High-efficiency cutting tools boost the development of CNC machining technology for aircraft structural components
2020-04-20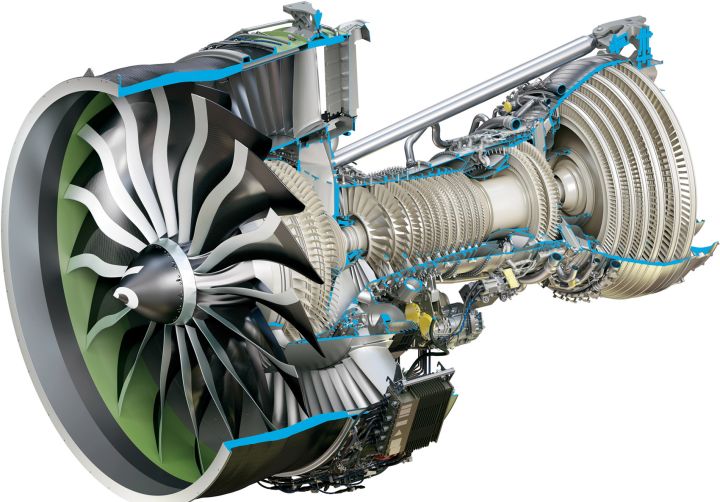
· In addition to the usual characteristics of the aircraft wing structure such as the theoretical curved surface of the aircraft, it also has the characteristics of large part profile size, deep groove cavity and strict requirements of the base plane profile.
· As the removal rate of raw materials usually reached 90%~95%, the highest reached 97%, and the depth of the groove is more than 80mm, the deepest reached more than 200mm, large overhang of cutting tools, poor rigidity, these are very easy to lead to long cutting cycle of parts, surface quality is not good, large processing deformation, low processing efficiency, etc., which puts forward higher requirements for aircraft structural parts digital control processing technology and efficient cutting tools.
Xi'an Aircraft Industry Group Company Limited (Xi'an) is an important research and development base for large and medium-sized civil aircraft in China. It not only undertakes the research and production of complete aircraft or components for large aircraft in China, but also undertakes international cooperative subcontracting projects such as the Boeing 737-700 tail and Airbus A319 wing boxes. The main products are wing beams, wall plates, inter-beam ribs, frames, large support joints and butt joints. The materials are mostly 2000 series and 7000 series super-hard aluminum alloys, but also a small amount of TC4 and TC6 titanium alloys and 30CrMnSiA and 300M high-strength structural steels, the rough types are mainly pre-drawn plates and free forgings.
In addition to the usual characteristics of the aircraft wing structure such as the theoretical curved surface with beveled angle, the aviation structural parts machined by the Westflight CNC Center have the characteristics of large profile size, deep cavity and strict contouring of the reference plane. As the removal rate of raw materials usually reached 90% to 95%, the highest reached 97%, and the depth of the cavity is more than 80mm, the deepest reached more than 200mm, large overhang of cutting tools, poor rigidity, these are very easy to lead to long cutting cycle of parts, surface quality is not good, large processing deformation, low processing efficiency and other problems, which puts forward higher requirements for aircraft structural parts CNC machining technology and efficient cutting tools.
The raw materials for the wing beam, wall plate and inter-beam rib parts of aircraft are super-hard aluminum alloy in Cs state, because the strength of aluminum alloy (super-hard aluminum alloy Cs state) σb is 0.48MPa, Brinell hardness is 156HBS, elongation δs is 5%, thermal conductivity of 1000℃ is 142W/(m-k), the strength and hardness are lower, the plasticity is smaller, the tool wear is smaller, and because the thermal conductivity is higher than copper alloy, the cutting temperature is lower, plus super-hard aluminum alloy has good cutting performance due to the generation of brittle compound CuAl2 distributed on the solid solution grain interface, which reduces the toughness and plasticity. So the aluminum wing beams, wall plates and inter-beam ribs are very suitable for high-speed cutting.
