你懂這些鎢鋼銑刀在航空產業中的應用嗎?
2020-04-17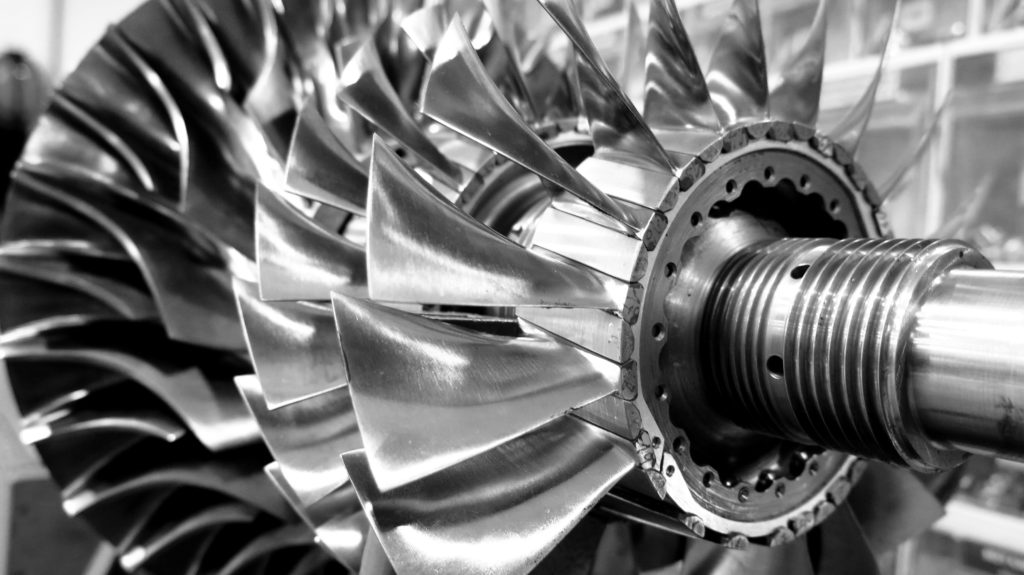
航空製造業典型零件用鎢鋼銑刀種類
航空製造零部件不僅採用了很多新結構、新技術和新材料,而且零件構型複雜,剛性較差,這些因素促使發動機等零件機械加工必須大量使用高性能的標準銑刀和專用鎢鋼銑刀進行加工。飛機標準非常嚴苛,許多航空業的零件必須從在一個硬質材料上進行整體加工,保證材料最大程度的完整性同時幫助飛機升空。這意味著銑削車床可能需要上拱金屬負荷,降低至凈形並最後得到最終部件。
加工零件凸起部分時,鎢鋼銑刀系統容易與零件、夾具干涉。因此必須對鎢鋼銑刀路徑進行優化,如用插銑加工代替側銑、空行程快速走刀、優化抬刀位置、採用螺旋插補等方式進行銑削。從工具機的選擇上來說,渦輪機匣需要在大功率的加工中心上加工。從加工工序上分析,機匣需要經過粗加工、半精加工、精加工。為了節省鎢鋼銑刀費用,在製造這類零件時,粗加工時可採用高性能陶瓷銑刀,半精加工和精加工時採用標準硬質合金鎢鋼銑刀和非標高性能專用鎢鋼銑刀,這樣可顯著提高生產效率。從加工經濟性方面上來說,鎢鋼銑刀配置方案需要不斷改進,儘量採用鎢鋼銑刀商最新研發的產品。
在航空工業中,鈦及鈦合金經常被用作製造各種關鍵的結構件,此類結構件的加工對工藝、工具機、鎢鋼銑刀以及切削液提出了非常高的要求。為滿足這些要求,巴索潤滑公司研製出了一種被稱為「革命性的」水溶性切削液Vasco 5000。與傳統產品相比,該切削液可提供更好和更快的加工效果,以及更長的鎢鋼銑刀壽命,從而提高可靠性和生產率。其中直接影響加工質量的關鍵因素之一就是對切削液的正確選擇。當然,冷卻液的使用還要有相應的創新技術支持,WOTEK在鈦合金深孔鑽加工中,發明了噴吸鑽,採用兩根相同的管道提供冷卻液和排屑,形成文丘里效應。後將HPC(高壓冷卻)與Capto(山特維克接口快換系統)融合,發展出完備的鈦合金銑削系列HP鎢鋼銑刀高壓冷卻系統解決方案。HP鎢鋼銑刀採用固定噴嘴技術,噴出高速的平行層射流,可準確的對準刀片需要冷卻的位置,所產生的射流精度和特性使得這種技術與眾不同。福斯的RENODRILL 2190適用於高硬度材質和高難度加工工藝,如深孔鑽、槍鑽、拉削和攻螺紋等。
鈦合金材料的優勢
鈦合金具有高強度、高斷裂韌性以及良好的抗腐蝕性和可焊接性。隨著飛機機身越來越多地採用複合材料結構,鈦基材料用於機身的比例也將日益增大,因為鈦與複合材料的結合性能遠遠優於鋁合金。例如:與鋁合金相比,鈦合金可使機身結構的壽命提高60%。鈦合金極高的強度/密度比(達20∶1,即重量可減輕20%)為減輕大型構件的重量(這是對飛機設計師的主要挑戰)提供了解決方案。此外,鈦合金固有的高耐蝕性(與鋼材相比)可以節省飛機日常運行和維護保養的成本。
因為採用快進給速度加工和空載快移動速度接近零件,極大地影響著加工時間的長短,尤其是大大減少「輔助時間」,所以能在加工鋁合金材料時,一般能減少整個生產周期的20%。「輔助時間」還包括新零件的裝夾定位和鎢鋼銑刀的交換時間等。
