Machinability of titanium alloys under various machining environment
2020-04-29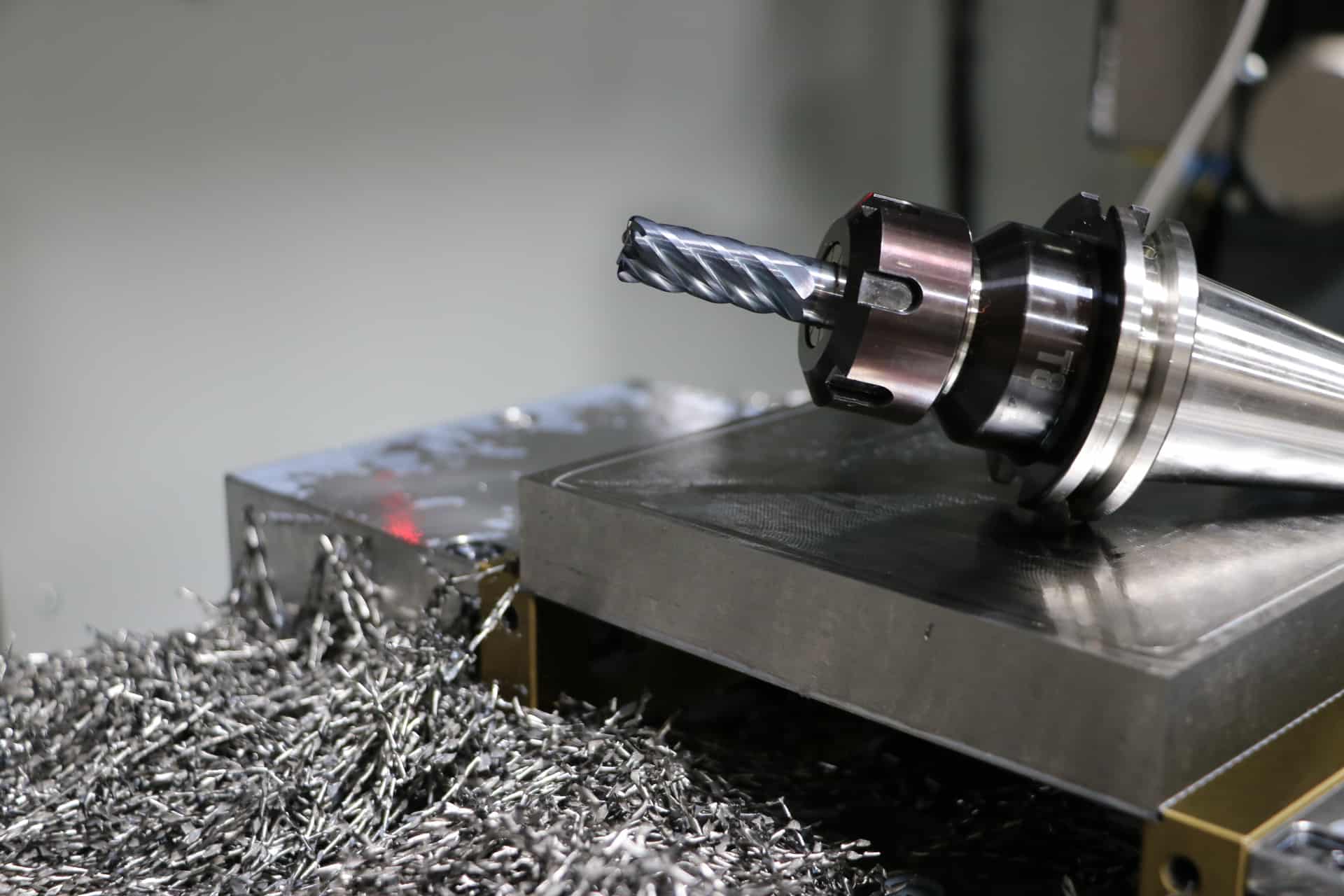
Abstract
Titanium alloys are widely used in aerospace, chemical, marine and automotive industries, especially high-end automobiles due to their excellent strength-to-weight ratio, corrosion resistance, and ability to retain strength at high temperature. However, these alloys are classified as a ‘difficult-to-cut’ due to their poor thermal conductivity, reactivity with tool material, high strength and low modulus of elasticity. Besides various measures to improve machinability of the titanium alloys, the key areas of research pertaining their machining are – cutting tool material and geometry development, formulation of new lubricants and techniques of lubricant application, use of varying machining environments to improve machinability and so on. This article focuses on machinability of titanium alloys under various machining environments such as - LN2, elevated temperature and mist jet cooling. The main objective of the paper is to understand the effect of change in machining environment on various aspects of machining of titanium alloys viz. tool wear, cutting forces, vibration and chatter, surface roughness and chip morphology. It is evident that the LN2 and mist jet environments effectively cool the cutting zone and reduce the tool wear. On the other hand, the elevated temperature environment reduces the cutting forces and thereby increases the material removal rate along and surface quality. Based on the study, recommendations to improve the machinability of titanium alloys have been evolved.
