利用準對稱加工法檢測7075鋁合金航空整體件的銑削變形
2020-05-05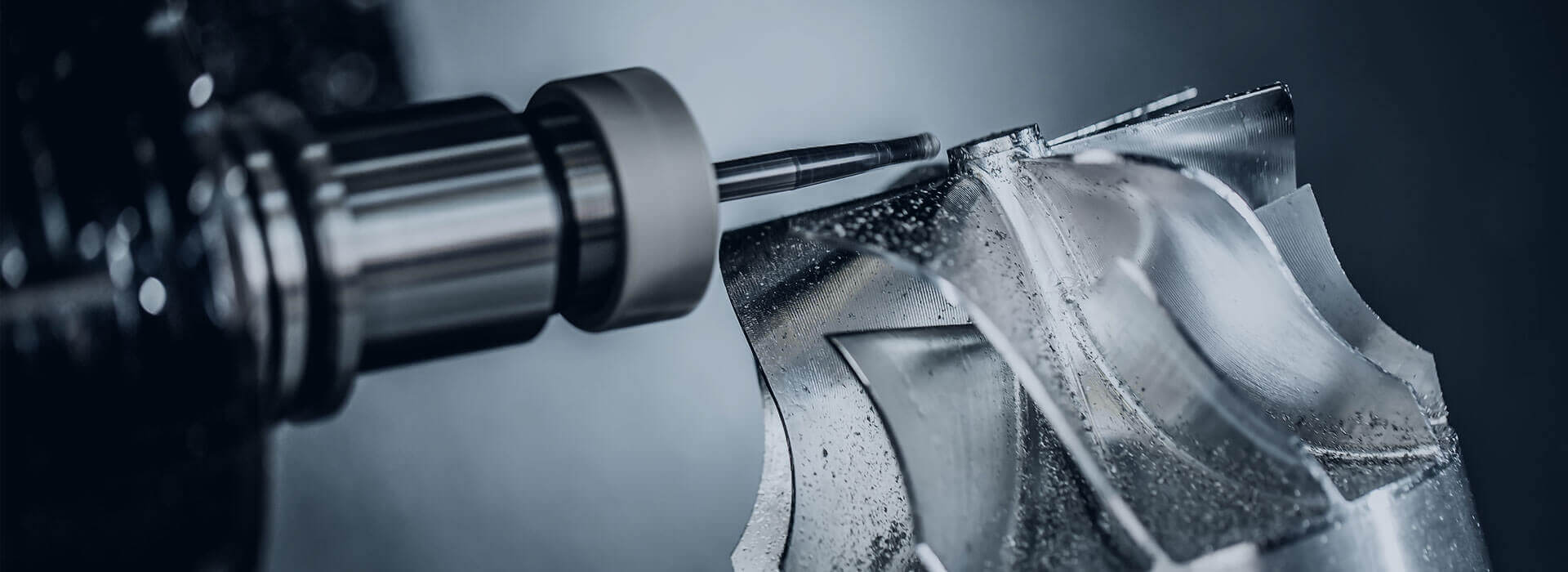
摘要
航空單體機零件因數控加工而產生的變形是航空工業中的棘手問題。在材料去除過程中,殘餘應力釋放和再分配,產生單體零件的變形。傳統的單面加工方法會產生過大的變形。本研究在三段式數控加工法的基礎上,利用殘餘應力的M對稱分佈規律,提出了準對稱加工法,通過對稱材料去除變形的方法來減少變形。研究了殘餘應力引起的銑削變形的機理。採用傳統的單面加工法和準對稱加工法進行了變形實驗,與有限元法進行了比較。通過對比結果驗證了變形參數。大部分誤差都在10%以內。確定了這些誤差的原因,以提高該方法的可靠性。此外,採用準對稱加工法的最大變形值比傳統單面加工法的最大變形值在20%以內。這一結果顯示,準對稱加工法能有效地減少殘餘應力引起的變形。因此,本研究介紹了一種有效降低單面薄壁零件在數控銑削加工中的變形的方法。
1. 導言
用各種方法生產的整機薄壁結構在航空技術中得到了廣泛的應用,尤其是用機械加工方法生產的整機薄壁結構。 Schubert等人提出,對於所有生產運動質量的分支來說,輕質構件是至關重要的利益。要達到減輕重量的目的,必須要有較高的生產效率和零件性能。 Mangalgiri提出,複雜和復合材料將廣泛使用。
然而,當過大的航空整體結構在加工時,大部分加工材去除後會造成其變形,這被認為是航空製造領域普遍存在的棘手問題。 Dong和Ke總結出造成變形的主要原因是,當大量材料被去除後,毛坯中的殘餘應力平衡被打破。為了使其重新平衡,殘餘應力重新分佈,同時產生單體構件的變形。同時,Wang等也提出了類似的觀點,在加工薄壁飛機零件時,90%以上的材料會被去除,由於剛性減弱和殘餘應力的釋放,導致零件嚴重變形。這也可能導致零件的應力集中和損壞。因此,殘餘應力是造成航空薄壁結構零件加工變形的重要原因之一。同時,大量的工件採用高速銑削加工,在高速銑削過程中可能會出現與震動有關的問題,這是一種不穩定的加工過程。顫震現像出現在高去除率的粗加工中,以及低剛度機身零件的精加工中也會出現顫震現象。
很多研究都集中在薄壁板不同加工工藝的影響上,以輔助機械製造工藝的優化。 Guo等建立了一個考慮初始殘餘應力場的三維(3-D)有限元模型,計算薄壁框形工件的加工變形。 Jomaa等提出了AA7075-T651合金的正交干法加工引起的表面光潔度和殘餘應力的實驗研究,並詳細研究了表面損傷機理。 Liu提出了螺旋刀具和帶懸臂薄壁零件的三維有限元模型,預測了Ti6Al4V鈦合金薄壁零件在銑削加工中的切削變形。
Maurel-Pantel等人利用Lagrangian公式與顯式求解方案和懲罰性接觸算法,利用商用軟件LS-Dyna研究了AISI 304L不銹鋼的肩部銑削作業模擬。 Eslampanah等採用熱彈性-塑性有限元法預測T型鋼焊接接頭的殘餘應力和變形,並建立了非耦合熱力學三維模型。 Ocana等人提出了一個模型,對激光作用引起的殘餘應力和表面變形進行了預測性評估,用於分析銑削過程中不同參數的影響。
為了提高鈦合金的加工生產率和刀具壽命,Nouari和Makich研究了鈦合金的加工性差,尤其是Ti-55531鈦合金切削時產生出極度的刀具磨損和切削力不穩定。 Denkena等提出了一種在瞬態銑削模擬中識別和建模這些工藝阻尼效應的方法,並介紹了一種基於仿真和實驗的程序,根據刀具倒角幾何形狀確定所需的仿真參數,並對其進行了評價。 Abe和Sasahara探討了層壓後殼結構中殘餘應力與溫度分佈的關係,並測量了殘餘應力釋放引起的變形。本文主要研究了減少銑削過程中殘餘應力引起的變形。
