難加工材料的銑削和鑽削加工
2020-04-03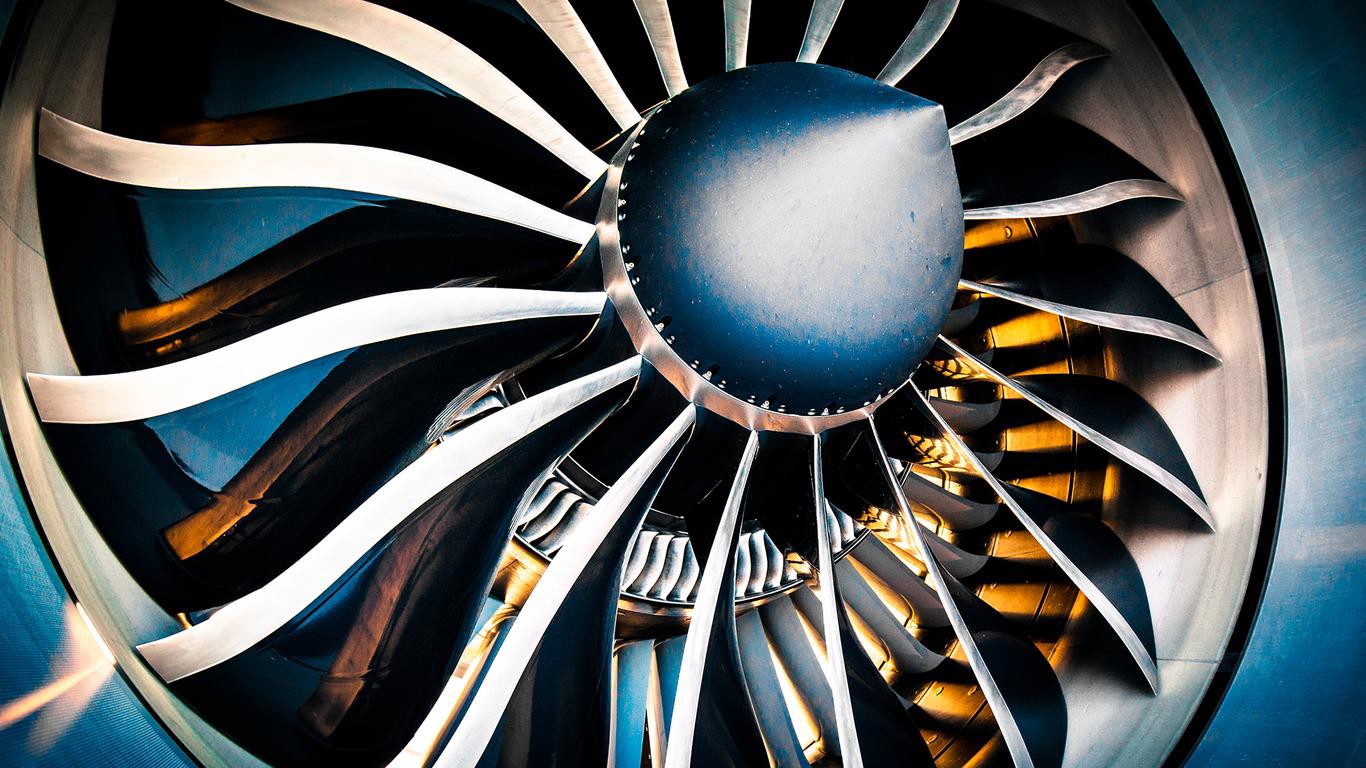
當前,減輕飛機重量這一目標正在促使航空航天工業採用越來越多的特種材料,如複合材料、鈦合金和鉻鎳鐵合金。相比普通材料,此類材料重量更輕、強度更高,但在加工方面,特別是銑削和鑽削方面,它們各自擁有不同的加工難題。在銑削和鑽削加工中,航空航天製造商通常使用整體硬質合金銑刀或整體高速鋼銑刀。在此類加工過程中,製造商必須儘可能達到最高的質量水平 - 這往往通過密切地監控和維護工藝安全性來實現。雖然存在對零件成本的擔憂,但在大多數情況下,生產完美的零件是優先考慮事項。
得益於工具機和銑刀技術,複合材料、鈦合金和鉻鎳鐵合金等材料已經從過去幾乎無法加工,發展到如今航空航天製造商能夠充滿信心地高效加工的階段。先進的特製整體銑刀和鑽頭能夠帶來更佳的工藝控制和一致性,這種銑刀專為克服此類材料的加工難題而開發。通過整合多種創新性鍍層和槽型,並配以先進的加工技術和方法,這些特製銑刀不僅能提供工藝安全性,而且能提高生產效率和產量。
碳纖維增強複合材料(CFRP)加工在航空航天工業中蓬勃發展。然而,由於此類材料極為耐磨和強韌,因此難以使用常規銑削銑刀進行加工。此外,加工時還必須防止發生分層,即各個碳纖維層分離。通過使用堅硬、鋒利且採用特殊表面鍍層的整體硬質合金銑刀,可以輕鬆應對這些挑戰。
常用的兩種鍍層工藝是物理氣相沉積(PVD)和化學氣相沉積 (CVD),此外還有一種高級切削材料多晶金剛石(PCD)。PVD鍍層屬於物理工藝,包括氮化鋁、氮化鉻和氮化鈦鍍層,其維氏硬度約為3000。通過化學工藝CVD形成的金剛石鍍層的硬度較PVD鍍層高出3倍以上,可達到10000維氏硬度等級。PCD銑刀採用整體PCD片,這些PCD片可通過銅焊固定到整體硬質合金基體上。
從槽型的角度來看,高效的複合材料銑刀採用低螺旋角來減小材料片層上承受的軸向力,以防止發生分層。此外,同時具有左螺旋和右螺旋的銑刀也是加工複合材料的高效槽型。此類銑刀通常被稱為壓縮銑刀,在側銑時,它們可將切削力導向到工件厚度的中心並進行壓縮,以保持片層完好無損。不僅如此,此類銑刀槽型還有利於更靈活地切削複合材料。
雖然壓縮銑刀是一種常用方法,但WOTEK等銑刀公司開發了具有不同新槽型(如雙螺旋)的壓縮銑刀。例如,WOTEK開發了兩款這種類型的雙螺旋壓縮銑刀。一款具有較少的刀刃,可提供更大的切屑間隙,而且其切削刃上還有斷屑槽,主要用於粗加工(圖1);另一款為無斷屑槽的具有平滑切削刃的多刃銑刀,可以提供理想的精加工性能。
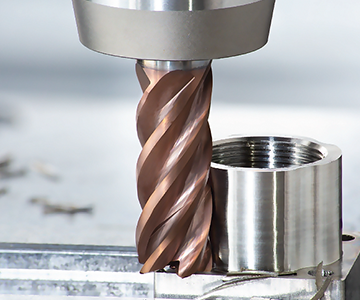
