改善難加工材料可加工性方法的研究進展
2020-04-27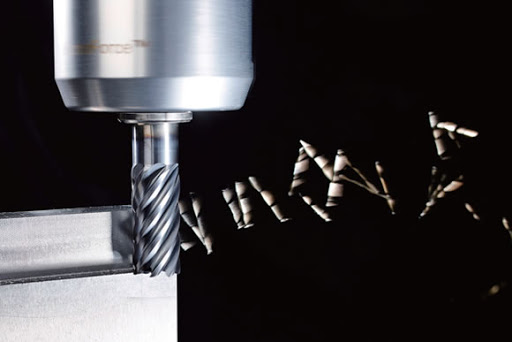
隨著航空航天業和核能工業的發展,難加工材料如鈦合金、高溫合金等被越來越廣泛地應用。因為高溫合金具有較高的高溫強度,抗氧化、抗熱腐蝕、抗疲勞和斷裂韌性等綜合性能良好,且能夠在 600℃以上長時間保持良好性能,所以該類材料被廣泛應用於航空航天、艦船及化工等行業。高溫合金的切削加工性差主要表現在:(1)高溫強度高,切削力大;(2)熱導率低,加工過程中切削溫度高達 1000℃ ;(3)刀具磨損嚴重,在高溫高壓下,造成刀具的黏結磨損和擴散磨損。
鈦合金比強度高、耐腐蝕和耐高溫等良好性能使其成為飛機發動機零部件的材料。鈦合金也是一種難加工材料,其切削溫度較高、加工變形係數小使得刀具易產生磨損。因此,加工鈦合金的切削速度一般在40m/min 以下,這影響著切削鈦合金的加工效率。
鈦合金比強度高、耐腐蝕和耐高溫等良好性能使其成為飛機發動機零部件的材料。鈦合金也是一種難加工材料,其切削溫度較高、加工變形係數小使得刀具易產生磨損。因此,加工鈦合金的切削速度一般在40m/min 以下,這影響著切削鈦合金的加工效率。
材料可加工性的分析方法
國內外學者對材料可加工性評價和分析方法有 6 種。
(1)單一指標評定方法:
根據刀具壽命或刀具壽命下所能達到的切削速度、切削力或切削溫度、切削加工後工件的表面質量、切屑控製或斷屑的難易程度等單一指標來評價材料的可加工性。
(2)相對加工性方法:
以正火狀態下的中碳鋼 45 鋼為基準來評價其他材料的可加工性。
(3)模糊綜合評判方法:
利用材料性能參數如硬度、抗拉強度、延伸率及導熱率等作為影響材料可加工性的主要性能指標,根據其對可加工性的影響,然後用模糊綜合評判方法對材料的可加工性進行綜合評價。
(4)利用切削加工過程的材料及工藝參數
(工件材料的物理機械性能指標、刀具材料及刀具的幾何參數等)對影響參數(刀具的磨損、切削力的大小、加工後的表面精度和尺寸精度)影響評價材料的可加工性。
(5)利用切削加工過程輸出參數評價材料的可加工性
基於切削力和表面粗糙度利用加權因子來評估鋼件可加工性的方法。
(6)利用相位圖方法
確定影響難加工材料可加工性的 5 個關鍵物理機械性能指標,即硬度、延展性、加工硬化、導熱性及磨蝕性。
難加工材料加工方法
1 高壓噴射冷卻加工
WOTEK公司採用高壓冷卻技術冷卻液直接噴向刃口區域,降低切削區域溫度,使易於卷屑,從而達到控制切屑的目的。在切削速度相同的情況下,其金屬去除量增加50% ;若切削速度提高 20%,金屬去除量同時增加 20%。對於鈦合金等難加工材料的切削,在用普通切削液加工時,由於切削熱量多、切削溫度高且集中於切削刃附近,易於形成月牙窪磨損。在切削鈦合金時,採用高壓內冷刀具,冷卻液通過高壓噴射到切削區域,直接對切削點的刀尖進行冷卻,降低切削刃的溫度和減輕刀具磨損,同時高壓液體打碎切屑並及時將切屑排走。而且冷卻液還可起潤滑的作用,減少刀具和工件之間的摩擦、使切削力降低,利用這種方法可提高刀具壽命,降低刀具成本,而且良好的斷屑和排屑效果能夠改善零件的加工質量。
2 微量潤滑切削加工
