, Japanese Frank, etc.
EDM is suitable for the machining of complex parts such as precision small cavities, narrow joints, grooves and corners. Where tools are difficult to reach complex surfaces, where deep cuts are required, and where long-diameter bits are particularly high, EDM processes are superior to milling processes. For the machining of highly technical parts, re-electrification of the milling electrode improves the success rate and is more suitable for re-electrification than for expensive tooling costs. In addition, where EDM finishing is required, EDM is used to provide a spark pattern surface.
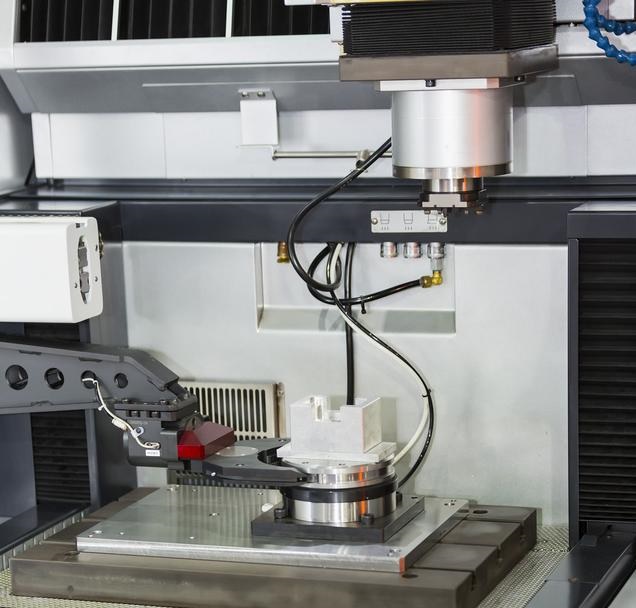
With the rapid development of high-speed milling today, the space for EDM development is being squeezed to a certain extent. At the same time, high-speed milling has brought greater technological advancement to EDM machining. For example, the use of high speed milling to manufacture electrodes allows the number of electrode designs to be greatly reduced due to the realization of narrow area machining and high quality surface results. In addition, the use of high-speed milling to manufacture electrodes can also increase production efficiency to a new level and ensure the high precision of the electrodes, which in turn increases the accuracy of EDM machining. If most of the machining of the cavity is done by high-speed milling, the EDM is only used as an auxiliary section to clear the corners and trim the edges, so that the retention is more even and less.
.jpg)
The precision discharge motor enables mirror EDM machining with Ra<0.1μm and uniform matte surface and textured surface machining at all levels when the machining area is less than 20 square centimeters. For fine parts, such as connectors, it is possible to achieve a clear angle of less than 0.02mm and a machining accuracy of less than 5μm. For the discharge of special and complex parts, special process modules such as ICs, LEDs, connectors, large cavities, narrow joints, RSM textures, etc. are provided for the optimization of the process is the integration of expert experience. The machine can be equipped with a quick-loading positioning clamp and an automatic electrode changer for long periods of time without any personalized automatic discharge machining.
Advanced foreign EDM equipment manufacturers include GF Machining Solutions (Switzerland), Makino (Japan), OPS (Germany), Sodick (Japan), Mitsubishi (Japan), Axor (Germany), Oona (Spain), etc.
A grinding machine is a precision machine for finishing the surface of a part, especially hardened parts. The main grinders used for die and mold machining are surface grinders, universal internal and external cylindrical grinders, and coordinate grinders (PG optical curve grinders).
Small flat grinders are mainly used to machine small size mold parts, such as precision inserts, precision dies, slides, etc. Large water grinders are often used for larger formwork sizes. Nowadays, the speed of grinding wheel line and table movement in surface grinding machines have become a common trend, and the speed of movement has improved greatly thanks to the use of advanced functional component technologies such as linear guides, linear motors, and static pressure levers. The minimum vertical feed to the grinding head can be 0.1μm, the grinding surface roughness Ra<0.05μm, and the machining accuracy can be controlled within 1μm, achieving ultra-fine grinding.
The foreign manufacturer of advanced grinding machine equipment is represented by the Schleifring Group, which has acquired many of the world's top grinding machine manufacturers, including STUDER, BLOHM, MAEGERLE, JUNG, SCHAUD, MIKROSA, EWAG and WALTER. The various types of grinding machines produced by well-known companies of Schleifring provide comprehensive grinding solutions. For surface grinding, most of the domestic precision mold mills use Japanese surface grinders, such as the Japanese Okamoto grinder.
