飛機結構件製造技術回顧
2020-05-14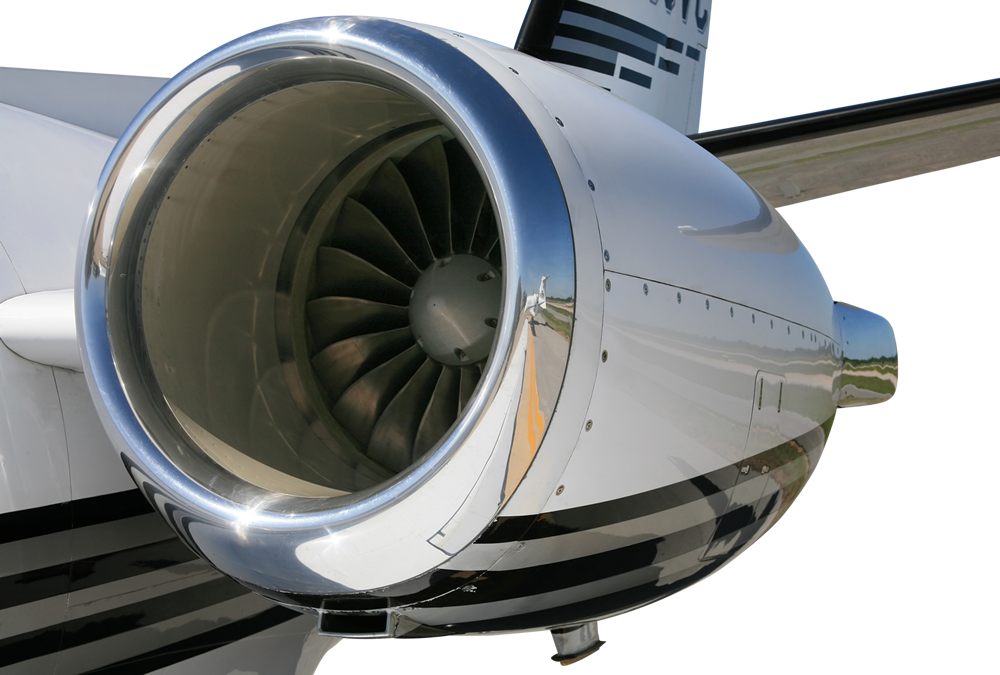
摘要
本文提出了飛機結構件的數字化設計製造技術,由於飛機結構件的規模化、集成化、複雜化,對製造精度要求較高,這對製造技術提出了挑戰。在飛機結構件製造過程中應用數字化技術和智能化技術,構建飛機結構件設計製造協同平台,實現飛機結構件的高效、優質、低成本、環保、柔性設計製造,對提高企業核心競爭力具有重要意義。
1. 導言
作為配備製造業的典型代表,航空製造業是反映一個國家綜合國力和整體產業水平的戰略性高新技術產業。也是中國製造2025的十大領域之一。高效率、高質量是飛機結構件設計和製造的重要條件,是保證飛機製造性能和進步的重要條件。這不僅要求將數字化技術的結合應用到飛機結構件設計和製造過程中去,還需要更加注重設計與製造的協同,即產品目標的設定將驅動程序,實時、分散的設計信息和分散的設計信息和生產信息的收集、優化和通過智能控制系統的集成,更加優化了產品設計和製造過程。為了更好的服務於產品的設計和製造的全過程。因此,如何將飛機結構件的設計過程與製造過程相融合,構建基於智能技術的飛機結構件設計製造體系,是我國裝備製造業的迫切需求。以智能製造為主導的第四次工業革命(工業4.0)自2011年德國漢諾威博覽會上首次提出以來,其他國家也提出了相應的智能製造發展規劃,如美國振興製造戰略、日本製造白皮書、中國製造2025等,可見智能製造正在成為新一輪產業競爭的高地。引起了世界的高度重視。飛機結構件是一種典型的小批量、多品種的生產模式,不利於知識的積累和再利用。因此,在飛機結構件的設計和製造過程中應用智能化技術,具有重要的現實意義。
2. 研究狀況
美國洛克希德-馬丁公司在JSF項目中使用產品生命週期管理(PLM)軟件作為集成平台和重組公司流程的應用數字化設計和製造管理,並給予合作夥伴充分發揮他們的最佳能力。JSF飛機的設計時間縮短50%,生產時間縮短66%。裝配工具減少90%,分立件減少90%,離散件減少90%。設計、製造和維護費用減少了50%。波音公司在新生代戰機中空間飛行器,通過應用MBD/MBI(型號:基於定義和模型的操作指令)減少裝配時間57%,並實現以下技術突破:設計三維轉型為三維製造數據技術,將三維產品和工藝信息傳輸給製造單位工人,製造作業現場的數字化數據可進行採集和反饋,並對數字化質量數據和達標文件進行管理。
國內航空製造企業緊跟世界先進航空製造技術和企業發展的步伐,通過近年來的持續投入,已實現了數字化設計的數字化產品和製造工藝為基礎的模式,關鍵零部件製造基本實現了數控加工工藝的加工過程。國內先進航空製造企業已初步建成數字化車間環境,開發了一系列業務系統和軟件工具,實現了製造過程的數字化控制。國內層面已基本接近國際航空製造企業的先進水平,具備了從數字化到自動化、智能製造的發展基礎。但與國外先進水平相比,從技術發展趨勢來看,現有的飛機結構件加工車間在集成化、柔性化、智能化方面還處於初級階段,主要依靠單一設備的先進性和自動化來實現飛機結構件的高效製造。