1. Introduction
Reducing the mass of a vehicle and thereby fuel consumption is one of the most important objective of research on automotive materials. Titanium alloys are the promising automotive materials due to their excellent ‘strength-to-weight’ ratio, high corrosion resistance and ability to maintain the strength at high temperature. However, titanium alloys have limited applications in the consumer automotive segments due to their higher processing cost. Properties of titanium alloys like poor thermal conductivity, low modulus of elasticity, ability to maintain strength at high temperature and reactivity with the tool material increases the processing cost of titanium alloys. A significant research has been carried out to reduce the processing cost of titanium alloys through advancement in tool material and geometry, formulation of new lubricants and techniques of lubricant application, coating, and varying machining environments and so on. This article presents an overview of research on the machining environments used to machine titanium alloys. Various environments for machining titanium alloys and their features are briefly explained as follows –
a. Dry machining environment
In this environment, machining is carried out without any lubrication. The advantage of this environment is cleaner part, no waste generation, reduced cost of machining and reduced cost of chip re-cycling as there is no residual oil.
b. High pressure coolant environment
A high pressure coolant penetrates into the tool-work and tool-chip contact region, thus providing a better cooling effect. It decreases tool wear through lubrication of the contact areas. The high pressure coolant jet creates a hydraulic wedge between tool and work, penetrating the interface with a speed exceeding that required even for the high-speed machining and also alters chip flow condition.
c. Cryogenic environment in this environment
Cryogenic lubricants particularly LN2, CO2, etc. are injected between chiptool interface which effectively cool the cutting zone. The method of application of cryogenic cooling are pre-cooling the work piece, indirect cooling of tool insert, general flooding, and machining in an enclosed bath. The LN2 absorbs heat, evaporates quickly, and forms a fluid gas cushion between the chip and the tool face that functions as a lubricant. LN2 environment is nontoxic, inexpensive and clean. It removes heat effectively from the cutting zone and minimizes tool wear. Also, it introduces compressive residual stresses on the machined surfaces which enhance its fatigue life.
d. Thermally-enhanced machining environment in this environment
The material to be machined is heated at elevated temperature thus, reducing its strength. The flow stress and strain hardening rate of the material decrease with an increase in the temperature. This approach aims at higher material removal rate without corresponding loss in the tool life. The elevated temperature of the work piece is achieved by heating it with Laser, plasma, gas or induction heating. Thus, machining titanium alloys at elevated temperature reduces the cutting forces, eliminate coolant thus, making it more environment friendly. In addition, it also reduces vibration in the tool-work-machine system due to the segmentation.
e. Minimum quantity lubrication in this kind of machining environment
A mixture of oil and compressed air in the form of mist is supplied between the work tool interfaces. Small oil droplets carried by air fly penetrates directly into the working zone, providing the needed cooling and lubricating action. Mist is generated by the atomization process which converts the bulk liquid into a spray or mist, by passing the liquid through a nozzle. The mist jet lubrication significantly reduces the temperature at the cutting zone thus improving the tool life. Table 1 summarizes the main features of the three machining environments.
