加工航空零件時如何防止銑刀破損
2020-04-21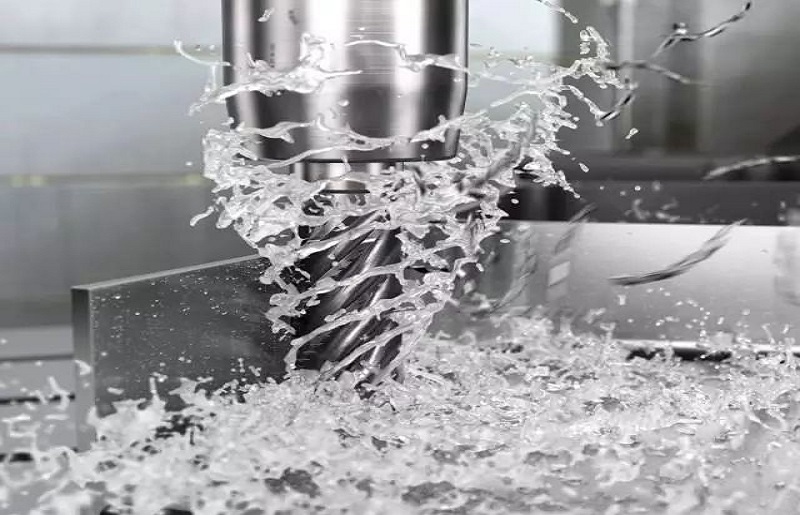
1. 航空零件加工成本控制
在切削加工過程中,如果銑刀發生了嚴重破損,通常會損壞被加工零件,有時甚至還會損壞加工機床。航空零件通常具有復雜的形狀,並採用價值不菲的特殊材料製造,加工這些零件需要耗費大量工時。因此,如果工件報廢,無論在原材料成本上,還是在加工附加值上,都會造成巨大的損失。
在航空製造業,單件小批量加工的情況並不鮮見,因此,損壞一件工件會對生產效益造成很大的損失。由於一個飛行器零件失效可能會導致災難性的後果,因此,在航空製造業,合規控制和降低風險的機制使得對損壞了的工件進行再加工比在其他行業更為複雜。因銑刀破損而造成的工件或機床損壞可能會嚴重影響製造商的盈利能力和客戶滿意度。
航空製造業使用的許多專用機床擔負著至關重要的加工任務。由於這些機床成本昂貴,加工準備時間很長,因此它們很可能是製造商的“瓶頸資產”,如果這些機床因銑刀破損而被損壞,就會對企業的生產能力造成重大影響。
2. 銑刀破損原因
在切削加工中,有許多原因會導致銑刀破損,但還沒有一種解決方案能夠確保100%地檢測出或完全避免銑刀破損的發生。專門製定的銑刀破損恢復循環程序可以挽救工件和生產損失。鑑於航空製造業的機床、材料成本以及在製品附加值的特點,為了保護企業的投資,制定不同層次的銑刀破損預防及檢測策略很有必要。
在航空製造業,工件的價值以及被加工材料的類型要求在大部分切削加工中必須採用質量最好的銑刀。但是,即使使用了最好的銑刀,如果在加工編程時,對於特定的銑刀或工藝採用了不正確的工藝參數,或操作者在銑刀安裝或調整過程中出現了失誤,仍然有可能造成銑刀破損。
航空零件通常是由鍛件、鑄件、棒材和板材毛坯,以及可加工性普遍較差的材料切削加工而成。材料成分、表面性狀以及切削深度和寬度的各種變化,使得在加工編程時很難準確地確定每一種被加工零件的最優切削參數。
航空發動機零件通常採用耐熱超級合金(HRSA)(如Inconel合金、鎳基合金、Waspaloy合金等)製造。鈦合金也被用於製造許多飛機零件。由於零件用途所需要的材料結構特性各異,這些合金的可加工性普遍較差。鑄件和鍛件的表面通常都粗糙不平。
在加工這些強韌的材料時,會產生很大的切削力和很高的切削溫度。耐熱超級合金材料結構中硬質碳化物具有的磨蝕性以及表面硬化傾向,可能會造成銑刀的刻劃磨損。如果在加工中採用了不正確的進給量、切削速度和切削深度,也可能會導致其他銑刀失效模式(如月牙窪、熱裂紋、崩刃、積屑瘤和變形),以及造成機床損壞。
因此,航空零件加工的特性可能會造成銑刀的不均勻磨損和高應力,這是銑刀提前失效的根本原因。不過,通過優化工藝參數,這些問題是完全可以避免的。然而,即使工藝參數正確無誤,在銑刀安裝和銑刀磨損補償的調整過程中也很容易出錯。測量、計算和數據輸入錯誤是銑刀破損和機床損壞的常見原因。
鑑於航空製造業的加工機床和在製品通常具有很高價值,因此,執行不同層次的銑刀破損預防措施,對於保護企業投資很有意義。一些可能的解決方案已經得到了很好證明,如聲發射或振動監測技術,以及在銑刀安裝和調整過程中使用檢測和對刀測頭消除誤差。數據採集和失效模式及後果分析(FMEA)技術可以提供對銑刀失效以及相關機床損壞的根本原因的寶貴洞見。這種分析有助於針對特定的加工任務選擇最有效的加工策略。
3. 航空零件模具銑削優化
磨料磨損是一種理想的銑刀失效模式,因為它往往具有可重複性和可預見性。當磨損過程平穩而均勻時,一些徵兆(如毛刺、表面光潔度或切削噪聲的變化)可以提醒操作者在出現災難性的銑刀失效之前採取正確的行動。也可以採用銑刀管理系統來提示操作者對銑刀進行定期維護。