其他研究集中在分析變形與殘餘應力關係的不同研究方法上,尤其是計算機仿真和實驗研究方法。 Wei和Wang建立了原始殘餘應力的有限元模型,通過加工航空薄壁零件,特別是加工大型航空航天零件時,建立了相應的撓度分析有限元模型,仿真結果與實驗結果近似一致。
Yaghi等討論了薄壁和厚壁不銹鋼管焊接構件中的殘餘應力,並對焊縫模擬進行了簡要論述,分析了更多的內半徑與壁厚比的FE模型,研究了管徑對殘餘應力的影響。 Wu和Li提出了一種數值方法來預測三維銑削過程中產生的表面殘餘應力和應變梯度。將有限元模擬的殘餘應力與基於不同切削條件下加工的7075樣品的X射線測量結果的實驗進行了比較。研究了切削條件對表面殘餘應力分佈的影響。
Husson等根據變形勢的假設,提出了一種估算某些因素對變形影響的方法,不僅考慮幾何形狀,還考慮了殘餘應力,並在此基礎上提出了估算變形勢的方法。為了研究毛坯初始殘餘應力對構件變形的影響,Huang等人採用化學銑削的方法去除加工引起的構件表面殘餘應力,證明了毛坯中的初始殘餘應力是三框單光束變形的主要因素。
考慮到薄壁零件的變形受材料被切除後產生的殘餘應力的影響較大,Li等分析了切削深度對殘餘應力再分佈的影響,證明在粗加工和精加工中通過控制和優化切削深度,可以有效地降低變形和殘餘應力的大小,並對其進行優化。本論文提出了準對稱加工方法和有限元分析法來降低殘餘應力引起的變形。
一些研究者集中在尋找分析和控制殘餘應力的方法。 Muñoz-Sánchez等建立並驗證了一種分析加工誘導殘餘應力中刀具磨損效應的數值模型。 Ballestra等通過實驗研究了金微束在殘餘應力梯度存在下,通過靜電激發對金微光束的動態表徵。此外,還對不同數值有限元模型和實驗結果進行了比較。
Chen等人研究了電接觸對微動開關熱接觸應力的影響。結果表明,殘餘應力隨著開關次數的增加而增多。 Jiang等基於未切割切屑厚度(UCT)模型,發現殘餘切向應力受UCT的影響,通過高速銑削控制UCT(進給率和刀具直徑)來優化殘餘應力分佈,為了控製材料去除率,他們提出了一種基於殘餘應力與UCT的關係,優化銑刀直徑的方法。 Zhang等人對大規模重疊激光衝擊強化衝擊產生的壓縮殘餘應力的均勻性提供了一定的啟示,在工程應用中具有很大的實際意義。
Mohammadpour等人基於非線性有限元代碼MSC.Mohammadpour等人進行了有限元分析。 Superform用於研究切削速度和進給率對正交切削後的表面和地下殘餘應力的影響。 Toribio等人研究了幾種殘餘應力曲線對預應力鋼絲在承受拉應力或彎矩作用下的疲勞裂紋擴展的影響。考慮到銑削過程中的刀具半徑,Li等建立了一個模型來分析高速銑削過程中的切削力和熱特性,並結合實驗驗證,表明機械力對殘餘應力的形成起著至關重要的作用。
Palkowski等提出了一種計算冷拔加工中拉拔管殘餘應力狀態的三維模型。 Krottenthaler提出了一種簡單的局部測定薄膜殘餘應力的方法,通過聚焦離子束(FIB)銑削和數字圖像相關(DIC)的應力鬆弛試驗,提出的方法為分析非晶態薄膜塗層中的殘餘應力提供了一種簡單的方法。此外,通過奈米壓痕法測定了薄膜的奈米硬度,並利用入射X射線衍射法測定了殘餘應力。
