提高無鉛黃銅合金的加工性能
2020-05-31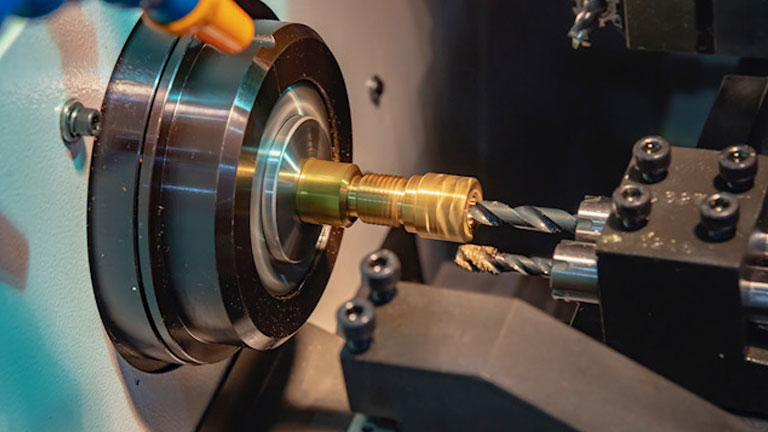
摘要
本文涉及無鉛黃銅合金的加工性的基礎研究。分析了微結構和矽作為合金元素對切屑形成、切削力、刀具溫度和刀具磨損的影響。在此基礎上,研究了提高加工性的各種方法,以實現高性能切削加工。本文重點研究了TiB2、DLC和金剛石等各種刀具塗層對磨料和黏性刀具磨損的影響。除了刀具磨損的顯著降低外,通過對刀具塗層的調整,實現了無鉛黃銅合金的乾式車削。此外,還對PCD刀具的性能和高壓冷卻液供應策略進行了研究。
1.導言
黃銅合金具有高導熱性、高導電性和出色的抗菌性能,因此被廣泛應用於電子電氣、汽車、衛生行業等各個行業。由於在製造黃銅零件時需要大量的切削加工,因此通常會在黃銅中加入不同的合金元素來提高加工性。在這種情況下,最重要的元素是鉛,它可以提高切削性,使其具有優良的斷屑率、低刀具磨損和高適用切削參數。這些方面可以用兩個基本現象來解釋。首先,鉛在黃銅中的溶解度很低,因此,鉛在整個微觀結構中,特別是在晶界處會發生偏析。因此,剪切強度明顯降低,導致斷屑現象非常好。其次,鉛的熔化溫度Tm=327.5℃,鉛的熔化溫度很低。在切削過程中,薄的半流體鉛膜可以減少摩擦力,從而減少切削力和刀具磨損。
然而,近年來,世界各國保護健康和環境的立法已經嚴立。由於鉛是一種危險的重金屬,因此鉛在銅合金中的使用受到限制。根據國家和應用的不同,銅合金中的鉛含量上限為0.1%(2011/55/EU[RoHS]指令、2000/53/EC[ELV]指令)至0.25%(美國《安全飲用水法》)。迄今為止,在許多情況下(如RoHS、ELV)的特殊規定仍然有效,允許銅合金中的鉛含量為4%。然而,這些特殊規定的必要性在某些時期受到政治的製約。與含鉛合金相比,無鉛黃銅的可加工性明顯比含鉛合金差,因為會形成長切屑,降低刀具壽命,導致生產率和工藝穩定性低。過去發現,添加硒和鉍以及石墨可以提高無鉛黃銅的加工性。
但是,該材料的製造工藝非常複雜,成本較高。此外,鉍的供應量有限。因此,這些材料的使用不可能大規模生產。大多數關於市售無鉛黃銅合金的研究是在二十多年前進行的。近年來,在法律規定的改變驅動下,開發出了新的無鉛黃銅合金,以滿足法律規定的最大含鉛量要求。在之前的研究工作中,這些材料的可加工性©2014年由Elsevier B.V.出版社出版。CC BY-NC-ND 許可下的開放訪問。第6屆CIRP國際高性能切削國際會議國際科學委員會負責的選題和同行評審工作,沒有對這些材料的可加工性進行過系統、全面的研究。因此,本文分析了當今市售無鉛黃銅合金的微觀結構和矽作為替代合金元素對加工性的影響。在此基礎上,研究了提高加工性的各種方法,以實現高性能的切削加工,特別是大規模生產。
2. 工件材料
