鎢鋼端銑刀高效能設計與研磨分析模式
2020-05-04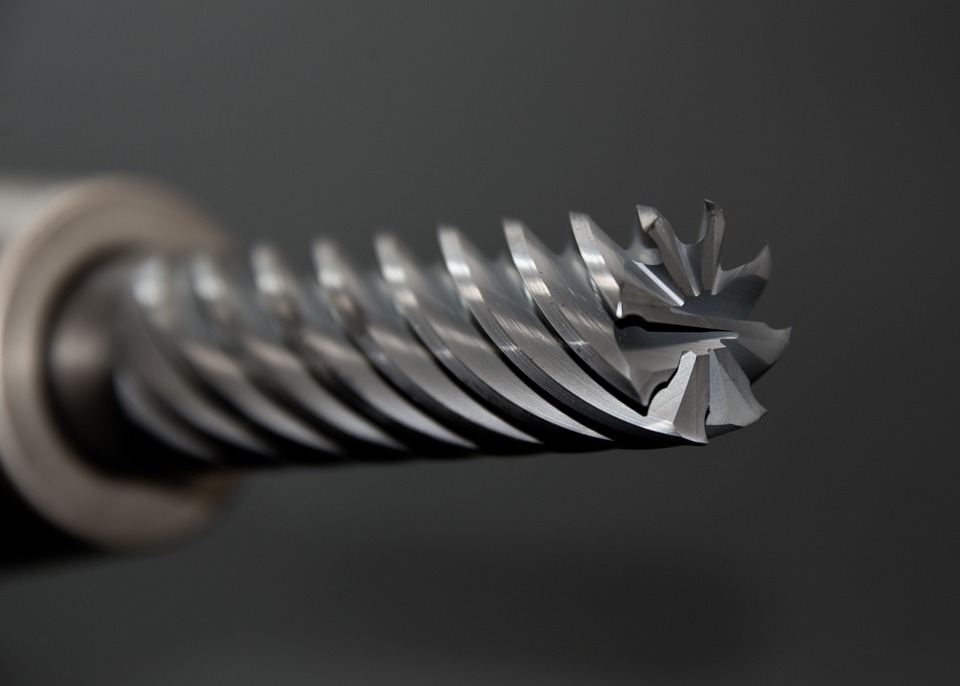
一、摘要
隨著半導體與微系統技術的進展,各種 3C/IA 等高科技產品之發展將走向高記憶容量及高功能性,因此零組件要求將朝向精密化與微形化,亦即精密模具之發展與需求將成未來主流。由於現代切削技術之高速發展,對各種類型 之高精度刀具要求相當地迫切需要,刀具之設計研磨是刀具製造最後也最重要過程,也是決定刀具幾何形狀精度及切削性能之關鍵,而刀具刀刃幾何形狀複雜,必須依賴精密的 CAD/CAM 軟體與五軸 CNC 工具磨床。首先,計畫重點在於建構高速加工用之切削性能最佳化分析模式。以 FEM 軟體配合五軸 CNC 工具磨床與刀具研磨 CAD/CAM 軟體進行端銑刀具的幾何角度設計與研磨, 再以不同的研磨參數進行刀具研磨,並且在高速 CNC 加工機上,進行 用田口方法來建構不同研磨參數之端銑刀在 SKD61 模具鋼的高速切削實驗,由實驗結果可得 知刀具磨耗與刀具壽命,再以多項式網路建構研 磨參數對高速切削的刀具壽命分析模式。再以 FEM 軟體配合五軸 CNC 工具磨床與刀具研磨 CAD/CAM 軟體進行端銑刀具的刃口形狀設計與研磨,並利用設計與研磨出的最佳切削性能端銑 刀(幾何角度、刃口形狀與研磨參數)在高速 CNC 加工機上進行銑削 SKD61 模具鋼的高速切削實驗。所以本計畫應可建構出高速加工用之切削性能最佳化分析模式。
二、報告內容
1. 前言
近年來,切削加工技術在高速銑削、微細形狀切削等領域有了快速發展。隨著新型工程材料的開發應用以及零件的小型化、精密化,刀具製造商正積極開發適用於各種加工用途的高效刀具,對於刀具產品的需求日趨增長,刀具製造商紛紛在國內外擴大生產能力。隨著全球性的成本競爭不斷增加,使用者要求刀具產生高附加值、高效率生產的需求與日俱增。從刀具使用者來看,模具製造業也是刀具用量最大的行業之一。在模具製造過程中,成型模、熱作模、冷作模、塑模等幾乎所有環節中都需要用到刀具。此外,汽車、高鐵、一般機械製造業、以及近年來逐漸擴大用量的木材加工業都已成為刀具行業的主要用戶,且航空業是最傳統也是最為重要的刀具應用領域。另外在高速硬銑削、復合切削等先進切削技術是實現以最少生產設備提高生產效率、速度以及彈性加工零件的生產方式。但是,任何切削方式都離不開選用合適的切削刀具和確切的刀具使用參數。
乾切削加工技術為未來綠色加工技術的主要發展方向之一。乾切削加工由於不採用切削液,刀具切削條件更為惡劣,壽命也會縮短。因此,選擇合理的刀具材料與刀具研磨參數以及進行適宜的塗層外,刀具幾何參數的選擇與設計對乾切削具有至關重要的作用。另一方面國內在刀具設計基礎技術上與國外存在有一定之差距,因此唯有透過 FEM 建構銑削切屑的成形模擬分析做為刀具開發與設計的基礎,再經由完整且詳細的建構出最適化切削性能之高速加工用端銑刀設計與研磨模式,由上述之開發模式將是最節省開發時間與金錢的最佳刀具設計模式,也將是提昇我國精密刀具設計製造水準的關鍵性技術,因此刀具設計與研磨技術是相當迫切而值得投入之工作。
2. 研究目的
