Sustainable Milling of Ti-6Al-4V: Investigating the Effects of Milling Orientation, End mill's Helix Angle, and Type of Cryogenic Coolant
2020-05-25Abstract
Ti-6Al-4V, the most commonly used alloy of titanium, possesses excellent mechanical properties and corrosion resistance, which is the prime reason for the continual rise in its industrial demand worldwide. The extraordinary mechanical properties of the alloy are viewed as a hindrance when it comes to its shaping processes, and the process of milling is no exception to it. The generation of intense heat flux around the cutting zones is an established reason of poor machinability of the alloy and unacceptably low sustainability of its machining. The work presented in this paper attempts to enhance sustainability of milling Ti-6Al-4V by investigating the effects of milling orientation, end mill's helix angle, cutting speed, and the type of cryogenic coolant and lubricant on the sustainability measures, such as end mill damage, cutting energy consumption, process cost, milling forces, and work surface roughness. It was found that micro-lubrication is more effective than the two commonly used cryogenic coolants (carbon dioxide snow and liquid nitrogen) in reducing end mill wear, work surface roughness, process cost, and energy consumption. Furthermore, down-milling enormously outperformed up-milling with respect to end mill wear, work surface quality, and process cost. Likewise, the high levels of end mill's helix angle and cutting speed also proved to be beneficial for milling sustainability.
1. Introduction
Titanium alloys gained an unprecedented rise in their demand from various engineering sectors due to their excellent mechanical properties and corrosion resistance. The same properties considered as excellent during the “use” phase are termed as unfavorable during the “manufacturing” phase of their life cycle. With regard to the machining domain, the same unfavorable properties are responsible for their low machinability, which render the cutting process unsustainable. The low machinability is attributed mainly to high strength, chemical affinity with the end mill materials, and a short chip-rake contact length. A titanium work is, thus, machined with formation of an intense heat flux around the cutting edge and consumption of exceedingly high cutting energy, leading to acceleration of the temperature-dependent modes of end mill wear.
The high end mill wear rates, resulting in frequent changes of cutting end mills or edges, leave the machining process highly unsustainable, economically as well as environmentally. The problem is generally negotiated either by lowering the material removal rates or by applying emulsion-based coolants, neither of which actually offers a sustainable solution. With regard to quashing the intense heat flux around the cutting areas, the application of cryogenic fluids, especially liquid nitrogen (LN2), fares very well. The fluids offer a viable solution because of extremely low operational temperatures, no waste generation, and controllable flow rates. Additionally, application of micro-lubrication, also known as minimum quantity of lubrication (MQL), also proved to be very beneficial in enhancing end mill life and improving surface quality in machining of titanium alloys conducted at medium cutting speeds. MQL is a near-dry machining method in which a miniscule quantity of lubricating oil is pulverized into a stream of air, and the resulting aerosol is applied onto the cutting areas.
Although steady progress is being made regarding quantification of the effects of cryogenic coolants with regard to the continuous machining processes, not much effort is being put up concerning interrupted machining processes, such as milling. Cryogenic milling is distinct from continuous machining processes performed under cryogenic environment in the sense that the cutting teeth of a milling end mill periodically and rapidly engage and disengage with the work material, leading to cyclic heating (caused by thermal energy released by work material’s plastic deformation) and cooling (caused by interaction with the incoming cryogenic fluid) of the cutting edges. Such a course is expected to induce thermal shocks in the teeth, leading to cracking, chipping, and more catastrophic forms of end mill damage. Furthermore, a comparative analysis regarding the cooling effects of an evaporative cryogenic fluid, such as LN2, and a throttling-based cryogenic fluid, such as CO2 snow, is also required. With regard to the milling process, two distinct parameters, milling orientation and end mill's helix angle, are also expected to have effects on the process’s sustainability measures, such as end mill damage rate, cutting energy consumption, work surface roughness, process cost, and cutting forces.
Literature Review
This sub-section presents a review of the published work concerning the issues of milling titanium alloys, application of cryogenic coolants in machining (especially milling) of titanium, potentials of using micro-lubrication in milling, and machining sustainability measures. It is reported that an increase in the flow rate of liquid nitrogen can prolong the end mill life in machining of titanium alloys. Furthermore, the surface integrity would be greatly improved when the pressure and flow rate of the coolant are increased. Milling of Ti-6Al-4V with liquid carbon dioxide can greatly reduce the lateral crack propagation and chipping. Therefore, it can be used to prolong end mill life as compared to emulsion-based cooling. The effects of end mill life criterion, work material’s temper state, cutting parameters, and micro-lubrication on the sustainability measures of a milling process were studied. It was found that the material’s temper state and the option of using MQL were the most influential parameters with respect to the sustainability measures, such as specific cutting energy, end mill life, and process cost.
Sartori et al. reported that an MQL system amalgamated with a CO2 and LN2 distribution system could optimize the lubrication and cooling effect, leading to a significant reduction in crater wear. In another study, it was reported that machining under flood coolant does not reduce surface roughness. The authors also reported that LN2 hybridized with oil-based MQL can yield the lowest cutting forces of all the tested coolants. Isakson et al. reported that the cooling methods utilizing LN2 and an emulsion-based coolant yielded similar effects on surface integrity. Furthermore, the authors also managed to reduce consumption of the cryogenic coolant to provide a good surface quality without conceding any negative environmental or economic impact. It was found that milling of Ti-6Al-4V with liquid CO2 could greatly reduce chipping and lateral crack propagation; therefore, it can be used to significantly prolong end mill life in comparison with emulsion-based cooling. The effects of using CO2 snow as a coolant and its merger with MQL were investigated in continuous machining of a high-strength β-titanium alloy.
It was found that the usage of CO2 snow and the location of its application was highly influential with respect to the sustainability measures. In another work, it was reported that the cryogenic cooling with LN2 could considerably reduce end mill wear and, thus, lead to an increase in material removal rate. It was concluded that cryogenic machining operating at a given cutting speed can cause much lower energy consumption than machining with a flood coolant. Mia et al. reported that the use of dual jets of LN2 is an excellent way to reduce energy consumption and working temperature, as well as to improve work surface quality. In another experimental study, it was reported that the use of liquid CO2 at a temperature of −79.5 ◦C in cutting of a nickel-chromium alloy could reduce average surface roughness by 42–47%, 24–27%, and 16–21% over dry, wet, and MQL cutting, respectively.
Furthermore, the cryogenic cooling was also found to increase the compressive stresses on the surface and decrease the flank wear. Li et al. presented optimization of milling Ti-6Al-4V alloy with a graphene-dispersed vegetable-oil-based cutting fluid. The results showed significant improvements in the milling performance measures including milling force, temperature, surface micro-hardness, and work surface roughness. Dry and MQL-based milling processes were compared for machining of Inconel 718. MQL was found to improve the end mill life, as well as the work surface finish. An experimental study focused on modeling the effects of end mill wear rate on economic sustainability of milling a titanium alloy. In total, 47.5% and 47.59% less electricity consumption cost and machine operational cost, respectively, were achieved for the cryogenic cooling approach in comparison with dry machining. In another experimental study concerning end-milling of Ti–6Al–4V titanium alloy, the effects of cryogenic cooling on work’s surface integrity were compared with those under dry and flood cooling environments.
The authors reported that cryogenic cooling resulted in up to 31% and 39% lower surface roughness when compared to flood cooling and dry approaches, respectively. A significant reduction in microscopic surface defects under the cryogenic environment was also reported. Dawood et al. studied the effects of the three cutting parameters on machining performance under flood cooling and sustainable dry environments. Dry machining was found to yield better surface finish, but it also sustained more severe adhesion wear, crater wear, and formation of built-up edge. An experimental study evaluated the effects of applying cryogenic cooling with MQL lubrication in contour milling of Inconel 718. The authors claimed superiority of the proposed CroMQL method over the other lubri-cooling techniques. Pusavec et al. presented an experimental study on sustainable machining of Inconel 718 under various lubri-cooling environments such as dry, MQL, cryogenic, and cryo-lubrication. Based on the statistical analyses of the results, the authors concluded that the cooling/lubrication condition had significant effects on the sustainability measures including end mill life, cutting forces, and power consumption.
Milling orientation (up- and down-milling) and end mill's helix angle are amongst the milling parameters, which do not receive much attention with respect to their influence on the process’s sustainability measures. It was reported that both the parameters possessed significant effects on end mill life and work surface roughness in high-speed milling of hardened steels using carbide end mills. End mills with 45◦ helix angle yielded significantly longer end mill life and marginally better surface finish than the 30◦ end mills. Moreover, down-milling was found to provide much better surface finish, but equal end mill life as compared to up-milling.
A end mill orientation optimization model was presented that includes the effect of deflection error caused by milling forces to achieve better machining precision controlling in five-axis surface milling. The effects of up- and down-milling were compared in peripheral milling of a high-alloy steel. The up-milling approach was found to generate compressive residual stresses in the work surface, but with a poor surface finish in comparison with down-milling. An experimental study was performed to compare the effects of up- and down-milling in end-milling of Inconel 718. It was found that the down-milling approach yielded better results in terms of end mill wear as compared to up-milling. Furthermore, the chips formed in up-milling were segmented and continuous as compared to discontinuous ones produced in down-milling. Wan et al. presented an analytical model to quantify the influence of end mill's helix angle on peak cutting force.
The authors found that the peak value of cutting forces decreased with an increase in helix angle for a single engaged cutting edge and that the optimal helix angle corresponding to the minimum peak cutting force was a function of the number of flutes, axial depth of cut, and end mill diameter. Another work focused on quantifying the effect of helix angle on performance of coated carbide end mills for dry side-milling of 304L stainless steel. It was found that the number of axis contact points and effective cutting length increased with increasing helix angle, leading to reduced end mill wear and thinner chips, but with higher cutting temperature. It was concluded that the TiAlN-coated end mill with a high helix angle of 60◦ yielded the best surface finish with an acceptably long end mill life. Another study presented a mathematical model for predicting surface topography and various surface roughness metrics by considering the effects of end mill's helix angle, feed rate, and end mill's eccentricity.
The literature review reveals the following gap between the state of the art and the objectives of this work:
(1) A very limited amount of work is done so far regarding application of cryogenic fluids to milling of titanium alloys as most of the published investigations have focused on turning process only;(2) No searchable work was found regarding comparison of cooling effectiveness between throttling and evaporation based cryogenic coolants applied to intermittent cutting processes;
(3) A limited amount of investigative work is available that quantifies the effects of milling orientation and end mill's helix angle on the sustainability measures of titanium machining.
In perspective of the above mentioned research gap, the presented work aims to quantify and improve the sustainability measures in respect of side- and end-milling of an α + β titanium alloy (Ti-6Al-4V) while employing three kinds of cutting fluids (an evaporative cryogenic coolant, a throttling-based cryogenic coolant, and micro-lubrication), two modes of milling orientation, and two levels each of cutting speed and milling end mill's helix angle. The sustainability measures of the milling process to be evaluated are cutting energy consumption, end mill damage, work surface roughness, machining forces, and process cost.
2. Experimental Work
This section presents the details regarding work material and tooling, predictor variables, responses (sustainability measures), design of experiments, fixed parameters, equipment, and measuring instruments.
2.1. Work Material and Tooling
The work material used in the study is Ti-6Al-4V, a commonly used α + β alloy of titanium. The annealed form of the material is used in the form of a plate having dimensions 75 mm × 200 mm × 19 mm. The heat treatment was done by soaking the work pieces at a temperature between 778 and 782 ◦C for about 70 min, followed by air cooling. The work material, after carrying out the heat treatment process, possessed ultimate tensile strength, yield strength (0.2% proof stress), and elongation of 1003.5 MPa, 927.3 MPa, and 15%, respectively.The end mills used in this study were FIRE-coated cemented tungsten carbide square end mills, having diameter of 8 mm and number of cutting flutes equal to four. FIRE is a multi-layer TiN + TiAlN ceramic coating system that provides extreme wear- and heat-resistant properties to the end mill. The hardness of the coating was 3300 HV, and the coefficient of friction was 0.6. The end mills with a helix angle of 30◦ had total and cutting lengths of 68 mm and 22 mm, respectively, while those with a helix angle of 42◦ had 63 mm and 19 mm, respectively. A new end mill cutter was used for each experimental run. Figure 1 presents the two kinds of end mills used in the experiments.
.jpg)
Figure 1. Ceramic-coated tungsten carbide side- and end mills having helix angles of (a) 42° and (b) 30°.
2.2. Predictors, Responses, and Design of Experiments
The following four predictor variables were controlled in the milling experiments:(1) Cutting fluid. The following three levels were tested with respect to this predictor: (a) evaporative cryogenic fluid (liquid nitrogen); (b) throttle cryogenic fluid (CO2 snow); (c) micro-lubrication (minimum quantity of lubrication).
(2) End mill's helix angle, λ (degrees). The two levels chosen for this predictor were 30◦ and 42◦ .
(3) Milling orientation. The two options for this binary predictor were up-milling and down-milling.
(4) Cutting speed, vc (m/min). The two levels chosen for this predictor were 100 m/min and 175 m/min.
The aforementioned levels of the four predictor variables yielded a total of 24 (= 3 × 2 × 2 × 2) experimental runs for the sake of executing a full-factorial design of experiments. Table 1 presents the details regarding the levels of the four predictors controlled in the experiments. It is to be noted that the first and the third predictors were categorical while the other two were numerical. The two levels of the cutting speed (100 and 175 m/min) were selected on the basis of the preliminary tests. Cutting speeds in excess of 200 m/min at the given feed rate and radial depth of cut resulted in the end mills getting red-hot toward the end of the cuts and the cutting edges getting covered with thick adhesions. This observation led to fixation of the upper level of the cutting speed equal to 175 m/min. The lower level, thereupon, was decided as a value between 50% and 60% of the upper one.
Table 1. Levels of the four predictor variables controlled in the experiments. MQL—minimum quantity of lubrication.
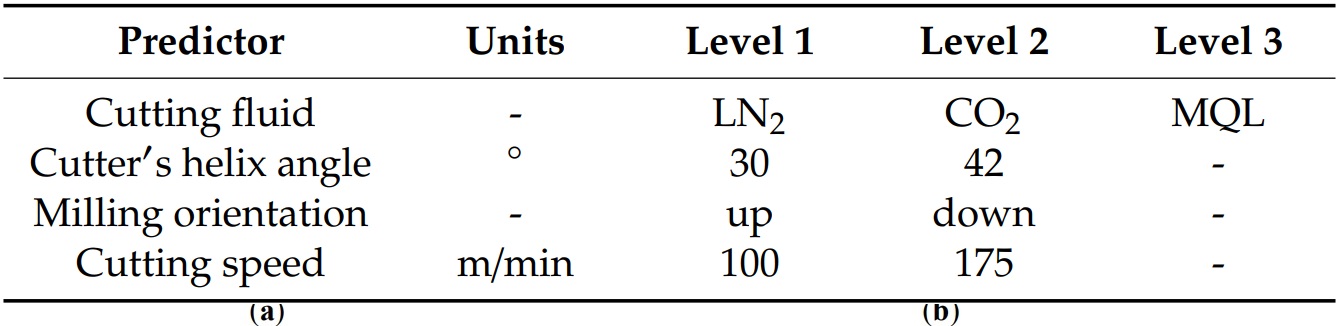
Each experimental run involved removing 600 mm3 of volume of the work material under the following dimensions: 0.5 mm (radial depth of cut) × 8 mm (axial depth of cut) × 150 mm (length of cut). The 150-mm length of cut was completed in two passes of equal length. Figure 2 presents the pictorial description regarding the length of cut and the two depths of cut. A new side- and end mill was used for each experimental run. Up-milling is a cutting approach in which a cutting tooth of the milling cutter enters the work surface with zero chip thickness and exits with a maximum. On the contrary, the tooth enters and exits the work surface with a maximum and zero chip thickness in the down-milling approach.
