一文搞懂模具高速切削加工!
2020-04-06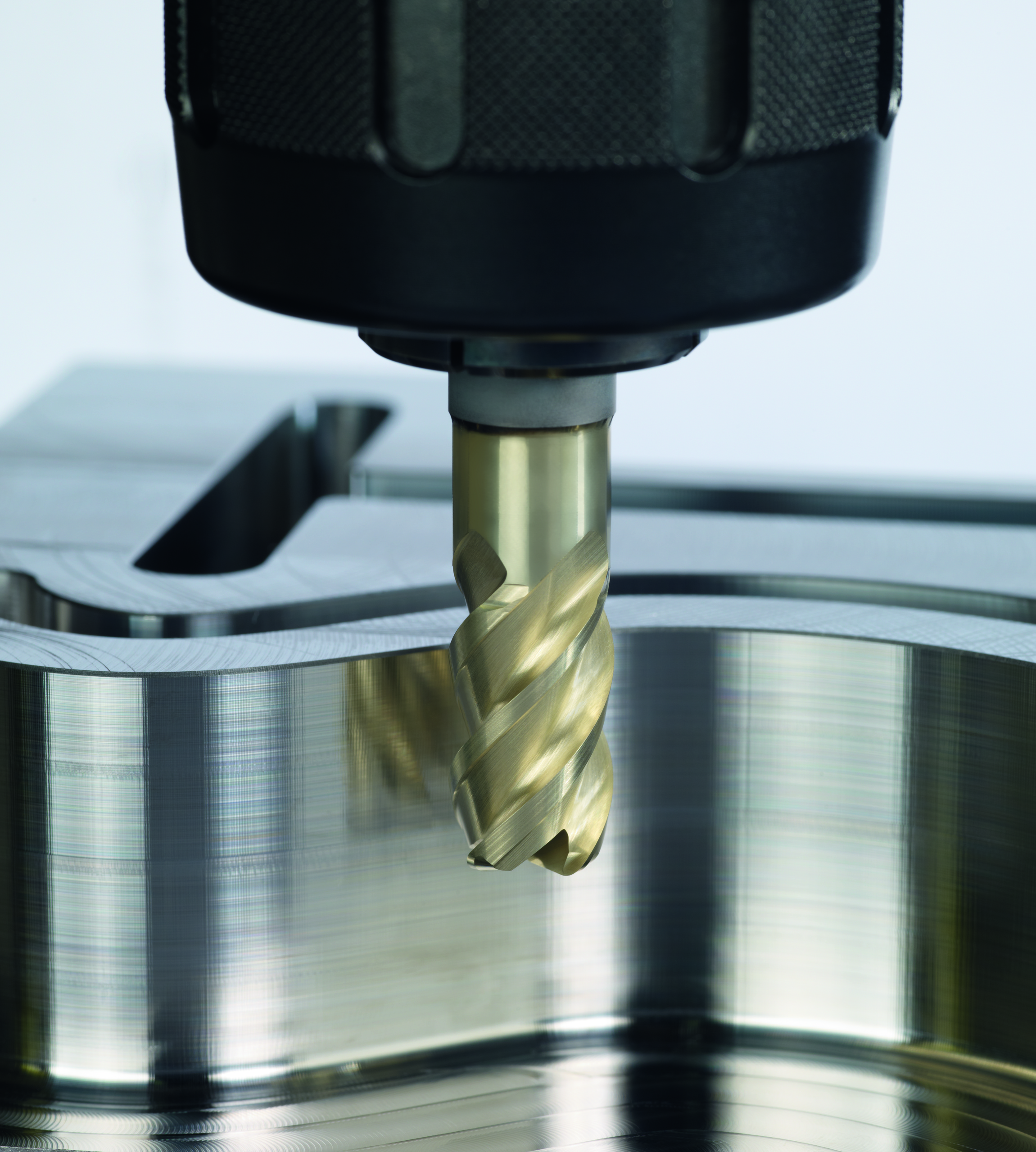
隨著產品的美觀度及功能要求越來越高,產品內部結構設計得越來越複雜,模具的外形設計也日趨複雜,自由曲面所占比例不斷增加,相應的模具結構也越來越複雜。這些都對模具加工技術提出了更高要求,高速加工技術已越來越多地應用於模具型腔的加工與製造中。
數控高速切削加工相對於傳統的切削加工,其切削速度、進給速度有了很大的提高,而且切削機理也不相同。高速切削使切削加工發生了本質性的飛躍,其單位功率的金屬切除率提高了30%~40%,切削力降低了30%,鎢鋼銑刀的切削壽命提高了70%,留於工件的切削熱大幅度降低,低階切削振動幾乎消失。
在模具的高淬硬鋼件(HRC45~HRC65)的加工過程中,採用高速切削可以取代部分EDM電加工和磨削拋光的工序,從而避免了電極的製造和費時的電加工,大幅度減少了鉗工的打磨與拋光量。對於一些市場上越來越需要的薄壁模具工件,高速切削也可順利完成,而且在高速切削CNC加工中心上,模具一次裝夾可完成多工步加工。
高速切削工具機的床身等支撐部件應具有很好的動、靜剛度,熱剛度和最佳的阻尼特性。大部分工具機都採用高質量、高剛性和高抗張性的灰鑄鐵作為支撐部件材料,有的工具機公司還在底座中添加高阻尼特性的聚合物混凝土,以增加其抗振性和熱穩定性,這不但可保證工具機精度穩定,也可防止切削時鎢鋼銑刀振顫。採用封閉式床身設計,整體鑄造床身,對稱床身結構並配有密布的加強筋等也是提高工具機穩定性的重要措施。
高速工具機的主軸性能是實現高速切削加工的重要條件。高速切削工具機主軸的轉速範圍為10000~100000m/min,主軸功率大於15kW。通過主軸壓縮空氣或冷卻系統控制刀柄和主軸間的軸向間隙不大於0.005mm。還要求主軸具有快速升速、在指定位置快速准停的性能(即具有極高的角加減速度),因此高速主軸常採用液體靜壓軸承式、空氣靜壓軸承式、熱壓氮化矽(Si3N4)陶瓷軸承磁懸浮軸承式等結構形式。潤滑多採用油氣潤滑、噴射潤滑等技術。主軸冷卻一般採用主軸內部水冷或氣冷。
為滿足模具高速加工的需要,高速加工工具機的驅動系統應具有下列特性:
(1) 高的進給速度。研究表明,對於小直徑鎢鋼銑刀,提高轉速和每齒進給量有利於降低鎢鋼銑刀磨損。目前常用的進給速度範圍為20~30m/min,如採用大導程滾珠絲槓傳動,進給速度可達60m/min;採用直線電機則可使進給速度達到120m/min。
(2)高的加速度。對三維複雜曲面廓形的高速加工要求驅動系統具有良好的加速度特性,要求提供高速進給的驅動器(快進速度約40m/min,3D輪廓加工速度為10m/min),能夠提供0.4m/s2到10m/s2的加速度和減速度。
工具機製造商大多採用全閉環位置伺服控制的小導程、大尺寸、高質量的滾珠絲槓或大導程多頭絲槓。
先進的數控系統是保證模具複雜曲面高速加工質量和效率的關鍵因素,模具高速切削加工對數控系統的基本要求為:
(1)高速的數字控制迴路,包括:32位或64位並行處理器及1.5Gb以上的硬碟。
(2)速度和加速度的前饋控制;數字驅動系統的爬行控制(Jerk control)。
(3)先進的插補方法,以獲得良好的表面質量、精確的尺寸和高的幾何精度。
(4)要求具有大容量緩衝寄存器,可預先閱讀和檢查多個程序段,以便在被加工表面形狀(曲率)發生變化時可及時採取改變進給速度等措施以避免過切等。
(5)誤差補償功能,包括因電機、主軸等發熱導致的熱誤差補償、象限誤差補償、測量系統誤差補償等功能。此外,模具高速切削加工對數據傳輸速度的要求也很高。
