切削刀具在加工超硬和硬態金屬材料時的耐用性
2020-06-14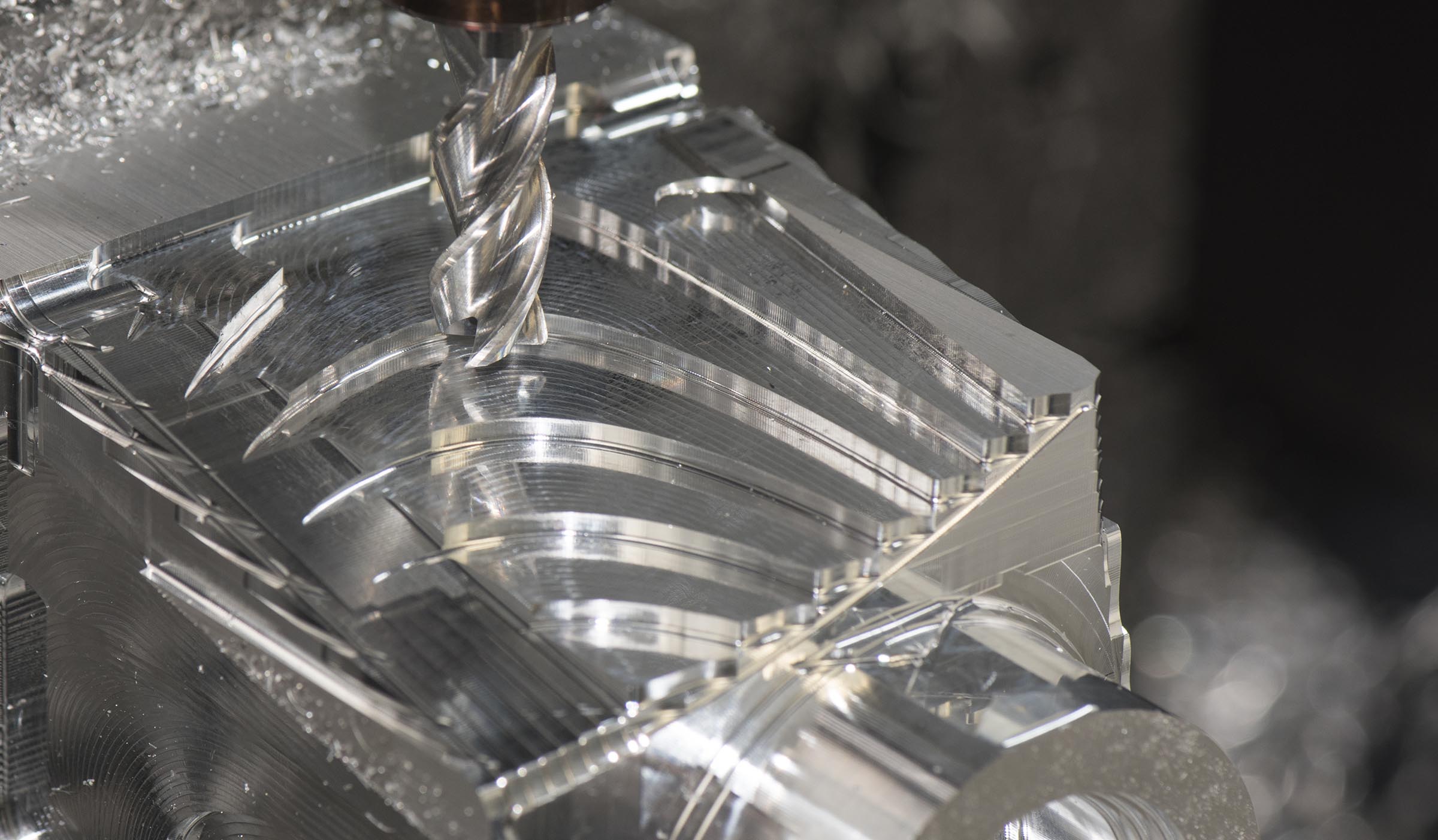
摘要
本文論述了用硬質合金端銑刀加工淬硬鋼的問題。研究中,比較了幾種不同銑刀在加工淬火鋼過程中的耐久性。對於切削刀具,採用了不同的幾何形狀、薄膜沉積或刀具材料的基體。主要目的是全面比較所有的切削刀具。測試工件材料採用DIN X210Cr12。通常這種材料用於生產高應力模具、磨削工具或冷成型工具。根據A. S. Kondratov的說法,在實驗的第一部分檢測切削條件,這是一個短期測試。切削條件在實驗的第二部分中使用,這是對所有刀具的長期測試。在淬火鋼的側銑過程中,測量側翼磨損,並確定每個刀具的耐久性。這項工作的結果將用於進一步研究和開發較硬加工用的切削刀具。
1.簡介
硬質材料和實心固化材料在機械工程行業中經常被使用,例如在切削工具、成型工具或模具的生產中。如果我們想在加工這些材料時具有生產力和競爭力,就必須不斷降低加工成本,提高加工質量。
相關名詞
ae,切削寬度
ap,切削深度
Fy,接續更多的相關名詞
Vc,切削速度v15切削速度為15分鐘的耐久性
VBB,側面磨損
VBkrit,側面嚴重磨損
VBBmax,達到最大的側面磨損值
T,加工時間
T0.1,關鍵側翼磨損耐久性0.1毫米
TK,加工的最後時間
選擇合適的切削刀具是非常重要的。最佳切削刀具的耐久性是選擇合適的切削刀具的要求之一。在加工硬質材料的過程中,切削刀具必須能夠擁有耐磨損、高壓和耐高溫。硬質材料的加工有其特定的問題。研究不同切削條件下淬火鋼加工過程中的切屑形成。切削刀具的耐用性和切削力受許多因素的影響,如切削刀具的材料、幾何形狀、微觀幾何或薄膜沉積等。為了實現高生產率和經濟效益,必須關注這些所有因素。
