Milling and drilling of difficult to cut materials
2020-04-03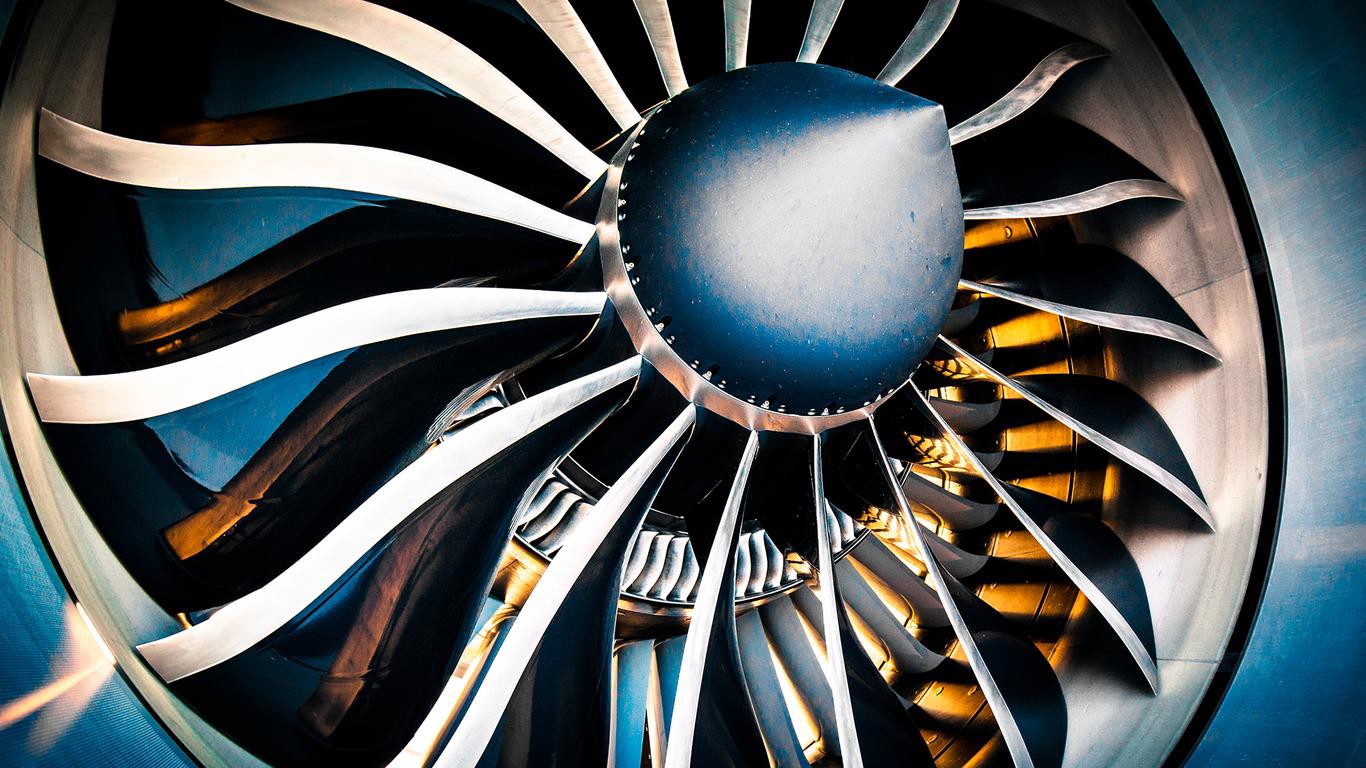
Currently, the goal of reducing aircraft weight is prompting the aerospace industry to adopt more and more specialty materials, such as composites, titanium alloys and chrome-nickel-iron alloys. Such materials are lighter in weight and stronger than ordinary materials, but they each have different machining difficulties when it comes to machining, especially milling and drilling. In milling and drilling operations, aerospace manufacturers typically use integral carbide end mills or integral high-speed steel end mills. In such processes, manufacturers must achieve the highest possible level of quality - often through close monitoring and maintaining process safety. While there are concerns about the cost of parts, in most cases, producing perfect parts is a priority.