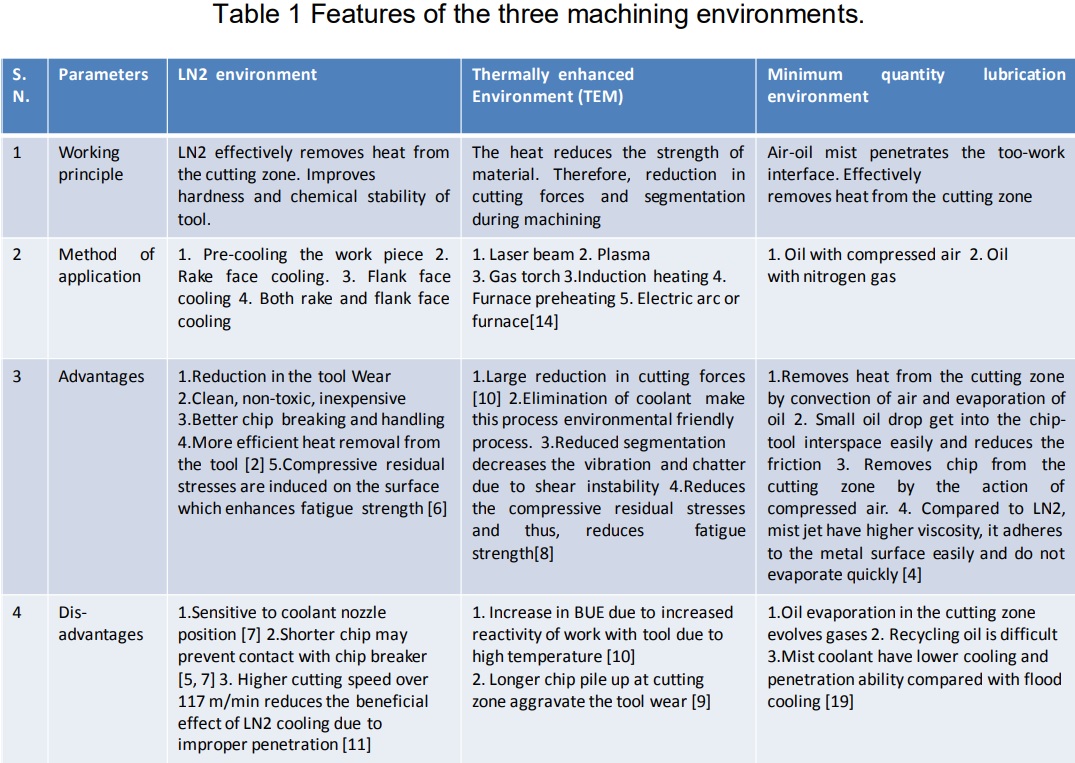
2. Comparison of LN2, elevated temperature and mist jet machining environment
As discussed in the previous section, the chip-tool and work-tool interface temperature obtained under LN2, elevated temperature and mist jet machining environment differs significantly. Here, a comparison of the three machining environments is presented considering the various machining parameters like tool wear, cutting forces, vibration and chatter, chip length, chip breaker position and chip morphology.