然而,傳統的單面加工方法會產生殘餘應力引起的過大變形。本文利用殘餘應力的M對稱分佈規律,提出了準對稱加工法,利用殘餘應力的M對稱分佈規律,通過材料的對稱去除來減小變形。並將得到的結果與FEM的結果進行了比較。驗證了準對稱加工法在減少殘餘應力引起的變形方面是一種可靠有效的方法。
然而,當過大的航空整體結構在加工時,大部分加工材去除後會造成其變形,這被認為是航空製造領域普遍存在的棘手問題。 Dong和Ke總結出造成變形的主要原因是,當大量材料被去除後,毛坯中的殘餘應力平衡被打破。為了使其重新平衡,殘餘應力重新分佈,同時產生單體構件的變形。同時,Wang等也提出了類似的觀點,在加工薄壁飛機零件時,90%以上的材料會被去除,由於剛性減弱和殘餘應力的釋放,導致零件嚴重變形。這也可能導致零件的應力集中和損壞。因此,殘餘應力是造成航空薄壁結構零件加工變形的重要原因之一。同時,大量的工件採用高速銑削加工,在高速銑削過程中可能會出現與震動有關的問題,這是一種不穩定的加工過程。顫震現像出現在高去除率的粗加工中,以及低剛度機身零件的精加工中也會出現顫震現象。
很多研究都集中在薄壁板不同加工工藝的影響上,以輔助機械製造工藝的優化。 Guo等建立了一個考慮初始殘餘應力場的三維(3-D)有限元模型,計算薄壁框形工件的加工變形。 Jomaa等提出了AA7075-T651合金的正交干法加工引起的表面光潔度和殘餘應力的實驗研究,並詳細研究了表面損傷機理。 Liu提出了螺旋刀具和帶懸臂薄壁零件的三維有限元模型,預測了Ti6Al4V鈦合金薄壁零件在銑削加工中的切削變形。
Maurel-Pantel等人利用Lagrangian公式與顯式求解方案和懲罰性接觸算法,利用商用軟件LS-Dyna研究了AISI 304L不銹鋼的肩部銑削作業模擬。 Eslampanah等採用熱彈性-塑性有限元法預測T型鋼焊接接頭的殘餘應力和變形,並建立了非耦合熱力學三維模型。 Ocana等人提出了一個模型,對激光作用引起的殘餘應力和表面變形進行了預測性評估,用於分析銑削過程中不同參數的影響。
為了提高鈦合金的加工生產率和刀具壽命,Nouari和Makich研究了鈦合金的加工性差,尤其是Ti-55531鈦合金切削時產生出極度的刀具磨損和切削力不穩定。 Denkena等提出了一種在瞬態銑削模擬中識別和建模這些工藝阻尼效應的方法,並介紹了一種基於仿真和實驗的程序,根據刀具倒角幾何形狀確定所需的仿真參數,並對其進行了評價。 Abe和Sasahara探討了層壓後殼結構中殘餘應力與溫度分佈的關係,並測量了殘餘應力釋放引起的變形。本文主要研究了減少銑削過程中殘餘應力引起的變形。
其他研究集中在分析變形與殘餘應力關係的不同研究方法上,尤其是計算機仿真和實驗研究方法。 Wei和Wang建立了原始殘餘應力的有限元模型,通過加工航空薄壁零件,特別是加工大型航空航天零件時,建立了相應的撓度分析有限元模型,仿真結果與實驗結果近似一致。
Yaghi等討論了薄壁和厚壁不銹鋼管焊接構件中的殘餘應力,並對焊縫模擬進行了簡要論述,分析了更多的內半徑與壁厚比的FE模型,研究了管徑對殘餘應力的影響。 Wu和Li提出了一種數值方法來預測三維銑削過程中產生的表面殘餘應力和應變梯度。將有限元模擬的殘餘應力與基於不同切削條件下加工的7075樣品的X射線測量結果的實驗進行了比較。研究了切削條件對表面殘餘應力分佈的影響。
Husson等根據變形勢的假設,提出了一種估算某些因素對變形影響的方法,不僅考慮幾何形狀,還考慮了殘餘應力,並在此基礎上提出了估算變形勢的方法。為了研究毛坯初始殘餘應力對構件變形的影響,Huang等人採用化學銑削的方法去除加工引起的構件表面殘餘應力,證明了毛坯中的初始殘餘應力是三框單光束變形的主要因素。