(6)傳統的數據接口, 如RS232串行口的傳輸速度為19.2kb,而許多先進的加工中心均已採用以太區域網進行數據傳輸,速度可達200kb。
高速加工採用帶塗層的硬質合金鎢鋼銑刀,在高速、高溫的情況下不用切削液,切削效率更高。這是因為:切削主軸高速旋轉,切削液若要達到切削區,首先要克服極大的離心力;即使它克服了離心力進入切削區,也可能由於切削區的高溫而立即蒸發,冷卻效果很小甚至沒有;同時切削液會使鎢鋼銑刀刃部的溫度激烈變化,容易導致裂紋的產生,所以要採用油/氣冷卻潤滑的乾式切削方式。這種方式可以用高壓氣體迅速吹走切削區產生的切削,從而將大量的切削熱帶走,同時經霧化的潤滑油可以在鎢鋼銑刀刃部和工件表面形成一層極薄的微觀保護膜,可有效地延長鎢鋼銑刀壽命並提高零件的表面質量。
由於高速切削加工時離心力和振動的影響,要求鎢鋼銑刀具有很高的幾何精度和裝夾重複定位精度以及很高的剛度和高速動平衡的安全可靠性。由於高速切削加工時較大的離心力和振動等特點,傳統的7:24錐度刀柄系統在進行高速切削時表現出明顯的剛性不足、重複定位精度不高、軸向尺寸不穩定等缺陷,主軸的膨脹引起鎢鋼銑刀及夾緊機構質心的偏離,影響鎢鋼銑刀的動平衡能力。目前應用較多的是HSK高速刀柄和國外現今流行的熱脹冷縮緊固式刀柄。熱脹冷縮緊固式刀柄有加熱系統,刀柄一般都採用錐部與主軸端面同時接觸,其剛性較好,但是鎢鋼銑刀可換性較差,一個刀柄只能安裝一種連接直徑的鎢鋼銑刀。由於此類加熱系統比較昂貴,在初期時採用HSK類的刀柄系統即可。當企業的高速工具機數量超過3台以上時,採用熱脹冷縮緊固式刀柄比較合適。
鎢鋼銑刀是高速切削加工中最活躍重要的因素之一,它直接影響著加工效率、製造成本和產品的加工精度。鎢鋼銑刀在高速加工過程中要承受高溫、高壓、摩擦、衝擊和振動等載荷,高速切削鎢鋼銑刀應具有良好的機械性能和熱穩定性,即具有良好的抗衝擊、耐磨損和抗熱疲勞的特性。高速切削加工的鎢鋼銑刀技術發展速度很快,應用較多的如金剛石(PCD)、立方氮化硼(CBN)、陶瓷鎢鋼銑刀、塗層硬質合金、(碳)氮化鈦硬質合金TIC(N)等。
在加工鑄鐵和合金鋼的切削鎢鋼銑刀中,硬質合金是最常用的鎢鋼銑刀材料。硬質合金鎢鋼銑刀耐磨性好,但硬度比立方氮化硼和陶瓷低。為提高硬度和表面光潔度,採用鎢鋼銑刀塗層技術,塗層材料為氮化鈦(TiN)、氮化鋁鈦(TiALN)等。塗層技術使塗層由單一塗層發展為多層、多種塗層材料的塗層,已成為提高高速切削能力的關鍵技術之一。直徑在10~40mm範圍內,且有碳氮化鈦塗層的硬質合金刀片能夠加工洛氏硬度小於42的材料,而氮化鈦鋁塗層的鎢鋼銑刀能夠加工洛氏硬度為42甚至更高的材料。
高速切削鋼材時,鎢鋼銑刀材料應選用熱硬性和疲勞強度高的P類硬質合金、塗層硬質合金、立方氮化硼(CBN)與CBN複合鎢鋼銑刀材料(WBN)等。切削鑄鐵,應選用細晶粒的K類硬質合金進行粗加工,選用複合氮化矽陶瓷或聚晶立方氮化硼(PCNB)複合鎢鋼銑刀進行精加工。
精密加工有色金屬或非金屬材料時,應選用聚晶金剛石PCD或CVD金剛石塗層鎢鋼銑刀。選擇切削參數時,針對圓刀片和球頭銑刀,應注意有效直徑的概念。高速切削鎢鋼銑刀應按動平衡設計製造。鎢鋼銑刀的前角比常規鎢鋼銑刀的前角要小,后角略大。主副切削刃連接處應修圓或導角,來增大刀尖角,防止刀尖處熱磨損。應加大刀尖附近的切削刃長度和鎢鋼銑刀材料體積,提高鎢鋼銑刀剛性。在保證安全和滿足加工要求的條件下,鎢鋼銑刀懸伸儘可能短,刀體中央韌性要好。刀柄要比鎢鋼銑刀直徑粗壯,連接柄呈倒錐狀,以增加其剛性。儘量在鎢鋼銑刀及鎢鋼銑刀系統中央留有冷卻液孔。球頭立銑刀要考慮有效切削長度,刃口要儘量短,兩螺旋槽球頭立銑刀通常用於粗銑複雜曲面,四螺旋槽球頭立銑刀通常用於精銑複雜曲面。