微量潤滑切割(Minimal Quantity Lubrication,MQL)是一種應用較廣的準乾式切削方法,它在壓縮空氣中混入微量的無公害油霧,代替大量油劑對切削區域冷卻、潤滑和排屑。研究表明 MQL 技術可以有效地減輕刀具、切屑及刀具、加工表面之間的摩擦阻力,降低最高切削溫度、減小刀具磨損、提高加工表面質量作用。WOTEK以鈦合金TC4 的高速銑削為對象,高速銑削力和刀具磨損特性分析表明,利用低溫氮氣和微量潤滑劑能夠有效地抑制加工區的溫升、降低切削力、 延長刀具的使用壽命及提高加工表面精度。WOTEK採用氣霧微量潤滑輔助 PCD 刀具切削鈦合金,並改善鈦合金的切削加工工藝。氣霧微量潤滑輔助 PCD 刀具切削鈦合金 裝置如圖 1 所示。
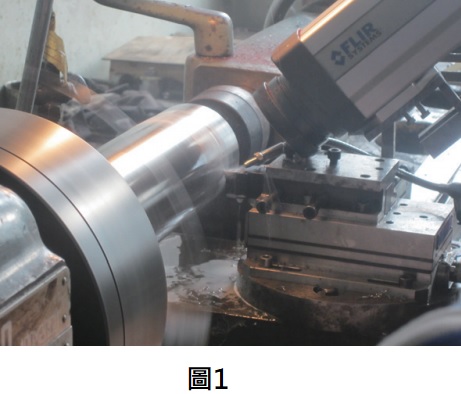
3 加熱輔助切削加工
加熱輔助切削是通過等離子或激光加熱源,把工件的整體或局部加熱到一定溫度後再進行切削加工的方法。通過等離子加熱源對切削區域局部加熱,如 Inconel 718 在750℃以上時屈服強度有明顯降低。Leshock 等, 利用離子加熱切削法(Plasma Enhanced Machinig, PEM)切削 Inconel 718 的研究表明,隨著表面溫度的提高,切削力明顯下降,同時加工後工件表面質量也有所改善。但是,當溫度超過 530℃以上時,工件表面會出現氧化現象,通過精確控制加熱源可避免這種現象。
Lopez de Lacalle LN 等研究等離子弧輔助銑削3 種難加工材料(Inconel 718、Haynes 25 和 Ti6Al4V),加工 Inconel 718 和Haynes 25 時,其切削力顯著降低,刀具使用壽命和表層質量提高;但是,加工 Ti6Al4V 時由於加熱改變材料微觀結構,反而使得刀具壽命降低和材料表面變脆,因此,等離子弧不適宜加工鈦合金。其中,激光加熱輔助切削(Laser Assisted Machining,LAM)技術是將高功率激光束聚焦到切削刃前的工件表面,短時間內將工件局部加熱到很高的溫度,軟化金屬材料並使其屈服強度降低,從而減輕切屑變形、降低切削力和減小刀具磨損,達到提高加工表面質量和加工效率的目的。
研究激光束對 Ti6Al4V 合金加工過程時切屑形成的影響,採用一個物理模型解析 LAM 高速切削時形成連續切屑機理。 Rashid 等研究了 LAM 加工 β 鈦合金 Ti-6Cr5Mo-5V-4Al 的特點,因激光照射工件表面升溫,使材料屈服強度降低、切削力下降且金屬去除率提高。Rashid 等研究了 LAM 改善難加工材料 Ti-10V-2Fe-3A 的切削加工性。Attia 等乾式下採用激光輔助高速精車高溫合金 Inconel 718,提高材料去除率,最高可達傳統車削的 8 倍,且刀具使用壽命和表面加工質量也得到提高。王岩針對激光加熱輔助銑削高溫合金 K24 研究,獲得工藝參數對切削力、刀具使用壽命及表面質量的影響規律。