Thanks to tooling machines and milling technology, materials such as composites, titanium alloys and chrome-nickel-iron alloys have evolved from being virtually impossible to process in the past to a stage where aerospace manufacturers are now able to process them with confidence and efficiency. Advanced, purpose-built monobloc end mills and drills that bring better process control and consistency have been developed to overcome the processing challenges of these materials. By integrating a variety of innovative coatings and grooves with advanced machining techniques and methods, these special end mills provide not only process safety, but also increased production efficiency and yield.
Carbon fiber reinforced composites (CFRP) processing is booming in the aerospace industry. However, because such materials are extremely wear-resistant and strong, they are difficult to machine with conventional solid end mills. In addition, the processing must prevent the occurrence of stratification, i.e. separation of the various carbon fiber layers. These challenges can be easily met by using hard, sharp, integral carbide cutters with a special surface coating.
The two commonly used coating processes are physical vapor deposition (PVD) and chemical vapor deposition (CVD), in addition to polycrystalline diamond (PCD), an advanced cutting material.PVD coatings are physical processes, including aluminum nitride, chromium nitride and titanium nitride, and have a hardness of approximately 3000 Vickers. Chemically formed CVD coatings are more than three times harder than PVD coatings, reaching a hardness rating of 10,000 Vickers.PCD cutters use integral PCD sheets, which can be fixed to an integral carbide matrix by copper welding.
For slotting, the efficient composite material cutter uses a low helix angle to reduce the axial forces on the material sheet to prevent delamination from occurring. Beside, solid end mills with both left and right spirals are also efficient groove types for processing composites. These cutters are often referred to as compression cutters, and in side milling they direct the cutting force to the center of the workpiece thickness and compress it to keep the sheet intact. Not only that, this type of solid end mill type also facilitates more flexible cutting of composite materials.
Although compression end mills are a common method, end mills companies such as WOTEK have developed compression end mills with different new groove types (e.g. double helix). For example, WOTEK has developed two versions of this type of double spiral compression cutter. One has fewer cutting edges to provide greater chip clearance and has a chipbreaker on the cutting edge, primarily for roughing (Figure 1); the other is a multi-flute solid end mill with a smooth cutting edge without a chipbreaker, which provides ideal finishing performance.
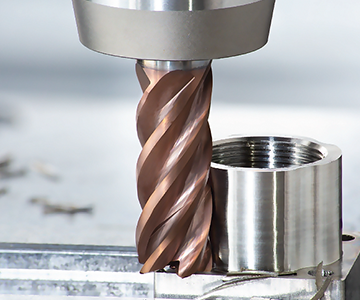
Overall machining, the cutting parameters of the composite material usually depend on the material itself. The typical speed of an overall carbide cutter used for composite materials is about 150m/min and the feed rate is about 0.07mm. However, that different types of adhesives are used in this group of materials, and each requires its own different speed and feed rate. The melting point of these adhesives usually determines the speed and feed rate when cutting composites. In addition, fiber content and fiber orientation have a significant impact on the machining process (determining cutting speed, feed rate and optimal milling path).
In the aerospace industry, titanium alloys are commonly used in three basic application areas: aircraft structural components, low-temperature segment components for jet engines, and landing gear systems. A commonly used titanium alloy is 5553, which is a near-β-phase alloy and is commonly used in the manufacture of landing gear parts. TiAl6-4 is an alpha-β-phase alloy and is one of the most widely used titanium alloys, especially for the manufacture of structural components.
The main factors that makes titanium alloys difficult to milling and have lower machinable properties are their lower thermal conductivity, higher adhesion and process hardening. Titanium alloy has low thermal conductivity, which means that the heat generated during the cutting process is transferred to the end mill rather than being carried away from the cutting area by the chips; the high adhesion of titanium alloy means that chips tend to stick to the end mill, resulting in extremely long chips rather than the shorter chips that are more easily discharged, as desired; the material's process-hardening properties occur during machining, resulting in a thin layer of hardening on the surface of the material due to the pressure effect of machining.
While titanium alloys can be machined with general-purpose integral carbide end mills that are suitable for a wide range of materials, those specifically designed for the machining characteristics of titanium alloys generally provide better results. This particular type of solid end mill has excellent performance, but can be less versatile when milling with many different materials.
