Research progress on methods to improve machining ability of difficult materials
2020-04-27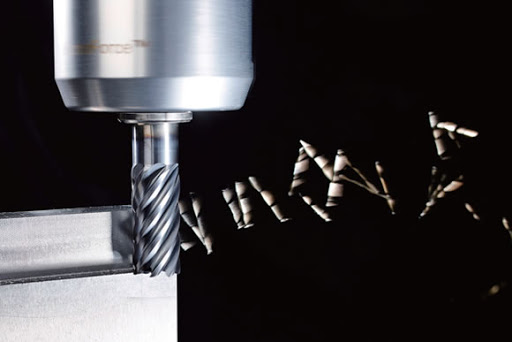
With the development of the aerospace and nuclear industries, difficult materials such as titanium alloys and high temperature alloys are being used more and more widely. Because high-temperature alloys have high temperature strength, good combination of oxidation resistance, heat corrosion resistance, fatigue resistance and fracture toughness, and can maintain good performance for a long time above 600 ℃, so this kind of material is widely used in aerospace, shipbuilding and chemical industry, etc. High-temperature alloy poor cutting performance is mainly manifested in: (1) high temperature strength, high cutting force; (2) low thermal conductivity, cutting temperature during processing up to 1000 ℃; (3) tool wear is serious, in the high temperature and high pressure, resulting in the bonding of the tool wear and diffuse wear.
The high specific strength, corrosion resistance and high temperature resistance of titanium alloy make it a material for aircraft engine parts. Titanium alloy is also a difficult material to work with, its high cutting temperature and small deformation coefficient make the tool susceptible to wear and tear. As a result, the cutting speed of machining titanium alloy is generally below 40m/min, which affects the efficiency of machining titanium alloy.
There are six methods of evaluating and analyzing the workability of materials by scholars at home and abroad.
The machinability of the material is evaluated according to a single indicator, such as the cutting speed, cutting force or cutting temperature, the surface quality of the workpiece after cutting, chip control or chip breakage, which can be achieved under the tool life or tool life.
The workability of other materials is evaluated based on the medium carbon steel 45 steel in the normal state.
Using material properties such as hardness, tensile strength, elongation and thermal conductivity as factors affecting the workability of the material
The main performance indicators of workability are based on their effect on workability, and then the material's workability is evaluated by a fuzzy composite evaluation method.
(the physical and mechanical properties of the workpiece material, the geometric parameters of the tool material and tool, etc.) affect the impact parameters (tool wear, the size of the cutting force, surface accuracy and dimensional accuracy after machining) on the evaluation of the machinability of the material.
A method based on cutting force and surface roughness using weighting factors to evaluate the machinability of steel parts.
Five key physical-mechanical property indicators that affect the machinability of difficult materials were identified, namely hardness, ductility, process hardening, thermal conductivity and abrasion resistance.
WOTEK uses high-pressure cooling technology where coolant is sprayed directly into the cutting edge area to reduce the temperature of the cutting area, making it easier to roll the chips, thus achieving chip control. At the same cutting speed, the metal removal increases by 50%; if the cutting speed increases by 20%, the metal removal increases by 20% at the same time. For the cutting of difficult materials such as titanium alloys, the high cutting heat, high cutting temperature and concentration near the cutting edge make it easy to form crescent-shaped wear when machining with ordinary cutting fluid. When cutting titanium alloy, a high-pressure internal cooling tool is used, and the coolant is injected into the cutting area under high pressure, which directly cools the tip of the cutting point, lowering the temperature of the cutting edge and reducing tool wear, while the high-pressure fluid breaks the chips and drains them away in time. Moreover, the coolant can also play a lubricating role, reducing the friction between the tool and the workpiece, so that the cutting force is reduced, using this method can improve the tool life, reduce the tool cost, and good chip breaking and chip removal effect can improve the machining quality of the parts.