Lopez de Lacalle LN 等研究等離子弧輔助銑削3 種難加工材料(Inconel 718、Haynes 25 和 Ti6Al4V),加工 Inconel 718 和Haynes 25 時,其切削力顯著降低,刀具使用壽命和表層質量提高;但是,加工 Ti6Al4V 時由於加熱改變材料微觀結構,反而使得刀具壽命降低和材料表面變脆,因此,等離子弧不適宜加工鈦合金。其中,激光加熱輔助切削(Laser Assisted Machining,LAM)技術是將高功率激光束聚焦到切削刃前的工件表面,短時間內將工件局部加熱到很高的溫度,軟化金屬材料並使其屈服強度降低,從而減輕切屑變形、降低切削力和減小刀具磨損,達到提高加工表面質量和加工效率的目的。
研究激光束對 Ti6Al4V 合金加工過程時切屑形成的影響,採用一個物理模型解析 LAM 高速切削時形成連續切屑機理。 Rashid 等研究了 LAM 加工 β 鈦合金 Ti-6Cr5Mo-5V-4Al 的特點,因激光照射工件表面升溫,使材料屈服強度降低、切削力下降且金屬去除率提高。Rashid 等研究了 LAM 改善難加工材料 Ti-10V-2Fe-3A 的切削加工性。Attia 等乾式下採用激光輔助高速精車高溫合金 Inconel 718,提高材料去除率,最高可達傳統車削的 8 倍,且刀具使用壽命和表面加工質量也得到提高。王岩針對激光加熱輔助銑削高溫合金 K24 研究,獲得工藝參數對切削力、刀具使用壽命及表面質量的影響規律。
4 低溫冷卻輔助切削加工
液氮冷卻的方法之一是將液氮作為切削液直接噴射到切削區(見圖2)。該方法是用液氮(最低溫可達-186℃)、液體二氧化碳(最低溫可達-76℃)及其他低溫液體作切削液噴射到加工區,對刀具和工件之間的加工部位進行潤滑。既可以冷卻切削區,也可以潤滑液在刀具表面形成的潤滑膜從而提高刀具的壽命。這種冷卻切削的冷卻能力比高壓噴射冷卻強,能夠顯著降低切削鈦合金和高溫合金等難加工材料時由高溫引起的刀具磨損。 TiAlN 塗層硬質合金刀具車削 Inconel 718 時,刀尖磨損在低溫油霧冷卻的情況下,已加工表面的表面質量相對於冷風和乾切削都有明顯改善。
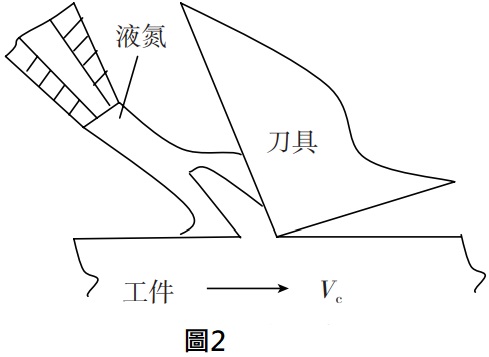
提高難加工材料切削效率的方法
為了提高航空航天難加工材料切削效率,可採用的措施有:刀具材料的選用、合理的刀具幾何參數選擇、切削用量的優選、加工方式的選擇和新型刀具設計等 5 種。
1 刀具材料的選用
因為 Co 材料熱穩定性好和高溫下能保持較高的硬度,如鈷高速鋼在切削溫度 645~650℃時,其硬度為67~70HRC,可用於加工高溫合金、鈦合金、奧氏體耐熱鋼及其他難加工合金。含鈷超硬高速鋼(W2Mo9Cr4Co8(M42))的硬度為 69~70HRC,適合加工鐵基高溫合金、鑄造高溫合金、鈦合金和超高強度鋼等難加工材料。
碳化物晶粒的平均尺寸在0.5μm以下的WC-Co硬質合金硬度為90~93HRA,其抗彎強度為2000~3500MPa,如 YS2(K30)適合加工鐵基、鎳基高溫合金和鈦合金。對於經過 PVD 工藝的 TiAlN 塗層硬質合金刀具,塗層表層生成高強度的非結晶氧化鋁薄膜(Al2O3),其硬度高、氧化溫度高、紅硬性好、附著力強、摩擦力小、導熱率低。該種刀具適合較高的切削速度,而較低的切削速度易於產生積屑瘤,從而導致微崩和溝槽磨損。陶瓷如 Si3N4、氧化鋁基陶瓷具有很高的高溫性能(Al2O3 熔點為2050 ℃)、高硬度和耐磨性(91~95 HRA),能加工鎳基或鈷基耐熱合金,如加工 Inconel 718(GH169)時,切削參數 V c=200m/min, fz=0.2mm/z,而採用硬度合金加工時切削參數 Vc=30m/min,fz=0.3mm/z。