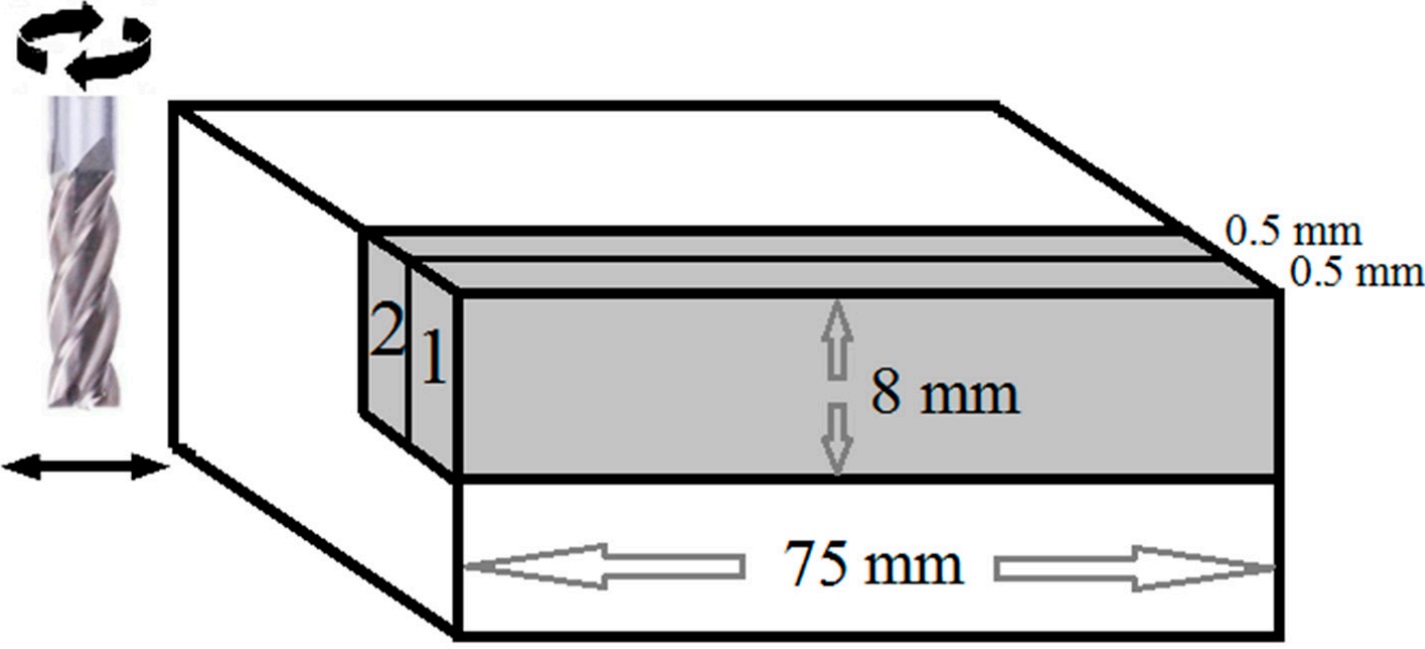
Figure 2. Cutting schematic for each experimental run showing length of cut = 2 × 75 mm2 (not to scale), axial depth of cut = 8 mm, and radial depth of cut = 0.5 mm. The numbers 1 and 2 show the order of the slice removal. The total volume (600 mm3) of material to be removed in each run is shaded gray.
The following responses were evaluated for each of the 24 experimental runs:
(1) Average width of flank wear land on the four cutting teeth of the milling cutter, VB (mm), to be determined after removing the given volume (600 mm3) of the work material.(2) Average arithmetic roughness of the milled surface, Ra (µm).
(3) Specific cutting energy, SCE (J/mm3), averaged for the entire length of cut.
(4) Machining force components, Fx, Fy, and Fz (N), averaged for the entire length of cut. Fx and Fz are aligned with the feed direction and the end mill's axis, respectively, while Fy is the third orthogonal component that falls perpendicular to the milled side surface of the work.
(5) Process cost, PC (TWD/mm3 of work material removed, converted to 100-scale comparative cost values)
Additionally, the other sustainability measures of the milling process, such as waste generation, operator’s safety, and health are discussed in a qualitative way.
2.3. Experimental Set-Up and Measurements
All experiments were performed on Mikron UCP 710, a five-axis, vertical machining center (Mikron Holding, Biel, Switzerland) having maximum rotational speed, feed rate, and power of 18,000 rpm, 20 m/min, and 16 kW, respectively. Milling was performed in a straight line, cutting through the 75-mm side twice during each run. Figure 3 presents the experimental set-up. The throttling-based cryogenic cooling equipment consisted of a storage bottle containing CO2 gas compressed at a pressure of 5.5 MPa. The compressed gas was transported from the bottle to the exit nozzle through a copper tube. The mass flow rate of the CO2 gas at the exit of the 2-mm-diameter nozzle was measured to be 0.5 kg/min against the storage pressure of 5.5 MPa. The exit of the nozzle was located very close to the machining area such that the CO2 gas impacted directly on to the end mill's teeth.The gas on exit expanded and absorbed heat from its surroundings due to the Joule-Thomson effect. The throttling gas, consequently, cooled down to a temperature of about −72 °C, which caused it to convert to a semi-solid state (CO2 snow) adhering to the tooling system and the work’s surface. The evaporation-based cryogenic cooling equipment consisted of a storage dewer containing nitrogen, which was cooled down to a liquid state. The jet of LN2 impinged on to the war containing nitrogen, which was cooled down to a liquid state. The jet of LN2 impinged on to the milling cutter under a flow rate and pressure of 0.5 L/min and 0.1 MPa, respectively, through a 6-mm-diameter nozzle. The temperature of the LN2 jet, measured at the nozzle’s exit, was −197 °C. The direction of the nozzle was adjusted such that the maximum mass of the fluid directly impacted that portion of the cutting teeth which periodically engaged and disengaged with the work material. The micro-lubrication, in the form of minimum quantity of lubrication, was supplied by mixing a vegetable-based oil at a rate 258 7 of 25 mL/h in the flow of air compressed to a pressure of 0.6 MPa. The resulting aerosol was applied to the milling cutter at the region adjacent to the work surface.
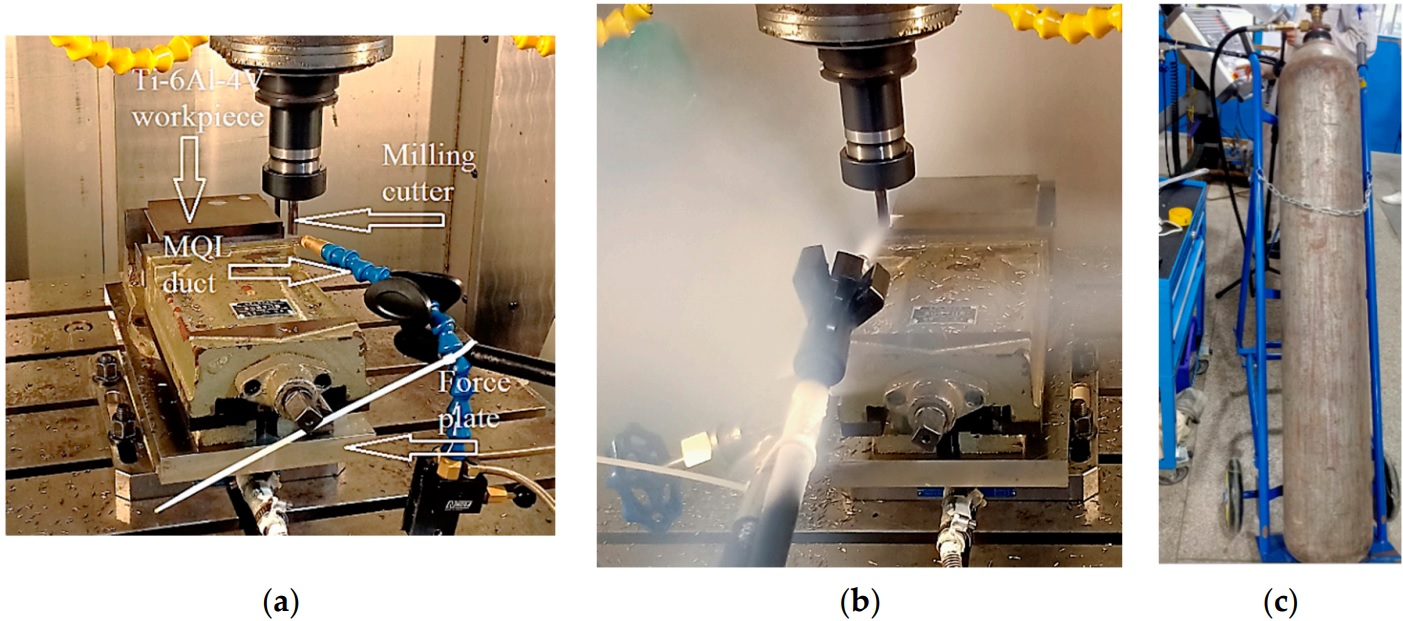
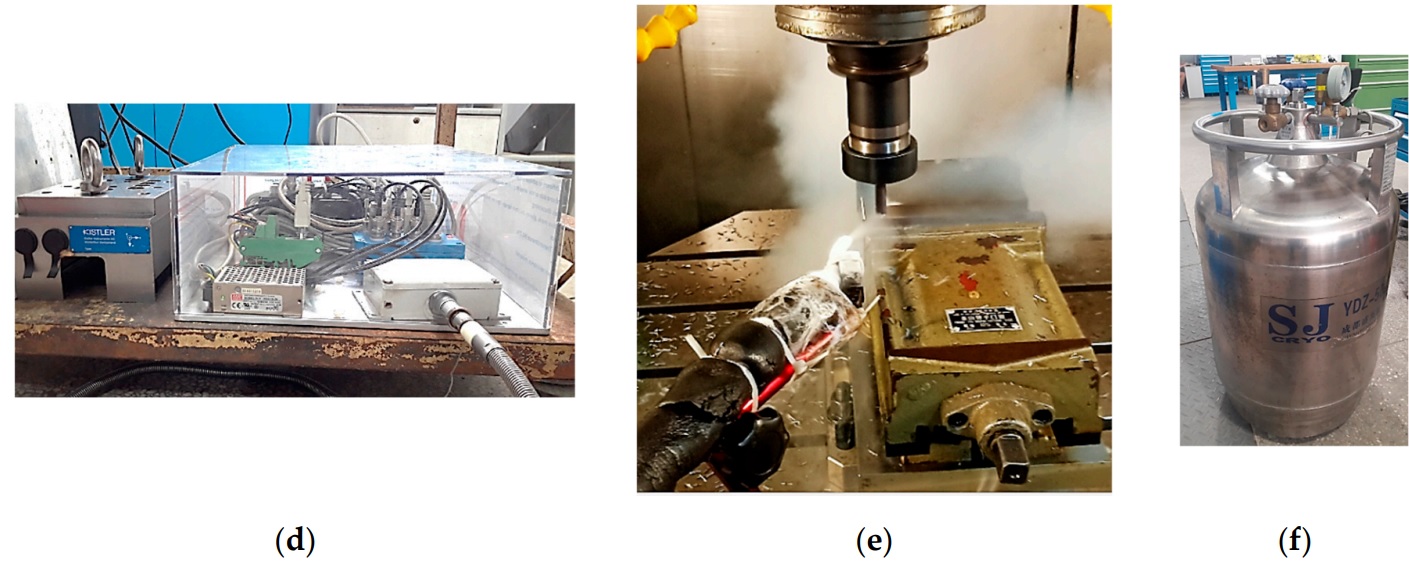
Figure 3. Experimental set-up: (a) Ti-6Al-4V work, milling cutter, and MQL duct; (b) application of CO2 snow; (c) CO2 gas storage bottle; (d) force data acquisition system; (e) application of LN2; (f) storage dewer for LN2.
Flank wear land of the used end mill's teeth was measured using a camera-fitted optical microscope ARTCAM 130-MT-WOM (Tokyo, Japan). The captured images of the flank faces were processed according to the scale to determine average width of flank wear land on each of the four cutting teeth. VB was then calculated out by taking average of the flank wears of the four teeth. The roughness of the side surface, after finishing two passes, was measured using Mahr MarSurf M 300 C (Mahr GmbH, Göttingen, Germany) a mobile roughness measuring instrument. The instrument used a 2-µm contact stylus to find the arithmetical mean height (Ra) of the milled surface according to ISO 11562 standard. The sampling length for each measurement was 4 mm, and Gaussian Profile Filter was used to get the roughness values. Four measurements were taken for each experimental run at the distances of 15, 30, 45, and 60 mm from the starting edge of the milled side surface. The Ra was then obtained by taking the average of the four measurements. Cutting forces were measured using a Kistler piezoelectric dynamometer 9265B (Kistler AG, Bern, Switzerland), utilizing a force plate 9443B. The dynamometer possessed a measuring range of 0–15 kN in the x- and y-directions and 0–30 kN in the z-direction. Process cost, PC, comprised five components. Firstly, tooling cost was quantified by multiplying VB(mm)/(0.3 mm × 600 mm3 ) by the current market price (TWD) of the milling cutter, where VB is the average flank wear of a milling cutter measured after removing 600 mm3 of the work material’s volume.
The number “0.3” in mm represents the commonly adopted end mill life criterion for the machining end mills. As the used end mills can be resold after grinding and recoating, the average resale price of the end mill was subtracted from the purchase cost of the new end mills. Clearly, a larger VB results in a higher tooling cost. Secondly, the direct electricity consumption cost, for each experimental run, was equal to the product of the commercial electricity tariff (TWD/kWh) and the specific energy (kWh/mm3) taken by the CNC machine end mill and other associated equipment (LN2/MQL) during the actual cutting process. Thirdly, the overhead cost included wage cost of one skilled operator (TWD/h) and costs of using lighting and heating, ventilation, and air conditioning (HVAC) in a small room containing the milling machine.
The latter was obtained as a product of the electricity tariff and the total wattage of the lights and the HVAC system (TWD/kWh × kW = TWD/h). The overhead cost was calculated for the actual duration of the cutting process. The cost in TWD/h was divided by the respective MRR to obtain the overhead cost in TWD/mm3. Fourthly, the equipment’s depreciation cost was calculated using the actual purchase cost of each equipment (CNC milling machine, MQL, LN2 equipment, and CO2 storage bottle), proportioned for the actual time spent removing 1 mm3 of work material’s volume. The useful life and the salvage value of each of the four equipment were taken as 10 years and zero, respectively. Machining times required for removing 600 mm3 of work material with respect to the runs employing the cutting speeds of 100 and 175 m/min were 5.65 s and 3.23 s, respectively.
The numbers of working days in a year and working hours in a day were taken as 250 and eight, respectively. The straight-line depreciation model was used for calculating the depreciation cost. Lastly, the cutting fluids’ consumption cost was obtained by multiplying the mass flow rate (kg/min) of the fluid (LN2, vegetable oil, or CO2) by its per mass unit purchase cost (TWD/kg) and dividing by the material removal rate (MRR) (mm3 /s) of the run. Fine details of the employed costing approach can be read in Reference. Consequently, the PC, for each run, was obtained in TWD/mm3 of the work material removed. It was quantified using the following equation:

Where A1 = purchase cost of a new end mill (TWD), A2 = average resale price of the end mill (TWD), SE = specific energy taken in by the machine end mill and the associated cooling/lubricating equipment (J/mm3 ), B = commercial electricity tariff (TWD/kWh), C = hourly wage of a skilled machine operator (TWD/h), D = total wattage of the lights and HVAC in kW, F = procurement cost of all the relevant equipment; G = purchase cost of the cutting fluid (TWD/kg), tm = actual machining time (5.65 s and 3.23 s), and m˙ = mass flow rate of the cutting fluid. The numbers 3.6e6 and 7.2e6 represent the factors for converting kWh to Joules and years to seconds, respectively.
