The Dual Revolution of Precision Manufacturing: The Perfect Integration of Mars Exploration and CNC Machine Tools
2025-04-08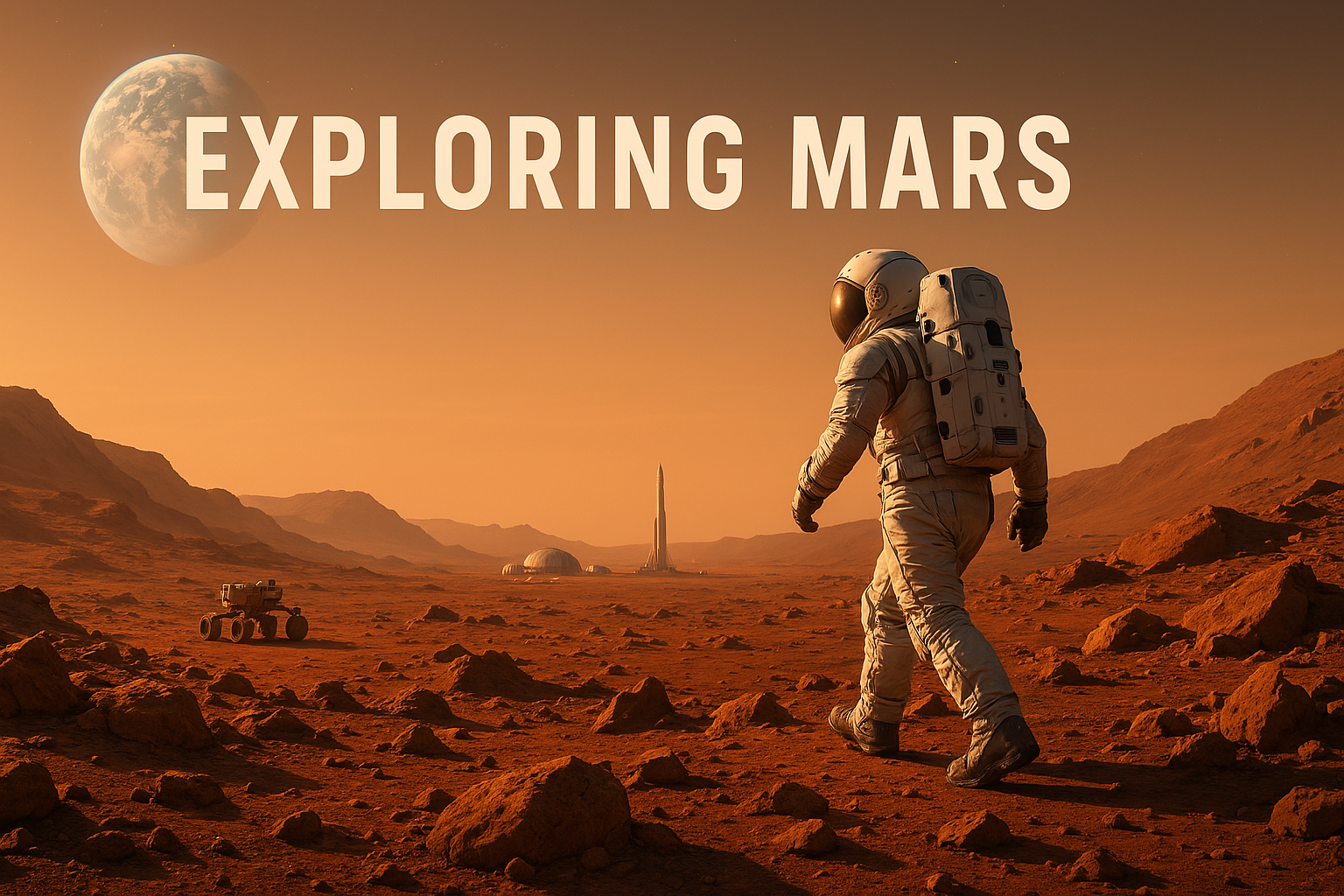
The Unsung Heroes Behind Mars Exploration: How CNC Machine Tools Are Shaping the Future of Space Technology
When we gaze at the stars and marvel at the high-definition images transmitted back by Mars rovers, few people think about a critical Earth-based technology behind these space miracles—CNC (Computer Numerical Control) machine tools. From Curiosity's precision gears to Perseverance's heat-resistant shell, from the lightweight structure of the Mars helicopter "Ingenuity" to future Mars base construction concepts, CNC machining technology plays an indispensable role in space exploration. This article will take you on a deep dive into the little-known tight connection between CNC machine tools and Mars missions, revealing how these metal-cutting specialists in ground factories have become the behind-the-scenes drivers of humanity's stride onto the Red Planet.