立方氮化硼CBN具有很高的硬度和耐磨性、熱穩定性(1400~1500 ℃時比金剛石高一倍;800℃時是陶瓷和硬質合金常溫性能),優良的化學穩定性及抗氧化能力(1000℃時會產生一層氧化硼B2O3 薄膜,防止進一步氧化),良好的導熱性,較低的摩擦係數(0.1~0.3)。CBN 的含量越高其硬度越高,適合加工耐熱鋼、高硬鋼;含量低的適合加工一般硬鋼及有衝擊的切削。CBN 晶粒尺寸小、耐磨性好(21μm減至 13μm 時,刀具壽命可提 高28%)。 CBN 刀具採用負前角(-6°~-18°),加工鎳基合金應採用正前角(0°~8°),後角可大些(6°~25°)。
金剛石(單晶)刃口鋒利、熱傳導率高,具有較少的刀尖滯留熱量,極高的硬度和耐磨性,很低的摩擦係數等特點。金剛石(碳)在鈦中的溶解度比在鐵中小得多,故其擴散磨損很小。硬質合金(K 類)加工 Ti6Al4V,V c=20~50m/min ;加工天然金剛石Vc=100~120m/min ,切削時間 30min,刀具幾乎沒有磨損;用濕式法切削Vc=200m/min,刀具幾乎沒有磨損。
碳化物晶粒的平均尺寸在0.5μm以下的WC-Co硬質合金硬度為90~93HRA,其抗彎強度為2000~3500MPa,如 YS2(K30)適合加工鐵基、鎳基高溫合金和鈦合金。對於經過 PVD 工藝的 TiAlN 塗層硬質合金刀具,塗層表層生成高強度的非結晶氧化鋁薄膜(Al2O3),其硬度高、氧化溫度高、紅硬性好、附著力強、摩擦力小、導熱率低。該種刀具適合較高的切削速度,而較低的切削速度易於產生積屑瘤,從而導致微崩和溝槽磨損。陶瓷如 Si3N4、氧化鋁基陶瓷具有很高的高溫性能(Al2O3 熔點為2050 ℃)、高硬度和耐磨性(91~95 HRA),能加工鎳基或鈷基耐熱合金,如加工 Inconel 718(GH169)時,切削參數 V c=200m/min, fz=0.2mm/z,而採用硬度合金加工時切削參數 Vc=30m/min,fz=0.3mm/z。立方氮化硼CBN具有很高的硬度和耐磨性、熱穩定性(1400~1500 ℃時比金剛石高一倍;800℃時是陶瓷和硬質合金常溫性能),優良的化學穩定性及抗氧化能力(1000℃時會產生一層氧化硼B2O3 薄膜,防止進一步氧化),良好的導熱性,較低的摩擦係數(0.1~0.3)。CBN 的含量越高其硬度越高,適合加工耐熱鋼、高硬鋼;含量低的適合加工一般硬鋼及有衝擊的切削。CBN 晶粒尺寸小、耐磨性好(21μm減至 13μm 時,刀具壽命可提 高28%)。 CBN 刀具採用負前角(-6°~-18°),加工鎳基合金應採用正前角(0°~8°),後角可大些(6°~25°)。
金剛石(單晶)刃口鋒利、熱傳導率高,具有較少的刀尖滯留熱量,極高的硬度和耐磨性,很低的摩擦係數等特點。金剛石(碳)在鈦中的溶解度比在鐵中小得多,故其擴散磨損很小。硬質合金(K 類)加工 Ti6Al4V,V c=20~50m/min ;加工天然金剛石Vc=100~120m/min ,切削時間 30min,刀具幾乎沒有磨損;用濕式法切削Vc=200m/min,刀具幾乎沒有磨損。