研究了無鉛黃銅合金CW508L、CW511L和CW510L以及矽合金特殊黃銅CW724R的加工性能,並將其與含鉛黃銅CW614N(名稱:EN編碼)的加工性能進行了比較。所有材料都是通過連鑄、棒材擠壓(熱擠壓)和拉擠(冷擠壓)的方式製造的。材料的化學成分如表1所示。銅和鋅的百分比分別對微觀結構和加工性能起著決定性的作用。一般來說,鋅含量高達37.5%的黃銅合金幾乎完全由Į相組成。這些α-相位的晶格結構是面心立方體(fcc),因此,含有大量的Į相的黃銅具有低硬度和高延展性。這適用於CW508L和CW511L這兩種合金,其α相位含量為90-98%,見圖1和表2。這兩種材料之間的巨大差異是剩餘的鉛含量為0.01%(CW508L)和0.18%(CW511L),見表1。增加鋅的含量超過38%,導致鋅的含量增加ȕ相的百分比。材料CW510L由42%的鋅含量組成,因此α-和β-相位的含量接近平衡,見圖1(d)和(e)。β-相位具有以體心為中心的立方晶格(bcc),其硬度和成形性比α-相位差很多。因此,CW510L的硬度和抗拉強度比CW508L和CW511L高,見表2。在本研究中,研究了兩種不同的CW510L合金,在Pb=0.07%(CW510L(A))和0.18%(CW510L(W))的含鉛量不同的情況下,以分析不同剩餘鉛含量的影響。
表1: 工件材料的化學成分
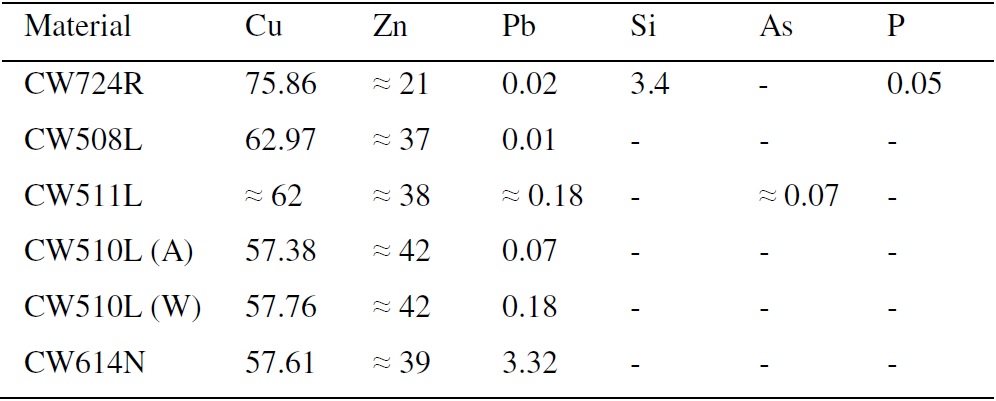
含鉛黃銅CW614N含有39%的鋅和3.32%的鉛,其微觀結構為70%的鋅相和30%的β相位。鉛幾乎不溶於黃銅,主要在晶界處析出,見圖1(f)。因此,剪切強度明顯降低,而斷裂伸長率與無鉛黃銅合金相似,表2。 CW724R是最近開發的一種特殊黃銅,其合金化矽含量為3.4%。由於鋅的含量較低,為21%,因此該材料具有約60%的高比例的Į相。此外,在微觀結構中還存在一種富含矽、脆性和高磨蝕性的ț相,導致材料具有較高的硬度和抗拉強度,表2。此外,金屬間化合物(γ相位)在晶界處有偏析,圖1(a)。
%20CW724R%20(b)%20CW508L.jpg)
圖1:圖中的微觀結構的橫截面圖(a) CW724R; (b) CW508L; (c) CW511L; (d) CW510L (A); (e) CW510L (W); (f) CW614N
表2: 工件材料的熱機械性能
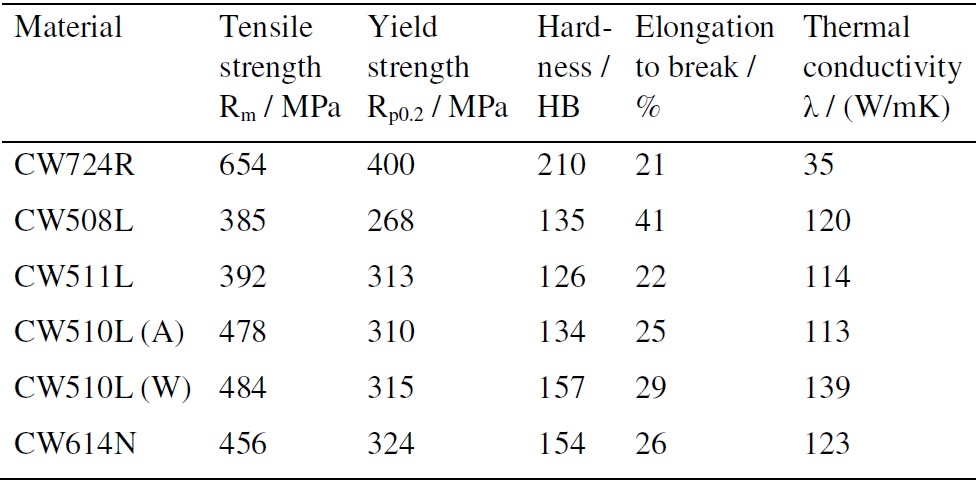
3. 顯微組織和合金元素對機械加工性的影響
不同無鉛黃銅合金的可加工性在數控車床Index GU 800,3.1、3.2節,以及自動車床Traub TNS 42,3.3節中的外部車削實驗中進行了研究。所有的實驗都是在潮濕的條件下進行的(乳化液Jokisch通用W5 RW TH,7%),主要使用硬質合金切削刀片。不同的切削參數、刀具幾何形狀和塗層被應用於粗加工和精加工條件下。邊界條件分別見圖2至6。
