Breaking the Skies: Advanced Engineering Plastics for Aerospace Applications
2024-03-19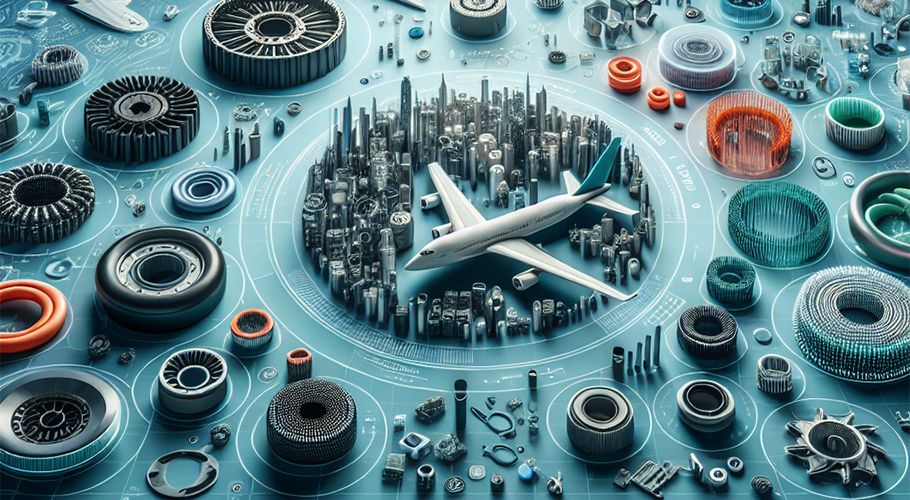
The aerospace industry has stringent material requirements, necessitating the use of specialized high-performance plastics to meet the demands of extreme environments. Here are some common aerospace-grade plastics:
- Polyimide (PI) Offering exceptional high-temperature resistance (over 300°C), low flammability, and excellent insulation properties, it is typically used in the manufacture of connectors, cable jacketing, and structural components.
- Polyetheretherketone (PEEK) Heat-resistant (up to 250°C), chemically resistant, and mechanically robust, PEEK is widely used in the production of gears, bearings, and sealing rings for load-bearing components.
- Polyamide-imide (PAI) With outstanding dimensional stability, insulation properties, resistance to high and low temperatures, and chemical corrosion, PAI can be used to make wire jackets, junction boxes, and other electrical components.
- Liquid Crystal Polymer (LCP) Boasting excellent dimensional stability, mechanical strength, and flowability, LCP is commonly used in the manufacture of aerospace connectors, radome housings, and other precision components.
- Polyetherketoneketoneketone (PEKEKK) With high-temperature resistance (up to 350°C), high rigidity, and mechanical strength, PEKEKK is suitable for manufacturing structural components subjected to extreme conditions, such as engine parts.
- Polytetrafluoroethylene (PTFE) Offering exceptional chemical stability and self-lubricating properties, PTFE is widely used in the production of sliding bearings, gaskets, seals, and other friction components.
Compared to traditional metallic materials, these high-performance engineering plastics offer advantages such as lightweight, corrosion resistance, high-temperature resistance, and insulation properties, making them indispensable key materials for spacecraft and aircraft. The development of advanced aerospace materials will remain a focal point in the future.
These aerospace-grade plastics that may require the use of tungsten carbide milling cutters during their manufacturing process include:
- Polyimide (PI) PI plastics have very high thermal stability and dimensional stability. During processing and molding, they often require higher temperatures and greater cutting forces. Tungsten carbide milling cutters can withstand these high-temperature and high-force cutting conditions without excessive wear or deformation.
- Polyetheretherketone (PEEK) PEEK is a semi-crystalline high-performance plastic that is difficult to machine. Using tungsten carbide milling cutters can improve machining accuracy and surface quality.
- Liquid Crystal Polymer (LCP) LCP plastics have good flowability, but are also very rigid. Machining precise components requires the use of hard alloy tools like tungsten carbide milling cutters.
- Polyetherketoneketoneketone (PEKEKK) PEKEKK has even higher heat resistance than PEEK. When machining at high temperatures, the hardness advantage of tungsten carbide tools becomes more pronounced.
- Polytetrafluoroethylene (PTFE) PTFE is a highly rigid plastic with self-lubricating properties. Machining requires the high hardness and strength of tungsten carbide milling cutters to overcome the cutting resistance from these properties.
In general, these high-performance aerospace plastics mostly possess excellent heat resistance, chemical stability, and high strength. Their machining and manufacturing place stringent demands on cutting tools. Using tungsten carbide or tungsten carbide-based alloy milling cutters can meet these demanding cutting conditions.