Considering the ever-present inflation, it is more meaningful to present the process cost in terms of a 100-scale comparative cost structure. In such an arrangement, the costliest result is presented as 100, the most economical as 0, and all others as proportionately determined numbers lying between 0 and 100.
The consumption of specific cutting energy for each experimental run was determined as follows:
I. Three current clamp meters,
Hantek CC 65, were applied to the three phases of the AC supply of the CNC machine tool to measure the electric power drawn during the machining process (Ptotal). The input voltage (V) and the power factor (PF) were measured as 220 V and 0.85, respectively. The total power was calculated using the following formula:
II. Where I1, I2, and I3 represent the current,
in amperes, as measured by the three clamp meters. The non-cutting power (Pnon-cut) was determined by rotating and linearly moving the end mill in the direction of feed at the given combination of rotational speed and feed speed. The end mill was moved linearly at the feed speeds of 1592 and 2785 mm/min for the runs employing the cutting speeds of 100 and 175 m/min, respectively.
IV. The Pcut (J/sec)
for each run was divided by the relevant material removal rate (MRR) to get the specific cutting energy, SCE (J/mm3 ). The MRR values for the runs conducted at the cutting speeds of 100 and 175 m/min were 106.2 and 185.8 mm3 /s, respectively.Analysis of variance (ANOVA) was also performed on the experimental data in order to have a better understanding of the individual effects of the controlled predictors, as well as their interactive effects on the measured responses. ANOVA not only helps to isolate the effect of each individual predictor; it also reveals the strength of the effect.
2.4. Fixed Parameters
The values of feed per tooth, axial depth of cut, and radial depth of cut were fixed to 0.1 mm/z, 8 mm, and 0.5 mm, respectively, for all the experimental runs. Each end mill was held in a collet at a distance of 28 mm from the cutting end. All the runs were performed by carrying out the milling cuts twice in a straight line. The supply of the relevant cutting fluid (LN2/CO2/MQL) was started 20 s prior to first engagement of the end mill with the work and was not stopped during the transition between the two passes. The supply was shut down immediately after completion of the second pass.
3. Experimental Results
The section provides details on the experimental results regarding end mill wear, surface roughness, specific cutting energy consumption, cutting forces, and process cost.
3.1. End mill Wear
Figure 4 presents the experimental results of the 24 runs regarding VB obtained after removing 600 mm3 of the work material. The results are grouped into three plots based on the type of cutting fluid used. A striking result is evident that, in general, micro-lubrication yielded lower levels of end mill wear as compared to the two cryogenic cooling options. Of the two cryogenic cooling options, it is evident that the evaporation-based coolant (LN2) fared better. Furthermore, the smallest VB (0.04 mm) of all the runs was also yielded by LN2. Furthermore, it is clearly observable that down-milling generated remarkably smaller wear than up-milling when the applied cutting fluid was LN2.With regard to end mill's helix angle, the larger angle (42◦) performed better than the smaller angle (30◦) with respect to end mill wear. Unfortunately, the dependence of helix angle on any other predictor with respect to VB was not clear from the plots. Although a higher helix angle favored higher material removal rates (realized by high levels of speeds and feeds), the resulting smaller flute spacing caused a problem in chip evacuation at these rates, especially for a sticky material such as Ti-6Al-4V. This is why no interactive effect between helix angle and cutting fluid was visible on end mill wear. Down-milling (also known as climb milling) generally yielded lower end mill wear than up-milling (conventional milling).
This effect was especially prominent in the milling conducted under LN2. The gradual decrease in chip thickness, as the cut proceeded in down-milling, reaching zero at the end, prevented the cutting edge and adjacent flank face from rubbing and burnishing against the work surface. The lower levels of flank wear observed in down-milling were attributed to this mode of frottage-free cutting. With respect to cutting speed, its higher level was generally found to yield higher levels of end mill wear, although the effect was quite insignificant. A high level of cutting speed instigated or accelerated the temperature-dependent modes of end mill damage because of an enhancement in the rate of heat generation and led to intensification of end mill wear. As a result, the cutting edge and the adjacent faces incurred higher magnitudes of wear per unit volume of work material removed.
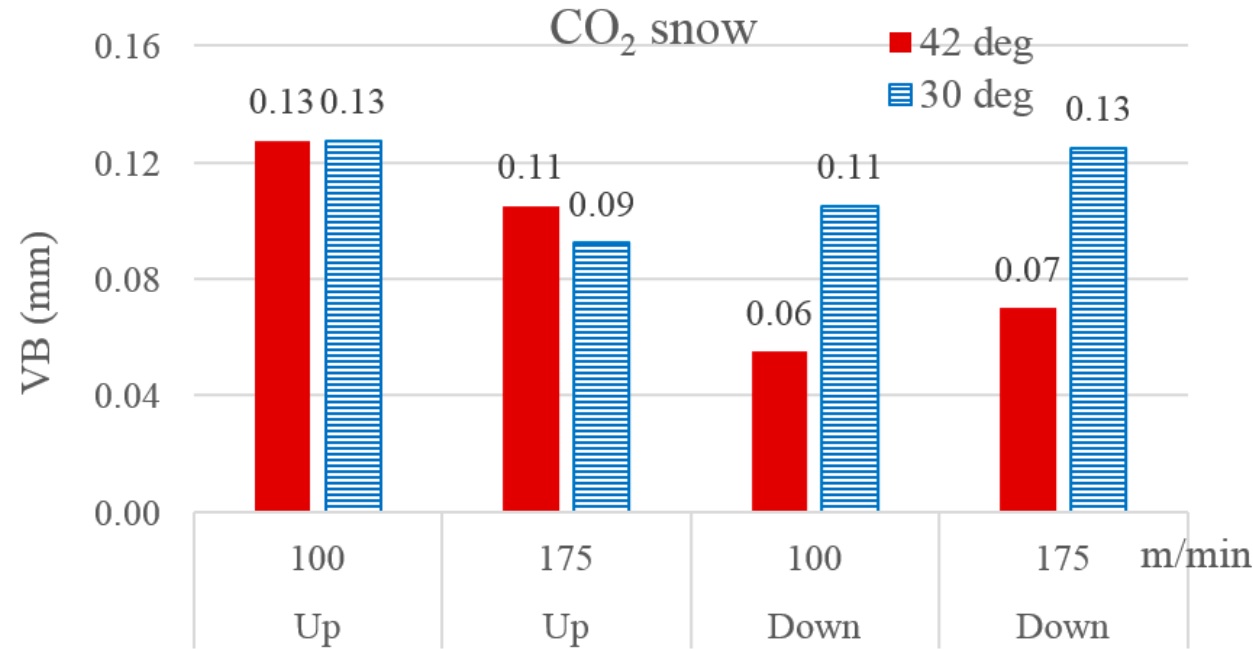
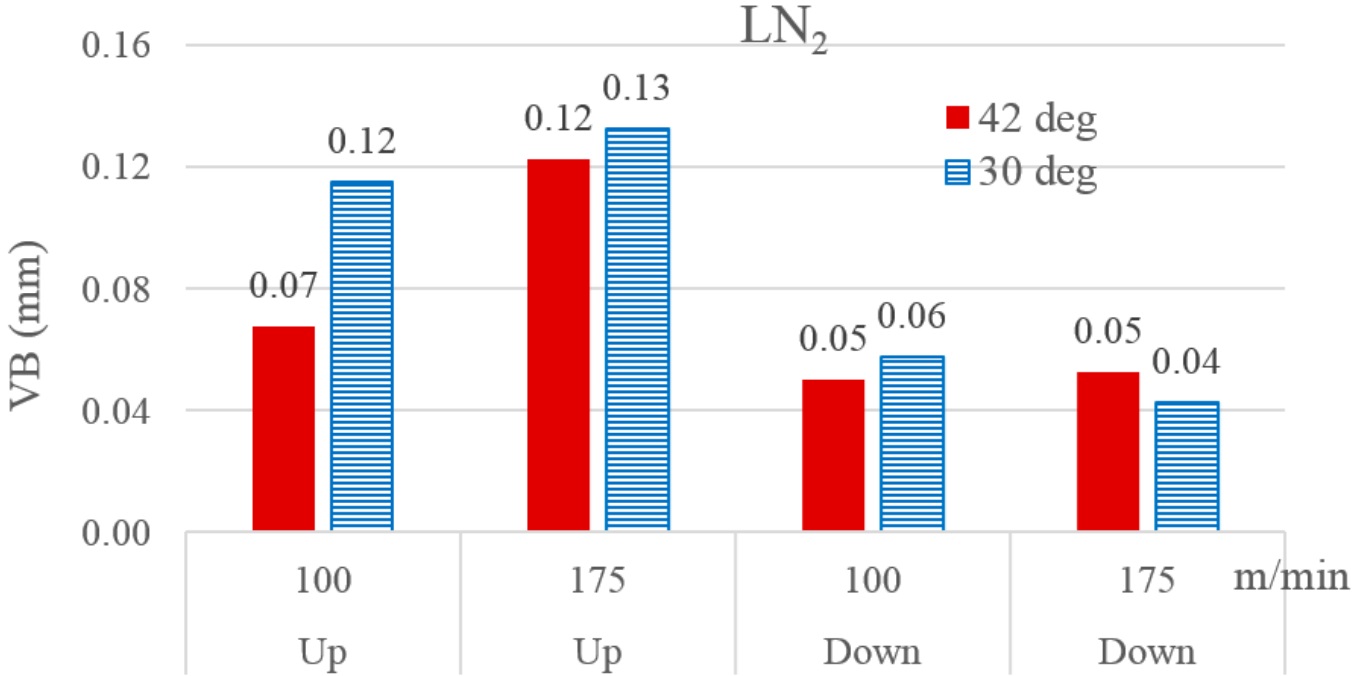
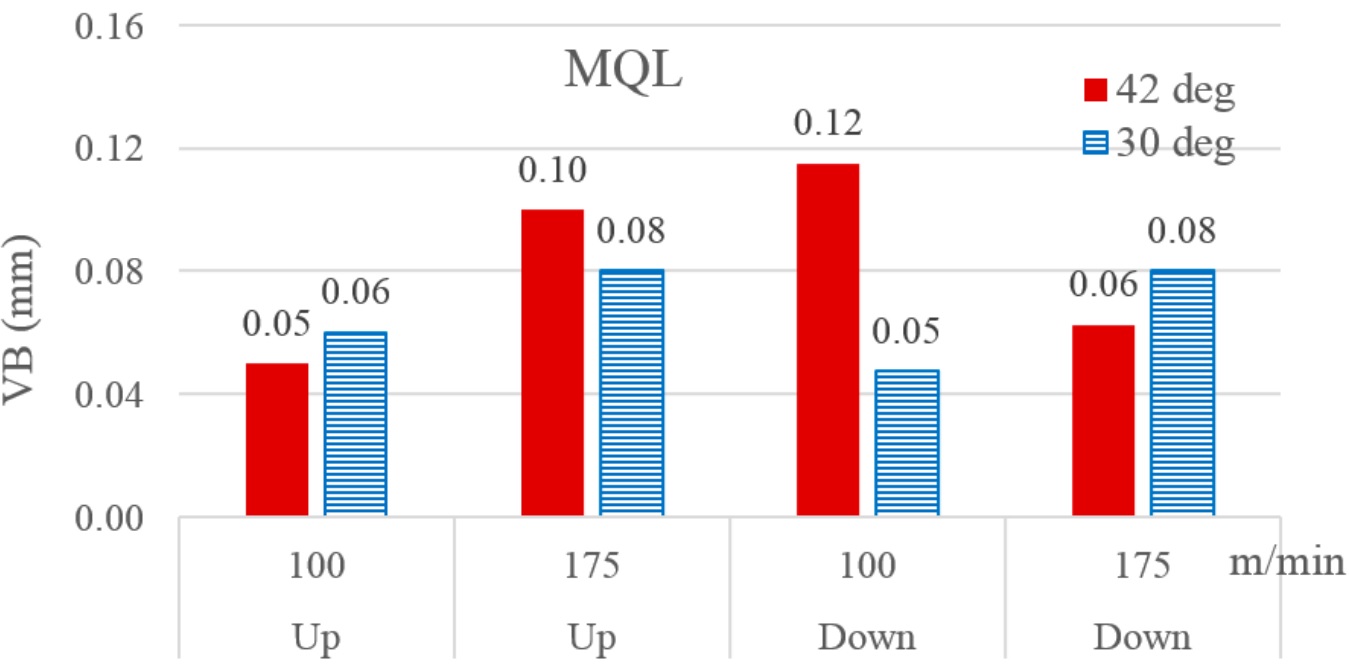
Figure 4. Bar graphs present the measurements of the average width of flank wear land (VB) for the 24 experimental runs.
ANOVA was performed on the data shown in Figure 4. The analysis revealed milling orientation as the most influential factor regarding VB, followed by the choice of cutting fluid. The interaction between milling orientation and cutting fluid stood third in terms of statistical significance, followed by the solitary effects of cutting speed and end mill's helix angle. The strong interactive effect between milling orientation and cutting fluid on end mill wear is evident from the three plots of Figure 4 in the manifestation that down-milling yielded vastly lower end mill wear than up-milling only when the applied cutting fluid was liquid nitrogen. Shokrani et al. claimed that the coated carbide end mill used for cryogenic (LN2) milling of Ti-6Al-4V, operated at 200 m/min cutting speed and 0.03 mm/tooth feed rate, showed the minimum level of flank wear. The current work, on the other hand, found MQL to be a better cutting fluid than the cryogenic fluids with respect to end mill damage.
The finding was based on milling performed at a slightly lower cutting speed but an enormously larger feed rate. Figure 5 presents the microscopic images of the selected used end mills. The six end mills were selected so as to ensure a maximum level of diversity regarding the predictor variables. The microscopic visual analysis revealed occurrence of progressive mechanical wear and adhesion of work material as the major modes of end mill damage, while chipping of cutting edge was also observed in a few end mills. As can be seen from Figure 5a,d, all the end mills used in the runs involving up-milling and either of the two cryogenic fluids experienced thick adhesion of work material at their cutting edges. The adhered material, in all these runs, was in the form of minute flakes. The observation tallies with the findings of the previous works. It was reported that adhesion wear was the main end mill damage mechanism in LN2-assisted machining of Ti-6Al-4V. In addition, up-milling was also reported to instigate more severe end mill wear in the peripheral milling of a hardened steel.