本研究計畫擬建構一套最適化切削性能之高速加工用端銑刀設計與研磨分析模式,端銑刀影響高速切削性能的主要因素有刀具的幾何形狀、刀具研磨精度以及刀具刃口形狀。首先利用 FEM 高速切削模擬分析為基礎,解析 rake angle、relief angle 對高速切削性能(切削力、切屑的形狀、刀 具最高温、…)的影響,結合田口實驗設計法與變異數分析,規劃一系列不同幾何形狀的端銑刀,進行 FEM 模擬分析,再利用五軸 CNC 工具磨床研磨出最適化刀具幾何形狀的圓鼻端銑刀,並配合高速切削加工機進行高速銑削驗証實驗,有助於瞭解銑削的特性與排除銑削加工中的不利因素,增加銑削的可靠性與精密度。影響高速切削性能的主要因素除了研磨精度、刀具的幾何形狀與切 削條件之外,另外刃口(cutting edge) 形狀(尖角或 倒角)對端銑刀於高速加工品質與切削性能應有相當程度的影響。再利用五軸 CNC 工具磨床研磨出不同刃口(cutting edge)形狀的端銑刀,並配合高速切削加工機進行高速銑削實驗。如此解析過程,將刀具研磨精度、幾何角度與切削條件的最適化設計再搭配刃口(cutting edge)形狀做有系統的分析與整合,應可建構一套最適化切削性能之高速加工用端銑刀設計與研磨分析模式。
3. 文獻探討
國內外有關刀具研磨與表面粗糙度的相關研究狀況如下:Chen利用 2 軸 CNC 工具磨床建立一套研磨 cone-end 端銑刀的方法,Lai針對 tapered 球頭端銑刀,開發出精密的設計與研磨方法,Agarwal利用機率與統計方法來預測陶瓷研磨的表面的粗糙。Kwak應用田口法與反應曲面法來探討表面研磨加工的誤差。Shaji分析出影響表面品質的研磨參數,如砂輪、工件、加 工以及機械參數等。Kim使用田口方法進行圓柱研磨過程的實驗分析,以獲取改善表面粗糙度的相對影響變數和最大的百分比。Alauddin使用反應曲面法來預測銑削過程,由二階預測模型得到刀具壽命的最佳切削條件。Suresh使用反應曲面法和遺傳演算法來預測表面粗糙度以及優化製程參數。Hecker利用算術平均數的表面粗糙度來預測磨削厚度的模型。刀具研磨相關業者是相當保守且封閉,較詳細且實用刀具研磨技術文獻都是公司的 Know-How,不容易取得,目前整個刀具研磨技術均在國外的大廠,如 WALTER、 ROLLOMATIC、ANCA、JUNGER、……等等。國內外有關於切削加工時切屑的成形分析有 Guo從不連續的切屑成形 FEM 模擬分析中,可以發現切屑的破斷是發生在刀刃口上方的位置。Qian模擬 CBN 刀具高速車削 AISI 52100 軸承鋼、AISI H13 熱作工具鋼、AISI D2 冷作工具鋼及 AISI 4340 低合金鋼等四種材料,主要針對切削角度與切削條件對切削力的影響關係。Ceretti應用 Arbitrary Lagrangian Eulerian 有限元素法公式模擬、分析在正交切削下其刀具-切屑介面間熱傳係數模型之建構。Attanasio使用 Deform-3D 商業模擬軟體並搭配 Arbitrary Lagrangian Eulerian 有限元素法模擬刀具磨耗模型。Shi應用 ABAQUS 軟體探討金屬正交切削沿著刀具-切屑介面其摩擦產生之熱的影響。 Ceretti使用 DEFORM-2D 體模擬正交切削時切削條件對切屑形成的趨勢關係。