就加工技術而言,複合材料的切削參數通常取決於材料自身。用於複合材料的整體硬質合金銑刀的典型速度約為150m/min,而進給率約為0.07mm。但要注意,在這組材料中使用了不同類型的粘接劑,而每種粘接劑都需要各自不同的速度和進給率。這些粘接劑的熔點通常決定切削複合材料時的速度和進給率。此外,纖維含量和纖維方向也對加工工藝(決定切削速度、進給率和最佳銑刀路徑)有著顯著的影響。
在航空航天工業中,鈦合金通常用於3個基本應用領域:飛機結構件、噴氣發動機的低溫段部件和起落架系統。一種常用的鈦合金是5553,屬於近-β相合金,通常用於製造起落架零件。TiAl6-4屬於α-β相合金,是應用最廣泛的鈦合金材料之一,尤其適用於製造結構件。
令鈦合金難以加工、具有較低可加工性能的主要因素是其較低的導熱性能、較高的粘著性和加工硬化等因素。鈦合金具有低導熱性,這意味著在切削過程中產生的熱量傳導到銑刀中,而不是被切屑從切削區帶走;鈦合金的高粘著性意味著切屑往往會粘在銑刀上,從而產生極長的切屑,而不是所希望的更易於排出的較短切屑;該材料的加工硬化性能會在加工時發生,導致材料表面由於加工產生的壓力效應而出現一層薄薄的硬化層。
雖然可以使用適合加工多種材料的通用型整體硬質合金銑刀對鈦合金進行加工,但那些針對鈦合金的加工特性而專門設計的銑刀一般會提供更出色的加工效果。此類特殊的銑刀具有極佳的性能,但在處理多種不同材料時,其通用性可能較差。
例如,WOTEK的方案中有專為鈦合金和不鏽鋼而設計的高速鋼(HSS)銑刀。WOTEK HPM(高性能加工)系列中的部分銑刀也是專為鈦合金等特定材料牌號設計的。此類銑刀採用了特殊的槽型和設計,特別適合加工鈦合金。其槽型和設計包括40°~50°之間的大螺旋角;內冷通道,可使切屑不會粘到刀刃上並快速排屑,同時還有助於冷卻切削區;不均等的齒距,可在高切深過程中減少振動;將硬質合金與氮化鋁鉻鍍層相結合。未使用氮化鈦,這可防止銑刀和材料之間發生化學反應。
一些特定因素可決定是使用整體硬質合金銑刀還是使用HSS銑刀,而主要因素是刀體直徑。當應用場合要求使用更小直徑的銑刀時,當工件幾何形狀極為複雜時,或如果需要大切深(ap)時,應使用整體硬質合金銑刀。
對於複雜性較低的大批量工件,如果要求大切寬(ae)和大切深(ap),則建議使用HSS銑刀。當使用高扭矩和高馬力的舊式傳統工具機時,也應考慮使用此類銑刀。
在航空航天製造業中,鉻鎳鐵合金零件通常非常昂貴,不僅僅是材料本身的成本,還包括在進入加工階段前的生產時間。在進行了數小時甚至數天的加工後,如果零件報廢,則會帶來巨大的損失。