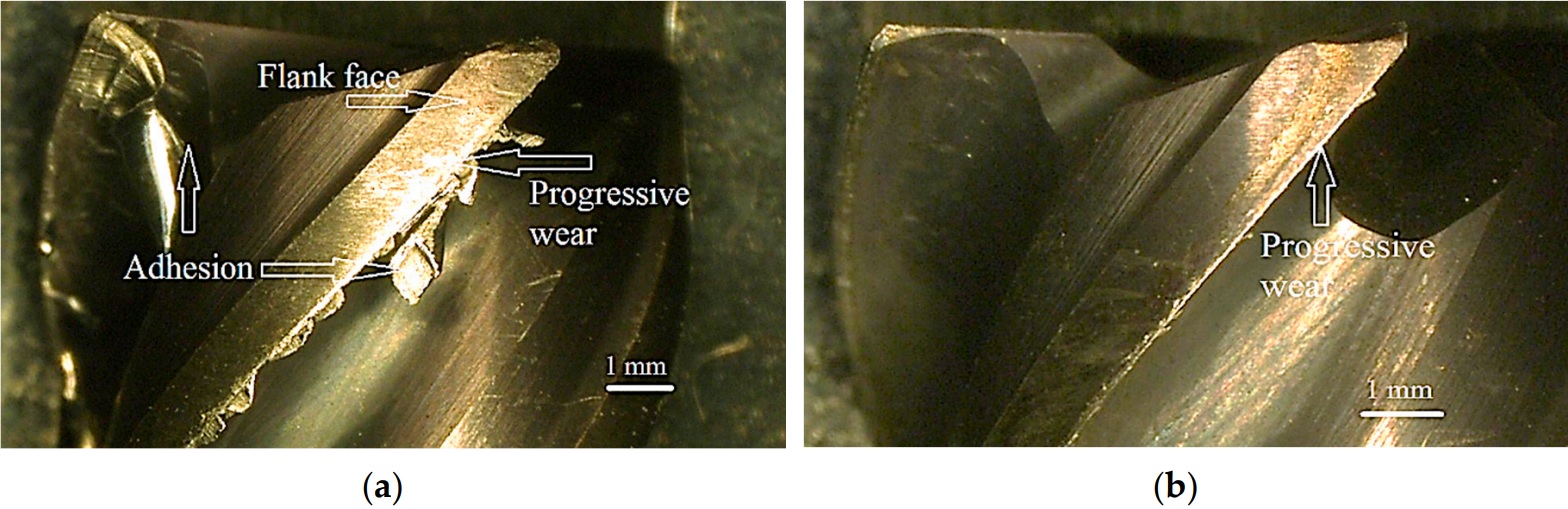
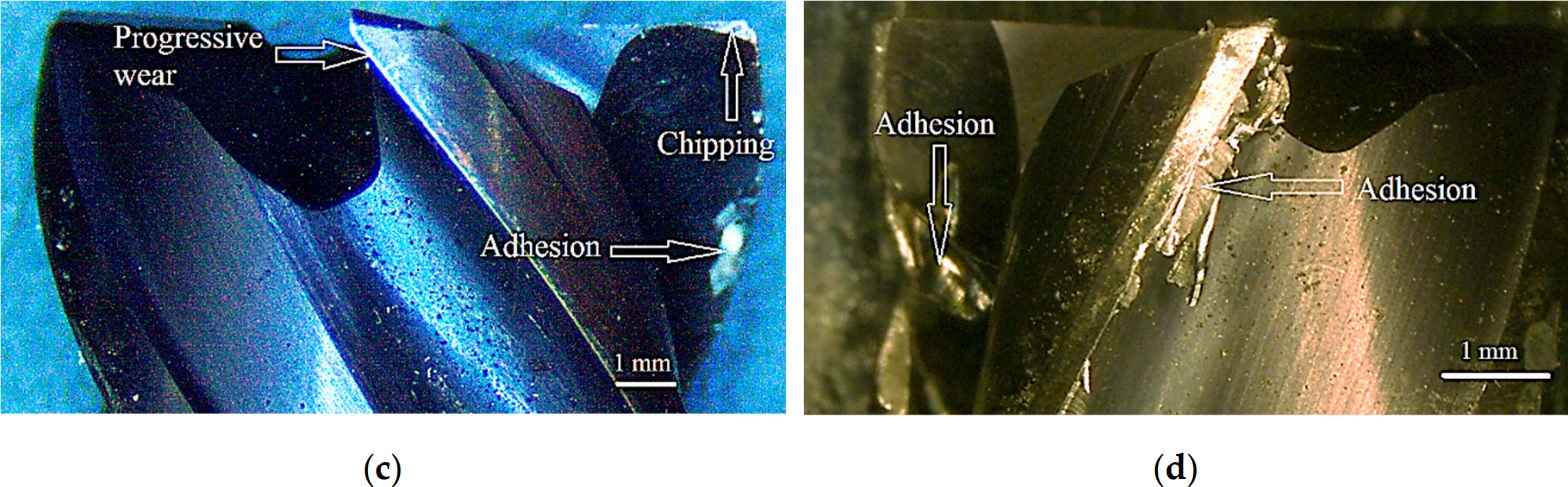
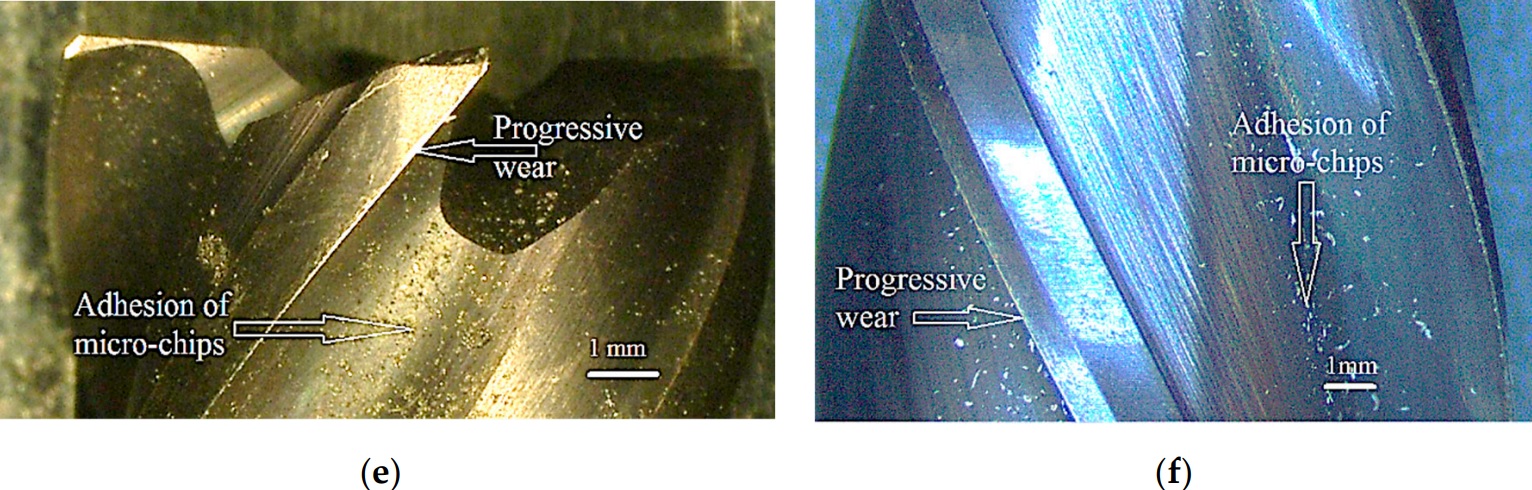
Figure 5. Micrographs showing the modes of damage incurred by the teeth of the end mills used in the following runs: (a) CO2 , 42◦ , up, 175 m/min; (b) CO2 , 42◦ , down, 175 m/min; (c) LN2 , 42◦ , down, 175 m/min; (d) LN2 , 30◦ , up, 100 m/min; (e) MQL, 42◦ , up, 100 m/min; (f) MQL, 30◦ , down, 100 m/min.
As a cutting edge, in up-milling, is known to enter the work with a minimum thickness and exit with a maximum, it sees a tendency of the removed chip to remain adhered to it under the influence of high temperature. Rapid cooling offered by the incoming cryogenic fluid strengthens the attachment of the chip, or part of it, to the edge and the adjacent faces. On the other hand, as is visible from Figure 5e,f, all the runs involving micro-lubrication yielded adhesion of micro-chips on the end mill surface located inside of the flutes and away from the cutting edges. Micro-sized particles of the removed material were vulnerable to be caught up by the oily surface of the flutes and remained clung even against the high centrifugal forces of the rotating end mill. Progressive mechanical wear (abrasion), in the form of a bright line existing close to the cutting edge, is evident in all the six images.
Not much information can be deduced from the images regarding dependence of its severity on the various predictors controlled in the experiments. It was reported that abrasion was not the wear-determining mechanism in cryogenic or wet milling of Ti-6Al-4V using coated and uncoated end mills irrespective of the coolant’s choice. Chipping was observed in no more than three end mills. One of them is shown in Figure 5c. All of them were involved in milling at the high level of cutting speed (175 m/min). Furthermore, the chipping, in all three instances, occurred at the corner of the relevant tooth. In a previous work, the application of CO2 was reported to slow down the chipping process. Thermal cracking of the cutting teeth, normally caused by rapid heating and cooling cycles of cryogenic milling, was not evident, probably, due to a considerably short length of cut employed in the experimental runs.
3.2. Work Surface Roughness
Figure 6 presents the measurements of Ra for the 24 runs, categorized by the type of cutting fluid used. The error bars present the standard deviation of the measured data for each experimental run. Quite a few conclusions can be drawn directly from the plots. As far as the type of cutting fluid is concerned, it is evident that micro-lubrication yielded better surface finish than the cryogenic fluids. Furthermore, down-milling fared better than up-milling. The effects of other two predictors were not clear from the graphs. ANOVA was performed on the Ra data to get further insights. The analysis revealed milling orientation to be the most influential predictor, followed by cutting speed and cutting fluid. The effect of end mill's helix angle was found to be statistically insignificant. With regard to milling of a hardened end tool steel, the end mills with a 45◦ helix angle were reported to yield significantly lower surface roughness than the 30◦ end mills. Up-milling is clearly not the better choice for the sake of good surface finish. As described in the previous sub-section, the cutting teeth, while following the up-milling approach, remove the work material with a lot of work material adhesion. The adhesion is believed to compromise the true geometry and sharpness of the cutting edge, thus leading to generation of a rougher surface. The superiority of down-milling regarding work surface finish was also reported for the milling of a tool steel.It is quite surprising to see micro-lubrication yielding better surface finish than the two cryogenic coolants. As far as a continuous machining process is concerned, many papers reported strikingly improved work surface finish caused by the use of a cryogenic coolant. On the contrary, cryogenic cooling, in this study, yielded a poor work surface quality regarding the milling process. A plausible explanation for this observation is that milling is an interrupted machining process in which cutting teeth periodically engage and disengage with the work. Each tooth engagement causes an increase in temperature of the tooth, as well as the newly generated work surface. The surface tends to expand due to the resulting increase in temperature but immediately gets impinged upon with the flow of a cryogenic fluid as the end mill clears the area following its feed. The impact of the super-cool fluid immediately lowers its temperature, pushing the surface into the contraction mode. Such an intense thermal effect instigated upon the newly generated surface, sending it into abrupt modes of expansion and contraction, causes deterioration of the surface quality. A 25% reduction in work surface roughness was reported when graphene-dispersed vegetable-oil-based micro-lubrication was applied in the milling of Ti-6Al-4V. An increase in cutting speed was found to reduce the surface roughness when the milling orientation was down-milling. Its influence on Ra with up-milling is not clear. An increase in cutting speed was also reported to reduce the work surface roughness in milling of a hardened steel (AISI D2).
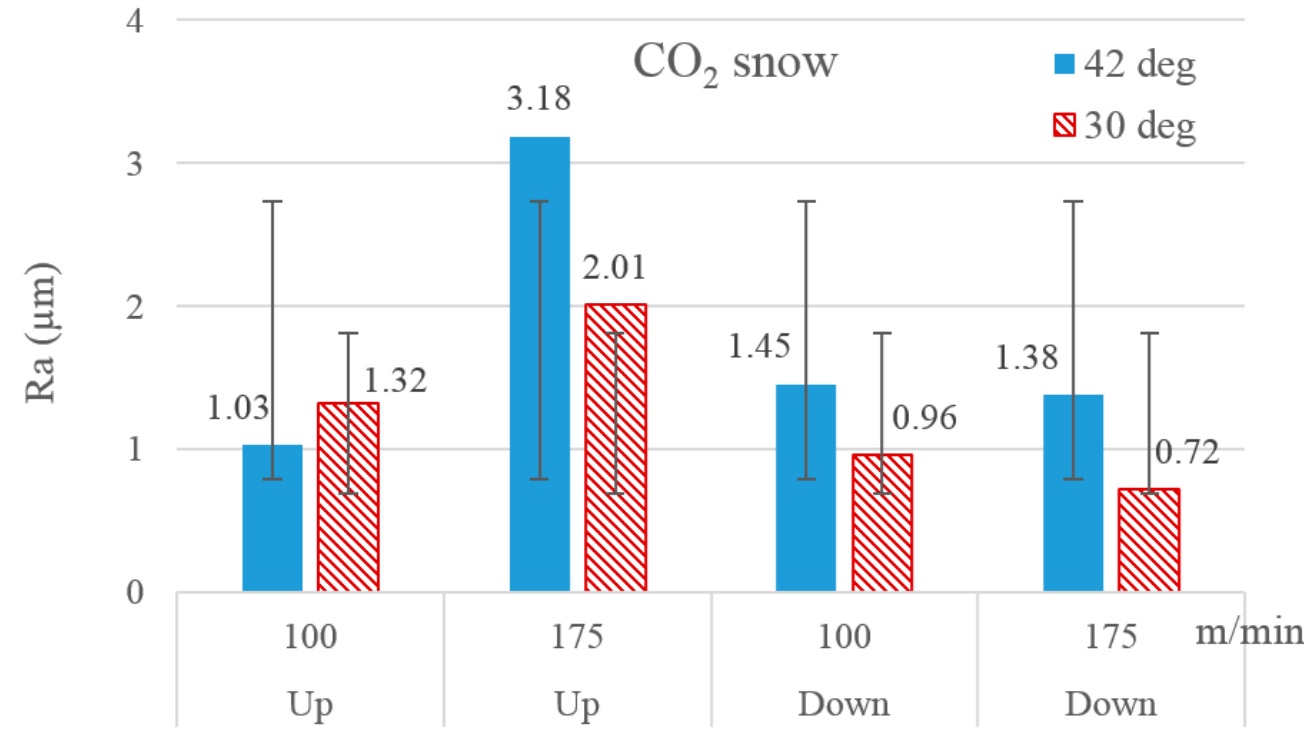
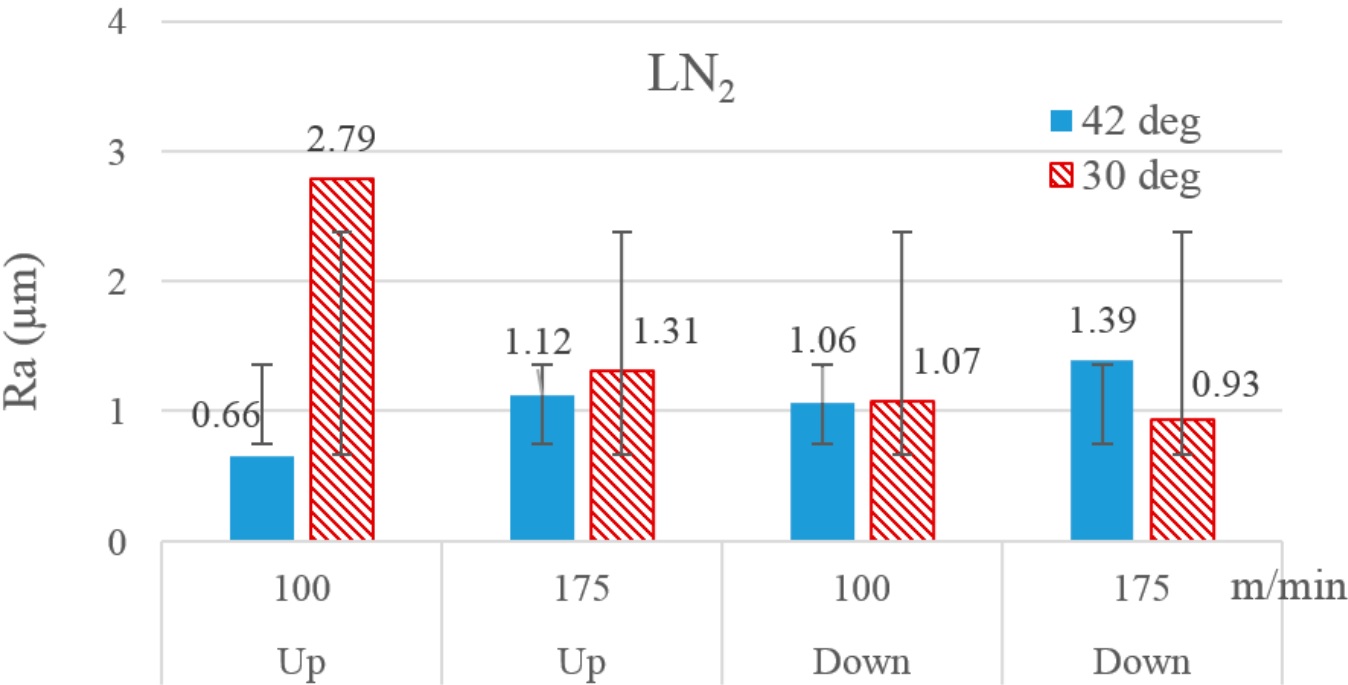
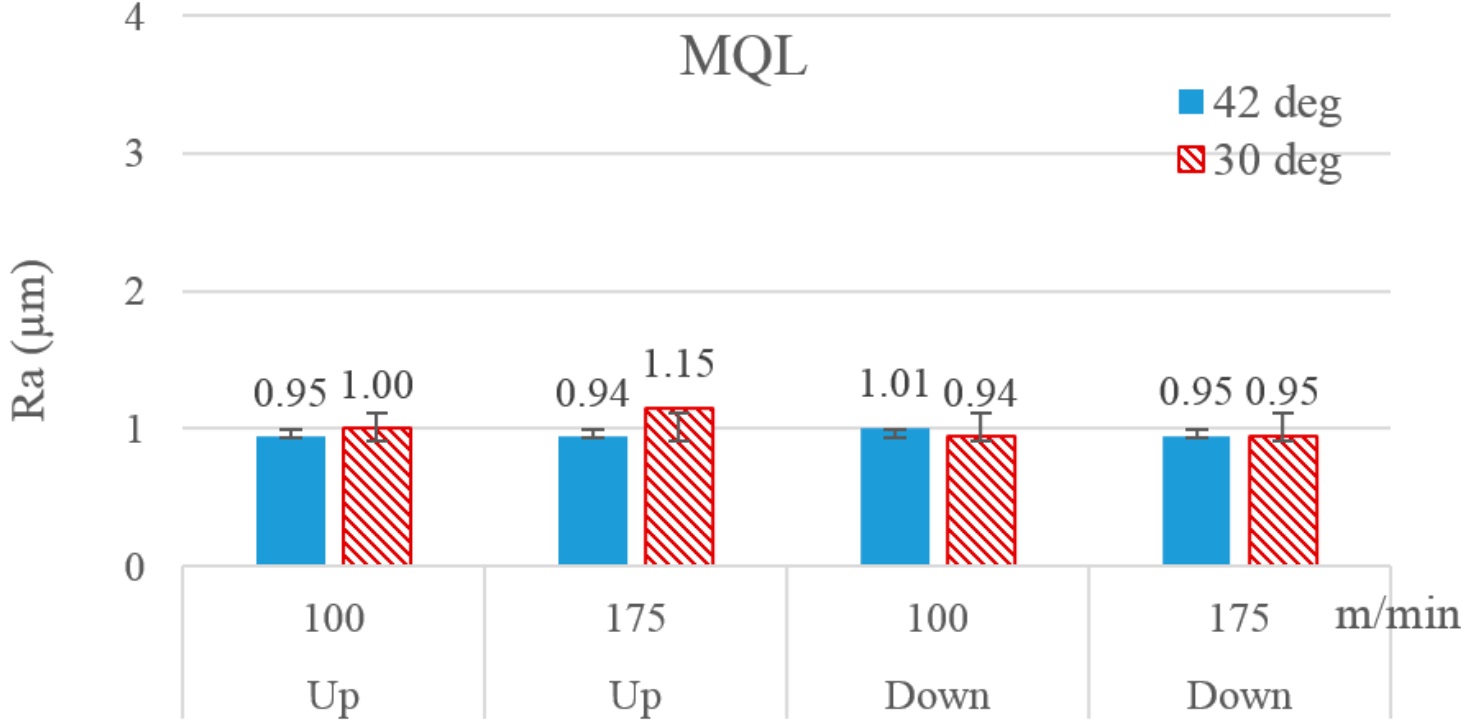
Figure 6. Bar graphs present the experimental results regarding arithmetic average surface roughness for the 24 runs.