隨著科技的進步,近年來高速加工的技術,在高速加工機與週邊技術不斷進步下,逐漸成長更趨完備。 Schulz在 90 年代發表了許多篇的相關論 文,定義出高速切削的真正意義,且說明高速切削不僅提高生產力之外,其切削力降低,工件和夾持系統熱變形減小,表面粗糙度良好、切削時 更穩定性。Tlusty對高速切削的穩定性也提出一套理論。國內學者蔡志成對模具合金做高速銑削最佳切削參數也做了一些研究。另外一些學者對高速切削應用於不同材料的切削性能做一些研究,與高速切削之發展做一些分析。
4. 研究方法
本研究方法首先是應用DEFORM 2D軟體,建立一套銑削SKD61模具鋼製程分析模型,藉此模型可以瞭解切屑形成的過程,並預測其刀具性能。以直交表規劃銑削模擬實驗,製程參數包括有效 rake angle、離隙角、切削速度和切削深度等四個參數。評估銑削製程性能主要有金屬移除率、刀具溫度、切屑溫度、切削力以及刀具最高溫度與刀尖距離等五個品質特性,此為多重品質特性問題。應用灰關聯分析將多重品質特性轉換為單一性能指標,即灰關聯度。再以田口參數設計找出滿足多重品質特性製程參數最佳解。最後利用刀具研磨軟體搭配五軸工具磨床研磨實驗所需的圓鼻端銑刀具,再對SKD61模具鋼進行銑削測試,以驗證模擬結果的正確性。由於對銑削中的銑刀使用壽命的瞭解,進而大大提升精密銑削品質的管理。由於瞭解刀具幾何與切削條件對於高速切削 SKD61 模具鋼的影響關係,本研究將進一步分析刀具研磨品質的影響關係,以刀具研磨時的砂輪粒度、磨削速度與進給速度為實驗因子並規劃全因子實驗,利用 Abductive 網路建構研磨端銑刀具切削面與離隙面的表面粗糙度預測模型。此預測模型可提供給刀具研磨業者做為提升刀具研磨精度的依據。最後將第一階段的最適化刀具幾何與切削條件做為刀具刃口形狀的設計基礎,利用 DEFORM 2D 軟體建構不同刀具刃口形狀的分析模型,藉此模型可以瞭解刀具刃口倒角角度對於切屑形成的過程。在相同的切削速度、切削深度以及有效切削角與離隙角的搭配之下,改變刀刃口倒角角度來做模擬實驗。評估實驗結果以切削力、刀具溫度與切屑溫度為基準,最後再利用刀具研磨軟體搭配五軸工具磨床研磨實驗所需的端銑刀具,再對 SKD61 模具鋼進行銑削測試,以驗證模擬結果的正確性。由上述三階段的實驗方法,將可建構出高效能端銑刀具設計與研磨分析模式。
5. 結果與討論
5.1 建構銑削最適化模型
本年度的切削模型建構是根據97年度國科會計畫中所建構的微小銑削最佳化設計模式為基礎,利用DEFORM- 2D 軟體,建構銑削最佳化設計模式。模擬結束後分別以金屬移除率、刀具溫度、切屑溫度、切削力以及刀尖與刀具最高溫距離等五個品質特性皆為判斷刀具壽命之性能指標。為減少模擬次數,本文則應用直交表來進行實驗的配置與分析,且仍可獲得與全因子實驗非常相近的分析結果。評估微小銑削製程之切削性能為刀具壽命,影響切削性能之製程參數有切削角(A)、離隙角 (B)、切削速度(C)及切削深度(D)等四個參數,故本計畫設定選四個參數為可控制因子,各可控因子分別設定三個水準。直交表的選擇與因子的總自由度是有關的。對3水準的因子而言,其自由度為2。本研究中四個可控制因子水準數均為3,因子總自由度為8。同時,在實驗中不考慮各因子間 交互作用,因此選用L9(34 )直交表。