3.1. 切屑的形成
黃銅零件全自動量產的一個重要因素是通過優異的斷屑性能來提高工藝穩定性。在外部車削過程中,根據進給量f和切削深度ap的不同,對切屑的形成進行了研究,切削速度保持恆定在vc = 200 m/min。從高f和ap值開始,圖2表示從長切屑(1-5)到完全鬆散的弧形切屑(6.2)、元素切屑(7.1)或針形切屑(8.1)的交叉情況(根據ISO 3685: 1993的分類標準)。由於鉛(Pb = 3.32%)的正面作用,CW614N的最佳斷屑率被確定為最佳。與切削參數無關,只有針狀切屑(8.1)形成。黃銅中加入矽會導致微觀結構中形成脆性ț相。因此,特殊黃銅CW724R(Si = 3.4%)的特殊黃銅CW724R表現出比無矽和無鉛黃銅更好的斷屑效果。在大多數切削參數下,形成了短元素切屑(7.1)。然而,與含鉛的CW614N相比,在低f和ap時檢測到較長的切屑。
在無鉛黃銅和無矽黃銅中,CW510L(A)和CW510L(W)表現出比CW511L和CW508L更好的斷屑率,原因是脆性bcc β-階段性的比例更高,圖2。根據切削參數的不同,觀察到了元素型(7.1)或管狀切屑(2.1/2.2)的形成。鉛含量為0.18%的CW510L(W)比鉛含量為0.07%的CW510L(A)的斷屑率稍好。因此,可以得出結論,即使是微小的鉛含量差異也會影響切屑的形成。在所有材料中,CW508L的斷屑率最差,因為CW508L是由高比例的延展性 fcc α-相位造成的,與CW511L相比,殘餘鉛含量Pb = 0.01 %的CW511L的殘餘鉛含量較低。兩種材料,CW508L和CW511L都傾向於形成長管狀或鋸齒狀切屑(2.1/2.3)。只有在相對較高的f和ap條件下,才會形成短弧形或元素切屑(6.2/7.1)。
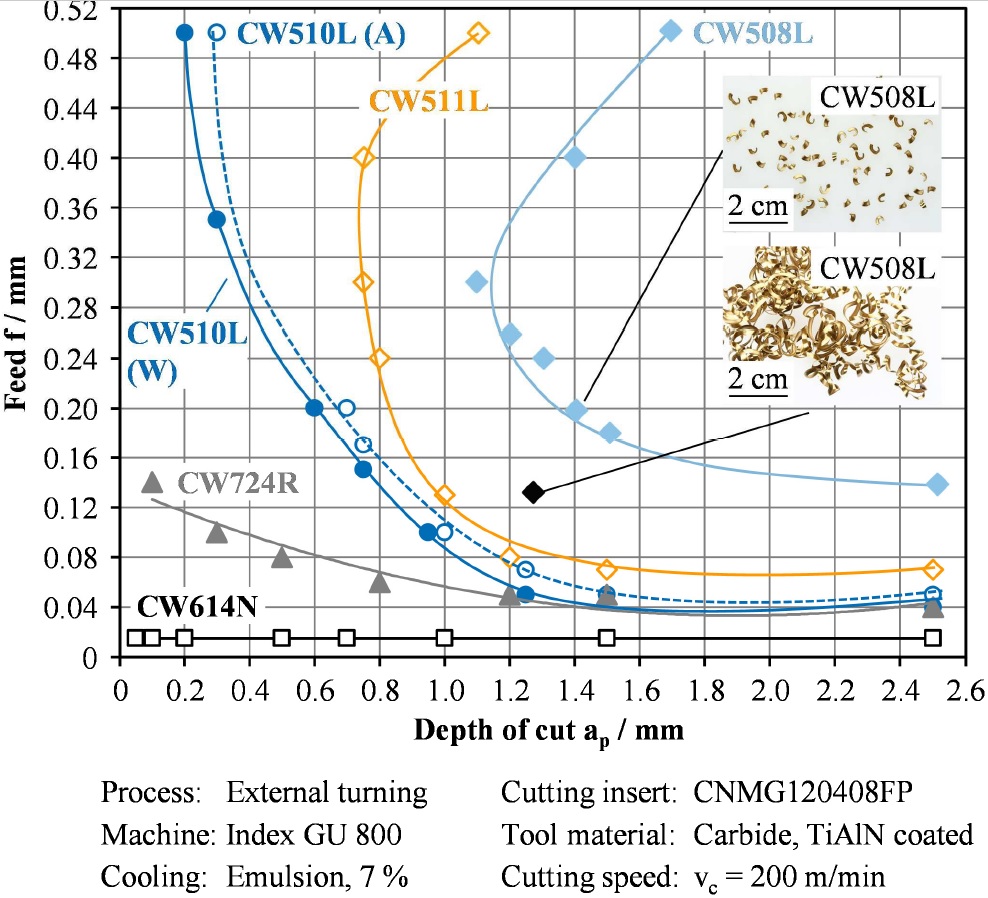
在無鉛黃銅和無矽黃銅中,CW510L(A)和CW510L(W)表現出比CW511L和CW508L更好的斷屑率,原因是脆性bcc β-階段性的比例更高,圖2。根據切削參數的不同,觀察到了元素型(7.1)或管狀切屑(2.1/2.2)的形成。鉛含量為0.18%的CW510L(W)比鉛含量為0.07%的CW510L(A)的斷屑率稍好。因此,可以得出結論,即使是微小的鉛含量差異也會影響切屑的形成。在所有材料中,CW508L的斷屑率最差,因為CW508L是由高比例的延展性 fcc α-相位造成的,與CW511L相比,殘餘鉛含量Pb = 0.01 %的CW511L的殘餘鉛含量較低。兩種材料,CW508L和CW511L都傾向於形成長管狀或鋸齒狀切屑(2.1/2.3)。只有在相對較高的f和ap條件下,才會形成短弧形或元素切屑(6.2/7.1)。
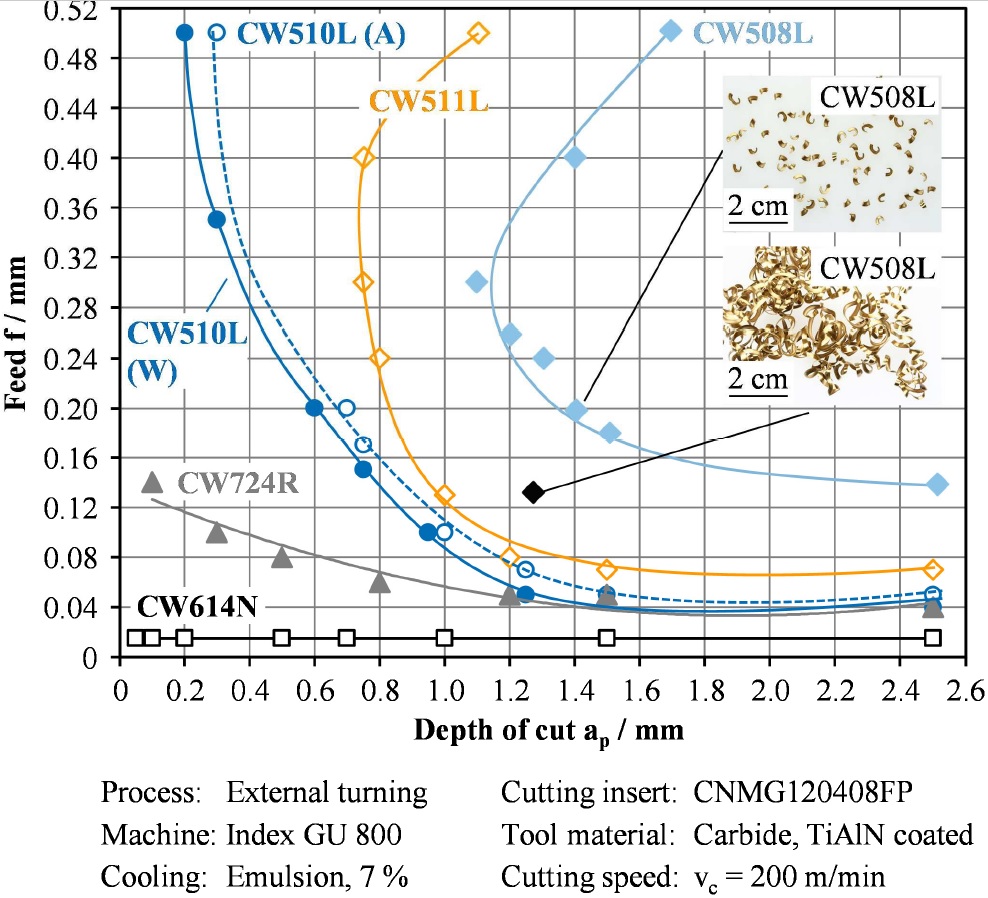
