帶有多層複合奈米結構塗層的雙組分立銑刀是整體硬質合金立銑刀的可行替代品
2020-07-02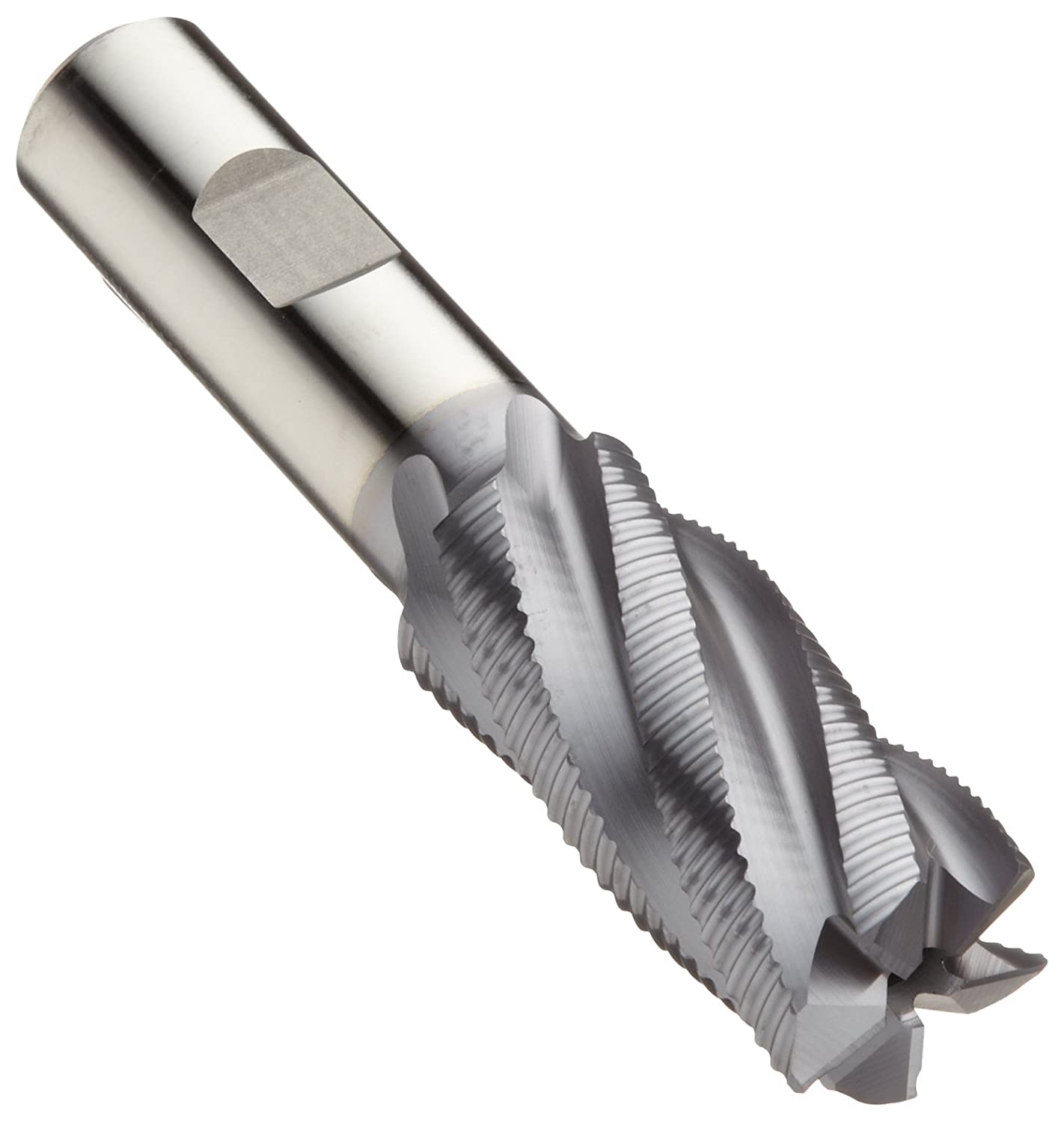
摘要
本文論述了雙組份立銑刀的應用挑戰,雙組份立銑刀代表了硬質合金切削部分和便宜結構材料製成的刀柄的結合。利用有限元法對複合銑刀的應變和變形進行了計算,並與實心硬質合金銑刀進行了比較。研究還涉及到用單體銑刀和雙組分銑刀加工不同刀柄材料的精度參數的對比分析。通過對使用單體銑刀和雙組分銑刀銑削鋁合金時進行的切削試驗,發現使用這種塗層可以減少應變,相應的也可以減少變形,從而提高加工精度。因此,應用具有多層複合納米結構塗層的雙組分立銑刀,可以在保持甚至提高銑刀壽命和加工精度參數的同時,降低加工成本。
1.簡介
現代化機械加工設備的運行成本非常高,這一事實導致了對切削刀具的操作條件要求嚴格,切削刀具的支出在生產成本中的比例也在增加。同時,全球競爭的日益激烈,使得我們必須利用一切資源來降低生產成本,提高生產效率。作為解決這一挑戰的方法之一,在保持切削工具高性能切削性能和可靠性的前提下,降低切削工具的支出具有重要作用。據S.I. Gonyalin統計,2012年,切削工具的生產量達400億美元。在上述生產量中,有相當一部分被硬質合金立銑刀所佔據,硬質合金立銑刀在現代機械工程生產中得到了廣泛的應用。除了單體硬質合金銑刀外,還使用了帶有硬質合金刀片機械緊固的銑刀;但是,這種設計的銑刀直徑較小,很難使用(一般情況下,銑刀直徑在20毫米以上)。還使用了帶有可換硬質合金銑刀頭和螺紋緊固在刀柄上的雙組份銑刀(幾家領先的切削工具公司已經推出了這種銑刀的生產;然而,這銑刀價格上仍然很昂貴,在顯刀直徑超過20毫米的情況下使用是合理的)。所提出的雙組分銑刀的設想是指銑刀的切削部分由硬質合金製成,刀柄由價格較低的結構材料製成。在這種情況下,由於切削部分是焊接在刀柄上的,所以對銑刀直徑沒有限制。很明顯,整體硬質合金立銑刀在剛性上超過了雙組分銑刀,相應的會有更高的加工精度。然而,在某些情況下,可以成功的使用雙組分立銑刀代替單組分立銑刀,大大節省了昂貴的硬質合金材料。使用特殊的多層複合奈米結構鍍層,可以擴大雙組分銑刀的應用範圍,使其在精度和效率上與單組分銑刀競爭。
2. 問題說明
有些學刊考量由於沉積耐磨塗層而提高立銑刀的耐磨性和可靠性。例如,Vereschaka仔細考量了使用塗層銑刀進行立銑的具體情況。Bouzakis等人非常關注端銑塗層。Fox-Rabinovich等人證明,在端銑時,與硬度高、韌性低的TiAlN塗層特點的銑刀壽命相比,具有相當高韌性的塗層,特別是AlCrN、AlTiN和AlTiCrN塗層的銑刀表現出更高的穩定性。同時,在車削過程中,TiAlN塗層的刀具與AlTiCrN塗層的刀具壽命相比,具有更高的穩定性。在磨損過程中,在具有奈米結構鍍層的刀具接觸部位形成了主要由氧化鋁(Al2O3)組成的抗摩擦薄膜,而對於標準TiAlN塗層,這種薄膜主要由金紅石(TiO2)組成。