i. Tool wear
Under the three machining environments, different mechanisms of tool wear operate in machining titanium alloys. Under LN2 environment, a large reduction of the order of 60% in the work-tool interface temperature is observed due to effective cooling at the shear zone. This reduces the reactivity of titanium with tool material. Therefore, a decrease in the diffusion of alloying elements particularly cobalt from the tool material is observed. This results in an improvement in the tool life. Also, an increase in the hardness and the chemical stability of tool due to LN2 cooling helps reduce the tool wear. On the other hand, at elevated temperature, higher temperature at the cutting zone increases diffusion of cobalt from the tool material. This gives rise to the diffusion type tool wear.At LN2 temperature, due to a smaller chip contact length on the rake face of the tool, crater is formed closer to the cutting edge. On the other hand, at elevated temperature, due to larger chip length, the contact of chip with the rake face increases. This forms wider crater, away from the cutting edge. Also, an increase in the friction between chip and the rake face increases the heat transferred to the tool. In addition, LN2 cooling increases the material brittleness. This reduces the sticking property of material to the tool. A smaller width of secondary deformation zone observed on the chip microstructure shows a reduction in the friction coefficient between work-tool interfaces. This decreases the possibility of formation of built-up edge at the cutting edge of the tool, under the LN2 machining environment. On the other hand, heating the work increases the sticking property of the tool material. Also, a higher temperature at the cutting zone welds the chip to the cutting edge of the tool thus, increasing the possibility of built-up edge formation. Therefore, at elevated temperature, an increase in the tool wear is observed.
In the case of mist jet environment, the micro-droplet of mist vaporizes as a blast of water vapour in the cutting zone. These droplets effectively penetrate at chip tool interface. They thus greatly reduce the friction, heat and the abrasion conditions on the cutting tool. The performance of the mist jet was good particularly at the higher cutting speed above 120 m/min. A study shows that mist jet lubrication with compressed nitrogen gas reduces the cutting edge temperature, thus minimizing the diffusion rate of cobalt from the work material and improving the tool life by about three times.
ii. Cutting forces
The three machining environments change the friction between chip-tool interfaces differently. Also, the extent of coolant approaching at the chip-tool interface affects the effectiveness of cooling.At LN2 temperature, cutting forces increase depending upon the method of cooling applied at the cutting zone. A large increase of 20% in the cutting force was observed when workpiece was pre-cooled before machining. A small increase in cutting and thrust forces by 7% and 13% respectively was observed when rake and flank faces of the tool were indirectly cooled with LN2. However, under the same machining conditions, thrust forces decreased by 8%. At elevated temperature, the cutting and the thrust forces decreased by 10% and 22 %, respectively when machined at the elevated temperature of 250 °C due to a reduction in the material strength. In a mist jet cooling environment, no significant change in the cutting forces was identified.
iii. Vibration and chatter