圖2: 黃銅合金的斷屑率取決於進給量和切削深度
除了切屑斷裂外,在切屑的形成機理方面也發現了巨大的差異。圖3比較了在相同的邊界條件下,在外部車削時產生的切屑的縱向橫截面。鉛能顯著降低切削區的摩擦力,因此,車削含鉛CW614N時,切屑厚度比接近1(Ȝh §1.2)。在這種情況下,由於材料的剪切強度較低,切屑在形成第一層後斷裂。當車削矽合金特殊黃銅CW724R時,由於脆性的 k-相位形成了不連續的切屑。切屑的厚度比和摩擦力都很低(ȜhȜh §1.2)。然而,巨大的切屑分割造成了高的加工動態,可能會導致工件表面的顫動痕跡或切削刃崩裂。在車削CW510L時形成了層狀切屑。由於缺乏鉛或矽等合金元素的影響,切削區的摩擦力較大,因此在切屑底面的微觀結構有明顯的變形。同樣,檢測到CW510L和CW510L兩種材料之間的差異,由於CW510L(A)的含鉛量較低,因此切屑厚度比較高(1.8,而CW510L的含鉛量為1.5)。在車削CW508L和CW511L時,確定了切屑底面微觀結構的最大變形。由於在CW508L和CW511L中,由於韌性 fcc α-相的量很大,所以形成了連續的切屑,並確定了這兩種材料的高切屑厚度比為2.8。
%20CW724R.jpg)
圖3:車削時的切屑形成機理(a)CW724R;(b)CW508L;(c)CW511L;(d)CW510L(A);(e)CW510L(W);(f)CW614N
3.2. 機械熱工具載荷
切屑形成機制和摩擦條件以及材料的機械性能的不同,高度影響切削力和溫度。具體的切削力kc1.1在寬度為b = 1毫米的未成形切屑和厚度為h = 1毫米的未成形切屑的厚度,以及具體的切削力1-mc的上升,計算出了Kienzle (Fc = kc1.1•b•h1-mc),見圖4 (a)。為此目的,切削力是通過一個3組份基斯勒平台9121型(濾波器:低通,頻率率:1千赫茲,採樣率100赫茲),在外部車削過程中測量。在f = 0.05 - 0.4 mm範圍內,切削刃半徑(rβ= 6微米)的影響可以忽略不計。此外,通過使用光纖雙色測溫儀在刀具內靠近切削刃的盲孔底部測量了溫度,見圖4(b)。測量點位於距離主刀面0.35毫米,最小距離耙面0.15毫米,直徑為0.5毫米。
為了防止因盲孔位置不同而產生誤差,所有的測量都使用相同的刀具。刀具磨損的影響可以忽略不計。所有的力和溫度測量都重複了兩次。對於有鉛黃銅CW614N,計算出的比切削力為kc1.1=392 N/mm2,刀具溫度為Tt=182 °C,圖4。相比之下,在車削無鉛黃銅和無矽黃銅時,比切削力和刀具溫度大約高兩到三倍。 CW508L的kc1.1值和刀具溫度最高(kc1.1 = 1221 N/mm2, Tt = 475 °C),儘管該材料的硬度和抗拉強度相對較低,見表2。與圖3所示的芯片壓縮和芯片底面微觀結構變形相關,假定高切削力和溫度可以由接觸區的高摩擦力來解釋,這是因為高比例的韌性 fcc α-相位和極低的鉛含量Pb = 0.01%導致的高切削力和溫度。