For example, WOTEK's solutions include High Speed Steel (HSS) cutters designed for titanium and stainless steel, and some of the cutters in the WOTEK HPM (High Performance Machining) range are also designed for specific material grades such as titanium. This type of solid end mill has a special groove shape and design that is especially suitable for machining titanium alloys. Its grooves and design include large helix angles between 40° and 50°; internal cooling channels that keep chips from sticking to the edge and evacuate quickly, while also helping to cool the cutting area; uneven tooth spacing that reduces vibration during high depths of cut; and a combination of carbide and aluminum chrome nitride coating. Titanium nitride is not used, which prevents chemical reactions between the cutter and the material.
Some specific factors can determine whether to use an overall carbide end mill or HSS end mill, and the main factor is the diameter of the cutter body. When the application requires a smaller diameter end mill, when the workpiece geometry is extremely complex, or if a larger depth of cut (AP) is required, use an integral carbide end mill.
For high volume workpieces with less complexity, HSS solid end mills are recommended if large cut width (AE) and large cut depth (AP) are required. Such solid end mills should also be considered when using old conventional tool machines with high torque and horsepower.
In the aerospace manufacturing industry, chrome-nickel ferroalloy parts are often very expensive, not only in terms of the cost of the material itself, but also in terms of the production time before moving on to the processing stage. After hours or even days of machining, if the part is scrapped, it will be a huge loss.
There are certain similarities between chromium-nickel iron alloys and titanium alloys. However, in terms of machinability, chromium-nickel-iron alloys (nickel-based high-temperature alloys) are the most difficult materials to milling. They have very low thermal conductivity and very high strain hardening, even higher than titanium alloys. The solid end mill grooves used for chrome-nickel alloys are very different from those used for titanium alloys. The chrome-nickel ferro alloy slotted model has a very steep rear corner. This slotted type minimizes contact between the cutter and the material because the chrome-nickel ferrite alloy is plastic and highly memorable, which means it will bend slightly under the force of the cutter. Therefore, the longer the inclination of the solid end mill and the contact time of the material, the greater the abrasion that occurs in the solid end mill and the shorter its service life. To further reduce friction between solid end mills and chrome-nickel-iron alloys, WOTEK uses an aluminium titanium nitride coating. The coating has been polished and has an extremely smooth and fine surface finish.
There are four basic machining techniques or methods for titanium and chromium-nickel-iron alloys.
(1) For conventional machining, the method requires seeking a balance between 1×1 AE and AP, i.e. machining using a full cut width (1x diameter), a certain depth of cut (up to 1x the diameter of the cutter body) and an average feed rate.
(2) High Performance Machining (HPM), which requires the use of solid end mills designed for titanium and chrome-nickel alloys, such as WOTEK's HPM series of solid end mills. These cutters run with a large cut depth AP (up to 1.5x diameter) and full cut width AE. Large amounts of metal can be removed in a short period of time, thereby increasing productivity.
(3) High Feed Machining (HFM), which uses a very small axial depth of cut AP and full cutting width AE, so the cutting width is 1 times the diameter. The method uses a specific end mill slot type that directs the cutting force to the spindle of the tooling machine and is therefore particularly suitable for applications where the overhang of the end mill and complex applications such as grooves with depths of 5 times the diameter or more create unstable machining conditions.
(4) High speed machining (HSM), which uses a fairly low AE radial cutting depth and an extremely large AP cutting depth. The relatively low radial depth of cut has a smaller contact arc, which helps to reduce the amount of heat generated in the cutting area (due to the shorter contact time), thus allowing for higher cutting speed compensation and increased productivity.
The development of tooling machines and cutting mills has made these methods possible, and WOTEK's HPM solid end mills have special features, such as uneven tooth spacing and curved helix angles, which provide the necessary stability for high-performance machining methods. In high feed and high speed machining, these methods often rely on the capabilities of the tooling machine and the slotted shape of the solid end mill.
For aerospace applications, the holes drilled in the composite must be complete and not allow for roughing or worn fibers that interfere with and affect subsequent component machining processes.
Two common problems with compound material drilling are material delamination and uncut fibers, especially on the back or exit side of the workpiece. When drilling, the force of the mill presses down on the material, and as the drill moves closer to the exit side, too much force can cause the drill to squeeze through (rather than drill) the last part of the hole raw. The result is that the composite material fibers are rough or worn rather than cleanly cut, resulting in material delamination.