實驗佈置如表 1 所示。而金屬移除率、刀具溫度、切屑溫度、切削力以及刀尖與刀具最高溫距離等五個品質特性與刀具壽命息息相關,故本研究選擇這四項品質特性,作為評估切削性能的重要指標。 5.1.1 模擬模型建構 實驗規劃完成後,應用DEFORM-2D軟體,依表1的實驗佈置參數建構銑削模型,如圖1所示。模擬步數定義1步為0.0001mm共2000步。 表 1 田口法 L9 實驗規劃表。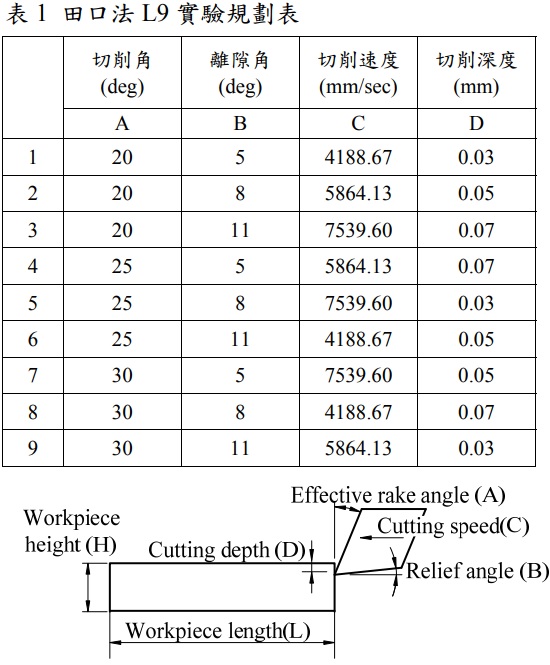
5.1.2 模擬結果
圖 2 為九組實驗的模擬結果,以切屑脫離工件時做為停止模擬的條件,實驗數據擷取依據為最大切削力時前後各 30 步(Step)的刀具溫度、切屑溫度、切削力以及刀尖與刀具最高溫距離等四個品質特性的平均值,另外在金屬移除率則是以固定軸向切深 1.0mm 再配合切削速度與切削深度進行計算,其整體模擬結果如表 2 所列。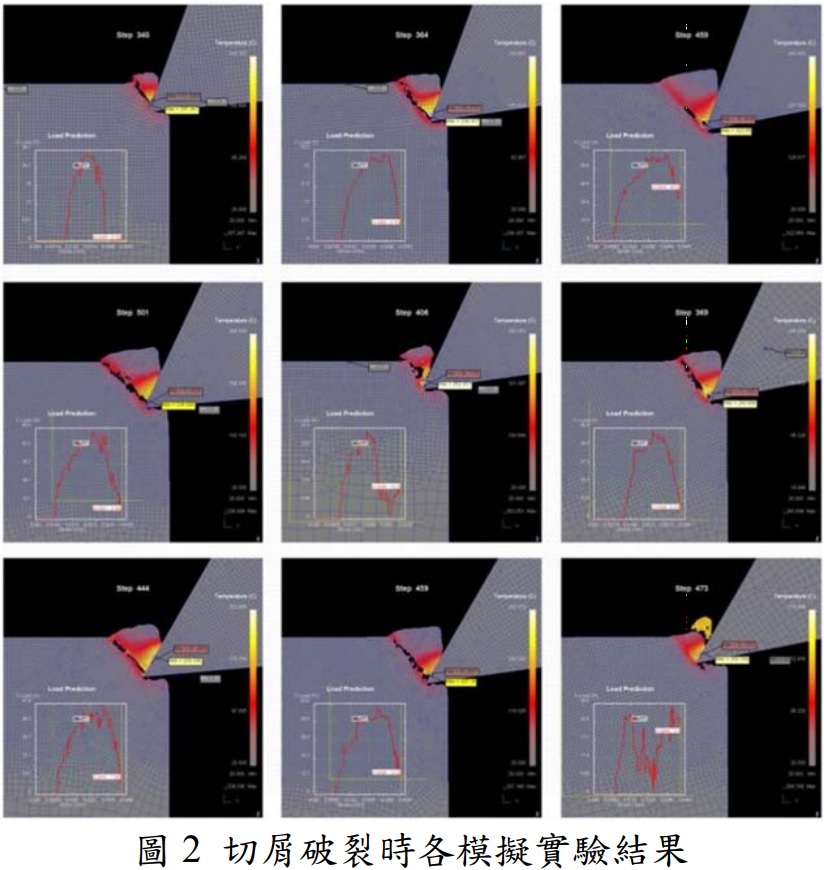
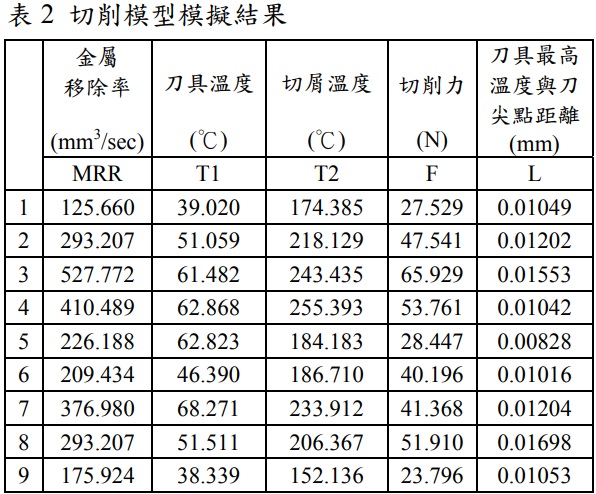
5.1.3 模擬數據分析與討論
經由銑削模擬結果,得到五個品質特性後,即金屬移除率、刀具溫度、切屑溫度、切削力以及刀尖與刀具最高溫距離等四個品質特性,以灰關聯田口法進行製程參數最佳設計分析,藉由控制因子的反應表以及變異數分析,找出最佳與最差之參數組合,參數設計最佳化的步驟如下:(1) 將實驗結果計算SN比
(2) 將SN比做正規化處理
(3) 計算灰關聯係數
(4) 計算灰關聯度
(5) 計算灰關聯度之因子反應
(6) 計算灰關聯度之變異數分析(ANOVA)
(7) 選擇切削參數最佳及最差之水準值
5.1.3.1 實驗數據計算
在本研究中以刀具壽命與金屬移除率來評估模擬的切削性能,當金屬移除率越大則代表刀具可移除較多金屬材料,故為望大特性,而刀具壽命方面則是由刀具溫度、切屑溫度、切削力與刀具最高溫度與刀尖點距離來評估,當刀具切削時在刀刃口有低的刀具溫度、切屑溫度與切削力以及較大的刀具最高溫與刀尖點距離時,能使刀刃口不易產生高溫而減少刀腹磨耗,因此在本研究中將刀具溫度、切屑溫度與切削力設定為望小特性,而刀具最高溫與刀尖點距離為望大特性。首先,將表2模擬結果依序帶入田口法的望大與望小公式做計算各SN比,再將各品項SN比做正規化處理,使其值介於0與1之間,將各品質特性數據作正規化之後,必須再將其轉換成灰關聯係數。最後,由表3可知,第9組的製程參數組合的模擬結果有最大的灰關聯度值(0.765),亦即第9組實驗在 9組的模擬實驗中有最好的多重品質特性。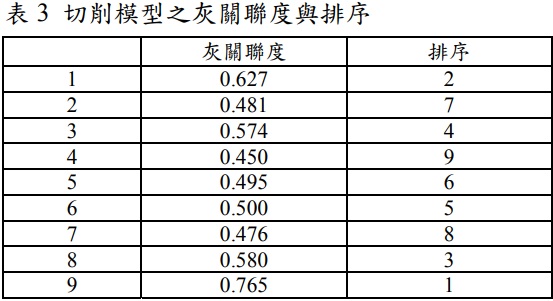
接著由表4中的整體灰關聯度值,計算每個切削參數在每一個水準值對多重品質特性整體影響的灰關聯度平均值,即做回應表,結果如表4所示。當平均灰關聯度值愈大,則多重品質特性愈佳。變異數分析的目的在以統計方法瞭解切削參數對多重品質特性影響的程度。以灰關聯度回應表進行變異數分析,結果如表5所示。由變異數分析可知,參數切削深度(D)對多重品質特性影響最大, 其次為切削角(A)、離隙角(B)及切削速度(C)。由 表4灰關聯度因子反應表中可得最佳切削參數水準組合為A3B3C1D1;最差水準組合為A2B1C3D2,其整理如表6所示。