高速加工包括以去除餘量為目的的粗加工、殘留粗加工,以及以獲取高質量的加工表面及細微結構為目的的半精加工、精加工和鏡面加工等。
模具粗加工的主要目標是追求單位時間內的材料去除率,並為半精加工準備工件的幾何輪廓。高速加工中的粗加工所應採取的工藝方案是高切削速度、高進給率和小切削用量的組合。
等高加工方式是眾多CAM軟體普遍採用的一種加工方式。應用較多的是螺旋等高和等Z軸等高兩種方式,也就是在加工區域僅一次進刀,在不抬刀的情況下生成連續光滑的鎢鋼銑刀路徑,進、退刀方式採用圓弧切入、切出。螺旋等高方式的特點是,沒有等高層之間的刀路移動,可避免頻繁抬刀、進刀對零件表面質量的影響及機械設備不必要的耗損。對陡峭和平坦區域分別處理,計算適合等高及適合使用類似3D偏置的區域,並且可以使用螺旋方式,在很少抬刀的情況下生成優化的鎢鋼銑刀路徑,獲得更好的表面質量。
在高速加工中,一定要採取圓弧切入、切出連接方式,以及拐角處圓弧過渡,避免突然改變鎢鋼銑刀進給方向,禁止使用直接下刀的連接方式,避免將鎢鋼銑刀埋入工件。加工模具型腔時,應避免鎢鋼銑刀垂直插入工件,而應採用傾斜下刀方式(常用傾斜角為20°~30°),最好採用螺旋式下刀以降低鎢鋼銑刀載荷。
加工模具型芯時,應儘量先從工件外部下刀然後水平切入工件。鎢鋼銑刀切入、切出工件時應儘可能採用傾斜式(或圓弧式)切入、切出,避免垂直切入、切出。採用攀爬式切削可降低切削熱,減小鎢鋼銑刀受力和加工硬化程度,提高加工質量。
模具半精加工的主要目標是使工件輪廓形狀平整,表面精加工餘量均勻,這對於工具鋼模具尤為重要,因為它將影響精加工時鎢鋼銑刀切削層面積的變化及鎢鋼銑刀載荷的變化,從而影響切削過程的穩定性及精加工表面質量。
粗加工是基於體積模型,精加工則是基於面模型。以前開發的CAD/CAM系統對零件的幾何描述是不連續的,由於沒有描述粗加工後、精加工前加工模型的中間信息,故粗加工表面的剩餘加工餘量分布及最大剩餘加工餘量均是未知的。因此應對半精加工策略進行優化以保證半精加工後工件表面具有均勻的剩餘加工餘量。優化過程包括:粗加工後輪廓的計算、最大剩餘加工餘量的計算、最大允許加工餘量的確定、對剩餘加工餘量大於最大允許加工餘量的型面分區(如凹槽、拐角等過渡半徑小於粗加工鎢鋼銑刀半徑的區域)以及半精加工時刀心軌跡的計算等。
現有的模具高速加工CAD/CAM軟體大都具備剩餘加工餘量分析功能,並能根據剩餘加工餘量的大小及分布情況採用合理的半精加工策略。
模具的高速精加工策略取決於鎢鋼銑刀與工件的接觸點,而鎢鋼銑刀與工件的接觸點隨著加工表面的曲面斜率和鎢鋼銑刀有效半徑的變化而變化。對於由多個曲面組合而成的複雜曲面加工,應儘可能在一個工序中進行連續加工,而不是對各個曲面分別進行加工,以減少抬刀、下刀的次數。然而,由於加工中表面斜率的變化,如果只定義加工的側吃刀量(Step over),就可能造成在斜率不同的表面上實際步距不均勻,從而影響加工質量。
一般情況下,精加工曲面的曲率半徑應大於鎢鋼銑刀半徑的1.5倍,以避免進給方向的突然轉變。在模具的高速精加工中,在每次切入、切出工件時,進給方向的改變應儘量採用圓弧或曲線轉接,避免採用直線轉接,以保持切削過程的平穩性。