To overcome these challenges, solid end mill companies minimize the feed force exerted on the material by using different drill tip and spiral angles on the drill bit. It should be noted that some drill groove patterns produce a smaller feed force and better performance compared to others.
For example, 140° drill tip angle (most commonly used for overall carbide bits) is great for drilling multiple holes when drilling composites. But as soon as the cutter becomes dull, it loses its effectiveness. With the C1 diamond-coated integral carbide bit for machining composites, WOTEK offers a groove pattern with two drill-tip angles (130° on the center and 60° on the chamfer of the bit).
During machining, the midpoint of the drill bit exits first from the end of the hole, cutting off part of the hole material. In this way, when the 60° section exits, the feed force of the drill through the material is significantly reduced. As a result, there will be less material layering and less uncut fiber (if any).
In addition to the 2-blade diamond-coated drill, WOTEK has developed a unique 3-blade PCD-tip drill slot pattern for composites (Figure 2). This new PCD drill slot type operates under the same conditions as a standard composite drill, but with better results because it has more cutting edges (3 edges). The drill bit has a sharper cutting edge and produces less feed force per revolution, especially when releasing holes. In addition, the drill has a full PCD tip compared to the diamond coating, which in most cases extends the life of the mill up to four times.
In aerospace, most boreholes are small. For diameters less than 1mm and up to 20mm, the overall carbide drill is widely used in the drilling of titanium and chrome-nickel alloys.
Same as milling titanium, the heat generated by the drilling process easily enters the solid end mill rather than being carried away in the chips. To solve this problem, drill groove types usually have a very sharp cutting edge. Usually, the drill bits used for titanium are not coated due to the need for an extremely sharp cutting edge. In addition, the plating increases friction to some extent, increasing heat generation. More importantly, the material will shrink after processing. Therefore, a larger inverted cone is needed on the drill body.
Because of the very strong abrasive and hardening properties of chrome-nickel iron alloys, the efficient drill groove type used for this material is essentially the same as that used for titanium alloys. However, a plating layer was added to the slotted version of the drill to increase wear resistance and reduce friction. For example, WOTEK uses a titanium nitride aluminum coating to protect its chrome-nickel ferroalloy drill bits and extend their service life.
Drilling chrome-nickel-iron alloys requires the use of lower speeds and feeds because the material is harder and more difficult to cut. As with milling chrome-nickel-iron alloys, the material's cutting properties come into play when drilling. In aerospace applications, chrome-nickel-iron alloy assemblies typically have holes no deeper than three times the diameter.
Coating plays a key role in improving the safety and productivity of the aerospace drilling process, and milling tool companies such as WOTEK have been striving to gain better control and mastery of the cutting edge treatment of their drill bits. Through effective coating variations (e.g. titanium nitride) and control of the cutting edge, WOTEK has been able to develop drill bits that can double the drilling speed and feed rate.
More modifications will be made to the existing groove pattern in the future to further improve the performance of the drill bit. Many of these small changes can only be realized or made possible with the help of today's advanced tool machine technology. The aerospace manufacturers who conduct millions of holes each year have set their sights on these specialty drill bits.
The key to efficiently processing the challenging materials currently encountered in the aerospace industry is to obtain a complete processing solution, not just a product. A complete solid end mill solution includes not only the necessary grooves and designs, but also application engineering support. The extensive knowledge and experience of the personnel combined with the advanced products can form a complete solution and achieve the desired results.
Part quality and process safety require the best end mills on hand, designed for specific applications, whether composite, titanium, or chrome-nickel-iron. However, the cutter must be obtained from a supplier who is able and willing to provide guidance on the operation of the cutter in order to achieve optimum performance. In order to take advantage of today's advanced solid end mills designed for tough aerospace materials, education and training are key.
Thanks to tooling machines and milling technology, materials such as composites, titanium alloys and chrome-nickel-iron alloys have evolved from being virtually impossible to process in the past to a stage where aerospace manufacturers are now able to process them with confidence and efficiency. Advanced, purpose-built monobloc end mills and drills that bring better process control and consistency have been developed to overcome the processing challenges of these materials. By integrating a variety of innovative coatings and grooves with advanced machining techniques and methods, these special end mills provide not only process safety, but also increased production efficiency and yield.