考慮到薄壁零件的變形受材料被切除後產生的殘餘應力的影響較大,Li等分析了切削深度對殘餘應力再分佈的影響,證明在粗加工和精加工中通過控制和優化切削深度,可以有效地降低變形和殘餘應力的大小,並對其進行優化。本論文提出了準對稱加工方法和有限元分析法來降低殘餘應力引起的變形。
一些研究者集中在尋找分析和控制殘餘應力的方法。 Muñoz-Sánchez等建立並驗證了一種分析加工誘導殘餘應力中刀具磨損效應的數值模型。 Ballestra等通過實驗研究了金微束在殘餘應力梯度存在下,通過靜電激發對金微光束的動態表徵。此外,還對不同數值有限元模型和實驗結果進行了比較。
Chen等人研究了電接觸對微動開關熱接觸應力的影響。結果表明,殘餘應力隨著開關次數的增加而增多。 Jiang等基於未切割切屑厚度(UCT)模型,發現殘餘切向應力受UCT的影響,通過高速銑削控制UCT(進給率和刀具直徑)來優化殘餘應力分佈,為了控製材料去除率,他們提出了一種基於殘餘應力與UCT的關係,優化銑刀直徑的方法。 Zhang等人對大規模重疊激光衝擊強化衝擊產生的壓縮殘餘應力的均勻性提供了一定的啟示,在工程應用中具有很大的實際意義。
Mohammadpour等人基於非線性有限元代碼MSC.Mohammadpour等人進行了有限元分析。 Superform用於研究切削速度和進給率對正交切削後的表面和地下殘餘應力的影響。 Toribio等人研究了幾種殘餘應力曲線對預應力鋼絲在承受拉應力或彎矩作用下的疲勞裂紋擴展的影響。考慮到銑削過程中的刀具半徑,Li等建立了一個模型來分析高速銑削過程中的切削力和熱特性,並結合實驗驗證,表明機械力對殘餘應力的形成起著至關重要的作用。
Palkowski等提出了一種計算冷拔加工中拉拔管殘餘應力狀態的三維模型。 Krottenthaler提出了一種簡單的局部測定薄膜殘餘應力的方法,通過聚焦離子束(FIB)銑削和數字圖像相關(DIC)的應力鬆弛試驗,提出的方法為分析非晶態薄膜塗層中的殘餘應力提供了一種簡單的方法。此外,通過奈米壓痕法測定了薄膜的奈米硬度,並利用入射X射線衍射法測定了殘餘應力。
然而,傳統的單面加工方法會產生殘餘應力引起的過大變形。本文利用殘餘應力的M對稱分佈規律,提出了準對稱加工法,利用殘餘應力的M對稱分佈規律,通過材料的對稱去除來減小變形。並將得到的結果與FEM的結果進行了比較。驗證了準對稱加工法在減少殘餘應力引起的變形方面是一種可靠有效的方法。
2. 殘餘應力釋放引起的變形分析
預拉伸的7075鋁合金板,在軋製、熱處理、拉伸過程中產生的初始殘餘應力,需要滿足通用假設。初始殘餘應力是一個自平衡力,在與應力垂直的截面上的結果力和結果力矩都為零;即: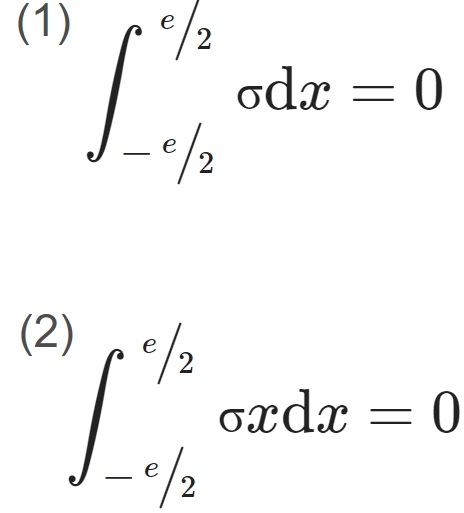
其中,e為薄壁板的厚度,σ為薄壁板的初始殘餘應力。
沿厚度方向平均劃分的各層殘餘應力,如圖1所示。各層厚度為t,各層的平均殘餘應力為.σ1,σ2,...........,σn。
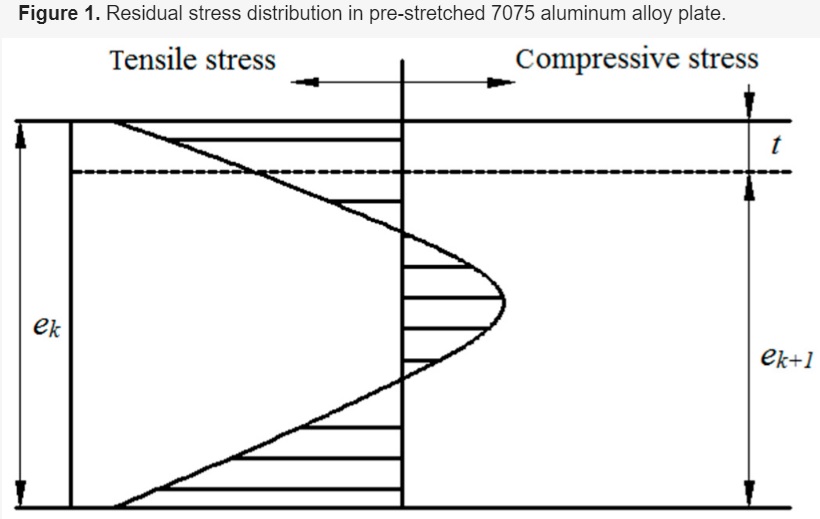
圖1.預拉伸7075鋁合金板的殘餘應力分佈。
當材料在銑削過程中被去除時,初始殘餘應力平衡被打破。為了重新平衡,殘餘應力要重新分佈,同時產生板的變形。工件在銑削前一層和銑削後的曲率關係如下: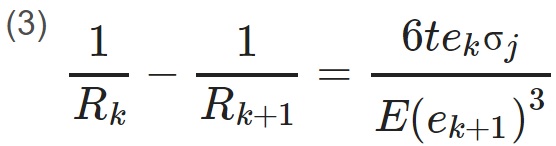