Figure 7 presents the textures of the four milled surfaces obtained after completion of the selected experimental runs. Clearly, the surfaces produced by up-milling (Figure 7a,b) were marred by the adhesion of micro-chips. The adhesion caused serious deterioration of the work surface. Figure 7a presents the roughest of all the surfaces generated in the 24 runs. All the runs employing the combination of CO2 snow and up-milling yielded severe adhesion of micro-chips on the milled surfaces.
Figure 7c,d do not show any sign of adhesion, as both of them were associated with the runs employing the down-milling orientation. It is to be noted that the pattern of vertical lines on the texture was the same in all the images. This is because all the runs were carried out at a fixed value of feed per tooth. Figure 7b shows a white horizontal line running through the generated surface. The line was generated by the chipped portions of the four flutes of the end mill, which might have encountered a hard phase during the first pass of the run.
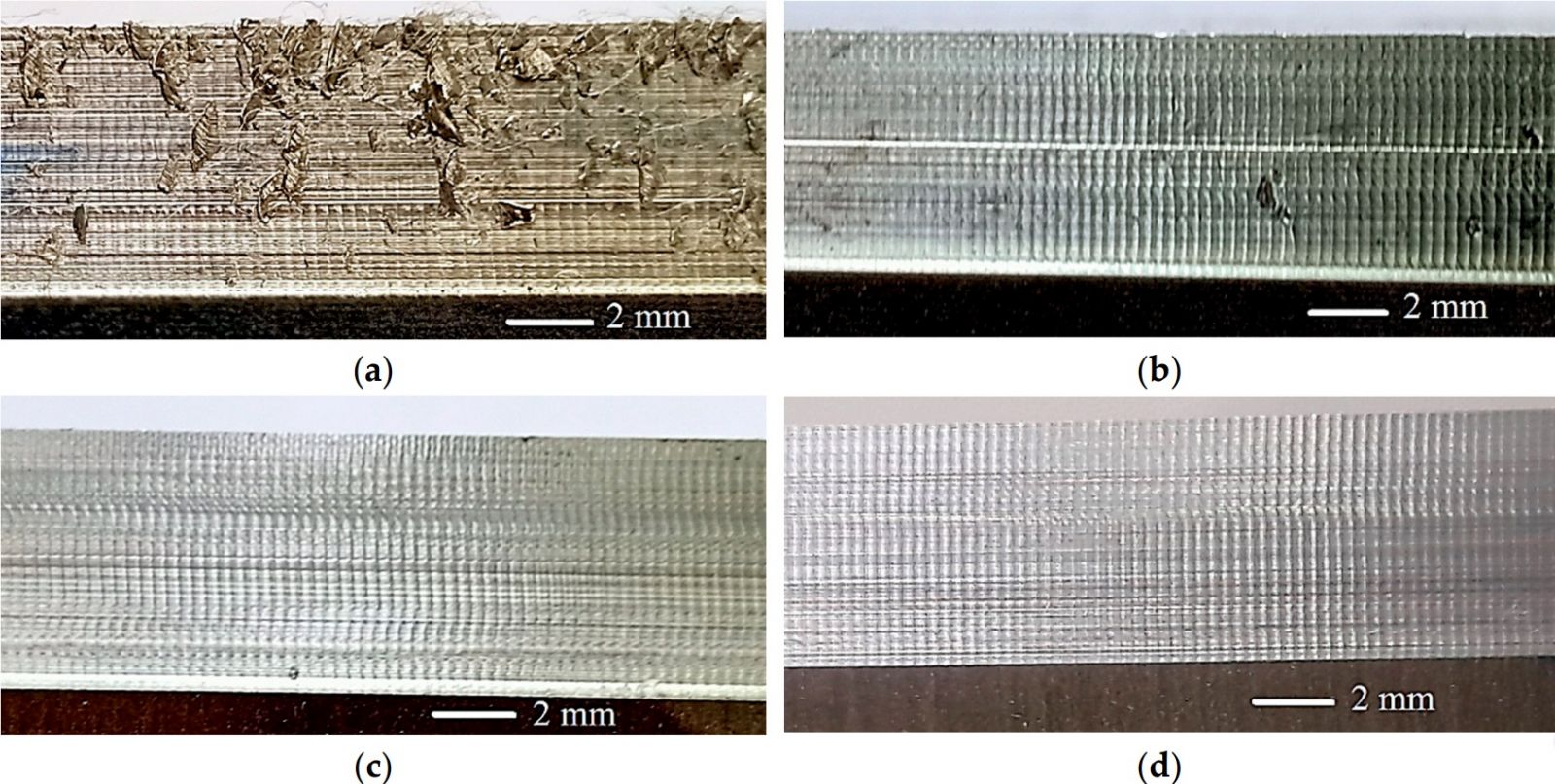
Figure 7. Work surface texture obtained after completion of the following runs: (a) CO2, 42°, up, 175 m/min; (b) LN2, 30°, up, 175 m/min; (c) LN2, 42°, down, 100 m/min; (d) MQL, 30°, down, 100 m/min.
3.3. Specific Cutting Energy and Machining Forces
Table 2 presents the data regarding measurement of total electric power and cutting and noncutting powers and evaluation of the SCEs for the 24 experiments. The procedure for measuring the electric powers was already detailed in sub-Section 2.3. Figure 8 presents the experimental results of the 24 runs regarding consumption of specific cutting energy. Two conclusions can be drawn directly from the plots. Firstly, the end mills with a 42° helix angle consumed less energy than those with a 30° helix angle. Secondly, the higher level of cutting speed caused a decline in energy consumption. ANOVA applied to the SCE data revealed extreme statistical influences of cutting speed and end mill's helix angle. The effect of cutting fluid was found to be marginally significant, and that of milling orientation was found to be insignificant.The resulting diminution in specific cutting energy caused by cutting speed was attributed to an increase in material removal rate to a larger extent and an increase in cutting power consumption to a smaller extent. As SCE is the ratio of cutting power to material removal rate, an increase in cutting speed resulted in lessening of its magnitude. The cutting power (and energy) is required at the cutting edge to plastically deform the work material in shear and convert it into a chip. The formation of the chip is realized along with the generation of process heat. A higher cutting speed results in a higher heat generation rate. The process heat was reported to reduce the flow stress of the work material causing reduction in the cutting energy required to remove the same volume of material. This phenomenon is termed thermal softening, and it was the reason for a lesser than expected increase in cutting power with increase in cutting speed. Hence, the specific cutting energy was found to decline with a step up in cutting speed. An increase in cutting speed, in side- and end-milling of hardened tool steel, was also reported to significantly reduce the specific energy consumption.
Table 2. Measurements and calculations regarding total power consumed by the machine tool, non-cutting power, cutting power, and specific cutting energy. MRR—material removal rate.
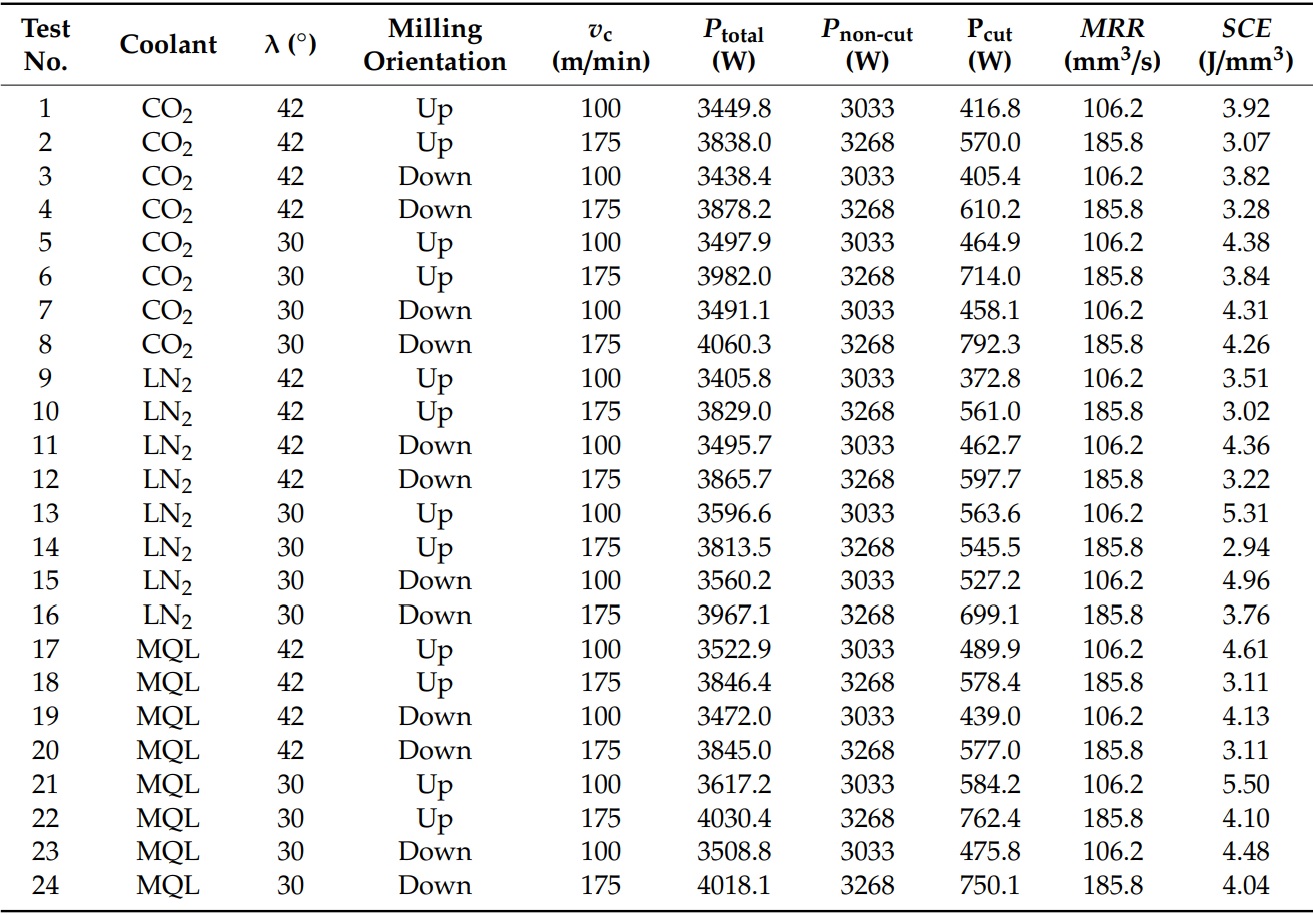
A end mill with a larger helix angle cuts the work material with a larger ratio of the axial force component to the radial. The radial component of the machining force is responsible for causing vibrations in the end mill and stirring instability in the milling process. Such a phenomenon becomes more prominent in machining a difficult-to-cut material, such as Ti-6Al-4V. Stronger vibrations and higher instability means a higher consumption of energy for removing the same volume of material. As such, a larger helix angle causes a reduction in the proportion of the radial force component, thus stabilizing the milling process and causing a diminution in cutting energy.
Among the three cutting fluids, the throttling-based cryogenic coolant (CO2 snow) produced the best results regarding specific cutting energy, although not by a momentous difference, followed by the evaporative cryogenic coolant (LN2). Both the cryogenic coolants reduced cutting energy consumption by curbing the end mill wear progress. The super-cool fluid put a check on the temperature-dependent end mill wear modes, which helped to maintain the cutting-edge geometry for a longer period of time. Consequently, the maintained sharpness of the cutting edge needed a smaller cutting force and lesser energy to cut the given volume of work material. In another work, cryogenic milling of Ti-6Al-4V was also found to be hugely energy conservative in comparison with wet milling due to avoidance of additional power drawn in by the coolant pump.