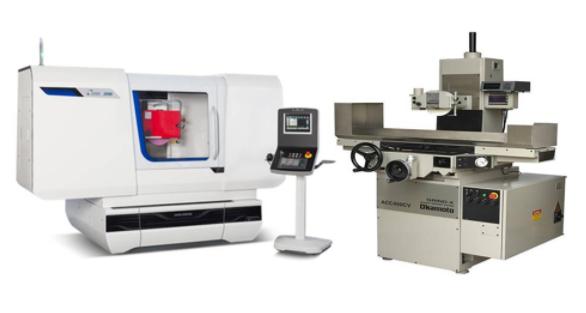
Mold rotating body parts with high precision and good surface finish, even complex curved parts, require the use of high-precision cylindrical grinding machines, such as the HALF inlays for bottle injection moulds. The grinding process is carried out using a high-speed rotary grinding wheel, which can be used to process hardened materials, such as hardened die steel, carbide, etc. The Stuttgart universal internal and external cylindrical grinding machine is designed for medium-sized single-component and batch grinding of workpieces and is suitable for customized solutions (external cylindrical grinding, non-circular grinding, threaded grinding, internal cylindrical grinding).
The optical curve grinder can grind holes with high accuracy and various profile shapes. Using a plotter to match the process, the plotter engraves the desired shape on the film, the film is affixed to the projection screen and corrected, and the processor will mold the shape according to the molding on the film. Optical projection grinding is suitable for profile grinding of hard materials, such as tungsten or carbide, and occasionally HSS parts. General machining of connector punching dies, punches, terminals, precision half-stroke punches, lower die feeders, unloading plate feeders, etc.
The famous optical curve grinders include the Swiss HAUSER, the American MOORE, and the Japanese AMADA, which has a spindle speed of up to 30,000 rpm and a machining accuracy within 2μm, the minimum inner R-angle of the machining is R0.03mm and the outer R-angle is R0.02mm, and the thinnest part of the processed shaped punch can be 0.06mm, and the deep groove diameter ratio of the processed groove is about 2:1, and the surface roughness Ra can be 0.025μm.
A CNC lathe is also a common machining equipment in a mold workshop. Its machining range is all rotating body parts. Due to the high level of development of digital control technology, complex shapes of the rotating body can be easily programmed, and the tooling machine can automatically change the tool, greatly increasing the production efficiency. The machining accuracy and manufacturing technology of CNC lathes is improving, and there is even a trend towards turning instead of grinding. Commonly used to process round inlays, supports, positioning rings and other parts in molds, and widely used in pen and bottle mouth molds. In fact, advanced CNC lathes are no longer limited to "turning", but have been expanded to include turning and milling machines, which are complex, multi-process parts that can even be machined all at once.
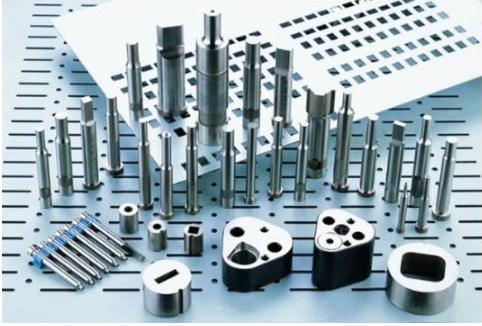
Advanced foreign manufacturers of CNC turning tools include German DMG, Swiss Tonas, Japanese Yamazaki Mazak, German Schutte, American Harding, American Haas, etc.
High precision measuring equipment plays an important role from digital mapping in the early stages of mold design, through the measurement of mold machining processes, to the measurement of mold acceptance and the measurement of mold repair at a later stage. There are mainly three coordinate measuring machines, image measuring machines, and portable joint arm measuring machines for large mold field measurements, etc.
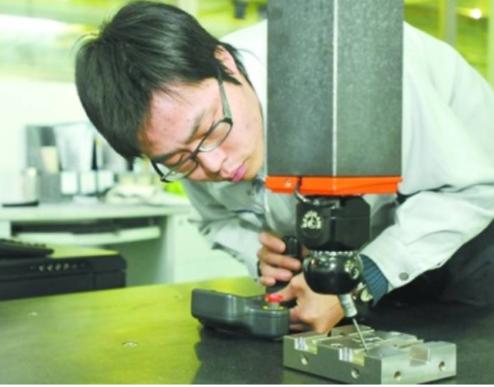
Three-coordinate inspection is a precision measurement method for inspecting workpieces. Based on the collection and calculation of space point coordinates, the three-coordinate measuring machine is used to check and measure the shape and position tolerance of the workpiece to determine whether the workpiece is within the tolerance range. A probing system generally consists of a probe and a contact probe, which makes slight contact with the surface of the workpiece to obtain the coordinates of the measurement point. During the measurement process, the coordinate measuring machine converts the measurement of the various geometric elements of the workpiece into the coordinate positions of the points on those geometric elements, and the software calculates the size, shape, relative position and other parameters of those geometric elements based on the mathematical model of the corresponding geometry. The coordinate measuring machine can be easily interfaced with CAD to provide real-time feedback to design and production departments to improve product design or production processes. Three-coordinate inspection is also sometimes used in reverse engineering design. Typical foreign equipment manufacturers are Sweden's Hexcon, Germany's Zeiss, Germany's Leeds, Japan's Mitutoyo, etc.