(AlTiCr)N(Ti0.2 Al0.65 Cr0.1)N塗層在高性能加工時也表現出較高的摩擦學適應性。與傳統的TiAlN塗層相比,它在硬度和抗氧化性方面表現出明顯的熱穩定性。與AlCrN塗層(25GPa)相比,TiAlN塗層的特點是在室溫下的硬度(30GPa)大大高於AlCrN塗層;但是,採用上述塗層的刀具在車削1040鋼時,刀具壽命大大縮短。Beake等研究發現,(Al0.66Ti0.34)N塗層在Ti6Al4V鈦合金的端銑時表現出比TiAlN塗層更好的耐磨性。有研究表明,鋁含量增加到67%,適合於端銑和面銑的操作,儘管這會導致塗層硬度的降低。鋁含量增加到50%-67%,可形成穩定的保護性抗摩擦鋁基薄膜。Hörling等人研究表明,AlTiN塗層(磁控濺射)的面銑效果比TiAlN塗層好得多。還發現,這些塗層的抗氧化性隨著鋁含量的增加而增加。Erkens等人證明,與鋁含量較低的塗層相比,採用AlTiN塗層(由高電離等離子體產生,表示為超氮化物納米晶塗層)的銑刀在高速銑削淬火鋼時的耐磨性明顯提高。
適應性AlTiCrSiYN基塗層在極端摩擦學條件下超高速乾式加工淬硬工具鋼和難切削的航空鎳合金時具有良好的應用前景。
不同力學性能的塗層,如Ti-TiN-(Ti,Cr,Al)N,Zr-(Zr,Cr)N-CrN,Ti-TiN-(Ti,Cr,Al)N,Ti-(Al,Cr)N-(Ti,Al)N、Ti-(Al,Cr)N-(Ti,Cr,Al)N、Zr-(Al,Cr)N-(Zr,Cr,Al)N和Zr-ZrN -(Zr,Nb,Cr,Al)N也是研究的重點。
Wang等人研究了淬火鋼的高速銑削。研究發現,由於減少了磨料磨損,採用TiSiN塗層的銑刀比採用TiAlN塗層的銑刀表現出更好的耐磨性。
論文主要研究了高速銑削(v=100-500 m/min)時,帶PVD塗層(Ti,Al)N的硬質合金立銑刀的工作效率。上述論文均以側面磨損為主。文中考慮了塗層中裂紋形成的問題。
近年來發表的論文中有多篇論文專門對端銑的振動、能耗、碳排放、切削力、刀具磨損、工件去除率、表面粗糙度、切削區溫度等各方面進行了模擬。其中,Cao等人對顫振進行了研究,顫振是一種自激振動,伴隨著端銑的不穩定、混沌行為和基本不正常的波動。研究了不同顫振條件下產生的振動信號以及穩定切削的振動信號,以了解顫振特性。考慮到銑削過程中顫振的非線性和非穩態特性,採用自適應分析方法,即集合經驗模分解來分析振動信號,並提取了兩個非線性指數作為顫振指標。所提出的方法通過精心設計的切削試驗進行了驗證。另一方面,Zhang等人開發了一種多目標優化模型,以實現乾式銑削的高效率、低能耗和低碳排放。