薄膜的沉積對切削性能有很大的影響,薄膜沉積對切削工具的耐久性有相當重要的作用。在Benga等人測試不同形狀絲錐的塗層和未塗層絲錐刀具的刀具壽命。無論刀具的幾何形狀如何,很明顯,塗有TiAlN的切削刀具比高速鋼刀具具有更長的刀具壽命。考慮到絲攻的孔數,TiAlN的使用使刀具壽命增加了1.35倍。薄膜增加了刀具的表面硬度,降低了摩擦係數,並在加工過程中保護切削刃免受高溫影響。刀具的磨損行為和性能直接受到塗層的影響。研究不同塗層對這種行為的影響。合適的薄膜選擇很重要,但薄膜的塗覆方法和塗覆前後切削刃微觀幾何形狀的製備也非常重要。Denkena等研究了切削刃製備方法對硬質合金塗層刀片在硬加工時性能的影響。結合適當的刀具材料和塗層對切削刀具的磨損形成有重要影響。文中,Aslan採用不同的刀具對硬度為62 HRC的X210 Cr12冷作工具鋼進行端銑加工。Aslan研究了不同塗層的碳化鎢刀具、金屬陶瓷刀具、陶瓷刀具和CBN刀具的性能和磨損行為。
在硬質材料的加工過程中,必須考慮到硬質材料的特殊性能,採用合適的切削條件。切削條件應發揮切削刀具的潛力。由於切削刀具的發展,HSC技術也應用於模具用淬硬鋼的加工中。研究顯示,用塗層硬質合金刀具對淬硬鋼AISI H13進行高速面銑加工,採用不同的切削速度和銑削策略。研究CBN刀具和PVD塗層硬質合金刀具在低速和高速加工策略下對淬硬鋼的切削性能。研究人員觀察了上下銑削策略下的側面磨損情況。切削條件會影響材料的去除率和加工表面的質量。表面質量可能是一個不可忽視的重要要求。能夠達到高耐用性,但不能達到理想表面質量的切削刀具是不經濟的,也是沒有生產力的。研究顯示了一種設計用於AISI D3硬化鋼面銑的特殊硬質合金刀具及其對表面質量的影響。
本文比較了幾種整體硬質合金端銑刀在加工硬度為62±2 HRC的DIN X210Cr12淬火鋼時的耐用性。對於不同幾何形狀的刀具,採用了薄膜沉積或刀具材料的基體。主要目的是對所有切削刀具進行綜合比較,確定其耐用性。此項工作的成果將用於進一步研究和開發硬質加工用切削刀具。
ap,切削深度
Fy,接續更多的相關名詞
Vc,切削速度v15切削速度為15分鐘的耐久性
VBB,側面磨損
VBkrit,側面嚴重磨損
VBBmax,達到最大的側面磨損值
T,加工時間
T0.1,關鍵側翼磨損耐久性0.1毫米
TK,加工的最後時間