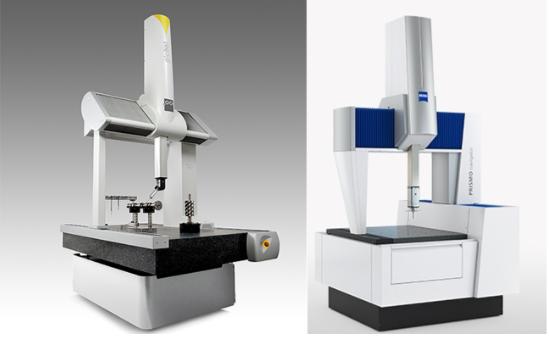
The image measuring instrument uses the image head to collect the image of the workpiece, and then uses digital image machining technology to extract the coordinate points on the surface of the workpiece with various complex shapes, and then uses coordinate conversion and data machining technology to convert the geometric elements in the coordinate measurement space. Typical equipment is Swedish Hexcon, Japanese Nikon, Japanese Mitutoyo, etc.
The above describes the six processes of mold making. In fact, one molded part often requires the use of multiple processes to be manufactured. In this process, the parts are constantly clamped and calibrated, which takes a lot of time, while the tooling machine is idle, and the machining capacity of the expensive equipment is not fully utilized. With the increasing competition in the manufacturing sector. Shorter production cycles are part of this growing trend. Foreign clamp manufacturers use a stable and accurate reference system to realize the unified reference interchangeability of milling, turning, measuring, EDM and other processes, it only takes about a minute to quickly complete the electrode clamping and alignment on the tooling machine, the repeat positioning accuracy is within 3μm, minimizing the setting time and greatly improving the actual running time of the tooling machine. It has proven to be an essential condition for modern production.
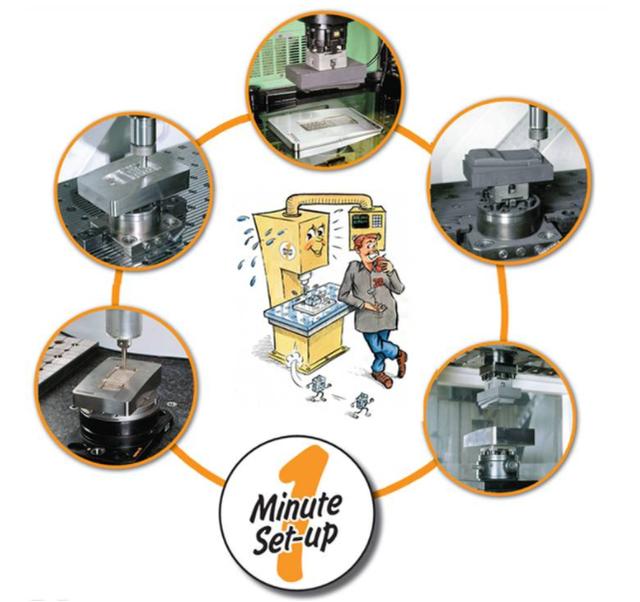
Foreign manufacturers of advanced quick-loading and positioning systems mainly include Swiss GF Machining Solutions System 3R clamps, Swiss EROWA clamps, etc.
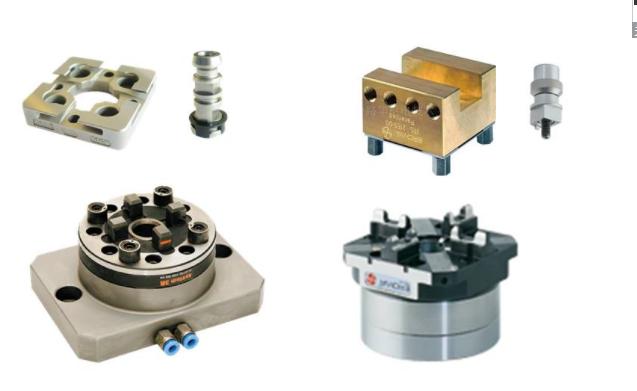
The basis for automation is already in place when the Quick-Clip positioning system is used. The advanced mold shop is equipped with robots and flexible system management software to form a mold machining center automation unit. Advanced foreign manufacturers have begun to evolve from being mere equipment providers to providers of packaged solutions. From the current point of view, the personalized mold manufacturing package can only adapt to the professional type of mold manufacturers, for a wide variety of varieties, a variety of complex mold manufacturing, due to the need to spend more pre-conditioning and preparation time, has not yet been well promoted, but the development of automation is a trend, there will certainly be more perfect development.
I. CNC Milling Machining
It can be said that the rapid development of the plastic mould manufacturing industry is mainly due to the innovation of CNC milling technology. From traditional general milling machines, to three-axis machining centers, to today's five-axis high-speed milling, the machining of even the most complex three-dimensional parts is almost a reality, and the hardness of the material is no longer a limitation. The main cavities and faces of plastic molds are finished by CNC milling.
