How to prevent breakage of end mills when machining aviation parts
2020-04-21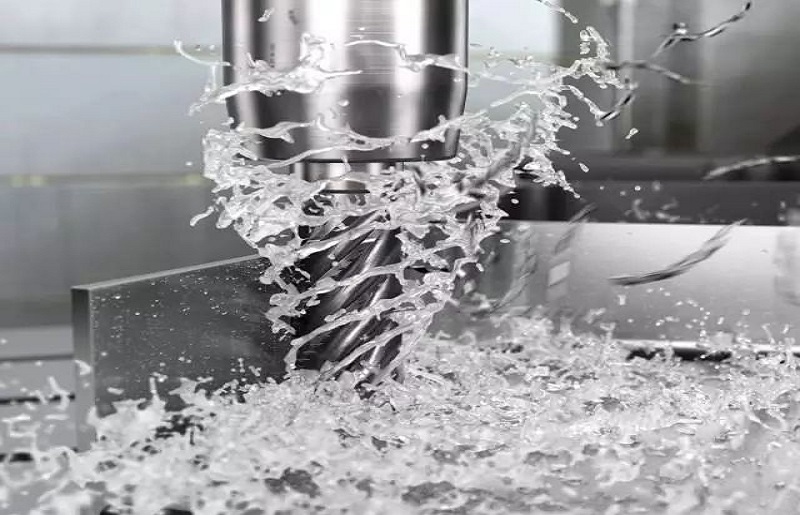
1. Cost control for aircraft parts cutting
During the cutting process, if the end mill is severely damaged, it usually damages the part being machined and sometimes even the machining machine. Aviation parts often have complex shapes and are made from special materials that are worth a lot of money, and machining these parts takes a lot of man-hours. Therefore, if the workpiece is scrapped, there is a huge loss, both in raw material costs and in processing added value.
In the aerospace manufacturing industry, it is not uncommon to see small batches of a single piece, so damaging a workpiece can cause a significant loss in production efficiency. Since the failure of an aircraft part can have catastrophic consequences, compliance controls and risk reduction mechanisms make reworking a damaged part more complicated in the aerospace manufacturing industry than in other industries. Workpiece or machine tool damage due to broken end mills can severely impact a manufacturer's profitability and customer satisfaction.
Many of the specialized machines used in the aerospace manufacturing industry have critical processing tasks. Since these machines are expensive and take a long time to prepare for machining, they are likely to be a "bottleneck asset" for manufacturers, and if these machines are damaged by a broken end mill, it can have a significant impact on a company's production capacity.
2. Cause of breakage of end mills
There are a number of reasons why end mills can break during cutting operations, but there is no one solution that can ensure 100% detection or completely prevent the occurrence of broken cutters. A specially designed end mill breakage recovery cycle can save workpieces and production losses. Given the characteristics of the aerospace manufacturing industry in terms of machine tools, material costs and value added in the product, it is necessary to develop different levels of end mill breakage prevention and detection strategies in order to protect the investment of the business.
In the aerospace industry, the value of the workpiece and the type of material being machined require the best quality end mills for most cutting operations. However, even with the best end mills, if incorrect process parameters are used for a particular end mill or process during machining programming, or if the operator makes an error in the installation or adjustment of the end mill, there is still the possibility of the cutter breaking.
Aerospace parts are typically machined from forgings, castings, bar and plate blanks, and from materials that are generally less machinable. Variations in material composition, surface properties, and depth and width of cut make it difficult to accurately determine the optimal cutting parameters for each type of part being machined during machining programming.
Aircraft engine parts are usually made from heat resistant super alloys (HRSA) such as Inconel alloys, nickel-based alloys, Waspaloy alloys, etc. Titanium alloy is also used in the manufacture of many aircraft parts. These alloys are generally less machinable due to the different structural properties of the materials required for part applications. Castings and forgings usually have a rough and uneven surface.
When machining these tough materials, a lot of cutting forces and high cutting temperatures are generated. The abrasive nature of hard carbides in the structure of heat-resistant superalloys and their tendency to harden the surface may cause marking wear on the end mill. If incorrect feeds, cutting speeds and depths of cut are used in machining, they can also cause other milling tool failure modes (e.g. crescent, thermal cracking, chipping, chip buildup and deformation) and cause machine tool damage.
As a result, the characteristics of machining aerospace parts can cause uneven wear and high stress on the end mill, which is the root cause of premature end mill failure. However, by optimizing the process parameters, these problems can be completely avoided. However, even if the process parameters are correct, errors can easily occur during the adjustment of the milling tool installation and milling tool wear compensation. Measurement, calculation and data entry errors are common causes of broken end mills and machine tool damage.
