Ti-6Al-4V(鈦-6鋁-4釩)的可持續銑削;研究銑削方向、銑刀螺旋角和低溫冷卻劑類型的影響
2020-05-25摘要
Ti-6Al-4V作為最常用的鈦合金,具有優異的機械性能和耐腐蝕性能,為其在世界範圍內工業需求量持續上升的首要原因。鈦合金的非比尋常的力學性能被視為其成型工藝的阻礙,銑削工藝也不例外。切削區周圍產生強烈的熱熔劑是造成合金加工性差和加工持續性低的一個既定原因。本文的介紹試圖通過研究銑削方向、銑刀的螺旋角、切削速度以及低溫冷卻液和潤滑劑的種類對銑刀損傷、切削能耗、加工成本、銑削力和工作面粗糙度等可持續性措施的影響,來提高銑削Ti-6Al-4V的可持續性。研究發現,與常用的兩種低溫冷卻劑(積雪二氧化碳和液氮)相比,微潤滑在降低銑刀磨損、工件表面粗糙度、工藝成本和能耗方面的效果更好。此外,在銑刀磨損、工件表面質量和加工成本方面,下銑加工的效果大大優於上銑加工。同樣,高水平的銑刀螺旋角和切削速度也證明對銑削的可持續性有幫助。
1. 導言
鈦合金因其優異的機械性能和耐腐蝕性能,在各個工程領域的需求量空前增加。同樣的性能在"用途上"階段被認為是優良的,但在其生命週期的"加工製造"階段卻被認為是不利的。就加工領域而言,同樣的不利特性降低了其可加工性,這使得切削工藝斷斷續續。可加工性低的原因主要是強度高,與銑刀材料的化學親和力大,切屑刃的接觸長度短。因此,在加工鈦合金工件時,切削刃周圍會形成強烈的熱流,並消耗極高的切削能量,導致銑刀磨損速度加快。
銑刀的高磨損率,導致頻繁更換鎢鋼銑刀,使加工過程在經濟上和環境上極不持久。這個問題一般是透過降低金屬去除率或應用乳化冷卻劑解決,但實際上這兩種方法都沒有持續性的解決方案。在抑制切削區域周圍的強烈熱流方面,應用低溫流體,特別是液氮(LN2),效果非常好。這種流體提供了可行的解決方案,因為它的工作溫度極低,不產生廢物,流速可控。此外,在中等切削速度的鈦合金加工中,應用微潤滑(也稱為最小潤滑量(MQL))也被證明對提高銑刀壽命和改善鈦合金的表面質量非常有益。MQL是一種近乾式加工方法,將微量的潤滑油弄成粉狀成空氣流,並將所產生的氣溶膠塗抹在切削部位。
雖然在量化低溫冷卻劑對連續加工過程的影響方面取得了穩定的成果,但對銑削等間斷加工過程的影響卻不多。低溫銑削不同於在低溫環境下進行的連續加工過程,因為在這個意義上,銑刀的切削刃與工件週期性的快速切入和切出,導致切削刃週期性地加熱(由工件的塑性變形釋放的熱能引起)和冷卻(由進入的低溫流體相互作用引起)。這樣的過程預計會引起刀齒的熱衝擊,導致開裂、崩裂和更多災難性的銑刀損壞。此外,還需要對LN2等蒸發式低溫流體和積雪CO2等節流式低溫流體的冷卻效果進行比較分析。關於銑削工藝,銑削方向和銑刀的螺旋角這兩個不同的參數也會對工藝的可持續發展措施產生影響,如銑刀損壞率、切削能耗、工作面粗糙度、工藝成本和切削力等。
文獻回顧
本節介紹已發表的有關鈦合金銑削問題、低溫冷卻劑在鈦的加工(特別是銑削)中的應用、在銑削中使用微潤滑的潛力以及加工的可持續性措施等方面的回顧。而增加液氮的流速可以延長鈦合金加工中的銑刀壽命。此外,當冷卻液的壓力和流量增加時,表面的完整性將得到極大的改善。用液態二氧化碳對Ti-6Al-4V進行銑削,可大大減少橫向裂紋的擴展和崩解。因此,與乳化液冷卻相比,可以延長銑刀的使用壽命。研究銑刀壽命標準、工件材料的回火狀態、切削參數和微潤滑對銑削工藝的可持續發展對應的影響。研究發現,材料的回火狀態和使用MQL的選擇是影響可持續發展措施的最大參數,如特定切削能量、銑刀壽命和加工成本。
Sartori等人研究,MQL系統與CO2和LN2分配系統混合在一起,可以優化潤滑和冷卻效果,從而顯著減少加工坑洞磨損。在另一項研究中,在大量冷卻液下加工並不能降低表面粗糙度。研究稱,LN2與油基MQL混合後的LN2在所有測試的冷卻劑中可以產生最低的切削力。Isakson等人報告,使用LN2和乳狀冷卻劑的冷卻方法對表面完整性產生了類似的效果。此外,研究中還設法減少了低溫冷卻劑的消耗,以提供良好的表面質量,同時又減少對環境或經濟的負面影響。研究發現,用液態二氧化碳對Ti-6Al-4V進行銑削,可大大減少崩裂和橫向裂紋的擴展;因此,與乳化液冷卻相比,可顯著延長銑刀壽命。研究了在高強度β-鈦合金連續加工中使用CO2積雪作為冷卻劑及其與MQL合併的效果。
研究發現,在持續發展方案方面,積雪二氧化碳的使用情況和應用地點對持續發展方案的影響很大。在另一項研究中,用LN2進行低溫冷卻可大大降低銑刀磨損,進而提高金屬去除率。結論是,在一定的切削速度下進行低溫加工,其能量消耗要比用大量冷卻液加工低得多。Mia等人研究,使用LN2雙噴嘴是降低能源消耗和工作溫度,以及改善加工表面質量的極佳方法。另一項研究中,報告了在-79.5◦C的溫度下使用液態二氧化碳對鎳鉻合金進行切削時,與乾式、濕式和MQL切削相比,平均表面粗糙度分別降低了42-47% 、24-27%和16-21%。
此外,還發現低溫冷卻可以增加表面的壓應力,減少側面的磨損。Li等人提出了用石墨烯分散植物油基切削液銑削Ti-6Al-4V合金的優化方案。結果顯示,銑削力、溫度、表面微硬度和工件表面粗糙度等銑削性能指標均有明顯改善。對Inconel 718的加工進行了乾式和MQL銑削工藝的比較。結果發現,MQL可以提高銑刀壽命和工件表面光潔度。實驗研究的重點是建立銑刀磨損率對銑削鈦合金的經濟性影響的模型。與乾式加工相比,低溫冷卻方式的耗電成本和機床運行成本分別降低了47.5%和47.59%。在另一項關於Ti-6Al-4V鈦合金端銑的實驗研究中,比較了低溫冷卻對工件表面完整性的影響和乾式加工和大量冷卻液加工環境下的影響。