該經驗模型是在用塗層硬質合金銑刀銑削AISI1045鋼的多次切削試驗基礎上建立的。Huang等人提出了一種新型的圓柱形立銑刀切削力模型,將立銑刀沿其圓周方向進行離散化處理。為驗證分析結果,進行了一組銑削實驗(在AISI1045鋼與塗層硬質合金立銑刀的端銑時)。為了全面評價切削性能,趙志明等建立了模糊綜合評價模型,分別考慮了粗銑和精銑的銑刀磨損、工件去除率、表面粗糙度和尺寸誤差。鮑海等人考慮了一種基於分析模型的新方法來預測端銑中銑刀的溫度。理論模型和實驗結果表明,銑刀溫度隨每刃進給量的增加而增加,但隨切削速度的增加而降低。
現代材料、焊料、技術和設備可以開發新設計的雙組分立銑刀,在一定的工作條件下,雙組分立銑刀的工作效率和加工質量並不遜色於單體銑刀。
從整體式立銑刀的運行經驗來看(特別是在阿穆爾州共青團市的一家工業企業),發現與最大限度地強化加工方式的需要有關,在銑刀柄緊固處,以銑刀柄脆性失效形式出現的立銑刀故障部分有不斷增加的趨勢(圖1)。因此,使用抗循環疲勞失效能力增強的刀柄材料,可以降低這種失效的比例。
%20brittle%20failure%20of%20shank%20and%20(b)%20distribution%20of%20failure%20causes%20of%20solid%20carbide%20end%20mills.jpg)
圖1 實心硬質合金立銑刀的(a)刀柄脆性失效實例和(b)失效原因分佈實例
3. 材料和方法
為了沉積奈米級多層複合塗層(NMCC),使用了一個真空電弧VIT-2裝置,該裝置是為在各種工具材料的基材上合成塗層而設計的。該裝置配備了一個帶有蒸汽離子流過濾的電弧蒸發器。在本研究中,該工藝被稱為過濾式陰極真空電弧沉積,用於在工具上沉積塗層,以顯著減少塗層形成過程中液滴相的形成。
硬質合金(WC+8%Co)被用作銑刀切削件的材料。採用5135鋼(HB180,σy=185MPa)、HSST1(HB255,σy=510MPa)和低WC硬質合金(WC+30%TiC+4%Co)(HRA92,σy=1000MPa)作為刀柄材料。使用低溫銅鎳焊料,通過焊接將柄部和切削刃結合起來。
切削試驗涉及到直徑為12mm,長度為90、120、220mm的整體式和雙組分式立銑刀,其三個刀齒的刃口為加工鋁合金的條件。研究了帶有"參考"TiN塗層的銑刀和擬採用NMCC Zr-ZrAlN-(ZrCrAl)N的銑刀。圖2為採用NMCC Zr-ZrAlN-(ZrCrAl)N的雙組分立銑刀的總體視圖。
切削試驗在高性能數控銑床(DMU-50 Ecoline型)上進行(切削速度vc=200;300 m/min,銑削深度ap=5和40 mm,每齒進給量fz=0.1;0.15 mm/齒),被加工工件採用1933型專用鋁鋰高強度合金,(Al-Zn-Mg-Cu-Zr)。銑床處的工件總圖及銑削過程如圖3所示。
考慮到實際的切削力,確定了應變和變形,並開發了一個測量台,使用專門的測功機(STD201-2型)測量其組成部分。通過見證樣品和測試樣品,通過在拉伸機(Instron 3382模型)上彎曲夾持的樑來評估變形的充分性。使用視頻測量機(MIKROVU模型)對磨損參數進行了評估。採用SolidWorks軟件中的有限元法(FEM)對立銑刀的應變和變形進行了模擬。