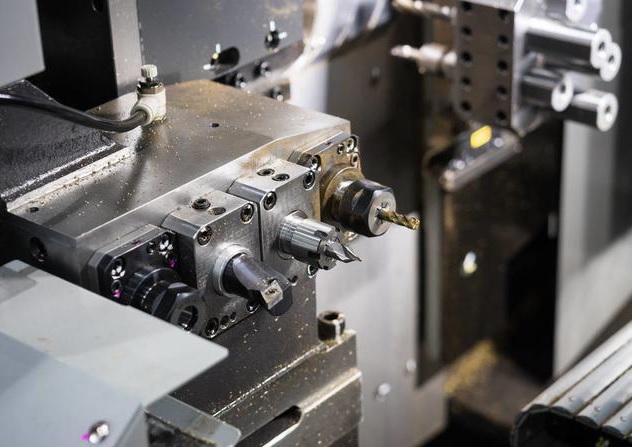
High-speed milling uses small diameter end mills (typical tools are integral carbide ball end mills, end mills and corrugated end mills), high rotational speeds (up to 40,000 rpm on the spindle), small cycle feeds, resulting in a significant increase in production efficiency and a stable accuracy of 5 μm; at the same time, due to the low milling force, the workpiece thermal deformation is reduced, the depth of milling is smaller and the feed is faster (linear motors, up to 80 m/min fast travel speed, up to 2 g acceleration), and the surface finish is Ra<0.15 μm. High-speed milling can process hardened die steel parts up to 60 HRC, so high-speed milling allows cutting after heat treatment, making the die manufacturing process greatly simplified.
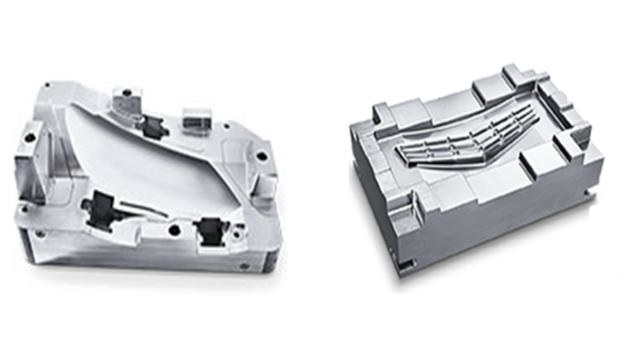
Advanced foreign manufacturers of CNC milling equipment include GF Machining Solutions (Switzerland), DMG (Germany), Hammer (Germany), Makino (Japan), Rhodes (Germany), OPS (Germany), Chiron (Germany), Index (Germany), Yamazaki Mazak (Japan), Big Nestle (Japan), Haas (USA), etc.
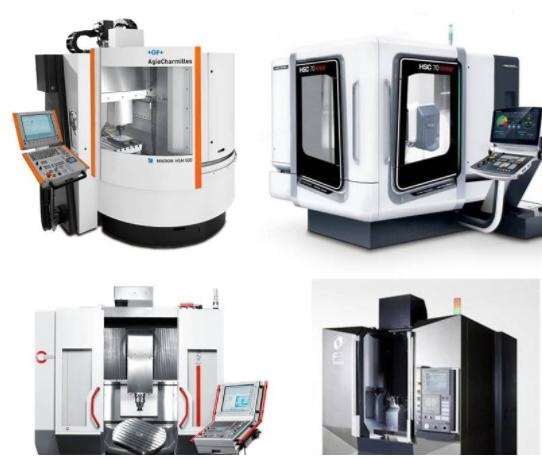
II. Low Speed Wire Machining
Low speed wire machining is mainly used for the machining of 2D and 3D straight grain parts such as stamping dies, plastic dies, powder metallurgy dies, etc. The largest proportion of them is the machining of press dies, the press die, die retaining plate, concave die and unloading plate and other precision hole machining, low speed wire cutting is indispensable key technology. In injection mould manufacturing, common applications include machining of inlay holes, ejector holes, beveled ejector holes, cavity clearing angles and sliders.
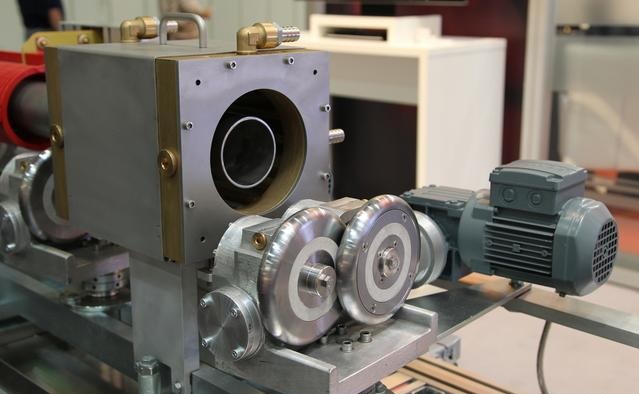
Low speed wire machining is a high-precision machining method, high-end tool machine can achieve less than 3μm machining accuracy, surface roughness up to Ra0.05μm, at present can achieve automatic wire-threading cutting of 0.02~0.03mm electrode wire, practical cutting efficiency up to 200mm 2/min or so.