3. 飛機結構件製造的設計技術
基於MBD的全三維設計技術已經逐漸廣泛應用,改變了國內飛機產品的研製方式,縮短了國內飛機產品的研製週期,在國內飛機設計過程中,基於MBD的全三維設計技術已經逐漸得到應用。但是,飛機結構件的設計過程中注重功能性,缺乏對其製造工藝的考慮,導致設計過程和製造工藝斷裂,增加了製造難度和生產成本。而且飛機結構件是典型的小批量、多品種的生產模式,難以通過大量的生產模式進行知識的積累和復用,因此,建立飛機結構件設計製造知識的獲取、復用和集成技術,以打破設計與製造之間的信息壁壘。在飛機結構件的設計過程中,我們需要考慮可製造性,實現以製造為導向的智能設計。面向製造型設計的核心在於知識的獲取、表達和建模技術。
3.1. 製造工藝知識的獲取和表達
飛機結構件的加工工藝是複雜的。如何準確、完整地掌握和表達飛機結構件的加工工藝知識,對促進飛機結構件設計工藝的智能化具有重要意義。雖然飛機結構件的加工工藝知識複雜多樣。但大量的工藝知識都與零件的特徵技術有關。特徵技術作為數字化製造的一種手段,在信息集成中發揮著重要作用。在傳統研究和商業軟件的應用中,特徵技術在CAD/CAM領域獲得廣泛的應用。特別是在CAM領域得到了廣泛的認可,它被認為可以有效地提高編程的過程效率,有利於知識的集成和共享,提高零件的製造效率和質量等。但如何使特徵技術作為連接設計過程和製造過程的樞紐,值得探討和關注。特徵是一組幾何體,具有特定的屬性和相互關係,其中包括對零件形狀、工藝和功能信息的一般描述。這是整合設計與製造信息的最佳載體,能有效提高產品設計自動化水平。其特點是可以將信息傳遞到下游製造過程中,以設計過程和製造過程為樞紐,溝通設計過程和製造過程。通過建立基於特徵的流程知識獲取和表徵模型,可以為設計過程建立特徵知識庫,實現設計製造過程中的知識共享,為面向製造的智能設計提供基礎。
3.2. 基於特徵的三維模型的參數化設計
飛機產業是代表著一個國家工業設計製造和裝配水平的各種高科技集成體。隨著全球經濟的趨緩,製造業的發展進入困難時期。企業需要改變以生產任務為中心,不注重生產成本控制的傳統模式。尤其是飛機結構件,材料成本高。而且加工過程較長。設計不合理很容易造成產品的質量難以控制,增加了產品的製造難度和生產成本。因此,迫切需要構建快速、高質量的飛機結構件設計方法,以提升飛機製造業的核心競爭力。
雖然飛機結構件的外部結構複雜。但在設計和製造過程中的特徵技術被廣泛應用。飛機結構件的特徵類型可分為槽型特徵、肋型特徵、孔型特徵和輪廓特徵,我們將其定義為幾何特徵。飛機結構件不僅在設計過程中需要定義零件的幾何形狀。但在設計過程中還需要定義參數信息,包括零件的工藝和材料及精度等參數信息,我們將其定義為工藝特徵,它是加工和檢驗的重要依據。在飛機結構件的設計過程中,基於特徵的參數化建模基於特徵的技術和工藝知識解釋器,結合基於MBD的全三維建模思想,將其應用於零件的幾何形狀的構建和工藝特徵的標註,使加工工藝知識充分融入到飛機結構件中。使設計過程成為製造過程,實現了飛機結構件的智能化設計。