研究顯示,與水冷和乾式加工相比,低溫冷卻使表面粗糙度分別降低了31%和39%。還使得低溫加工環境下微觀表面缺陷的顯著減少。Dawood等人研究了三種切削參數對大量冷卻液和持續乾式加工環境下的性能的影響。研究發現,乾式加工可以獲得較好的表面光潔度,但承受了更嚴重的黏附磨損、坑洞磨損和切屑堆積的形成的磨損。實驗研究評估了低溫冷卻與MQL潤滑在Inconel 718輪廓銑削中的效果。研究顯示所提出的CroMQL方法比其他潤滑冷卻技術具有優越性。Pusavec等人對Inconel 718在乾式、MQL、低溫和低溫潤滑等各種潤滑環境下的持續加工進行了實驗研究。根據對結果的統計分析,作者認為冷卻/潤滑條件對銑刀壽命、切削力和動力消耗等可持續發展措施有顯著影響。
銑削方向(上銑和下銑)和銑刀的螺旋角是銑削參數之一,但這些參數對加工過程與持續性發展的對應措施影響不大。研究顯示,這兩個參數對硬質合金銑刀高速銑削淬火鋼的銑刀壽命和工件表面粗糙度都有明顯的影響。具有45◦螺旋角的銑刀,其銑刀壽命明顯比30◦螺旋角的銑刀要長得多,表面光潔度也稍好。此外,研究發現,與上銑相比,下銑可以提供更好的表面光潔度,但與上銑相比,銑刀壽命相同。
本文提出了一種銑刀方向優化模型,將銑削力引起的偏轉誤差的影響納入其中,以實現五軸曲面銑削加工中更好的加工精度控制。比較高合金鋼的上銑和下銑的效果。研究發現,上銑的方法在工件表面容易產生壓縮殘餘應力,而與下銑相比,表面光潔度較差。為了比較上銑和下銑在Inconel 718端銑中的效果,進行了一項實驗研究。結果發現,與上銑相比,下銑法有較低的銑刀磨損表現。此外,與下銑加工時產生的不連續的切屑相比,上銑加工時形成的切屑是分段的、連續的。Wan等人提出了一個分析模型來量化銑刀的螺旋角對切削力巔峰值的影響。
研究顯示,切削力的巔峰值隨螺旋角的增加而降低,而與最小切削力巔峰值相對應的最佳螺旋角是銑刀刃數、軸向切削深度和銑刀直徑。另一項研究的重點是量化螺旋角對304L不銹鋼乾式側銑的塗層硬質合金立銑刀性能的影響。研究發現,軸接觸點的數量和有效切削長度隨螺旋角的增大而增加,導致銑刀磨損降低,切屑變薄,但切削溫度升高。結論是,採用高螺旋角為60◦的TiAlN塗層立銑刀可獲得最佳的表面光潔度和較長的銑刀壽命。另一項研究通過考慮銑刀的螺旋角、進給率和銑刀的偏心率的影響,提出了一個預測工件表面和各種表面粗糙度指標的數學模型。
從文獻綜述中可以看出,目前的現狀與這項研究的目標有如下差距。
(1)迄今為止,關於低溫流體在鈦合金銑削中的應用,由於大部分的研究都只集中在車削工藝上,因此,迄今為止所有的加工研究都非常有限。(2)沒有關於節流冷卻劑和蒸發型低溫冷卻劑在間歇性切削過程中的冷卻效果比較的可檢索研究。
(3)量化銑削方向和銑刀的螺旋角對鈦合金加工的持續發展應對措施的影響研究工作有限。
針對上述研究,本研究以α+β鈦合金(Ti-6Al-4V)的側銑和端銑為例,採用3種切削液(蒸發式低溫冷卻液、節流式低溫冷卻液和微潤滑)、2種銑削方向、切削速度和銑刀螺旋角各2個級別的切削液,對側銑和端銑的可持續發展措施進行量化和改進。要評價的銑削過程的可持續性措施是切削能耗、銑刀損傷、工件表面粗糙度、加工力和加工成本。
2. 研究實驗
本節介紹了有關加工材料和工具、預測變量、反應(可持續性措施)、實驗設計、固定參數、設備和測量儀器等方面的細節。
2.1. 工件材料和工具
本研究中使用的工件材料為Ti-6Al-4V,是一種常用的α+β鈦合金。該材料的退火形式採用尺寸為75 mm×200 mm×19 mm的板狀材料。熱處理時,將工件在778~782◦C的溫度下浸泡約70min,然後進行空冷。經過熱處理後的工件材料的極限抗拉強度、屈服強度(0.2%的證明應力)和伸長率分別為1003.5MPa、927.3MPa和15%。本研究中使用的銑刀是經過FIRE塗層的硬質合金方頭銑刀,直徑為8mm,切削刃數4刃。 FIRE是一種多層TiN+TiAlN陶瓷塗層體系,可使銑刀有極強的耐磨性和耐熱性。該塗層的硬度為3300HV,摩擦係數為0.6。螺旋角為30◦的銑刀的總長度和切削長度分別為68 mm和22 mm,螺旋角為42◦的銑刀的總長度和切削長度分別為63 mm和19 mm。每次實驗中都使用新的立銑刀。圖1列出了實驗中使用的兩種銑刀。
.jpg)
圖1.陶瓷塗層碳化鎢側銑刀和端銑刀的螺旋角分別為(a.) 42° 和 (b) 30°。
2.2. 預測因素、反應和實驗設計
銑削實驗中控制了以下四個預測變量。
(1)切削液。對該預測變量進行了以下三個水平的測試。(a)蒸發低溫液(液氮);(b)節流低溫液(積雪CO2);(c)微潤滑(最小潤滑量)。
(2)銑刀螺旋角,λ(度)。該預測值選擇了30◦和42◦兩個等級。
(3)銑削方向。該二元預測器的兩個選項是上銑和下銑。
(4)切削速度,vc(m/min)。該預測器的兩個級別選擇為100米/分鐘和175米/分鐘。
上述四個預測變量的級別共產生了24組(=3×2×2×2)的實驗運行,以執行全因素設計的實驗。表1列出了實驗中控制的四個預測變量級別的詳細信息。需要特別注意的是,第一個和第三個預測因子是分類的,而另外兩個是數值。在前期試驗的基礎上,選擇了兩個級別切削速度(100和175 m/min)。在特定的進給速度和徑向切削深度下,切削速度超過200m/min時,銑刀在切削過程中會發紅發熱,切削邊緣會被厚厚的黏附屑覆蓋。根據觀察結果,將上述的切削速度固定為175m/min。因此,下限值被確定為上限值的50%到60%之間。