製作了雙組份立銑刀的樣品進行試驗。然後,對這些立銑刀進行實驗測試,測量切削力、振動和切削區域的溫度等成分。所獲得的切削力值被納入模擬雙組分立銑刀的應變和變形的計算模型中,銑刀長度和銑削深度的不同版本。
為了評價模型的充分性和銑刀變形的結果,進行了切削試驗。此外,還利用高精度拉力機對類似的見證樣品按照懸臂樑方案進行變形的實驗試驗進行評價。
之後,利用完善的銑刀模型進行數值模擬,確定控制加工精度和效率的最佳方法。利用上述手段確定了銑刀的設計參數,如銑刀的長度和刀柄材料等。根據得到的結果,對雙組份銑刀的設計參數進行了優化模擬,發現其對加工精度和效率的影響程度。經過優化,確定了銑刀各種工況下的優選設計。
N.jpg)
圖2 雙組份NMCC Zr-ZrAlN-(ZrCrAl)N的立銑刀
%20Workpiece%20at%20the%20milling%20machine%20and%20(b)%20the%20milling%20process.jpg)
圖3 (a)銑床上的工件和(b)銑削過程
4. 結果和討論
4.1雙組分立銑刀變形模擬結果
根據第2節所述方法進行數值模擬的結果,建立了一個研究對像數據庫,並按以下特徵進行分類。
• 一個或兩個組件:
• 帶或不帶塗層。
• 各種長度的銑刀(不超過220毫米)。
• 銑刀材料的品牌。
• 刀柄材料的品牌。
仿真結果如下端銑刀變形的計算方案,如圖4所示。
FCN=3000N時,銑刀體應變的計算結果如圖5所示。從圖5中可以看出,銑刀體緊固在機床柄部的部位出現的應變最大。上圖中應變值的計算結果如圖6所示,銑刀的變形(與垂直方向的偏移)值。
從圖6可以看出,在切削力FCN=3000N時,雙組份銑刀的最大撓度約為0.4mm。所進行的計算證實,整體硬質合金銑刀的剛性超過雙組份銑刀的剛性。折衷的辦法是採用雙組分銑刀,通過使用適當的結構材料保證刀柄的高循環強度,並通過使用硬質合金和多層複合奈米結構塗層的最佳組合的硬質合金切削件以及優化切削方式來保證所需的加工效率。需要指出的是,在重新計算加工表面的變形值時,得到的銑削變形值符合現有的航空零部件幾個表面的製造精度要求。因此,可以論證使用雙組份銑刀代替整體式銑刀的可能性。此外,由於雙組份銑刀設計的改進,還為提高其剛性做了準備。
下面以工件槽壁中偏移量В從垂直方向的比較名義圖的形式,介紹所得到的模擬結果。圖7a-c中顯示了在雙組分銑刀不利操作條件下的情況下(溝槽深度為40mm,即等於銑刀切削硬質合金部分的長度)的名義圖。研究還包括切削模式參數值恆定的情況(vc=200m/min,ap=40mm,fz=0.1mm/齒)。在所有考慮的情況下,切削力的徑向(法向)分量FCN被假定為3000N。