At LN2 temperature, chip morphology obtained is segmented, see Fig. 1 a. The segmentation increases chatter and vibration in machine-tool-work system. However, at elevated temperature, a reduction in the segmentation is observed in the machined chips of titanium alloys, see Fig. 1 b. At elevated temperature, a reduction in the shear band forming tendency in the titanium alloys is observed. Therefore, a fluctuation in the cutting forces due to the segmentation decreases thus, reducing the chatter and vibration in work-tool-machine system.
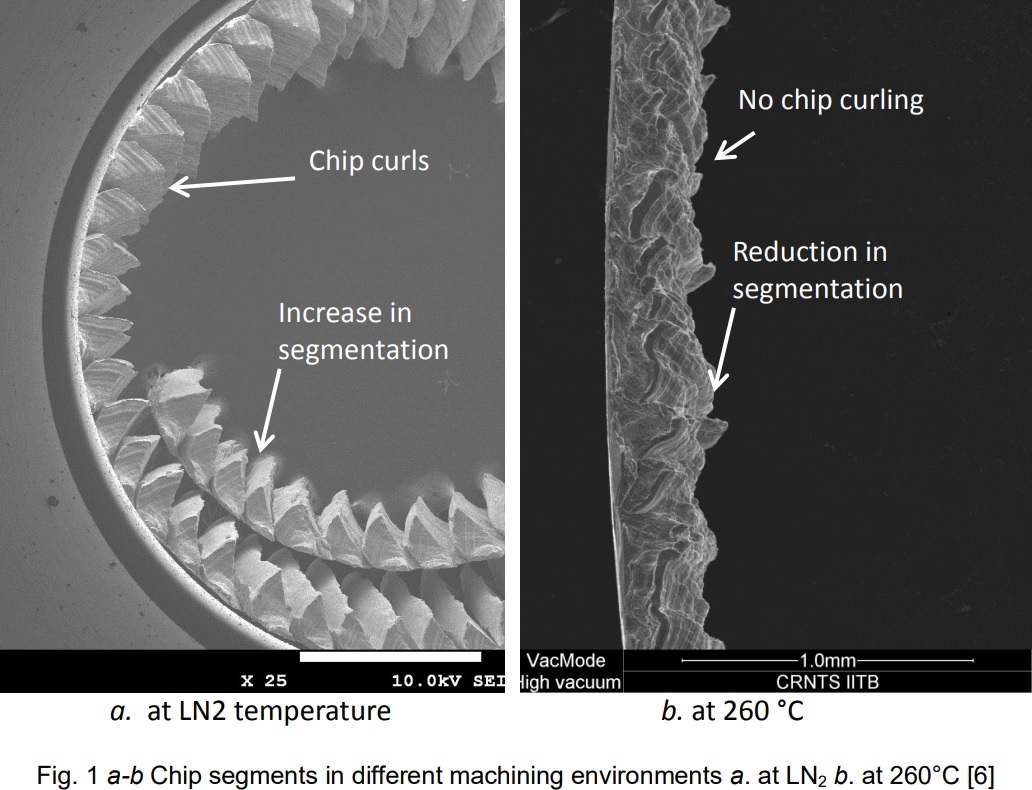
iv. Chip length
A smaller chip-tool contact length is observed under LN2 environment. Due to the cracks at the shear plane, the chips formed at LN2 temperature break easily. Therefore, chips of shorter length are formed. These chips easily get disposed off from the cutting zone. Also, smaller chiptool contact length reduces the heat transferred to the cutting tool. On the other hand, at elevated temperature, an increase in the chips-tool contact length increases the chip length formed during machining. It also increases the heat transferred from chip to the tool. Thus, tools wear increases at the elevated temperature.In mist jet cooling environment, better cooling and high impact velocity of jet particle form short coiled chips. These chips get lifted and cooled down before striking the chip breaker to form short chips which are the desired one.
v. Modification of chip breaker position
At LN2 temperature, the chips do not reach the chip breaker due to its shorter length. Therefore, chip breaker position needs to be located closer to the cutting edge. However, at elevated temperature, due to longer chip length, chips reach the chip breaker and break easily. The mist cooling produces longer chips than the LN2 environment thus, chip breaker breaks the chips easily.
vi. Surface roughness
At LN2 temperature, an improvement in the surface roughness is observed due to a reduction in the tool wear. The surface roughness of 1.5 µm was achieved with indirect cooling of the flank and rake face of the tool. However, direct cooling of chip-tool interface with LN2 increases the surface roughness to 4.5 µm under the same cutting parameter. At elevated temperature, a smoother cutting action is observed due to a reduction in cutting forces. A reduction in the surface roughness value of the order of 0.3 µm at 200 to 600 °C was observed.In case of mist jet cooling, abundance of water vapour in the cutting zone provides enough lubrication, thus a reduction in the surface roughness was observed as compared with the dry machining. With an increase in the cutting speed from 38 m/min to 120 m/min, a reduction in the Ra value from 1.5 µm to 1 µm was observed thus, resulting in a better surface quality.
vii. Chip morphology
Microstructure of chip shows grain size, shape, orientation and the deformation mechanism. This data is related with chip hardness, strain in the chip, and nature of shear and normal stresses which gives insight into the change in the machinability of the titanium alloys under different machining environments.The microstructure of chips obtained at two different machining environments and at same cutting speed of 23.4 m/min and 0.11 mm/rev feed rate is shown in Fig. 2 a-d. At LN2 temperature, grains in the chip were highly elongated. However, at the elevated temperature of 260°C, no elongation in grains was evident; see Fig. 2 c, d. At both machining environments, very thin shear bands are observed, see Fig. 2 b, d. But, at LN2 temperature, larger cracks along the shear plane are observed, see Fig. 2 a, b.