選擇合適的切削刀具是非常重要的。最佳切削刀具的耐久性是選擇合適的切削刀具的要求之一。在加工硬質材料的過程中,切削刀具必須能夠擁有耐磨損、高壓和耐高溫。硬質材料的加工有其特定的問題。研究不同切削條件下淬火鋼加工過程中的切屑形成。切削刀具的耐用性和切削力受許多因素的影響,如切削刀具的材料、幾何形狀、微觀幾何或薄膜沉積等。為了實現高生產率和經濟效益,必須關注這些所有因素。
薄膜的沉積對切削性能有很大的影響,薄膜沉積對切削工具的耐久性有相當重要的作用。在Benga等人測試不同形狀絲錐的塗層和未塗層絲錐刀具的刀具壽命。無論刀具的幾何形狀如何,很明顯,塗有TiAlN的切削刀具比高速鋼刀具具有更長的刀具壽命。考慮到絲攻的孔數,TiAlN的使用使刀具壽命增加了1.35倍。薄膜增加了刀具的表面硬度,降低了摩擦係數,並在加工過程中保護切削刃免受高溫影響。刀具的磨損行為和性能直接受到塗層的影響。研究不同塗層對這種行為的影響。合適的薄膜選擇很重要,但薄膜的塗覆方法和塗覆前後切削刃微觀幾何形狀的製備也非常重要。Denkena等研究了切削刃製備方法對硬質合金塗層刀片在硬加工時性能的影響。結合適當的刀具材料和塗層對切削刀具的磨損形成有重要影響。文中,Aslan採用不同的刀具對硬度為62 HRC的X210 Cr12冷作工具鋼進行端銑加工。Aslan研究了不同塗層的碳化鎢刀具、金屬陶瓷刀具、陶瓷刀具和CBN刀具的性能和磨損行為。
在硬質材料的加工過程中,必須考慮到硬質材料的特殊性能,採用合適的切削條件。切削條件應發揮切削刀具的潛力。由於切削刀具的發展,HSC技術也應用於模具用淬硬鋼的加工中。研究顯示,用塗層硬質合金刀具對淬硬鋼AISI H13進行高速面銑加工,採用不同的切削速度和銑削策略。研究CBN刀具和PVD塗層硬質合金刀具在低速和高速加工策略下對淬硬鋼的切削性能。研究人員觀察了上下銑削策略下的側面磨損情況。切削條件會影響材料的去除率和加工表面的質量。表面質量可能是一個不可忽視的重要要求。能夠達到高耐用性,但不能達到理想表面質量的切削刀具是不經濟的,也是沒有生產力的。研究顯示了一種設計用於AISI D3硬化鋼面銑的特殊硬質合金刀具及其對表面質量的影響。