其中,k為層數,Rk和Rk+1為第k層剝離前後的曲率半徑,ek和ek+1為第k層剝離前後的工件厚度,σj為第k層剝離前的應力,E為彈性模量。在此方程中,j=k-1(當k=1時,σj=σ1)。當k=1時,σj代表初始應力。
第k層被剝離後,每層被剝離後的剩餘應力σkr,由第k層被剝離前的應力σim與產生的應力Ski之間的向量運算得到。其計算過程為:
第k層被剝離後,每層被剝離後的剩餘應力σkr,由第k層被剝離前的應力σim與產生的應力Ski之間的向量運算得到。其計算過程為:
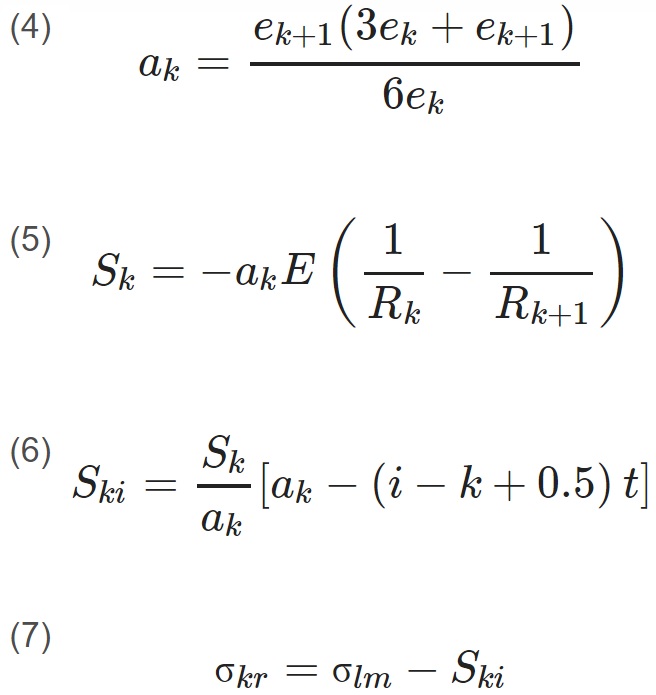
其中l = k - 1,m = r + 1,i = r + k - 1,r = 1,2,...n - k,k≥2。
當k=1時,則:

第k層被剝離後,ak和bk分別為上表面和下表面到中性平面的距離。 Sk和Sk'分別是工件的上表面和下表面恢復到第k層被剝離前的形狀時產生的應力。如圖2所示。
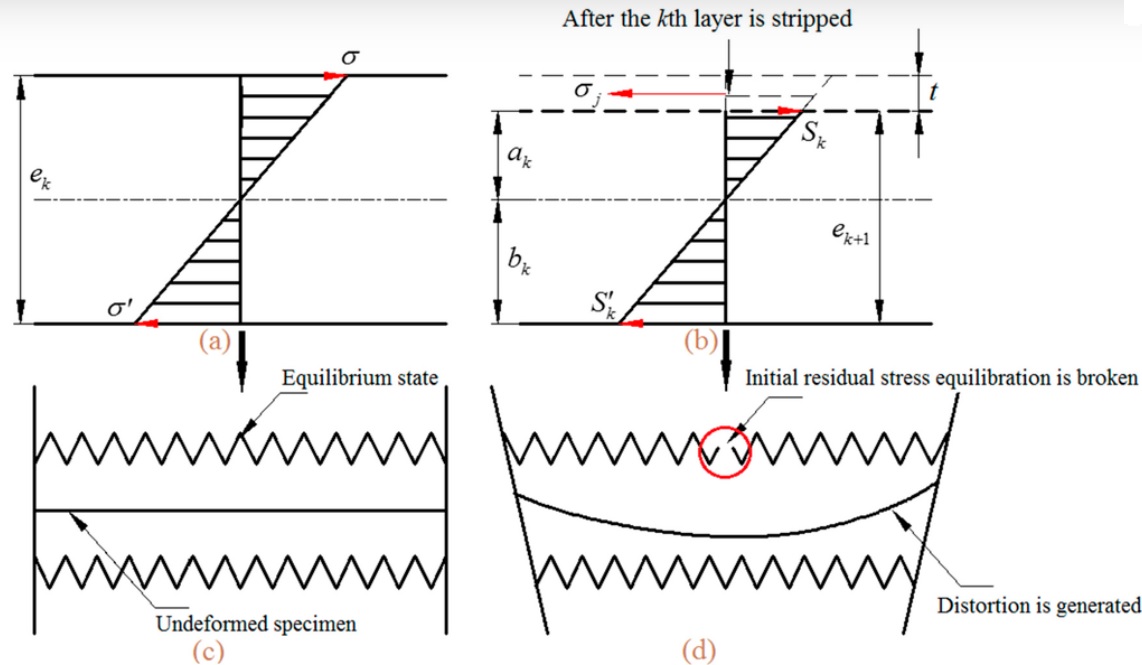
圖2所示。第k層剝離前後試樣的應力狀態和變形情況。 (a)、(c)表示平衡應力狀態和未變形狀態;(b)、(d)表示再平衡應力狀態和變形狀態。
為了更直觀地描述變形原理,對應力狀態和變形條件進行了簡化,如圖2所示。如圖2a、c所示,它們是試樣在第k層剝離前的平衡應力狀態和未變形狀態。此外,圖2b,d所示為第k層剝離後的再平衡應力狀態和變形狀態。在第k層材料被剝離的過程中,殘餘應力釋放和重新分佈,產生了單體構件的變形。
3. 準對稱處理技術分析
切斷技術是一種材料的破壞性測量方法,它是依靠測量材料從試樣中取出後殘餘應力的釋放引起的變形。在切割過程中釋放的應變一般採用電應變片或機械應變片進行測量。如圖3所示,採用切割技術,得到了很好的殘餘應力測量結果,預拉伸7075鋁合金板中殘餘應力的分佈呈現出沿厚度的M對稱分佈(圖4)。殘餘應力分別為表面和中間的拉伸應力和上部和下部的壓縮應力。這種沿厚度方向的拉應力或壓應力分佈不均勻是造成後續變形的主要原因。經過一番調整後,7075鋁合金板的初始殘餘應力只減少了一部分。儘管如此,M對稱分佈規律的趨勢不會再有任何變化。
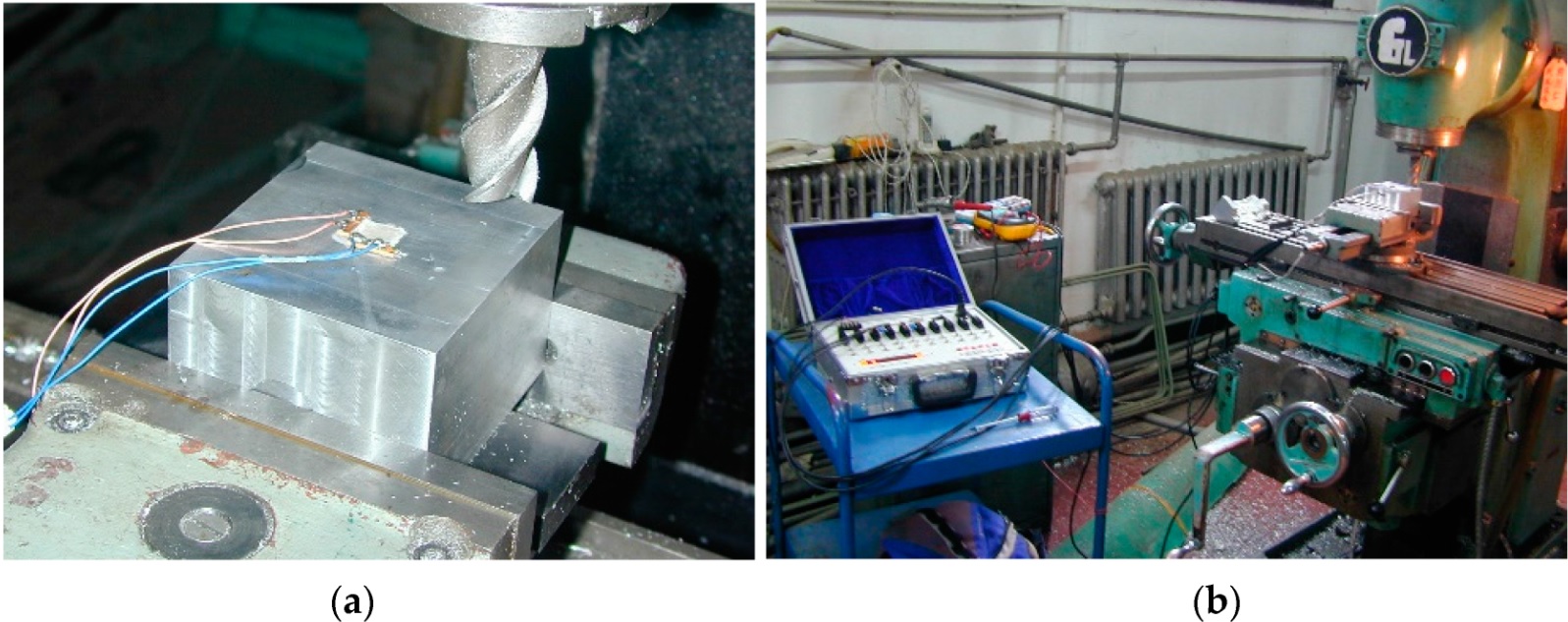
圖3. 用於測量殘餘應力分佈的準無損試驗。 (a) 應力計和導線連接;(b) 測試設備。
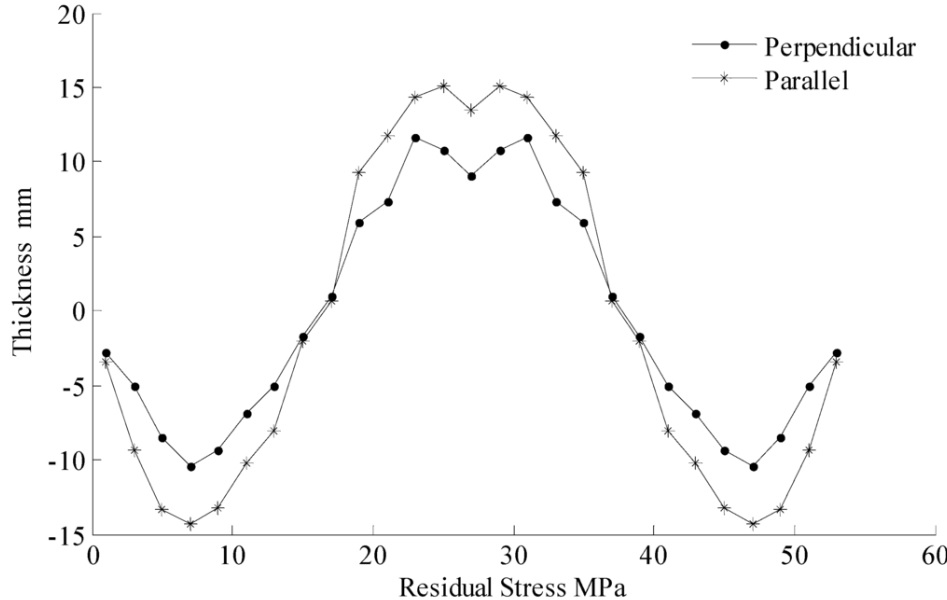
圖4. 初始殘餘應力的M對稱分佈規律。
由於預拉伸7075鋁合金板中殘餘應力的分佈沿厚度呈M型對稱分佈,對稱加工法可以減少初始殘餘應力的釋放和再分佈所引起的變形。對於雙面加工,採用三段式數控加工法,先將上表面加工成小餘量,再將下表面加工成精密尺寸,再將上表面的餘量加工成精密尺寸。在三段式數控加工法的基礎上,發展出準對稱加工法,利用殘餘應力的M對稱分佈規律,通過對稱材料的去除來減少變形。板材兩面多次加工,反覆加工,達到準確的尺寸。
4. 使用FEM的板塊的解決方案
由於切削速度高、切削深度小,在高速機床數控加工過程中生產的預拉伸7075鋁合金板在數控加工過程中的切削力和切削熱可以忽略不計。另外,在數控加工過程中,裝夾方案對加工變形的影響可以忽略不計。因此,本文主要研究航空單體零件在數控銑削過程中殘餘應力的釋放和再分配引起的工件變形。