Thus, chips obtained at LN2 temperature appear highly strained. The elongated grains indicate no sign of recovery during the machining operation. This is due to the low work-tool interface temperature. The elongated grains make the chip harder which exerts significant abrading forces on the rake face of the cutting tool. However, at the elevated temperature of 350°C, grains in the chips are not elongated. These chips exert low abrading forces on the rake face of the cutting tool.
Normal stresses are responsible for the crack initiation on the shear plane. The cracks propagate from the free surface of the chip to the tool end. At LN2 temperature, the appearance of cracks along the shear plane shows an increase in the intensity of normal stresses responsible for the tearing of work material. On the other hand, at elevated temperature, the absence of cracks at the free surface of the chip points to a decrease in the magnitude of normal stresses on the shear plane.
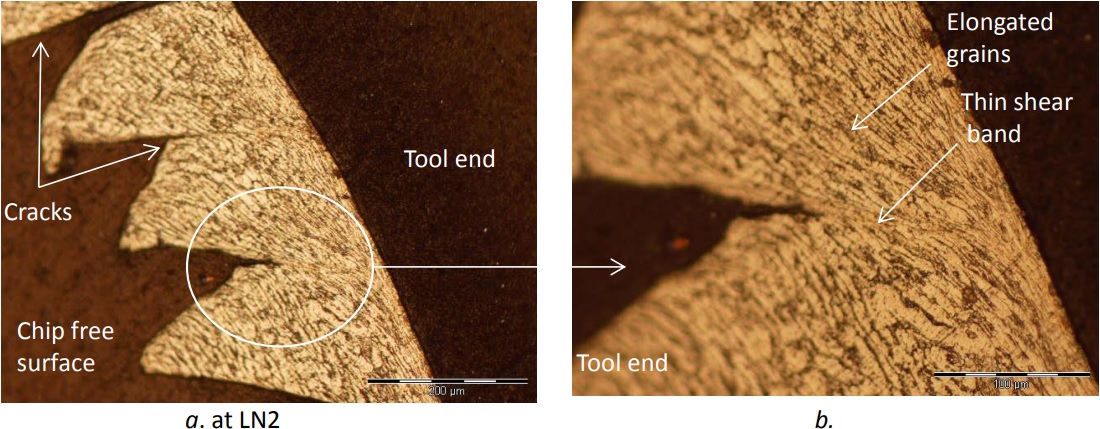
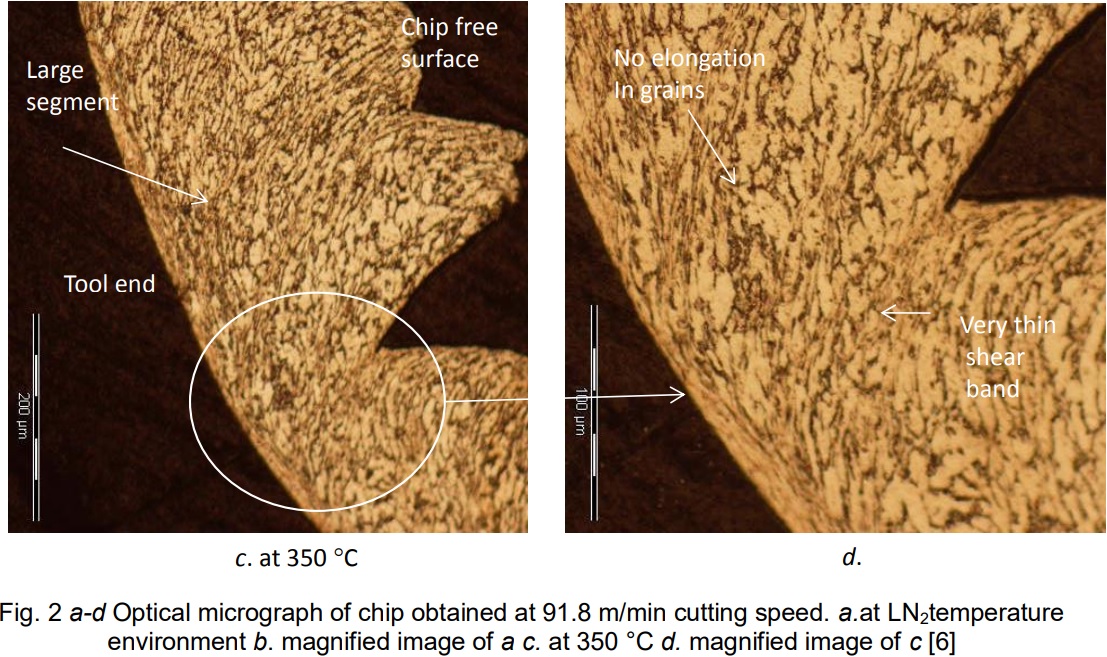
A summary of the influence of three machining environments under different machining parameters as discussed above is presented in the Table 2.