CNC Technology: The Precision Manufacturing Foundation of Space Exploration
CNC (Computer Numerical Control) machine tools are core equipment in modern manufacturing. They precisely control cutting tool paths and movements through computer programs, capable of machining metals, composite materials, and other raw materials into precision parts with complex shapes. This technology has continuously evolved since its emergence in the 1950s and has now become an indispensable production tool for the aerospace industry, playing a particularly crucial role in the manufacturing process of Mars exploration equipment.
The working principle of CNC machine tools is quite ingenious: engineers first use CAD (Computer-Aided Design) software such as AutoCAD, Fusion 360, or SolidWorks to design 3D models of parts, then use CAM (Computer-Aided Manufacturing) software to convert these designs into G-code—a command language that CNC machines can understand, including detailed parameters such as tool movement paths, cutting depth, feed rate, and more. Once these instructions are input into the CNC controller, the machine can automatically execute high-precision cutting operations to produce parts that meet strict space standards.
In Mars missions, the value of CNC technology is primarily reflected in three aspects:
-
Unparalleled Precision: Mars probe components often require micron-level (0.001mm) precision to ensure reliable operation in extreme environments. For example, even a slight deviation in the rover's gear system could cause the rover to lose mobility billions of kilometers away.
-
Realization of Complex Geometries: CNC machine tools can precisely create lightweight honeycomb structures, streamlined curved shells, and other shapes difficult to manufacture with traditional methods. This is crucial for reducing launch weight (each kilogram of payload costs tens of thousands of dollars).
-
Ability to Process Special Materials: Mars equipment requires special materials such as titanium alloys, nickel-based superalloys, and carbon fiber composites to withstand launch vibrations, space radiation, and extreme temperature variations on Mars. CNC machine tools equipped with specialized cutting tools can effectively process these difficult-to-cut materials.
Top global CNC manufacturers such as Japan's Yamazaki Mazak, Germany's DMG Mori, and Trumpf have made their advanced five-axis machining centers core equipment in the aerospace parts supply chain. These machines can cost hundreds of thousands of dollars but can produce critical space components worth millions of dollars, yielding an extremely high return on investment.
From Parts to Whole: Specific Applications of CNC in Mars Missions
Almost every critical component in Mars exploration missions is closely related to CNC machining technology. Let's delve into some of the most representative application examples to understand how these ground-manufactured marvels have become the cornerstones of space exploration.
The mobility system of Mars rovers is a perfect demonstration of CNC precision machining. Taking NASA's Perseverance rover as an example, each aluminum alloy hub of its six-wheel independent suspension system requires dozens of hours of precision cutting on a five-axis CNC mill. These hubs not only need an extremely high strength-to-weight ratio but also require special traction patterns machined on their surfaces to handle the loose soil and sharp rocks on the Martian surface. Even more impressive is the rover's gearbox—composed of dozens of precisely machined gears from CNC gear cutting machines, with tolerance control within 5 microns, ensuring smooth operation in the Martian temperature range of -120°C to 20°C.
The scientific instruments on probes similarly rely on the ultra-high precision of CNC technology. For example, the Laser-Induced Breakdown Spectroscopy (LIBS) on the Mars rover is a core tool for chemical analysis. Its optical mirror mount requires CNC lathes to machine titanium alloy components with a surface roughness of 0.1 micron to ensure absolute collimation of the laser beam. The Mars sample collection system's drill bits use ultra-hard tungsten carbide materials machined by CNC grinders, capable of drilling into the hardest Martian rocks without deformation.
The Mars helicopter "Ingenuity" pioneered powered flight outside Earth, and its success is largely due to its CNC-machined lightweight structure. The rotor head of this 1.8-kilogram helicopter is CNC-milled from a solid block of aluminum alloy, ensuring strength while maximizing weight reduction. Its carbon fiber rotors use CNC routers to precisely trim edge contours, optimizing lift efficiency in the thin Martian atmosphere (only 1% of Earth's).
Thermal protection systems are another area where CNC excels. Mars probes must withstand temperatures up to 2,000°C when entering the atmosphere, and their heat shields must perfectly conform to aerodynamic requirements. Large CNC mills are used to machine heat shield molds with a precision of 0.025mm, ensuring ablative materials are evenly distributed and provide maximum protection at critical locations.