表1. 實驗中控制的四個預測變量的水平。MQL-最小潤滑量
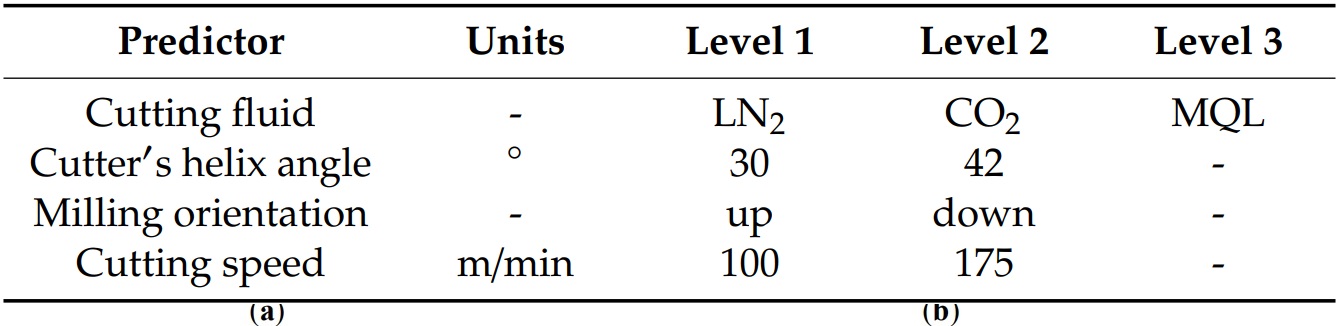
每次加工實驗皆在指定尺寸下去除600 mm3的工件材料體積。0.5毫米(切削的徑向深度)×8毫米(切削的軸向深度)×150毫米(切削長度)。150mm的切削長度分兩道等長的工序完成。圖2是關於切口長度和兩個切口深度的圖形描述。在每次加工中都使用新的側銑刀和端銑刀。上銑是指銑刀的切削方式,銑刀的切削刃以零切屑厚度進入工件表面,並以最大切屑厚度離開工件表面。相反,在下銑方式中,銑刀的刀刃切入和切出工作面的切屑厚度為最大,下銑切屑厚度為零。
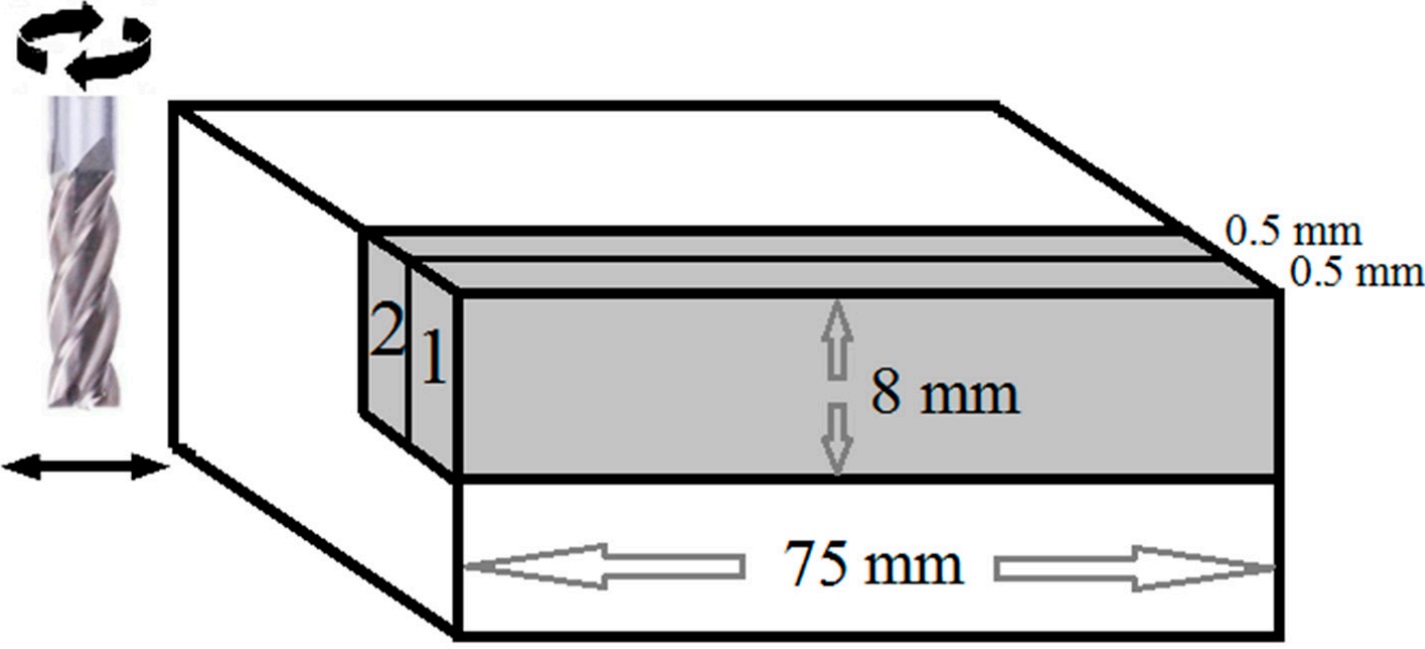
圖2.切削示意圖,每個實驗運行顯示的切削長度 =2×75 mm2(非比例尺),軸向切削深度=8 mm,徑向切削深度=0.5 mm。切削示意圖為每個實驗運行顯示切削長度= 2×75毫米2(不按比例),切削的軸向深度= 8毫米,和切削的徑向深度= 0.5毫米。數字1和2顯示了切片切除的順序。每道工序中要切除的材料總體積(600 mm3)顯示為灰色區塊。
在24次加工實驗中每次的結果得到以下結論。
(1)銑刀的四個切削刃上的側翼磨損面的平均寬度VB(mm),在去除固定體積(600 mm3)的工件材料後為確定相同。(2)銑削面的平均計算表面粗糙度為Ra(μm)。
(3)特定切削能量,SCE(J/mm3),整個切削長度的平均值。
(4)加工力分量,Fx、Fy和Fz (N),整個切削長度的平均值。 Fx和Fz分別與進給方向和銑刀軸線對齊,而Fy是垂直於被加工物側表面的第三個正交分量。
(5)加工成本,每個工件(台幣/去除的工作材料mm3,換算成100比額度的比較成本值)。
此外,對銑削過程中的其他可持續發展應對措施,如廢料的產生、操作者的安全和健康等進行了定性討論。
2.3. 實驗設置和測量
所有加工實驗均在Mikron UCP 710上進行,五軸立式加工中心(Mikron Holding, Biel, Switzerland),最大轉速、進給速度和功率分別為18,000轉/分、20米/分和16千瓦。銑削是以直線方式進行的,每次銑削過程中,在75mm的邊上切削兩次。圖3顯示加工實驗裝置。基於節流的低溫冷卻設備由一個儲存瓶組成,其中含有在5.5兆帕壓力下壓縮的二氧化碳氣體。壓縮後的氣體通過銅管從瓶中輸送到出口噴嘴。在2毫米直徑的噴嘴出口處的二氧化碳氣體的質量流量為0.5公斤/分鐘,而儲存壓力為5.5兆帕。噴嘴的出口距離加工區域很近,CO2氣體直接衝擊到刀刃上。由於焦耳-湯姆森效應,噴嘴出口處的氣體膨脹並吸收了周圍環境的熱量。因此,節流氣體冷卻到-72℃左右的溫度,使其轉化為半固態(積雪CO2)附著在模具系統和工件表面。以蒸發為基礎的低溫冷卻設備儲存含有氮氣的儲存槽中,將該儲存槽裡的氮氣冷卻至液態。LN2的射流沖擊到含有氮氣的冷凝氣體中,被冷卻成液態。在噴嘴出口處測量到的LN2射流溫度為-197℃。調整噴嘴的方向,使液體大量直接噴向切削刃的部分,穩定降低工件材料切入和切出的切削刃切削區域溫度。以最小潤滑量的形式提供微潤滑,在壓縮至0.6兆帕的空氣流中,以25 mL/h的速度將植物油混合在一起,以最小的潤滑量提供。所產生的氣霧劑被塗抹在銑刀的切削區域周圍。
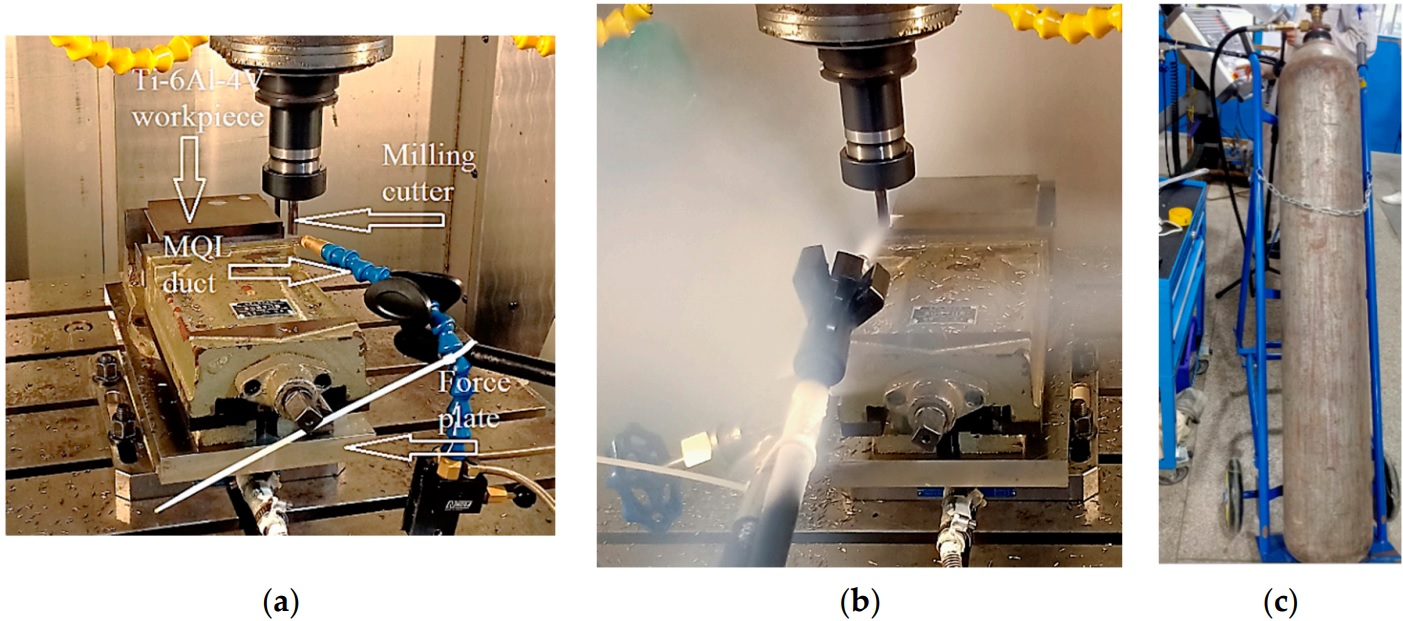
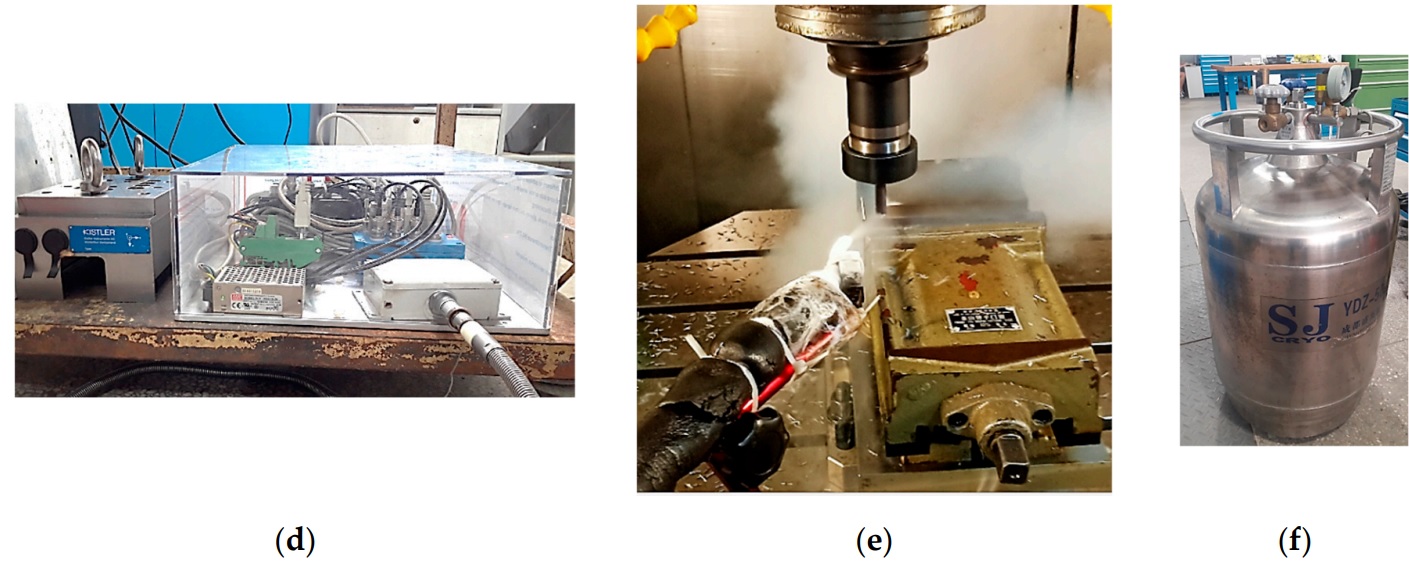
圖3. 實驗裝置。 (a)Ti-6Al-4V工件,銑刀和MQL風道;(b)積雪CO2的應用;(c)CO2氣體儲存瓶;(d)切削力數據採集系統;(e)LN2的應用;(f)LN2的儲存槽。
使用裝有照相機的光學顯微鏡ARTCAM 130-MT-WOM測量使用過的刀刃側面磨損情況。將採集到的側翼面圖像按照比例尺進行處理,確定四個切削刃上的側翼磨損的平均寬度。然後,VB是取四個刃的側翼磨損的平均數計算出來的。在完成兩道工序後,使用Mahr MarSurf M 300 C (Mahr GmbH, Göttingen, Germany)移動式粗糙度測量儀對側表面的粗糙度進行測量。該儀器採用2μm的接觸式測針,根據ISO 11562標準,找到銑削面的算術平均高度(Ra)。每次測量的採樣長度為4mm,採用高斯曲線濾波,得到粗糙度值。每次實驗運行時,分別在距離銑削側表面的起始邊緣15、30、45和60毫米的距離上進行了四次測量。然後,通過取四次測量的平均值,得到Ra。使用基斯勒壓電式測功機9265B(Kistler AG,瑞士伯爾尼),使用9443B測力板測量切削力。該測功機在x和y方向的測量範圍為0-15 kN,z方向為0-30 kN。加工成本,PC,由五個部分組成。首先,銑刀成本通過VB(mm)/(0.3 mm×600 mm3)乘以銑刀的當前市場價格(TWD)來量化,其中VB是銑刀的平均側刃磨損,是在去除600 mm3的工件材料體積後測量的平均側刃磨損。
以毫米為單位的數字 "0.3 "代表加工銑刀普遍採用的銑刀壽命標準。由於用過的銑刀經過研磨和重塗後可以轉售,因此,從新銑刀的購買成本中減去銑刀的平均轉售價格。顯然,VB越大,銑刀成本越高。其次,每一次實驗的直接用電成本,等於商業電價(TWD/kWh)和數控機床及其他相關設備在實際切削過程中所消耗的具體能量(kWh/mm3)的乘積(LN2/MQL)。第三,間接費用包括1名熟練操作人員的工資費用(TWD/h)和在裝有銑床的小房間內使用照明和暖通空調的費用。