提供連續問題近似有解的有限元模型是評估加工過程中殘餘應力引起的潛在變形的有力工具。本文應用有限元軟件ANSYS對傳統的單面加工工藝和準對稱加工工藝中的航空單體零件的變形進行了測量,並對其進行了進一步的驗證。
假設預拉伸的7075鋁合金板為彈性塑料材料。其物理規格如表1所示,尺寸為300 mm×200 mm×26 mm。工作台在ANSYS模型中被認為是一個剛體。在本文中,為了更真實地模擬真實的夾具,採用了雙面約束的解法。此外,假定剛度為無窮大,位移為零。同時,忽略了溫度、銑削力、夾持力的影響。
提供連續問題近似有解的有限元模型是評估加工過程中殘餘應力引起的潛在變形的有力工具。本文應用有限元軟件ANSYS對傳統的單面加工工藝和準對稱加工工藝中的航空單體零件的變形進行了測量,並對其進行了進一步的驗證。
假設預拉伸的7075鋁合金板為彈性塑料材料。其物理規格如表1所示,尺寸為300 mm×200 mm×26 mm。工作台在ANSYS模型中被認為是一個剛體。在本文中,為了更真實地模擬真實的夾具,採用了雙面約束的解法。此外,假定剛度為無窮大,位移為零。同時,忽略了溫度、銑削力、夾持力的影響。

在第二節中提到的殘餘應力的M對稱分佈規律的基礎上,我們將相應的殘餘應力值逐層分配到工件中。利用 "生死元法" ,模擬了銑削過程中材料被去除的真實情況。為了達到 "元素死亡" 的效果,ANSYS並沒有實際去除 "死亡" 元素。相反,透過將它們的剛度乘以一個嚴酷的還原係數(默認為10-6),使它們呈現 "死亡狀態"。然後,對殘餘應力釋放引起的變形過程進行了模擬。
在模擬傳統的單面加工工藝時,上表面的材料被一次性加工去除。相比之下,對於準對稱加工工藝,兩個表面的材料是相繼被去除。
為便於描述,採用傳統的單面加工法和準對稱加工法加工的航空單體零件分別標為試樣1和2。
利用上述仿真程序,通過ANSYS計算出銑削後的變形分佈。該分析生成的模型如圖5所示。從圖5a可以看出,試樣1的變形趨勢是兩端向上凸起,中間向下凹陷,而最大變形位於試樣的末端。相反,由圖5b可知,試樣2的變形趨勢是兩端向下凹陷,中間凸起,而最大變形量位於試樣的中部。由變形腎圖可以看出,與傳統的單面加工法相比,採用準對稱加工法,最大變形量減少了約0.28 mm。這一結果在本文第4節關於變形測量的實驗研究中得到了證實。
在模擬傳統的單面加工工藝時,上表面的材料被一次性加工去除。相比之下,對於準對稱加工工藝,兩個表面的材料是相繼被去除。
為便於描述,採用傳統的單面加工法和準對稱加工法加工的航空單體零件分別標為試樣1和2。
利用上述仿真程序,通過ANSYS計算出銑削後的變形分佈。該分析生成的模型如圖5所示。從圖5a可以看出,試樣1的變形趨勢是兩端向上凸起,中間向下凹陷,而最大變形位於試樣的末端。相反,由圖5b可知,試樣2的變形趨勢是兩端向下凹陷,中間凸起,而最大變形量位於試樣的中部。由變形腎圖可以看出,與傳統的單面加工法相比,採用準對稱加工法,最大變形量減少了約0.28 mm。這一結果在本文第4節關於變形測量的實驗研究中得到了證實。
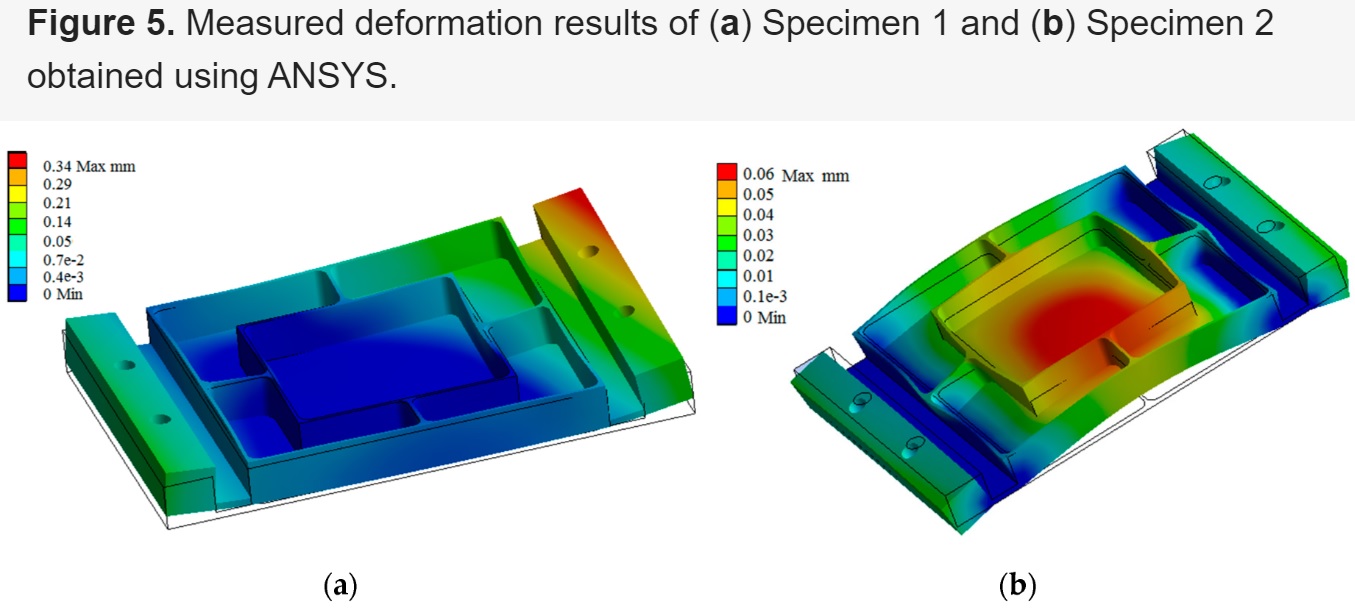
5. 實驗和模擬結果分析
考慮到增硬板的數量和腔體剖面的特點,考慮到實際加工中的航空單體構件的合理簡化。該結構不僅能反映真實的變形情況,而且有利於數據的採集。
在加工過程中,每次的軸向進給量為0.8mm。 3次後,我們將試樣從夾具上取下試樣,測量變形量。試樣2在反面加工過程中的裝夾方案與試樣1相似,而在正面加工過程中的裝夾方案如圖6所示。