Milling and machining
1. Composite materials
Carbon fiber reinforced composites (CFRP) processing is booming in the aerospace industry. However, because such materials are extremely wear-resistant and strong, they are difficult to machine with conventional solid end mills. In addition, the processing must prevent the occurrence of stratification, i.e. separation of the various carbon fiber layers. These challenges can be easily met by using hard, sharp, integral carbide cutters with a special surface coating.The two commonly used coating processes are physical vapor deposition (PVD) and chemical vapor deposition (CVD), in addition to polycrystalline diamond (PCD), an advanced cutting material.PVD coatings are physical processes, including aluminum nitride, chromium nitride and titanium nitride, and have a hardness of approximately 3000 Vickers. Chemically formed CVD coatings are more than three times harder than PVD coatings, reaching a hardness rating of 10,000 Vickers.PCD cutters use integral PCD sheets, which can be fixed to an integral carbide matrix by copper welding.
For slotting, the efficient composite material cutter uses a low helix angle to reduce the axial forces on the material sheet to prevent delamination from occurring. Beside, solid end mills with both left and right spirals are also efficient groove types for processing composites. These cutters are often referred to as compression cutters, and in side milling they direct the cutting force to the center of the workpiece thickness and compress it to keep the sheet intact. Not only that, this type of solid end mill type also facilitates more flexible cutting of composite materials.
Although compression end mills are a common method, end mills companies such as WOTEK have developed compression end mills with different new groove types (e.g. double helix). For example, WOTEK has developed two versions of this type of double spiral compression cutter. One has fewer cutting edges to provide greater chip clearance and has a chipbreaker on the cutting edge, primarily for roughing (Figure 1); the other is a multi-flute solid end mill with a smooth cutting edge without a chipbreaker, which provides ideal finishing performance.
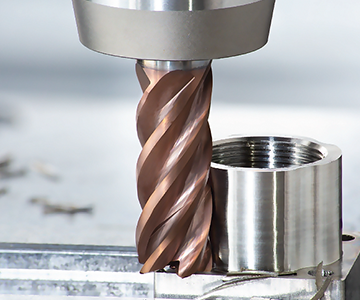
Overall machining, the cutting parameters of the composite material usually depend on the material itself. The typical speed of an overall carbide cutter used for composite materials is about 150m/min and the feed rate is about 0.07mm. However, that different types of adhesives are used in this group of materials, and each requires its own different speed and feed rate. The melting point of these adhesives usually determines the speed and feed rate when cutting composites. In addition, fiber content and fiber orientation have a significant impact on the machining process (determining cutting speed, feed rate and optimal milling path).
2.Titanium
In the aerospace industry, titanium alloys are commonly used in three basic application areas: aircraft structural components, low-temperature segment components for jet engines, and landing gear systems. A commonly used titanium alloy is 5553, which is a near-β-phase alloy and is commonly used in the manufacture of landing gear parts. TiAl6-4 is an alpha-β-phase alloy and is one of the most widely used titanium alloys, especially for the manufacture of structural components.The main factors that makes titanium alloys difficult to milling and have lower machinable properties are their lower thermal conductivity, higher adhesion and process hardening. Titanium alloy has low thermal conductivity, which means that the heat generated during the cutting process is transferred to the end mill rather than being carried away from the cutting area by the chips; the high adhesion of titanium alloy means that chips tend to stick to the end mill, resulting in extremely long chips rather than the shorter chips that are more easily discharged, as desired; the material's process-hardening properties occur during machining, resulting in a thin layer of hardening on the surface of the material due to the pressure effect of machining.
While titanium alloys can be machined with general-purpose integral carbide end mills that are suitable for a wide range of materials, those specifically designed for the machining characteristics of titanium alloys generally provide better results. This particular type of solid end mill has excellent performance, but can be less versatile when milling with many different materials.
For example, WOTEK's solutions include High Speed Steel (HSS) cutters designed for titanium and stainless steel, and some of the cutters in the WOTEK HPM (High Performance Machining) range are also designed for specific material grades such as titanium. This type of solid end mill has a special groove shape and design that is especially suitable for machining titanium alloys. Its grooves and design include large helix angles between 40° and 50°; internal cooling channels that keep chips from sticking to the edge and evacuate quickly, while also helping to cool the cutting area; uneven tooth spacing that reduces vibration during high depths of cut; and a combination of carbide and aluminum chrome nitride coating. Titanium nitride is not used, which prevents chemical reactions between the cutter and the material.