Minimal Quantity Lubrication (MQL) is a more widely used method of quasi-dry cutting, in which a small amount of harmless oil mist is mixed in compressed air to cool, lubricate and evacuate the cutting area instead of a large amount of oil agent. Research shows that MQL technology can effectively reduce the frictional resistance between tool, chip and tool, and machining surface, reduce the maximum cutting temperature, reduce tool wear, and improve the quality of machining surface.WOTEK targets high-speed milling of titanium alloy TC4, and the analysis of high-speed milling force and tool wear characteristics shows that the use of low-temperature nitrogen and trace lubricants can effectively suppress the temperature rise in the machining area, reduce cutting force, extend the service life of the tool and improve machining surface accuracy. WOTEK used an aerosol microlubrication-assisted PCD tool to cut titanium alloy and improve the cutting process of titanium alloy. Aerosol microlubrication assisted PCD tool cutting titanium alloy device is shown in Figure 1.
Heat-assisted cutting is a method of machining a workpiece by heating the whole or part of the workpiece to a certain temperature through a plasma or laser heating source. Local heating of the cutting area by plasma heating sources, such as Inconel 718, showed a significant reduction in yield strength above 750°C. Leshock et al. showed that cutting Inconel 718 by ion-heated cutting method (Plasma Enhanced Machinig, PEM) showed a significant reduction in cutting force with increasing surface temperature and an improvement in surface quality of the workpiece after machining. However, when the temperature exceeds 530°C, oxidation occurs on the surface of the workpiece, which can be avoided by precisely controlling the heating source.
Lopez de Lacalle LN plasma studied plasma arc-assisted milling of three difficult materials (Inconel 718, Haynes 25 and Ti6Al4V), which resulted in a significant reduction in cutting forces and an increase in tool life and surface quality when machining Inconel 718 and Haynes 25; however, machining Ti6Al4V was not suitable for titanium alloy due to heating altering the microstructure of the material, which instead resulted in a reduction in tool life and brittle material surface. Among them, Laser Assisted Machining (LAM) technology focuses a high-powered laser beam on the surface of the workpiece in front of the cutting edge, which locally heats the workpiece to a very high temperature for a short period of time, softening the metal material and reducing its yield strength, thereby reducing chip deformation, reducing cutting force and reducing tool wear, achieving the goal of improving the quality of the machining surface and machining efficiency.
To study the effect of laser beam on chip formation during Ti6Al4V alloy machining, a physical model was used to analyze the mechanism of continuous chip formation during LAM high-speed cutting. Rashid et al. studied the characteristics of LAM machining β titanium alloy Ti-6Cr5Mo-5V-4Al, which resulted in reduced material yield strength, reduced cutting force and improved metal removal due to laser irradiation of workpiece surface heating. Rashid et al. studied LAM to improve the cutting machinability of difficult material Ti-10V-2Fe-3A. Attia et al. used laser-assisted high-speed finishing high-temperature alloy Inconel 718 under dry mode to improve the material removal rate up to 8 times that of conventional turning, and improved tool life and surface finish quality. Wang Yan researched K24, a high-temperature alloy for laser heating-assisted milling, and obtained the laws of influence of process parameters on cutting force, tool life and surface quality.
One method of liquid nitrogen cooling is to spray liquid nitrogen as a cutting fluid directly into the cutting zone (see Figure 2). The method uses liquid nitrogen (minimum temperature up to -186°C), liquid carbon dioxide (minimum temperature up to -76°C) and other low-temperature liquids as cutting fluids that are injected into the machining area to lubricate the machining area between the tool and the workpiece. Both the cutting area can be cooled and the lubricant can be used to form a lubricant film on the surface of the tool, thereby increasing the life of the tool. This cooling cutting ability is stronger than high-pressure jet cooling and can significantly reduce tool wear caused by high temperature when cutting difficult materials such as titanium alloys and high temperature alloys. TiAlN coated carbide tool turning Inconel 718, tip wear was cooled by low temperature oil mist and the surface quality of the machined surface was significantly improved relative to both cold air and dry cutting.
In order to improve the cutting efficiency of difficult aerospace materials, five measures can be used: selection of tool material, selection of reasonable tool geometry parameters, optimization of cutting amount, selection of machining method and new tool design.
Because Co material has good thermal stability and can maintain high hardness at high temperature, such as cobalt HSS at cutting temperature 645~650℃, its hardness is 67~70HRC, which can be used to process high temperature alloy, titanium alloy, austenitic heat resistant steel and other difficult to process alloy. The hardness of cobalt-containing high speed steel (W2Mo9Cr4Co8(M42)) is 69~70HRC, which is suitable for processing iron-based high temperature alloys, casting high temperature alloys, titanium alloys and ultra-high strength steel and other difficult materials.