本文比較了幾種整體硬質合金端銑刀在加工硬度為62±2 HRC的DIN X210Cr12淬火鋼時的耐用性。對於不同幾何形狀的刀具,採用了薄膜沉積或刀具材料的基體。主要目的是對所有切削刀具進行綜合比較,確定其耐用性。此項工作的成果將用於進一步研究和開發硬質加工用切削刀具。
2. 實驗
實驗的主要目的是測定四種硬質合金端銑刀的耐久性。實驗分為兩部分,在實驗的第一部分,檢測切削條件,並將其用於實驗的第二部分,即所有刀具的長期測試。在加工淬火鋼的過程中,每隔一段時間測量一次側面磨損,直到磨損達到臨界值。根據獲得的數值確定各刀具的耐用性。四把硬質合金端銑刀用於DIN X210Cr12淬硬鋼的側銑。所有切削刀具如圖1所示,並標有A、B、C、D.表1顯示了切削刀具的基本參數。所有刀具的直徑相同,但刀具D的切削刃數量較少,楔角不同。刀具D被定義為WOTEK切削刀具。切削刃與楔角的斷面如圖2所示。為了測量切削刃的幾何參數,採用了Alicona公司的IFM-G4測量裝置。
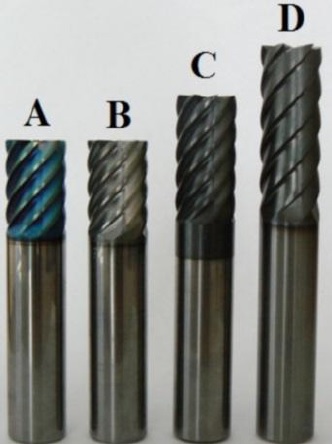
圖1. 銑削工具
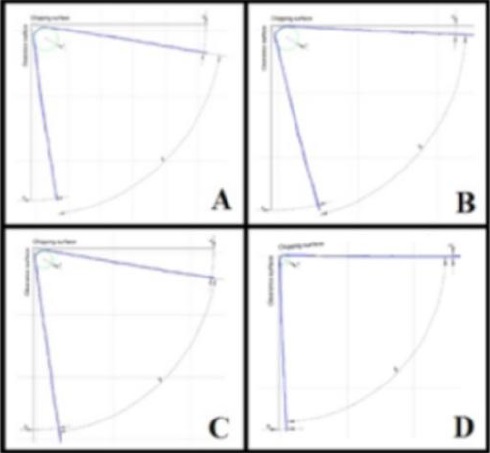
圖2. 切削邊緣的剖面圖
表1.切削刀具的基本參數

實驗採用淬火鋼DIN X210Cr12。尺寸為150x150x17mm的工件如圖4所示。每塊板的硬度為62±2 HRC。工件用夾具為KISTLER 9225 A測力計上(圖4),因為在實驗過程中還測量了切削力及其進度。側銑的策略如圖5所示。材料被加工過整個工件的厚度。切削刀具去除了所有加工材的側面。圖中還顯示了在切削刀具上的力的分量加工方向。
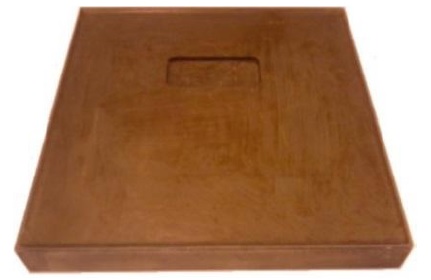
圖3. 工件
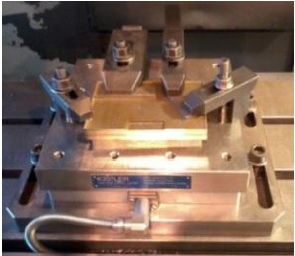
圖4. 夾持在測力計上的工件
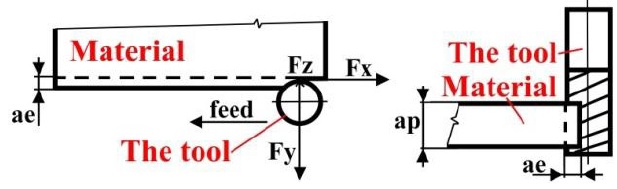