Some specific factors can determine whether to use an overall carbide end mill or HSS end mill, and the main factor is the diameter of the cutter body. When the application requires a smaller diameter end mill, when the workpiece geometry is extremely complex, or if a larger depth of cut (AP) is required, use an integral carbide end mill.
For high volume workpieces with less complexity, HSS solid end mills are recommended if large cut width (AE) and large cut depth (AP) are required. Such solid end mills should also be considered when using old conventional tool machines with high torque and horsepower.
3. Chrome-nickel-iron alloy
In the aerospace manufacturing industry, chrome-nickel ferroalloy parts are often very expensive, not only in terms of the cost of the material itself, but also in terms of the production time before moving on to the processing stage. After hours or even days of machining, if the part is scrapped, it will be a huge loss.There are certain similarities between chromium-nickel iron alloys and titanium alloys. However, in terms of machinability, chromium-nickel-iron alloys (nickel-based high-temperature alloys) are the most difficult materials to milling. They have very low thermal conductivity and very high strain hardening, even higher than titanium alloys. The solid end mill grooves used for chrome-nickel alloys are very different from those used for titanium alloys. The chrome-nickel ferro alloy slotted model has a very steep rear corner. This slotted type minimizes contact between the cutter and the material because the chrome-nickel ferrite alloy is plastic and highly memorable, which means it will bend slightly under the force of the cutter. Therefore, the longer the inclination of the solid end mill and the contact time of the material, the greater the abrasion that occurs in the solid end mill and the shorter its service life. To further reduce friction between solid end mills and chrome-nickel-iron alloys, WOTEK uses an aluminium titanium nitride coating. The coating has been polished and has an extremely smooth and fine surface finish.
4. Machining of titanium alloys and chromium-nickel-iron alloys
There are four basic machining techniques or methods for titanium and chromium-nickel-iron alloys.(1) For conventional machining, the method requires seeking a balance between 1×1 AE and AP, i.e. machining using a full cut width (1x diameter), a certain depth of cut (up to 1x the diameter of the cutter body) and an average feed rate.
(2) High Performance Machining (HPM), which requires the use of solid end mills designed for titanium and chrome-nickel alloys, such as WOTEK's HPM series of solid end mills. These cutters run with a large cut depth AP (up to 1.5x diameter) and full cut width AE. Large amounts of metal can be removed in a short period of time, thereby increasing productivity.
(3) High Feed Machining (HFM), which uses a very small axial depth of cut AP and full cutting width AE, so the cutting width is 1 times the diameter. The method uses a specific end mill slot type that directs the cutting force to the spindle of the tooling machine and is therefore particularly suitable for applications where the overhang of the end mill and complex applications such as grooves with depths of 5 times the diameter or more create unstable machining conditions.
(4) High speed machining (HSM), which uses a fairly low AE radial cutting depth and an extremely large AP cutting depth. The relatively low radial depth of cut has a smaller contact arc, which helps to reduce the amount of heat generated in the cutting area (due to the shorter contact time), thus allowing for higher cutting speed compensation and increased productivity.
The development of tooling machines and cutting mills has made these methods possible, and WOTEK's HPM solid end mills have special features, such as uneven tooth spacing and curved helix angles, which provide the necessary stability for high-performance machining methods. In high feed and high speed machining, these methods often rely on the capabilities of the tooling machine and the slotted shape of the solid end mill.
Drilling and Machining
1. Composite materials
For aerospace applications, the holes drilled in the composite must be complete and not allow for roughing or worn fibers that interfere with and affect subsequent component machining processes.Two common problems with compound material drilling are material delamination and uncut fibers, especially on the back or exit side of the workpiece. When drilling, the force of the mill presses down on the material, and as the drill moves closer to the exit side, too much force can cause the drill to squeeze through (rather than drill) the last part of the hole raw. The result is that the composite material fibers are rough or worn rather than cleanly cut, resulting in material delamination.
To overcome these challenges, solid end mill companies minimize the feed force exerted on the material by using different drill tip and spiral angles on the drill bit. It should be noted that some drill groove patterns produce a smaller feed force and better performance compared to others.