鉻鎳鐵合金和鈦合金之間存在某些相似之處。但就可加工性而言,鉻鎳鐵合金(鎳基高溫合金)是最難加工的材料。它們具有極低的導熱性和極高的應變硬化,甚至高於鈦合金。鉻鎳鐵合金還具有高粘著性,因此在用於傳統加工方法時,切削速度很少會超過25m/min或30m/min。用於加工鉻鎳鐵合金的銑刀槽型與用於鈦合金加工的槽型有很大的不同。鉻鎳鐵合金槽型具有非常陡的后角。這種槽型可最大限度減少銑刀和材料的接觸,因為鉻鎳鐵合金具有塑性和高記憶性,這意味著它會在受到銑刀的作用力時稍微彎曲。因此,銑刀傾角和材料的接觸時間越長,銑刀發生的磨蝕就越大,而其使用壽命就越短。為進一步降低銑刀和鉻鎳鐵合金間的摩擦,WOTEK採用了氮化鋁鈦鍍層。該鍍層已進行了拋光,擁有極其平滑精細的表面粗糙度。
鈦合金和鉻鎳鐵合金有4種基本的加工技術或方法。
(1)傳統加工,該方法需要在1×1的ae和ap之間尋求平衡,即加工採用全切寬(1倍直徑)、一定的切深(最大為刀體直徑1倍)和平均進給率。
(2)高性能加工(HPM),該方法需要使用專為鈦合金和鉻鎳鐵合金設計的銑刀,如WOTEK的HPM系列銑刀。這些銑刀在採用大切深ap(最大為1.5倍直徑)和 全切寬ae的情況下運行。在短時間內可切除大量金屬,從而提高生產率。
(3)高進給加工(HFM),該方法使用極小的軸向切深ap和全切寬ae,因此切寬為1倍直徑。該方法使用的特定銑刀槽型可將切削力引導到工具機主軸上,因此尤其適用於以下應用場合:因銑刀懸伸長和複雜應用(如深度為5倍直徑及以上的槽)而造成不穩定的加工工況。
(4)高速加工(HSM),該方法使用相當低的ae徑向切深和極大的ap切深。由於徑向切深相對較低,因此具有較小的接觸弧,這有助於減少切削區內產生的熱量(因接觸時間較短),從而允許較高的切削速度進行補償和提高生產率。
工具機和切削銑刀的發展使得這些方法得以實現。WOTEK的HPM銑刀槽型具有特殊特性,如不均等的齒距、彎曲的螺旋角,這為高性能加工方法提供了必要的穩定性。在高進給和高速加工中,這些方法通常依賴於工具機的能力和銑刀槽型。
對於航空航天應用,複合材料中的鑽孔必須完整,不允許有干涉和影響後續組件加工工序的粗糙或磨損的纖維。
複合材料鑽削的兩個常見難題是材料分層和纖維未切斷,特別是在工件的背側或出口側。鑽削時,銑刀的作用力向下壓材料,隨著鑽頭靠近出口側,過大的作用力會導致鑽頭生硬地擠破(而不是鑽削)孔的最後一部分。結果會造成複合材料纖維粗糙或磨損,而不是乾淨地切削,從而導致材料分層。
為了克服這些挑戰,銑刀公司通過在鑽頭上使用不同的鑽尖角和螺旋角來儘可能減小鑽頭在材料上施加的進給作用力。應注意,一些鑽頭槽型會產生與其他鑽頭相比更小的進給作用力,性能更出色。