後者是由電費和電燈及暖通空調系統的總瓦數(TWD/kWh×kW=TWD/h)的乘積得出。間接費用按實際切削過程中的時間計算。用TWD/h除以相應的MRR,得出間接費用,單位為TWD/mm3。第四,設備的折舊費是以各設備(數控銑床、MQL、LN2設備、CO2儲存瓶)的實際購置成本,按實際去除1 mm3工件材料體積的實際時間按比例計算。4台設備的使用壽命和殘值分別取0至10年。在採用100和175 m/min的切削速度下,去除600 mm3工件材料所需的加工時間分別為5.65 s和3.23 s。
一年的工作天數和每天的工作時間分別為250天和8小時。採用直線折舊模式計算折舊成本。最後,切削液的消耗成本是將切削液(LN2、植物油或CO2)的質量流量(kg/min)乘以單位質量的採購成本(TWD/kg),再除以運行時的物料去除率(MRR)(mm3/s),得出切削液的消耗成本。所採用的成本計算方法的具體細節可參見參考文獻。因此,每次運行的PC成本是以去除的工件材料的TWD/mm3為單位。使用以下公式進行量化:

其中A1=新立銑刀的採購成本(台幣),A2=銑刀的平均轉售價格(台幣),SE=機床及相關冷卻/潤滑設備的比能量(J/mm3),B=商業電價(台幣/kWh),C=熟練的機床操作人員的時薪(台幣/小時),D=燈和暖通空調的總瓦數,單位為kW,F=所有相關設備的採購成本。 G=切削液的採購成本(TWD/kg);tm=實際加工時間(5. 65 s和3.23 s),m˙=切削液的質量流量。其中3.6e6和7.2e6分別代表千瓦時換算成焦耳和年數換算成秒的係數。
考慮到不斷出現的通貨膨脹,以100為比例額度的比較成本結構來表示工藝成本更有意義。在這種安排中,最節省開支的結果以100表示,最經濟的結果以0表示,所有其他的數字按比例確定在0和100之間。
每個實驗運行的具體切削能量的消耗量確定如下:
一、3個電流鉗式電錶。
在數控機床的三相交流電源上安裝了Hantek CC 65,用於測量加工過程中的電功率(Ptotal)。輸入電壓(V)和功率因數(PF)分別為220V和0.85。總功率按以下公式計算。
二、其中I1、I2和I3代表電流。
用三個鉗形表測量的安培值來表示。非切削功率(Pnon-cut)是通過在既定的轉速和進給速度組合下沿進給方向旋轉和線性移動銑刀來確定的。銑刀分別以1592和2785 mm/min的進給速度線性移動,在採用100和175 m/min的切削速度下運行。
三、非切削功率式
銑削過程中的平均切削功率(Pcut)是由數控機床在銑削過程中所消耗的相關平均總功率減去,得到平均切削功率(Pcut)。
四、平均切削功率(J/秒)
每次運行時,將每次運行的MRR值除以相關的材料去除率(MRR),就可以得到特定的切削能量,即SCE(J/mm3)。在切削速度為100 m/min和175 m/min時的MRR值分別為106.2和185.8 mm3 /s。為了更加了解受控預測因子的個體效應,以及它們對測得反應的交互影響,我們還對實驗數據進行了方差分析。方差分析不僅有助於分離出各個預測因子的效應,還能揭示出效應的強弱。
2.4. 固定參數
在所有實驗中,每刃進給量、軸向切削深度和徑向切削深度分別固定為0.1 mm/z、8 mm和0.5 mm。每把銑刀都被固定在距切削端28 mm的夾頭中。所有的運行都是通過在一條直線上進行兩次銑削來進行的。相關切削液(LN2/CO2/MQL)的供應是在銑刀與工件首次接觸前20s開始,在兩道工序之間的過渡期間沒有停止。第二道工序完成後,立即停用了相關切削液。
3. 實驗結果
本節詳細介紹了有關銑刀磨損、表面粗糙度、特定切削能量消耗、切削力和加工成本的實驗結果。
3.1. 銑刀磨損
圖4顯示了24次運行的實驗結果,關於VB在去除600mm3的工件材料後獲得的實驗結果。實驗結果根據所使用的切削液類型分為三個圖。結果是顯而易見的,一般來說,與兩種低溫冷卻方案相比,微潤滑產生的銑刀磨損程度較低。在兩種低溫冷卻方案中,顯然是蒸發冷卻液(LN2)的表現更好。此外,LN2的VB最小(0.04 mm)也是所有運行中的最小VB。此外,可以明顯看出,當使用LN2切削液時,下銑加工產生的磨損明顯小於上銑加工。關於銑刀的螺旋角,大角度(42◦)在銑刀磨損方面的表現優於小角度(30◦)。遺憾的是,從圖中可以看出,螺旋角對任何其他預測因素對VB的依賴性並不明顯。雖然較高的螺旋角有利於較高的材料去除率(通過高速度和高進給量實現),但由此產生的較小的刃口間距在此速度下產生了排屑問題,尤其是對於像Ti-6Al-4V這樣的黏性材料來說,更是如此。這就是為什麼螺旋角和切削液之間沒有看到螺旋角和切削液對銑刀磨損的交互影響。下銑(也稱為爬坡銑)的銑刀磨損率一般比上銑(傳統銑削)低。
此效果在LN2下進行的銑削中尤為突出。在下銑過程中,隨著切削過程的進行,切屑厚度逐漸減少,最後達到零,從而防止了切削刃和相鄰的側翼面與工件面的摩擦和灼傷。在向下銑削過程中觀察到的側翼磨損程度較低的原因是由於這種無摩擦切削模式。在切削速度方面,通常發現較高的切削速度會產生較高的銑刀磨損,但影響不大。較高的切削速度會引起或加速銑刀損壞的溫度依賴性模式,因為發熱率的提高,導致銑刀磨損加劇。因此,切削刃和相鄰面的磨損程度較高,單位體積的工件材料的磨損程度較高。
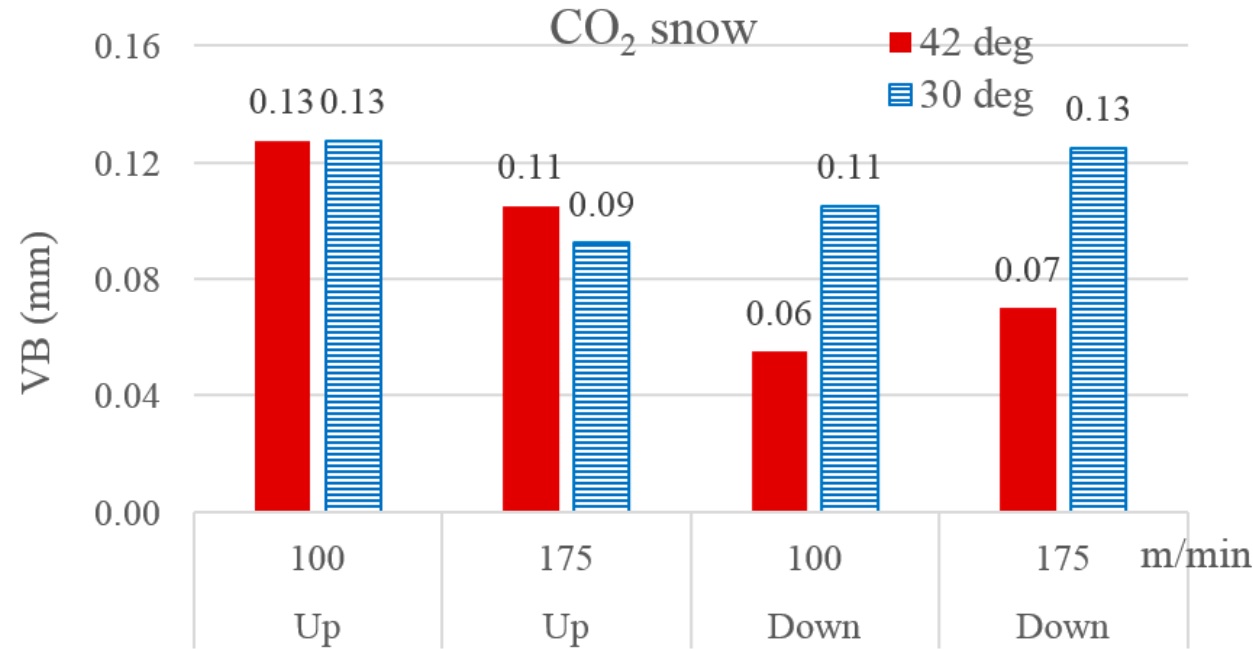