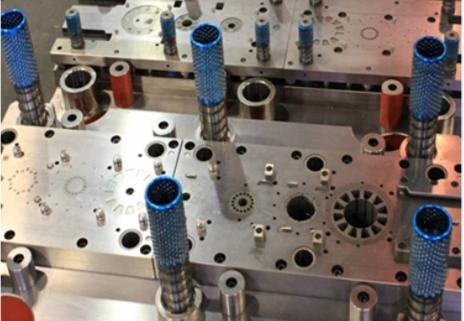
Advanced foreign manufacturers of low speed wire machining equipment include Swiss GF Machining Solutions, Japanese Mitsubishi, Western Japan, Japanese Sodick, Japanese Makino, Japanese Frank, etc.
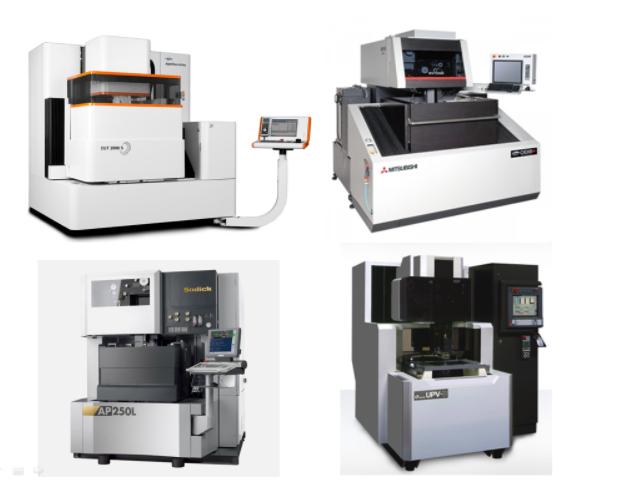
III. EDM
EDM is suitable for the machining of complex parts such as precision small cavities, narrow joints, grooves and corners. Where tools are difficult to reach complex surfaces, where deep cuts are required, and where long-diameter bits are particularly high, EDM processes are superior to milling processes. For the machining of highly technical parts, re-electrification of the milling electrode improves the success rate and is more suitable for re-electrification than for expensive tooling costs. In addition, where EDM finishing is required, EDM is used to provide a spark pattern surface.
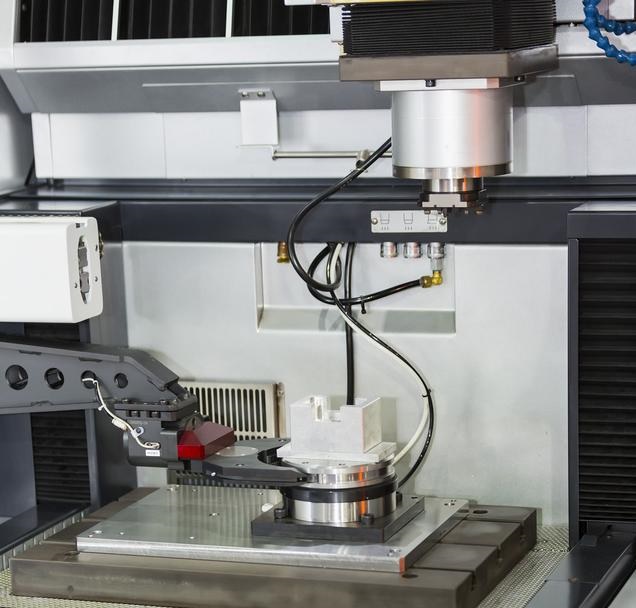
With the rapid development of high-speed milling today, the space for EDM development is being squeezed to a certain extent. At the same time, high-speed milling has brought greater technological advancement to EDM machining. For example, the use of high speed milling to manufacture electrodes allows the number of electrode designs to be greatly reduced due to the realization of narrow area machining and high quality surface results. In addition, the use of high-speed milling to manufacture electrodes can also increase production efficiency to a new level and ensure the high precision of the electrodes, which in turn increases the accuracy of EDM machining. If most of the machining of the cavity is done by high-speed milling, the EDM is only used as an auxiliary section to clear the corners and trim the edges, so that the retention is more even and less.
.jpg)
The precision discharge motor enables mirror EDM machining with Ra<0.1μm and uniform matte surface and textured surface machining at all levels when the machining area is less than 20 square centimeters. For fine parts, such as connectors, it is possible to achieve a clear angle of less than 0.02mm and a machining accuracy of less than 5μm. For the discharge of special and complex parts, special process modules such as ICs, LEDs, connectors, large cavities, narrow joints, RSM textures, etc. are provided for the optimization of the process is the integration of expert experience. The machine can be equipped with a quick-loading positioning clamp and an automatic electrode changer for long periods of time without any personalized automatic discharge machining.