然而,有許多零件的加工並非採用的是最優切削參數。或許企業的計算機輔助製造(CAM)系統採用的是一台普通的後處理器,從生產車間反饋回來的優化數據並未可靠地饋入系統;或許某種新型銑刀在一次加工中顯示出了令人印象深刻的效果,因而被生產車間所採用,但新的工藝參數尚未編入每一個工件的加工程序中。
銑刀製造商通常會為其銑刀產品的應用提供免費諮詢服務。他們可以基於特定的銑刀技術提出各種不同的加工模式,例如,採用較大的進給量、較快的切削速度和較小的切削深度;或者採用較小的進給量、較慢的切削速度和較大的切削深度。從而獲得令人滿意的加工效果,顯著縮短工件加工時間。但更重要的是,銑刀將在銑刀製造商推薦的切削參數範圍內使用。
一旦所有的切削參數都被確認,一個電子換刀管理系統可以確保對加工過程的控制,該系統可以同時管理工件加工程序和銑刀設置表。
更新銑刀的幾何參數和磨損補償量是很容易出錯的一個步驟,有可能引起銑刀失效、工件損壞,或許還會危及加工機床。
為了完成一次典型的銑刀磨損補償更新,操作者首先要對銑刀或工件進行測量。然後,操作者必須分析測量結果的影響,併計算出需要輸入機床數控系統的補償值。計算時,符號常常會混淆,半徑與直徑換算的問題也會使計算複雜化。將補償值輸入數控系統也提供了額外的出錯機會。小數點和符號輸入錯誤相當常見,有時補償值還會被輸入到錯誤的補償位置。
4. 銑刀檢測
使用檢測和對刀測頭是防止銑刀幾何尺寸及磨損補償出現錯誤的一種傳統解決方案,這些測頭在航空製造業已被廣泛應用。
不過,通過利用大多數機床CNC數控系統都具備的高水平宏編程功能,也能解決大多數防錯問題。數控系統可以提示操作者進行測量,並將測量值輸入到數控系統中一個容易記住的補償位置。該參數可以是一個與刀座位置相匹配的補償數字,也可以是一個恆定的補償數字,例如99或999。
工件加工程序宏語言可以執行一系列檢查,防止輸入的數據出錯。它可以檢查預期補償位置的變化情況,確認操作者已將測量值輸入到正確的位置。它可以確保輸入的測量值處於合理的範圍之內。然後,它可以在考慮輸入值、尺寸和公差以及現有補償值的基礎上,計算出正確的補償值。它還可以對考慮了銑刀磨損範圍規定的最大合理補償值設置上限。如果一切正常,正確的銑刀補償就會自動更新,從而避免了所有的手工計算和數據輸入錯誤。
在對複雜形狀工件進行輪廓加工時,很多時候銑刀需要進行部分切削。如果銑刀的切削負荷很大,就難以保持正確的切屑成形,並可能會引起摩擦。在切屑無法正確成形的情況下,切削熱難以從銑刀和工件材料中消散,銑刀就可能出現積屑瘤或月牙窪磨損失效模式。
自適應控制技術通常被認為是一種用於提高生產率的解決方案,而它有一種有益的附加功能,就是能保持銑刀切削負荷恆定。如果自適應系統檢測到銑刀的切削負荷下降,它就會通過增大進給率來維持設定的目標負荷。如果切削負荷增大,超過了目標負荷,切削速度就會相應降低。保持銑刀切削負荷恆定有利於改善成屑和排屑,而且可以避免產生積屑瘤、月牙窪磨損、切屑二次切削等問題。
如果對某種加工的工藝參數進行了優化,銑刀就能顯示出可靠的、可預測的磨料磨損失效模式。在這種情況下,銑刀管理系統就能提示操作者主動更換銑刀,以防止銑刀破損造成嚴重後果。
機床的CNC數控系統能監測銑刀的使用情況(包括加工時間和加工循環數)。它可以設定銑刀磨鈍標準,提示操作者及時更換刀片,如果發出警告後操作者仍未採取行動,它就會自動關停機床。為了延長對銑刀進行維護檢查的周期,對於使用頻率很高的銑刀,可以採用“姊妹銑刀”策略(如果刀庫中有多餘刀座的話)。如果一台機床具有在不中斷加工的情況下安全更換已磨損銑刀的功能,那麼還能顯著提高加工效率。
如果銑刀是在工具室集中管理,或由外部銑刀供應商管理,那麼在銑刀整個生命週期中跟踪其使用參數可能比較困難。可以利用射頻識別(RFID)電子標籤來預設銑刀負荷,或測量CNC系統中設定的銑刀幾何參數,以及更新銑刀壽命表。當銑刀暫時不使用時,可以將銑刀壽命值和所有已更新的磨損補償值重新寫入嵌裝在刀柄中的RFID芯片中,以在下次使用時供機床讀取。如果操作者決定越過CNC銑刀管理系統,在達到預定的銑刀壽命之前命令更換銑刀,也可以將這些信息標記在RFID芯片上。