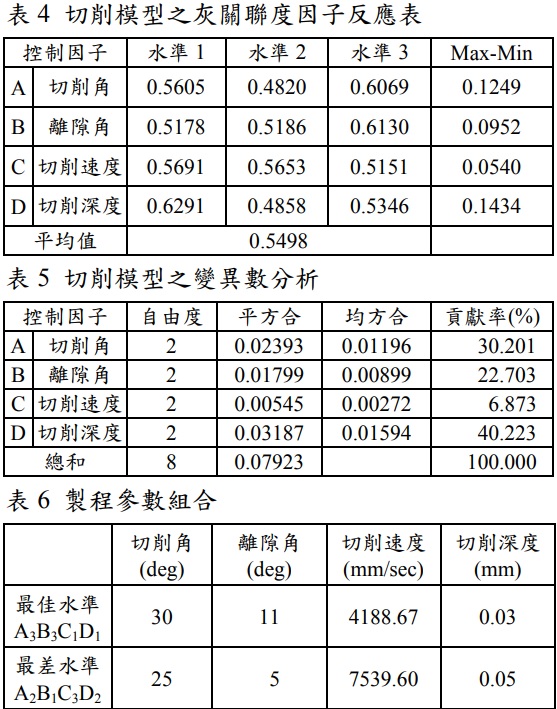
5.1.3.2 模擬結果驗證
端銑刀研磨之基本角度有徑向切削角、徑向離隙角、螺旋角、軸向切削角、軸向離隙角與端面凹角。將表6製程參數組合依據斜切削原理,切削角需依據螺旋角轉換成端銑刀的徑向切削角,在本研究中將螺旋角設定成35度,軸向切削角為切削角的1/3,徑軸向離隙角與模擬結果相同。驗證實驗之端銑刀具其固定刀具幾何參數為刀具直徑:8mm;螺旋角:35度;端刃凹角:1.5度;圓鼻R 角:0.5R,由上述本研究之驗證實驗所需的圓鼻端銑刀具角度如表7所列。根據表7所需研磨的端銑刀具幾何,使用TG-5 PLUS工具磨床研磨所需的 端銑刀具。本研究之驗證實驗,將以實際切削來驗證DEFORM- 2D軟體所建立的切削模式與最佳化設計模式的可行性。驗證實驗是以匠澤B8型高速綜合加工機進行。在驗證實驗中以固定軸向切深(AD)1.0mm與徑向切深(RD)1.0mm採用逆銑削進行。實驗結果如表8所列。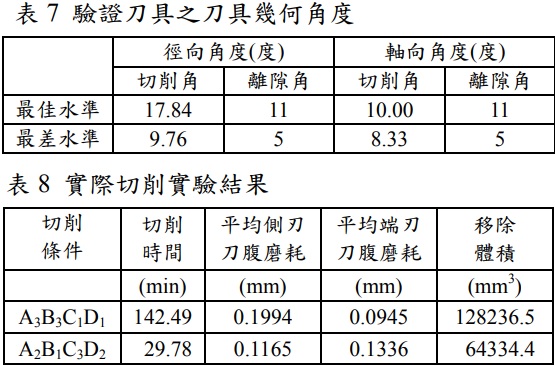
表 8 中刀具壽命為當切削時刀腹破損之總切削時間(此時刀腹磨耗未達 0.2mm)。由表 8 可知,最佳切削條件確實比最差條件有較佳的切削性能,其切削時間相差 112.71(min),移除體積相差 63902.1(mm3 )。圖 3 與圖 4 表示在最佳切削條件與最差切削條件下,切削時間對端刃刀腹磨耗及周刃刀腹磨耗之關係。
.jpg)
圖 4 切削時間與端刃刀腹磨耗之關係由圖 3 與圖 4 顯示,刀具磨耗不論是在周刃磨耗或端刃磨耗上,在一開始時皆會出現劇烈之磨損,然後才漸趨緩和。由以上結果分析,說明了本研究所提出的多重品質特性製程參數最佳化演算的可行性。
5.2 建構刀具研磨表面粗糙度預測系統
本實驗以刀具表面粗糙度Ra來做評估指標,一般而言刀具表面粗糙度越好,其加工可得較好 的表面粗糙度值。為了增加實驗與實際研磨加工 準確性,因此實驗針對開槽(徑像切削面)與徑向離隙分別採用 33 全因子實驗規劃。響表面粗糙度的 磨削條件有砂輪粒度、磨削速度、進給速度。本 實驗將製程參數視為可控制因子,各控制因子分 別設定為三個水準值,有關本實驗選用之製程參 數級水準值如表 9 與表 10 所示。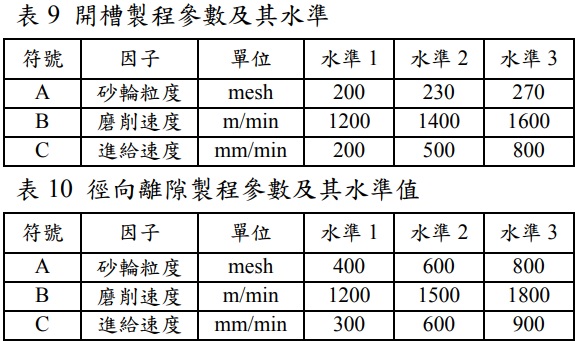
5.2.1 表面粗糙度的量測與分析
實驗完成後,利用 Surfcorder SEF-3500 非接觸式表面粗度儀量測各刀具的表面粗糙度變化,量測刀具幾何部分為開槽溝底與徑向離隙等 Ra 值。開槽(徑向切削面)的表面粗糙度量測設定參數為 V.mag=2000 、 H.mag=100 、 Cutoff=0.08 、 E.length= Cutoffx5 與 Speed=0.1m/s。徑向離隙面 的表面粗糙度量測設定參數為 V.mag=2000、 H.mag=100、Cutoff=0.25、E.length= Cutoffx5 與 Speed=0.1m/s。量測結果如圖 5 與圖 6 所示。根據刀具徑向切削面與徑向離隙面的表面粗糙度量測結果歸納如下:
(1). 由圖 5(a)-(c)得知
當磨削速度為 1200m/min 時,在不同進給速度下,其 Ra 有其相對應關係,但磨削速度在 1400 與 1600m/min 時,可發現進給速度 500 與 800mm/min 其 Ra 呈現幾乎重疊現象,但可確定砂輪粒度細,其 Ra 較佳。由圖 5(d)-(f)中,磨削速度與 Ra 關係與上述相同結果。
(2). 由圖 5(g)-(i)得知
當磨削速度在 1200 與 1400m/min 時,不同砂輪粒度的研磨效應作用下,其 Ra 值變化量並不明顯,但在相同磨削速度時,較低的進給速度 200mm/min 可得較佳 Ra。
(3). 由圖5(h)得知
當磨削速度為1600m/min時,磨削速度 200 至 800mm/min,粒度 230 與 270mesh 其 Ra 變化並不明顯,粒度 200mesh 有明顯的 Ra 變化,但在進給速度 200mm/min 時,砂輪粒度200至270mesh在研磨刀具時,對 Ra 的變化不明顯。
(4). 由圖 6(a)-(c)得知
磨削速度對於不同進給速 度在粒度 400mesh 中,Ra 幾乎重疊,在磨削速度 1200 與 1500m/min 中,進給對於 Ra 的關係變化不明顯,但在粒度 600mesh 與進給 300mm/min 時 , Ra 較差,在磨削速度 1800m/min 時,進給 300 與 900mm/min 中粒度 400 與 600mesh 對於 Ra 差異性不大,但在相同粒度下磨削速度 600mm/min 其 Ra 表現 較佳,而在粒度 800mseh 時,進給速度 300mm/min 時 Ra 較佳。
(5). 由圖 6(d)-(f)得知
在不同鑽石粒度時,磨削速度 1500 與 1800m/min 其 Ra 並沒有明顯變化,磨削速度越慢,其 Ra 表現越差。粒度越細,Ra 越佳,在粒度 400mesh 以上時,進給 300mm/min 表面粗度較差,進給 600 與 900mm/min 影響不顯著。
(6). 由圖 6(g)-(i)得知
進給速度越快,粒度 400mesh 的 Ra 並不明顯變化,但磨削速度越快,其 Ra 表現越好,但粒度 600mesh 進給速度 300mm/min 時,其 Ra 比較差,在進給速度 600mm/min 時,其 Ra 較佳,在磨削速度 1500 與 1800m/min 時,粒度 600mesh 與 800mesh 隨進給速度提升,Ra 較差。.jpg)
(a)磨削速度 1200m/min (b)磨削速度 1400m/min (c)磨削速度 1600m/min (d)砂輪粒度 200mesh (e)砂輪粒度 230mesh (f)砂輪粒度 270mesh (g)磨削速度 1200m/min (h)磨削速度 1400m/min (i)磨削速度 1600m/min
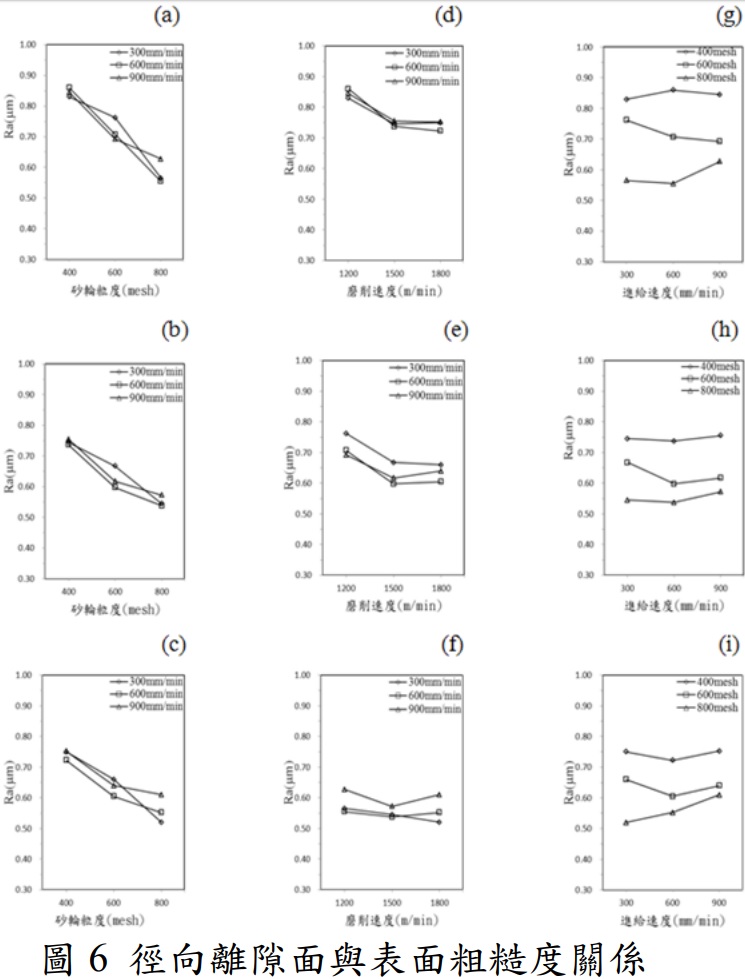
(a)磨削速度 1200m/min (b)磨削速度 1500m/min (c)磨削速度 1800m/min
(d)砂輪粒度 400mesh (e)砂輪粒度 600mesh (f)砂輪粒度 800mesh (g)磨削速度 1200m/min (h)磨削速度 1500m/min (i)磨削速度 1800m/min