Advanced foreign EDM equipment manufacturers include GF Machining Solutions (Switzerland), Makino (Japan), OPS (Germany), Sodick (Japan), Mitsubishi (Japan), Axor (Germany), Oona (Spain), etc.
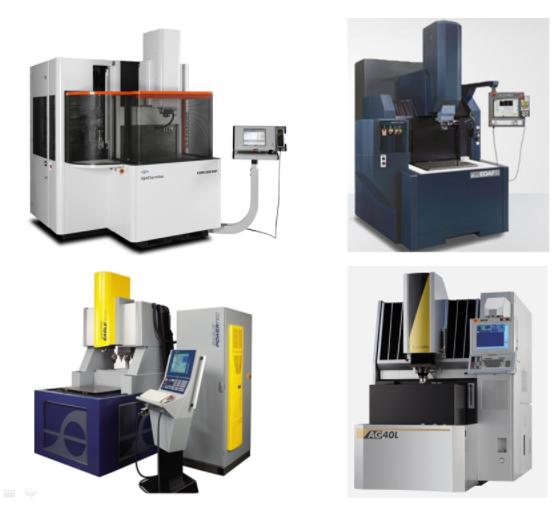
IV. Grinder Machining
A grinding machine is a precision machine for finishing the surface of a part, especially hardened parts. The main grinders used for die and mold machining are surface grinders, universal internal and external cylindrical grinders, and coordinate grinders (PG optical curve grinders).
Small flat grinders are mainly used to machine small size mold parts, such as precision inserts, precision dies, slides, etc. Large water grinders are often used for larger formwork sizes. Nowadays, the speed of grinding wheel line and table movement in surface grinding machines have become a common trend, and the speed of movement has improved greatly thanks to the use of advanced functional component technologies such as linear guides, linear motors, and static pressure levers. The minimum vertical feed to the grinding head can be 0.1μm, the grinding surface roughness Ra<0.05μm, and the machining accuracy can be controlled within 1μm, achieving ultra-fine grinding.
The foreign manufacturer of advanced grinding machine equipment is represented by the Schleifring Group, which has acquired many of the world's top grinding machine manufacturers, including STUDER, BLOHM, MAEGERLE, JUNG, SCHAUD, MIKROSA, EWAG and WALTER. The various types of grinding machines produced by well-known companies of Schleifring provide comprehensive grinding solutions. For surface grinding, most of the domestic precision mold mills use Japanese surface grinders, such as the Japanese Okamoto grinder.
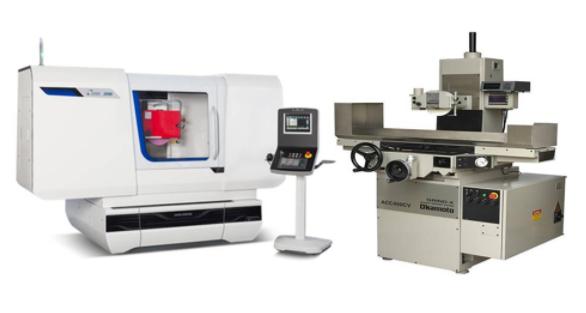
Mold rotating body parts with high precision and good surface finish, even complex curved parts, require the use of high-precision cylindrical grinding machines, such as the HALF inlays for bottle injection moulds. The grinding process is carried out using a high-speed rotary grinding wheel, which can be used to process hardened materials, such as hardened die steel, carbide, etc. The Stuttgart universal internal and external cylindrical grinding machine is designed for medium-sized single-component and batch grinding of workpieces and is suitable for customized solutions (external cylindrical grinding, non-circular grinding, threaded grinding, internal cylindrical grinding).
The optical curve grinder can grind holes with high accuracy and various profile shapes. Using a plotter to match the process, the plotter engraves the desired shape on the film, the film is affixed to the projection screen and corrected, and the processor will mold the shape according to the molding on the film. Optical projection grinding is suitable for profile grinding of hard materials, such as tungsten or carbide, and occasionally HSS parts. General machining of connector punching dies, punches, terminals, precision half-stroke punches, lower die feeders, unloading plate feeders, etc.
The famous optical curve grinders include the Swiss HAUSER, the American MOORE, and the Japanese AMADA, which has a spindle speed of up to 30,000 rpm and a machining accuracy within 2μm, the minimum inner R-angle of the machining is R0.03mm and the outer R-angle is R0.02mm, and the thinnest part of the processed shaped punch can be 0.06mm, and the deep groove diameter ratio of the processed groove is about 2:1, and the surface roughness Ra can be 0.025μm.