圖5. 加工策略
刀具每次加工過程中,都要去除工件一側的材料。"從去除材料和側面磨損的角度觀察,向下銑削比向上銑削更有利",因此採用爬(下)銑的策略。各刀具的切片厚度ae以及每齒進給量都是恆定的。切削深度ap等於工件的厚度。切削刀具夾在液壓刀架上,加工過程中不使用切削液,以避免熱衝擊。所有實驗加工均在MCV 750A立式數控中心上進行。
在實驗的第一部分,根據A.S.Kondratov的說法,採用短期試驗來確定15分鐘耐久性的最佳切削速度v15。對每一種工具進行了測試,所得的切削速度值如表2所示。刀具B的切削速度無法確定,因為在加工過程中切削刃被破壞。
表2. 15分鐘耐久性的切削速度

實驗的第二部分採用長時間切削試驗。所有的刀具A、B、C、D都在恆定的切削條件下進行試驗。切削速度根據第一部分實驗中得到的結果確定。所有切削參數如表3所示。加工策略與短時間切削試驗相同。
測試材料用各刀具以恆定的切削速度進行加工。在加工過程中,每隔一段時間測量一次側面的磨損量VBB。繼續加工,直到磨損達到臨界值VBkrit。對每個切削刀具獲得臨界值VBkrit=0.1mm的耐久性。還得到了總加工時間和長時間切削試驗期間的材料去除量。側面磨損是在三個切削刃上,距切削刀具表面恆定距離處測量的(圖6)。
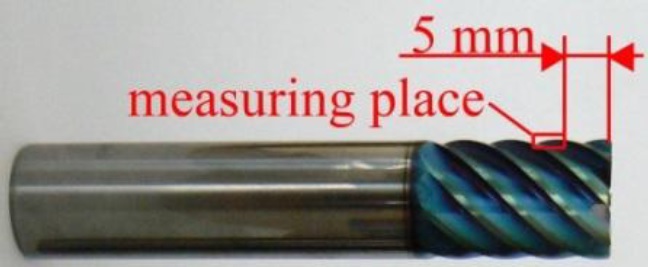
圖6. 測量位置,銑刀A
表3. 切削條件

刀具A如圖6所示。在加工過程中,大約每2分鐘測量一次側面磨損。測量時,使用Multicheck PC500光學顯微鏡。刀具A的側翼磨損值如表4所示。在加工過程中,刀具磨損均勻增加(圖7),但部分去除的切屑開始黏在銑刀的切削刃上。在最後一次TK時,銑刀的凹槽因黏附而被切屑堵塞。它造成了切削刃的開裂和銑刀的破壞。銑刀的最終狀態如圖9所示。槽口堵塞對工件表面的影響可見(圖10)。在銑刀的最後一次加工過程中,由於摩擦力大,產生了高熱量。未達到刃口磨損的臨界值。
測量切削力的進度,在最後一次通過時,切削力Fy的y分量增加到5000N以上。