所得的記號圖顯示了所用材料的物理和機械特性與銑體變形值之間的關係趨勢,相對的,與槽壁的加工公差,即與加工精度之間的關係(在這種情況下,它是槽壁從理想(垂直)位置的偏移值В)。命名圖顯示,對於不相鄰的工件表面,用雙組份銑刀進行加工的這種精度是可以接受的。
此外,應該指出的是,隨著銑刀總長度的減少,撓度В的差值也會減小,這就使得雙組份銑刀有可能成為單體銑刀的替代品。
隨著溝槽深度的減小,命名圖看起來不一樣,溝槽壁的製造精度差異也會減小。需要注意的是,用立銑刀加工,一般來說,意味著相對較小的銑削深度。我們有理由認為,在如此小的銑削深度下,FCN切削力的徑向(法向)分量將大大降低。計算表明,在銑刀長度為90mm時,刀柄材料的影響很小,整體式和雙組分式銑刀的撓度В相當。此外,切削力的分量FCN為1200N。
上述情況的特點是,銑削時切削刃磨損平衡,沒有崩裂和剝落。在銑削深度較小(5 mm)的情況下,進給量和切削速度都能達到最大(切削速度vc=300 m/min,銑削深度ap=5 mm,fz=0.15 mm/齒)。在圖7中,顯示了加工槽壁的精度參數比較的命名圖(a,b,c)vc=200;(d,e,f)300 m/min,(a,b,c)ap= 40;(d,e,f)5 mm,(a,b,c)fz=0.1;(d,e,f)0.15 mm/齒)。圖中顯示了以下參數。
• 槽深40mm,銑刀總長220mm。
• 槽深40mm,銑刀總長120mm。
• 槽深40mm,銑刀總長90mm。
• 槽深5mm,總銑刀長度為90mm。
• 槽深5mm,銑刀總長度為120mm。
• 槽深5mm,銑削總長度為220mm。
通過對命名圖的分析可以看出,在銑刀長度較短的情況下,採用增加加工製度是可能的,因為對於較長的銑刀長度,這種增加加工製度會大大降低雙組份銑刀的使用效率。
%20FCN%20component%20of%20cutting%20force.jpg)
• 一個或兩個組件:
• 帶或不帶塗層。
• 各種長度的銑刀(不超過220毫米)。
• 銑刀材料的品牌。
• 刀柄材料的品牌。
仿真結果如下端銑刀變形的計算方案,如圖4所示。
FCN=3000N時,銑刀體應變的計算結果如圖5所示。從圖5中可以看出,銑刀體緊固在機床柄部的部位出現的應變最大。上圖中應變值的計算結果如圖6所示,銑刀的變形(與垂直方向的偏移)值。
從圖6可以看出,在切削力FCN=3000N時,雙組份銑刀的最大撓度約為0.4mm。所進行的計算證實,整體硬質合金銑刀的剛性超過雙組份銑刀的剛性。折衷的辦法是採用雙組分銑刀,通過使用適當的結構材料保證刀柄的高循環強度,並通過使用硬質合金和多層複合奈米結構塗層的最佳組合的硬質合金切削件以及優化切削方式來保證所需的加工效率。需要指出的是,在重新計算加工表面的變形值時,得到的銑削變形值符合現有的航空零部件幾個表面的製造精度要求。因此,可以論證使用雙組份銑刀代替整體式銑刀的可能性。此外,由於雙組份銑刀設計的改進,還為提高其剛性做了準備。