「在精益生產術語中,它是一個應該取消的無用的時間消耗。為在高加/減速度下實現快進給速度,幾年前,MAG Cincinnati公司研發出HyperMach型立式仿形銑床系列 ,其主要特點是快進給速度可達101m/min,這在當時是能大大減小「輔助時間」的最高的進給速度,」Von Moll說。而MAG辛辛那提公司最讓自己引以為豪的是HyperMach型立式仿形銑床除X、Y、Z三軸外,還設計出A、B、C三軸旋轉。其中,X軸的工作行程長達33m ,Y軸是3500mm,Z軸為1250mm,主軸最高轉速30 000 r/min。在工具機的結構設計上的最大特點,是將一對獨立的工作主軸裝配在X軸的橋式橫樑上。「該工具機能為用戶提供加工2000mm×4000mm大型零件的加工能力,在IMTS 2008展出後,很受飛機製造廠用戶的青睞。」據Von Moll介紹。
鋁及鋁合金
鋁及其合金是銀白色的金屬材料。鋁的密度為2.7g/cm3,僅為鋼的1/3左右,它還具有良好的耐腐蝕性,因為在它的表面上很容易形成一層緻密的Al2O3保護膜。純鋁的強度不足,熔煉時在鋁中加入適量的矽、銅、鎂、鋅、錳等元素就成為鋁合金。鋁合金具有較高的強度,能用於製造承受載荷的機械零件。經過一定的熱處理,其強度可以進一步提高。雖然鋁合金的用量呈下降趨勢,但在民航機中,使用最多的仍然是鋁合金,鋁合金是首選的航空材料,在軍用機中也占有較大比例。
(1)以整體件為代表的鋁合金結構件。
在航空產品製造中,鋁合金切削加工量很大。首先,鋁合金構件比重大。在一架高性能的戰鬥機中,高強度鋁合金構件占飛機整機重量的比例高達70%~80%。其次,材料去除率高。為了提高零件的可靠性和減輕重量,傳統的鉚接結構逐步被整體薄壁的機加工結構件所代替。這類零件多數採用整體實心鋁合金材料製成,70%~95%的材料要在加工中去除。如機身隔框毛坯是重達0.5t鋁合金鍛件,加工成薄壁整體結構框架時,重量僅有40kg左右。再次,薄壁、細筋結構件多,不能承受較大切削力。
(2)難加工材料的切削加工技術。
航空動力部門大量採用鎳基合金(如Inconel718)和鈦合金(如TiAl6V4)製造飛機發動機零件。對於這些難加工材料,目前國內的切削加工技術水平還比較低,僅少數企業開展了部分研究應用,切削速度僅能達到80~100m/min,還沒有在生產中大規模應用。
航空MJ加強外螺紋的最佳解決方案
對航空鈦合金、高溫合金MJ加強外螺紋而言,通用銑刀已不能很好地滿足零件的使用要求,而需要從設計、製造等環節提供最佳加工方案,其中涉及到選擇鎢鋼銑刀材料、改進鎢鋼銑刀工藝、選擇合適的切削速度等。滾壓法是一種塑性加工工藝,它在不破壞金屬纖維的前提下,使金屬體作出塑性位移,做到無切屑使金屬成形,這樣既能改善被加工螺紋的機械性能,也大大節約了航空航天零件用的特殊材料。外螺紋零件經滾壓塑性變形後,其強度和硬度都有所提高,而塑性則有所降低,螺紋部分的金屬纖維沒有被切斷,只是沿螺紋牙型發生了變形。經過滾壓的零件材料,材質比較緻密,且表面產生冷作硬化層,並存在殘餘壓應力,因而滾壓後零件的耐磨性有比較大的提高,螺紋的疲勞強度可提高20%~40%.經過滾壓的零件,螺紋表面的粗糙度也大大提高,優異的表面質量可提高螺紋的循環強度。材料發生塑性變形後,隨著變形程度的增大,強度越來越高,因此滾壓出來的螺紋,其抗拉強度可提高20%~30%,抗剪強度提高5%.同時,MJ加強外螺紋對強度要求較高,採用金屬塑性變形原理滾壓螺紋的方法較好地解決了牙底為加大圓弧這一難題。因此航空航天企業鈦合金、高溫合金MJ加強外螺紋零件加工的最佳鎢鋼銑刀應選用滾絲輪。
對於許多航空航天的機加工而言,解決方案就是讓步。對於進給和速度,應謹慎行事。操作人員將假設出最差的加工環境,並對工具進行編程,降低穿過材料的速度。