高速精加工策略包括三維偏置、等高精加工和最佳等高精加工、螺旋等高精加工等策略。這些策略可保證切削過程光順、穩定,確保能快速切除工件上的材料,得到高精度、光滑的切削表面。精加工的基本要求是要獲得很高的精度、光滑的零件表面質量,輕鬆實現精細區域的加工,如小的圓角、溝槽等。對許多形狀來說,精加工最有效的策略是使用三維螺旋策略。使用這種策略可避免使用平行策略和偏置精加工策略中會出現的頻繁的方向改變,從而提高加工速度,減少鎢鋼銑刀磨損。這個策略可以在很少抬刀的情況下生成連續光滑的鎢鋼銑刀路徑。這種加工技術綜合了螺旋加工和等高加工策略的優點,鎢鋼銑刀負荷更穩定,提刀次數更少,可縮短加工時間,減小鎢鋼銑刀損壞機率。它還可以改善加工表面質量,最大限地減小精加工後手工打磨的需要。在許多場合需要將陡峭區域的等高精加工和平坦區域三維等距精加工方法結合起來使用。
數控編程也要考慮幾何設計和工藝安排,在使用CAM系統進行高速加工數控編程時,除鎢鋼銑刀和加工參數根據具體情況選擇外,加工方法的選擇和採用的編程策略就成為了關鍵。一名出色的使用CAD/CAM工作站的編程工程師應該同時也是一名合格的設計與工藝師,他應對零件的幾何結構有一個正確的理解,具備對於理想工序安排以及合理鎢鋼銑刀軌跡設計的知識和概念。
高速切削加工對數控編程系統的要求越來越高,價格昂貴的高速加工設備對軟體提出了更高的安全性和有效性要求。高速切削有著比傳統切削特殊的工藝要求,除了要有高速切削工具機和高速切削鎢鋼銑刀外,具有合適的CAM編程軟體也是至關重要的。數控加工的數控指令包含了所有的工藝過程,一個優秀的高速加工CAM編程系統應具有很高的計算速度、較強的插補功能、全程自動過切檢查及處理能力、自動刀柄與夾具干涉檢查、進給率優化處理功能、待加工軌跡監控功能、鎢鋼銑刀軌跡編輯優化功能和加工殘餘分析功能等。高速切削編程首先要注意加工方法的安全性和有效性;其次,要盡一切可能保證鎢鋼銑刀軌跡光滑平穩,這會直接影響加工質量和工具機主軸等零件的壽命;最後,要儘量使鎢鋼銑刀載荷均勻,這會直接影響鎢鋼銑刀的壽命。
高速加工中採用非常小的進給量與切深,其NC程序比對傳統數控加工程序要大得多,因而要求軟體計算速度要快,以節省鎢鋼銑刀軌跡編輯和優化編程的時間。
高速加工以傳統加工近10倍的切削速度進行加工,一旦發生過切對工具機、產品和鎢鋼銑刀將產生災難性的後果,所以要求其CAM系統必須具有全程自動防過切處理的能力及自動刀柄與夾具干涉檢查、繞避功能。系統能夠自動提示最短夾持鎢鋼銑刀長度,並自動進行鎢鋼銑刀干涉檢查。
高速加工對加工工藝走刀方式比傳統方式有著特殊要求,為了能夠確保最大的切削效率,又保證在高速切削時加工的安全性,CAM系統應能根據加工瞬時餘量的大小自動對進給率進行優化處理,能自動進行鎢鋼銑刀軌跡編輯優化、加工殘餘分析並對待加工軌跡監控,以確保高速加工鎢鋼銑刀受力狀態的平穩性,提高鎢鋼銑刀的使用壽命。
因高速加工工藝要求嚴格,過切保護更加重要,故需花多的時間對NC指令進行仿真檢驗。一般情況下,高速加工編程時間比一般加工編程時間要長得多。為了保證高速加工設備足夠的使用率,需配置更多的CAM人員。現有的CAM軟體,如hyperMILL、PowerMILL、MasterCAM、UnigraphicsNX等都提供了相關功能的高速切削鎢鋼銑刀軌跡策略。
高速切削技術目前主要應用於汽車工業和模具行業,尤其是在加工複雜曲面的領域、工件本身或鎢鋼銑刀系統剛性要求較高的加工領域等,其高效、高質量為人們所推崇。
數控高速切削加工相對於傳統的切削加工,其切削速度、進給速度有了很大的提高,而且切削機理也不相同。高速切削使切削加工發生了本質性的飛躍,其單位功率的金屬切除率提高了30%~40%,切削力降低了30%,鎢鋼銑刀的切削壽命提高了70%,留於工件的切削熱大幅度降低,低階切削振動幾乎消失。