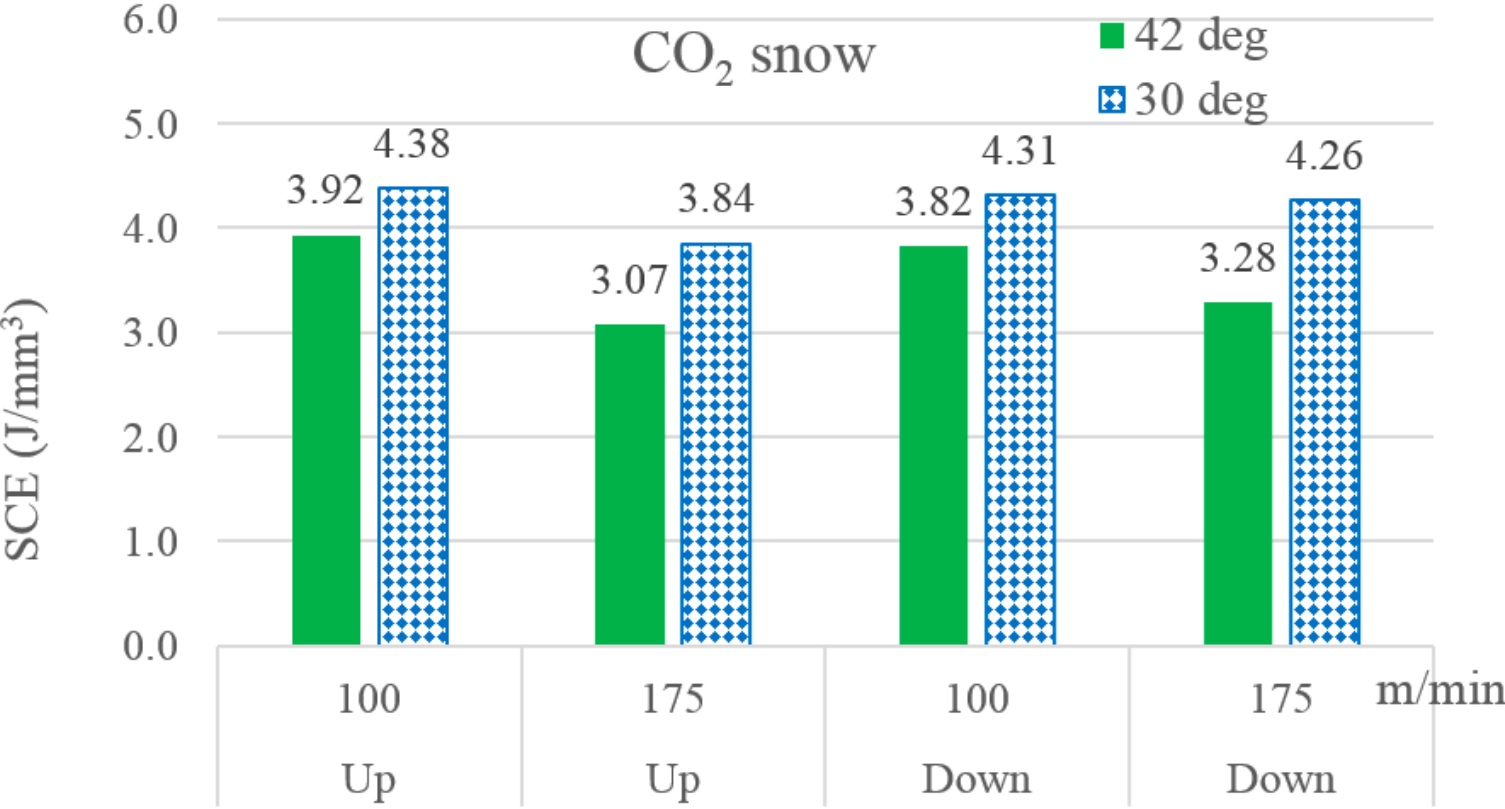
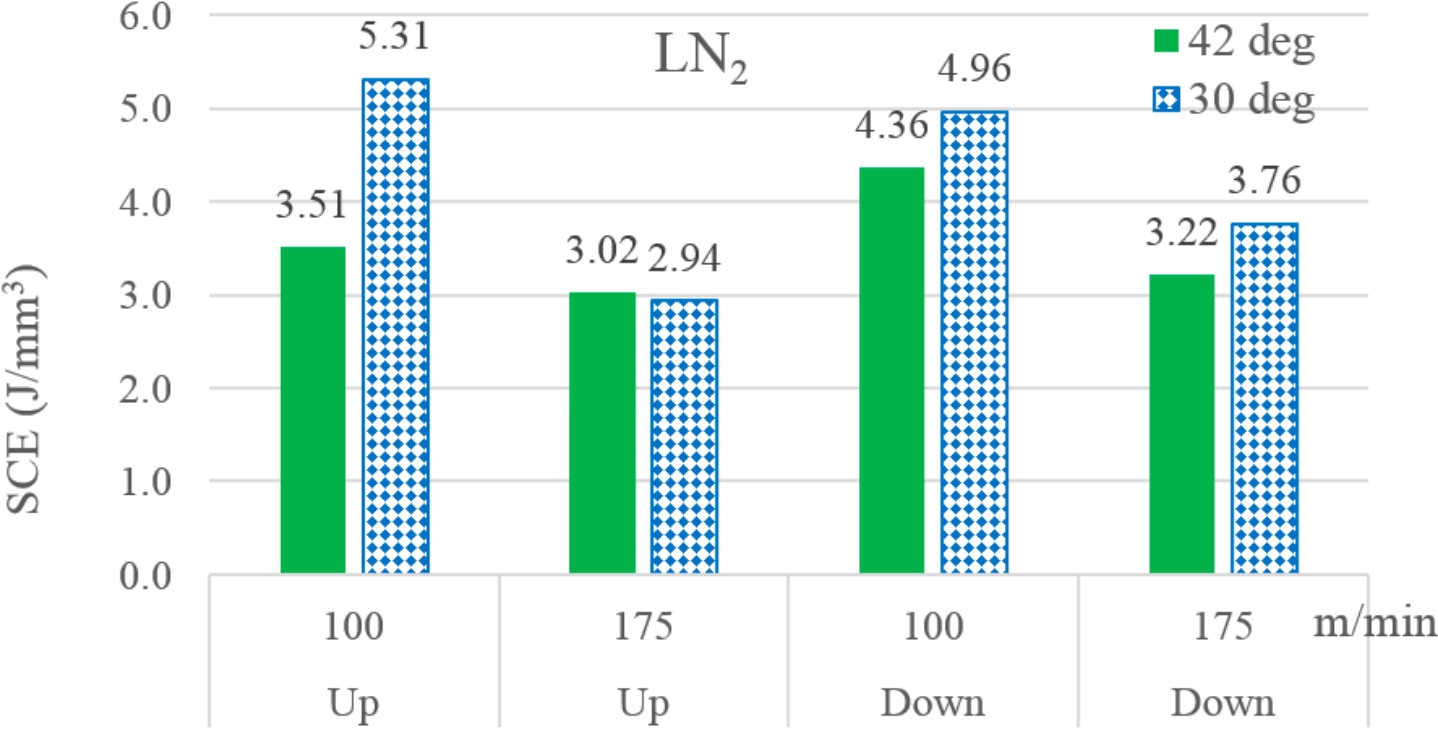
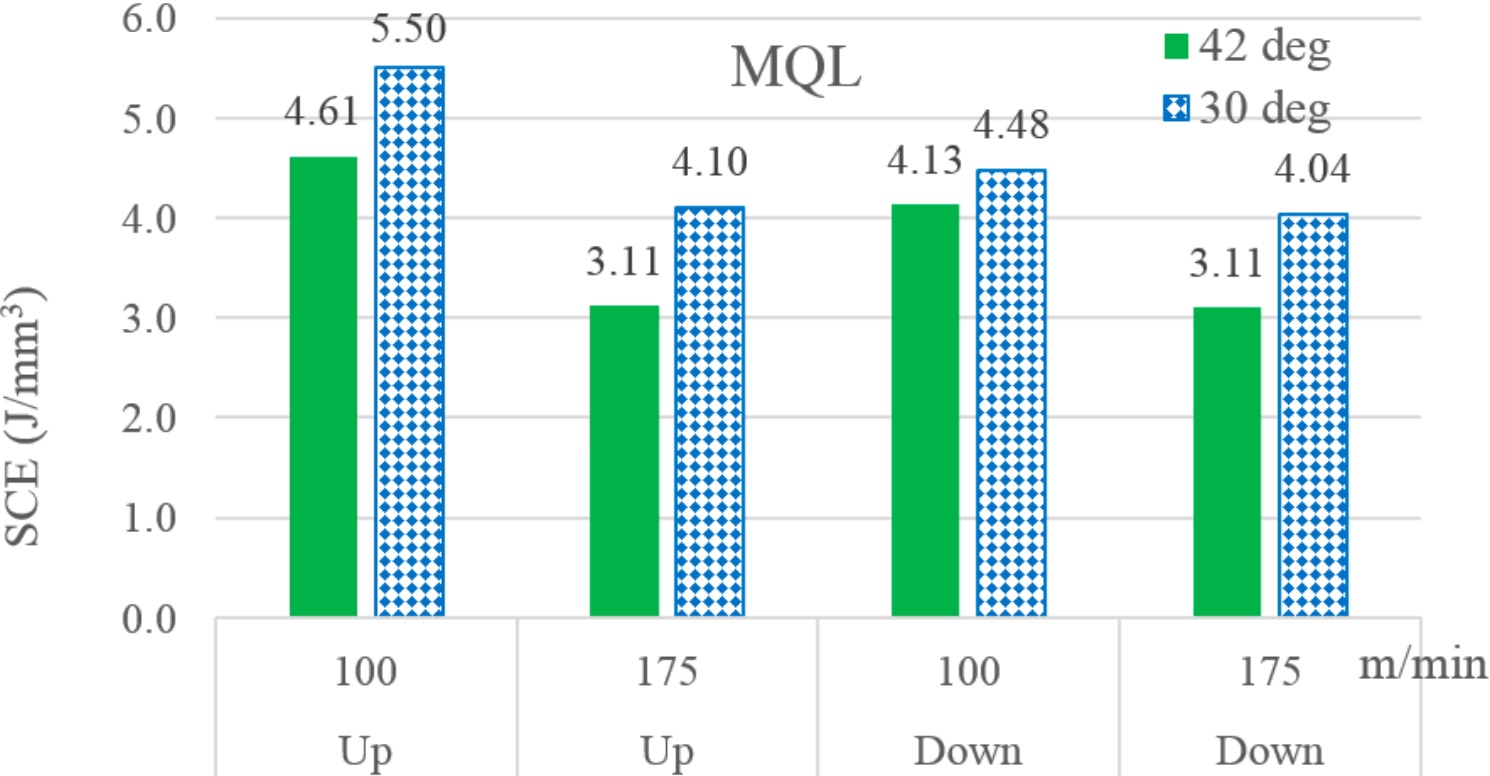
Figure 8. Bar graphs present the experimental results regarding the SCE for the 24 runs.
From the perspective of machining sustainability, it is often urged to include the relevant energies required to liquefy, compress, and deliver per unit mass of the cutting fluids in the SCE calculations. The authors would like to present some quantifications in this regard. For this study, the measured volumetric flow rate of LN2 as a coolant was 0.5 L/min. Furthermore, the density of nitrogen in the liquid state was equal to 804 kg/m3 at a temperature of −195.8 ◦C. European Industrial Gases Association (EIGA) reported that separating nitrogen at 0.1013 MPa and liquefying it from a temperature of 285 K requires consumption of electrical energy of about 549 kWh per ton of the gas. Converting this figure into the power requirement against the mass flow rate of 0.402 kg/min gives 13.24 kW. Moreover, the storage dewer used in the experimental work consumes additional 50 watts of power to pump the LN2 at the given flow rate. It was reported that capture and compression of CO2 gas consumes electrical energy in the range of 250–300 kWh/ton of the gas. For the average value of the reported range, 275 Wh/kg, and the mass flow rate of 0.5 kg/min, the average electric power required to supply and maintain the given flow rate of the CO2 gas is 8.25 kW. Lastly, the average power required to drive the employed MQL system at the air pressure, oil mixing rate, and air flow rate of 0.6 MPa, 30 mL/h, and 0.4 L/s, respectively, is 418 Watts. The details regarding the calculations can be seen in Reference. By adding the above calculated values of power requirements, the SCE values ranged from 57.6 to 82 J/mm3 , 74.5 to 131 J/mm3 , and 5.2 to 8.3 J/mm3 , respectively, for CO2 snow, LN2, and micro-lubrication. Clearly, the modified values of SCE rendered the comparisons among the three cutting fluids trivial, with LN2 topping the list of the tested fluids by an unprecedented margin.
Figure 9 presents the experimental data regarding the three components of the machining forces obtained from the 24 experimental runs. As described before, Fx and Fz are aligned with the feed direction and the end mill's axis, respectively, while Fy is perpendicular to the side surface of the work. Thus, it can be said that the axial component of the milling force is Fz, while the radial component is the resultant of the other two.
A few inferences can be drawn directly from the three plots. Firstly, the end mill with the larger helix angle experienced lower magnitudes of all the force components. Secondly, Fx rose unusually for all the three cutting fluids when a 30◦ helix end mill was used to mill at the high level of cutting speed using the down-milling orientation. Thirdly, with respect to the choice of cutting fluid, LN2 yielded the lowest magnitudes of the milling force components, followed by CO2 snow. ANOVA was applied to get in-depth results. For all the three force components, end mill's helix angle was found to be a highly and the most influential predictor. The effects of milling orientation and cutting fluid were found to be marginally significant, whereas that of cutting speed was found to be insignificant. Furthermore, an interactive effect between cutting fluid and milling orientation was found to be significant on the radial components only.
A end mill with a large helix angle is ideal for dynamic stability in milling, machining with small depths of cut, and gaining a good work surface quality. On the other hand, a end mill with a small helix angle is good for rough machining and removing work material at high removal rates. Dynamic stability of milling is reflected by small magnitudes of machining forces. The results in this study show that a 42◦ helix angle yielded better dynamic stability than a 30◦ angle, as reflected by the results regarding the milling force components. The observed effectiveness of LN2, in curbing machining forces, can be attributed to its more effective heat dissipation capability. An extremely low operational temperature of the fluid is believed to equip it with such a capability. Better heat dissipation mechanism helps keeping a check on end mill wear progress, which, in turn, helps maintaining cutting edge’s geometry and suppressing the machining forces. In other works, hybrid cryogenic cooling/lubrication was reported to yield the lowest machining forces compared to both emulsion and cryogenic conditions in machining of titanium alloys. The effect of milling orientation was neither very significant nor clear. Down-milling yields lower magnitudes of force components for CO2 snow and MQL and higher magnitudes for the third fluid. Moreover, up-milling was found to be the better orientation to be used at higher cutting speeds. Li et al. reported an 18% reduction in milling forces when graphene-dispersed vegetable-oil-based MQL was applied in the milling of Ti-6Al-4V.