As Mars missions become increasingly complex, CNC multi-tasking machines (such as DMG Mori's NTX series) have become more important. These machines, worth hundreds of thousands of dollars, combine turning, milling, grinding, and other functions, completing all machining of complex parts in a single setup, avoiding cumulative errors from multiple setups. This is critical for key components in Mars probes such as precision gyroscope brackets and antenna universal joints.
Material Revolution: How CNC Machining Overcomes Mars' Extreme Environmental Challenges
Mars exploration equipment faces extreme environmental challenges rarely seen on Earth, from violent vibrations during launch, strong radiation in space, to extreme temperature variations and dust storms on the Martian surface. These harsh conditions place extraordinary demands on material performance, and CNC machining technology is key to realizing the potential of these special materials.
Titanium alloys play a central role in Mars missions, thanks to their excellent strength-to-weight ratio and corrosion resistance. Critical components such as the structural frame of Mars rovers and scientific instrument brackets widely use aerospace-grade titanium alloys like Ti-6Al-4V. However, titanium alloys have poor thermal conductivity and high chemical activity, making traditional machining methods prone to excessive tool wear and part deformation. Modern CNC machine tools equipped with high-pressure cooling systems and specially coated tools can precisely control cutting parameters, achieving efficient machining of titanium alloys. For example, the sample containers in NASA's Mars Sample Return mission use CNC-machined titanium alloy sealed structures to ensure Mars rock samples remain uncontaminated during their return to Earth.
Nickel-based superalloys such as Inconel 718 are used in Mars lander propulsion systems and thermal protection components due to their excellent performance at extreme temperatures. These materials are even more difficult to machine, with traditional methods often resulting in extremely short tool life. CNC machine tools successfully address the forming problems of these "difficult-to-machine materials" by optimizing cutting paths, using ceramic or cubic boron nitride (CBN) tools, and precisely controlling feed per tooth. For example, the injector face plate of a Mars lander engine needs to be precisely milled from a solid block of Inconel alloy, with the size tolerance of its hundreds of fuel injection holes controlled within ±0.005mm.
Carbon Fiber Reinforced Polymers (CFRP) are increasingly important in space applications seeking lightweight solutions. Components such as the Mars helicopter rotors and probe antenna reflectors use this high-strength composite material. CNC routers equipped with diamond-coated tools can precisely cut CFRP without causing delamination or burrs. Notably, some CFRP components are manufactured using CNC-machined aluminum alloy molds, which themselves need to achieve extremely high surface finishes (Ra<0.4μm) to ensure perfect forming of composite parts.
The combination of additive manufacturing and CNC has opened a new era in Mars component production. For example, NASA has begun using CNC-machined metal 3D printed parts, such as the PIXL instrument bracket on the Perseverance rover in the Mars 2020 mission. Germany's Trumpf company's Laser Metal Fusion (LMF) technology combines 3D printing and CNC precision machining to produce complex internal cooling channel structures impossible with traditional methods. This hybrid manufacturing method is particularly suitable for critical components in Mars missions that require high customization and low volume production.
As materials science advances, CNC machining technology continues to evolve to meet new challenges. For example, to address the abrasiveness of Martian dust, researchers are developing new surface treatment technologies that significantly enhance the wear resistance of aluminum alloy components through CNC-controlled laser surface texturing or micro-arc oxidation treatment. These innovations will allow future Mars exploration equipment to operate longer in harsh environments.
From Earth to Mars: The Future Role of CNC Technology in Space Exploration
As humanity sets its sights on Mars colonization and long-term exploration, CNC machine tool technology is facing new development opportunities and challenges. Future Mars missions will require more complex and reliable equipment, and CNC manufacturing technology will play an even more diverse role in the new chapter of space exploration.
In-Situ Resource Utilization (ISRU) equipment will be key to future Mars missions, with CNC technology at the core of its realization. NASA plans to deploy systems in Mars missions in the 2030s that can produce oxygen, fuel, and building materials from carbon dioxide in the Martian atmosphere and water ice in the soil. The reactors, compressors, and separation membrane components of these ISRU systems require extremely high sealing properties and corrosion resistance, achievable only through high-precision CNC machining. For example, the titanium alloy bipolar plates of carbon dioxide electrolyzers require five-axis CNC machining of complex flow channel patterns with precision requirements of ±0.01mm to ensure optimal gas distribution and reaction efficiency.