在模具的高淬硬鋼件(HRC45~HRC65)的加工過程中,採用高速切削可以取代部分EDM電加工和磨削拋光的工序,從而避免了電極的製造和費時的電加工,大幅度減少了鉗工的打磨與拋光量。對於一些市場上越來越需要的薄壁模具工件,高速切削也可順利完成,而且在高速切削CNC加工中心上,模具一次裝夾可完成多工步加工。
高速切削技術 | |||||
切削材料 | 機床 | 加工 | 工件 | 銑刀 | 功能部件 |
鋼合鑄鐵 輕金屬材料 複合材料 特殊材料 |
CNC 控制系統 冷卻系統 環境 安全設施 |
加工工藝過程 感和監視 系統 |
工件裝夾 操作技術 |
銑刀材料 銑刀切削刃 幾何參數設計 |
高頻電主軸 快速進給系統 裝卡刀具裝置 框架 ,輕結構 |
一、高速切削加工工具機
1. 高穩定性的工具機支撐部件
高速切削工具機的床身等支撐部件應具有很好的動、靜剛度,熱剛度和最佳的阻尼特性。大部分工具機都採用高質量、高剛性和高抗張性的灰鑄鐵作為支撐部件材料,有的工具機公司還在底座中添加高阻尼特性的聚合物混凝土,以增加其抗振性和熱穩定性,這不但可保證工具機精度穩定,也可防止切削時鎢鋼銑刀振顫。採用封閉式床身設計,整體鑄造床身,對稱床身結構並配有密布的加強筋等也是提高工具機穩定性的重要措施。
2. 工具機主軸
高速工具機的主軸性能是實現高速切削加工的重要條件。高速切削工具機主軸的轉速範圍為10000~100000m/min,主軸功率大於15kW。通過主軸壓縮空氣或冷卻系統控制刀柄和主軸間的軸向間隙不大於0.005mm。還要求主軸具有快速升速、在指定位置快速准停的性能(即具有極高的角加減速度),因此高速主軸常採用液體靜壓軸承式、空氣靜壓軸承式、熱壓氮化矽(Si3N4)陶瓷軸承磁懸浮軸承式等結構形式。潤滑多採用油氣潤滑、噴射潤滑等技術。主軸冷卻一般採用主軸內部水冷或氣冷。
3. 工具機驅動系統
為滿足模具高速加工的需要,高速加工工具機的驅動系統應具有下列特性:(1) 高的進給速度。研究表明,對於小直徑鎢鋼銑刀,提高轉速和每齒進給量有利於降低鎢鋼銑刀磨損。目前常用的進給速度範圍為20~30m/min,如採用大導程滾珠絲槓傳動,進給速度可達60m/min;採用直線電機則可使進給速度達到120m/min。
(2)高的加速度。對三維複雜曲面廓形的高速加工要求驅動系統具有良好的加速度特性,要求提供高速進給的驅動器(快進速度約40m/min,3D輪廓加工速度為10m/min),能夠提供0.4m/s2到10m/s2的加速度和減速度。
工具機製造商大多採用全閉環位置伺服控制的小導程、大尺寸、高質量的滾珠絲槓或大導程多頭絲槓。
4. 數控系統
先進的數控系統是保證模具複雜曲面高速加工質量和效率的關鍵因素,模具高速切削加工對數控系統的基本要求為:(1)高速的數字控制迴路,包括:32位或64位並行處理器及1.5Gb以上的硬碟。
(2)速度和加速度的前饋控制;數字驅動系統的爬行控制(Jerk control)。
(3)先進的插補方法,以獲得良好的表面質量、精確的尺寸和高的幾何精度。
(4)要求具有大容量緩衝寄存器,可預先閱讀和檢查多個程序段,以便在被加工表面形狀(曲率)發生變化時可及時採取改變進給速度等措施以避免過切等。
(5)誤差補償功能,包括因電機、主軸等發熱導致的熱誤差補償、象限誤差補償、測量系統誤差補償等功能。此外,模具高速切削加工對數據傳輸速度的要求也很高。