Aluminum alloy large support joints and butt joint blanks are free forgings or die forgings, the raw materials are annealed, the main processing processes are roughing, strengthening heat treatment and finishing. Due to the low melting point of aluminum alloy, the plasticity increases when the temperature rises, under high temperature and high pressure, the chip interface friction is very high, and it is easy for the sticky knife to form a scabbard, especially the annealed aluminum alloy is not easy to obtain good surface quality. In addition, most of these joints have deep grooves, high lugs, large tool overhang, poor rigidity, very easy to produce chatter, and low cutting efficiency.
Titanium alloy has a high specific strength (tensile strength to density ratio) of 23 to 29, and can maintain high specific strength at 300℃ to 500℃, and has good corrosion resistance to alkali, acid and other media. At present, the proportion of titanium alloy material in the aircraft structure is increasing, and titanium alloy material is also used more and more in large load-bearing frames with contour sizes larger than 1000mm and large butt joints larger than 400mm in special key parts. However, due to the easy chemical reaction between titanium alloy and oxygen, nitrogen, hydrogen and carbon, high hardness or brittle surface is formed, and poor thermal conductivity (1/5 to 1/7 of 45# steel), resulting in heavy cutting edge load, high cutting temperature and severe tool wear when cutting titanium alloy parts.
After years of accumulation, especially through the national "Ninth Five-Year Plan", "Tenth Five-Year Plan" and recent years of special technical transformation, the domestic aviation manufacturing industry has introduced a large number of high-precision CNC machining equipment from Europe, the United States and Japan, which has the characteristics of high speed, high power, fast moving speed, high precision and precision retention, alleviating the long-standing passive situation of insufficient capacity of aircraft structural components manufacturing equipment. However, this has exposed the backwardness of the processing technology, especially the low performance and poor quality of toolholders and tools, which has severely limited the normal performance of digital control equipment. To this end, since 2000, the aviation manufacturers through the technology summary and learning introduction, especially through the use of efficient cutting tools, high-speed and efficient cutting as the representative of the rapid development of digital controlled cutting technology, product surface processing quality and processing efficiency have been improved, a variety of typical aircraft structural parts in the process of digital controlled machining of long-standing problems have been initially solved.
Deep groove cavities are a typical structural feature of aircraft beams and joints, and an important cause of poor surface quality, local gnawing, and low processing efficiency of parts. When the tool runs from the straight edge to the corner of the groove, due to the change in cutting volume, it will cause the size and direction of the tool load to change greatly, resulting in tool chatter, it is very easy to occur the corner gnawing tool, resulting in the surface quality and geometric size of the parts of the ultra-worse, this ultra-worse will become more and more serious with the faster and faster feeding, with the depth of the groove deeper and more easily occur. This problem was solved a few years ago by the adoption of a new process of inserting and milling and new types of tools such as inserting and milling cutters, such as multi-layer line cutting, pencil-head milling cutters and five-coordinate programming for corner structures with small radii, which achieved good results. The application of this new technology and new tools not only solves the technical problems of the cavity corner overturning, but also solves the problem of low processing efficiency, after calculation and statistical analysis of field data, the cutting cycle of the CNC machine for aircraft beams and joints was reduced by more than 10%.
Roughing is the process of removing a large amount of cutting residue, while semi-finishing and finishing is the process of achieving the geometrical accuracy and surface quality required by the process through tool cutting. In addition to making the best possible use of the spindle output power for different processes, high speed and high efficiency technology has a different focus on new processes and new tools.
Roughing is the process of removing a large amount of cutting residue, while semi-finishing and finishing is the process of achieving the geometrical accuracy and surface quality required by the process through tool cutting. In addition to making the best possible use of the spindle output power for different processes, high speed and high efficiency technology has a different focus on new processes and new tools.