WC-Co hard alloys with carbide grain size below 0.5μm are 90~93HRA with bending strength of 2000~3500MPa, such as YS2 (K30), which is suitable for processing iron-based, nickel-based high-temperature alloys and titanium alloys. For TiAlN-coated carbide tools with PVD process, the coated surface generates a high strength amorphous alumina film (Al2O3) with high hardness, high oxidation temperature, good red hardness, strong adhesion, low friction and low thermal conductivity. The tool is suitable for higher cutting speeds, while lower cutting speeds are prone to the formation of phyllodes, which can lead to micro chipping and groove wear. Ceramics such as Si3N4, alumina-based ceramics have high temperature performance (Al2O3 melting point is 2050 ℃), high hardness and wear resistance (91~95 HRA), can process nickel-based or cobalt-based heat-resistant alloys, such as processing Inconel 718 (GH169), the cutting parameters V c=200m/min, fz=0.2mm/z, while the hardness alloy processing when the cutting parameters
Vc=30m/min, fz=0.3mm/z. Cubic boron nitride CBN has high hardness, abrasion resistance, thermal stability (1400~1500 ℃ is twice as high as diamond; 800 ℃ is ceramic and hard alloy ambient temperature performance), excellent chemical stability and oxidation resistance (1000 ℃ will produce a boron oxide B2O3 film to prevent further oxidation), good thermal conductivity, low friction coefficient (0.1~0.3).The higher the content of CBN, the higher the hardness, suitable for processing heat-resistant steel, high hard steel; low content is suitable for processing general hard steel and impact cutting. CBN grain size is small, good abrasion resistance (21μm to 13μm, tool life can be increased by 28%). The CBN tool adopts negative front angle (-6°~-18°), and the front angle (0°~8°) should be positive, and the back angle can be larger (6°~25°) for nickel-based alloy.
Diamond (single crystal) has a sharp edge, high thermal conductivity, less heat retention at the tip, very high hardness and abrasion resistance, very low coefficient of friction, etc. Diamond (carbon) is much less soluble in titanium than in iron, so its diffuse wear is small. Carbide (K type) machining Ti6Al4V, V c=20~50m/min; machining natural diamond Vc=100~120m/min, cutting time 30min, almost no tool wear; using wet method to cut Vc=200m/min, the tools almost no wear.
Generally speaking, positive front angle (γ) inserts reduce cutting force, cutting heat, machining hardening, etc., but the strength is reduced; large back angle α (6°~10°) reduces tool and workpiece friction, sharpness, cutting force, cutting heat, heat dissipation, etc.; main offset angle kr (45°~90°) increases tool heat dissipation, reduces cutting force, chip thickness and width, etc.; edge inclination angle λs (0°~20°) affects chip flow, increases tip strength, etc.; tip rε is smaller, but tip strength should be considered. When casting high-temperature alloys with ceramic tools γ=0°~3°, α=10°~15°; deformed high-temperature alloys α=0°~10°, α=10°~15°; cubic boron nitride and diamond tools: deformed high-temperature alloys γ=0°~8°, α=8°~20°; about the tool coating application for cutting high-temperature alloy materials, of which CVD coating is suitable for roughing, PVD for semi-finishing and finishing, and PVD for finishing.
When cutting high-temperature alloys, the cutting speed should not be too high, because high-temperature alloys have high strength and viscosity, it is easier to generate and accumulate heat in the cutting area during cutting, and the thermal conductivity is poor. As far as the current tools are concerned, the cutting speed of titanium alloy is generally between 30~80m/min and that of nickel-based alloy is also within 250m/min.
Choosing a reasonable cutting speed requires consideration: a high cutting speed can avoid the material's pockets of neoplasm; increasing the cutting speed can increase the temperature, either by reducing the cutting speed to achieve low temperatures or by using cooling. Table 1 shows the selection of cutting speed for machining high temperature alloy, titanium alloy for different tool materials.