例如,140°的鑽尖角(最常用於整體硬質合金鑽頭)在鑽削複合材料時非常適合鑽削多個孔。但只要銑刀變鈍就會失去效力。憑藉用於加工複合材料的C1金剛石鍍層整體硬質合金鑽頭,WOTEK提供了一個具有兩個鑽尖角(中心為130°,鑽頭倒角上為60°)的槽型。
加工時,鑽頭的中間點先從孔末端退出,切掉孔的部分材料。這樣,當60°部分退出時,鑽頭穿過材料的進給作用力會顯著減少。因此,材料分層和未切削的纖維(如果有)會更少。
除了2刃金剛石鍍層鑽頭外,WOTEK還為複合材料開發了一種獨特的3刃PCD尖鑽頭槽型(圖2)。這種新型PCD鑽頭槽型的工作條件與標準複合材料鑽頭相同,但其效果更好,因為它的切削刃更多(3刃)。鑽頭有更鋒利的切削刃且每轉產生的進給作用力更小,特別是在退孔時。此外,與金剛石鍍層相比,該鑽頭擁有完整的PCD鑽尖,在多數情況下銑刀壽命可延長多達4倍。
在航空航天領域,大多數孔徑都很小。對於小於1mm,最大不超過20mm的直徑,整體硬質合金鑽頭廣泛用於鈦合金和鉻鎳鐵合金的鑽削領域。
與銑削鈦合金一樣,鑽削工藝產生的熱量也易於進入銑刀中,而不是在切屑內帶走。為了解決這一問題,鑽頭槽型通常都具有非常鋒利的切削刃。通常,由於需要極為鋒利的切削刃,用於鈦合金的鑽頭都沒有鍍層。另外,鍍層在一定程度上會增加摩擦,增大了熱量生成。更重要的一點是,在加工後材料會收縮。因此,鑽體上需要一個更大的倒錐。
由於鉻鎳鐵合金具有非常強的磨蝕性和硬化性,因此用於該材料的高效鑽頭槽型基本上與用於鈦合金的鑽頭槽型相同。但是,該鑽頭槽型添加了鍍層,以便增加耐磨性並減小摩擦。例如,WOTEK使用氮化鈦鋁鍍層來保護其鉻鎳鐵合金鑽頭並延長使用壽命。
鑽削鉻鎳鐵合金時,需要使用較低的速度和進給量,因為該材料更硬、更難以切削。與銑削鉻鎳鐵合金一樣,在鑽削時,該材料的切削性能也會發揮作用。在航空航天應用領域中,鉻鎳鐵合金組件的孔深通常不超過3倍直徑。
鍍層在提高航空航天鑽削工藝安全性和生產率方面發揮著關鍵作用,WOTEK等銑刀公司一直致力於獲得更好的控制和掌握鑽頭切削刃的處理技術。通過鍍層的各種有效變化(如氮化鈦鋁)和對切削刃的控制,WOTEK已能夠開發出可將鑽削速度和進給率提升一倍的鑽頭。
將來會對現有槽型進行更多的改造,以進一步提高鑽頭性能。很多這些微小變化只有在當今先進工具機技術的幫助下才能實現或變為可能。每年進行數百萬鑽孔作業的航空航天製造商已經將他們的目光投向了這些特製鑽頭上。
要高效地加工航空航天業中目前遇到的挑戰性材料,關鍵是獲得完整的加工解決方案,而不僅僅是獲得一個產品。完整的銑刀解決方案不僅包括必要的槽型和設計,還包括應用工程支持。人員的豐富知識和經驗與先進的產品相結合,可以形成一個完整的解決方案並實現理想的結果。