在加工過程中,每次的軸向進給量為0.8mm。 3次後,我們將試樣從夾具上取下試樣,測量變形量。試樣2在反面加工過程中的裝夾方案與試樣1相似,而在正面加工過程中的裝夾方案如圖6所示。
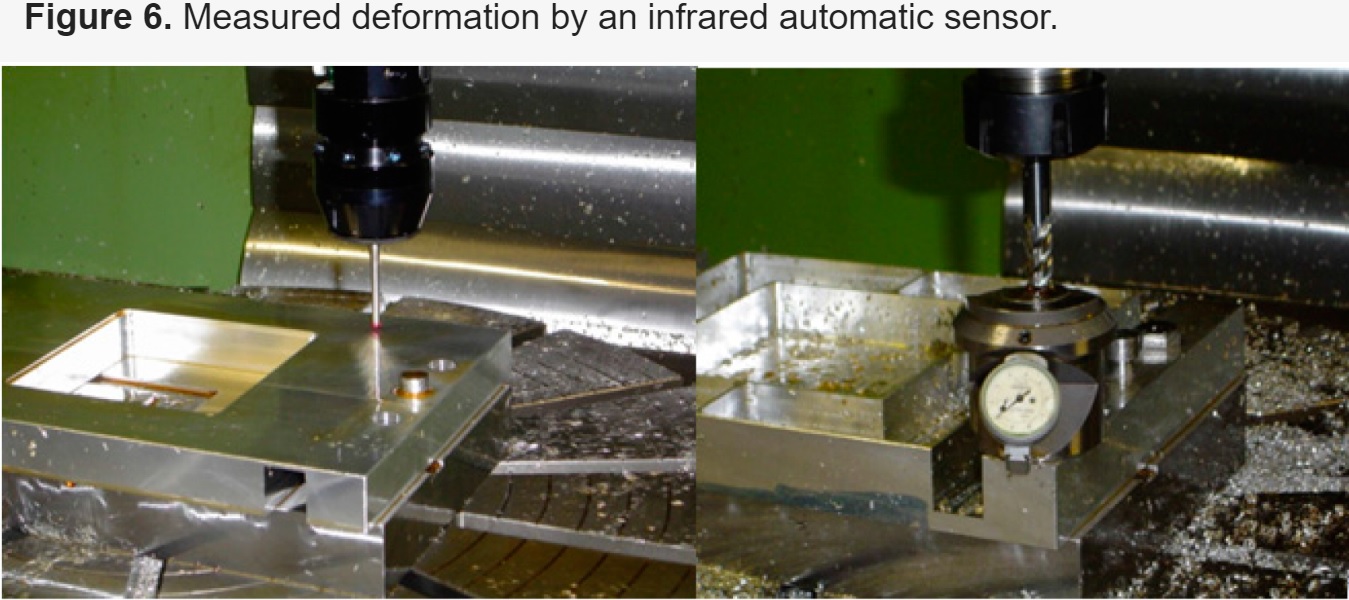
本實驗設計了交錯的內銑形式的加工順序和進給路線。在WF74CH-mikron數控機床(Mikron Group, Boudry, Switzerland)上,正面加工採用φ10 mm的四刃硬質合金銑刀,反面加工採用φ20 mm的兩齒硬質合金端面銑刀。其加工參數如表2所示。圖6是使用MP8紅外自動感應頭測量試樣軸向變形的過程示意圖。
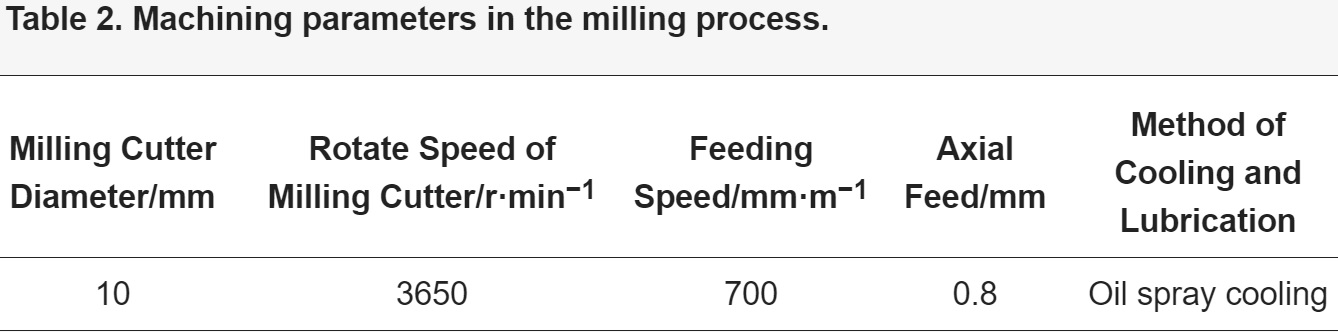
從直觀上看,試樣2的整體變形量比試樣1小。試樣1的最大變形發生在工件的末端。如圖7a所示,0.32mm厚的石蕊插入試樣1的最大變形處,相比之下,試樣2的最大變形發生在試樣的中部。如圖7b所示,試樣2的最大變形處插入0.045毫米厚的石蕊插入試樣2的最大變形處。
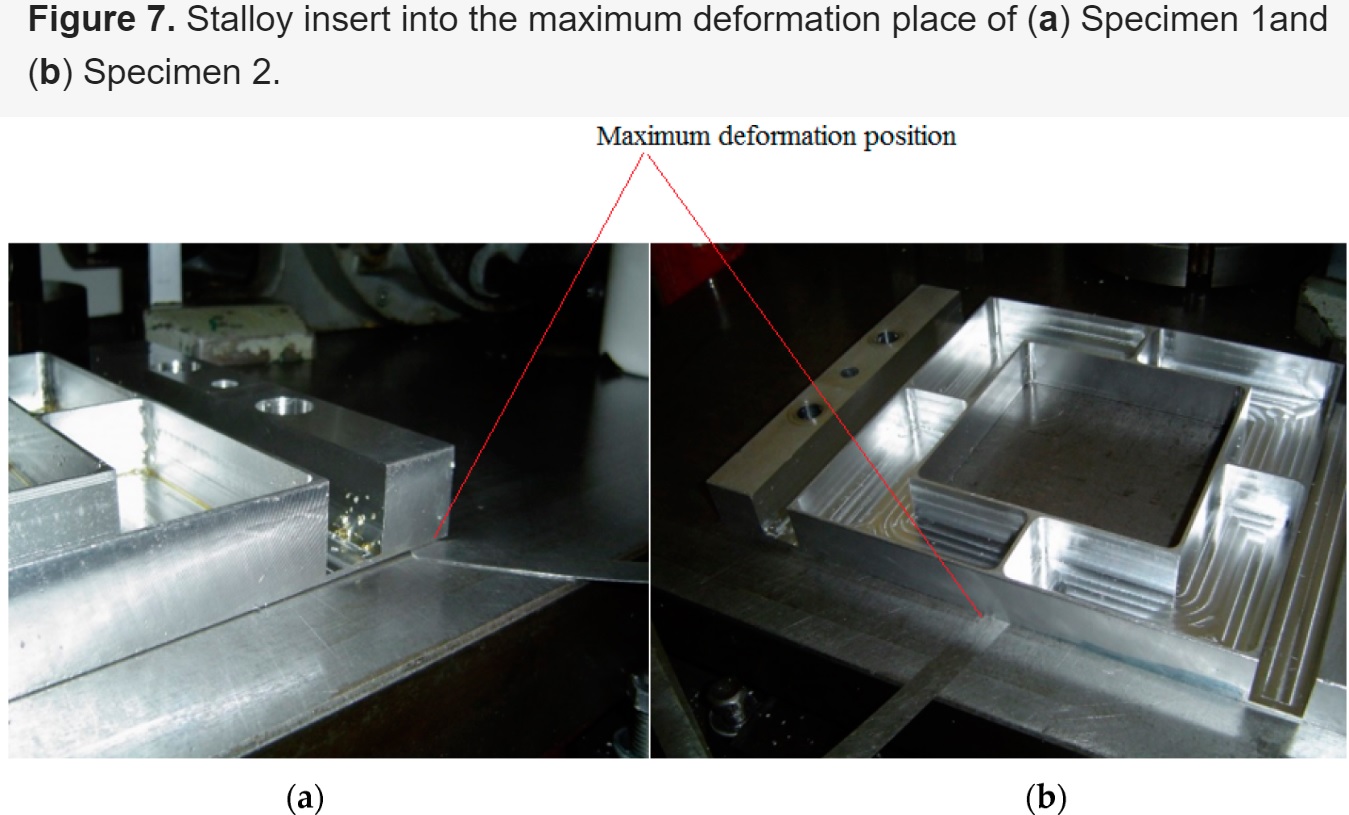
數控加工過程是一個動態變形過程。為便於描述,將試樣1、2沿x坐標分為7個橫截面,即橫截面A-G,7個橫截面均垂直於X-Y平面,如圖8所示。截面A-G的橫截面A-G的斜面X分別為100 mm、70 mm、35 mm、35 mm、0 mm、-35 mm、-70 mm、-100 mm。試樣的尺寸和結構如圖8所示,試樣的尺寸和結構如圖8所示。
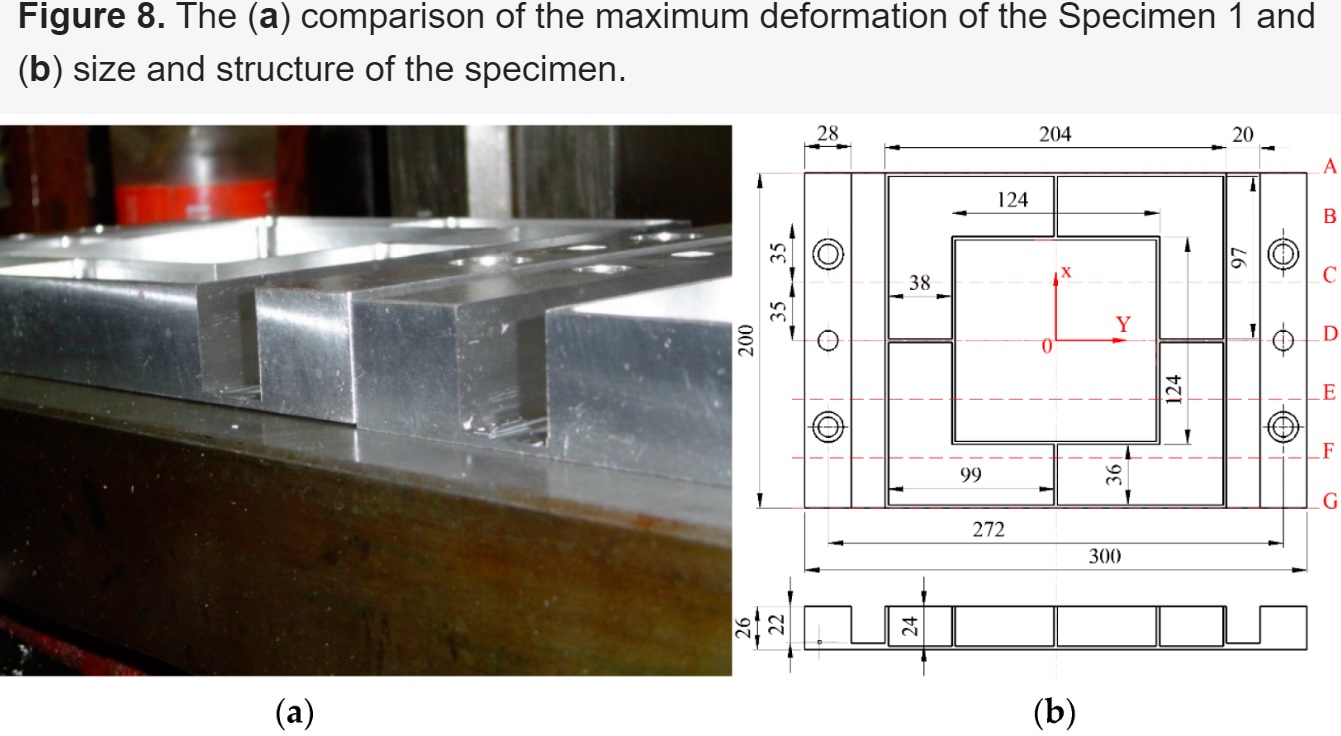
圖8.試樣1的最大變形和(b)試樣的尺寸和結構比較。 (a)試樣1的最大變形比較和(b)試樣的尺寸和結構。
在銑削過程中,材料被逐層去除。圖9為試樣1和2在不同工藝階段的斷面A-G的動態變形曲線。從圖9中可以很容易觀察到最後六層剝離過程中的變形趨勢和數值。
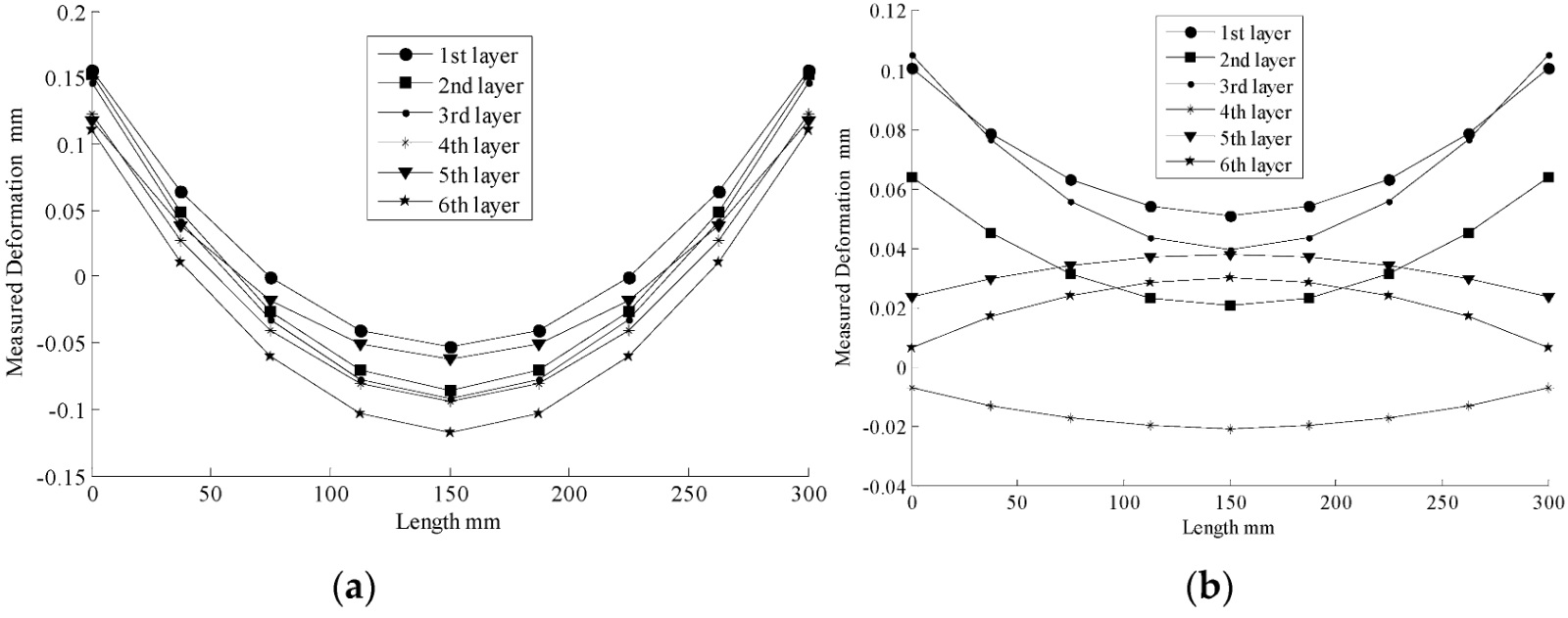
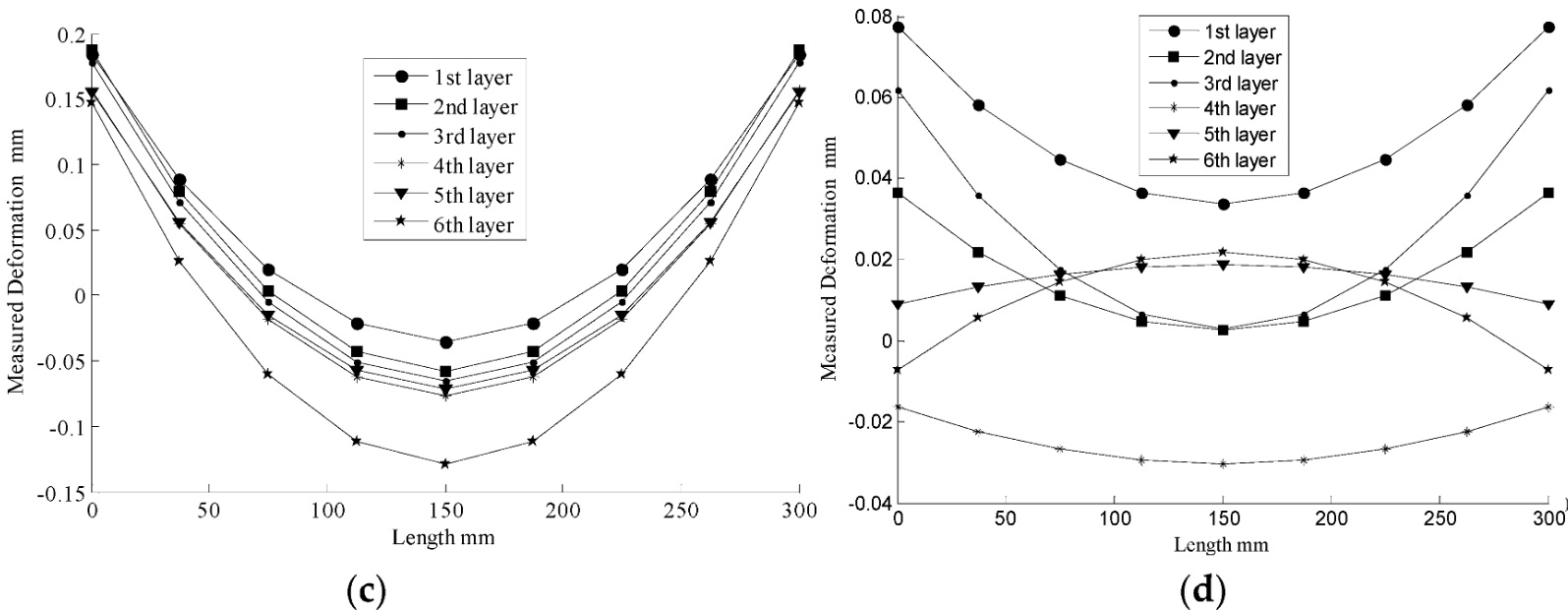
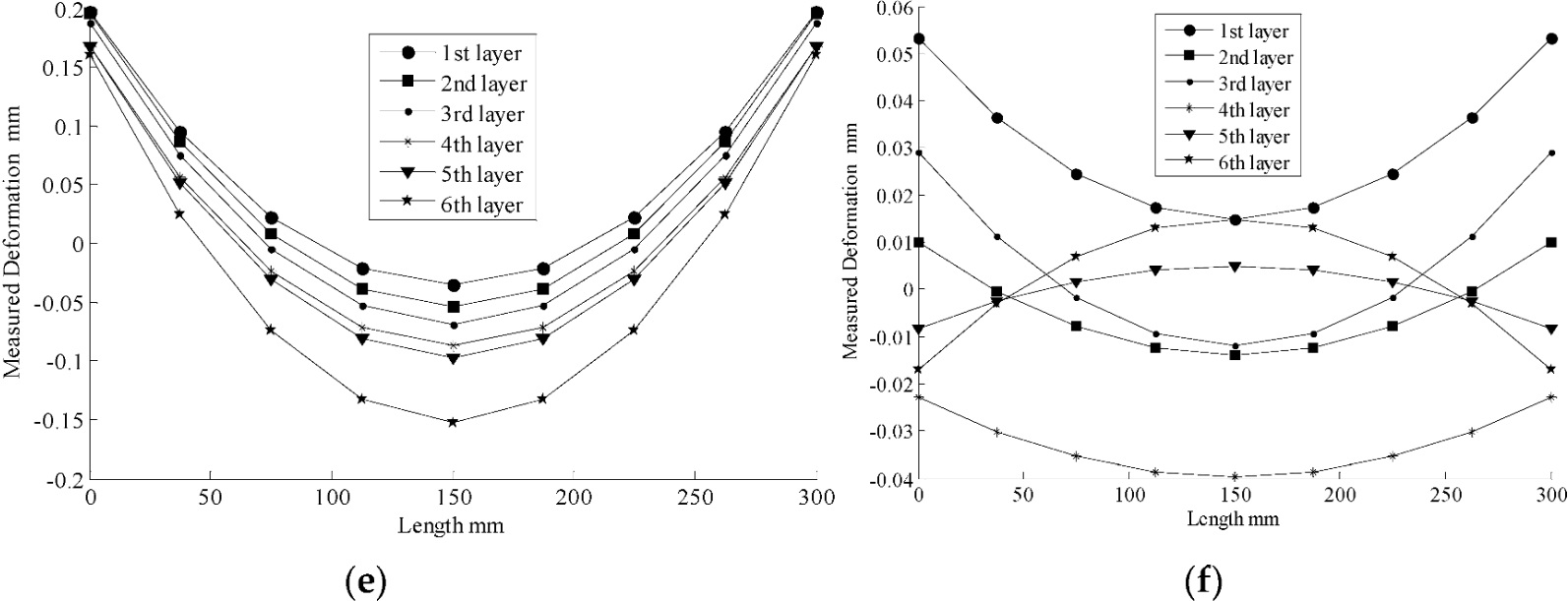
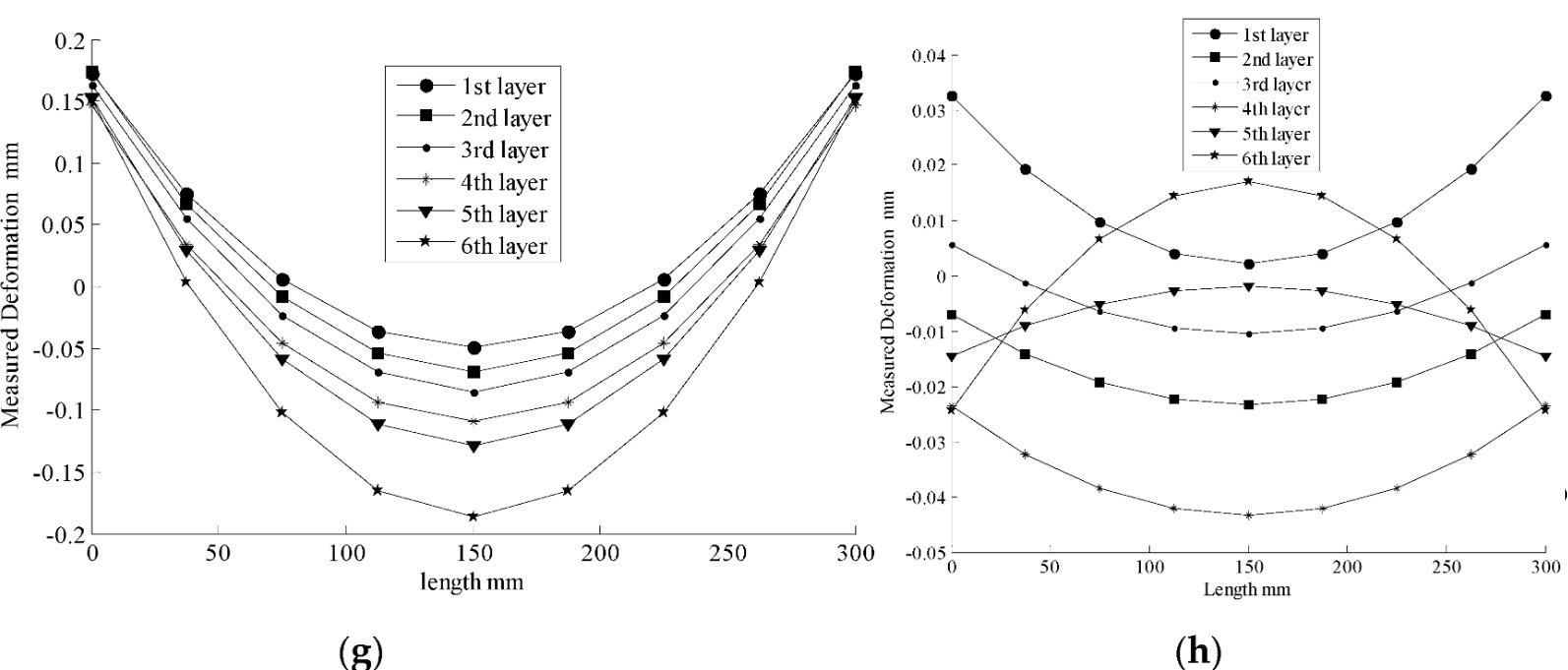
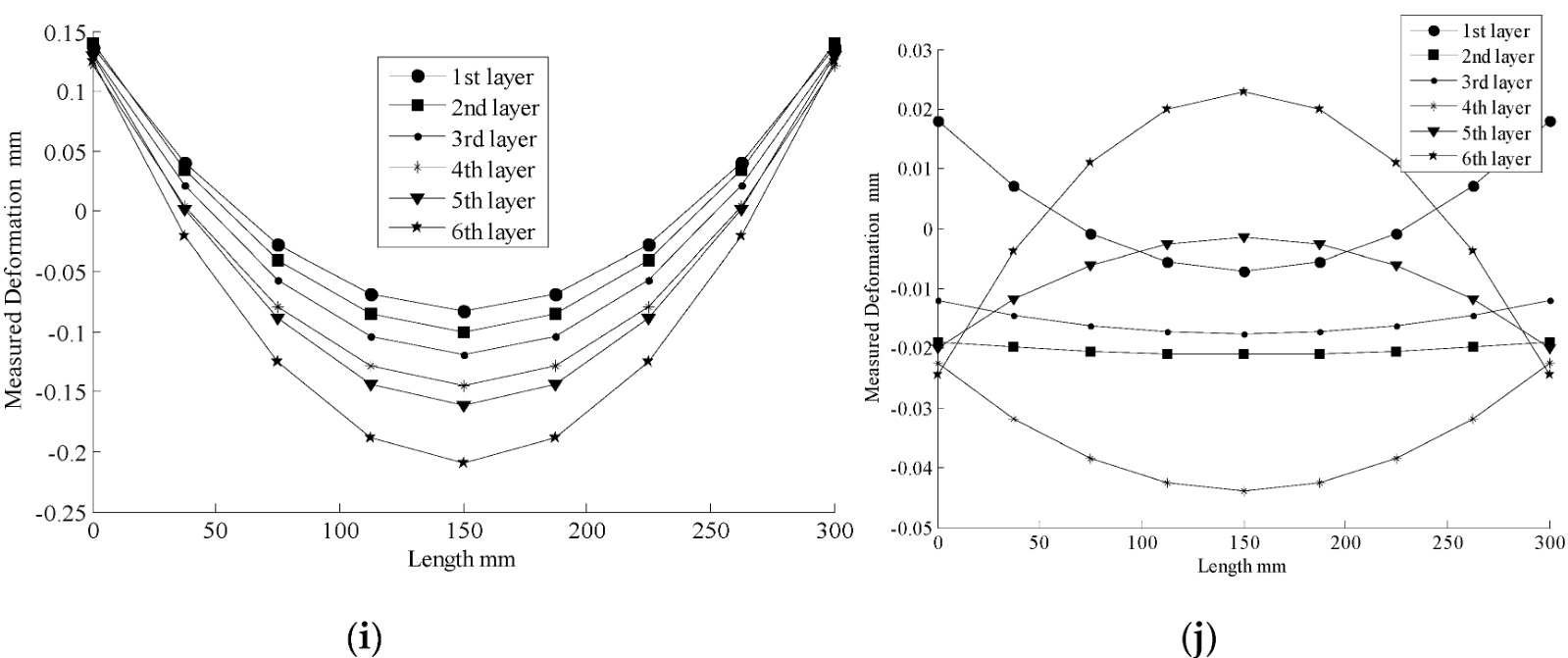
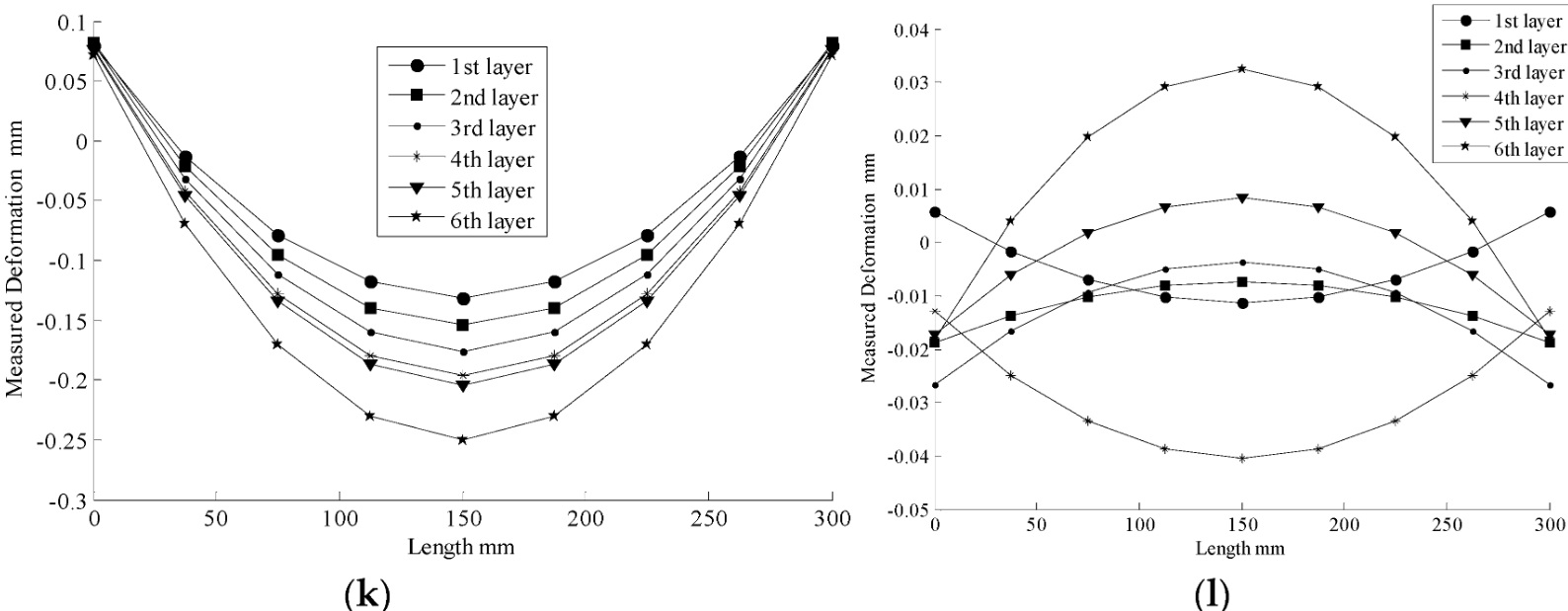
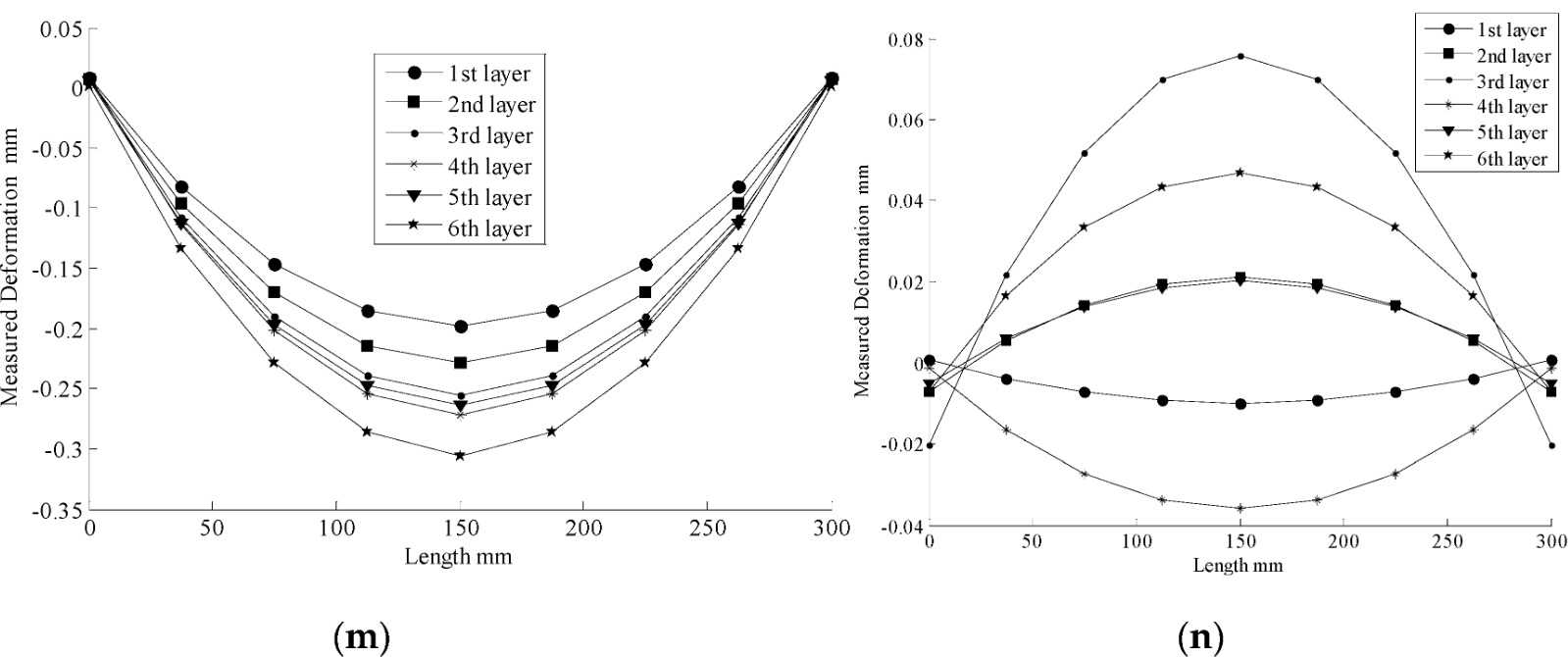
圖9.試樣1和2在不同工藝階段的截面A-G變形曲線 試樣1和試樣2在不同加工階段的橫截面A-G的變形曲線。
(a)試樣1的橫截面A;
(b)試樣2的橫截面A;
(c)試樣1的橫截面B;
(d)試樣2的橫截面B;
(e)試樣1的橫截面C;
(f)試樣2的橫截面C;
(g)試樣1的橫截面D;
(h)試樣2的橫截面D;
(i)試樣1的橫截面E;
(j)試樣2的橫截面E;
(k)試樣1的橫截面F;
(l)試樣2的橫截面F;
(m)試樣1的橫截面G;
(n)試樣2的橫截面G。
從圖9的曲線可以看出,試樣1的橫截面A-G的變形趨勢,在整個加工時間內,兩端均為凸起向上,中間向下凹陷,而最大的變形發生在試樣的末端。同時,在材料被逐層去除的過程中,變形值增大。相比較而言,圖9的曲線也表明,試樣2的橫截面AG的變形趨勢是兩端向下凹陷,中間凸起,或者兩端向上凸起,中間向下凹陷,這是一個對稱的、反覆的過程。特別是,在這個過程中,變形值的增大和減小是交替進行的。此外,最大變形發生在試樣末端。