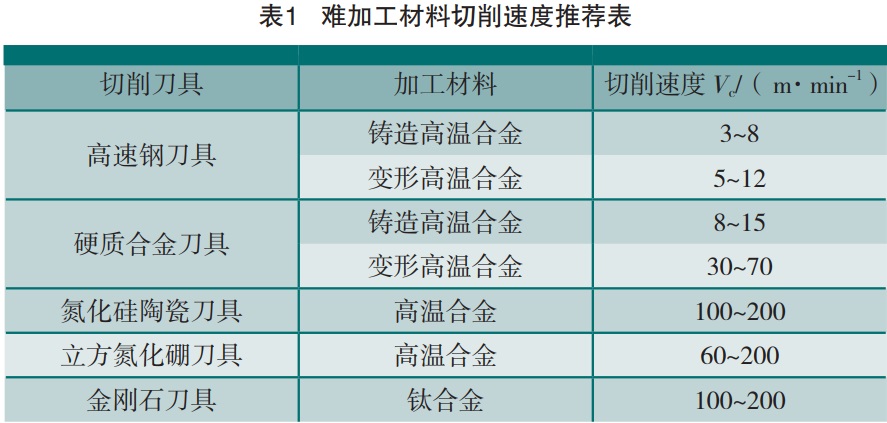
High-temperature alloys have a high cutting temperature and also have the problem of machining hardening. If the feed per tooth is too high, the cutting force is too high and the cutting temperature is too high and the tool is burned; if the feed per tooth is too small, the tool will wear out quickly because the cutting edge is always working in the hardening layer. Generally speaking, the cutting parameters are taken as fz=0.1~0.5mm/z per tooth feed, and small values are taken when the rigidity of the process system is not good during finishing and milling processing, and large values are taken when the rigidity of the process system is good during rough machining. Take machining Inconel 718 (GH169) as an example: cutting parameters with carbide tools: V c=25m/min, ap=3.4mm, fz=0.23mm/z; cutting parameters with silicon nitride ceramic tools: V c=172m/min, ap=10mm, fz=0.18mm/z.
In the case of high-temperature alloys, the backmilling chips are thin to thick, and the tool is prone to dry friction with the workpiece during the initial cut, which aggravates the sticky and chipped edge of the tool, therefore, as far as possible, the use of backmilling machining, i.e., the tooth of the tool touches the hard skin at the beginning of the cut, which can easily cause the tool to break. For turbine blade machining, efficient milling and insertion techniques are used, i.e., milling and insertion of turbine blades on 3- or 4-axis dedicated milling machines: a downward motion of the insertion and milling cutter from the top of the turbine blade, directly to its root, and complex curved surfaces can be machined by a CNC-controlled plane motion in the X-Y plane.
WOTEK tooling company has developed a stand milling cutter for roughing nickel-based alloy with a 20º spiral angle, 4~6 cutter slots, 6~20mm diameter and smooth chip removal (see Figure 3). Tool manufacturers provide actionable machining solutions for typical part machining [20]. For example, WOTEK's rotary parts such as turbines made of high-temperature alloys of difficult materials, which have a variety of cavities, require that the design, selection of tools and the planning of toolpaths take into account a reasonable clearance between the tool and the workpiece to avoid interference.
WOTEK curved inserts have a unique structure and are difficult to process efficiently.
Work the groove. The blade controls the chips to ensure
Surface integrity meets requirements.
It enables low axial cutting forces and improves tool life for high temperature alloy drilling.
This paper describes methods for machining titanium and high-temperature alloys of difficult aerospace materials; it also discusses methods to improve the cutting efficiency of difficult materials in terms of preferential tool materials, selection of suitable tool geometry parameters, adoption of optimized machining process parameters, selection of suitable milling machining methods and design of new tools for difficult typical parts 5.
The high specific strength, corrosion resistance and high temperature resistance of titanium alloy make it a material for aircraft engine parts. Titanium alloy is also a difficult material to work with, its high cutting temperature and small deformation coefficient make the tool susceptible to wear and tear. As a result, the cutting speed of machining titanium alloy is generally below 40m/min, which affects the efficiency of machining titanium alloy.
Method of analyzing the machining ability of materials
There are six methods of evaluating and analyzing the workability of materials by scholars at home and abroad.
(1) Single Indicator Assessment Methodology.