5.2.2 建構表面粗糙度預測系統
經鑽石砂輪研磨刀具實驗後,利用 Surfcorder SEF-3500 表面粗度儀量測徑向切削面與徑向離隙面的表面粗糙度 Ra 值,將實驗配置與量測數據運用 Abductive 多項式網路建構刀具研磨精度的預測系統。此系統可協助刀具研磨業者做為提升刀具研磨精度的依據。圖 7 與圖 8 分別列出端銑刀具徑向切削面與徑向離隙面的多項式網路模型。預測系統與實際研磨之表面粗糙度的誤差之在 7%以內,故可證明本研究所建構的多項式網路預測系統可有有效的預測刀具研磨精度。.jpg)
5.3 刀具刃口形狀對於高速切削的影響
本研究的第三階段是探討刀具刃口形狀對於高速切削的影響,根據第一階段最佳切削參數(切削角:30 度、離隙角 11 度、切削速度:4188.67 mm/sec 以及切削深度:0.03mm)做為刀具刃口模擬的基礎。
5.3.1 模擬刀具刃口倒角之實驗規劃
首先,固定切削速度與切削深度,另外將切削角與離隙角的組合分成 3 組,分別針對刀刃口倒角角度 15、30 以及 45 度做模擬分析,刀具幾何示意圖如圖 9 所示,其中 α 為切削角、δ為離隙角、γ 為倒角角度、w 為倒角長度以及 r 為接觸圓角,在刀具刃口倒角模型中,固定參數 w 為 10μm 以及 r 為 0。評估模擬結果為平均切削力、刀具溫度與切屑溫度,其模擬規劃與結果,如表 11 所列。由表 11 模擬結果可得知,當倒角角度為 45 度時,在 3 組切削角與離隙角的組合中,其平均切削力會變大但刀具溫度會降低,而切屑溫度則無明顯變化。另一方面在切削角 20 度與離隙角 5 度的模擬組合當中,倒角角度由 15 度變成 45 度時,平均切削力與刀具溫度分別相差 6.48(N)與 5 度,有較大的平均切削力變化與較小刀具溫度變化量;而切削角 30 度與離隙角 11 度的模擬組合當中,倒角角度由 15 度變成 45 度時,平均切削力與刀具溫度分別相差 1.98(N)與 20 度,有較小的平均切削力變化與較大刀具溫度變化量。
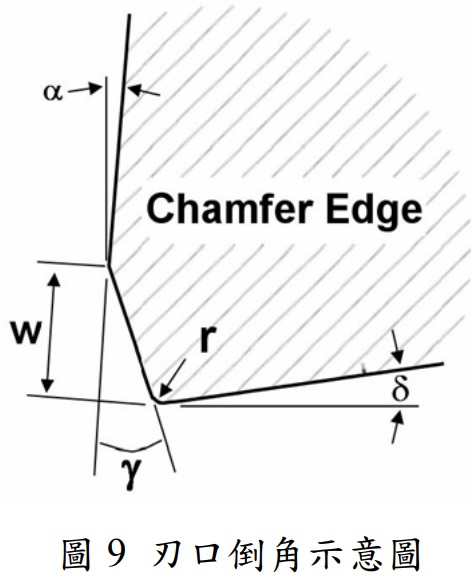
由上述的分析可得知,當切削角為 30 度與離隙角 11 度(第一階段最佳刀具幾何)以及刃口倒角 45 度時,在模擬切削時其平均切削力雖然變大但較無明顯差距,但刀具溫度則有 20 度的差距,因此在刀具刃口形狀的模擬驗證部分,將延續第一階段最佳刀具幾何參數再配合刃口倒角 45 度,利用刀具設計軟體與五軸工具磨床研磨驗證實驗所需之平端銑刀具。圖 10 至圖 12 為刃口倒角角度與切削力的關係圖。
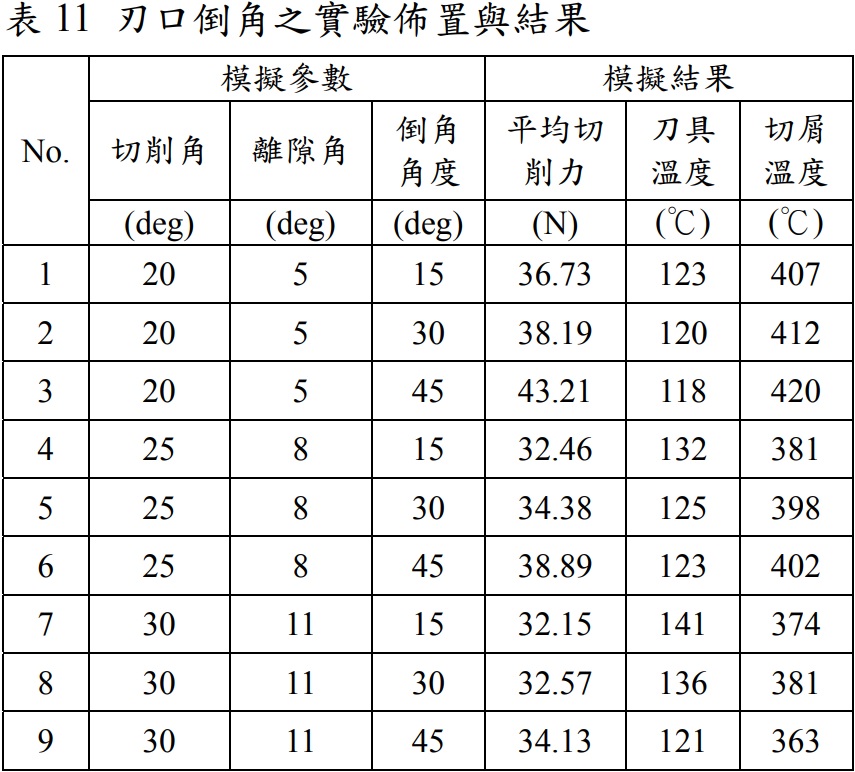
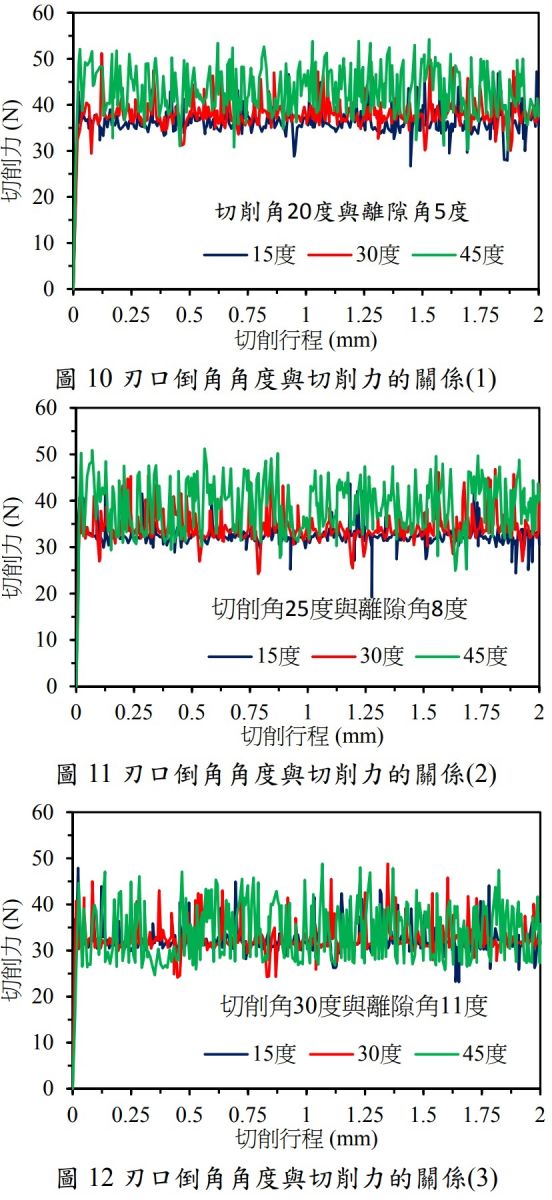
5.3.2 刃口倒角驗證實驗
本研究之驗證實驗,將以實際切削來驗證 DEFORM- 2D 軟體所建立的刀具刃口形狀切削模式的可行性。驗證實驗是以匠澤 B8 型高速綜合加工機進行。在驗證實驗中以相同的切削速度 4188.67 mm/sec、每刃進給(切削深度)0.03 mm、 軸向切深 1.0 mm 與徑向切深 1.0mm 採用逆銑削進行,單存針對刀具刃口形狀對於高速銑削 SKD61 模具剛的影響關係做模擬驗證探討。實驗結果如表 12 所列。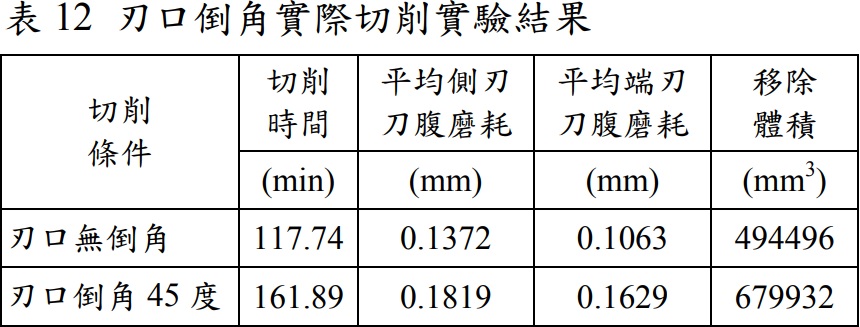
