考慮刀具和工件剛度特性的鈦合金薄壁零件的銑削穩定性研究
2020-05-15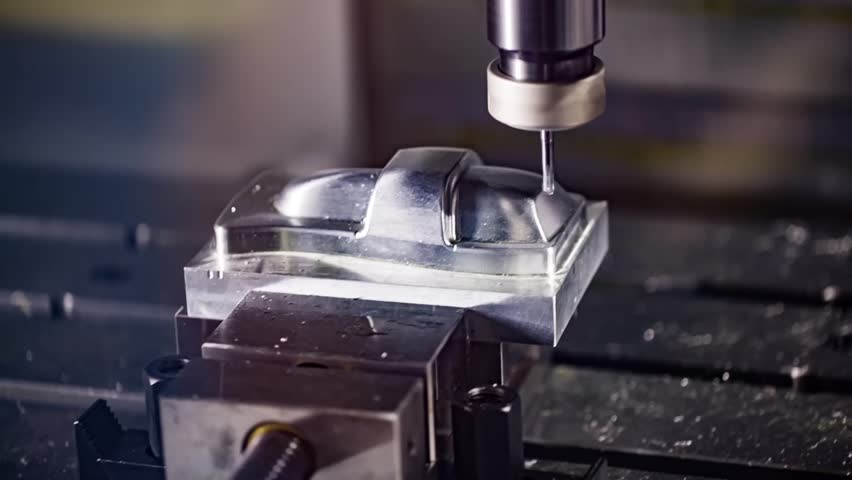
摘要
為了消除鈦合金薄壁零件在銑削過程中的顫動,考慮到刀具和工件的剛度特性,建立了銑削動態模型。分別進行了模態分析和銑削實驗,獲得系統動態性能參數和銑削力係數。繪製了不同剛度條件下的切削穩定性葉狀圖。結果表明,該模型是有效的,通過不同切削深度下的銑削實驗,驗證了葉狀圖的準確性。
1. 導言
現代飛機的性能不斷提高,所以在設計過程中,設計人員要利用整體式構件和薄壁結構來提高設備的性能,如整體式面板、框架殼、薄壁構件等。
儘管薄壁零件具有明顯的優勢,但由於工藝複雜,剛性差,在機械加工過程中,但其工藝複雜,剛性差,變形、震動嚴重,仍然是一個很大的問題。震動機制的概念最早是由F.W.Taylor在1907年提出的,此後,許多專家學者對震動機制進行了探討。建立了簡化過程系統的線性模型和考慮切削過程和機床結構的非線性因素的非線性模型。到目前為止,震動理論的發展有了很大的躍進,但研究還處於起步階段。顫振理論的指導作用在實際生產中起著微弱的作用,有待於進一步研究。傳統條件下建立的理論模型由於剛性較差,不能應用於薄壁零件,對於薄壁零件的工藝穩定性較難保證。
Altinas分析了各種銑刀在軸向、切向和徑向的切削力引起的動態位移,並建立了考慮到各方向切削力對工藝穩定性的影響的動態模型。Budak和Altintas在動態模型的基礎上,研究了刀具結構參數、切削速度、切削深度和切削寬度等參數對切削穩定性的影響,並探討了不同加工條件下薄壁零件軸向動態穩定性的頻域仿真和實驗驗證。Gonzalo利用FE軟件對鋁合金薄壁零件的切削加工過程進行了模擬,以優化切削條件,提高加工精度和表面質量。Gonzalo一方面利用機械模型模擬了時域中的銑削過程,另一方面利用FE模型獲得了零件在不同加工階段的動態特性參數。Bravo提出了一種取機床結構和工件的動態行為的不穩定性或穩定性裂片的獲取方法,並提出了覆蓋薄壁零件銑削過程中所有中間階段的三維裂片圖。