離線系統也可以監測RFID芯片中存儲的銑刀數據。這些信息可用於在工具室對銑刀進行定期維護,或用於分析任何不同尋常的失效模式,以及確定銑刀失效的根本原因是否與特定的工件、操作者、生產班次、加工機床或其他因素有關。
當銑刀在加工過程中發生破損時,操作者停止加工可能需要幾分鐘的時間。如果銑刀在粗加工時發生破損,從理論上說,恢復正常需要做的全部事情就是:退回銑刀,更換刀片,然後從上次加工的最後正常位置重新開始加工。但在實際生產中,銑刀破損的恢復並不會如此簡單。
一種選擇是退回到工件加工程序中一個便於重新開始的程序塊。該步驟可能需要使加工中斷幾分鐘或幾小時,從而降低生產率。由於新銑刀的磨損程度比所替換的銑刀輕,因此新銑刀可能會二次切削工件,而切削負荷很輕的銑刀可能會引起切屑成形不良,從而有可能導致銑刀再次失效。
5. 結語
更好的解決方案是利用專門開發的CNC數控功能來管理銑刀破損恢復。啟動退刀功能將銑刀從工件表面快速移開。然後可將機床軸緩慢移動到一個刀片更換檢查點。可利用銑刀補償移動及存儲功能更新主動補償,清除在銑刀破損的時間點與操作者退刀的時間點之間不能實現正確加工的所有軌跡。然後,可以觸發銑刀退刀-恢復循環,將銑刀移回退刀點。接下來,可利用CNC返回功能將工件加工程序退回到工件上未出現錯誤軌蹟的某一點。最後,再次利用銑刀補償移動及存儲功能,(最好用手輪)移動銑刀,直到它與工件材料表面接觸。此時,銑刀已完全處於具有新的、適當的銑刀補償值的正確位置。
在某些情況下,銑刀破損尤其可能會造成災難性的後果(例如,如果在鑽削基礎孔的加工失敗後,試圖在一台機床上對其進行攻絲)。如果切斷銑刀在雙主軸車床的軸與軸轉換之前發生破損,就可能會對機床造成嚴重損壞。在這種情況下,每次加工後對銑刀進行檢查,以確認其仍然完好無損是必不可少的。
多年來,人們一直使用接觸式和非接觸式銑刀測量裝置來檢測銑刀破損。非接觸式測量裝置通常測量速度較快,由於不存在機械接觸,意味著被檢銑刀能高速通過激光束。不過,此類測量系統很難安裝在移動工作台上,並且由於立式加工中心的工作台通常是一個可移動的托盤,因此在此類機床上的加工更為複雜。
建昌(WOTEK)公司新開發的銑刀破損檢測傳感器在銑刀破損的高速檢測上具有很多優勢。這種單面測量裝置可以安裝在任何穩定的垂直表面上,能在換刀位置附近對銑刀進行監測,而無需將銑刀下移到安裝在工作台上的傳感器處。它的採樣算法能準確區分銑刀與冷卻液滴,實現快速、可靠的檢測。它還能在雙主軸車床加工中主軸轉換的情況下,用於對已經通過切斷加工而分離的工件進行檢測。
無論在加工中採取了多少防錯措施,仍有可能發生始料不及的問題,而且銑刀可能會根據程序指令向工件或某個機床部件高速運動而造成碰撞。對於昂貴的工件和擔負關鍵使命的加工機床而言,監測伺服電機產生的扭矩,及時發現異乎尋常的高扭矩值是很有意義的。
與正常的機床快速移動或切削進給相比,發生機械碰撞和銑刀破損會使作用於伺服電機和主軸電機上的負載轉矩異常增大。為此,可以在工件加工程序中設置最大扭矩上限,使CNC數控系統能實時檢測出超限負載。如果CNC系統檢測到一個突然出現的大扭矩擾動值,它就可以立即關停伺服電機,乃至通過指令值使電機反轉,以盡量減小對工件和機床可能造成的損害。
為了更全面地保護工件和機床,精密扭矩傳感裝置可以感知被加工零件的特定扭矩波形,並將其存儲在內存中。以後再加工相同的零件時,精密扭矩傳感裝置通過監測超出已知扭矩波形規定公差帶的主軸扭矩值,就能發現任何異常情況。
在航空製造業,對在製品和加工設備的投資非常高。通過採用最佳做法、防錯措施和其他自動化策略,盡可能減少意料之外的銑刀失效,可以成為多層次全面解決方案的一部分。