When finishing, high machining efficiency is achieved by increasing the cutting area per unit time while ensuring the quality of machining. Due to the extensive use of pre-balanced and tested tooling systems, abrasion-resistant powder metallurgy high speed steel or carbide tools, high hardness and good abrasion resistance tool coating, more reliable Big-plus BBT, HSK strong hydraulic and hot-mounted toolholders, the connection between the tool and the toolholder, the toolholder and the tooling machine is more precise and more rigid, when machining, the tooling machine speed can reach 20,000-30,000r/min, the feed movement speed of more than 10,000mm/min.
Aircraft structures, such as support joints and butt joints, are mainly composed of structural features such as groove cavities, lugs, assembly positioning holes with high precision and large diameter on lugs, and contours. The traditional process is to process the structure of the cavity, lugs, profile, etc. on a CNC milling machine, then transfer the processing to the boring machine and use the special boring clamps to locate the parts, thus finally processing the holes required by the drawing. Before the use of new tools such as U-drills, ultra-precise drills and high-speed reaming tools, these holes were generally drilled with CNC tools, and the parts were clamped with drilling dies or drilling samples, and the reaming holes were drilled by hand or on a drilling machine.
However, the above method of hole making not only leads to a reduction in the accuracy of the machining position due to the need for re-clamping, but also increases the process flow and prolongs the manufacturing cycle of the parts. In recent years, the introduction of simple pre-tuning and reliable CNC tool machine high precision boring drills has made it possible to promote the application of boring and milling compounding technology for finishing, boring and milling in a single clamping. The application of this technology has not only reduced the need for boresetting jigs in the development of new aircraft, saved the cost of development, but also significantly reduced the production cycle of parts. At the same time, this type of boring drills can guarantee high machining accuracy, stable product quality and production efficiency in batch production because of its precise and simple pre-conditioning.
For smaller diameter holes in the web and edge plates, the use of new precision hole making tools such as U-drills, ultra-precision drills and high speed reamers, as well as the use of angle milling heads, the precision holes and side wall recesses of these parts can be machined with a small angle of oscillation of the spindle of a three- or five-coordinate CNC tooling machine. As a result of the adoption of new tools, the development of digital control hole technology, making it possible to complete the processing of all the process structure of the parts through one or two clamps on the CNC tool machine, this process centralized, complex processing technology has become the development direction of modern aircraft structure CNC machining.
In the part machining deformation control, in addition to the use of layering, symmetrical removal of residual amount, reasonable design of the trajectory, selection of suitable process cutting parameters, etc., in the CNC machine with the spindle cooling function, the use of high pressure cooling of the tool center is also an effective way to ensure adequate cooling of the parts during deep groove machining and reduce the machining deformation caused by cutting heat.
In the cutting of titanium alloy parts, the large number of integral carbide tools using tungsten and cobalt carbide materials, integral carbide drills and reamers, tooth welding tools and indexable tools instead of traditional cobalt HSS tools has resulted in sharper cutting edges and improved cutting edge strength and chipping resistance, reducing the severity of tool wear when machining titanium alloy. Using the appropriate cut width AE, cut depth AP and feed, the machining efficiency of titanium alloy parts is improved by increasing the cutting speed. Thanks to the new tool, the cutting speed of titanium alloy has been increased from the traditional 20~30m/min to 90~110m/min, and the cutting capacity of aircraft titanium alloy structural parts has been greatly improved.
The introduction and promotion of high-efficiency cutting tools has facilitated another rapid development of CNC machining technology for aircraft structural parts, shortening the technological gap between us and our foreign counterparts. However, at present, the domestic use of high-precision shanks, high-performance high-speed cutting tools, high-precision hole-making tools, etc. rely heavily on foreign imports, long procurement cycle, high acquisition costs, and the high-precision repeated sharpening and repeated coating of the tool cannot be guaranteed, low utilization rate of tool repetition.