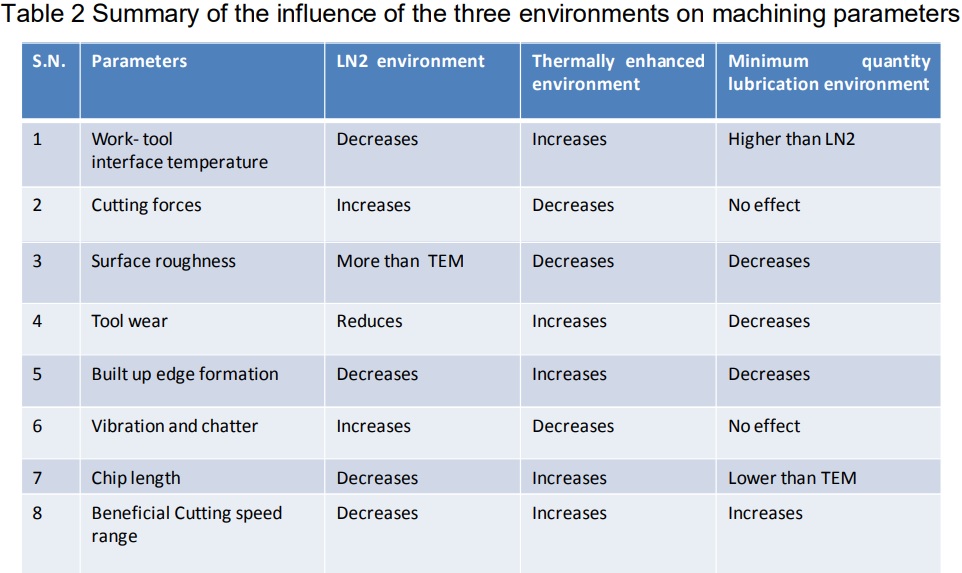
Summary and recommendations
The machining parameters along with the machining environments cause several changes in the mechanics of machining of titanium alloys. LN2 and mist jet lubrication environments effectively reduce the temperature at the cutting zone. They help minimize the tool wear in machining of titanium alloys. Also, these two machining environments show smaller chip contact length and improved machined surface quality. However, at elevated temperature environment, a reduction is observed in the magnitude of cutting forces and vibrations at the tool-workmachine system due to segmentation. Machining at elevated temperature reduces the segmentation and approaches the machining process towards forming continuous chips. However, at elevated temperature, diffusion-type tool wear increases due to higher temperature at the cutting zone. The hybrid machining, which heats the work material and reduce its strength, and cools the tool such that it reduces the diffusion from the tool material, provides a promising solution to achieve higher material removal rate at the lowest tool wear rate. A comparative study of LN2 and mist jet cooling shows that the mist jet coolant has a better lubrication property. Therefore, at higher cutting speeds, above 120 m/min, mist jet cooling serves the purpose better than the LN2 cooling.