Given the generally high value of machining machines and work-in-progress products in the aerospace manufacturing industry, it makes sense to implement different levels of milling tool breakage prevention to protect business investments. Some possible solutions have been well proven, such as acoustic emission or vibration monitoring techniques, as well as the use of detection and alignment probes to eliminate errors during milling tool installation and adjustment. Data acquisition and failure mode and consequence analysis (FMEA) techniques can provide valuable insight into the root causes of milling tool failure and associated machine tool damage. This type of analysis helps to select the most effective machining strategy for a particular machining task.
3. Milling optimization for aviation parts and dies
Abrasive wear is an ideal failure mode for end mills because it tends to be repeatable and predictable. When the wear process is smooth and even, signs such as burrs, changes in surface finish or cutting noise can alert the operator to take the right action before a catastrophic cutter failure occurs. A milling tool management system can also be used to prompt the operator to perform regular maintenance on the milling tool.
However, there are many parts that are not machined using optimal cutting parameters. Perhaps a company's computer-aided manufacturing (CAM) system uses a common post-processor and the optimized data fed back from the production shop is not fed reliably into the system; perhaps a new end mill shows impressive results in a single pass and is adopted by the production shop, but the new process parameters are not yet programmed into every workpiece.
End mill manufacturers often offer free consultation services for the application of their end mill products. They can propose a variety of different machining modes based on a particular milling tool technology, e.g., using a larger feed, faster cutting speed and smaller depth of cut; or using a smaller feed, slower cutting speed and larger depth of cut. This results in satisfactory machining results and a significant reduction in workpiece machining time. But more importantly, the end mill will be used within the cutting parameters recommended by the end mill manufacturer.
Once all cutting parameters have been identified, control of the machining process is ensured by an electronic tool change management system that manages both the workpiece machining program and the milling tool setup table.
Updating the geometry of the end mill and the amount of wear compensation is a very error-prone step that can cause the end mill to fail, damage the workpiece, and perhaps endanger the machining machine.
In order to complete a typical milling tool wear compensation update, the operator first takes measurements of the milling tool or workpiece. The operator must then analyze the impact of the measurement results and calculate the compensation value that needs to be entered into the machine tool's CNC system. Symbols are often confused when calculating, and the problem of radius versus diameter conversion can complicate the calculation. Entering the compensation value into the digital control system also provides an additional opportunity for error. Decimal point and symbol input errors are common, and sometimes compensation values are entered into the wrong compensation position.
4. End mills inspection
The use of inspection and tool setting probes is a traditional solution to prevent errors in tool geometry and wear compensation, and these probes have been widely used in the aerospace industry.
However, most of the error prevention problems can be solved by using the high level of macro-programming that most machine tool CNC control systems are equipped with. The numerical control system prompts the operator to take the measurement and enter the measurement into an easy-to-remember compensation position in the numerical control system. The parameter can be a compensation number that matches the position of the holder, or it can be a constant compensation number, such as 99 or 999.
The workpiece process macro language performs a series of checks to prevent errors in the data entered. It checks for changes in the expected compensation position and confirms that the operator has entered the measured value into the correct position. It ensures that the input measurements are within a reasonable range. It can then calculate the correct compensation value, taking into account the input value, dimensions and tolerances, and the existing compensation value. It can also set an upper limit on the maximum reasonable compensation value that takes into account the mill wear range requirements. If all is well, the correct end mill compensation is automatically updated, thus eliminating all manual calculations and data entry errors.
When contouring complex shaped workpieces, many times the end mill requires partial cutting. If the end mill has a heavy cutting load, it can be difficult to maintain proper chip formation and can cause friction. In cases where chips are not shaped correctly, the cutting heat is difficult to dissipate from the cutter and workpiece material, and the cutter may develop a pattern of pebble or crescent wear failure.
Adaptive control technology is often considered a solution for increasing productivity, and it has the beneficial added feature of keeping the cutting load of the end mill constant. If the adaptive system detects a drop in the cutting load of the end mill, it maintains the set target load by increasing the feed rate. If the cutting load increases beyond the target load, the cutting speed will be reduced accordingly. Keeping the cutting load of the end mill constant is beneficial for improving chip formation and debris removal, as well as avoiding problems such as accumulation of psoriasis, crescent wear, and secondary cutting of chips.
If the process parameters for a particular process are optimized, the end mill can show a reliable and predictable pattern of abrasive wear failure. In this case, the milling tool management system prompts the operator to proactively replace the end mill to prevent serious consequences of a broken cutter.
The CNC numerical control system of the machine tool monitors the use of the milling tool (including machining time and number of cycles). It can set milling tool sharpening standards, prompt the operator to change inserts in a timely manner, and automatically shut down the machine if the operator does not take action after a warning. In order to prolong the cycle of maintenance checks on end mills, a "sister end mill" strategy can be used for end mills that are used very frequently (if there are extra holders in the tool bank). If a machine has the ability to safely replace worn out milling tools without interrupting the process, it can also significantly improve machining efficiency.