零件質量和工藝安全性要求手頭上擁有專為特定應用(無論是複合材料、鈦合金、還是鉻鎳鐵合金)而設計的最佳銑刀。但是,該銑刀必須從能夠並且願意提供銑刀操作指導的供應商處獲取,以實現最優性能。為了充分利用當今專為堅韌的航空航天材料而設計的先進銑刀,教育和培訓是關鍵。
得益於工具機和銑刀技術,複合材料、鈦合金和鉻鎳鐵合金等材料已經從過去幾乎無法加工,發展到如今航空航天製造商能夠充滿信心地高效加工的階段。先進的特製整體銑刀和鑽頭能夠帶來更佳的工藝控制和一致性,這種銑刀專為克服此類材料的加工難題而開發。通過整合多種創新性鍍層和槽型,並配以先進的加工技術和方法,這些特製銑刀不僅能提供工藝安全性,而且能提高生產效率和產量。
銑削加工
1.複合材料
碳纖維增強複合材料(CFRP)加工在航空航天工業中蓬勃發展。然而,由於此類材料極為耐磨和強韌,因此難以使用常規銑削銑刀進行加工。此外,加工時還必須防止發生分層,即各個碳纖維層分離。通過使用堅硬、鋒利且採用特殊表面鍍層的整體硬質合金銑刀,可以輕鬆應對這些挑戰。常用的兩種鍍層工藝是物理氣相沉積(PVD)和化學氣相沉積 (CVD),此外還有一種高級切削材料多晶金剛石(PCD)。PVD鍍層屬於物理工藝,包括氮化鋁、氮化鉻和氮化鈦鍍層,其維氏硬度約為3000。通過化學工藝CVD形成的金剛石鍍層的硬度較PVD鍍層高出3倍以上,可達到10000維氏硬度等級。PCD銑刀採用整體PCD片,這些PCD片可通過銅焊固定到整體硬質合金基體上。
從槽型的角度來看,高效的複合材料銑刀採用低螺旋角來減小材料片層上承受的軸向力,以防止發生分層。此外,同時具有左螺旋和右螺旋的銑刀也是加工複合材料的高效槽型。此類銑刀通常被稱為壓縮銑刀,在側銑時,它們可將切削力導向到工件厚度的中心並進行壓縮,以保持片層完好無損。不僅如此,此類銑刀槽型還有利於更靈活地切削複合材料。
雖然壓縮銑刀是一種常用方法,但WOTEK等銑刀公司開發了具有不同新槽型(如雙螺旋)的壓縮銑刀。例如,WOTEK開發了兩款這種類型的雙螺旋壓縮銑刀。一款具有較少的刀刃,可提供更大的切屑間隙,而且其切削刃上還有斷屑槽,主要用於粗加工(圖1);另一款為無斷屑槽的具有平滑切削刃的多刃銑刀,可以提供理想的精加工性能。
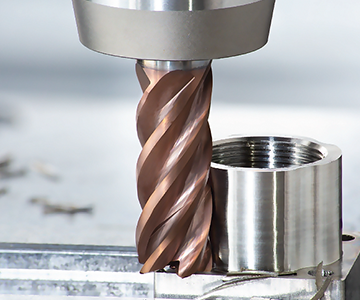
就加工技術而言,複合材料的切削參數通常取決於材料自身。用於複合材料的整體硬質合金銑刀的典型速度約為150m/min,而進給率約為0.07mm。但要注意,在這組材料中使用了不同類型的粘接劑,而每種粘接劑都需要各自不同的速度和進給率。這些粘接劑的熔點通常決定切削複合材料時的速度和進給率。此外,纖維含量和纖維方向也對加工工藝(決定切削速度、進給率和最佳銑刀路徑)有著顯著的影響。
2.鈦合金