The machinability of the material is evaluated according to a single indicator, such as the cutting speed, cutting force or cutting temperature, the surface quality of the workpiece after cutting, chip control or chip breakage, which can be achieved under the tool life or tool life.
(2) Relative processing methods.
The workability of other materials is evaluated based on the medium carbon steel 45 steel in the normal state.
(3) Fuzzy composite assessment method.
Using material properties such as hardness, tensile strength, elongation and thermal conductivity as factors affecting the workability of the materialThe main performance indicators of workability are based on their effect on workability, and then the material's workability is evaluated by a fuzzy composite evaluation method.
(4) Material and process parameters using the cutting process
(the physical and mechanical properties of the workpiece material, the geometric parameters of the tool material and tool, etc.) affect the impact parameters (tool wear, the size of the cutting force, surface accuracy and dimensional accuracy after machining) on the evaluation of the machinability of the material.
(5) Evaluate the machinability of the material by the output parameters of the cutting process
A method based on cutting force and surface roughness using weighting factors to evaluate the machinability of steel parts.
(6) Using the phase diagram method
Five key physical-mechanical property indicators that affect the machinability of difficult materials were identified, namely hardness, ductility, process hardening, thermal conductivity and abrasion resistance.
Machining methods for difficult materials
1 High-pressure spray cooling process
WOTEK uses high-pressure cooling technology where coolant is sprayed directly into the cutting edge area to reduce the temperature of the cutting area, making it easier to roll the chips, thus achieving chip control. At the same cutting speed, the metal removal increases by 50%; if the cutting speed increases by 20%, the metal removal increases by 20% at the same time. For the cutting of difficult materials such as titanium alloys, the high cutting heat, high cutting temperature and concentration near the cutting edge make it easy to form crescent-shaped wear when machining with ordinary cutting fluid. When cutting titanium alloy, a high-pressure internal cooling tool is used, and the coolant is injected into the cutting area under high pressure, which directly cools the tip of the cutting point, lowering the temperature of the cutting edge and reducing tool wear, while the high-pressure fluid breaks the chips and drains them away in time. Moreover, the coolant can also play a lubricating role, reducing the friction between the tool and the workpiece, so that the cutting force is reduced, using this method can improve the tool life, reduce the tool cost, and good chip breaking and chip removal effect can improve the machining quality of the parts.
2 Micronutrient lubrication cutting
Minimal Quantity Lubrication (MQL) is a more widely used method of quasi-dry cutting, in which a small amount of harmless oil mist is mixed in compressed air to cool, lubricate and evacuate the cutting area instead of a large amount of oil agent. Research shows that MQL technology can effectively reduce the frictional resistance between tool, chip and tool, and machining surface, reduce the maximum cutting temperature, reduce tool wear, and improve the quality of machining surface.WOTEK targets high-speed milling of titanium alloy TC4, and the analysis of high-speed milling force and tool wear characteristics shows that the use of low-temperature nitrogen and trace lubricants can effectively suppress the temperature rise in the machining area, reduce cutting force, extend the service life of the tool and improve machining surface accuracy. WOTEK used an aerosol microlubrication-assisted PCD tool to cut titanium alloy and improve the cutting process of titanium alloy. Aerosol microlubrication assisted PCD tool cutting titanium alloy device is shown in Figure 1.