雖然飛機結構件的外部結構複雜。但在設計和製造過程中的特徵技術被廣泛應用。飛機結構件的特徵類型可分為槽型特徵、肋型特徵、孔型特徵和輪廓特徵,我們將其定義為幾何特徵。飛機結構件不僅在設計過程中需要定義零件的幾何形狀。但在設計過程中還需要定義參數信息,包括零件的工藝和材料及精度等參數信息,我們將其定義為工藝特徵,它是加工和檢驗的重要依據。在飛機結構件的設計過程中,基於特徵的參數化建模基於特徵的技術和工藝知識解釋器,結合基於MBD的全三維建模思想,將其應用於零件的幾何形狀的構建和工藝特徵的標註,使加工工藝知識充分融入到飛機結構件中。使設計過程成為製造過程,實現了飛機結構件的智能化設計。
4. 航空器結構件高效數字化加工的關鍵技術
現代飛機結構件採用了大量的一體化設計模式。其結構複雜,功能類型多樣,導致製造難度較大。經過多年的技術研究和應用,飛機結構件實現了數字化製造工藝。但與國外先進技術相比,還存在以下問題。如大型飛機結構件的數控編程週期較長,質量問題。程序化程度較低。在加工中,容易產生變形。變形控制難度大。而且加工效率不高。零件的質量難以控制。總之,飛機結構件的加工還是要靠人員的經驗。在這個過程中仍然需要持續的人工干預和控制,這 阻礙了自動化的實施。因此,發展飛機結構件製造過程中的自動化、智能化加工技術的研究,實現飛機結構件的柔性製造,對提高飛機製造業的技術水平具有重要意義。
4.1. 綜合流程編程平台
飛機結構件工藝編程的效率和質量已成為制約飛機結構件製造工藝週期的主要瓶頸之一。李穎光等人提出了面向用戶訂製的複雜飛機結構件加工特徵建模方法和基於整體屬性鄰接圖的加工特徵識別技術。同時,他們開發了一套基於功能的智能編程系統,實現了複雜飛機結構件的智能編程。系統可實現對飛機結構件加工特徵的自動識別和飛機結構件加工工藝規劃和數控程序的自動編制,配合工藝知識數據庫、切削參數數據庫和製造資源數據庫平台,為飛機結構件編程過程提供完整的解決方案。典型特徵識別率高達95%以上,編程效率提高3倍以上。隨著系統功能的擴展,該系統將成為集工藝檢驗、特徵識別和工藝規劃、刀具路徑生成、後處理、仿真和優化為一體的綜合性平台,實現對飛機結構件的整個編程過程的優化。同時,隨著工藝知識數據庫、切削參數數據庫和製造資源數據庫的不斷改進和完善,未來飛機結構件編程任務將全部由計算機完成。工程師也將從繁重的工藝編程任務中解放出來,進行工藝技術研究和工藝知識的維護和更新。
4.2. 數控設備的自動性能評價和安全技術