高含量的fccα-階段性,也導致了CW511L車削時的kc1.1值和刀具溫度較高(kc1.1=1129 N/mm2,Tt=455 °C)。然而,主要是由於鉛含量較高(Pb = 0.18 %),與CW508L相比,這兩個值都略低。 CW510L表現出更高的脆性bcc β-階段性,因此,與CW508L和CW511L相比,CW510L的硬度和強度都較高。然而,隨著摩擦和切屑壓縮的減少,計算出的kc1.1值較低(CW510(A):kc1.1=945 N/mm2;CW510(W):kc1.1=852 N/mm2)。 CW510L (W)的刀具溫度也是如此(Tt = 425°C),而CW510L (A)車削時的刀具溫度與CW508L和CW511L相同(Tt = 470°C)。因此,CW510L和CW510L材料在熱機械刀具負荷方面的加工性存在差異,主要是殘餘鉛含量不同。
%20Specific%20cutting%20force%20and%20the%20rise%20of%20specific%20cutting%20force.jpg)
%20Specific%20cutting%20force%20and%20the%20rise%20of%20specific%20cutting%20force.jpg)
為了防止因盲孔位置不同而產生誤差,所有的測量都使用相同的刀具。刀具磨損的影響可以忽略不計。所有的力和溫度測量都重複了兩次。對於有鉛黃銅CW614N,計算出的比切削力為kc1.1=392 N/mm2,刀具溫度為Tt=182 °C,圖4。相比之下,在車削無鉛黃銅和無矽黃銅時,比切削力和刀具溫度大約高兩到三倍。 CW508L的kc1.1值和刀具溫度最高(kc1.1 = 1221 N/mm2, Tt = 475 °C),儘管該材料的硬度和抗拉強度相對較低,見表2。與圖3所示的芯片壓縮和芯片底面微觀結構變形相關,假定高切削力和溫度可以由接觸區的高摩擦力來解釋,這是因為高比例的韌性 fcc α-相位和極低的鉛含量Pb = 0.01%導致的高切削力和溫度。
高含量的fccα-階段性,也導致了CW511L車削時的kc1.1值和刀具溫度較高(kc1.1=1129 N/mm2,Tt=455 °C)。然而,主要是由於鉛含量較高(Pb = 0.18 %),與CW508L相比,這兩個值都略低。 CW510L表現出更高的脆性bcc β-階段性,因此,與CW508L和CW511L相比,CW510L的硬度和強度都較高。然而,隨著摩擦和切屑壓縮的減少,計算出的kc1.1值較低(CW510(A):kc1.1=945 N/mm2;CW510(W):kc1.1=852 N/mm2)。 CW510L (W)的刀具溫度也是如此(Tt = 425°C),而CW510L (A)車削時的刀具溫度與CW508L和CW511L相同(Tt = 470°C)。因此,CW510L和CW510L材料在熱機械刀具負荷方面的加工性存在差異,主要是殘餘鉛含量不同。