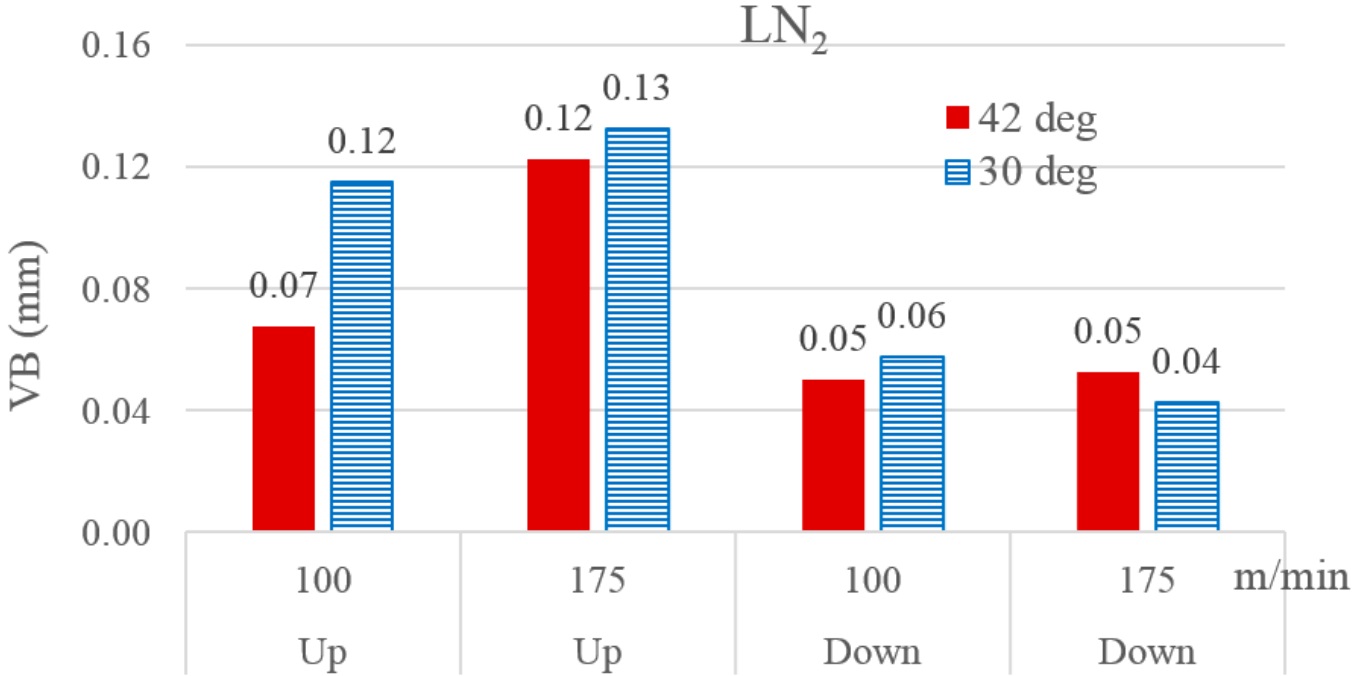
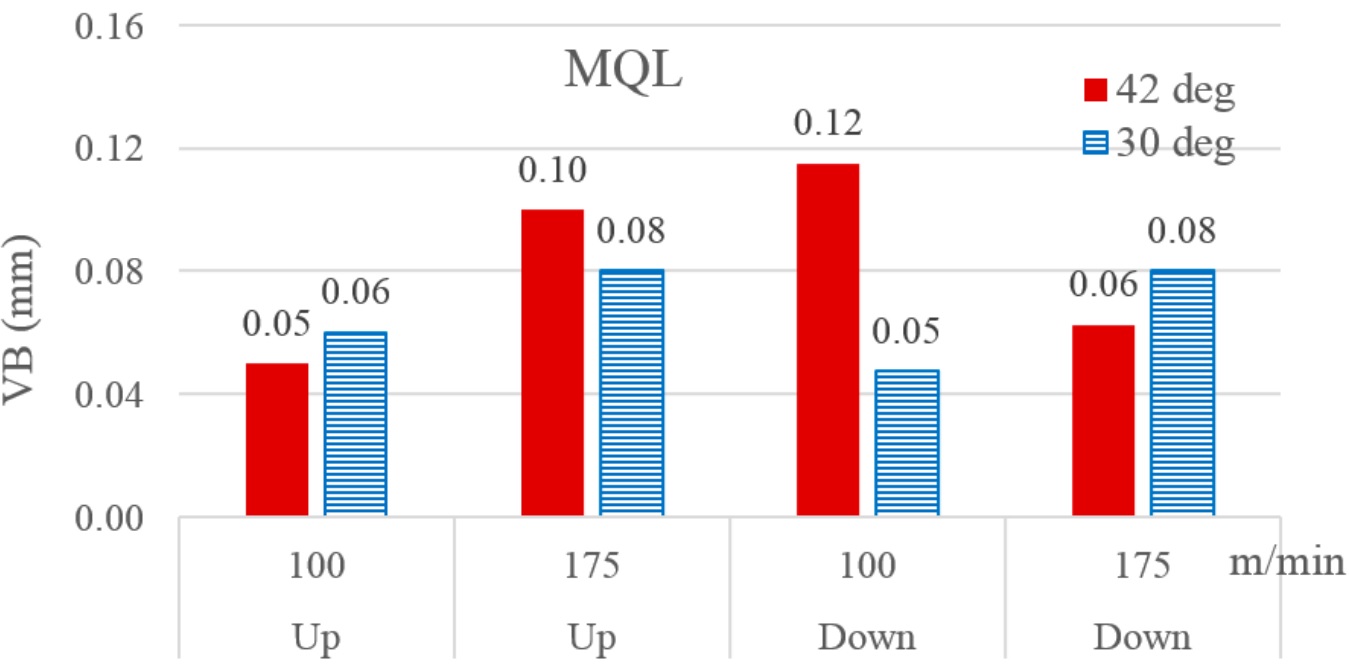
圖4.條形圖顯示了24個實驗運行的側翼磨損地平均寬度(VB)
對圖4所示的數據進行了方差分析。分析結果顯示,銑削方向是對VB影響最大的因素,其次是切削液的選擇。銑削方向與切削液之間的交互作用在統計學意義上排在第三位,其次是切削速度和銑刀螺旋角的單獨影響。銑削方向和切削液對銑刀磨損的強烈交互作用,從圖4的3張圖中可以看出,只有當切削液為液氮時,下銑削的銑刀磨損率遠遠低於上銑削。 Shokrani等人聲稱,在200 m/min的切削速度和0.03 mm/每齒進給率下,用於Ti-6Al-4V低溫(LN2)銑削的塗層硬質合金銑刀的側面磨損最小。目前研究發現,MQL在銑刀磨損表現比低溫切削液更好。
這個研究發現是基於在稍低的切削速度下進行的銑削,但進給速度極大的提高了。圖5顯示了所選銑刀的微觀圖像。這六種銑刀的選擇是為了確保預測變量的最大程度的多樣性。顯微鏡下的視覺分析顯示,漸進式機械磨損和工件材料的黏附是銑刀損壞的主要方式,而在少數銑刀中也觀察到了切削刃的崩裂。從圖5a,d可以看出,所有的銑刀在上銑和兩種低溫液體中都會在其切削刃處出現厚厚的黏附切屑。所有切削加工中,黏附的材料都是小片狀的。這一觀察結果與以前的研究結果相吻合。據報導,在LN2輔助加工Ti-6Al-4V時,黏附磨損是主要的銑刀損傷主因。此外,據報導,在淬火鋼的外圍銑削中,上銑也會引起嚴重的銑刀磨損。
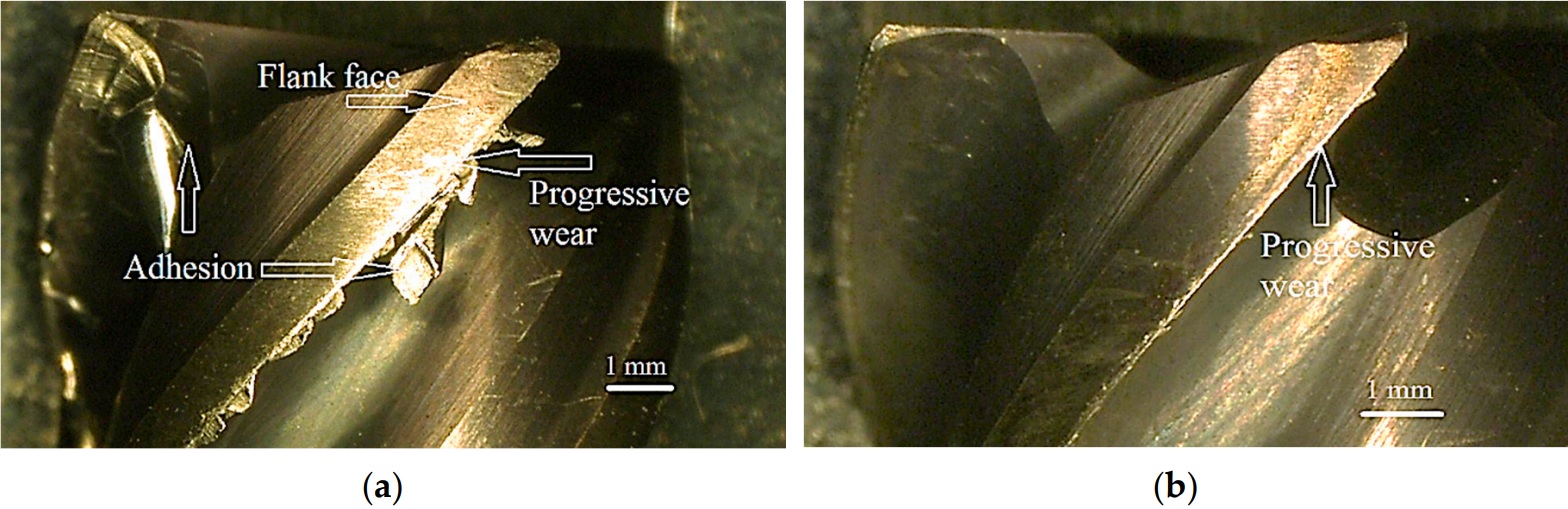
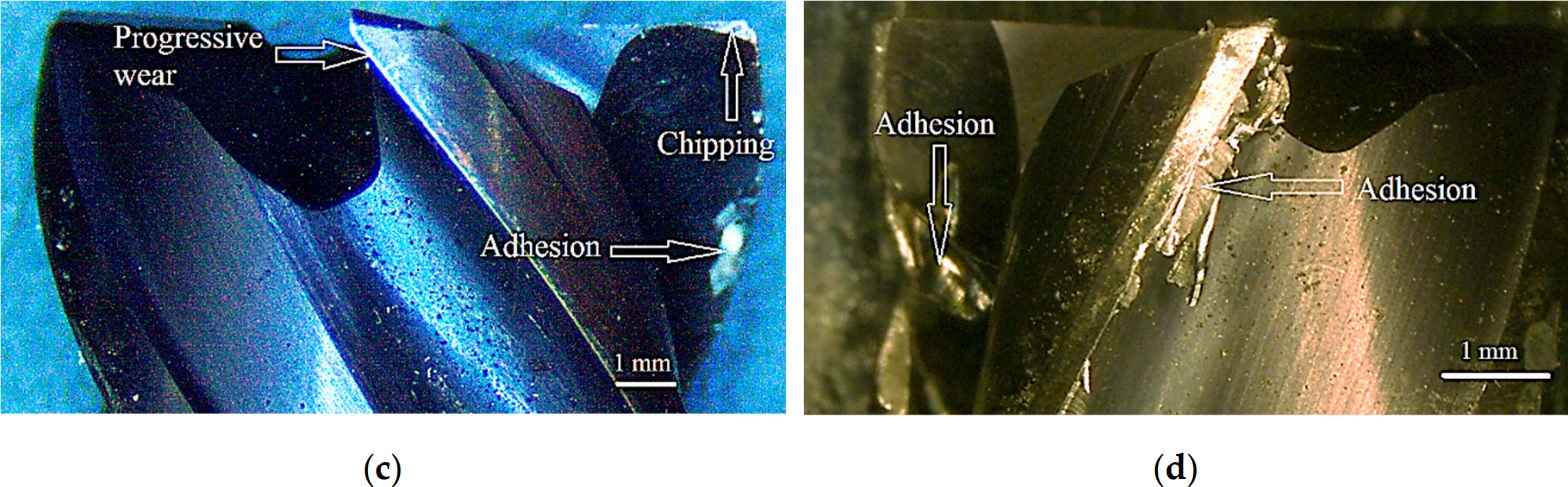
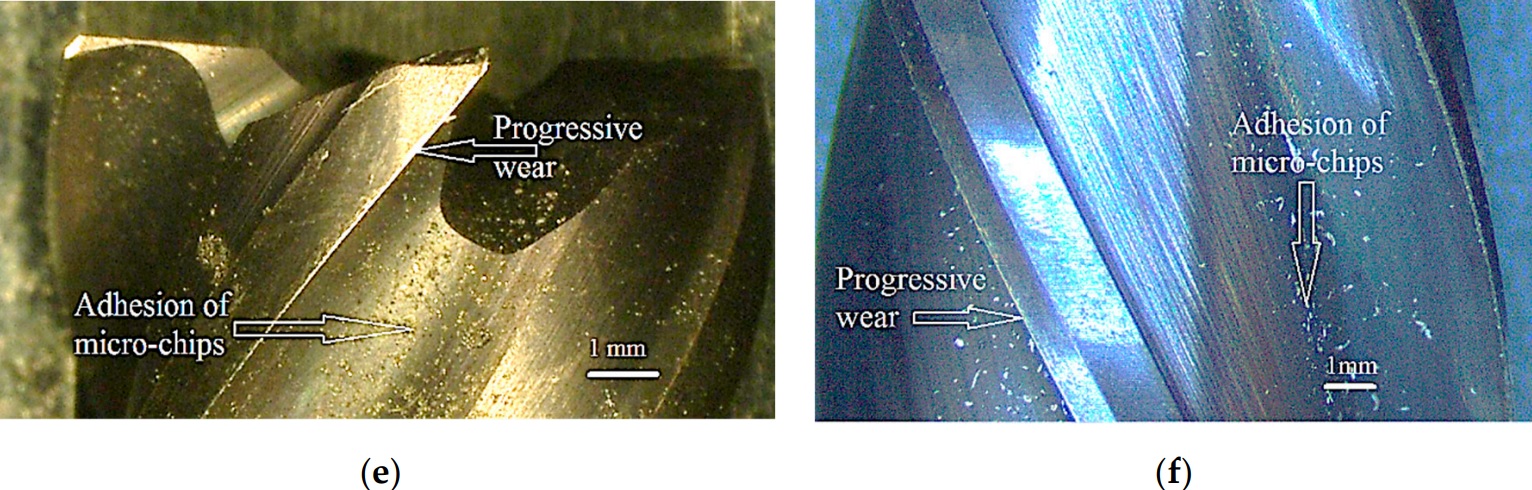
圖5. 顯示以下運行中使用的銑刀齒所產生的損傷模式的顯微圖。 (a) CO2,42◦,上銑,175 m/min;(b) CO2,42◦,下銑,175 m/min;(c) LN2,42◦,下銑,175 m/min;(d) LN2,30◦,上銑,100 m/min;(e) MQL,42◦,上銑,100 m/min;(f) MQL,30◦,下銑,100 m/min。
由於在上銑過程中,切削刃以最小的厚度進入工件,以最大的厚度離開工件,因此,在高溫的影響下,被去除的切屑仍然黏附在銑刀上。而低溫流體提供的快速冷卻可以加強切屑或部分切屑與邊緣和相鄰面的附著力。此外,從圖5e,f中可以看出,所有涉及到微潤滑的切削都產生了位於凹槽內的銑刀表面和遠離切削邊緣的微切屑的附著力。被去除的材料中的微小顆粒很容易被凹槽的油性表面吸附,即使在高轉速銑刀的高離心力作用下也會被黏住。在所有的六張圖片中,都可以明顯地看到機械磨損,其形式為接近切削刃的亮線。
圖中可以推斷出的關於磨損嚴重程度對實驗中控制的各種預測因素的依賴性信息不多。據報導,在使用塗層和非塗層銑刀的Ti-6Al-4V的低溫或濕法銑削中,磨損不是決定磨損的機制,而不論冷卻液的選擇如何。在不超過三把銑刀上觀察到了磨損。其中一個如圖5c所示。所有這些銑刀都是在高切削速度(175 m/min)下進行銑削。此外,在這三種情況下,崩裂都發生在相關刃角。在之前的其中一項切削加工中,有研究稱應用二氧化碳可以減緩崩解過程。通常由於低溫銑削的快速加熱和冷卻循環造成的切削刃的熱裂紋並不明顯,這可能是由於實驗運行中使用的切削長度很短。
3.2. 工件表面粗糙度
圖6顯示了24次實驗的Ra測量結果,按所使用的切削液類型分類。誤差條表示每個實驗運行測量數據的標準偏差。從圖中可以直接得出不少結論。就切削液的類型而言,微潤滑的表面光潔度明顯優於低溫液。此外,下銑加工比上銑加工效果更好。其他兩個預測因素的影響從圖中看並不明顯。對Ra數據進行了方差分析,以獲得更多的信息。分析表示,銑削方向是影響最大的預測因素,其次是切削速度和切削液。銑刀螺旋角的影響在統計學上不明顯。關於淬火工具鋼的銑削,報告顯示,螺旋角為45◦的銑刀表面粗糙度明顯低於30◦的銑刀。為了獲得良好的表面粗糙度,上銑顯然不是更好的選擇。如上一小節所述,切削刃使用上銑去除工件材料時,會產生大量的工件材料附著力。這種附著力會影響到切削刃的真實幾何形狀和鋒利度,從而導致表面粗糙度的產生。在工具鋼的銑削加工中,也有報告稱,下銑法在加工表面光潔度銑銷具有優越性。微量潤滑比兩種低溫冷卻劑的表面光潔度更好,這是相當令人驚訝的。就連續加工過程而言,許多論文報導使用低溫冷卻劑後,工件表面光潔度得到明顯改善。相反,在本研究中,低溫冷卻在銑削加工過程中產生了較差的加工表面質量。此觀察結果的合理解釋是,銑削是一個間斷的加工過程,在這個過程中,切削刃會定期與工件嚙合和脫離。每刃的嚙合都會導致齒的溫度升高,新產生的工作表面也會隨之升高。由於溫度的升高,加工表面往往會膨脹,但當銑刀在進給銑銷區域時,會立即受到低溫流體的衝擊。超冷流體的衝擊立即降低了溫度,使表面進入收縮模式。這種強烈的熱效應對新切削的表面產生了強烈的熱效應,使其進入突然的膨脹和收縮模式,導致表面質量下降。此研究在Ti-6Al-4V的銑削加工中應用石墨烯分散的植物油基微潤滑,使加工表面粗糙度降低了25%。研究發現,當銑削方向為下銑時,切削速度的提高可降低表面粗糙度。其對上銑時Ra的影響尚不清楚。在銑削硬化鋼(AISI D2)時,提高切削速度也能降低工作表面粗糙度。
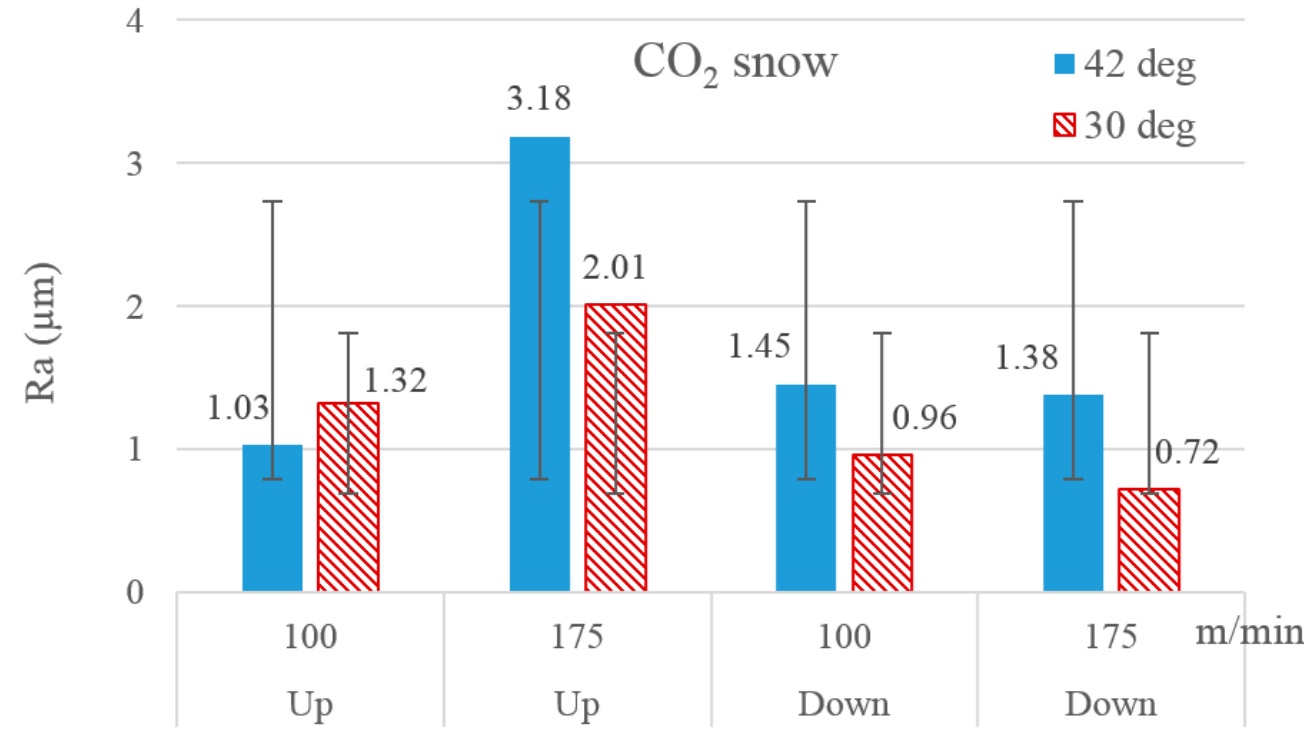