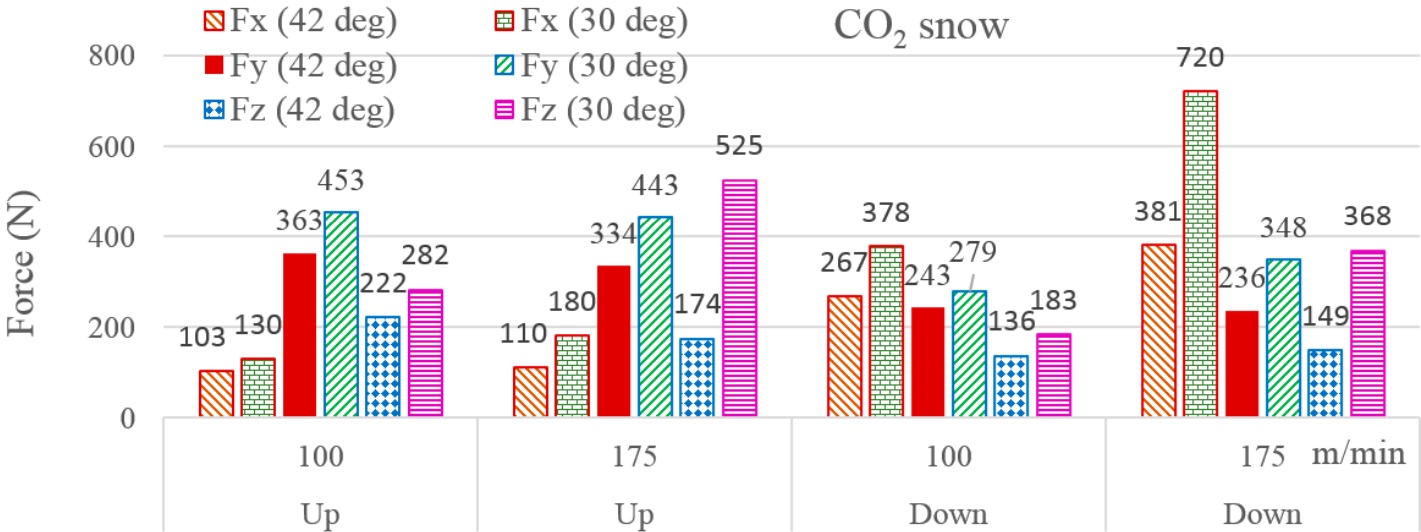
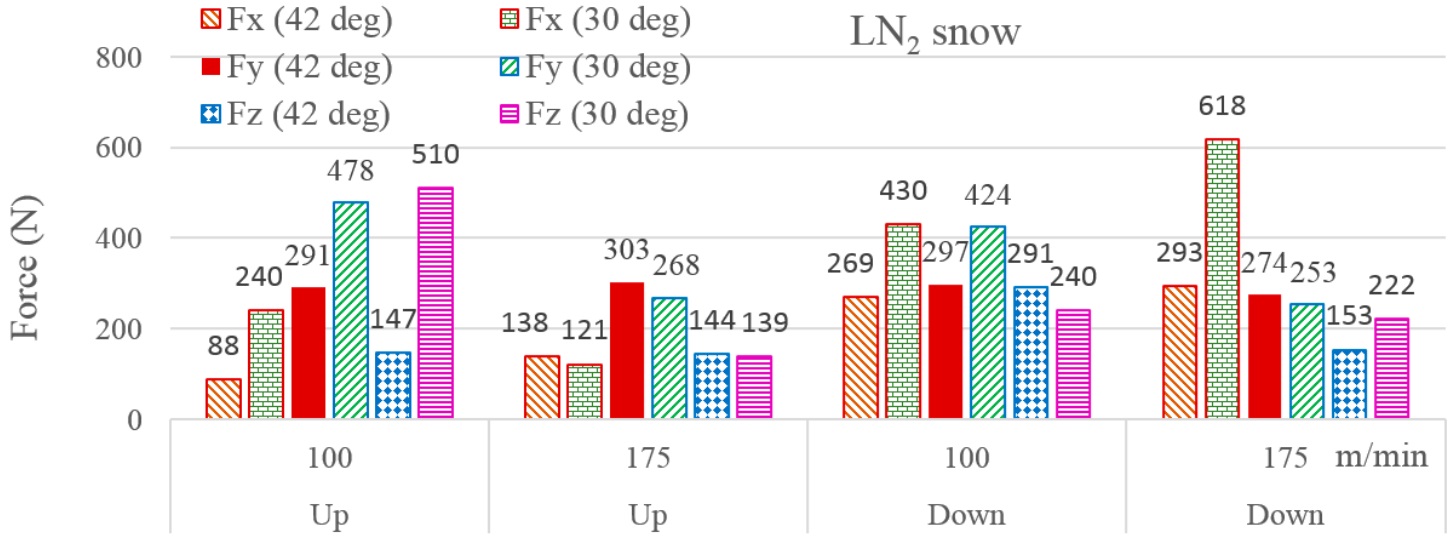
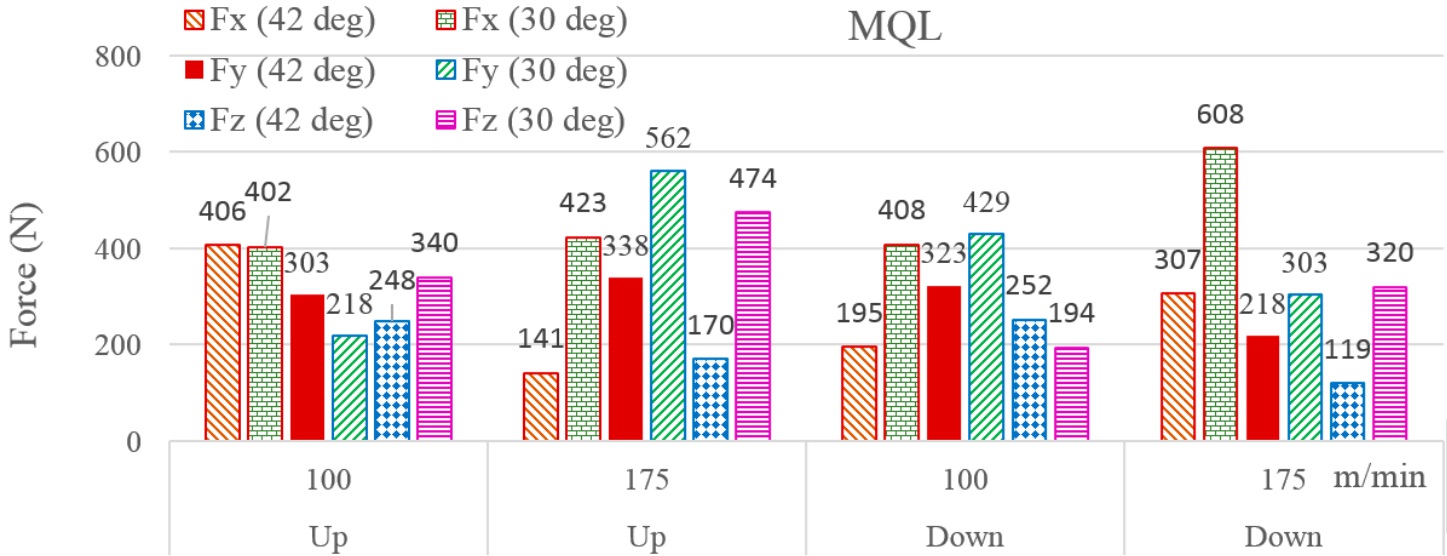
Figure 9. Bar graphs present the experimental results regarding the three components of the machining forces (Fx, Fy, and Fz) for the 24 runs.
Figure 10 presents the progress of the three force components with time for the selected experimental runs. Two concentration zones are visible in each of the three graphs representing the two cutting passes per experimental run. The two zones in Figure 10a are thinner than those in the others because they represent the cutting passes conducted at the higher speed level. Based on the feed directions, the radial force components (Fx and Fy) were found in the positive and negative regions for down- and up-milling, respectively. The axial component (Fz) was located in the negative region irrespective of the milling orientation.
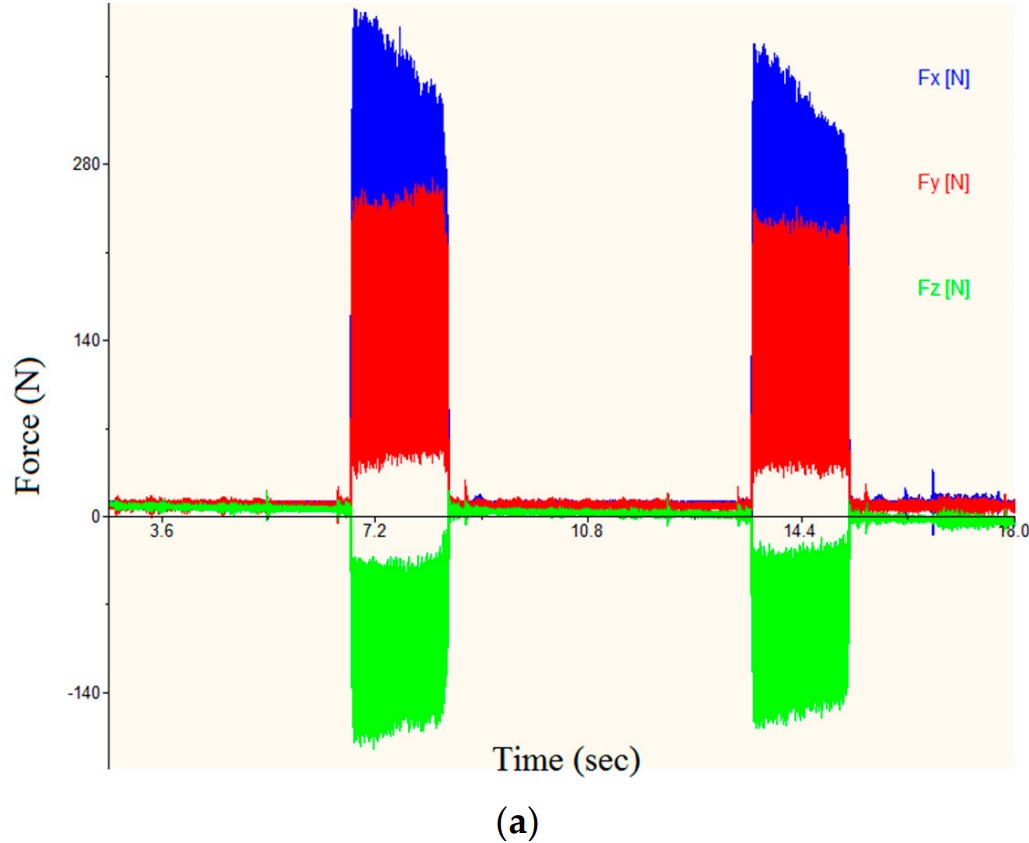
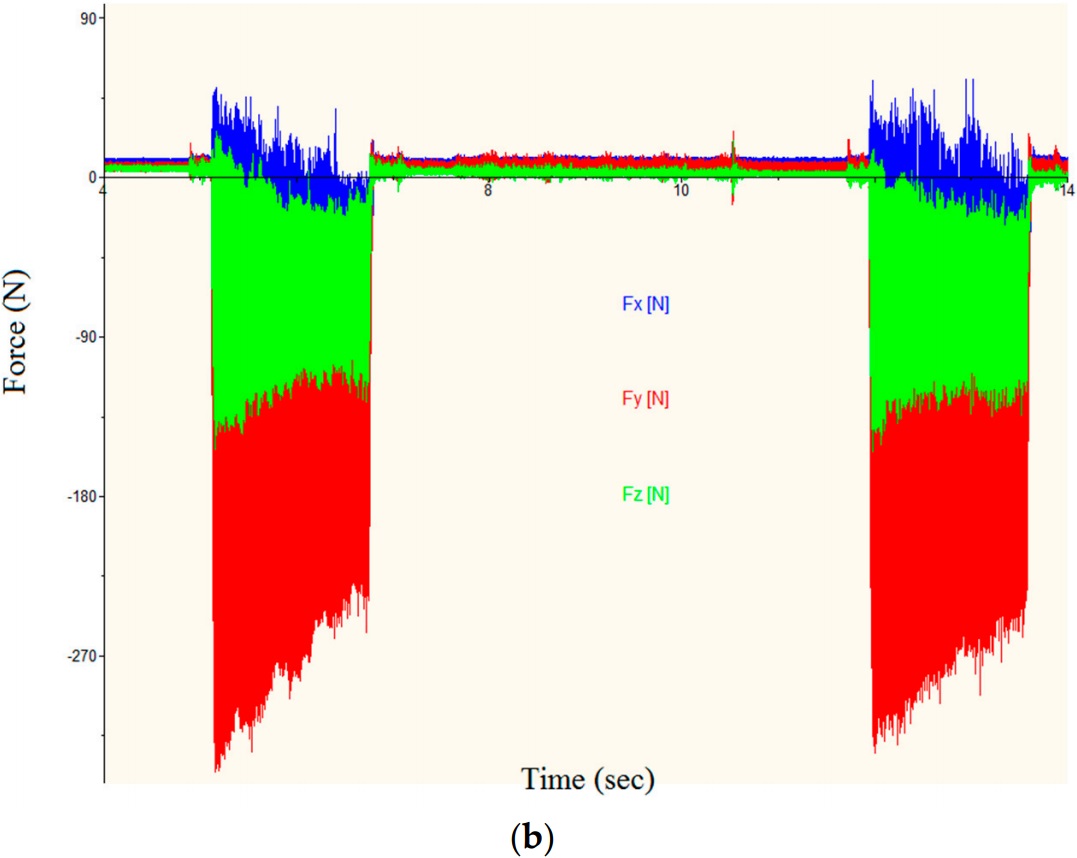
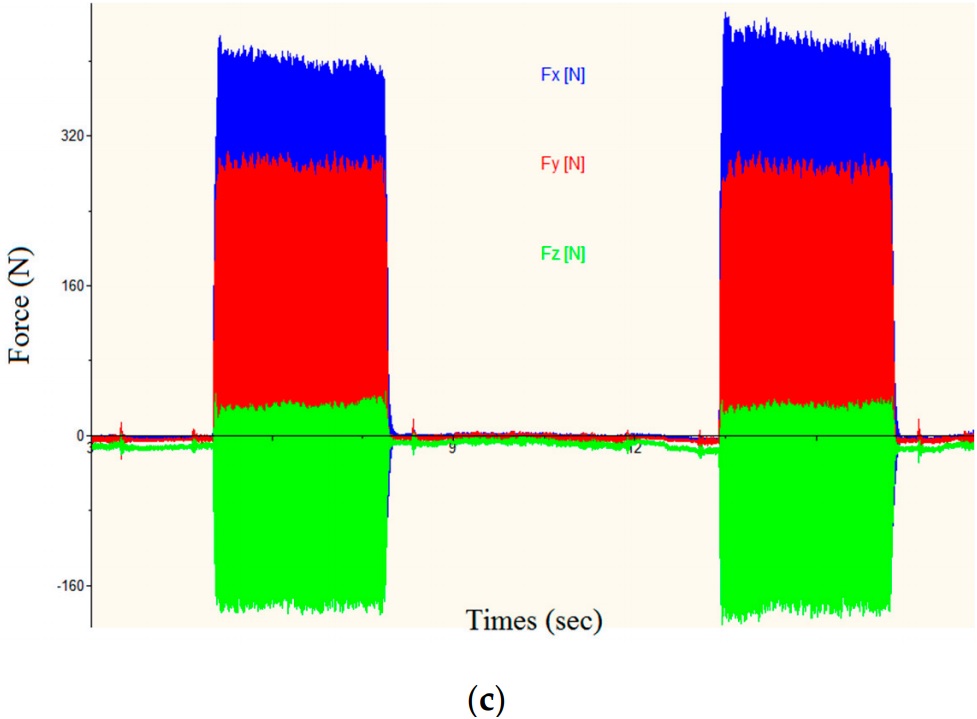
Figure 10. Progress of the milling force components with time for the following experimental runs: (a) CO2, 42◦, down, 175 m/min; (b) LN2, 30◦, up, 100 m/min; (c) MQL, 30◦, down, 100 m/min.
The graphs highlight a phenomenon that sets apart the cryogenic fluids from micro-lubrication. It can be seen from Figure 10a,b that the instantaneous values of the force components sharply decreased as the cutting pass progressed. The magnitudes remained fairly constant in the third graph. This is attributed to the temperature dependent variation in yield strength/flow stress of the work material. As described before, the supply of a cryogenic fluid was opened 20 s prior to the start of the first milling pass. As the cryogenic fluid was also received by the work, in addition to the end mill, the surface temperature fell sharply, raising the material’s yield strength. Thereafter, as the cutting process started, the process heat raised the temperature of the work material, thereby reducing its flow stress. The fall in the work material’s flow stress is reflected by the diminution in the force components as the cutting process proceeded.