These have led to the high cost of tools in the manufacturing process of domestic aircraft structural parts, because of late delivery of parts production phenomenon also occurs from time to time, to a certain extent, restricting the use of new tools and the promotion of new technologies, therefore, the need for efficient cutting tools nationalization is increasingly urgent. At the same time, at present, the domestic cutting tools in the full-life monitoring and management is just in the initial stage, in the future period, self-design, manufacture and use of efficient cutting tools, to promote the early realization of our country from a manufacturing power to create a great power leap, both for China's cutting tool manufacturing industry and aviation manufacturing industry, must face and as soon as possible to solve the problem.
· As the removal rate of raw materials usually reached 90%~95%, the highest reached 97%, and the depth of the groove is more than 80mm, the deepest reached more than 200mm, large overhang of cutting tools, poor rigidity, these are very easy to lead to long cutting cycle of parts, surface quality is not good, large processing deformation, low processing efficiency, etc., which puts forward higher requirements for aircraft structural parts digital control processing technology and efficient cutting tools.
Xi'an Aircraft Industry Group Company Limited (Xi'an) is an important research and development base for large and medium-sized civil aircraft in China. It not only undertakes the research and production of complete aircraft or components for large aircraft in China, but also undertakes international cooperative subcontracting projects such as the Boeing 737-700 tail and Airbus A319 wing boxes. The main products are wing beams, wall plates, inter-beam ribs, frames, large support joints and butt joints. The materials are mostly 2000 series and 7000 series super-hard aluminum alloys, but also a small amount of TC4 and TC6 titanium alloys and 30CrMnSiA and 300M high-strength structural steels, the rough types are mainly pre-drawn plates and free forgings.
In addition to the usual characteristics of the aircraft wing structure such as the theoretical curved surface with beveled angle, the aviation structural parts machined by the Westflight CNC Center have the characteristics of large profile size, deep cavity and strict contouring of the reference plane. As the removal rate of raw materials usually reached 90% to 95%, the highest reached 97%, and the depth of the cavity is more than 80mm, the deepest reached more than 200mm, large overhang of cutting tools, poor rigidity, these are very easy to lead to long cutting cycle of parts, surface quality is not good, large processing deformation, low processing efficiency and other problems, which puts forward higher requirements for aircraft structural parts CNC machining technology and efficient cutting tools.
The raw materials for the wing beam, wall plate and inter-beam rib parts of aircraft are super-hard aluminum alloy in Cs state, because the strength of aluminum alloy (super-hard aluminum alloy Cs state) σb is 0.48MPa, Brinell hardness is 156HBS, elongation δs is 5%, thermal conductivity of 1000℃ is 142W/(m-k), the strength and hardness are lower, the plasticity is smaller, the tool wear is smaller, and because the thermal conductivity is higher than copper alloy, the cutting temperature is lower, plus super-hard aluminum alloy has good cutting performance due to the generation of brittle compound CuAl2 distributed on the solid solution grain interface, which reduces the toughness and plasticity. So the aluminum wing beams, wall plates and inter-beam ribs are very suitable for high-speed cutting.
Aluminum alloy large support joints and butt joint blanks are free forgings or die forgings, the raw materials are annealed, the main processing processes are roughing, strengthening heat treatment and finishing. Due to the low melting point of aluminum alloy, the plasticity increases when the temperature rises, under high temperature and high pressure, the chip interface friction is very high, and it is easy for the sticky knife to form a scabbard, especially the annealed aluminum alloy is not easy to obtain good surface quality. In addition, most of these joints have deep grooves, high lugs, large tool overhang, poor rigidity, very easy to produce chatter, and low cutting efficiency.