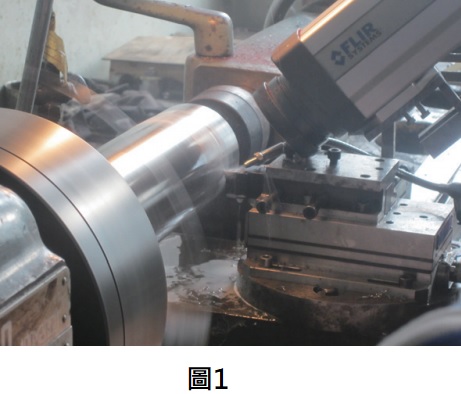
3 Heat-assisted cutting
Heat-assisted cutting is a method of machining a workpiece by heating the whole or part of the workpiece to a certain temperature through a plasma or laser heating source. Local heating of the cutting area by plasma heating sources, such as Inconel 718, showed a significant reduction in yield strength above 750°C. Leshock et al. showed that cutting Inconel 718 by ion-heated cutting method (Plasma Enhanced Machinig, PEM) showed a significant reduction in cutting force with increasing surface temperature and an improvement in surface quality of the workpiece after machining. However, when the temperature exceeds 530°C, oxidation occurs on the surface of the workpiece, which can be avoided by precisely controlling the heating source.Lopez de Lacalle LN plasma studied plasma arc-assisted milling of three difficult materials (Inconel 718, Haynes 25 and Ti6Al4V), which resulted in a significant reduction in cutting forces and an increase in tool life and surface quality when machining Inconel 718 and Haynes 25; however, machining Ti6Al4V was not suitable for titanium alloy due to heating altering the microstructure of the material, which instead resulted in a reduction in tool life and brittle material surface. Among them, Laser Assisted Machining (LAM) technology focuses a high-powered laser beam on the surface of the workpiece in front of the cutting edge, which locally heats the workpiece to a very high temperature for a short period of time, softening the metal material and reducing its yield strength, thereby reducing chip deformation, reducing cutting force and reducing tool wear, achieving the goal of improving the quality of the machining surface and machining efficiency.
To study the effect of laser beam on chip formation during Ti6Al4V alloy machining, a physical model was used to analyze the mechanism of continuous chip formation during LAM high-speed cutting. Rashid et al. studied the characteristics of LAM machining β titanium alloy Ti-6Cr5Mo-5V-4Al, which resulted in reduced material yield strength, reduced cutting force and improved metal removal due to laser irradiation of workpiece surface heating. Rashid et al. studied LAM to improve the cutting machinability of difficult material Ti-10V-2Fe-3A. Attia et al. used laser-assisted high-speed finishing high-temperature alloy Inconel 718 under dry mode to improve the material removal rate up to 8 times that of conventional turning, and improved tool life and surface finish quality. Wang Yan researched K24, a high-temperature alloy for laser heating-assisted milling, and obtained the laws of influence of process parameters on cutting force, tool life and surface quality.
4 Low temperature cooling-assisted cutting
One method of liquid nitrogen cooling is to spray liquid nitrogen as a cutting fluid directly into the cutting zone (see Figure 2). The method uses liquid nitrogen (minimum temperature up to -186°C), liquid carbon dioxide (minimum temperature up to -76°C) and other low-temperature liquids as cutting fluids that are injected into the machining area to lubricate the machining area between the tool and the workpiece. Both the cutting area can be cooled and the lubricant can be used to form a lubricant film on the surface of the tool, thereby increasing the life of the tool. This cooling cutting ability is stronger than high-pressure jet cooling and can significantly reduce tool wear caused by high temperature when cutting difficult materials such as titanium alloys and high temperature alloys. TiAlN coated carbide tool turning Inconel 718, tip wear was cooled by low temperature oil mist and the surface quality of the machined surface was significantly improved relative to both cold air and dry cutting.
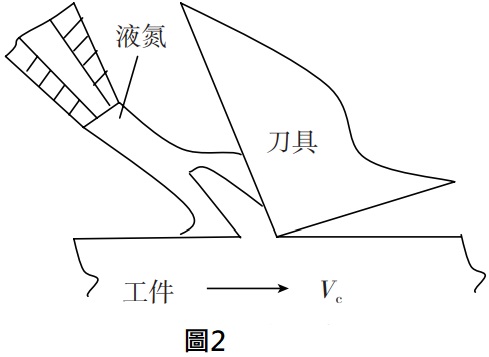
Ways to improve the cutting efficiency of difficult materials
In order to improve the cutting efficiency of difficult aerospace materials, five measures can be used: selection of tool material, selection of reasonable tool geometry parameters, optimization of cutting amount, selection of machining method and new tool design.