表4. 銑刀A的側面磨損值
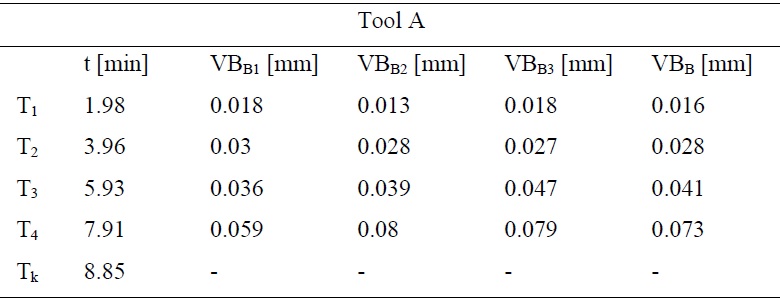
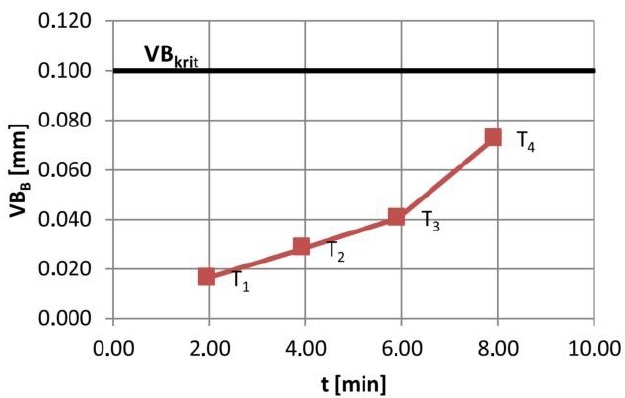
圖7. 側面磨損的進展,銑刀A
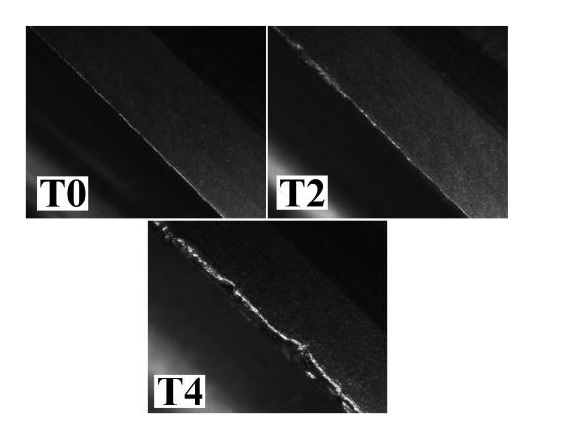
圖8. 刃口磨損
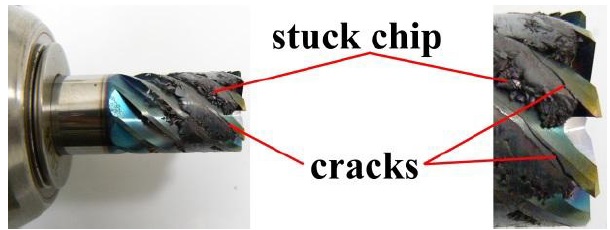
圖9. 銑刀A的最終狀態
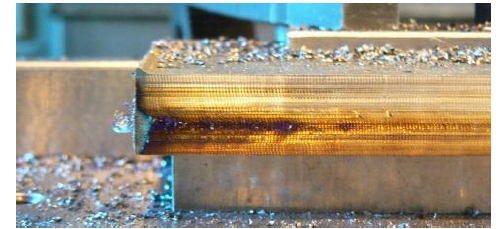
圖10. 最後一次加工後的工件表面
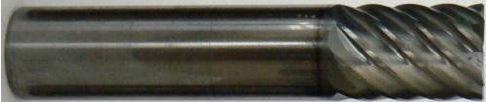
圖11. 銑刀B
端銑刀B如圖11所示。為了更深入檢視側翼磨損的狀況,測量間隔大約設定為1分鐘。端銑刀B的側翼磨損值如表5所示。側面磨損的臨界值是在切削第三分鐘後達到的。圖12顯示了端磨磨損隨時間的進展。大約在銑削第五分鐘時,側翼磨損達到VBB=0.15mm的值。在加工過程中,切屑黏附在切削刃上,它造成了端銑槽的堵塞。導致了切削刃的損壞(圖14)。圖13為測量間隔的切削刃側面磨損情況。
表5. 側面磨損值,端銑刀B
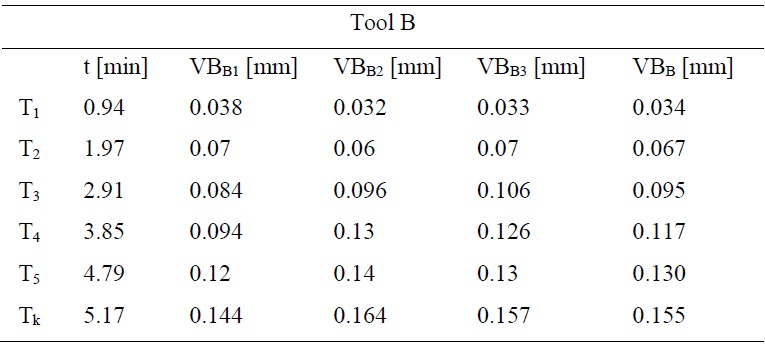
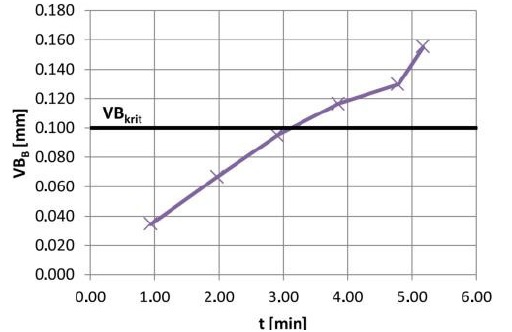
圖12. 側面磨損的狀況,端銑刀B
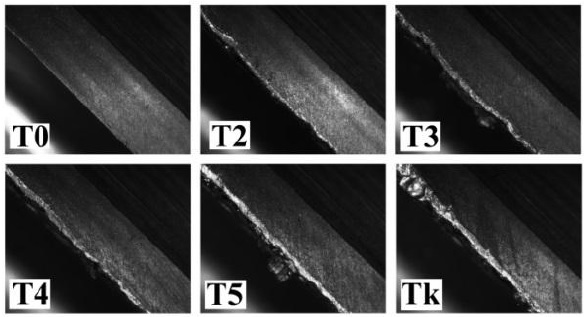
圖13. 刀刃上的側面磨損
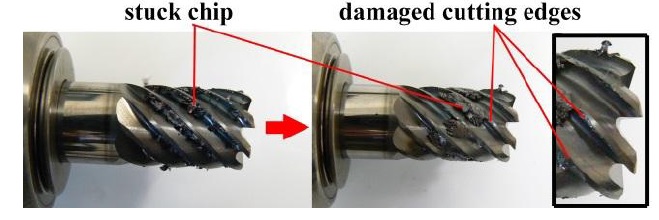
圖14. 端銑刀B的最終狀態
端銑刀C如圖15所示。在切削過程中,與端銑刀A一樣,大約每2分鐘測量一次側翼磨損,圖16顯示了隨著加工時間增加側翼磨損的狀況,測量得到的所有結果見表6。側面磨損的臨界值在時間t=27.6分鐘時達到。在加工的第4分鐘到第25分鐘之間,側翼磨損的進展幾乎是線性的。之後,側翼磨損急劇增加,切削刃被破壞。選定時間的側翼磨損情況如圖17所示。在端銑破壞之前,產生了一些堆積的刃口,出現了與以往切削刀具相同的粘屑效果(圖18)。在切削刃破壞之前,切削力的y分量迅速增加,達到4000N。