Titanium alloy has a high specific strength (tensile strength to density ratio) of 23 to 29, and can maintain high specific strength at 300℃ to 500℃, and has good corrosion resistance to alkali, acid and other media. At present, the proportion of titanium alloy material in the aircraft structure is increasing, and titanium alloy material is also used more and more in large load-bearing frames with contour sizes larger than 1000mm and large butt joints larger than 400mm in special key parts. However, due to the easy chemical reaction between titanium alloy and oxygen, nitrogen, hydrogen and carbon, high hardness or brittle surface is formed, and poor thermal conductivity (1/5 to 1/7 of 45# steel), resulting in heavy cutting edge load, high cutting temperature and severe tool wear when cutting titanium alloy parts.
After years of accumulation, especially through the national "Ninth Five-Year Plan", "Tenth Five-Year Plan" and recent years of special technical transformation, the domestic aviation manufacturing industry has introduced a large number of high-precision CNC machining equipment from Europe, the United States and Japan, which has the characteristics of high speed, high power, fast moving speed, high precision and precision retention, alleviating the long-standing passive situation of insufficient capacity of aircraft structural components manufacturing equipment. However, this has exposed the backwardness of the processing technology, especially the low performance and poor quality of toolholders and tools, which has severely limited the normal performance of digital control equipment. To this end, since 2000, the aviation manufacturers through the technology summary and learning introduction, especially through the use of efficient cutting tools, high-speed and efficient cutting as the representative of the rapid development of digital controlled cutting technology, product surface processing quality and processing efficiency have been improved, a variety of typical aircraft structural parts in the process of digital controlled machining of long-standing problems have been initially solved.
Promotion of new technologies and applications of new cutting tools
1 Improved surface finish quality of deep groove cavities
Deep groove cavities are a typical structural feature of aircraft beams and joints, and an important cause of poor surface quality, local gnawing, and low processing efficiency of parts. When the tool runs from the straight edge to the corner of the groove, due to the change in cutting volume, it will cause the size and direction of the tool load to change greatly, resulting in tool chatter, it is very easy to occur the corner gnawing tool, resulting in the surface quality and geometric size of the parts of the ultra-worse, this ultra-worse will become more and more serious with the faster and faster feeding, with the depth of the groove deeper and more easily occur. This problem was solved a few years ago by the adoption of a new process of inserting and milling and new types of tools such as inserting and milling cutters, such as multi-layer line cutting, pencil-head milling cutters and five-coordinate programming for corner structures with small radii, which achieved good results. The application of this new technology and new tools not only solves the technical problems of the cavity corner overturning, but also solves the problem of low processing efficiency, after calculation and statistical analysis of field data, the cutting cycle of the CNC machine for aircraft beams and joints was reduced by more than 10%.
2 Substantial increase in material removal rate and processing area per unit time
Roughing is the process of removing a large amount of cutting residue, while semi-finishing and finishing is the process of achieving the geometrical accuracy and surface quality required by the process through tool cutting. In addition to making the best possible use of the spindle output power for different processes, high speed and high efficiency technology has a different focus on new processes and new tools.Roughing is the process of removing a large amount of cutting residue, while semi-finishing and finishing is the process of achieving the geometrical accuracy and surface quality required by the process through tool cutting. In addition to making the best possible use of the spindle output power for different processes, high speed and high efficiency technology has a different focus on new processes and new tools.
When finishing, high machining efficiency is achieved by increasing the cutting area per unit time while ensuring the quality of machining. Due to the extensive use of pre-balanced and tested tooling systems, abrasion-resistant powder metallurgy high speed steel or carbide tools, high hardness and good abrasion resistance tool coating, more reliable Big-plus BBT, HSK strong hydraulic and hot-mounted toolholders, the connection between the tool and the toolholder, the toolholder and the tooling machine is more precise and more rigid, when machining, the tooling machine speed can reach 20,000-30,000r/min, the feed movement speed of more than 10,000mm/min.