數控機床被稱為行業內的 "機床之母"。它的性能和運行狀態將直接影響到飛機結構件的加工質量和加工時間。特別是在無人工干預的要求下,對機床的精度和性能及故障的實時預測評估和分析處理提出了更高的要求。機床的精度是飛機結構件加工質量的重要保證。傳統的機床精度評定方法存在以下問題:一是檢測時間長。需要對大量的數據進行分析。其二是對需要人工干預的機床精度無法實現實時在線補償。德國DST機床公司開發了一套機床精度計算機輔助診斷系統(SQS)。該系統可以自動檢測並快速補償機床的空間精度和五軸聯動精度,並通過運行一套預先設定的標準測試程序,對補償後的空間精度進行計算和評估。主要是通過光學原理檢測空間誤差和R-TEST檢測旋轉頭的姿態誤差。 DST公司研發的這套機床精度自動化系統,可以在30分鐘內完成機床精度的自動檢測和補償。在智能製造車間,實現了對機床精度的實時跟蹤。與車間的信息系統進行整合,可以即時更新製造資源數據庫,為飛機結構件製造過程中的機床選型提供依據。
數控機床本身就是一個非常複雜的系統。如果能及時預測機床的故障並進行預維護,將大大提高機床的利用率。先進製造技術和信息技術與數字化車間環境下的智能技術深度融合,實現機床的智能化預測與維護。通過傳感器網絡系統,實現了對機床設備的振動、電流、噪聲和機械電氣、機械特徵信號的實時採集。並實現其自我感知的狀態和環境。傳感信號通過工業以太網傳輸到控制系統。控制系統根據接收到的信號,在專家知識庫的支持下,基於神經元網絡等推理算法,對關鍵功能部件的健康狀態給出預警和決策。機床接收到決策信息後,機床自適應地調整自身運行方式或由維護工程師維護,減少因機床故障造成的產品質量事故和閉鎖。
數控機床本身就是一個非常複雜的系統。如果能及時預測機床的故障並進行預維護,將大大提高機床的利用率。先進製造技術和信息技術與數字化車間環境下的智能技術深度融合,實現機床的智能化預測與維護。通過傳感器網絡系統,實現了對機床設備的振動、電流、噪聲和機械電氣、機械特徵信號的實時採集。並實現其自我感知的狀態和環境。傳感信號通過工業以太網傳輸到控制系統。控制系統根據接收到的信號,在專家知識庫的支持下,基於神經元網絡等推理算法,對關鍵功能部件的健康狀態給出預警和決策。機床接收到決策信息後,機床自適應地調整自身運行方式或由維護工程師維護,減少因機床故障造成的產品質量事故和閉鎖。
4.3. 加工過程的自適應控制技術
飛機結構件的加工質量和加工效率的高低,不僅與機床和數控碼有關。而是與刀具和夾具以及測量和變形控制技術等有關。自適應夾持夾具及加工過程實時監控和加工與測量一體化技術將是未來智能柔性生產線中智能加工工廠的重要組成部分。
通過對切削力和工件剛度的實時監控,根據加工過程中的特點,自適應夾具可以根據工件和切削力的變化,調整固定狀態和力的匹配,防止工件變形。
同時,為了適應無人工干預的柔性生產模式,根據飛機結構件的結構特點,對零件進行了分類劃分。同時,考慮到製造工藝和結構尺寸的特點,採用標準快速夾具模型實現不同規格的零件,並在不同的機床上進行專用夾具加工,以適應飛機結構件數字化車間自動化生產模式。