(6)傳統的數據接口, 如RS232串行口的傳輸速度為19.2kb,而許多先進的加工中心均已採用以太區域網進行數據傳輸,速度可達200kb。
5. 冷卻潤滑
高速加工採用帶塗層的硬質合金鎢鋼銑刀,在高速、高溫的情況下不用切削液,切削效率更高。這是因為:切削主軸高速旋轉,切削液若要達到切削區,首先要克服極大的離心力;即使它克服了離心力進入切削區,也可能由於切削區的高溫而立即蒸發,冷卻效果很小甚至沒有;同時切削液會使鎢鋼銑刀刃部的溫度激烈變化,容易導致裂紋的產生,所以要採用油/氣冷卻潤滑的乾式切削方式。這種方式可以用高壓氣體迅速吹走切削區產生的切削,從而將大量的切削熱帶走,同時經霧化的潤滑油可以在鎢鋼銑刀刃部和工件表面形成一層極薄的微觀保護膜,可有效地延長鎢鋼銑刀壽命並提高零件的表面質量。
二、高速切削加工的刀柄和鎢鋼銑刀
由於高速切削加工時離心力和振動的影響,要求鎢鋼銑刀具有很高的幾何精度和裝夾重複定位精度以及很高的剛度和高速動平衡的安全可靠性。由於高速切削加工時較大的離心力和振動等特點,傳統的7:24錐度刀柄系統在進行高速切削時表現出明顯的剛性不足、重複定位精度不高、軸向尺寸不穩定等缺陷,主軸的膨脹引起鎢鋼銑刀及夾緊機構質心的偏離,影響鎢鋼銑刀的動平衡能力。目前應用較多的是HSK高速刀柄和國外現今流行的熱脹冷縮緊固式刀柄。熱脹冷縮緊固式刀柄有加熱系統,刀柄一般都採用錐部與主軸端面同時接觸,其剛性較好,但是鎢鋼銑刀可換性較差,一個刀柄只能安裝一種連接直徑的鎢鋼銑刀。由於此類加熱系統比較昂貴,在初期時採用HSK類的刀柄系統即可。當企業的高速工具機數量超過3台以上時,採用熱脹冷縮緊固式刀柄比較合適。
鎢鋼銑刀是高速切削加工中最活躍重要的因素之一,它直接影響著加工效率、製造成本和產品的加工精度。鎢鋼銑刀在高速加工過程中要承受高溫、高壓、摩擦、衝擊和振動等載荷,高速切削鎢鋼銑刀應具有良好的機械性能和熱穩定性,即具有良好的抗衝擊、耐磨損和抗熱疲勞的特性。高速切削加工的鎢鋼銑刀技術發展速度很快,應用較多的如金剛石(PCD)、立方氮化硼(CBN)、陶瓷鎢鋼銑刀、塗層硬質合金、(碳)氮化鈦硬質合金TIC(N)等。
在加工鑄鐵和合金鋼的切削鎢鋼銑刀中,硬質合金是最常用的鎢鋼銑刀材料。硬質合金鎢鋼銑刀耐磨性好,但硬度比立方氮化硼和陶瓷低。為提高硬度和表面光潔度,採用鎢鋼銑刀塗層技術,塗層材料為氮化鈦(TiN)、氮化鋁鈦(TiALN)等。塗層技術使塗層由單一塗層發展為多層、多種塗層材料的塗層,已成為提高高速切削能力的關鍵技術之一。直徑在10~40mm範圍內,且有碳氮化鈦塗層的硬質合金刀片能夠加工洛氏硬度小於42的材料,而氮化鈦鋁塗層的鎢鋼銑刀能夠加工洛氏硬度為42甚至更高的材料。
高速切削鋼材時,鎢鋼銑刀材料應選用熱硬性和疲勞強度高的P類硬質合金、塗層硬質合金、立方氮化硼(CBN)與CBN複合鎢鋼銑刀材料(WBN)等。切削鑄鐵,應選用細晶粒的K類硬質合金進行粗加工,選用複合氮化矽陶瓷或聚晶立方氮化硼(PCNB)複合鎢鋼銑刀進行精加工。
精密加工有色金屬或非金屬材料時,應選用聚晶金剛石PCD或CVD金剛石塗層鎢鋼銑刀。選擇切削參數時,針對圓刀片和球頭銑刀,應注意有效直徑的概念。高速切削鎢鋼銑刀應按動平衡設計製造。鎢鋼銑刀的前角比常規鎢鋼銑刀的前角要小,后角略大。主副切削刃連接處應修圓或導角,來增大刀尖角,防止刀尖處熱磨損。應加大刀尖附近的切削刃長度和鎢鋼銑刀材料體積,提高鎢鋼銑刀剛性。在保證安全和滿足加工要求的條件下,鎢鋼銑刀懸伸儘可能短,刀體中央韌性要好。刀柄要比鎢鋼銑刀直徑粗壯,連接柄呈倒錐狀,以增加其剛性。儘量在鎢鋼銑刀及鎢鋼銑刀系統中央留有冷卻液孔。球頭立銑刀要考慮有效切削長度,刃口要儘量短,兩螺旋槽球頭立銑刀通常用於粗銑複雜曲面,四螺旋槽球頭立銑刀通常用於精銑複雜曲面。
