Do you know the application of these carbide end mills in aerospace?
2020-04-17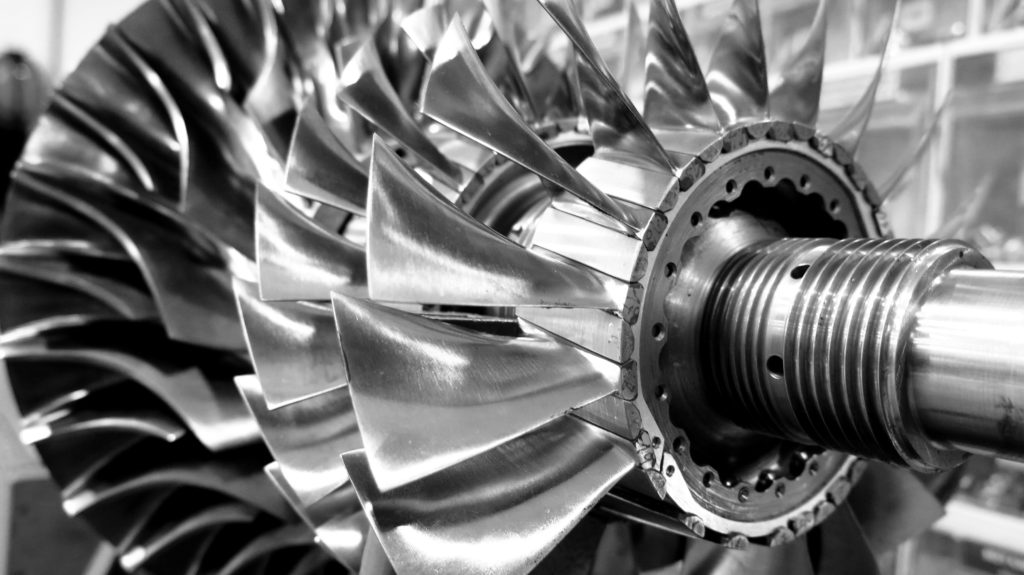
Types of Carbide End Mills for Typical Parts of Aerospace Manufacturing Industry
Not only do aerospace components use many new structures, technologies and materials, but also the complex construction and poor rigidity of the parts have made it necessary to machine parts such as engines with high performance standard end mills and special carbide end mills in large quantities.
Aircraft standards are so stringent that many aerospace components must be machined from a single hard material to ensure maximum material integrity while helping to lift the aircraft into the air. This means that the milling lathe may need to up-arch the metal load, reduce it to a net shape and finally get the final part.
When machining raised parts, the carbide end mills system can easily interfere with parts and holders. Therefore, it is necessary to optimize the path of the carbide milling tool, such as inserting and milling instead of side milling, straight milling, optimizing the position of the lift tool, using spiral interpolation for milling, etc. In terms of tooling machine selection, the turbine cartridge needs to be machined on a high-powered machining center. Analyzed from the processing process, the chassis needs to go through roughing, semi-finishing and finishing.
In order to save the cost of carbide end mills, high performance ceramic end mills can be used for roughing, standard carbide end mills and non-standard high performance special carbide end mills for semi-finishing and finishing in the manufacture of such parts, which can significantly increase the production efficiency. In terms of machining economy, the carbide end mills configuration needs to be continuously improved, using the latest products developed by the carbide end mills manufacturer as much as possible.
In the aerospace industry, titanium and titanium alloys are often used to manufacture various key structural components, the machining of which places has very high demanded on processes, tooling machines, carbide end mills and cutting fluids. To meet these requirements, Basil Lubrication has developed what it calls a "revolutionary" water-soluble cutting fluid, the Vasco 5000, which provides better and faster machining results and longer carbide end mill life than conventional products, resulting in increased reliability and productivity. One of the key factors that directly affect machining quality is the correct selection of the cutting fluid. Of course, the use of coolant is supported by a corresponding technological innovation.
WOTEK invented the suction drill for deep hole drilling in titanium alloy, which uses two identical pipes to provide coolant and chip removal, creating the venturi effect. The HP carbide cutting tools uses a fixed nozzle technology that emits a high speed parallel layer jet to accurately align the inserts where they need to be cooled, and the resulting jet accuracy and characteristics make this technology unique. The RENODRILL 2190 from FOSS is suitable for high hardness materials and difficult machining processes such as deep hole drilling, gun drilling, broaching and tapping.
Advantages of titanium alloy material
Titanium alloy has high strength, high fracture toughness and good corrosion resistance and weldability. As aircraft fuselages are increasingly constructed with composite materials, a growing proportion of titanium-based materials will be used in the fuselage, as titanium and composite materials combine far better than aluminum alloys. For example, titanium alloy can increase the life of the fuselage structure by 60% compared to aluminum alloy.
The extremely high strength/density ratio of titanium (up to 20:1, i.e. 20% weight reduction) provides a solution to reduce the weight of large components, a major challenge for aircraft designers. In addition, the inherent high corrosion resistance of titanium alloys (compared to steel) saves on the cost of daily operation and maintenance of aircraft.