傳統的單面加工法,殘餘應力的釋放和再分佈始終發生在試樣的一側,殘餘應力的釋放和再分佈是在試樣的一側,殘餘應力引起的變形是累積的。相比之下,準對稱加工法,殘餘應力的釋放和再分佈是在試樣的兩邊交替發生。殘餘應力引起的變形被抵消了。
同時,試樣1和2的橫截面A-G的最大變形值如圖9所示。其比較結果如表3所示。
傳統的單面加工法,殘餘應力的釋放和再分佈始終發生在試樣的一側,殘餘應力的釋放和再分佈是在試樣的一側,殘餘應力引起的變形是累積的。相比之下,準對稱加工法,殘餘應力的釋放和再分佈是在試樣的兩邊交替發生。殘餘應力引起的變形被抵消了。
同時,試樣1和2的橫截面A-G的最大變形值如圖9所示。其比較結果如表3所示。
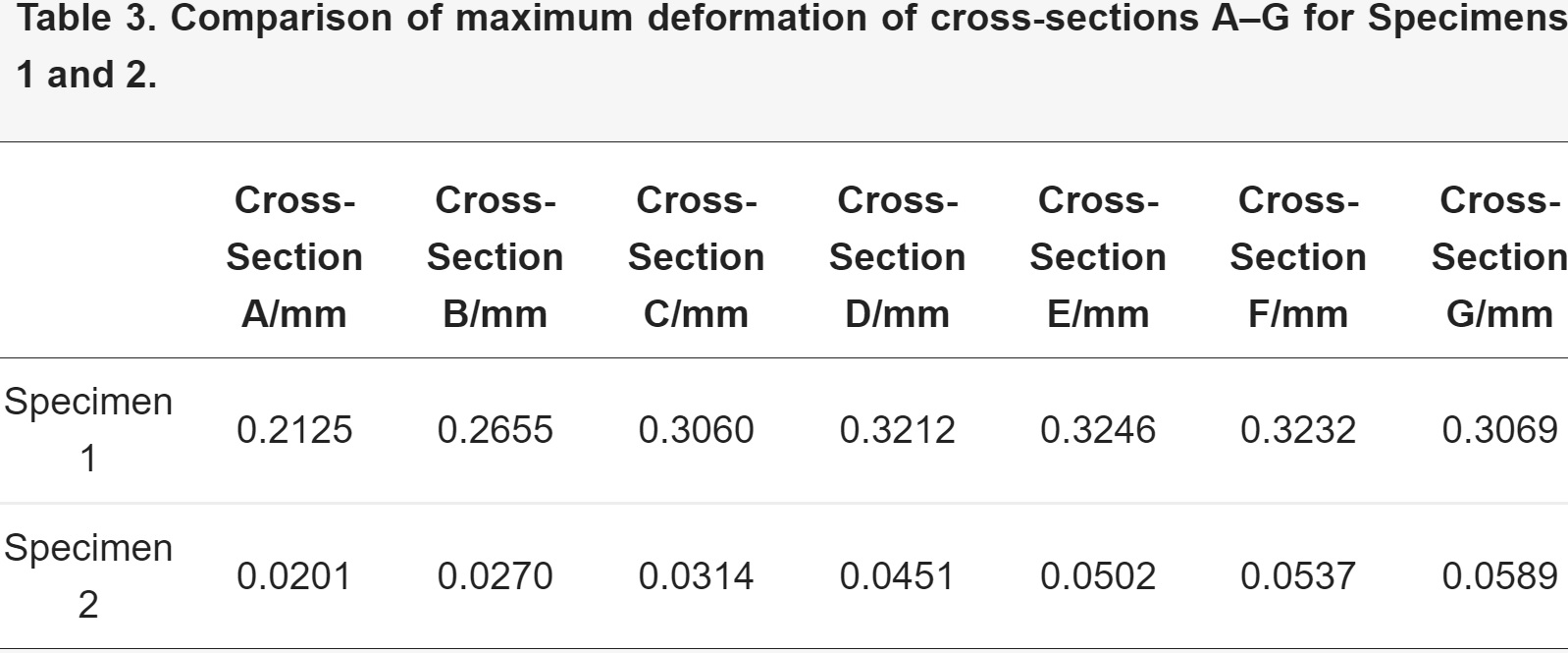
此外,根據試樣1的結果除以試樣2的結果,分別比較橫截面A-G的最大變形量。最大變形量的百分比依次為9.459%、10.17%、10.17%、10.26%、14.04%、15.47%、16.62%、19.19%。顯然,試樣1的最大變形量遠大於試樣2的最大變形量,而試樣2的最大變形量百分比僅為19.19%。由此可見,準對稱加工法能有效地減少殘餘應力引起的單片薄壁構件的變形。
圖10為傳統單面加工工藝和準對稱加工工藝中航空單體零件截面D的實驗和仿真的實測變形結果和變形趨勢圖。變化曲線表示了有限元模型的實測變形結果與實驗的關係。圖10所示的原始數據曲線和二次方程擬合曲線都是適合的,因此表明有限元的結果與實驗結果是一致的。這些結果證實了FEM和實驗在銑削過程中表現出較高的精度。
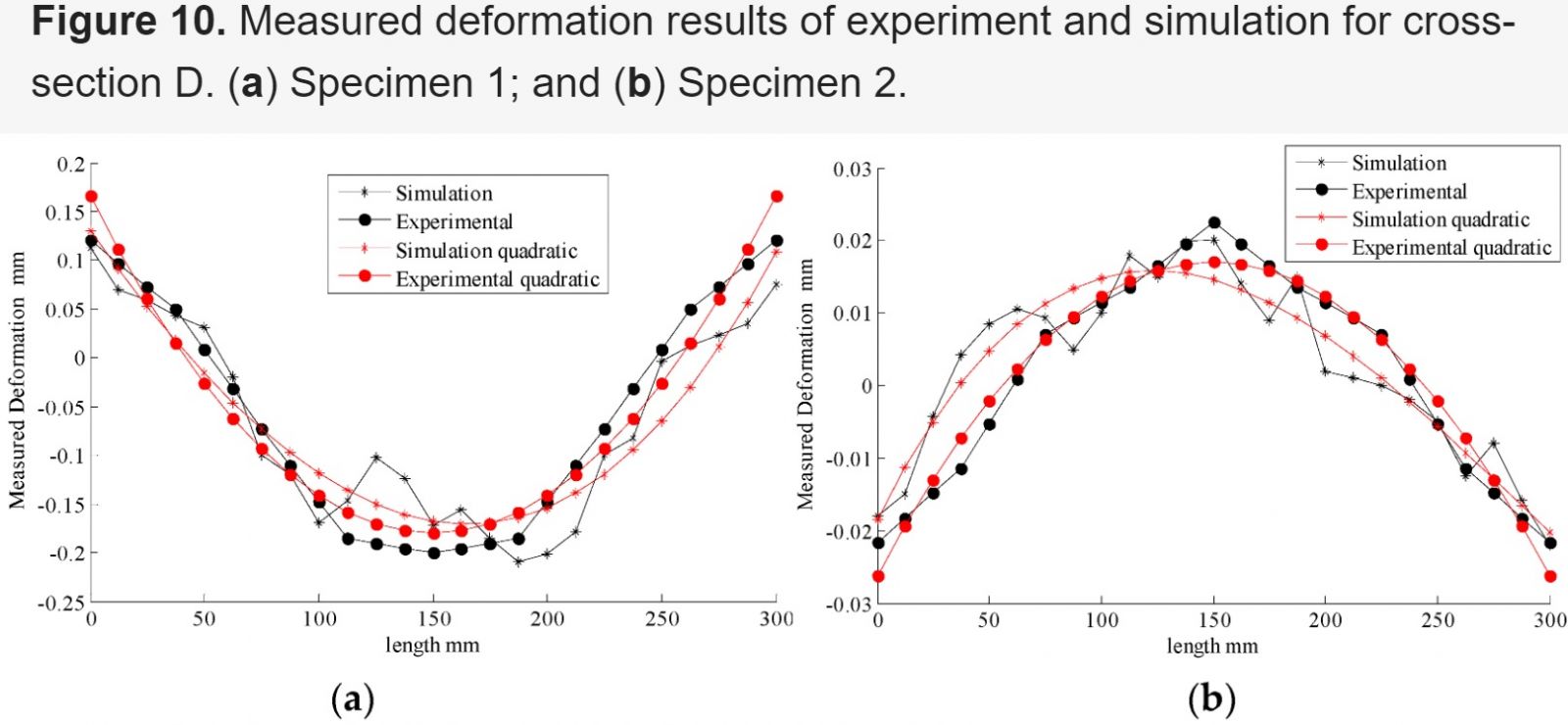
圖10為傳統單面加工工藝和準對稱加工工藝中航空單體零件截面D的實驗和仿真的實測變形結果和變形趨勢圖。變化曲線表示了有限元模型的實測變形結果與實驗的關係。圖10所示的原始數據曲線和二次方程擬合曲線都是適合的,因此表明有限元的結果與實驗結果是一致的。這些結果證實了FEM和實驗在銑削過程中表現出較高的精度。
對於試樣1,實驗的最大變形為0.32毫米,而模擬的最大變形為0.34毫米。相比之下,實驗的最大變形為0.045 mm,模擬的最大變形為0.06 mm。儘管與模擬和實驗相比,結果略有偏差,但結果非常相似。儘管如此,模擬結果仍不如實驗結果,所有結果均在允許誤差範圍內。造成這種偏差的主要原因如下:
1. FDM基於近似法,便於用有限差分方程代替微分方程。因此,這種計算方法不可避免地會出現系統誤差。
2. 在實際應用中,仿真和實驗中的邊界條件不盡相同。理想條件有待於確定。
3. 仿真與實驗之間的殘餘應力狀態不一致。 FEM模擬殘餘應力釋放和再分佈的真實狀態,不可能完全模擬出殘餘應力的真實狀態。雖然有一些客觀原因,導致了必然的誤差,但大部分誤差都在允許的誤差範圍內。
6. 結論
使用準對稱加工法的最大變形值是傳統單面加工法的20%以內。這一結果表明,準對稱加工法對減少殘餘應力引起的單片薄壁構件的變形是可行的,也是有效的。誤差較低,修改有限元和實驗對比結果的誤差大多在10%以內。這些結果證實了準對稱加工法是一種可靠、合適的釋放變形的方法。
在準對稱加工過程中,試樣2的變形趨勢是兩端向下凹陷,中間凸起,而最大的變形發生在試樣的中部。