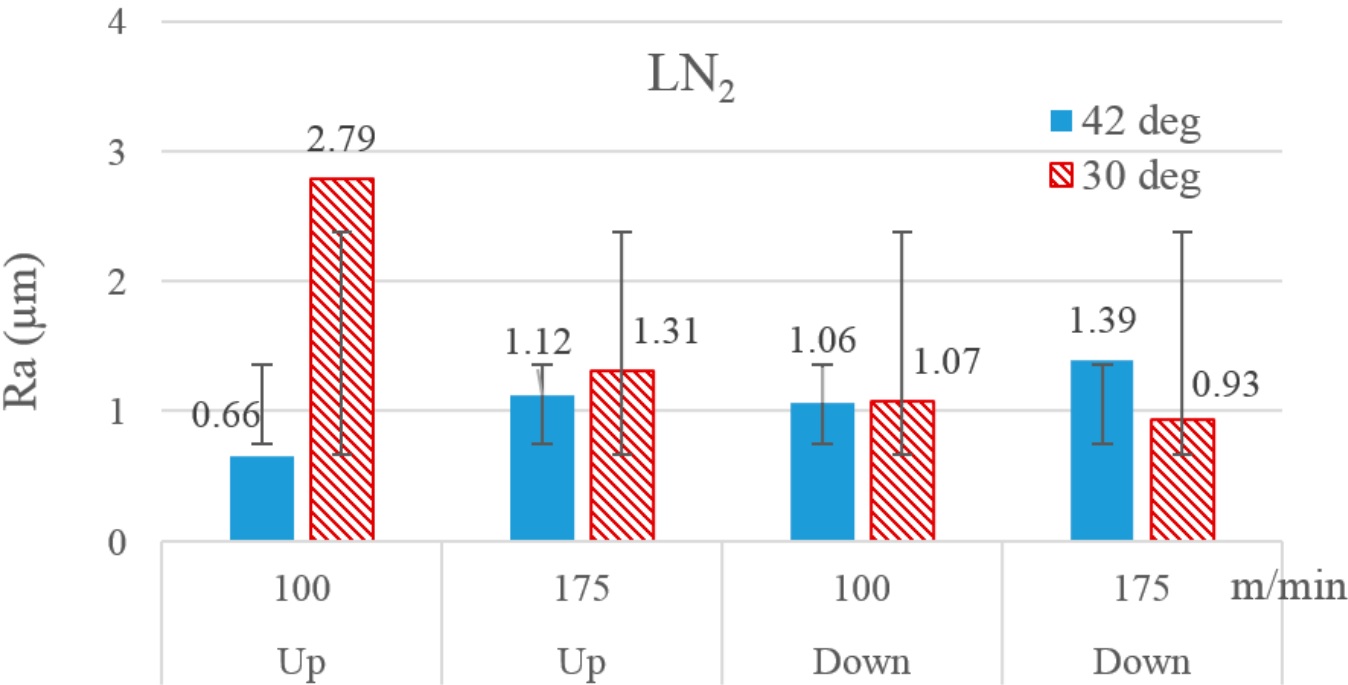
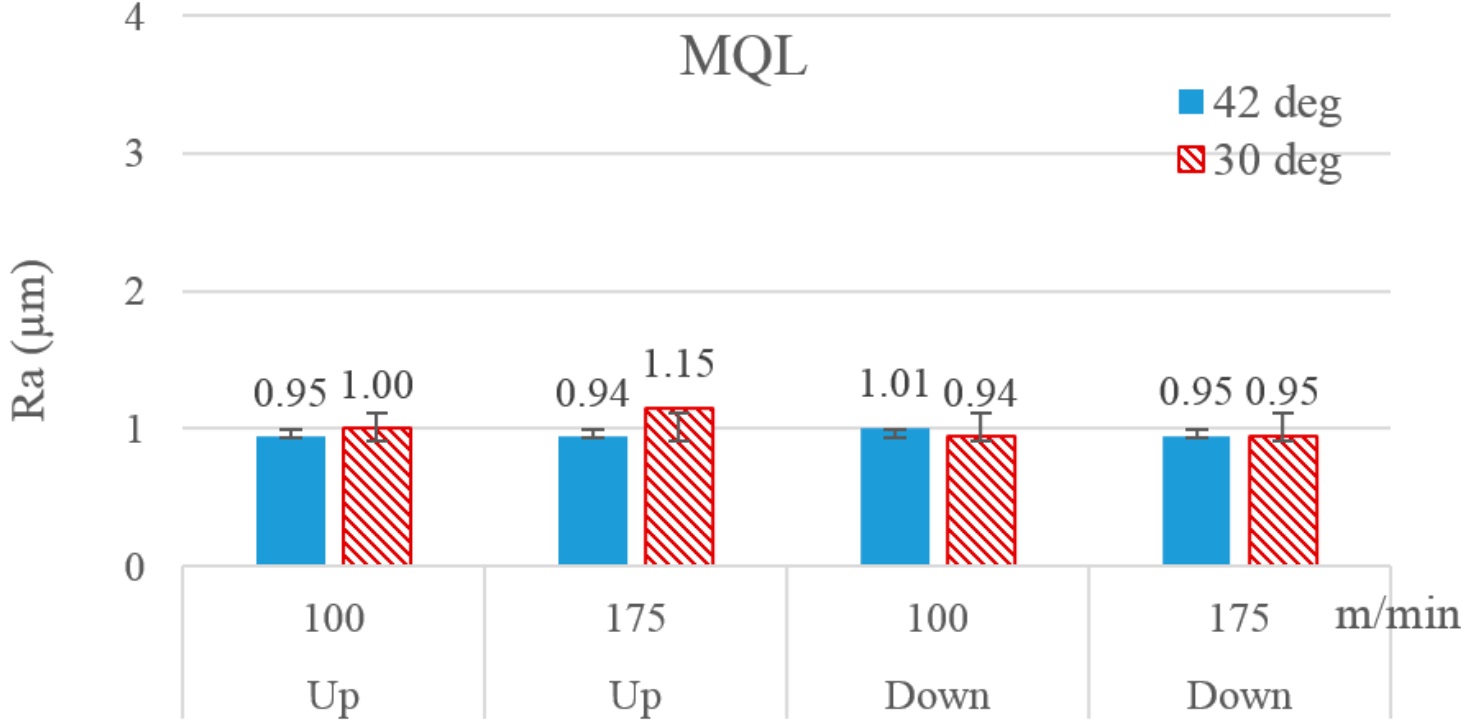
圖6.條形圖顯示了24次運行的算術平均表面粗糙度實驗結果。
圖7顯示了選定的實驗運行完成後得到的四個銑削表面的紋理。很明顯,通過上銑產生的表面(圖7a,b)由於微切屑的黏附而損壞了表面。這種黏附造成了工件表面的嚴重惡化。圖7a顯示了在24道工序中產生的最粗糙的表面。所有採用積雪CO2和上銑的組合工藝的試樣都在銑削後的表面上產生了嚴重的微切屑黏附。
圖7c,d沒有顯示出任何黏附跡象,因為此兩張圖都採用下銑方向運行。應當指出,在所有圖像中,紋理上的垂直線圖案都是一樣的。這是因為所有的運行都是以固定的每齒進給量值進行的。圖7b顯示了一條白色水平線貫穿生成的表面。這條線是由銑刀四個凹槽的碎屑部分產生的,在運行的第一道工序中可能遇到了堅硬材質。
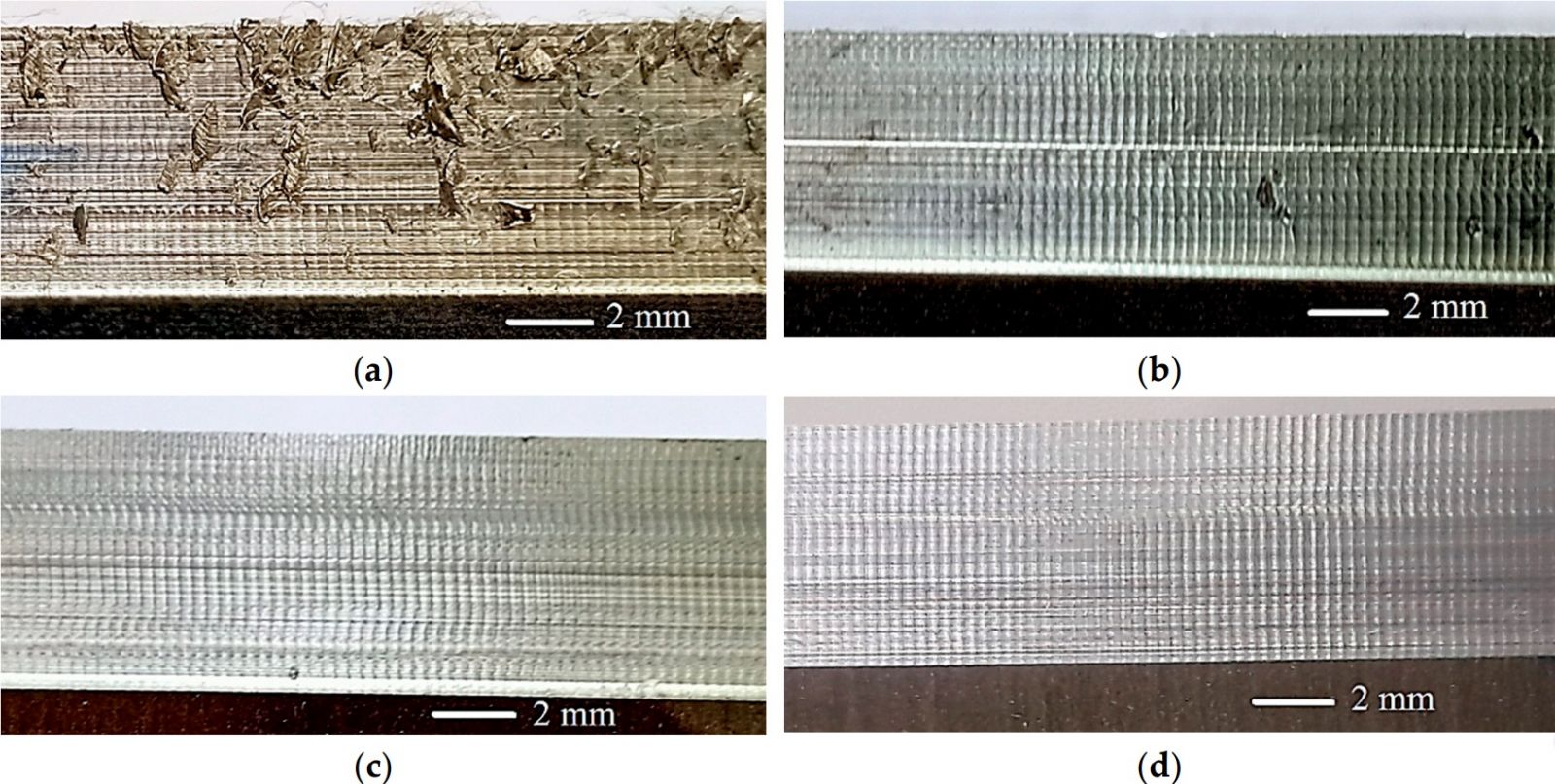
圖7.在完成以下運行後獲得的工作面紋理。(a) CO2,42°,上銑,175米/分鐘;(b) LN2,30°,上銑,175米/分鐘;(c) LN2,42°,下銑,100米/分鐘;(d) MQL,30°,下銑,100米/分鐘。
3.3. 特定切削能量和加工力
表2列出了24個實驗中的總電功率、切削和非切削功率的測量數據以及SCEs的評價。測量電功率的過程在2.3小節中已經詳細介紹過。圖8顯示了24次實驗的具體切削能量消耗的實驗結果。從圖中可以直接得出兩個結論。首先,螺旋角為42°的鎢鋼銑刀比螺旋角為30°的鎢鋼銑刀消耗的能量要少。其次,較高的切削速度導致了能量消耗的下降。對SCE數據進行方差分析,發現切削速度和銑刀螺旋角的影響在統計學上是極端的。發現切削液的影響略微顯著,而銑削方向的影響不顯著。切削速度的切削能量減少是由於金屬去除率的增加導致的,而切削功率消耗的增加則是由於切削速度的增加導致的。由於SCE是切削功率與金屬去除率的比值,因此,切削速度的增加會導致切削能量的減少。切削刃處的切削力(和能量)與切削功率,在切削時使工件發生塑性變形,轉化為切屑。切屑的形成是隨著加工切屑熱的產生而實現的。切削速度越高,產生的熱量就越大。據報導,加工過程熱能可以減少工件材料的流動應力,進而減少了去除相同體積材料所需的切削能量。這種現像被稱為熱軟化,這也是切削速度提高後,切削功率增加的原因。因此,切削速度越高,熱量比越低。據報告,在淬火工具鋼的側銑和端銑中,提高切削速度也能顯著降低能量比消耗。
表2. 關於機床總功率、非切削功率、切削功率、特定切削能量的測量和計算。 MRR-材料去除率。
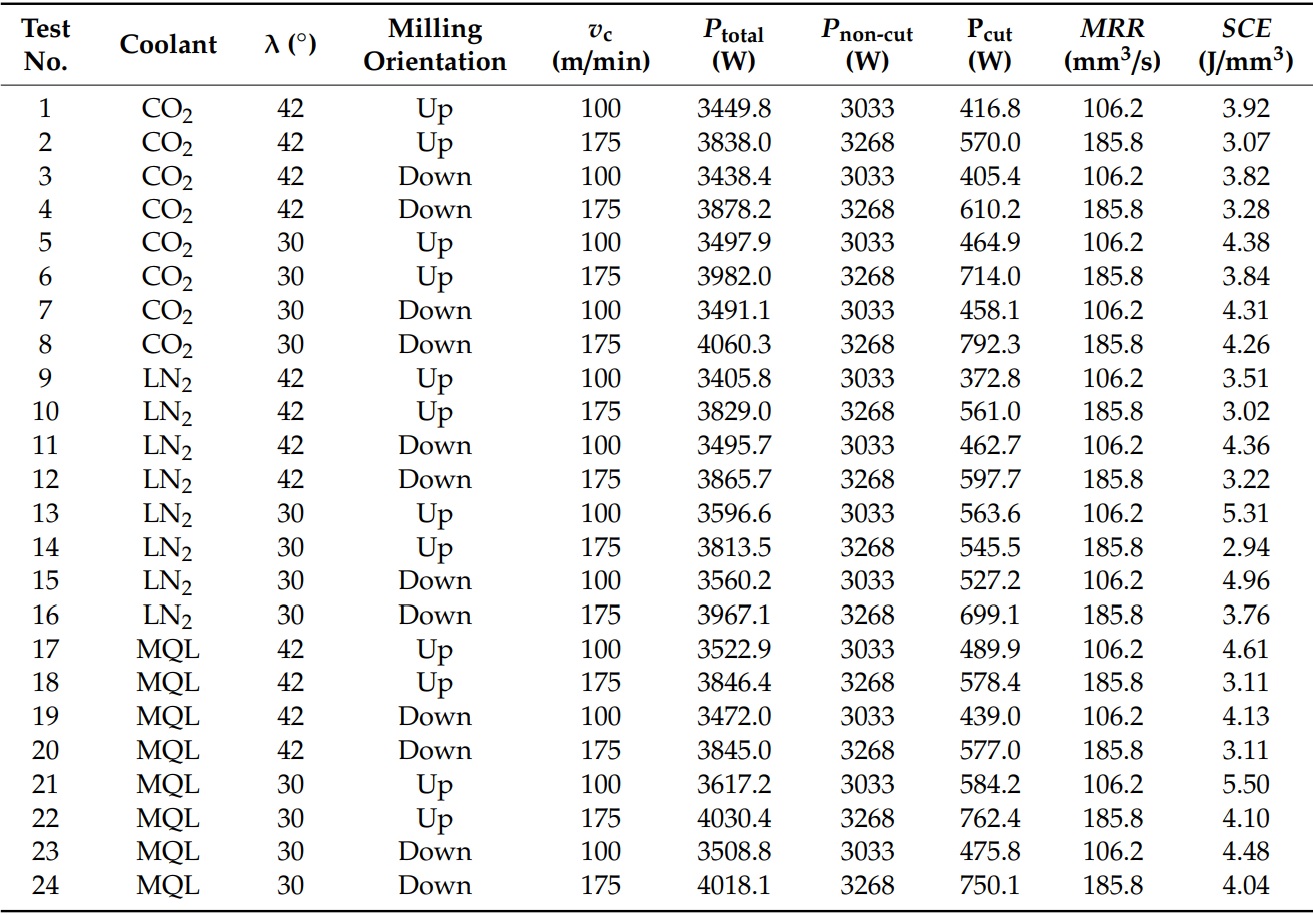
螺旋角較大的銑刀在切削加工材料時,軸向力分量與徑向力的比值較大。加工力的徑向力分量是造成銑刀震動和銑削過程中切削不穩定的原因。這種現像在加工難切削材料(如Ti-6Al-4V等)時就會變得更加突出。更強的震動和更高的不穩定性意味著在加工相同體積的材料時,需要消耗更多的能量。因此,較大的螺旋角會導致徑向力分量的比例降低,從而使銑削過程穩定,切削能量減少。
在三種切削液中,節流型低溫冷卻液(積雪CO2)在特定切削能量方面的效果最好,但差異不大,其次是蒸發型低溫冷卻液(LN2)。兩種低溫冷卻液都通過抑製銑刀的磨損進度而降低了切削能量的消耗。超冷液抑制了溫度依賴性的銑刀磨損模式,有助於在較長的時間內保持切削刃的幾何形狀。因此,保持鋒利的切削刃需要較小的切削力和較少的能量來切削既定體積的工件材料。在另一項加工銑削中,由於避免了冷卻液泵的額外功率,與Ti-6Al-4V的低溫銑削與濕式銑削相比,還發現它非常節省能量消耗。
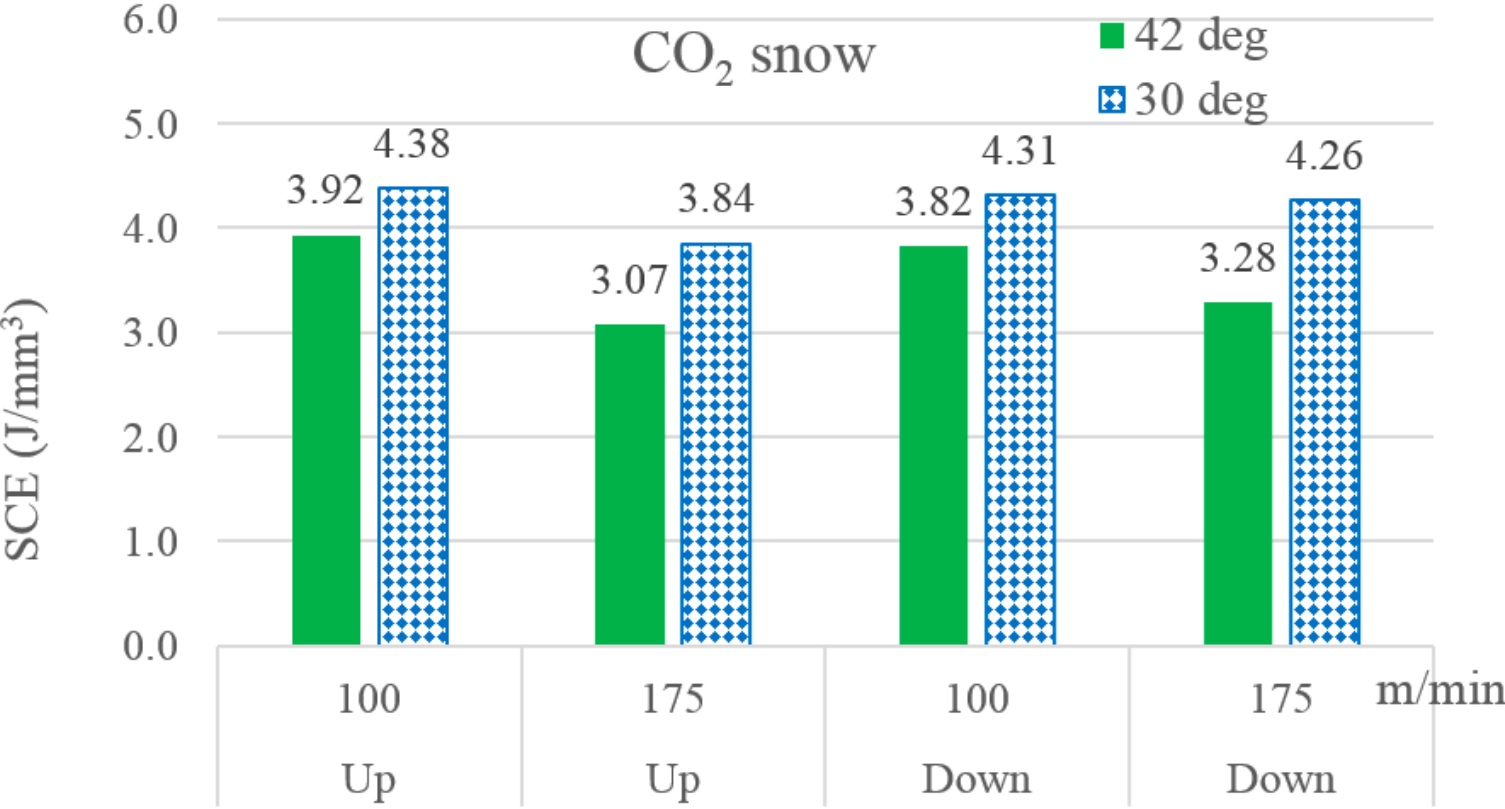
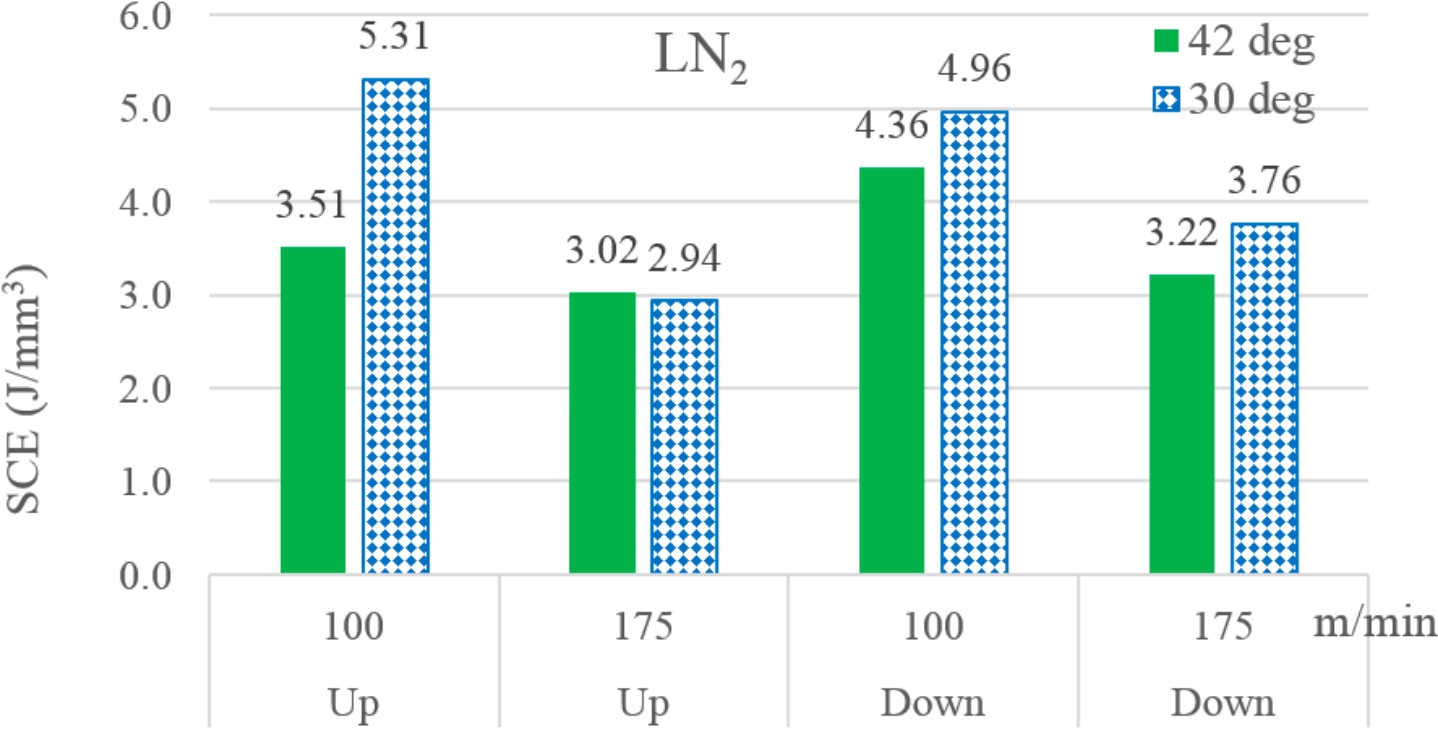
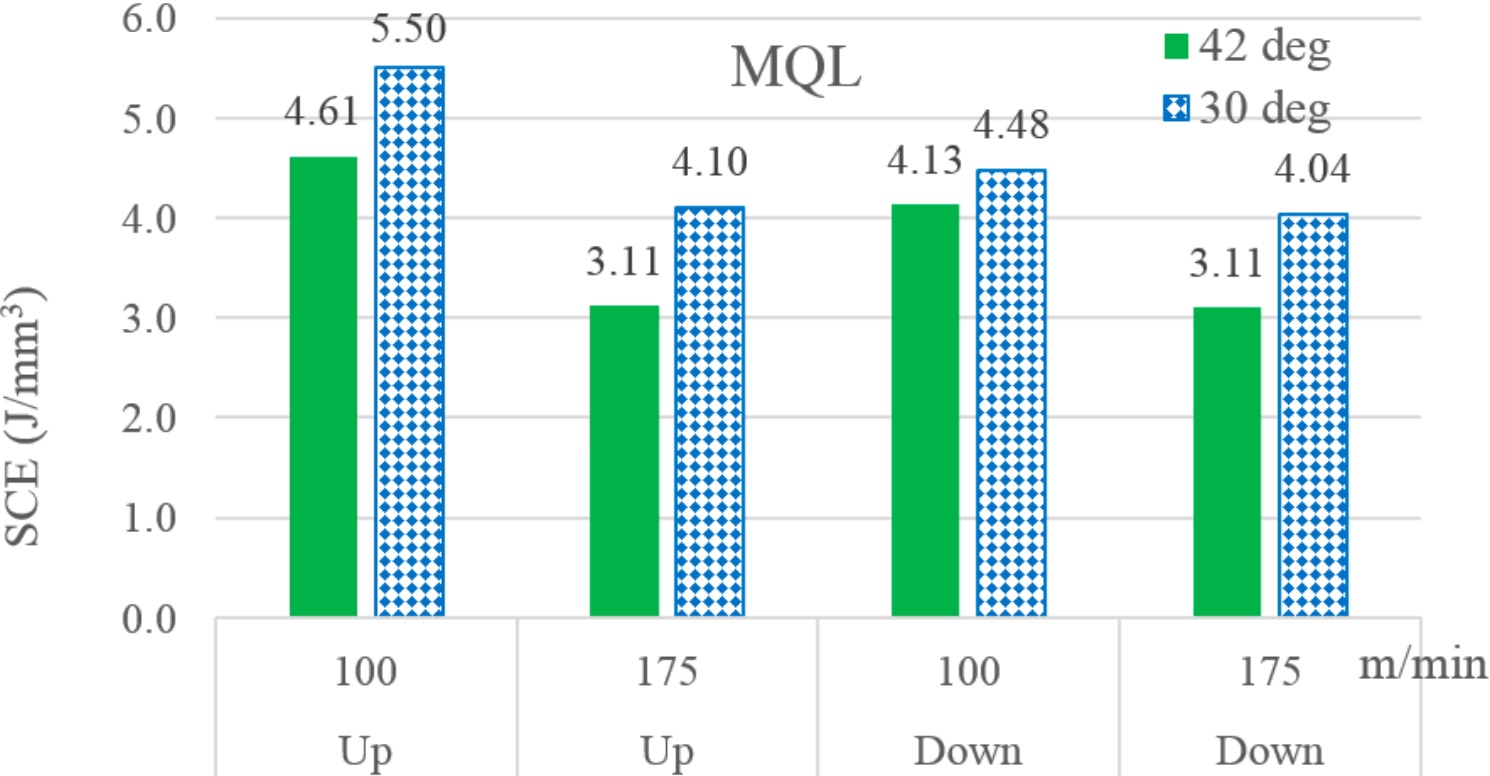
圖8.條形圖顯示了24次運行的SCE實驗結果。
從機械加工的持續性發展角度來看,需經常將單位質量的切削液液化、壓縮和輸送所需的相關能量納入SCE計算中。研究希望在此方面提出量化方法。在本研究中,作為冷卻劑的LN2的測量體積流量為0.5L/min。此外,在溫度為-195.8◦C時,液態氮的密度等於804 kg/m3。歐洲工業氣體協會(EIGA)報告稱,在0.1013兆帕的溫度下分離氮氣並在285K的溫度下液化,每噸氣體需要消耗約549千瓦時的電能。將這個數字換算成質量流速為0.402千克/分鐘的電能需求量,就可得到13.24千瓦。此外,在實驗加工中使用的儲氣槽在既定流量下抽送LN2需要額外消耗50瓦的功率。據報,擷取和壓縮二氧化碳氣體所消耗的電能在250-300千瓦時/噸的氣體範圍內。對於研究範圍的平均值,即275 Wh/kg,質量流量為0.5kg/min,供應和維持既定流量的CO2氣體所需的平均電能為8.25kW。最後,在0.6 MPa、30 mL/h、30 mL/h、0.4 L/s的氣壓、混油率和空氣流量下,驅動所使用的MQL系統所需的平均功率為418瓦特。有關計算的詳細情況,請參考文獻。將上述計算出的功率需求值相加後,積雪CO2、LN2、微潤滑的SCE值分別為57.6~82 J/mm3、74.5~131 J/mm3、5.2~8.3 J/mm3。顯然,SCE的修正值使三種切削液之間的比較變得微不足道,LN2以前所未有的優勢位居測試液的首位。