下面以工件槽壁中偏移量В從垂直方向的比較名義圖的形式,介紹所得到的模擬結果。圖7a-c中顯示了在雙組分銑刀不利操作條件下的情況下(溝槽深度為40mm,即等於銑刀切削硬質合金部分的長度)的名義圖。研究還包括切削模式參數值恆定的情況(vc=200m/min,ap=40mm,fz=0.1mm/齒)。在所有考慮的情況下,切削力的徑向(法向)分量FCN被假定為3000N。
所得的記號圖顯示了所用材料的物理和機械特性與銑體變形值之間的關係趨勢,相對的,與槽壁的加工公差,即與加工精度之間的關係(在這種情況下,它是槽壁從理想(垂直)位置的偏移值В)。命名圖顯示,對於不相鄰的工件表面,用雙組份銑刀進行加工的這種精度是可以接受的。
此外,應該指出的是,隨著銑刀總長度的減少,撓度В的差值也會減小,這就使得雙組份銑刀有可能成為單體銑刀的替代品。
隨著溝槽深度的減小,命名圖看起來不一樣,溝槽壁的製造精度差異也會減小。需要注意的是,用立銑刀加工,一般來說,意味著相對較小的銑削深度。我們有理由認為,在如此小的銑削深度下,FCN切削力的徑向(法向)分量將大大降低。計算表明,在銑刀長度為90mm時,刀柄材料的影響很小,整體式和雙組分式銑刀的撓度В相當。此外,切削力的分量FCN為1200N。
上述情況的特點是,銑削時切削刃磨損平衡,沒有崩裂和剝落。在銑削深度較小(5 mm)的情況下,進給量和切削速度都能達到最大(切削速度vc=300 m/min,銑削深度ap=5 mm,fz=0.15 mm/齒)。在圖7中,顯示了加工槽壁的精度參數比較的命名圖(a,b,c)vc=200;(d,e,f)300 m/min,(a,b,c)ap= 40;(d,e,f)5 mm,(a,b,c)fz=0.1;(d,e,f)0.15 mm/齒)。圖中顯示了以下參數。
• 槽深40mm,銑刀總長220mm。
• 槽深40mm,銑刀總長120mm。
• 槽深40mm,銑刀總長90mm。
• 槽深5mm,總銑刀長度為90mm。
• 槽深5mm,銑刀總長度為120mm。
• 槽深5mm,銑削總長度為220mm。
通過對命名圖的分析可以看出,在銑刀長度較短的情況下,採用增加加工製度是可能的,因為對於較長的銑刀長度,這種增加加工製度會大大降低雙組份銑刀的使用效率。
%20FCN%20component%20of%20cutting%20force.jpg)
圖4 (1)在切削力徑向(法向)FCN分量作用下,槽壁垂直位置的偏轉量В的示意圖;(2)銑刀柄;(3)銑刀的硬質合金切削刃部分;(4)機床卡盤系統;(5)工件槽的加工表面。表1為計算參數
表1. 計算參數
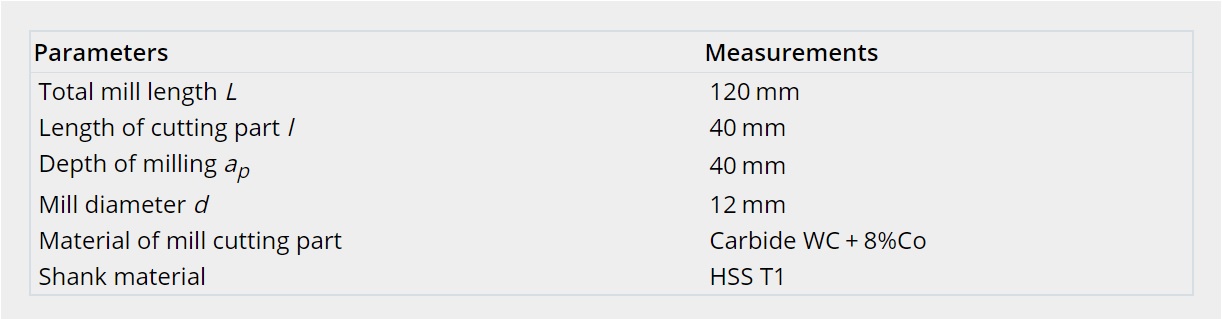
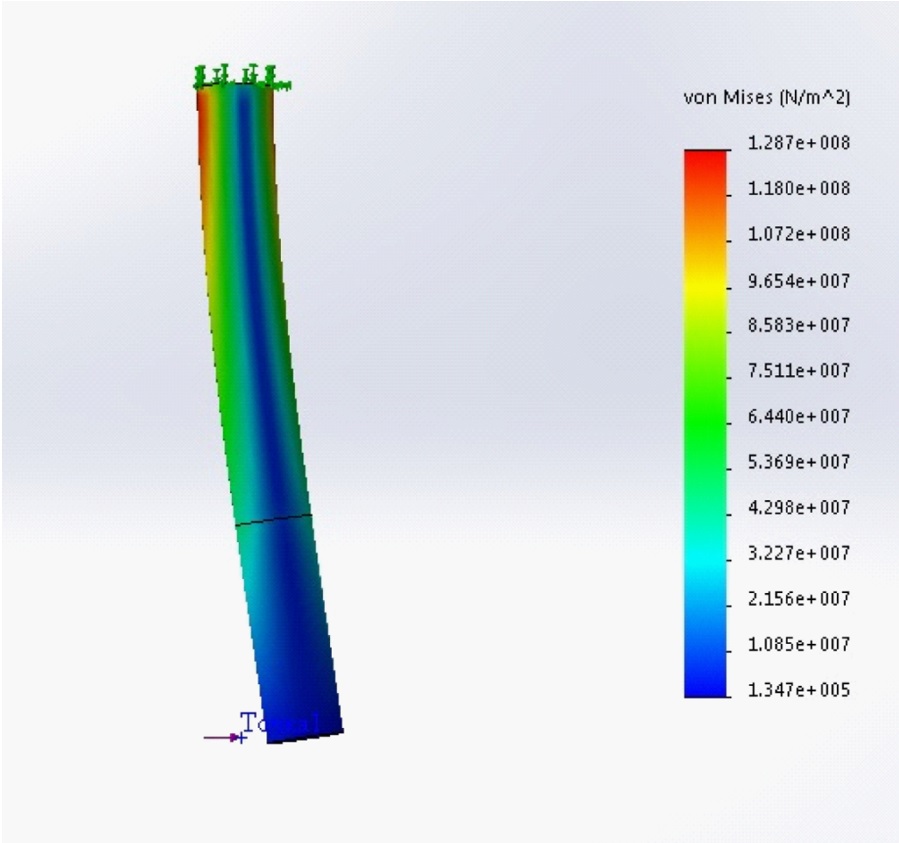
圖5 雙組份銑刀模型中應變值的分佈規律
.jpg)
圖6 變形值的變化規律(垂直撓度)
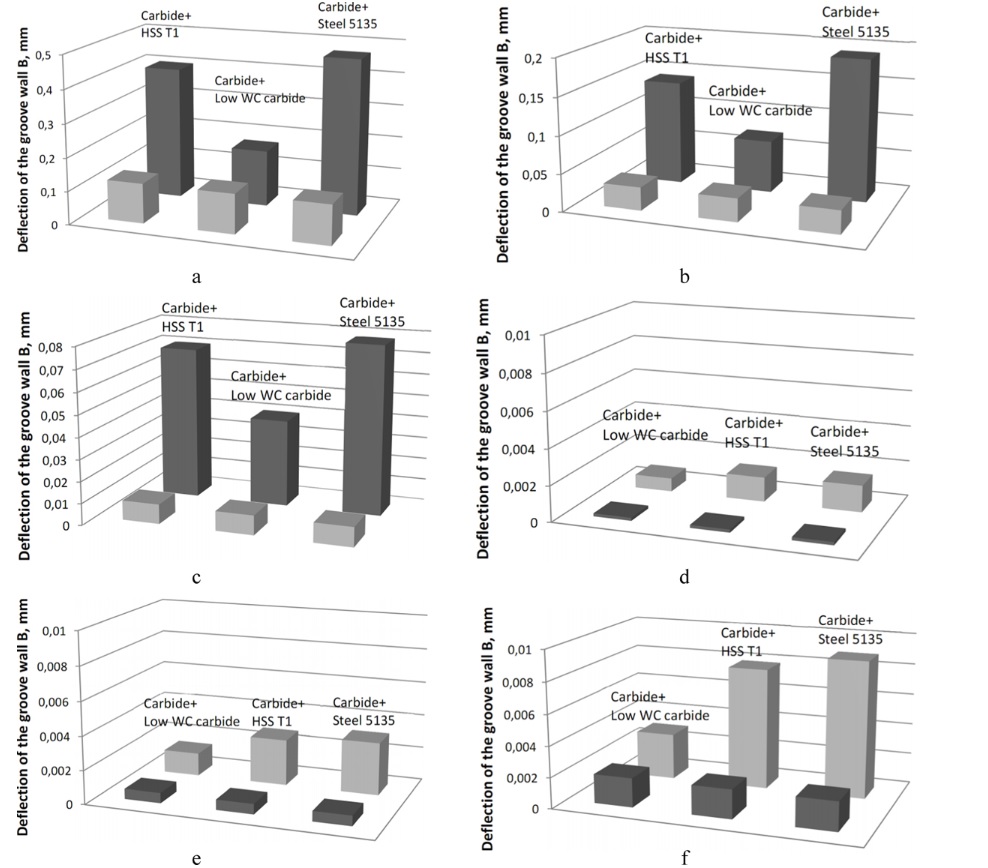