%20Specific%20cutting%20force%20and%20the%20rise%20of%20specific%20cutting%20force.jpg)
%20Specific%20cutting%20force%20and%20the%20rise%20of%20specific%20cutting%20force.jpg)
圖4:(a)比切削力和比切削力的上升;(b)黃銅合金車削過程中的刀具溫度
在比較不同工件材料的切削過程中的刀具溫度時,材料的導熱性對工件和切屑以及刀具散失熱量的百分比起著決定性的作用。在這種情況下,所有的無矽黃銅合金的導熱係數都有相似的特點,從Ȝ=114 W/mK(CW511L)到139 W/mK(CW510L(W))之間的變化。因此,可以認為,被研究的無矽黃銅合金在車削過程中的刀具溫度差異不是由導熱係數不同造成的,而是由微觀結構不同造成的。相反,矽合金特種黃銅CW724R的導熱係數明顯較低(Ȝ=35 W/mK),這往往會導致在刀具中測得的溫度較高。然而,由於高比例的富矽ț相和由此產生的低摩擦和切屑壓縮,與所有無鉛黃銅和無矽黃銅合金相比,刀具溫度更低(Tt = 410℃)。同樣的影響對於低比切削力kc1.1=559 N/mm2的低比切削力也是至關重要的。然而,與含鉛的CW614N相比,可以說熱機械刀具載荷顯著增加。
3.3. 刀具磨損
為了分析較高的熱力學刀具載荷對刀具磨損的影響程度,在外圓車削時,每一種黃銅合金在vc=200 m/min、ap=1 mm和f=0.1 mm的條件下,使用TiAlN塗層硬質合金切削刀片進行外圓車削。然而,在這些條件下,在規定的切削時間tc=150分鐘後,刀具磨損差異不明顯。因此,為了增加刀具的負荷,在車削某些黃銅合金時採用了較高的進給量f = 0.3 mm,以增加刀具的負荷。在切削時間tc=100 min後,可以發現用於車削含鉛CW614N的切削刀片處的刀具磨損非常低,見圖5(d)。研磨片磨損和彈坑磨損幾乎無法檢測到。在極小的接觸區後面,只能看到一些高鋅含量的工件材料粘附物(根據EDX分析)。在這些黏附物的後面,刀具的基體在某些區域因撞擊切屑而暴露出來,但這並不影響切削過程。
%20CW724R.jpg)
%20CW724R.jpg)
%20CW724R.jpg)
%20CW724R.jpg)
圖5:車削時刀具磨損的SEM照片 (a) CW724R; (b) CW511L; (c) CW510L (A); (d) CW614N