2 合理的刀具幾何參數選擇
一般來說,正前角(γ)刀片降低切削力、切削熱、加工硬化等,但強度減弱;大後角 α(6°~10°)減輕刀具與工件摩擦、鋒利、切削力、切削熱、散熱性等;主偏角 kr(45°~90°)增強刀具散熱、減少切削力,切屑厚度和寬度等;刃傾角 λs(0°~20°)影響切屑流向、增強刀尖強度等;刀尖 rε小些好,但刀尖強度要考慮。採用陶瓷刀具加工鑄造高溫合金時 γ=0°~3°,α=10°~15°;變形高溫合金 α=0°~10°,α=10°~15°;立方氮化硼和金剛石刀具:變形高溫合金 γ=0°~8°,α=8°~20°;關於刀具塗層應用於切削高溫合金材料,其中 CVD 塗層適用於粗加工,PVD 適用半精加工和精加工,而 PVD 適用於精加工。
3 切削用量的優選
切削高溫合金時切削速度不宜過高,因為高溫合金的強度高、黏性大,切削中更容易在切削區產生和積聚熱量,且導熱性差,在大切除量的切削時,如果切削速度過高,有引起刀具和工件燒傷的趨勢。就目前的使用刀具而言,鈦合金的切削速度一般在 30~80m/min 之間,鎳基合金也在 250m/min 之內。
選擇合理切削速度需要考慮:高的切削速度可以避開材料的積屑瘤區;增加切削速度可使溫度上升,通過減少切削速度達到低溫或採用冷卻。表 1 為不同刀具材料加工高溫合金、鈦合金的切削速度選擇。
選擇合理切削速度需要考慮:高的切削速度可以避開材料的積屑瘤區;增加切削速度可使溫度上升,通過減少切削速度達到低溫或採用冷卻。表 1 為不同刀具材料加工高溫合金、鈦合金的切削速度選擇。
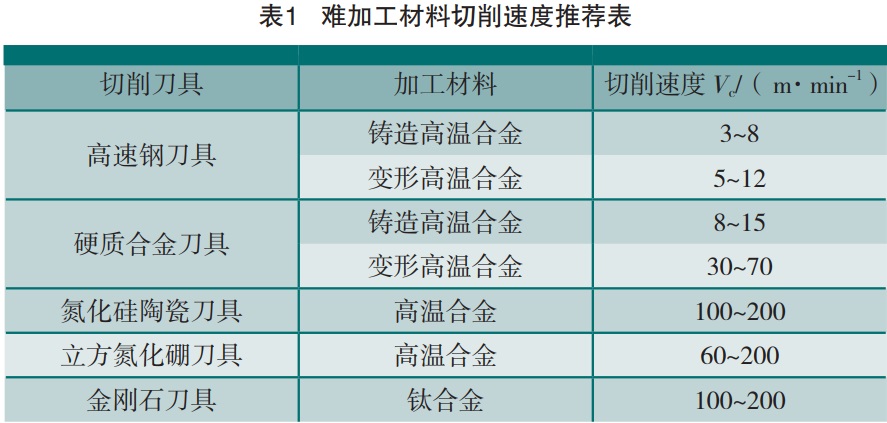
高溫合金切削溫度高,同時存在加工硬化的問題。每齒進給量過大,則切削力過大而導致崩刃或是切削溫度過高而燒刀;而每齒進給量過小,則因刀刃始終在加工硬化層中工作而快速磨損。一般來說,切削參數取每齒進給量fz=0.1~0.5mm/z,且精車和銑削加工時工藝系統剛性不好時取小值,粗車加工工藝系統剛性好時可取大值。以加工 Inconel 718(GH169)為例:採用硬質合金刀具切削參數:Vc=25m/min,ap=3.4mm,fz=0.23mm/z ;採用氮化矽陶瓷刀具切削參數:Vc=172m/min, ap =10mm,fz=0.18mm/z。
4 加工方式選擇
就高溫合金而言,逆銑切屑是由薄到厚,在最初切入時刀具易與工件發生幹摩擦,加重刀具的粘屑和崩刃,因此盡量採用順銑加工,即刀齒一開始切入就碰到硬皮而容易導致刀具破損。對於渦輪葉片加工,可採用高效插銑技術,即在 3 軸或 4 軸專用銑床上插銑加工渦輪葉片:從渦輪葉片頂部插銑刀向下運動,直接到達其根部,並通過 X-Y 平面的數控控制平面運動可加工出複雜曲面。
5 新型刀具設計
波型刃的立銑刀有效改善刀具切入和切出時刀刃受到機械衝擊和熱衝擊的影響,從而盡量避免其脆性破損。WOTEK刀具公司開發用於粗加工鎳基合金波型刃的立銑刀,其螺旋角 20º ,有 4~6 刀槽,直徑為 6~20mm,排屑順暢(見圖 3)。刀具生產廠商為典型零件加工提供可操作的加工方案。如WOTEK就難加工材料高溫合金製造的如渦輪盤類迴轉零件,該零件有多種凹腔,要求設計、選擇刀具和規劃走刀路徑時考慮到刀具與工件之間的合理間隙以避免干涉。