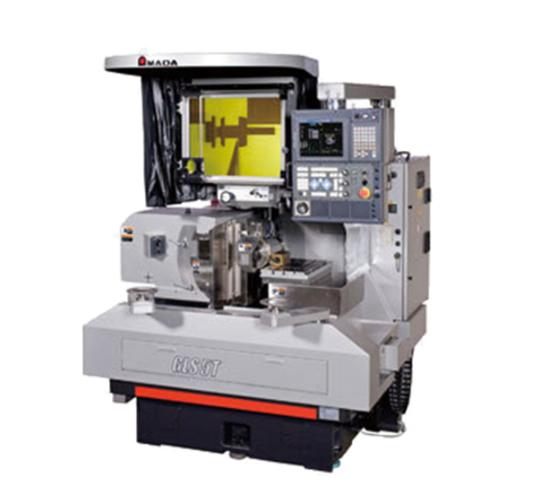
V. CNC Lathe
A CNC lathe is also a common machining equipment in a mold workshop. Its machining range is all rotating body parts. Due to the high level of development of digital control technology, complex shapes of the rotating body can be easily programmed, and the tooling machine can automatically change the tool, greatly increasing the production efficiency. The machining accuracy and manufacturing technology of CNC lathes is improving, and there is even a trend towards turning instead of grinding. Commonly used to process round inlays, supports, positioning rings and other parts in molds, and widely used in pen and bottle mouth molds. In fact, advanced CNC lathes are no longer limited to "turning", but have been expanded to include turning and milling machines, which are complex, multi-process parts that can even be machined all at once.
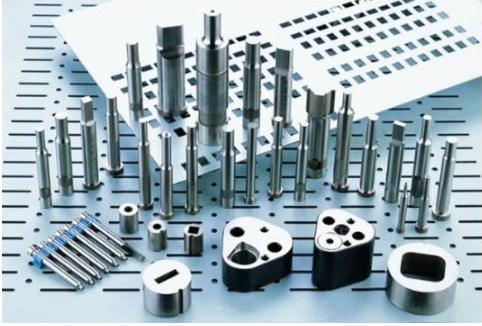
Advanced foreign manufacturers of CNC turning tools include German DMG, Swiss Tonas, Japanese Yamazaki Mazak, German Schutte, American Harding, American Haas, etc.
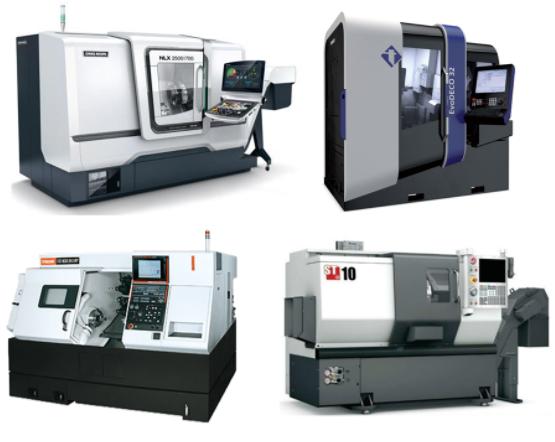
VI. Measurement
High precision measuring equipment plays an important role from digital mapping in the early stages of mold design, through the measurement of mold machining processes, to the measurement of mold acceptance and the measurement of mold repair at a later stage. There are mainly three coordinate measuring machines, image measuring machines, and portable joint arm measuring machines for large mold field measurements, etc.
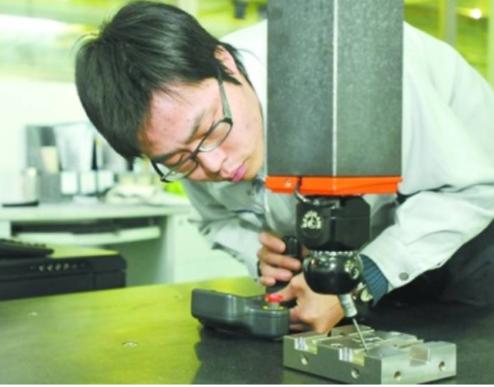
Three-coordinate inspection is a precision measurement method for inspecting workpieces. Based on the collection and calculation of space point coordinates, the three-coordinate measuring machine is used to check and measure the shape and position tolerance of the workpiece to determine whether the workpiece is within the tolerance range. A probing system generally consists of a probe and a contact probe, which makes slight contact with the surface of the workpiece to obtain the coordinates of the measurement point. During the measurement process, the coordinate measuring machine converts the measurement of the various geometric elements of the workpiece into the coordinate positions of the points on those geometric elements, and the software calculates the size, shape, relative position and other parameters of those geometric elements based on the mathematical model of the corresponding geometry. The coordinate measuring machine can be easily interfaced with CAD to provide real-time feedback to design and production departments to improve product design or production processes. Three-coordinate inspection is also sometimes used in reverse engineering design. Typical foreign equipment manufacturers are Sweden's Hexcon, Germany's Zeiss, Germany's Leeds, Japan's Mitutoyo, etc.