目前,國外已開發出多套商業化的監控軟件。但僅基於監控信號的加工狀態識別。複雜飛機結構件的加工過程中,容易受到加工狀態波動的影響而產生頻繁的誤報,影響正常生產。因此,我們有必要對遠程的監控和控制數控系統技術。將主軸切削力實時監控,結合工藝信息對加工狀態進行識別。一旦發現加工狀態異常,應立即控制機床停止加工,防止因刀具磨損破損、刀具路徑錯誤等引起的零件質量問題,提高加工狀態的識別精度。
加工與測量一體化技術主要應用於零件裝夾加工或完成單步或部分工序加工。通過檢測系統內置的機床檢測系統對零件的空間位置和特徵尺寸進行測量。然後根據測量數據的誤差分佈分析,重新調整機床坐標系和零件的數控碼,以保證設計的尺寸要求,進行進一步的加工。保證了柔性生產線中零件的加工質量,減少了零件的裝夾、刀具與零件的定位、零件的變形等這些因素造成的加工誤差。
通過對切削力和工件剛度的實時監控,根據加工過程中的特點,自適應夾具可以根據工件和切削力的變化,調整固定狀態和力的匹配,防止工件變形。
同時,為了適應無人工干預的柔性生產模式,根據飛機結構件的結構特點,對零件進行了分類劃分。同時,考慮到製造工藝和結構尺寸的特點,採用標準快速夾具模型實現不同規格的零件,並在不同的機床上進行專用夾具加工,以適應飛機結構件數字化車間自動化生產模式。
目前,國外已開發出多套商業化的監控軟件。但僅基於監控信號的加工狀態識別。複雜飛機結構件的加工過程中,容易受到加工狀態波動的影響而產生頻繁的誤報,影響正常生產。因此,我們有必要對遠程的監控和控制數控系統技術。將主軸切削力實時監控,結合工藝信息對加工狀態進行識別。一旦發現加工狀態異常,應立即控制機床停止加工,防止因刀具磨損破損、刀具路徑錯誤等引起的零件質量問題,提高加工狀態的識別精度。
加工與測量一體化技術主要應用於零件裝夾加工或完成單步或部分工序加工。通過檢測系統內置的機床檢測系統對零件的空間位置和特徵尺寸進行測量。然後根據測量數據的誤差分佈分析,重新調整機床坐標系和零件的數控碼,以保證設計的尺寸要求,進行進一步的加工。保證了柔性生產線中零件的加工質量,減少了零件的裝夾、刀具與零件的定位、零件的變形等這些因素造成的加工誤差。
4.4. 製造過程中的智能生產管理與控制
智能化生產管理控制中心將是未來飛機結構件加工廠的大腦,實現集數據採集、分析、決策等功能於一體,負責廠內所有資源的統一調配和管理。在數字化生產管理系統的支持下,飛機結構件數控製造過程控制、作業調度、現場管理和製造資源管理正在實現。在此基礎上,應建立一個與實際工廠車間實時運行的虛擬工廠。生產調度需要在虛擬工廠中進行模擬,以確定調度的有效性。同時,將實際工廠的運行數據傳輸到智能生產控制中心,驅動虛擬工廠的運行。智能生產控制中心會根據虛擬工廠模擬的反饋數據做決策,實現對實際工廠的調度控制。智能化生產管理控制中心有效地延伸了人腦的功能,對實現飛機結構件的無人工干預或少人工干預製造有很大的作用。