1 Choice of tool material
Because Co material has good thermal stability and can maintain high hardness at high temperature, such as cobalt HSS at cutting temperature 645~650℃, its hardness is 67~70HRC, which can be used to process high temperature alloy, titanium alloy, austenitic heat resistant steel and other difficult to process alloy. The hardness of cobalt-containing high speed steel (W2Mo9Cr4Co8(M42)) is 69~70HRC, which is suitable for processing iron-based high temperature alloys, casting high temperature alloys, titanium alloys and ultra-high strength steel and other difficult materials.WC-Co hard alloys with carbide grain size below 0.5μm are 90~93HRA with bending strength of 2000~3500MPa, such as YS2 (K30), which is suitable for processing iron-based, nickel-based high-temperature alloys and titanium alloys. For TiAlN-coated carbide tools with PVD process, the coated surface generates a high strength amorphous alumina film (Al2O3) with high hardness, high oxidation temperature, good red hardness, strong adhesion, low friction and low thermal conductivity. The tool is suitable for higher cutting speeds, while lower cutting speeds are prone to the formation of phyllodes, which can lead to micro chipping and groove wear. Ceramics such as Si3N4, alumina-based ceramics have high temperature performance (Al2O3 melting point is 2050 ℃), high hardness and wear resistance (91~95 HRA), can process nickel-based or cobalt-based heat-resistant alloys, such as processing Inconel 718 (GH169), the cutting parameters V c=200m/min, fz=0.2mm/z, while the hardness alloy processing when the cutting parameters
Vc=30m/min, fz=0.3mm/z. Cubic boron nitride CBN has high hardness, abrasion resistance, thermal stability (1400~1500 ℃ is twice as high as diamond; 800 ℃ is ceramic and hard alloy ambient temperature performance), excellent chemical stability and oxidation resistance (1000 ℃ will produce a boron oxide B2O3 film to prevent further oxidation), good thermal conductivity, low friction coefficient (0.1~0.3).The higher the content of CBN, the higher the hardness, suitable for processing heat-resistant steel, high hard steel; low content is suitable for processing general hard steel and impact cutting. CBN grain size is small, good abrasion resistance (21μm to 13μm, tool life can be increased by 28%). The CBN tool adopts negative front angle (-6°~-18°), and the front angle (0°~8°) should be positive, and the back angle can be larger (6°~25°) for nickel-based alloy.
Diamond (single crystal) has a sharp edge, high thermal conductivity, less heat retention at the tip, very high hardness and abrasion resistance, very low coefficient of friction, etc. Diamond (carbon) is much less soluble in titanium than in iron, so its diffuse wear is small. Carbide (K type) machining Ti6Al4V, V c=20~50m/min; machining natural diamond Vc=100~120m/min, cutting time 30min, almost no tool wear; using wet method to cut Vc=200m/min, the tools almost no wear.
2 Reasonable selection of tool geometry parameters
Generally speaking, positive front angle (γ) inserts reduce cutting force, cutting heat, machining hardening, etc., but the strength is reduced; large back angle α (6°~10°) reduces tool and workpiece friction, sharpness, cutting force, cutting heat, heat dissipation, etc.; main offset angle kr (45°~90°) increases tool heat dissipation, reduces cutting force, chip thickness and width, etc.; edge inclination angle λs (0°~20°) affects chip flow, increases tip strength, etc.; tip rε is smaller, but tip strength should be considered. When casting high-temperature alloys with ceramic tools γ=0°~3°, α=10°~15°; deformed high-temperature alloys α=0°~10°, α=10°~15°; cubic boron nitride and diamond tools: deformed high-temperature alloys γ=0°~8°, α=8°~20°; about the tool coating application for cutting high-temperature alloy materials, of which CVD coating is suitable for roughing, PVD for semi-finishing and finishing, and PVD for finishing.
3 Preferred cutting amount
When cutting high-temperature alloys, the cutting speed should not be too high, because high-temperature alloys have high strength and viscosity, it is easier to generate and accumulate heat in the cutting area during cutting, and the thermal conductivity is poor. As far as the current tools are concerned, the cutting speed of titanium alloy is generally between 30~80m/min and that of nickel-based alloy is also within 250m/min.Choosing a reasonable cutting speed requires consideration: a high cutting speed can avoid the material's pockets of neoplasm; increasing the cutting speed can increase the temperature, either by reducing the cutting speed to achieve low temperatures or by using cooling. Table 1 shows the selection of cutting speed for machining high temperature alloy, titanium alloy for different tool materials.