由表 12 刃口倒角實際切削結果可得知,刃口倒角 45 度的平端銑刀具有較佳的切削性能,在相同切削條件下,其切削時間增加 44.15(min),移除體積相差 185436(mm3 )。圖 13 與圖 14 表示刃口無倒角與刃口倒角 45 度之平端銑刀具切削時間對側刃刀腹磨耗及端刃刀腹磨耗之關係。
值得注意的是在刀具切削前 15 分鐘時,其刃口倒角 45 度的平端銑刀具之側刃刀腹磨耗量皆大於刃口無倒角的平端銑刀具,如圖 15 所示。此現象為倒角刀具比無倒角刀具承受較大的切削力所造成,但在切削 15 分鐘以後刃口倒角刀具的刀腹磨耗量皆小於刃口無倒角刀具,這是因為無倒角刀具(刃口尖銳)在切削初期承受一瞬間的切削力使刃口產生不均勻的破裂,進而影響後續切削時刀腹磨耗的變化,由上述現象可證實本研究利用 DEFORM 2D 模擬切削找出在刀刃口上以寬度 10μm 倒角 45 度的方式,減低刀刃口的鋒利度,經過驗證實驗可證實此方法能夠有效改善平端銑刀具在高速切削 SKD61 模具鋼的刀具壽命。
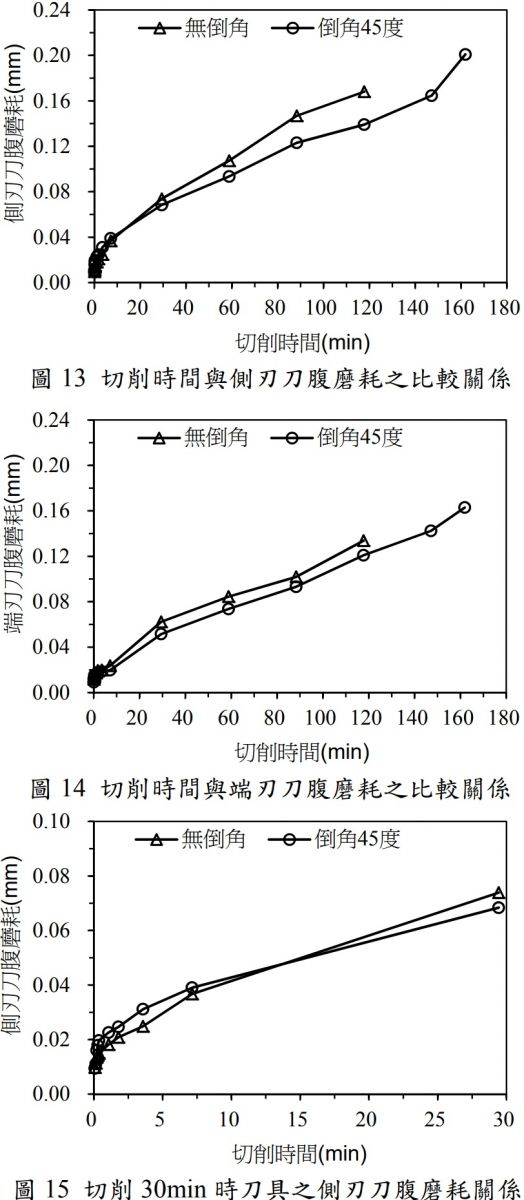
由模擬高速切削 SKD61 模具鋼之 ANOVA 分析得知刀具幾何與切削參數影響因素分別為 52.904%與 47.096%,其中又以切削深度 40.223% 與切削角 30.201%最為重要,以此做為高效能端銑刀具的設計基礎。運用 Abductive 多項式網路以刀具研磨條件預測研磨刀具之徑向切削面與徑向離隙面的表面粗糙度,進而提升刀具研磨的表面完整性。最後由刀具刃口倒角的設計來減低刃口鋒利度,使切削初期能呈現穩定的刀腹磨耗,以增加刀具壽命,經由了解影響高速切削 SKD61 模具鋼的關鍵因子並由運用刀具研磨參數預測系統提升刀具研磨精度,最後再搭配刃口形狀設計提升刀具壽命,經由本研究詳細的分析與探討,可明確解析出高效能端銑刀設計與研磨的關鍵因素,能有效提升刀具壽命並可將此技術推廣到刀具研磨產業以提升我國刀具研磨市場的國際競爭力。
6. 計畫成果自評
由本研究針對高效能端銑刀具設計與研磨以三種方式建構分析模型,第一階段運用 DEFORM 2D 建構銑削模型找出高速切削 SKD61 模具剛的最佳刀具幾何與切削參數,由驗證實驗結果說明了本研究所提出的多重品質特性之製程參數最佳化演算與切削模擬模型的可行性。第二階段利用 Abductive 多項式網路建構刀具研磨精度(徑向切削面與徑向離隙面)的預測系統,預測系統與實際研磨之表面粗糙度的誤差之在 7%以內,故可證明本研究所建構的多項式網路預測系統可有有效的預測刀具研磨精度。第三階段則根據第一階段之最佳刀具幾何與切削條件為基礎,運用 DEFORM 2D 軟體對刀具刃口形狀做設計與分析,由驗證實驗在刀刃口上以寬度 10μm 倒角 45 度的方式,能夠有效改善刀具壽命。由上述三階段的分析與探討,可明確解析出高效能端銑刀設計與研磨的關鍵因素,並可將此技術提供給國內刀具研磨業者對於設計與研磨高效能端銑刀具的基礎與依據。