圖7 槽壁加工精度參數比較命名圖((a、b、c)vc=200;(d、e、f)300 m/min,(a、b、c)ap=40;(d、e、f)5 mm,(a、b、c)fz=0.1;(d、e、f)0.15 mm/齒)
4.2奈米級多層複合塗層(NMCC)雙組份銑刀的應用
從眾多論文中可以看出,使用改性塗層不僅可以提高銑刀的壽命和可靠性,而且對切削過程中的參數,如切削力以及切削區的溫度和振動等都會產生很大影響。而這些參數的變化又會直接影響加工精度。因此,可以認為,使用改性塗層,特別是NMCC,將進一步提高雙組分銑刀的加工精度參數。選用總厚度為3μm的NMCC Zr-ZrN-(ZrCrAl)N作為改性塗層。選擇上述NMCC的原因是需要提供足夠的硬度,同時具有良好的韌性和抗裂性,選擇的依據是以往的研究。圖8為NMCC Zr-ZrAlN-(ZrCrAl)N的橫向截面上的微觀結構。奈米層的厚度為20-40nm,塗層厚度為3μm。
所進行的切削試驗(圖9)證實了上述假設,並發現使用NMCC可以將使用雙組分銑刀的加工精度參數設置為接近使用整體式銑刀的加工參數,在某些情況下(使用低WC硬質合金的刀柄時),甚至可以超過這些特性。
N%20on%20a%20transversal%20cross%20section.jpg)
所進行的切削試驗(圖9)證實了上述假設,並發現使用NMCC可以將使用雙組分銑刀的加工精度參數設置為接近使用整體式銑刀的加工參數,在某些情況下(使用低WC硬質合金的刀柄時),甚至可以超過這些特性。
N%20on%20a%20transversal%20cross%20section.jpg)
圖8 NMCC Zr-ZrAlN-(ZrCrAl)N的橫向截面上的微觀結構
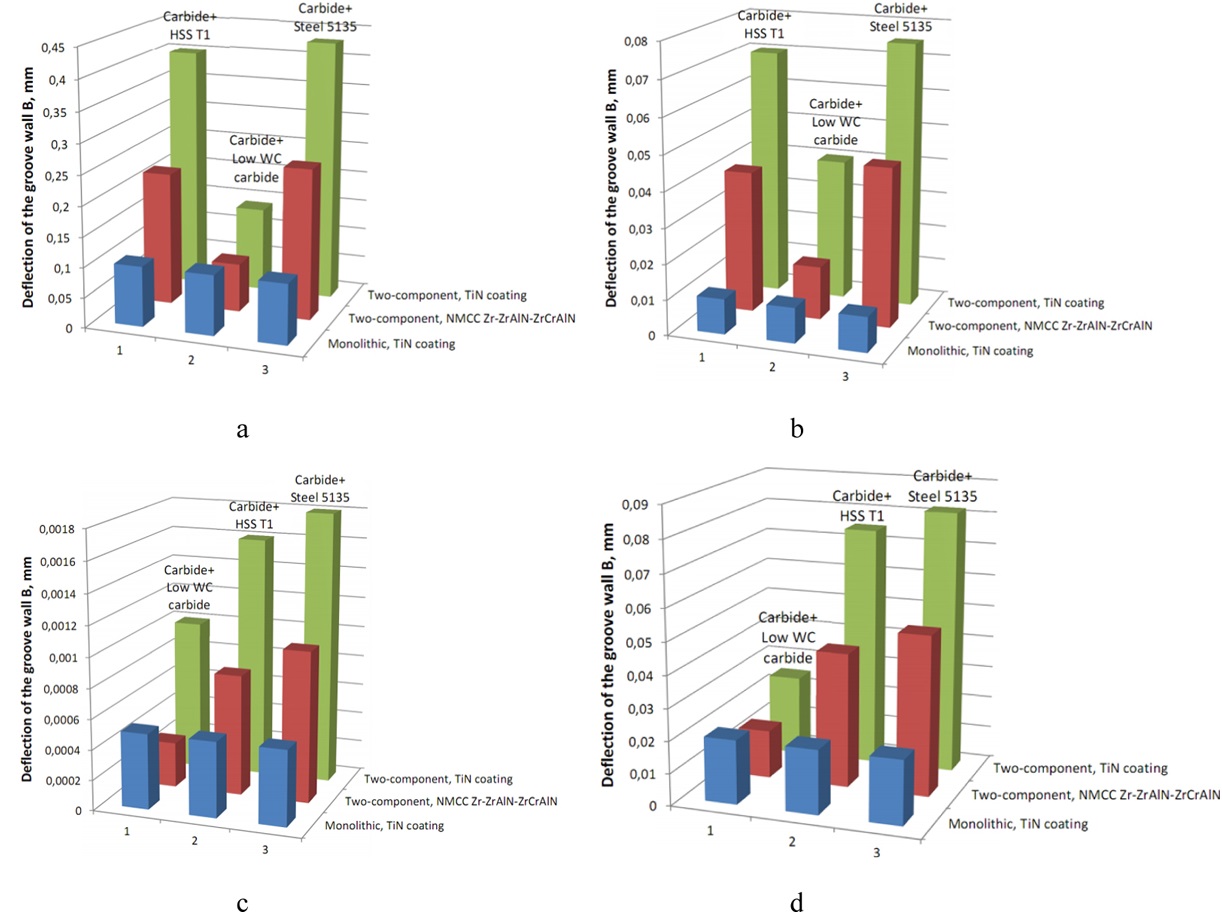
圖9 槽壁加工精度參數比較命名圖(a,b)vc=200;(c,d)300 m/min,(a,b)ap=40;(c,d)5 mm,(a,b )fz=0.1;(c,d)0.15 mm/齒)。(a)槽深40mm,銑刀總長220毫米;(b)槽深40毫米,銑刀總長90毫米;(c)槽深5毫米,銑刀總長90毫米;(d)槽深5毫米,銑刀總長220毫米
4.3 端銑磨損的性質研究
考慮到整體式和雙組份端銑刀的磨損性質的差異,刀柄為低WC硬質合金,溝槽深度為40mm,端銑刀總長度為90mm(vc=200m/min,ap=40mm ,fz=0.1mm/齒)。銑削25 min後,側面磨損的磨損值和磨損性質的比較見圖10。
考慮到上述銑削參數下,銑削25min後的端銑齒的磨損性質。對於帶有TiN塗層的雙組份立銑刀,可以觀察到脆性斷裂,導致災難性的磨損(圖11a和b)。這種類型的磨損可能與雙組份立銑刀的剛性降低而產生的振動和衝擊載荷增加有關。對於帶有TiN塗層的整體式立銑刀(圖11c和d),平均磨損是典型的,沒有明顯的剝落。側翼磨損地值約為130μm。對於採用NMCC Zr-ZrAlN-(ZrCrAl)N的雙組份立銑刀(圖11e和f),磨損的平衡性是典型的,沒有形成微缺口和脆性失效。經過25min的研磨,端銑的側面磨損值最低,為59μm。