在航空航天工業中,鈦合金通常用於3個基本應用領域:飛機結構件、噴氣發動機的低溫段部件和起落架系統。一種常用的鈦合金是5553,屬於近-β相合金,通常用於製造起落架零件。TiAl6-4屬於α-β相合金,是應用最廣泛的鈦合金材料之一,尤其適用於製造結構件。令鈦合金難以加工、具有較低可加工性能的主要因素是其較低的導熱性能、較高的粘著性和加工硬化等因素。鈦合金具有低導熱性,這意味著在切削過程中產生的熱量傳導到銑刀中,而不是被切屑從切削區帶走;鈦合金的高粘著性意味著切屑往往會粘在銑刀上,從而產生極長的切屑,而不是所希望的更易於排出的較短切屑;該材料的加工硬化性能會在加工時發生,導致材料表面由於加工產生的壓力效應而出現一層薄薄的硬化層。
雖然可以使用適合加工多種材料的通用型整體硬質合金銑刀對鈦合金進行加工,但那些針對鈦合金的加工特性而專門設計的銑刀一般會提供更出色的加工效果。此類特殊的銑刀具有極佳的性能,但在處理多種不同材料時,其通用性可能較差。
例如,WOTEK的方案中有專為鈦合金和不鏽鋼而設計的高速鋼(HSS)銑刀。WOTEK HPM(高性能加工)系列中的部分銑刀也是專為鈦合金等特定材料牌號設計的。此類銑刀採用了特殊的槽型和設計,特別適合加工鈦合金。其槽型和設計包括40°~50°之間的大螺旋角;內冷通道,可使切屑不會粘到刀刃上並快速排屑,同時還有助於冷卻切削區;不均等的齒距,可在高切深過程中減少振動;將硬質合金與氮化鋁鉻鍍層相結合。未使用氮化鈦,這可防止銑刀和材料之間發生化學反應。
一些特定因素可決定是使用整體硬質合金銑刀還是使用HSS銑刀,而主要因素是刀體直徑。當應用場合要求使用更小直徑的銑刀時,當工件幾何形狀極為複雜時,或如果需要大切深(ap)時,應使用整體硬質合金銑刀。
對於複雜性較低的大批量工件,如果要求大切寬(ae)和大切深(ap),則建議使用HSS銑刀。當使用高扭矩和高馬力的舊式傳統工具機時,也應考慮使用此類銑刀。
3.鉻鎳鐵合金
在航空航天製造業中,鉻鎳鐵合金零件通常非常昂貴,不僅僅是材料本身的成本,還包括在進入加工階段前的生產時間。在進行了數小時甚至數天的加工後,如果零件報廢,則會帶來巨大的損失。鉻鎳鐵合金和鈦合金之間存在某些相似之處。但就可加工性而言,鉻鎳鐵合金(鎳基高溫合金)是最難加工的材料。它們具有極低的導熱性和極高的應變硬化,甚至高於鈦合金。鉻鎳鐵合金還具有高粘著性,因此在用於傳統加工方法時,切削速度很少會超過25m/min或30m/min。用於加工鉻鎳鐵合金的銑刀槽型與用於鈦合金加工的槽型有很大的不同。鉻鎳鐵合金槽型具有非常陡的后角。這種槽型可最大限度減少銑刀和材料的接觸,因為鉻鎳鐵合金具有塑性和高記憶性,這意味著它會在受到銑刀的作用力時稍微彎曲。因此,銑刀傾角和材料的接觸時間越長,銑刀發生的磨蝕就越大,而其使用壽命就越短。為進一步降低銑刀和鉻鎳鐵合金間的摩擦,WOTEK採用了氮化鋁鈦鍍層。該鍍層已進行了拋光,擁有極其平滑精細的表面粗糙度。