相反,在車削無鉛黃銅合金CW511L和CW510L(A)後,側面和耙面上的強黏連明顯可見,見圖5(b)和(c)。這些黏附物可能會使工件的表面質量下降。此外,黏附的材料可能會拉出塗層和基體的顆粒,導致切削刃處崩裂。由於這種影響,CW510L(A)車削後,基體在轉角半徑末端的主要切削刃的小範圍內暴露出來。當使用非常鋒利的刀具加工小型黃銅零件時,發生崩邊的風險會更大。除了黏性刀具磨損外,加工CW511L和CW510L(A)後,磨料磨損也會增加。對於這兩種材料,測量到的是VB = 40 - 50 µm範圍內的側翼磨損地寬度。不過,這些區域的基體還沒有露出來。必須指出的是,為了更詳細地研究不同材料引起的磨俱磨損,切削時間必須大大增加。由於矽合金CW724R中的強脆性k-相位,與CW511L和CW510L(A)相比,接觸區和黏性刀具磨損明顯減少,見圖5(a)。但是,富含矽的k-相位具有較強的磨蝕性,因此,側翼磨損增加。側面磨損的寬度很難測量,但由於塗層的相干剝落發生。據推測,剝落主要是由工件材料的矽、塗層的鋁和大氣中的氧氣之間的化學反應引起的。通過EDX分析檢測到這些元素,得出了氧化矽鋁形成的結論。由於氧化鋁的體積較大,可能造成塗層內應力增大,從而導致剝落。此外,不連續的切屑形成,見圖3(a),以及由此產生的高工藝動態可能加劇了塗層的剝落。
工件表面質量的分析不是本文的重點。但可以歸納為:無鉛黃銅與有鉛的CW614N相比,車削後的表面粗糙度與有鉛的CW614N相近,而毛刺的形成隨著無鉛黃銅合金延展性的提高而增加。
%20TiAlN%3B%20(b)%20TiB2%3B%20(c)%20DLC.jpg)
%20TiAlN%3B%20(b)%20TiB2%3B%20(D)%20DLC.png)
圖6:車削CW510L時,塗有(a)TiAlN;(b)TiB2;(c)DLC;(d)金剛石的硬質合金刀片的刀具磨損(A)
與未塗層的硬質合金相比,TiAlN和TiB2塗層的工件材料在刀具上的附著力略有下降。但是,特別是在TiB2塗層的刀具的耙面上,通過光鏡觀察,仍然可以清楚地看到很強的材料附著力,見圖6(b)。相反,使用DLC塗層時,黏附傾向明顯降低。解釋不同結果的重要因素是塗層材料的表面粗糙度和摩擦係數。此外,由於DLC塗層的導熱性較高,切割區的溫度較低,可能會降低附著傾向。此外,TiB2塗層刀具的基體暴露在切削刃附近的耙面上,導致與未塗層的硬質合金刀具的附著力不相上下。與TiAlN和TiB2塗層相比,除黏著磨損外,DLC塗層也減少了磨料磨損,這主要是由於塗層材料的硬度和耐磨性較高。經測量,DLC塗層的側面磨損寬度僅為VB = 8 µm,而TiAlN塗層的VB為17 µm,TiB2塗層的VB為32 µm。