Because the use of high feed speed machining and high speed of no-load close to the part greatly affect the length of the machining time, especially to greatly reduce the "auxiliary time", it can generally reduce the entire production cycle by 20% when machining aluminum alloy material. The "auxiliary time" also includes such things as the clamping of new parts, the positioning of clamps, and the changing of tungsten steel cutters. "In lean manufacturing jargon, it is a useless time drain that should be eliminated.
In order to achieve fast feed rates at high add/drop speeds, several years ago MAG Cincinnati developed the HyperMach series of vertical profiling mills, the main feature of which is a fast feed rate of 101m/min, the highest feed rate at that time that could significantly reduce the 'assist time'," says Von Moll. And what MAG Cincinnati is most proud of is the HyperMach Vertical Profiling Milling Machine, which is designed to rotate in A, B, and C axes in addition to X, Y, and Z. The X-axis has a working stroke of 33m, the Y-axis is 3500mm, the Z-axis is 1250mm and the spindle has a maximum speed of 30 000 r/min. The most important feature of the structural design of the tool machine is the assembly of a pair of independent working spindles on the X-axis bridge beam.
The tooling capability, which provides users with the ability to machine large parts of 2000mm x 4000mm, has been well received by aircraft manufacturers since its exhibition at IMTS 2008. According to Von Moll.
Aluminum and Aluminum Alloy
Aluminum and its alloys are silvery white metallic materials. The density of aluminum is 2.7g/cm3, which is only about 1/3 that of steel, and it also has good corrosion resistance, because it is easy to form a dense Al2O3 protective film on its surface. Pure aluminum is not strong enough, and when melted, the right amount of silicon, copper, magnesium, zinc, manganese and other elements are added to aluminum to form an aluminum alloy. Aluminum alloys have a high strength and can be used to manufacture load-bearing mechanical parts. After a certain heat treatment, its strength can be further improved. Although the use of aluminum is on a downward trend, it is still the most used in civil aircraft, with aluminum alloy being the preferred aviation material and a larger percentage in military aircraft.
(1) Aluminum alloy structural, represented by integral parts.
In the manufacture of aerospace products, there is a large amount of aluminum alloy cutting and machining. First of all, aluminum alloy components are significant. In a high-performance fighter aircraft, high-strength aluminum alloy components account for 70 to 80 percent of the aircraft's total weight. Second, there is a high rate of material removal. In order to improve the reliability of the parts and reduce the weight, the traditional riveted structure is gradually replaced by the overall thin-walled machined structural parts. Most of these parts are made of overall solid aluminum alloy material, 70% to 95% of the material has to be removed in the process. If the frame blank is a 0.5t aluminum alloy forged part, the weight is only about 40kg when it is processed into a thin-walled overall structural frame. Again, thin-walled, thin-reinforced structural members are plentiful and cannot withstand large cutting rates.
(2) Cutting technology for difficult materials.
The aerodynamics department uses nickel-based alloys (such as Inconel718) and titanium alloys (such as TiAl6V4) in large quantities to manufacture engine parts for aircraft engines. For these difficult to process materials, the current level of domestic cutting processing technology is relatively low, only a few enterprises have developed some research applications, cutting speed can only reach 80 ~ 100m/min, has not been in the production of large-scale applications.
The best solution for aerospace MJ reinforced external threads
For aerospace titanium alloy, high temperature alloy MJ reinforced external threads, general purpose end mills can no longer meet the requirements of the use of parts, but need to provide the best machining solution from the design, manufacturing and other aspects, which involves the selection of carbide end mills material, improve the carbide end mills process, choose the appropriate cutting speed, etc. Rolling method is a plastic processing technology, it does not destroy the metal fiber on the premise that the metal body to make plastic displacement, so that no chips make the metal forming, which can improve the mechanical properties of the threads being processed, but also greatly save the aerospace parts with special materials.
The outer threaded part was deformed by rolling plasticity, and its strength and hardness increased, while its plasticity decreased, and the metal fibers of the threaded part were not cut off, but only deformed along the threaded tooth shape. The material of the rolled parts is denser, and the surface produces a cold hardening layer, and there is residual pressure stress, so the wear resistance of the rolled parts is improved, and the fatigue strength of the threads can be increased by 20% to 40%. The roughness of the threaded surface is also greatly improved after rolling, and the excellent surface quality can increase the cyclic strength of the thread. After the material plastic deformation, with the degree of deformation, the strength is higher and higher, so the tensile strength of the rolled out thread can be increased by 20%~30%, and the shear strength is increased by 5%. At the same time, MJ reinforced external threads have higher strength requirements, using the principle of metal plastic deformation of rolling threads better solve the problem of increasing the arc of the tooth base.
Therefore, the best carbide end mills for the machining of titanium and MJ reinforced external threaded parts in the aerospace industry should be made with a roller wheel.
Business Solutions
Aerospace components manufacturing is not only about carbide end mills and materials, but also related to efficient parts production, controlling inventory of carbide end mills and reducing all other costs. This is where WOTEK's Component Engineering Tooling (CET), WOTEK's Carbide End Mill Tool Management System and Production Rate Cost Analysis (PCA) system offer many advantages for the manufacturing process.