三、模具高速加工工藝及策略
高速加工包括以去除餘量為目的的粗加工、殘留粗加工,以及以獲取高質量的加工表面及細微結構為目的的半精加工、精加工和鏡面加工等。
1. 粗加工
模具粗加工的主要目標是追求單位時間內的材料去除率,並為半精加工準備工件的幾何輪廓。高速加工中的粗加工所應採取的工藝方案是高切削速度、高進給率和小切削用量的組合。等高加工方式是眾多CAM軟體普遍採用的一種加工方式。應用較多的是螺旋等高和等Z軸等高兩種方式,也就是在加工區域僅一次進刀,在不抬刀的情況下生成連續光滑的鎢鋼銑刀路徑,進、退刀方式採用圓弧切入、切出。螺旋等高方式的特點是,沒有等高層之間的刀路移動,可避免頻繁抬刀、進刀對零件表面質量的影響及機械設備不必要的耗損。對陡峭和平坦區域分別處理,計算適合等高及適合使用類似3D偏置的區域,並且可以使用螺旋方式,在很少抬刀的情況下生成優化的鎢鋼銑刀路徑,獲得更好的表面質量。
在高速加工中,一定要採取圓弧切入、切出連接方式,以及拐角處圓弧過渡,避免突然改變鎢鋼銑刀進給方向,禁止使用直接下刀的連接方式,避免將鎢鋼銑刀埋入工件。加工模具型腔時,應避免鎢鋼銑刀垂直插入工件,而應採用傾斜下刀方式(常用傾斜角為20°~30°),最好採用螺旋式下刀以降低鎢鋼銑刀載荷。
加工模具型芯時,應儘量先從工件外部下刀然後水平切入工件。鎢鋼銑刀切入、切出工件時應儘可能採用傾斜式(或圓弧式)切入、切出,避免垂直切入、切出。採用攀爬式切削可降低切削熱,減小鎢鋼銑刀受力和加工硬化程度,提高加工質量。
2. 半精加工
模具半精加工的主要目標是使工件輪廓形狀平整,表面精加工餘量均勻,這對於工具鋼模具尤為重要,因為它將影響精加工時鎢鋼銑刀切削層面積的變化及鎢鋼銑刀載荷的變化,從而影響切削過程的穩定性及精加工表面質量。粗加工是基於體積模型,精加工則是基於面模型。以前開發的CAD/CAM系統對零件的幾何描述是不連續的,由於沒有描述粗加工後、精加工前加工模型的中間信息,故粗加工表面的剩餘加工餘量分布及最大剩餘加工餘量均是未知的。因此應對半精加工策略進行優化以保證半精加工後工件表面具有均勻的剩餘加工餘量。優化過程包括:粗加工後輪廓的計算、最大剩餘加工餘量的計算、最大允許加工餘量的確定、對剩餘加工餘量大於最大允許加工餘量的型面分區(如凹槽、拐角等過渡半徑小於粗加工鎢鋼銑刀半徑的區域)以及半精加工時刀心軌跡的計算等。
現有的模具高速加工CAD/CAM軟體大都具備剩餘加工餘量分析功能,並能根據剩餘加工餘量的大小及分布情況採用合理的半精加工策略。
3. 精加工
模具的高速精加工策略取決於鎢鋼銑刀與工件的接觸點,而鎢鋼銑刀與工件的接觸點隨著加工表面的曲面斜率和鎢鋼銑刀有效半徑的變化而變化。對於由多個曲面組合而成的複雜曲面加工,應儘可能在一個工序中進行連續加工,而不是對各個曲面分別進行加工,以減少抬刀、下刀的次數。然而,由於加工中表面斜率的變化,如果只定義加工的側吃刀量(Step over),就可能造成在斜率不同的表面上實際步距不均勻,從而影響加工質量。一般情況下,精加工曲面的曲率半徑應大於鎢鋼銑刀半徑的1.5倍,以避免進給方向的突然轉變。在模具的高速精加工中,在每次切入、切出工件時,進給方向的改變應儘量採用圓弧或曲線轉接,避免採用直線轉接,以保持切削過程的平穩性。