圖9顯示了從24次加工實驗中獲得加工切削力的三個組成部分的實驗數據。如前所述,Fx和Fz分別與進給方向和銑刀軸線對齊,而Fy垂直於工件的側表面。因此,可以說,銑削力的軸向分量是Fz,而徑向分量是其他兩個分量的結果。
從這三個圖中可以直接得出幾個推論。首先,螺旋角較大的銑刀切削力都較小。其次,當使用30◦螺旋角的銑刀以下銑方向高切削速度進行銑削時,所有三種切削液的Fx都異常上升。第三,在切削液的選擇方面,LN2的銑削力分量最小,其次是積雪CO2。採用方差分析來得到深入的結果。對所有3種切削力成分,銑刀的螺旋角是影響最大的預測因素。銑削方向和切削液的影響被發現有一定的顯著性,而切削速度的影響則不明顯。此外,發現切削液和銑削方向之間的交互效應僅對徑向切削工件有顯著影響。
螺旋角大的銑刀適合於動態穩定的銑削加工,加工深度小,有良好的工件表面質量。另一方面,螺旋角較小的銑刀適合於粗加工,有較高的金屬去除率。銑削的動態穩定性是由小量切削力來體現的。本研究的結果表示,42◦螺旋角比30◦螺旋角的銑刀的動態穩定性更好,這一點從關於銑削力分量的結果中得到應證。LN2在抑制切削力方面的有效性可歸因於其更有效的散熱能力。相信極低的工作溫度使其具有這樣的能力。更好的散熱機制有助於控製銑刀的磨損進度,進而有助於保持切削刃的幾何形狀和抑制加工力。在其他研究中,與乳化和低溫條件相比,混合低溫冷卻/潤滑在鈦合金加工中的加工力最低。銑削方向的影響不明顯。下銑削對積雪CO2和MQL產生的力分量較低,而對第三種流體產生的切削力分量較高。此外,在較高的切削速度下,上銑方向被發現是較好的切削方向。Li等人報導,當石墨烯分散的植物油基MQL應用於Ti-6Al-4V的銑削時,銑削力降低了18%。
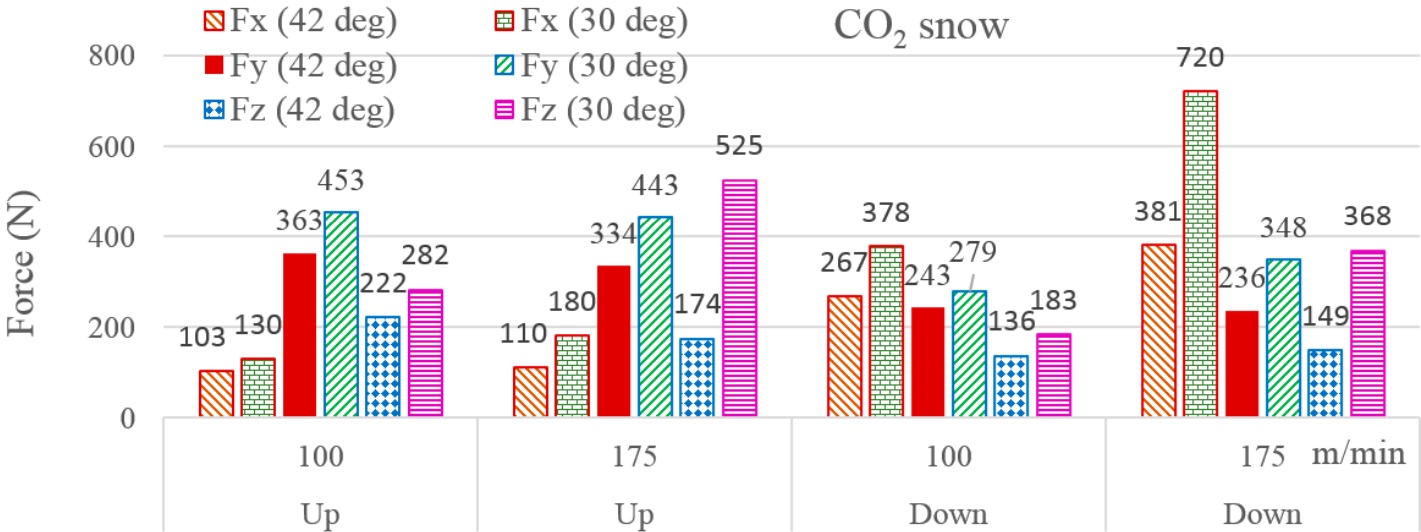
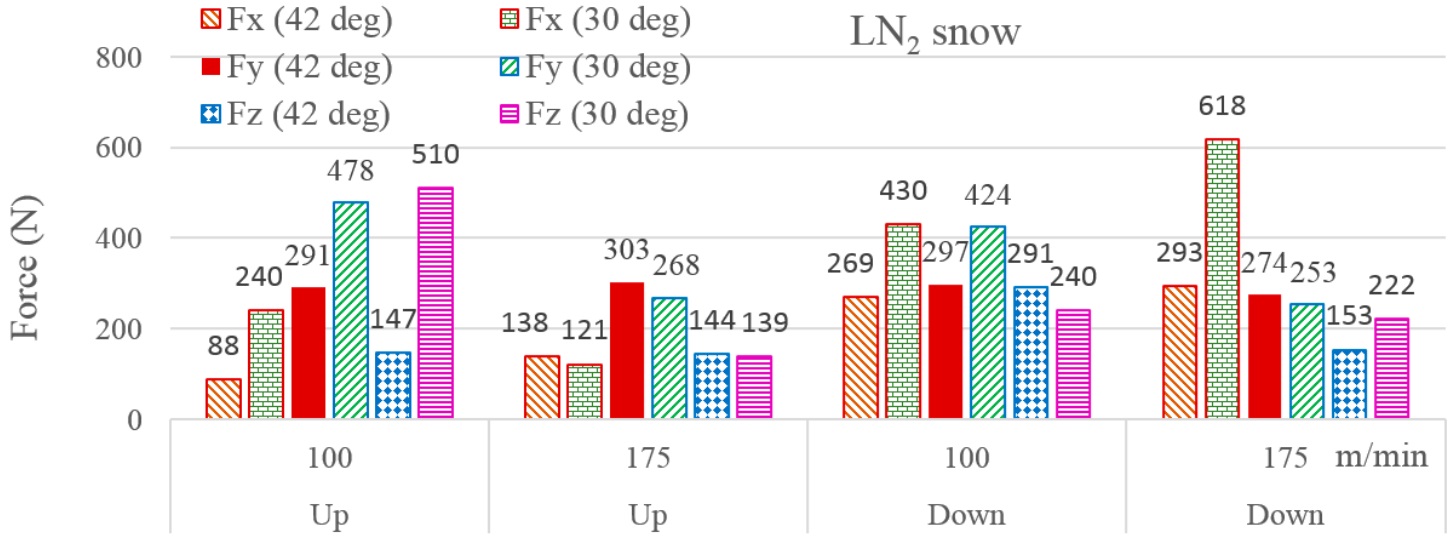
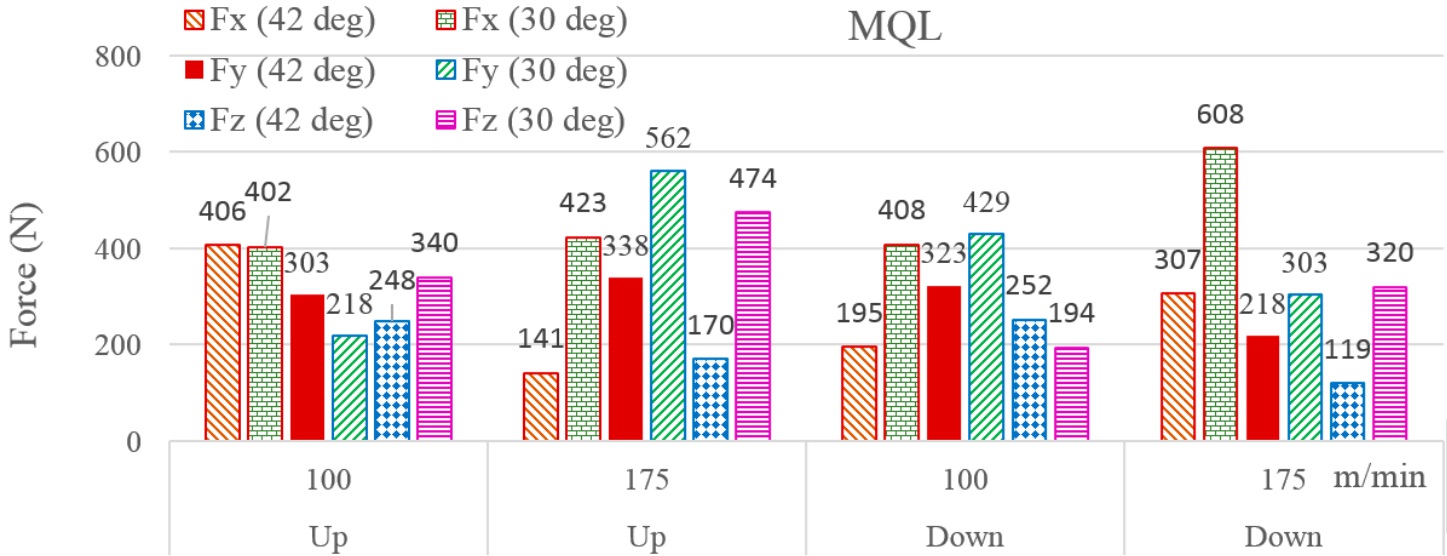
圖9.柱形圖顯示了24次運行時的三個分量(Fx、Fy和Fz)的實驗結果。
圖10顯示了所選實驗運行中三種切削力的進度隨時間的變化。在三張圖中的個別圖裡,可看到兩個集中區域,代表每個加工實驗運行的兩個切削槽。圖10a中的兩個區域比其他區域要薄,因為它們代表了在較高速度下進行的切削槽。根據進給方向,下銑和上銑的徑向力分量(Fx和Fy)分別位於正負區域。軸向力分量(Fz)位於負區域,與銑削方向無關。
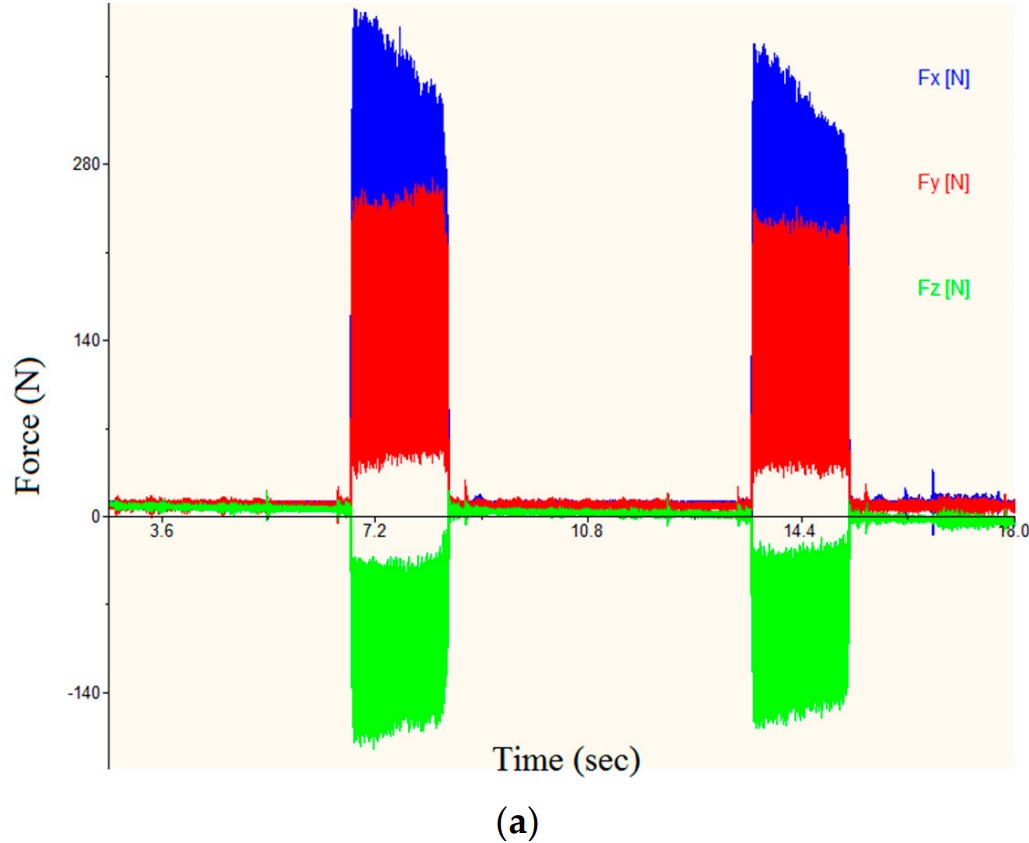
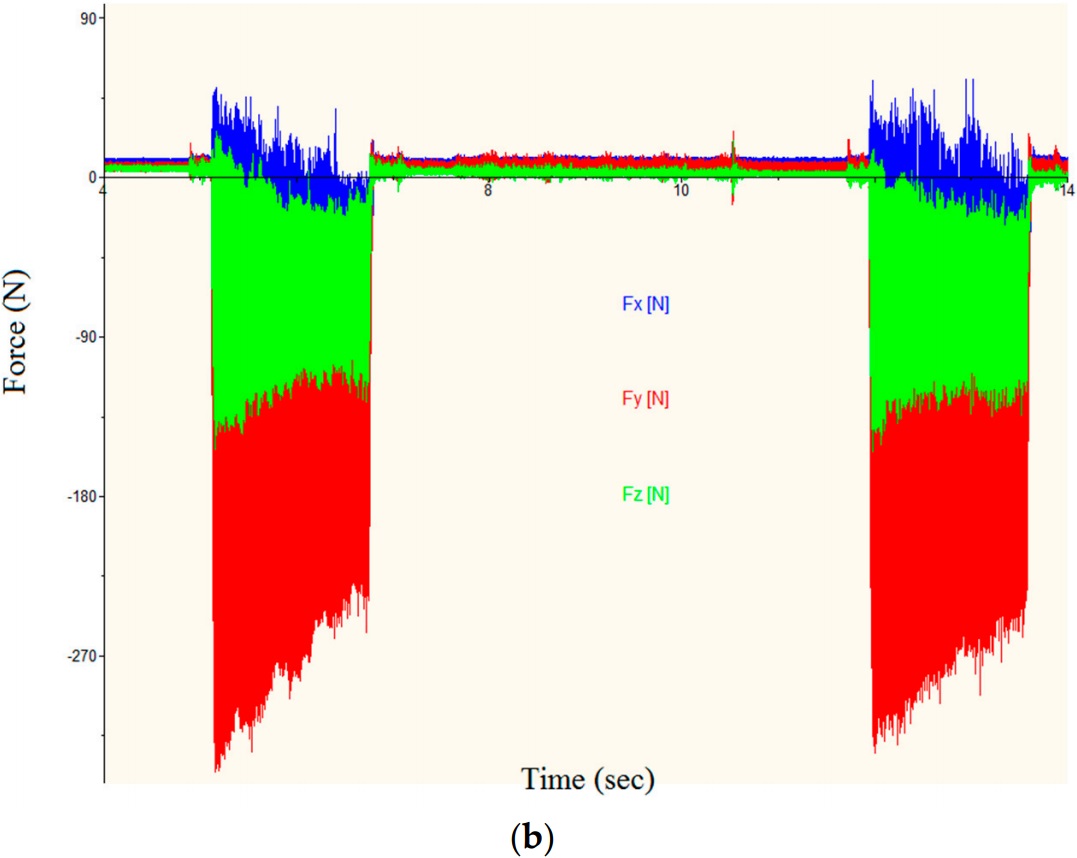
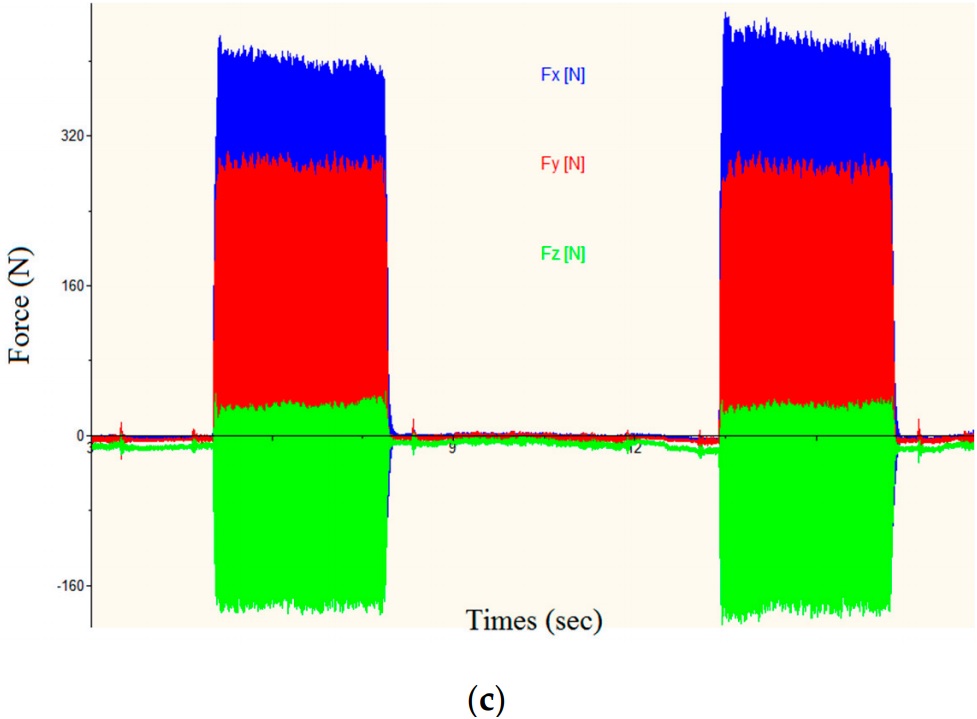
圖10. 在以下實驗運行中,銑削力成分隨時間的進展情況。(a) CO2,42◦,下銑,175米/分鐘;(b) LN2,30◦,上銑,100米/分鐘;(c) MQL,30◦,下銑,100米/分鐘。
圖中突顯低溫流體與微潤滑不同的一個現象。從圖10a,b可以看出,隨著切削過程的進行,切削力的瞬時值急劇下降。在第三張圖中,其量級保持相對穩定。這是由於工件材料的屈服強度/流動應力隨溫度不同而變化。如前所述,在第一道銑削工序開始前20s開啟低溫流體的供應。由於低溫流體同時也被工件接收,除銑刀外,表面溫度急劇下降,提高了材料的屈服強度。此後,隨著切削過程的開始,切削熱能提高了工作材料的溫度,從而降低了工件材料的流動應力。工件材料流動應力的下降反應在切削過程中,隨著切削過程的進行,受力成分減少。
將工件材料塑化成切屑所需的切削力在切削刃處的切削力是由切削力和切削速度的乘積(Pcut = vc × Fc)表示,其中Fc,在周向銑削中,Fc是三個正交力分量、銑刀幾何形狀和切削平面角的函數。也就是說,切削力應與測得的正交加工力成分呈正比。 Pcut與垂直於銑刀軸線的兩個力分量的結果(=[Fx 2 + Fy 2 ] 1/2)之間的相關係數為0.66。同樣,Pcut與所有三個力的結果(=[Fx 2 + Fy 2 + Fz 2 ] 1/2)之間的相關係數為0.68。這兩個相關係數表明,切削力和加工力之間存在較強的上銑關係。因此,可以肯定地說,加工力數據可以相當準確的估計出切削能量的消耗。
3.4. 工藝成本
在對24次實驗中的PC進行評估時,發現模具成本是最重要的貢獻因素,依次是切削液購置成本、間接費用、直接能耗成本和設備折舊成本。工藝成本的估算結果如圖11所示。從圖中可以清楚的看出,在測試的三種切削液中,微潤滑得到的結果是最經濟的,這是由於相關切削液的VB含量較低,單位成本和消耗率較低。在兩種低溫冷卻液中,當銑削為上銑時,積雪CO2的效果更好,而LN2在向下銑削時顯得更經濟。此外,由於相關的銑刀損傷程度較低,高螺旋角能產生較好的效果,尤其是在低溫冷卻環境下。最後,切削速度對加工成本的影響並不十分明顯,因為這一預測因素對PC的所有五種成分都有不同的影響。關於連續切削工藝,據報告,與傳統加工相比,高速加工Ti-6Al-4V的表面光潔度較好,而且比傳統加工消耗的能量更低,但在銑刀壽命和加工成本的可持續性措施方面表現不佳。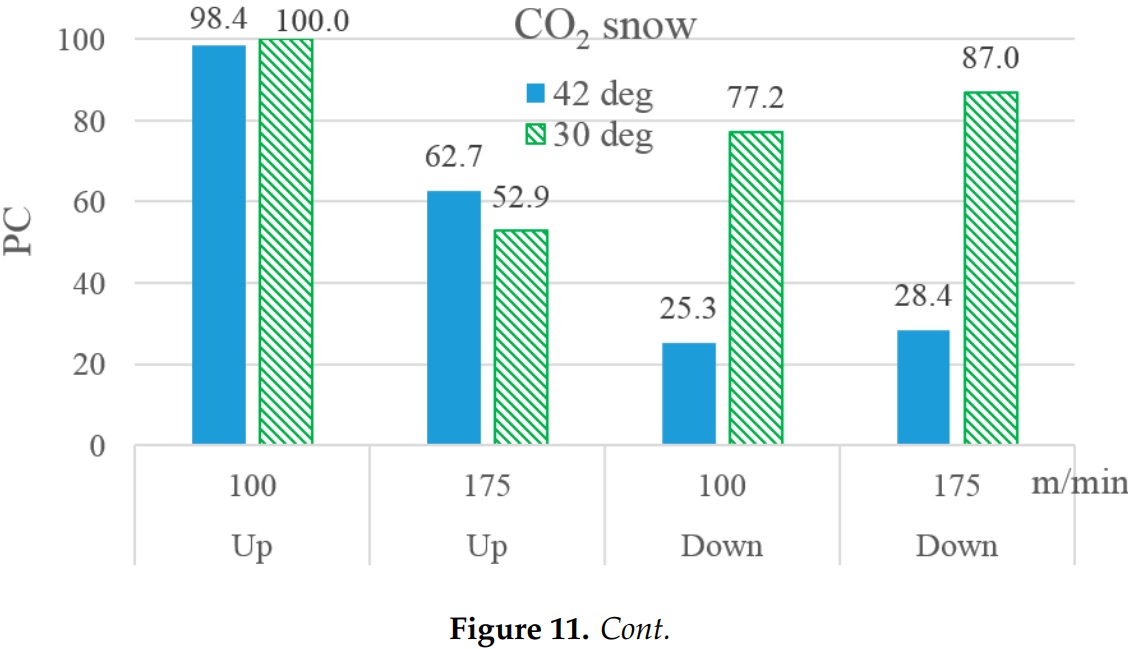
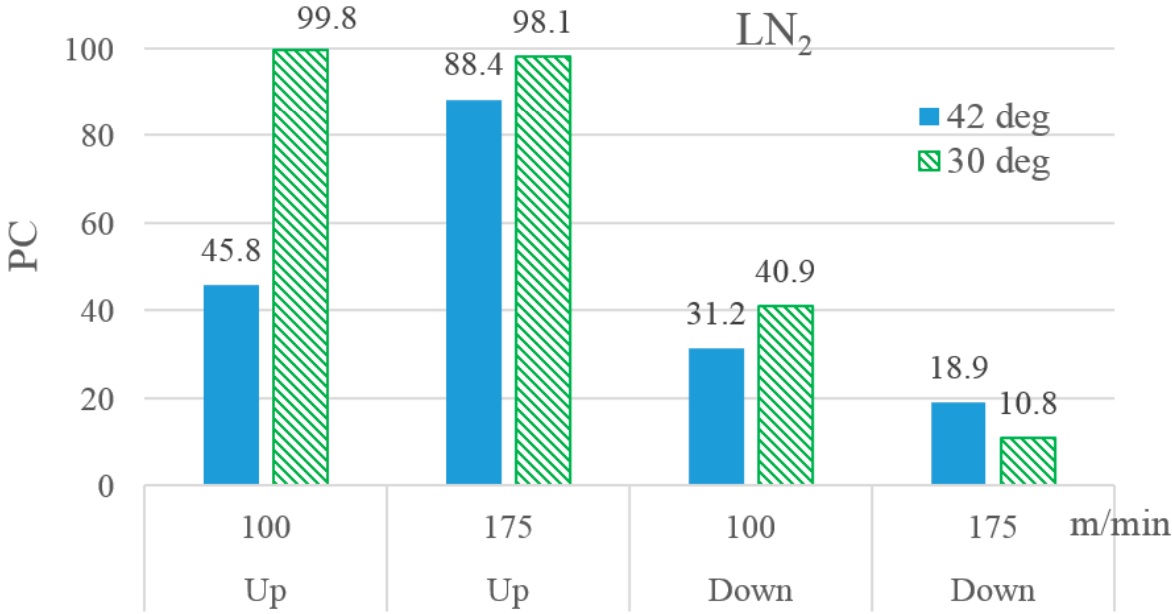
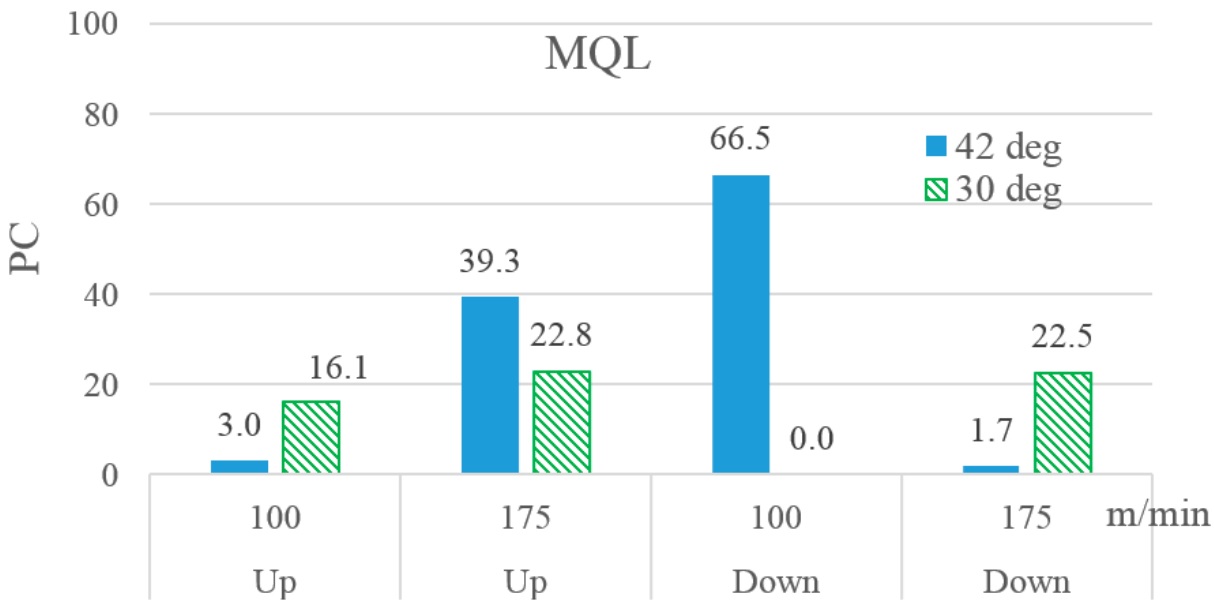
圖11.條形圖顯示了24次加工實驗的工藝成本。
4. 關於銑削的可持續發展的討論