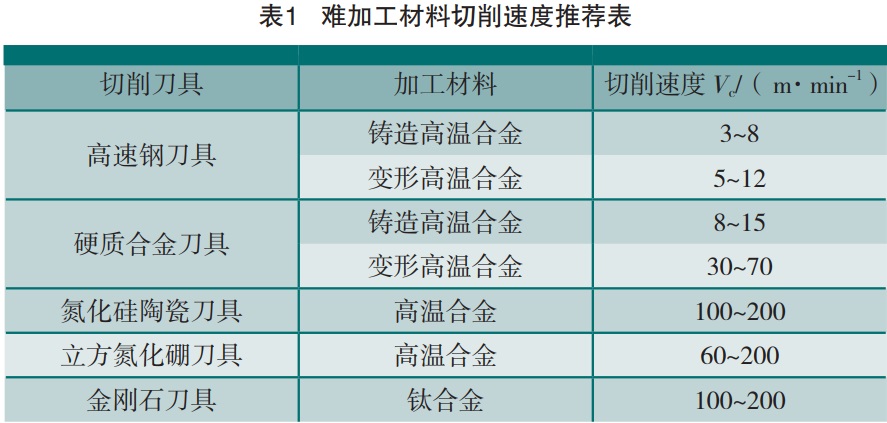
High-temperature alloys have a high cutting temperature and also have the problem of machining hardening. If the feed per tooth is too high, the cutting force is too high and the cutting temperature is too high and the tool is burned; if the feed per tooth is too small, the tool will wear out quickly because the cutting edge is always working in the hardening layer. Generally speaking, the cutting parameters are taken as fz=0.1~0.5mm/z per tooth feed, and small values are taken when the rigidity of the process system is not good during finishing and milling processing, and large values are taken when the rigidity of the process system is good during rough machining. Take machining Inconel 718 (GH169) as an example: cutting parameters with carbide tools: V c=25m/min, ap=3.4mm, fz=0.23mm/z; cutting parameters with silicon nitride ceramic tools: V c=172m/min, ap=10mm, fz=0.18mm/z.
4 Selection of machining method
In the case of high-temperature alloys, the backmilling chips are thin to thick, and the tool is prone to dry friction with the workpiece during the initial cut, which aggravates the sticky and chipped edge of the tool, therefore, as far as possible, the use of backmilling machining, i.e., the tooth of the tool touches the hard skin at the beginning of the cut, which can easily cause the tool to break. For turbine blade machining, efficient milling and insertion techniques are used, i.e., milling and insertion of turbine blades on 3- or 4-axis dedicated milling machines: a downward motion of the insertion and milling cutter from the top of the turbine blade, directly to its root, and complex curved surfaces can be machined by a CNC-controlled plane motion in the X-Y plane.
5 New tool design
WOTEK tooling company has developed a stand milling cutter for roughing nickel-based alloy with a 20º spiral angle, 4~6 cutter slots, 6~20mm diameter and smooth chip removal (see Figure 3). Tool manufacturers provide actionable machining solutions for typical part machining [20]. For example, WOTEK's rotary parts such as turbines made of high-temperature alloys of difficult materials, which have a variety of cavities, require that the design, selection of tools and the planning of toolpaths take into account a reasonable clearance between the tool and the workpiece to avoid interference.
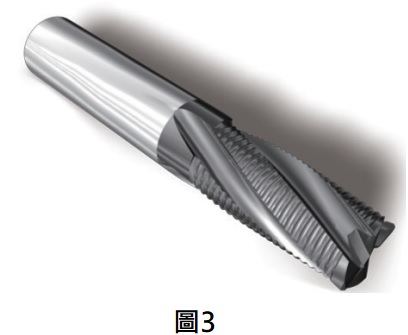
(1) Slotting curved inserts.
WOTEK curved inserts have a unique structure and are difficult to process efficiently.Work the groove. The blade controls the chips to ensure
Surface integrity meets requirements.
(2) Optimized tip and groove shape of WOTEK's overall carbide drill
It enables low axial cutting forces and improves tool life for high temperature alloy drilling.
Concluding Remarks
This paper describes methods for machining titanium and high-temperature alloys of difficult aerospace materials; it also discusses methods to improve the cutting efficiency of difficult materials in terms of preferential tool materials, selection of suitable tool geometry parameters, adoption of optimized machining process parameters, selection of suitable milling machining methods and design of new tools for difficult typical parts 5.