If the end mill is managed centrally in a tool room or by an external end mill supplier, it may be more difficult to track its usage parameters throughout the life cycle of the cutter. Radio Frequency Identification (RFID) tags can be used to preset the milling tool load, or to measure the milling tool geometry set in the CNC system, and to update the milling tool life table. When the cutter is temporarily out of use, the cutter life value and all updated wear compensation values can be rewritten into the RFID chip embedded in the shank for the machine to read at the next use. This information can also be marked on the RFID chip if the operator decides to cross the CNC milling tool management system and order a milling tool change before reaching the predetermined milling tool life.
The offline system can also monitor the milling tool data stored in the RFID chip. This information can be used to perform regular maintenance on end mills in the tool room, or to analyze any unusual failure patterns, and to determine whether the root cause of end mill failure is related to a specific workpiece, operator, production shift, machining machine, or other factor.
When a end mill breaks during machining, it can take several minutes for the operator to stop machining. If the end mill breaks during roughing, theoretically all that is needed to return to normal is: return the cutter, replace the insert, and start the process again from the last normal position of the last process. But in actual production, the recovery of broken end mills is not so simple.
One option is to return to an easy-to-start-again block in the workpiece machining program. This step may require interrupting the process for a few minutes or hours, thereby reducing productivity. Since the new end mill is less abrasive than the one replaced, the new cutter may cut the workpiece twice, and a very light cutting load may cause poor chip formation, which may cause the cutter to fail again.
5. Conclusion
A better solution is to manage end mill breakage recovery with specially developed CNC numerical controls. Activating the rewind function quickly removes the end mill from the workpiece surface. The machine tool shaft can then be moved slowly to a blade change checkpoint. The active compensation can be updated with the milling tool compensation movement and storage function, which removes all traces that do not allow correct machining between the point in time when the milling tool is broken and the point in time when the operator retires the tool. You can then trigger the End End mill Return-Recovery cycle to move the end mills back to the return point. Next, the CNC return function can be used to return the machining process to a point on the workpiece where there is no error trajectory. Finally, use the milling tool again to compensate for the movement and storage function, moving the milling tool (preferably with a hand wheel) until it makes contact with the surface of the workpiece material. At this point, the end mill is fully in the correct position with the new, appropriate compensation value for the end mill.
In some cases, a broken end mill can be particularly disastrous (e.g., if an attempt is made to tap a base hole on a machine after a failed process of drilling it). If the cutter breaks before the shaft-to-shaft change on a double spindle lathe, it can cause serious damage to the machine. In this case, it is essential to inspect the end mill after each machining to make sure it is still intact.
For years, people have been using contact and non-contact end mill measuring devices to detect broken end mills. Contactless measuring devices typically measure faster, and since there is no mechanical contact, this means that the cutter being checked can pass through the laser beam at high speed. However, this type of measuring system is difficult to install on a moving table, and machining on this type of machine is further complicated by the fact that the table of a vertical machining center is usually a moving tray.
WOTEK's newly developed end mill breakage detection sensor has many advantages in the high-speed detection of broken cutters. This single-sided measuring device can be mounted on any stable vertical surface and can monitor the end mill near the tool change position without the need to move the cutter down to the sensor mounted on the table. Its sampling algorithm accurately distinguishes between end mills and cooling droplets for fast and reliable inspection. It can also be used to inspect workpieces that have been separated by cutting in the case of a spindle change in a double spindle lathe.
No matter how much error prevention is taken in the machining, there is still the possibility that problems may occur from the beginning, and that the end mill may cause a collision by moving at high speed toward the workpiece or a machine part according to program instructions. For expensive workpieces and mission-critical machining machines, it makes sense to monitor the torque generated by servo motors and discover unusually high torque values in a timely manner.
The occurrence of mechanical collisions and end mill breakage can abnormally increase the load torque acting on servo motors and spindle motors compared to the normal rapid movement of the machine tool or cutting feeds. To this end, a maximum torque limit can be set during the workpiece machining process to enable the CNC control system to detect the overload in real time. If the CNC system detects a sudden high torque disturbance value, it can immediately shut down the servo motor, or even reverse the motor by commanding the value to minimize possible damage to the workpiece and machine tool.
For more comprehensive protection of workpieces and machines, precision torque sensing devices can sense the specific torque waveform of the part being machined and store it in memory. When machining the same part again in the future, the precision torque sensing device can detect any abnormalities by monitoring the spindle torque value beyond the tolerance zone specified by the known torque waveform.
In the aerospace manufacturing industry, investment in in-processing and processing equipment is very high. Minimizing unanticipated mill tool failures through the use of best practices, error prevention and other automation strategies can be part of a comprehensive multi-level solution.