The Way of Machining: Precise Control of GRX-810 Alloy Milling
2024-03-29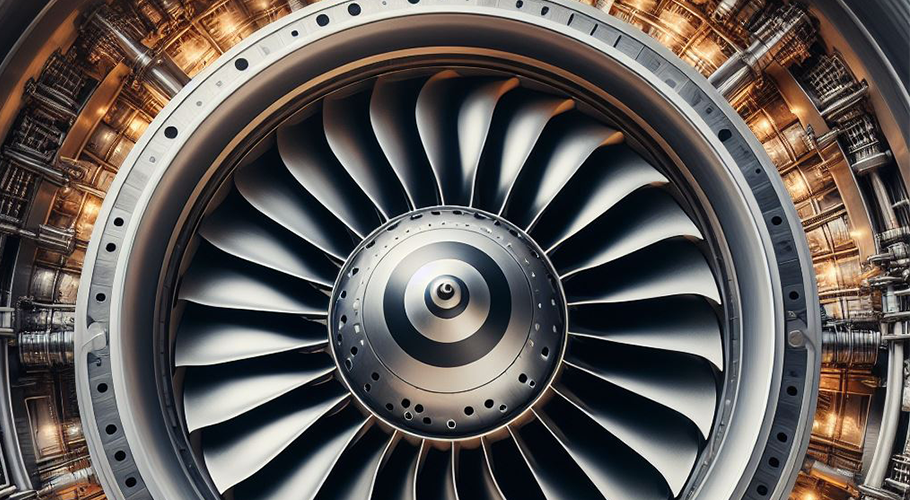
GRX-810 is a heat-resistant alloy mainly used in mechanical, aerospace, and other industries. The following are some of the main characteristics of the GRX-810 alloy:
- Excellent high-temperature strength: GRX-810 can maintain good strength even at high temperatures up to 1200°C, which is its most significant feature. This makes it highly suitable for manufacturing turbine disks for jet engines and other high-temperature components.
- Superior oxidation resistance: In high-temperature environments, GRX-810 can form a dense oxide protective film, giving it excellent resistance to oxidation and corrosion.
- Good hot workability: The GRX-810 alloy has good hot working properties such as forging and extrusion at high temperatures, which is advantageous for manufacturing complex-shaped components.
- Excellent sustained hardness: Even after long-term use at high temperatures, GRX-810 can still maintain relatively high hardness and excellent resistance to long-term tensile stresses.
- Good creep resistance: Creep is a common problem for high-temperature components, but GRX-810 can effectively resist creep deformation below 1000°C.
Overall, GRX-810 is an outstanding heat-resistant, high-temperature alloy material widely used in aerospace engines, rocket engines, nuclear power plants, and other fields. However, its processing cost is relatively high, which is a factor that needs to be considered.
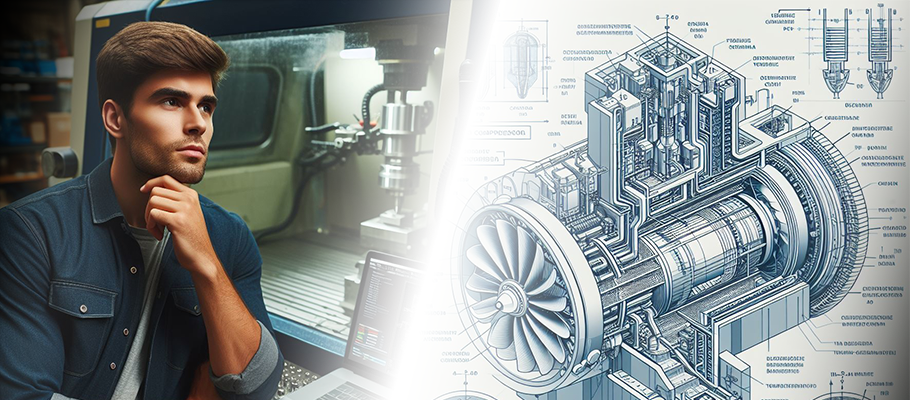
Key Points for Machining GRX-810 Heat-Resistant Alloy
As CNC machine tool technicians, we often encounter the task of machining highly challenging materials, among which the GRX-810 heat-resistant alloy is a formidable one. This alloy possesses outstanding high-temperature strength and oxidation resistance, widely used in the manufacturing of aircraft engines and other high-temperature components. However, its properties also present some difficulties for CNC machining, and we must strictly control the following points:
As CNC machine tool technicians, we often encounter the task of machining highly challenging materials, among which the GRX-810 heat-resistant alloy is a formidable one. This alloy possesses outstanding high-temperature strength and oxidation resistance, widely used in the manufacturing of aircraft engines and other high-temperature components. However, its properties also present some difficulties for CNC machining, and we must strictly control the following points:
- Select suitable tungsten carbide end mills: GRX-810 alloy is considered a difficult-to-machine material, requiring the use of high-hardness and high-toughness tungsten carbide end mills. We typically choose titanium aluminum nitride-coated tungsten carbide tools, as the coating can enhance wear resistance and lubricity. Appropriate helix angles and nose radii are also crucial, taking the material's hardness and cutting forces into full consideration.
- Adjust cutting parameters: When machining the GRX-810 alloy, we need to appropriately reduce the feed rate and spindle speed of the cutting tool to avoid overloading, which can lead to tool wear or flank wear. During each cut, the depth of cut should not be too deep, ideally controlled within 0.2-0.5 mm. Additionally, a moderate cutting volume must be selected, neither too large nor too small.
- Ensure proper tool cooling: The high hardness of GRX-810 generates a substantial amount of heat during the cutting process, which, if not promptly dissipated, will accelerate tool wear. Therefore, we must ensure adequate tool cooling, typically using water-soluble semi-synthetic cutting fluids for both cooling and lubrication. Reasonable pressure and flow rates should be set to allow the coolant to act directly on the cutting zone at the tool tip.
- Prevent thermal cracking: The GRX-810 alloy is prone to thermal cracking after machining due to sudden thermal stress changes. To address this, we need to adopt a controlled machining path strategy, such as initially opening small pilot holes and then gradually enlarging them during the roughing process. After completing the machining, the cooling rate of the workpiece should be appropriately slowed down to reduce thermal stress differences.
- Frequently inspect tool condition: The high hardness of the GRX-810 alloy presents a severe challenge to the cutting tools. During work breaks, we need to periodically inspect the tool wear condition and determine a reasonable tool change cycle based on the actual situation. Never wait until the tool is completely dull or damaged before stopping the machine and replacing it, as this will affect the workpiece quality and may potentially damage the machine table surface.
As CNC machine tool technicians, only by mastering these points can we efficiently and precisely complete the machining processes for the GRX-810 alloy and other difficult-to-machine materials. The accumulation of experience and the optimization of machining processes are crucial. We also hope that in the future, we can apply new machining techniques and tools to solve such challenging tasks.