上一節介紹了關於最常用的鈦合金加工重要可持續性指標的全面量化和分析。本節從可持續發展的三大支柱----經濟、社會和環境----的角度討論了實驗結果的意義。工藝成本是與可持續發展的經濟性相關的最重要的性能指標。如上一節所詳述,銑刀成本和切削液的取得成本是最重要的貢獻因素。銑刀成本受銑刀磨損(VB)的影響;數值越大,成本越高。另一方面,VB也受到切削液應用的影響。
關於PC的實驗結果表明,微潤滑與下銑的方法相結合,確保了Ti-6Al-4V的銑削最經濟,實現了最輕微的銑刀磨損。工件表面粗糙度對經濟性也有重要意義。可接受的表面粗糙度可以避免由於以下因素造成的經濟損失。
(1)因再加工造成的額外加工成本,以及(2)因再加工造成的額外材料和加工成本。在這方面,如3.2節所述,微潤滑和下銑加工再次作為理想的組合。機械加工可持續發展的社會層面是高度定性的。此支柱所涉及的因素有工人的安全、健康保護、工效學、支付公平、工作壓力和集約化等。
切削速度預計會影響到工效學和工作壓力,因為切削速度過低可能會增加機器操作人員的工作時間,並增加生產懈怠,導致工作壓力增加。切削液的選擇是另一個影響社會支柱的參數。在這項工作中測試的三種級別的切削液都需要額外的空間和工作量來設置和操作供液系統。在使用微潤滑和低溫液的銑削過程結束後,還需要進行少量的清洗工作。
微潤滑中輸送到加工區的油量很小,需要的清洗工作很容易。此外,常用的油是植物油,因此沒有危害性。將LN2應用到銑削區域,可使油液立即變成氣態,單純的置入環境中,不會對操作人員造成影響。同樣的,壓縮後的二氧化碳氣體在節流後會轉化為雪,逐漸昇華為氣態,並以氣態形式逸出。氣體的小流量(0.5公斤/分鐘)不會造成任何窒息危險。
銑削可持續發展的環境支柱是由特定的切削能量、銑刀損傷和廢料產生量來評估的。關於SCE的實驗結果表明,Ti-6Al-4V應採用中高螺旋角的銑刀進行高切削速度的銑削。此外,微潤滑的應用比低溫液更節能。高VB會導致更頻繁的更換銑刀,導致去除既定體積的工件材料所需的銑刀數量更多。因此,更多的能源消耗在廢舊銑刀的再製造/再循環上,或者更糟糕的情況下,需要更多的報廢銑刀提取原材料來製造新的銑刀。這種情況會加速自然資源的消耗,並對環境造成有害影響。通過對銑刀磨損數據的分析,鈦合金在加工時應採用下銑方向,並使用微潤滑進行銑削。關於加工廢品的產生問題,測試的銑削方向、銑刀的螺旋角、切削速度的高低並沒有什麼區別。
對於這三種預測因子的任何組合,產生的切屑總質量是相同的。另一方面,本研究中測試的三種切削液方案都比傳統的大量乳狀液冷卻方法要好。眾所周知,乳化液冷卻液會產生切屑,導致在切屑開始回收處理之前需要對切屑進行清洗。此外,乳化液需要過濾和泵送,以便反覆使用,直到因切屑、油底殼和暴露在空氣中的污染而變得有毒。低溫和MQL環境下的銑削不會產生任何切屑,因此,切屑保持清潔。此外,沒有溫室氣體排放,也不需要回收使用過的液體。關於LN2的選擇,氮氣對人體健康無害,對環境無害。此外,作為低溫冷卻劑,使用CO2氣體不會增加碳排放量,因為只用了少量的冷卻液。在使用天然金剛石銑刀加工鈦合金時,在泛冷劑的作用下,加工鈦合金的切削速度可達到200m/min。另一方面,目前的加工研究提出了鈦合金的可持續加工速度可達175米/分鐘,且使用更經濟的銑刀和環保型冷卻劑。
在上述討論的背景下,研究得出結論,就Ti-6Al-4V的側銑和端銑而言,微潤滑的應用比測試的兩種低溫流體更有利。在所有的可持續發展措施方面,即銑刀損傷、加工成本、工件表面質量和能源消耗(包括流體的能量),它的表現都明顯更好。並非所有先前發表的報告都聲稱低溫流體比傳統方法更優越。Isakson等人報告說,在鈦合金加工中,在LN2冷卻液下銑刀磨損的發展速度比在乳化冷卻液下快,但由於冷卻液的供應量有限,導致其性能不佳。此外,在目前的加工中,下銑方向在銑刀損傷、加工成本和加工表面質量方面明顯優於上銑方向。在其他兩個預測因素方面,高水平的銑刀螺旋角和切削速度通常會產生更好的結果,但觀察到的效果並不明顯。
5. 結論
本研究旨在量化和提高常用鈦合金在微潤滑和低溫冷卻環境下銑削的可持續性。低溫冷卻環境是通過應用節流式和蒸發式兩種冷卻劑,分別通過壓縮CO2氣體的膨脹和液氮的蒸發來實現。此外,還量化了採用兩種銑削方向和銑刀螺旋角和切削速度各兩級對可持續發展措施的影響。
這項工作最突出的發現是,在Ti-6Al-4V銑削加工中應用微潤滑比低溫冷卻劑更具有可持續性。最小潤滑量在銑刀磨損、工件表面質量、工藝成本和能耗方面均優於低溫冷卻劑。在銑削加工中,使用低溫冷卻劑的過程散熱效果不如車削等連續加工過程中那麼好。在超冷流體的作用下,切削過程中切削刃在工作中的周期性嚙合和脫離所造成的切削過程的間斷性,使低溫冷卻劑的效果大打折扣。在其他的預測因素中,銑削方向對鈦合金銑削的可持續性措施的影響非常明顯。在銑刀磨損、工件表面質量和加工成本方面,向下銑削比向上銑削要好很多。因此,強烈建議採用微潤滑和下銑相結合的方法對Ti-6Al-4V合金進行可持續銑削。
銑刀的螺旋角和切削速度對不同措施可持續性的影響是不一樣的,而且它們的作用力也不高。高級別的螺旋角對於降低特定的切削能量有很好的效果,對降低加工成本、銑刀磨損和銑削力也有很好的表現。同樣,高切削速度有利於降低工件表面粗糙度和具體切削能耗。
作者貢獻
A.I.構思和設計實驗,分析實驗結果,並撰寫部分論文;HS安排工具和工作材料;W.Z.和M.J.進行實驗;M.M.N.安排測量儀器,並進行可持續性分析;J.Z.繪製圖表,並撰寫部分論文。所有作者均已閱讀並同意稿件的出版版本。