4.鈦合金和鉻鎳鐵合金的加工方法
鈦合金和鉻鎳鐵合金有4種基本的加工技術或方法。(1)傳統加工,該方法需要在1×1的ae和ap之間尋求平衡,即加工採用全切寬(1倍直徑)、一定的切深(最大為刀體直徑1倍)和平均進給率。
(2)高性能加工(HPM),該方法需要使用專為鈦合金和鉻鎳鐵合金設計的銑刀,如WOTEK的HPM系列銑刀。這些銑刀在採用大切深ap(最大為1.5倍直徑)和 全切寬ae的情況下運行。在短時間內可切除大量金屬,從而提高生產率。
(3)高進給加工(HFM),該方法使用極小的軸向切深ap和全切寬ae,因此切寬為1倍直徑。該方法使用的特定銑刀槽型可將切削力引導到工具機主軸上,因此尤其適用於以下應用場合:因銑刀懸伸長和複雜應用(如深度為5倍直徑及以上的槽)而造成不穩定的加工工況。
(4)高速加工(HSM),該方法使用相當低的ae徑向切深和極大的ap切深。由於徑向切深相對較低,因此具有較小的接觸弧,這有助於減少切削區內產生的熱量(因接觸時間較短),從而允許較高的切削速度進行補償和提高生產率。
工具機和切削銑刀的發展使得這些方法得以實現。WOTEK的HPM銑刀槽型具有特殊特性,如不均等的齒距、彎曲的螺旋角,這為高性能加工方法提供了必要的穩定性。在高進給和高速加工中,這些方法通常依賴於工具機的能力和銑刀槽型。
鑽削加工
1.複合材料
對於航空航天應用,複合材料中的鑽孔必須完整,不允許有干涉和影響後續組件加工工序的粗糙或磨損的纖維。複合材料鑽削的兩個常見難題是材料分層和纖維未切斷,特別是在工件的背側或出口側。鑽削時,銑刀的作用力向下壓材料,隨著鑽頭靠近出口側,過大的作用力會導致鑽頭生硬地擠破(而不是鑽削)孔的最後一部分。結果會造成複合材料纖維粗糙或磨損,而不是乾淨地切削,從而導致材料分層。
為了克服這些挑戰,銑刀公司通過在鑽頭上使用不同的鑽尖角和螺旋角來儘可能減小鑽頭在材料上施加的進給作用力。應注意,一些鑽頭槽型會產生與其他鑽頭相比更小的進給作用力,性能更出色。
例如,140°的鑽尖角(最常用於整體硬質合金鑽頭)在鑽削複合材料時非常適合鑽削多個孔。但只要銑刀變鈍就會失去效力。憑藉用於加工複合材料的C1金剛石鍍層整體硬質合金鑽頭,WOTEK提供了一個具有兩個鑽尖角(中心為130°,鑽頭倒角上為60°)的槽型。
加工時,鑽頭的中間點先從孔末端退出,切掉孔的部分材料。這樣,當60°部分退出時,鑽頭穿過材料的進給作用力會顯著減少。因此,材料分層和未切削的纖維(如果有)會更少。