5. 設計和製造飛機結構件的協作平台
現代飛機研發一般採用多廠家、遠程協作開發的模式。小批量、多品種飛機結構件的生產模式。特別是在研製生產過程中伴隨著大量的設計變更,需要製造工藝快速響應,包括製造廠家選擇、工藝和資源準備等。同時,在傳統的飛機結構研製過程中,設計過程和製造過程相對獨立,只具備設計到製造的數據傳輸的單向性。製造過程數據無法反饋給設計部門。因此,建立基於數字化技術的飛機結構件設計製造過程的多信息溝通渠道,構建飛機結構件設計製造的協同平台,實現飛機結構件全生命週期多部門、多領域的數據共享,才能真正實現協同設計、協同製造和設計製造的協同。
從協同研發的總體目標來看,產品數字化協同開發有兩種模式。分別是橫向的(多學科協作開發MDO)和縱向的(協作開發的產品生命週期)。空中巴士在Viva Ce(通過虛擬航空協同企業提升價值)系統研究項目中應用協同技術研究,從可行性研究、概念設計到全生命週期的詳細設計,構建了MDO多學科協同開發體系框架。它應用於直升機、飛機和發動機三大航空領域。在空中巴士A380的研製過程中,多主體協同研製的思想在飛機的設計中得到了充分的運用。但這些數字化協同研製方法只是實現了數據從上游到下游之間的單向或橫向傳輸,缺乏下游數據對上游的反饋。
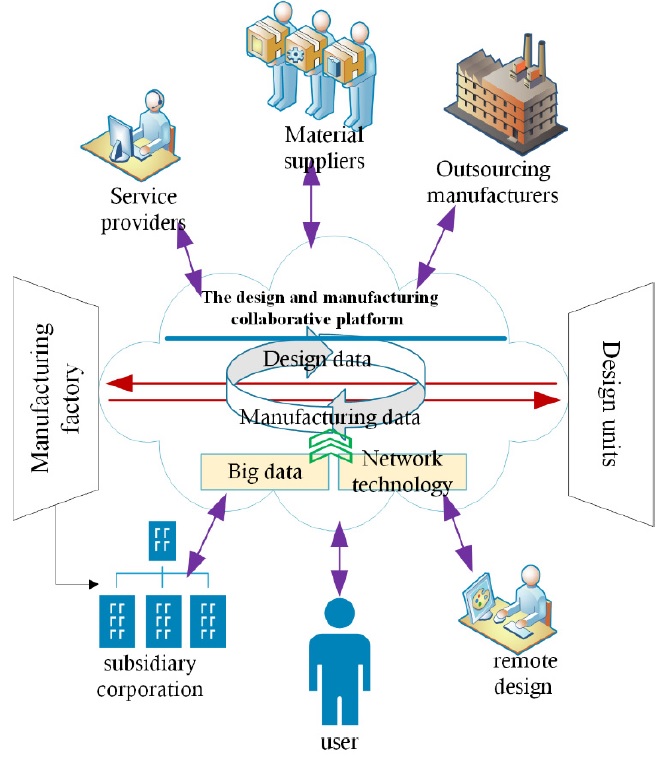
圖1 飛機結構件的設計製造協同平台
大數據技術和網絡技術的發展,為協同平台的建設提供了基礎條件。在協同平台中,屬於不同級別、不同區域、不同區域設計部門、不同區域廠家的軟件資源(CAD、CAE軟件)、硬件資源(數控設備、檢測設備等)和知識資源(工藝知識庫、參數庫)可以實現橫向和縱向共享。設計製造過程中的智能協調調度數據的直接傳輸,可以快速完成飛機結構設計和製造過程中的智能協調調度,實現分佈式資源的同步化。同時,飛機結構件製造工藝數據可以通過協同平台快速、及時地反饋給設計部門,指導和優化飛機結構件的設計流程,提高飛機結構件的可製造性,縮短飛機結構件和飛機產品研發週期。圖1所示為飛機結構件設計與製造的協同平台架構。
致謝
數字化技術在飛機結構件設計製造中的應用,有效提高了飛機結構件的加工質量和加工效率,但飛機結構件是一種小批量、多品種的生產模式,不僅需要提高質量和效率,更需要提高靈活性和自動化程度。未來飛機結構件設計與製造應逐步向智能化發展,打破傳統的設計與製造工藝分離的思維,構建飛機結構件設計與製造協同平台,實現飛機結構件的柔性自動化生產,為飛機結構件的高效率、高質量的柔性自動化生產提供保障。但智能製造需要以高度集成的自動化生產為基礎,國內航空企業離這個要求還有很大的差距。開展飛機結構件智能設計與製造的相關關鍵技術研究,推動相關技術和標準的應用,實現智能製造在飛機結構設計與製造領域的落地,勢在必行。作者對國家科技重大專項(2013ZX04001-021)表示感謝。