圖15. 端銑刀C
表6. 側面磨損值,端銑刀C
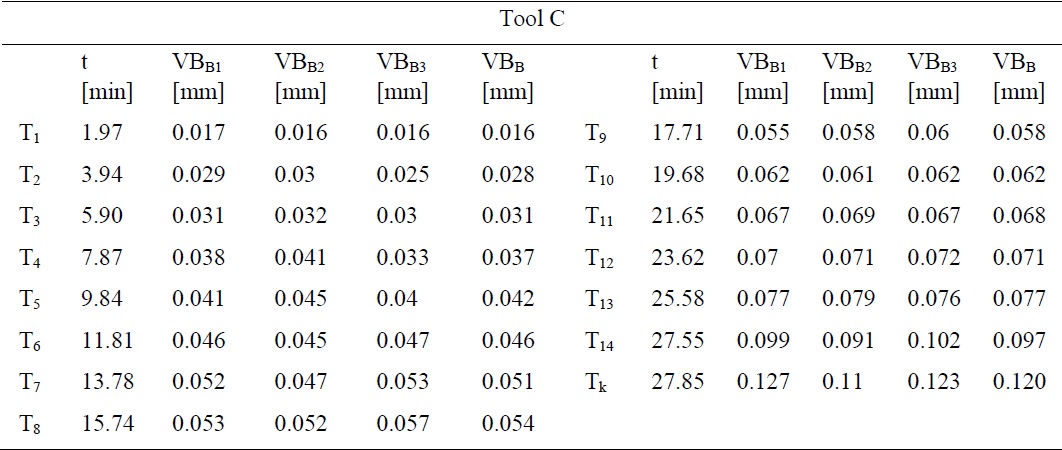
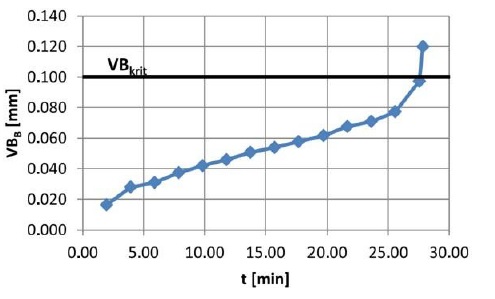
圖16. 側面磨損的進展,端銑刀C
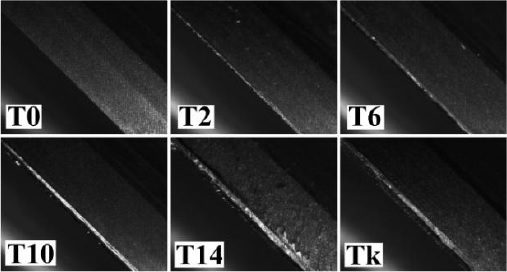
圖17. 刀刃上的側面磨損
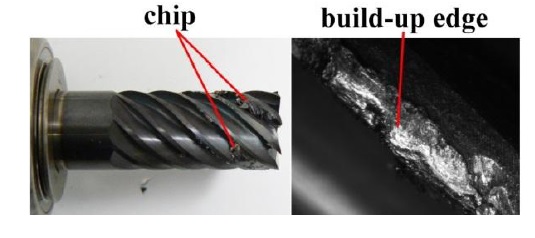
圖18. 端銑刀C的最後狀態
在時間t=43.47分鐘內達到磨損側翼的臨界值。所有切削刃上的磨損都均勻增加(圖20)。在加工過程中,在工件底部的立銑刀切削刃的所有側面都產生了切口磨損(圖22)。凹槽磨損大約在T20=37.8min時開始。在加工結束時,切口的尺寸達到了1.2mm。實驗加工結束前,側面的切口數值較大。

圖19. 端銑刀D
表7. 側面磨損值,端銑刀D
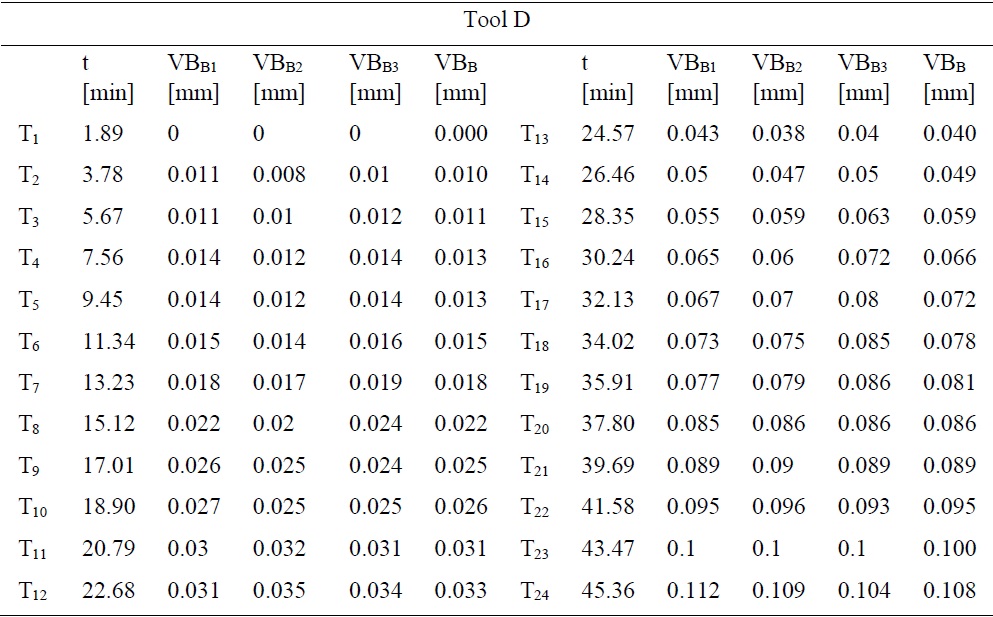
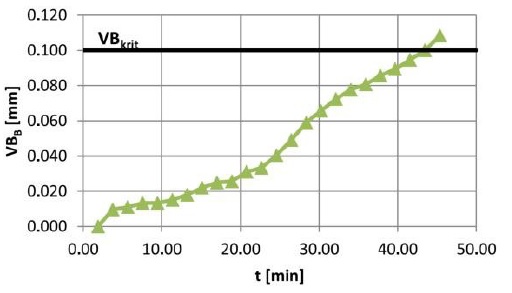
圖20. 銑刀側面磨損的進展情況,端銑刀D
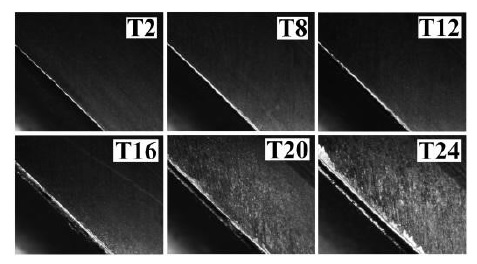
圖21. 刀刃上的側面磨損
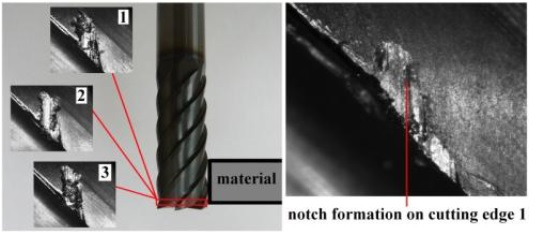
圖22. 端銑刀D上的凹槽形成
3. 結果摘要
在實驗的第一部分,使用了A.S.Kondratov所說的短時間加工試驗。該試驗的目的是確定每種試驗工具(A、B、C、D)15分鐘耐久性的最佳切削速度(v15)。結果如表8所示。 vbbmax是指短時試驗中刀具達到的最大側面磨損值。對於刀具B,由於加工過程中切削刃出現裂紋,故未確定切削速度v15。由此得出的切削條件,在實驗的第二部分中使用,如表所示。