For example, 140° drill tip angle (most commonly used for overall carbide bits) is great for drilling multiple holes when drilling composites. But as soon as the cutter becomes dull, it loses its effectiveness. With the C1 diamond-coated integral carbide bit for machining composites, WOTEK offers a groove pattern with two drill-tip angles (130° on the center and 60° on the chamfer of the bit).
During machining, the midpoint of the drill bit exits first from the end of the hole, cutting off part of the hole material. In this way, when the 60° section exits, the feed force of the drill through the material is significantly reduced. As a result, there will be less material layering and less uncut fiber (if any).
In addition to the 2-blade diamond-coated drill, WOTEK has developed a unique 3-blade PCD-tip drill slot pattern for composites (Figure 2). This new PCD drill slot type operates under the same conditions as a standard composite drill, but with better results because it has more cutting edges (3 edges). The drill bit has a sharper cutting edge and produces less feed force per revolution, especially when releasing holes. In addition, the drill has a full PCD tip compared to the diamond coating, which in most cases extends the life of the mill up to four times.
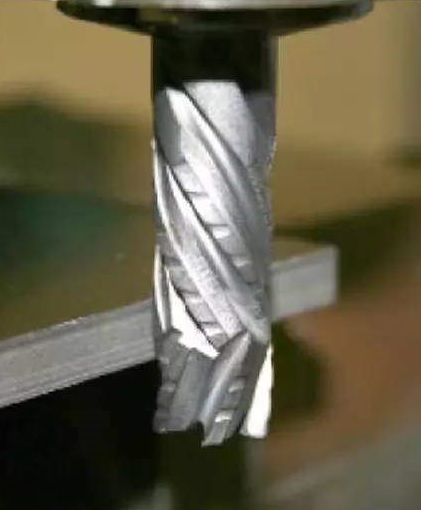
2.Titanium
In aerospace, most boreholes are small. For diameters less than 1mm and up to 20mm, the overall carbide drill is widely used in the drilling of titanium and chrome-nickel alloys.Same as milling titanium, the heat generated by the drilling process easily enters the solid end mill rather than being carried away in the chips. To solve this problem, drill groove types usually have a very sharp cutting edge. Usually, the drill bits used for titanium are not coated due to the need for an extremely sharp cutting edge. In addition, the plating increases friction to some extent, increasing heat generation. More importantly, the material will shrink after processing. Therefore, a larger inverted cone is needed on the drill body.
3. Chrome-nickel-iron alloy
Because of the very strong abrasive and hardening properties of chrome-nickel iron alloys, the efficient drill groove type used for this material is essentially the same as that used for titanium alloys. However, a plating layer was added to the slotted version of the drill to increase wear resistance and reduce friction. For example, WOTEK uses a titanium nitride aluminum coating to protect its chrome-nickel ferroalloy drill bits and extend their service life.Drilling chrome-nickel-iron alloys requires the use of lower speeds and feeds because the material is harder and more difficult to cut. As with milling chrome-nickel-iron alloys, the material's cutting properties come into play when drilling. In aerospace applications, chrome-nickel-iron alloy assemblies typically have holes no deeper than three times the diameter.
Coating plays a key role in improving the safety and productivity of the aerospace drilling process, and milling tool companies such as WOTEK have been striving to gain better control and mastery of the cutting edge treatment of their drill bits. Through effective coating variations (e.g. titanium nitride) and control of the cutting edge, WOTEK has been able to develop drill bits that can double the drilling speed and feed rate.
More modifications will be made to the existing groove pattern in the future to further improve the performance of the drill bit. Many of these small changes can only be realized or made possible with the help of today's advanced tool machine technology. The aerospace manufacturers who conduct millions of holes each year have set their sights on these specialty drill bits.
Conclusion
The key to efficiently processing the challenging materials currently encountered in the aerospace industry is to obtain a complete processing solution, not just a product. A complete solid end mill solution includes not only the necessary grooves and designs, but also application engineering support. The extensive knowledge and experience of the personnel combined with the advanced products can form a complete solution and achieve the desired results.
Part quality and process safety require the best end mills on hand, designed for specific applications, whether composite, titanium, or chrome-nickel-iron. However, the cutter must be obtained from a supplier who is able and willing to provide guidance on the operation of the cutter in order to achieve optimum performance. In order to take advantage of today's advanced solid end mills designed for tough aerospace materials, education and training are key.