3 Newly constructed tooling systems expand CNC machining capabilities
Aircraft structures, such as support joints and butt joints, are mainly composed of structural features such as groove cavities, lugs, assembly positioning holes with high precision and large diameter on lugs, and contours. The traditional process is to process the structure of the cavity, lugs, profile, etc. on a CNC milling machine, then transfer the processing to the boring machine and use the special boring clamps to locate the parts, thus finally processing the holes required by the drawing. Before the use of new tools such as U-drills, ultra-precise drills and high-speed reaming tools, these holes were generally drilled with CNC tools, and the parts were clamped with drilling dies or drilling samples, and the reaming holes were drilled by hand or on a drilling machine.However, the above method of hole making not only leads to a reduction in the accuracy of the machining position due to the need for re-clamping, but also increases the process flow and prolongs the manufacturing cycle of the parts. In recent years, the introduction of simple pre-tuning and reliable CNC tool machine high precision boring drills has made it possible to promote the application of boring and milling compounding technology for finishing, boring and milling in a single clamping. The application of this technology has not only reduced the need for boresetting jigs in the development of new aircraft, saved the cost of development, but also significantly reduced the production cycle of parts. At the same time, this type of boring drills can guarantee high machining accuracy, stable product quality and production efficiency in batch production because of its precise and simple pre-conditioning.
For smaller diameter holes in the web and edge plates, the use of new precision hole making tools such as U-drills, ultra-precision drills and high speed reamers, as well as the use of angle milling heads, the precision holes and side wall recesses of these parts can be machined with a small angle of oscillation of the spindle of a three- or five-coordinate CNC tooling machine. As a result of the adoption of new tools, the development of digital control hole technology, making it possible to complete the processing of all the process structure of the parts through one or two clamps on the CNC tool machine, this process centralized, complex processing technology has become the development direction of modern aircraft structure CNC machining.
4 Machining deformation control and high-speed cutting of titanium alloys developed
In the part machining deformation control, in addition to the use of layering, symmetrical removal of residual amount, reasonable design of the trajectory, selection of suitable process cutting parameters, etc., in the CNC machine with the spindle cooling function, the use of high pressure cooling of the tool center is also an effective way to ensure adequate cooling of the parts during deep groove machining and reduce the machining deformation caused by cutting heat.In the cutting of titanium alloy parts, the large number of integral carbide tools using tungsten and cobalt carbide materials, integral carbide drills and reamers, tooth welding tools and indexable tools instead of traditional cobalt HSS tools has resulted in sharper cutting edges and improved cutting edge strength and chipping resistance, reducing the severity of tool wear when machining titanium alloy. Using the appropriate cut width AE, cut depth AP and feed, the machining efficiency of titanium alloy parts is improved by increasing the cutting speed. Thanks to the new tool, the cutting speed of titanium alloy has been increased from the traditional 20~30m/min to 90~110m/min, and the cutting capacity of aircraft titanium alloy structural parts has been greatly improved.
Conclusion
The introduction and promotion of high-efficiency cutting tools has facilitated another rapid development of CNC machining technology for aircraft structural parts, shortening the technological gap between us and our foreign counterparts. However, at present, the domestic use of high-precision shanks, high-performance high-speed cutting tools, high-precision hole-making tools, etc. rely heavily on foreign imports, long procurement cycle, high acquisition costs, and the high-precision repeated sharpening and repeated coating of the tool cannot be guaranteed, low utilization rate of tool repetition.
These have led to the high cost of tools in the manufacturing process of domestic aircraft structural parts, because of late delivery of parts production phenomenon also occurs from time to time, to a certain extent, restricting the use of new tools and the promotion of new technologies, therefore, the need for efficient cutting tools nationalization is increasingly urgent. At the same time, at present, the domestic cutting tools in the full-life monitoring and management is just in the initial stage, in the future period, self-design, manufacture and use of efficient cutting tools, to promote the early realization of our country from a manufacturing power to create a great power leap, both for China's cutting tool manufacturing industry and aviation manufacturing industry, must face and as soon as possible to solve the problem.