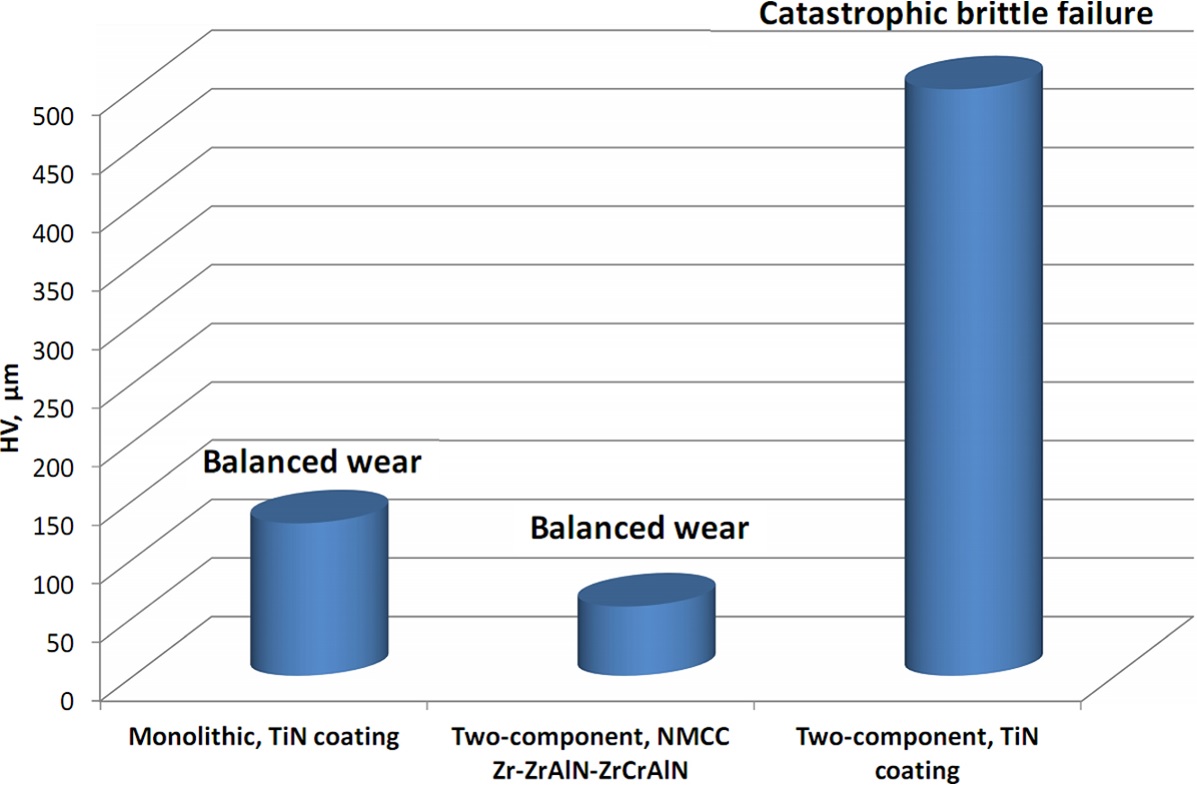
考慮到上述銑削參數下,銑削25min後的端銑齒的磨損性質。對於帶有TiN塗層的雙組份立銑刀,可以觀察到脆性斷裂,導致災難性的磨損(圖11a和b)。這種類型的磨損可能與雙組份立銑刀的剛性降低而產生的振動和衝擊載荷增加有關。對於帶有TiN塗層的整體式立銑刀(圖11c和d),平均磨損是典型的,沒有明顯的剝落。側翼磨損地值約為130μm。對於採用NMCC Zr-ZrAlN-(ZrCrAl)N的雙組份立銑刀(圖11e和f),磨損的平衡性是典型的,沒有形成微缺口和脆性失效。經過25min的研磨,端銑的側面磨損值最低,為59μm。
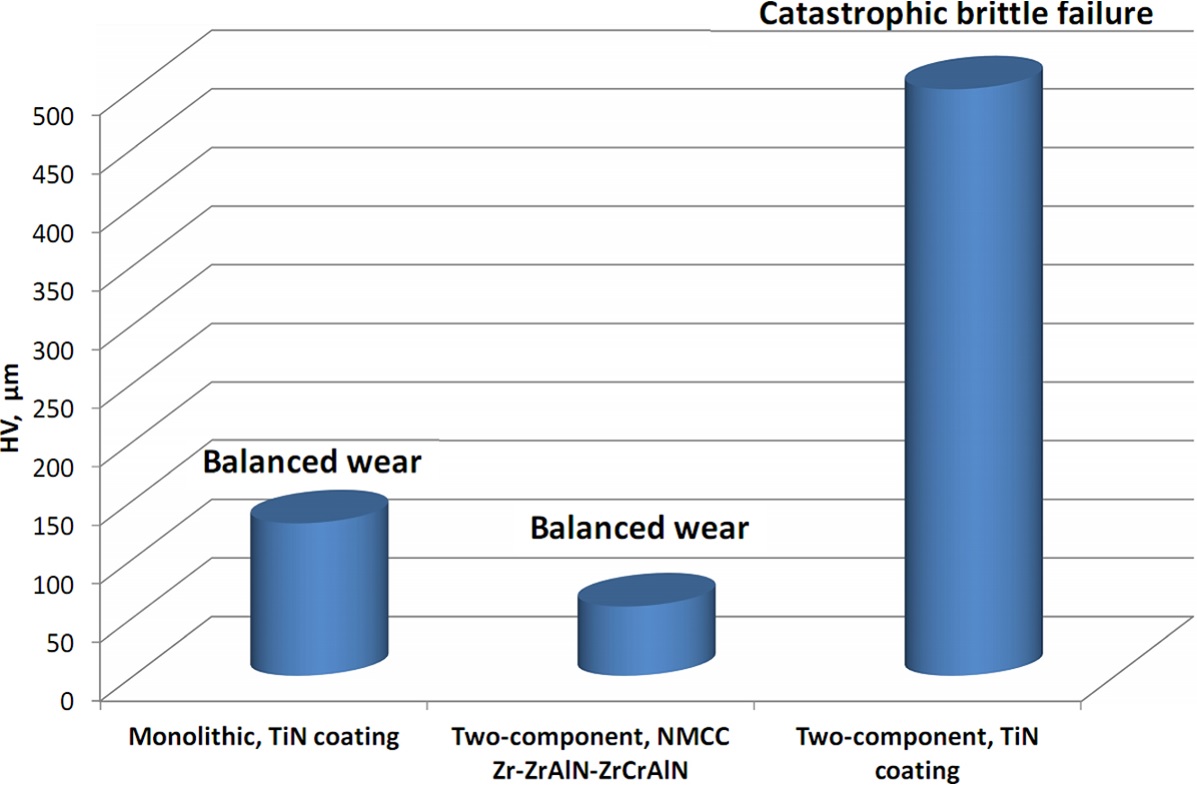
圖10 整體式和雙組分式立銑刀在溝槽深度為40毫米、立銑刀總長度為90毫米(vc=200米/分鐘,ap=40毫米,fz=0.1毫米/齒)的情況下,銑削25分鐘後,側面磨損地磨損值和磨損性質的比較
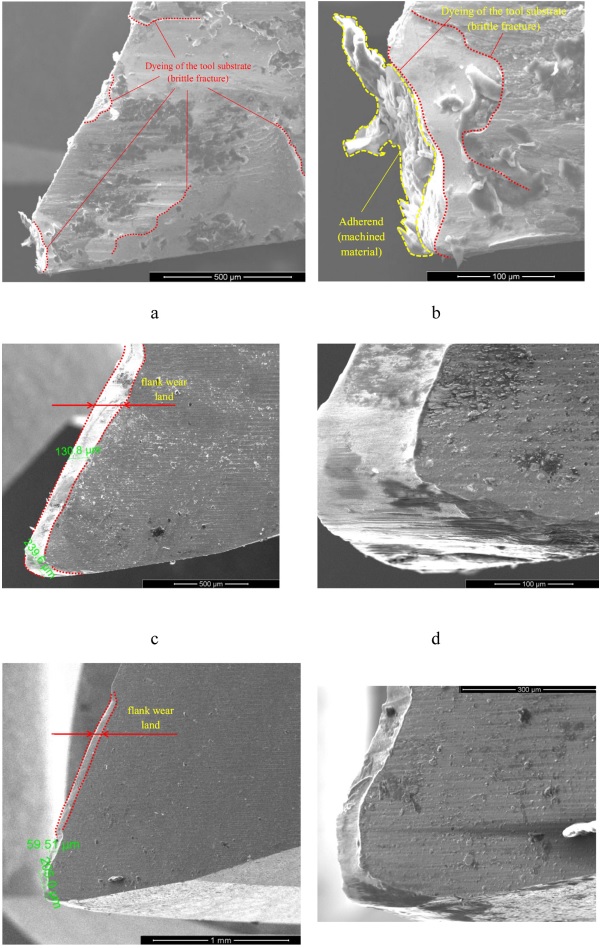
圖11 溝槽深度為40mm,端銑總長度為90的情況下,切削25分鐘後,端銑刀齒的磨損性質:(a,b)硬質合金+5135鋼,TiN塗層,(c,d)整體式,TiN塗層,(e,f)硬質合金+低WC硬質合金,NMCC Zr-ZrAlN-(ZrCrAl)N
5. 結論
考慮了雙組分立銑刀作為整體式立銑刀替代品的各方面應用。研究表明,在一定的加工條件下(相對較短的立銑刀長度和銑削深度),雙組分立銑刀的加工精度與整體式立銑刀相當。採用多層複合奈米結構塗層,特別是Zr-ZrAlN-(ZrCrAl)N,由於降低了切削力、溫度和切削區的振動,使加工精度進一步提高成為可能。在加工可加工性好的材料製成的工件時,宜採用雙組分立銑刀。在加工難切削材料,特別是鋁鋰合金時,採用多層複合奈米結構塗層的雙組份立銑刀也可以替代整體式立銑刀。
應用SolidWorks軟件進行有限元模擬,我們可以得到端銑刀的應變空間模式及其各部分相應的變形值。
根據研究結果,還可以得出以下結論。
• 與切削部分的材料相比,刀柄材料應具有較高的抗循環疲勞失效能力和保持較低硬度的能力。
• 雙組分端銑刀的變形量比實心端銑刀的變形量略高;但總的來說,能滿足一般機械工程行業工件的精度參數和飛機、船舶部件工件的非相鄰表面的精度參數。
• 使用特殊的多層複合奈米結構塗層,可以保證立銑刀磨損的平衡性,同時顯著提高其耐磨性。
因此,使用具有多層複合奈米結構塗層的雙組份立銑刀,可以降低加工成本(通過降低立銑刀成本20%~25%),同時保持甚至提高銑刀壽命(與採用商業塗層的整體式立銑刀相比,壽命在30%~50%)和加工精度參數。