除了2刃金剛石鍍層鑽頭外,WOTEK還為複合材料開發了一種獨特的3刃PCD尖鑽頭槽型(圖2)。這種新型PCD鑽頭槽型的工作條件與標準複合材料鑽頭相同,但其效果更好,因為它的切削刃更多(3刃)。鑽頭有更鋒利的切削刃且每轉產生的進給作用力更小,特別是在退孔時。此外,與金剛石鍍層相比,該鑽頭擁有完整的PCD鑽尖,在多數情況下銑刀壽命可延長多達4倍。
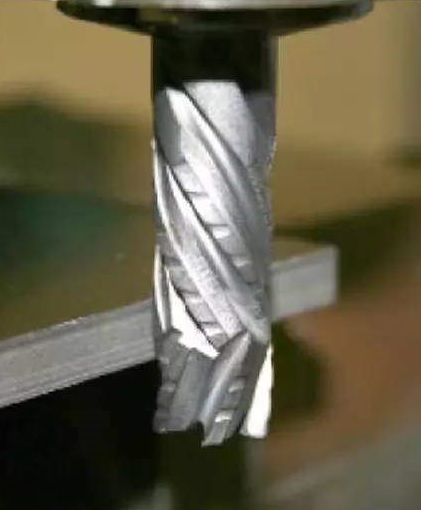
2.鈦合金
在航空航天領域,大多數孔徑都很小。對於小於1mm,最大不超過20mm的直徑,整體硬質合金鑽頭廣泛用於鈦合金和鉻鎳鐵合金的鑽削領域。與銑削鈦合金一樣,鑽削工藝產生的熱量也易於進入銑刀中,而不是在切屑內帶走。為了解決這一問題,鑽頭槽型通常都具有非常鋒利的切削刃。通常,由於需要極為鋒利的切削刃,用於鈦合金的鑽頭都沒有鍍層。另外,鍍層在一定程度上會增加摩擦,增大了熱量生成。更重要的一點是,在加工後材料會收縮。因此,鑽體上需要一個更大的倒錐。
3.鉻鎳鐵合金
由於鉻鎳鐵合金具有非常強的磨蝕性和硬化性,因此用於該材料的高效鑽頭槽型基本上與用於鈦合金的鑽頭槽型相同。但是,該鑽頭槽型添加了鍍層,以便增加耐磨性並減小摩擦。例如,WOTEK使用氮化鈦鋁鍍層來保護其鉻鎳鐵合金鑽頭並延長使用壽命。鑽削鉻鎳鐵合金時,需要使用較低的速度和進給量,因為該材料更硬、更難以切削。與銑削鉻鎳鐵合金一樣,在鑽削時,該材料的切削性能也會發揮作用。在航空航天應用領域中,鉻鎳鐵合金組件的孔深通常不超過3倍直徑。
鍍層在提高航空航天鑽削工藝安全性和生產率方面發揮著關鍵作用,WOTEK等銑刀公司一直致力於獲得更好的控制和掌握鑽頭切削刃的處理技術。通過鍍層的各種有效變化(如氮化鈦鋁)和對切削刃的控制,WOTEK已能夠開發出可將鑽削速度和進給率提升一倍的鑽頭。
將來會對現有槽型進行更多的改造,以進一步提高鑽頭性能。很多這些微小變化只有在當今先進工具機技術的幫助下才能實現或變為可能。每年進行數百萬鑽孔作業的航空航天製造商已經將他們的目光投向了這些特製鑽頭上。
結語
要高效地加工航空航天業中目前遇到的挑戰性材料,關鍵是獲得完整的加工解決方案,而不僅僅是獲得一個產品。完整的銑刀解決方案不僅包括必要的槽型和設計,還包括應用工程支持。人員的豐富知識和經驗與先進的產品相結合,可以形成一個完整的解決方案並實現理想的結果。
零件質量和工藝安全性要求手頭上擁有專為特定應用(無論是複合材料、鈦合金、還是鉻鎳鐵合金)而設計的最佳銑刀。但是,該銑刀必須從能夠並且願意提供銑刀操作指導的供應商處獲取,以實現最優性能。為了充分利用當今專為堅韌的航空航天材料而設計的先進銑刀,教育和培訓是關鍵。