高速精加工策略包括三維偏置、等高精加工和最佳等高精加工、螺旋等高精加工等策略。這些策略可保證切削過程光順、穩定,確保能快速切除工件上的材料,得到高精度、光滑的切削表面。精加工的基本要求是要獲得很高的精度、光滑的零件表面質量,輕鬆實現精細區域的加工,如小的圓角、溝槽等。對許多形狀來說,精加工最有效的策略是使用三維螺旋策略。使用這種策略可避免使用平行策略和偏置精加工策略中會出現的頻繁的方向改變,從而提高加工速度,減少鎢鋼銑刀磨損。這個策略可以在很少抬刀的情況下生成連續光滑的鎢鋼銑刀路徑。這種加工技術綜合了螺旋加工和等高加工策略的優點,鎢鋼銑刀負荷更穩定,提刀次數更少,可縮短加工時間,減小鎢鋼銑刀損壞機率。它還可以改善加工表面質量,最大限地減小精加工後手工打磨的需要。在許多場合需要將陡峭區域的等高精加工和平坦區域三維等距精加工方法結合起來使用。
數控編程也要考慮幾何設計和工藝安排,在使用CAM系統進行高速加工數控編程時,除鎢鋼銑刀和加工參數根據具體情況選擇外,加工方法的選擇和採用的編程策略就成為了關鍵。一名出色的使用CAD/CAM工作站的編程工程師應該同時也是一名合格的設計與工藝師,他應對零件的幾何結構有一個正確的理解,具備對於理想工序安排以及合理鎢鋼銑刀軌跡設計的知識和概念。
四、高速切削數控編程
高速切削加工對數控編程系統的要求越來越高,價格昂貴的高速加工設備對軟體提出了更高的安全性和有效性要求。高速切削有著比傳統切削特殊的工藝要求,除了要有高速切削工具機和高速切削鎢鋼銑刀外,具有合適的CAM編程軟體也是至關重要的。數控加工的數控指令包含了所有的工藝過程,一個優秀的高速加工CAM編程系統應具有很高的計算速度、較強的插補功能、全程自動過切檢查及處理能力、自動刀柄與夾具干涉檢查、進給率優化處理功能、待加工軌跡監控功能、鎢鋼銑刀軌跡編輯優化功能和加工殘餘分析功能等。高速切削編程首先要注意加工方法的安全性和有效性;其次,要盡一切可能保證鎢鋼銑刀軌跡光滑平穩,這會直接影響加工質量和工具機主軸等零件的壽命;最後,要儘量使鎢鋼銑刀載荷均勻,這會直接影響鎢鋼銑刀的壽命。
1. CAM系統應具有很高的計算編程速度
高速加工中採用非常小的進給量與切深,其NC程序比對傳統數控加工程序要大得多,因而要求軟體計算速度要快,以節省鎢鋼銑刀軌跡編輯和優化編程的時間。
2. 全程自動防過切處理能力及自動刀柄干涉檢查能力
高速加工以傳統加工近10倍的切削速度進行加工,一旦發生過切對工具機、產品和鎢鋼銑刀將產生災難性的後果,所以要求其CAM系統必須具有全程自動防過切處理的能力及自動刀柄與夾具干涉檢查、繞避功能。系統能夠自動提示最短夾持鎢鋼銑刀長度,並自動進行鎢鋼銑刀干涉檢查。
3. 豐富的高速切削鎢鋼銑刀軌跡策略
高速加工對加工工藝走刀方式比傳統方式有著特殊要求,為了能夠確保最大的切削效率,又保證在高速切削時加工的安全性,CAM系統應能根據加工瞬時餘量的大小自動對進給率進行優化處理,能自動進行鎢鋼銑刀軌跡編輯優化、加工殘餘分析並對待加工軌跡監控,以確保高速加工鎢鋼銑刀受力狀態的平穩性,提高鎢鋼銑刀的使用壽命。因高速加工工藝要求嚴格,過切保護更加重要,故需花多的時間對NC指令進行仿真檢驗。一般情況下,高速加工編程時間比一般加工編程時間要長得多。為了保證高速加工設備足夠的使用率,需配置更多的CAM人員。現有的CAM軟體,如hyperMILL、PowerMILL、MasterCAM、UnigraphicsNX等都提供了相關功能的高速切削鎢鋼銑刀軌跡策略。
高速切削技術目前主要應用於汽車工業和模具行業,尤其是在加工複雜曲面的領域、工件本身或鎢鋼銑刀系統剛性要求較高的加工領域等,其高效、高質量為人們所推崇。