The cutting power required at the cutting edge for plastically deforming the work material into a chip is presented as the product of cutting force and cutting speed (Pcut = vc × Fc), where Fc, in peripheral milling, is a function of the three orthogonal force components, end mill geometry, and shear plane angle. This means that the cutting power should have positive correlations with the measured orthogonal machining force components. The correlation coefficient between Pcut and the resultant of the two force components acting perpendicular to the end mill's axis (= [Fx 2 + Fy 2 ] 1/2 ) was found to possess a value of 0.66. Likewise, the correlation coefficient between Pcut and the resultant of all the three force components (= [Fx 2 + Fy 2 + Fz 2 ] 1/2 ) was 0.68. The two correlations suggest that strong uphill relationships exist between the cutting power and the machining forces. It can, thus, be safely stated that machining force data can estimate cutting energy consumption fairly accurately.
3.4. Process Cost
While evaluating PC for the 24 experimental runs, it was found that tooling cost was the most weighted contributing factor, followed, in descending order of weightage, by acquisition cost of cutting fluids, overhead cost, direct energy consumption cost, and equipment depreciation cost. The process cost’s estimation is shown in Figure 11. The figure clearly shows that, of the three cutting fluids tested, micro-lubrication yielded the most economical results, which is attributed to the low levels of VB and low unit cost and consumption rate of the associated cutting fluid. Of the two cryogenic coolants, CO2 snow yielded better results when milling orientation was up, while LN2 was clearly more economical for down-milling. Furthermore, a high helix angle produced better results, especially under the cryogenic cooling environments, due to the associated low levels of end mill damage incurred. Lastly, the effect of cutting speed on process cost was not very clear, as this predictor asserted its effects on all five constituents of PC in different ways. With regard to a continuous cutting process, it was reported that high-speed machining of Ti-6Al-4V yielded better surface finish and caused lower consumption of specific energy than conventional machining, but fared poorly with respect to the sustainability measures of end mill life and process cost.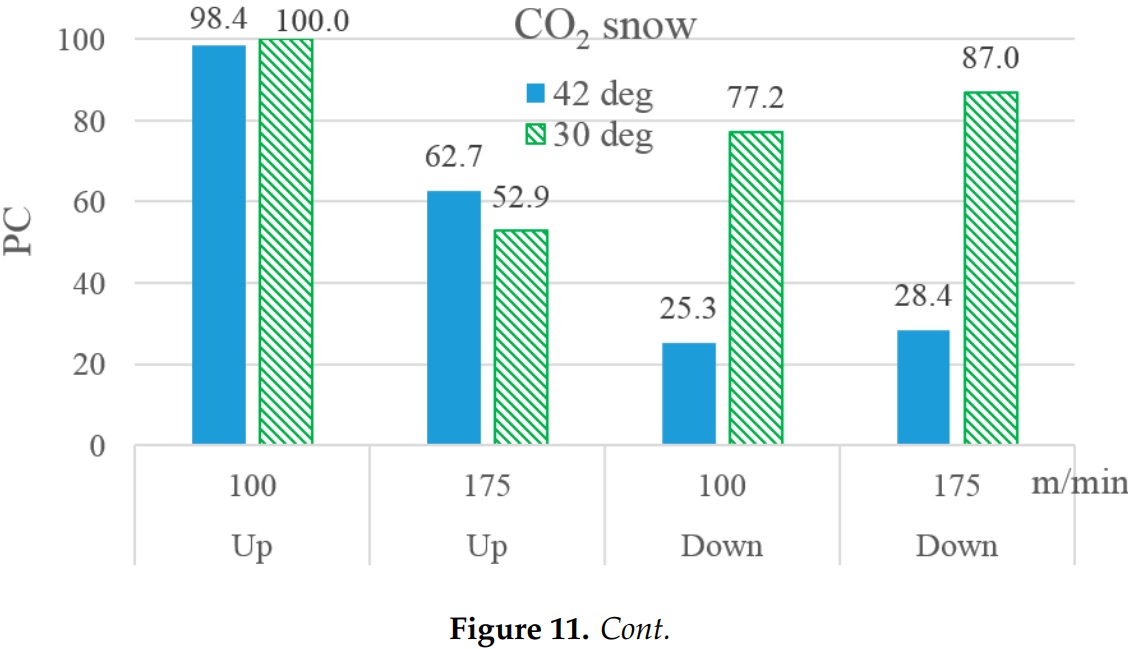
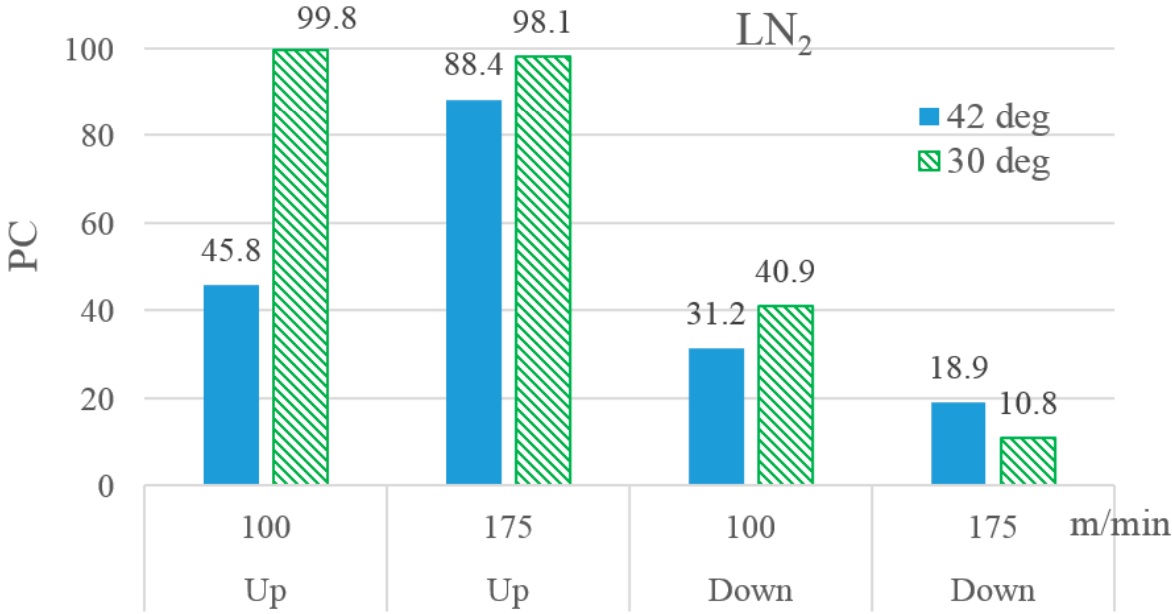
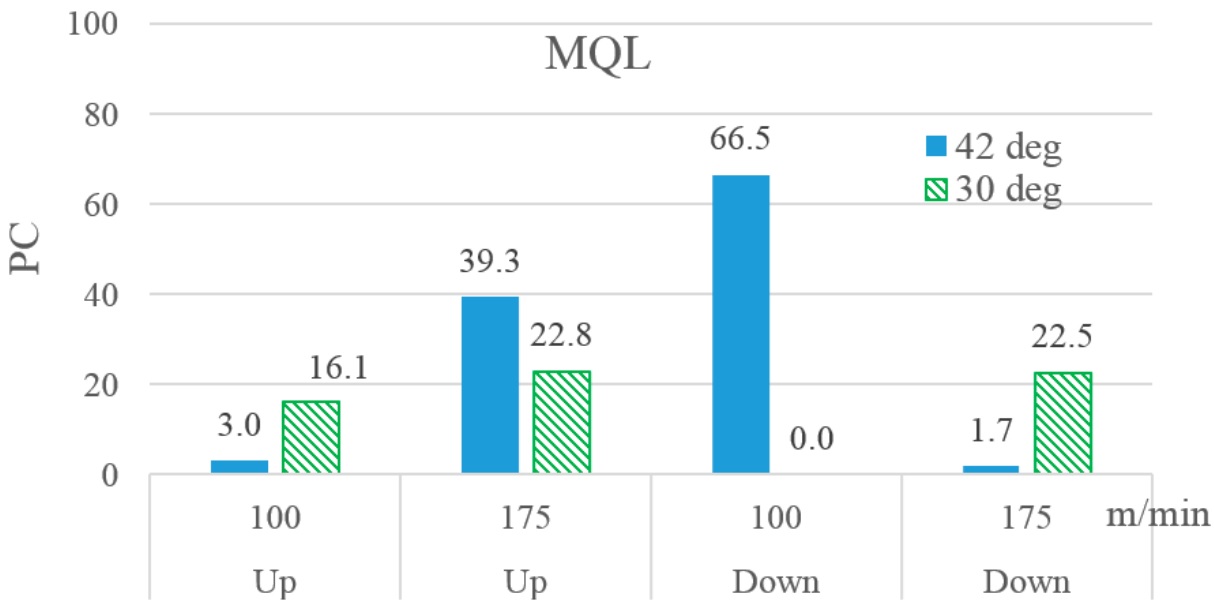
Figure 11. Bar graphs present the process costs for the 24 experimental runs.
4. Discussion on Milling Sustainability
The previous section presented comprehensive quantifications and analyses with respect to the vital sustainability metrics regarding milling of the most commonly used titanium alloy. The current section discusses the implications of the experimental results in the perspective of the three pillars of sustainability: economic, social, and environmental. Process cost is the most important performance measure related to the economic aspect of sustainability. As detailed in the previous section, tooling cost and cutting fluid’s acquisition cost are the most important contributors. Tooling cost is governed by tool wear (VB); a larger value results in a higher cost. On the other hand, VB is also influenced in a positive way by the application of cutting fluids.
The experimental results regarding PC suggest that micro-lubrication, combined with the down-milling approach, ensured the most economical milling of Ti-6Al-4V, realized in the form of slightest tool wear. Work surface roughness also possesses significance with respect to the economic aspect. An acceptable level of surface finish avoids financial losses due to the following factors:
(1) additional processing cost caused by rework, and (2) additional material and processing cost incurred by rejection of the work. In this regard, once again, micro-lubrication and down-milling arose as the ideal combination, as explained in Section 3.2. The social dimension of machining sustainability is highly qualitative. The factors covered under this pillar are worker’s safety, health protection, ergonomics, payment equity, and work pressure and intensification.
Cutting speed is expected to affect ergonomics and work pressure as its low levels may increase working hours of the machine operators and build-up on production slack, leading to enhancement of work pressure. Choice of cutting fluid is another influential parameter with respect to the social pillar. All three levels of cutting fluid tested in this work demand extra space and workload for setting up and operating the fluid supply system. A minor cleaning effort is also required after the milling process utilizing micro-lubrication and cryogenic fluids is over.
The oil delivered to the machining area in micro-lubrication is of minute quantity, which requires an easy cleaning effort. Moreover, the commonly used oils are vegetable-based and are, thus, not hazardous. Application of LN2 to the milling area immediately turns the fluid into its gaseous form, which simply escapes into the environment without affecting the operators. Likewise, compressed CO2 gas, after throttling, converts into snow, which gradually sublimates to a gaseous form and escapes. A small flow rate (0.5 kg/min) of the gas does not pose any asphyxiation risk.
The environmental pillar of milling sustainability is estimated by specific cutting energy, tool damage, and waste generation. The experimental results regarding SCE suggest that Ti-6Al-4V should be milled at a high level of cutting speed using a cutter of a medium-to-high helix angle. Moreover, the application of micro-lubrication is much more energy-conservative than the cryogenic fluids. A high VB causes more frequent tool replacements, leading to a higher number of tools required to remove a given volume of work material. As a result, more energy is consumed for remanufacturing/recycling the worn-out tools or, in a worse case, more landfilling of the end-of-life tooling and extraction of the raw material for making new tools is required. Such a situation quickens depletion of natural resources and causes a harmful effect on the environment. The analysis carried out on tool wear data suggests that the titanium alloy should be milled with the down-milling orientation and under the effect of micro-lubrication. Regarding the issue of machining waste generation, the tested levels of milling orientation, cutter’s helix angle, and cutting speed did not make any difference.
The total mass of chips generated was the same for any combination of these three predictors. On the other hand, all three options of cutting fluid tested in the work were better than the conventional approach of emulsion-based flood cooling. Emulsion coolant is known to create swarf, leading to the need for cleaning the chips before the commencement of their recycling process. Furthermore, the emulsion fluid requires filtration and pumping for its repeated use until it becomes toxic due to contamination from swarf, sump, and exposure to air. Milling under cryogenic and MQL environments does not create any swarf; thus, the chips remain clean. Furthermore, no greenhouse gases are emitted and recycling of the used fluid is not required. Regarding the option of LN2, nitrogen gas is harmless to human health and is also environmentally benign. Moreover, the use of CO2 gas, as a cryogenic coolant, does not increase carbon footprint because a minute quantity is used for cooling. A viable cutting speed of up to 200 m/min was claimed in machining titanium alloys using a natural diamond tool and under the effect of flood coolant. On the other hand, the current work presented sustainable machining of the titanium alloy up to a speed of 175 m/min, but with more economical tooling and environmentally friendly coolants.
In the context of the discussion provided above, the authors would conclude that, with respect to side- and end-milling of Ti-6Al-4V, the application of micro-lubrication is more favorable than the two cryogenic fluids tested. It fared significantly better in terms of all the sustainability measures, namely, tool damage, process cost, work surface quality, and energy consumption (with inclusion of the fluids’ energies). Not all the previously published reports claimed superiority of the cryogenic fluids over conventional approaches. Isakson et al. reported development of tool wear at a faster rate under LN2 than under emulsion-based coolant in the machining of titanium alloy, although the limited supply of coolant was blamed for its below-par performance. Additionally, in the current work, the down-milling orientation clearly outperformed up-milling with respect to tool damage, process cost, and work surface quality. With regard to the other two predictors, the high levels of cutter’s helix angle and cutting speed generally yielded better results, but the observed effects were not emphatic.
5. Conclusions
The presented work aimed to quantify and enhance sustainability of milling a commonly used titanium alloy under the environments of micro-lubrication and cryogenic cooling. The cryogenic cooling environment was set up by the application of two kinds of coolants, throttle and evaporative, realized by expansion of compressed CO2 gas and evaporation of liquid nitrogen, respectively. Additionally, the effects of employing two milling orientations and two levels each of tool’s helix angle and cutting speed on the sustainability measures were also quantified.
The most prominent finding of the work is that application of micro-lubrication in milling of Ti-6Al-4V is more sustainable than that of a cryogenic coolant. Minimum quantity of lubrication outperformed both the cryogenic coolants in terms of tool wear, work surface quality, process cost, and energy consumption. Dissipation of process heat using a cryogenic coolant is not as viable in milling as it is in a continuous machining process such as turning. The interrupted nature of cutting caused by periodic engagement and disengagement of cutting teeth in the work under the action of a super-cool fluid renders the cryogenic coolant far less effective. Among the other predictors, the effects of milling orientation on the sustainability measures in milling of the titanium alloy were highly significant. Down-milling was found to be enormously better than up-milling with respect to tool wear, work surface quality, and process cost. Thus, it is highly recommended to use the combination of micro-lubrication and down-milling for sustainable milling of Ti-6Al-4V.
The effects of tool’s helix angle and cutting speed were different for different measures of sustainability, and they were not highly assertive. The high level of helix angle was excellent for reducing specific cutting energy and also performed well for the sake of reduction in process cost, tool wear, and milling forces. Likewise, high cutting speed was good for reducing work surface roughness and specific cutting energy consumption.
Author Contributions
A.I. conceived and designed the experiments, analyzed the results, and partially wrote the paper; H.S. arranged the tooling and work material; W.Z. and M.J. performed the experiments; M.M.N. determined the responses from the measurements; N.H. arranged the measuring instruments and performed the sustainability analysis; and J.Z. developed the graphs and partially wrote the paper. All authors have read and agreed to the published version of the manuscript.