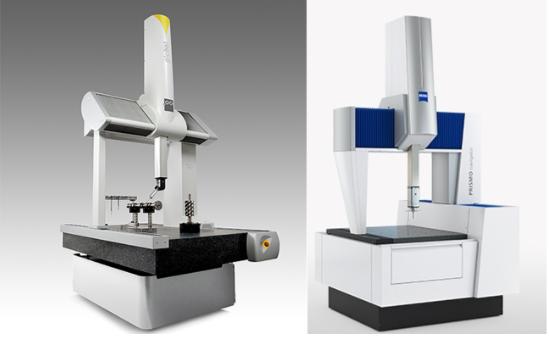
The image measuring instrument uses the image head to collect the image of the workpiece, and then uses digital image machining technology to extract the coordinate points on the surface of the workpiece with various complex shapes, and then uses coordinate conversion and data machining technology to convert the geometric elements in the coordinate measurement space. Typical equipment is Swedish Hexcon, Japanese Nikon, Japanese Mitutoyo, etc.
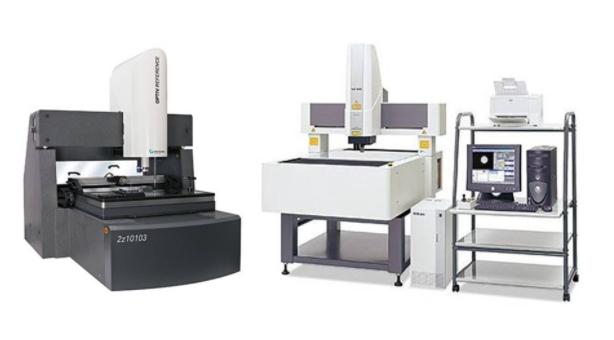
VII. Quick-clamp Positioning System and Automation
The above describes the six processes of mold making. In fact, one molded part often requires the use of multiple processes to be manufactured. In this process, the parts are constantly clamped and calibrated, which takes a lot of time, while the tooling machine is idle, and the machining capacity of the expensive equipment is not fully utilized. With the increasing competition in the manufacturing sector. Shorter production cycles are part of this growing trend. Foreign clamp manufacturers use a stable and accurate reference system to realize the unified reference interchangeability of milling, turning, measuring, EDM and other processes, it only takes about a minute to quickly complete the electrode clamping and alignment on the tooling machine, the repeat positioning accuracy is within 3μm, minimizing the setting time and greatly improving the actual running time of the tooling machine. It has proven to be an essential condition for modern production.
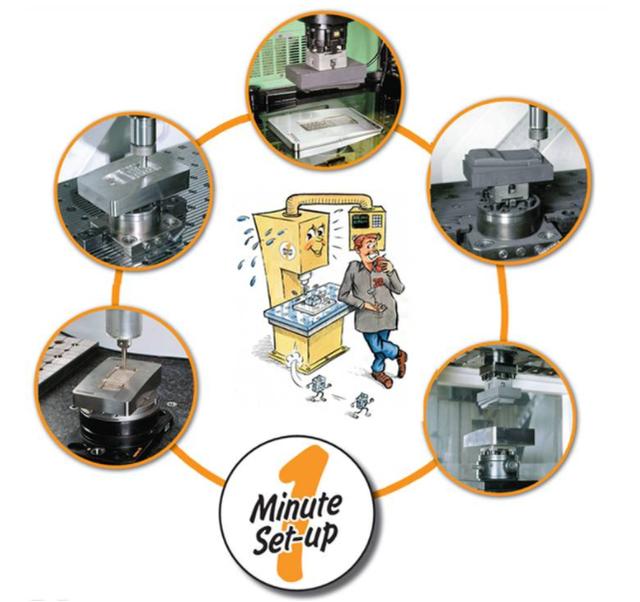
Foreign manufacturers of advanced quick-loading and positioning systems mainly include Swiss GF Machining Solutions System 3R clamps, Swiss EROWA clamps, etc.
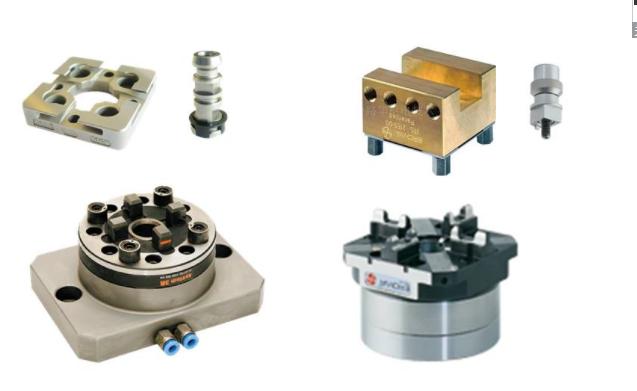
The basis for automation is already in place when the Quick-Clip positioning system is used. The advanced mold shop is equipped with robots and flexible system management software to form a mold machining center automation unit. Advanced foreign manufacturers have begun to evolve from being mere equipment providers to providers of packaged solutions. From the current point of view, the personalized mold manufacturing package can only adapt to the professional type of mold manufacturers, for a wide variety of varieties, a variety of complex mold manufacturing, due to the need to spend more pre-conditioning and preparation time, has not yet been well promoted, but the development of automation is a trend, there will certainly be more perfect development.