通過金剛石CVD塗層進一步提高了切削性能。如圖6(d)所示,沒有任何材料黏附在刀具的刀桿和刀面上。此外,金剛石塗層的硬度和耐磨性也非常高,因此幾乎沒有發現磨蝕性的側面磨損。在進一步的實驗中,金剛石塗層刀具在CW510L(A)乾式車削中得到了成功的應用。但是,金剛石塗層的缺點是,由於需要對基體進行預處理以及塗層厚度較高,因此切削刃圓度較高。所使用的金剛石塗層刀片的切削刃半徑(塗層厚度為8微米)被測得的切削刃半徑為rβ§15微米。在加工無鉛黃銅合金時,為了減少毛刺的形成和切削力,一般情況下,銳利的切削刃是首選。後者對於電子和汽車工業中的小型零件的製造尤其重要。對於這些應用,DLC塗層可能更適合,因為可以實現鋒利的切削刃(rβ § 4 - 5微米)。
作為硬質合金刀具的替代材料,多晶金剛石(PCD)由於其高耐磨性和低附著力,以及實現鋒利切削刃的可能性,被認為是很有前途的。因此,在CW510L(A)和矽合金CW724R的外圓車削中,使用了切削刃半徑僅為rβ§4微米、斜角為γ=10°的PCD刀片。在切削時間tc = 50 min,應用vc = 200 m/min,ap = 1 mm,f = 0.3 mm的切削時間後,均未發現磨料磨損和黏性刀具磨損。但是,在CW510L(A)和其他無鉛黃銅和無矽黃銅的情況下,由於工藝穩定性較低,形成長長的管狀切屑的趨勢阻礙了平坦的PCD刀片的批量生產。為此,應用了一種具有激光斷屑器幾何形狀的PCD刀具,可顯著改善斷屑率。但激光切割PCD刀片的製造成本較高,幾何形狀的靈活性有限。
作為替代方案,高壓冷卻液供應的應用是合理的。在這種供液策略下,通過使用特殊的刀架和切削刀片,冷卻液直接集中到刀具和切屑之間的楔子中。在以往的研究工作中,發現這種技術在使用平面PCD刀具時,對所有被研究的黃銅合金刀具都能實現良好的斷屑效果。
5. 結論和展望
本研究的第一個目的是分析無鉛黃銅合金的加工性。可以歸納為:與含鉛黃銅CW614N相比,形成的切屑較長,切削力和溫度較高,刀具磨損和黏性較高。這一點尤其適用於CW511L等含fcc α-相位含量較高的韌性黃銅合金。與無鉛黃銅相比,矽合金特種黃銅CW724R表現出了更好的加工性能,在斷屑率和熱機械刀具載荷方面表現出了更好的加工性能,但由於其K相位的磨蝕性,造成了更高的側面磨損。
在基礎研究的基礎上,討論了無鉛黃銅合金高性能切削的各種方法。通過使用類金剛石碳(DLC)PVD塗層和金剛石CVD塗層,與TiAlN和TiB2 PVD塗層以及未塗層的硬質合金相比,黏著性和磨蝕性磨損明顯降低。扁平PCD刀具表現出較高的耐磨性,但長切屑的形成阻礙了其批量生產。為了確保在使用硬質合金或PCD刀具時控制切屑的斷裂,提高工藝穩定性,提出了集中高壓冷卻液的應用。今後的研究將重點關注工件的表面質量,這不在本文的研究範圍內。此外,還將研究刀具宏觀幾何形狀的適應性,以確保無鉛黃銅合金高含量ccα-相位的斷屑。
致謝
感謝 "聯邦經濟和技術部(BMWi)"和 "AiF "對本研究項目的資助。