表8. 短時間加工測試結果

表9. 切削條件

長時間加工試驗是在實驗的第二部分。對淬硬鋼DIN X210Cr12採用側銑策略,用各刀具進行加工。在加工過程中,在顯微鏡上測量側面磨損,直到達到臨界值。對於該值,確定了各刀具的耐久性T0.1。結果見表10。該表還顯示了每個刀具在加工過程中達到的最大側面磨損VBBmax和加工的總時間tfin。刀具A是唯一沒有達到側翼磨損臨界值的刀具。圖23顯示了各刀具的刀具磨損進度。很明顯,刀具D(WOTEK刀具)在所有刀具中達到了最高的耐用度,並且在加工43.5分鐘後達到了側翼磨損的臨界值。刀具D在加工過程中沒有裂紋形成,但在每個切削刃的相同位置都有缺口磨損。從主觀上看,WOTEK銑刀也達到最佳的的加工表面質量。在圖25中是刀具的切削刃在其有限加工時間內的情況。圖24為各刀具的Fy進度。
表10. 長時間加工試驗結果

結論
硬質材料和固體材料在機械工程行業中經常被使用,例如在切削工具、成型工具或模具的生產中。如果我們想高效、有競爭力地加工這些材料,就必須不斷降低加工成本,提高加工質量。本文根據DIN X210Cr12淬火鋼加工過程中的耐用性對四種不同的銑刀進行了比較。最大的問題是加工過程中材料黏在刀具的切削刃上。這個問題發生在刀具A、B和C上,導致了切削刃的破壞。對於刀具A和B,在銑削過程中,凹槽被堵塞。刀具B的耐久性在所有刀具中最低。雖然刀具B在損壞前達到了較高的刃口磨損值,但與刀具C和D相比,加工時間非常短。在測試期間,測量了切削力。切削力的主要分量是y分量Fy,它隨著加工時間的增加而增加。在加工過程中,切削力的其他分量幾乎保持不變,沒有超過600 N。
銑刀D(WOTEK銑刀)獲得了最高的耐久性。塗層及相關工藝對良好的結果影響最大。適當的切削刃製備(微觀幾何形狀)和適當的硬質合金基體選擇,使薄膜和硬質合金基體具有良好的一致性,沒有任何缺陷。該項加工的成果將用於進一步研究和開發硬質合金加工用切削刀具。
致謝
本文基於SGS-2013-031項目贊助的工作。