The construction of Mars habitat modules will rely on advanced CNC technology. Unlike the prefabricated aluminum alloy modules used on the International Space Station, Mars habitation modules may require a combination of on-site 3D printing and precision machining. Portable CNC equipment will be used to trim the connecting surfaces of 3D printed structures, machine installation interfaces for radiation protection shields, and manufacture support frames inside habitation modules. Taiwan's Jedi Precision Machinery and other manufacturers' high-speed drilling and milling machining centers, known for their high precision and stability, could become candidate technologies for such space applications.
Autonomous repair of Mars rovers is key to the success of long-term missions. Future Mars rovers may be equipped with small CNC repair units capable of replacing worn parts or machining emergency components in the Martian environment. This requires the development of extremely compact CNC systems that can withstand Martian temperature variations and dust. The smart factory technology developed by Japan's Mazak, including real-time monitoring and predictive maintenance functions, may provide insights for such space CNC systems.
The rise of space manufacturing will further expand the application boundaries of CNC technology. "Space factories" established in near-Earth orbit or on the Moon may use CNC equipment to machine satellite parts or deep space probe components, avoiding subjecting these precision instruments to the violent vibrations of rocket launches. Germany's Trumpf company's space laser processing technology has demonstrated the feasibility of metal cutting and welding in microgravity environments, which could form the basis of future space CNC systems.
Notably, CNC technology itself is constantly evolving to adapt to space requirements. Traditional CNC machine tools rely on Earth's gravity to ensure structural stability and chip evacuation, while in Mars' 1/3 gravity or space microgravity environments, spindle bearings, cooling systems, and chip removal mechanisms need to be redesigned. Some innovative designs such as magnetic levitation spindles and mist cooling systems are being tested in laboratories and may become standard configurations for future "space-grade CNC."
With advances in artificial intelligence and machine learning, autonomous CNC systems will greatly enhance the self-sustaining capability of Mars missions. CNC equipment with autonomous decision-making capabilities can automatically optimize cutting parameters based on material characteristics and even independently complete the design and manufacture of emergency parts without real-time guidance from Earth engineers. This is crucial for Mars bases located hundreds of millions of kilometers from Earth with communication delays of dozens of minutes.
From precision gears to large habitat module structures, from Earth factories to the Martian surface, CNC technology continues to expand its boundaries with human space exploration. This manufacturing technology, which began in the mid-20th century, will continue to play an irreplaceable role in humanity's great journey to become an interplanetary species.
Conclusion: CNC Machine Tools—The Unsung Heroes of Mars Exploration
As we look back on humanity's Mars exploration journey, from early flyby missions to today's sample return missions, every achievement has the silent contribution of CNC machine tool technology behind it. These metal-cutting specialists in Earth factories, with their unparalleled precision and reliability, have created space miracles that can operate perfectly hundreds of millions of kilometers away.
The value of CNC technology to Mars exploration is reflected not only in the manufacture of individual parts but also in the extreme reliability it brings to space equipment. In a place as remote and environmentally harsh as Mars, repair is almost impossible; equipment must be nearly perfect before launch. The micron-level precision and consistency provided by CNC machining ensures this, allowing Mars rovers to continue operating for years after their design life ends (such as the Opportunity rover, which lasted 15 years on a mission originally planned for 90 days).
With the rise of commercial aerospace and more countries joining Mars exploration, CNC technology has also become more widespread and democratized. High-end CNC equipment that once only large space agencies like NASA could afford is now increasingly accessible to private enterprises and small research teams. Taiwan's CNC controller manufacturers such as Syntec and Advantech LNC have become important suppliers in the Asia-Pacific region, showing the diverse development of the global CNC technology ecosystem.
The next decade will be a golden period for human Mars exploration, from sample return missions to possible human landings. Every ambitious plan will rely on the continued innovation of CNC technology. Whether processing lighter and stronger new materials or achieving breakthroughs in in-situ space manufacturing, CNC machine tools will continue to serve as the "mother machines of manufacturing," supporting humanity's advance toward the Red Planet.
The next time you see the latest images transmitted by Mars rovers, think about the Earth-based technology behind these amazing achievements. CNC machine tools may not be as eye-catching as rocket launches, but it is these precision craftsmen in factories that have turned human scientific dreams into solid metal reality, allowing our exploration steps to steadily march toward Mars and even farther into the stars.