在本研究中,考慮到刀具和工件的剛度特性,提出了以薄壁零件為研究對象的顫動理論模型。根據模態試驗和切削實驗得到的必要參數,建立了不同剛度條件下使用立銑刀進行銑削加工的穩定性葉狀圖。並進行了不同切削深度的銑削實驗,以驗證葉面圖的準確性。
2. 加工穩定性理論
根據刀具剛度和工件剛度的匹配,將銑削動態模型應用於薄壁零件的切削過程,如圖1所示。該模型是在傳統模型的基礎上建立的,具有兩個自由度。從圖1中可以看出,在圖1中,假設銑刀有N個齒,考慮到銑刀有兩個自由度軸向(x方向和y方向)。工件的DOF與銑刀相同。
在x和y方向上的銑削系統模式被假定為非耦合,那麼得到的薄壁零件的動態方程式為
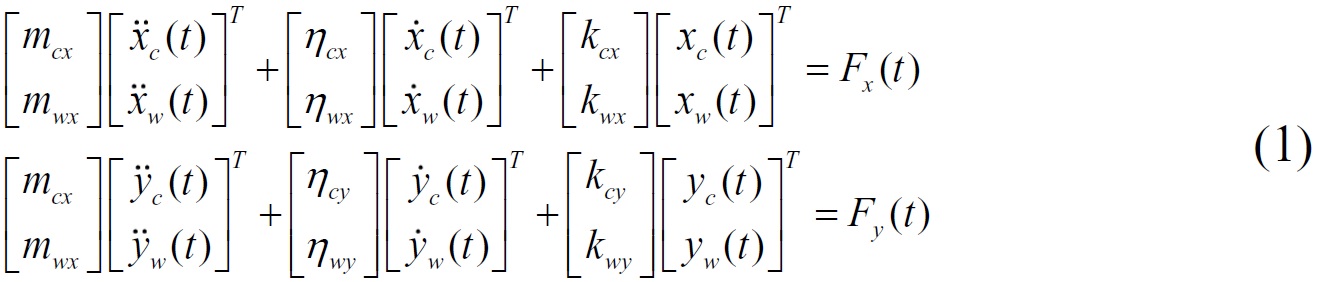
其中,mc和mw分別為刀具和工件的模型質量,ηc和ηw分別為刀具和工件的阻尼係數,kc和kw分別為刀具和工件的剛度。其中,Fx(t)和Fy(t)分別為銑削時間為t時,在x、y方向上的切削力。
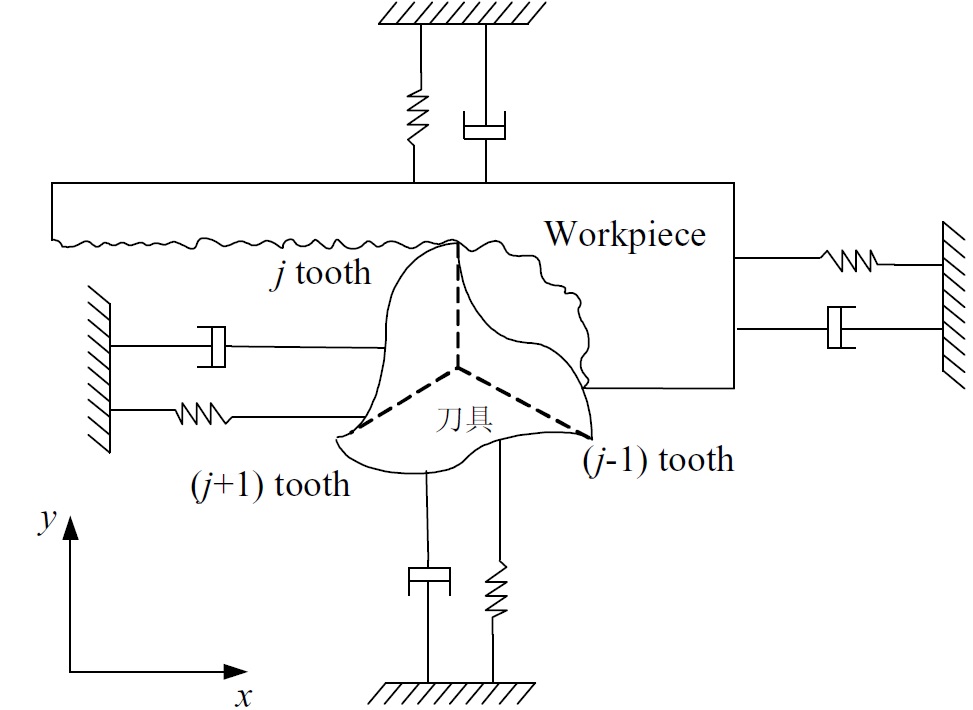
圖1. 基於刀具剛度與工件剛度匹配的銑削動態模型
2.1. 動態切屑厚度
j 齒切削時的動態切屑厚度可通過現前齒與前齒的位移差來計算,如式(2)所示。

其中 Øj 是 j 齒的瞬時接觸角,從正向線到 y 軸的順時針方向測量。當主軸以棱角速度 ω 旋轉時,接觸角隨時間變化為 Øj = (j-1) Øp +ωt。其中 Øp 為齒距角 Øp = 2π/ N。

其中 Øj 是 j 齒的瞬時接觸角,從正向線到 y 軸的順時針方向測量。當主軸以棱角速度 ω 旋轉時,接觸角隨時間變化為 Øj = (j-1) Øp +ωt。其中 Øp 為齒距角 Øp = 2π/ N。
2.2. 動態切削力
切向切削力 Ftj 和徑向切削力 Frj 與切削深度 ap 和切削厚度 h 成正比。

其中,切削力係數 Kr 和 Kt 為常數。所有的切削力單位在 x、y 方向上進行分解並相加。切削力之和用矩陣形式表示,如表(4)所示。
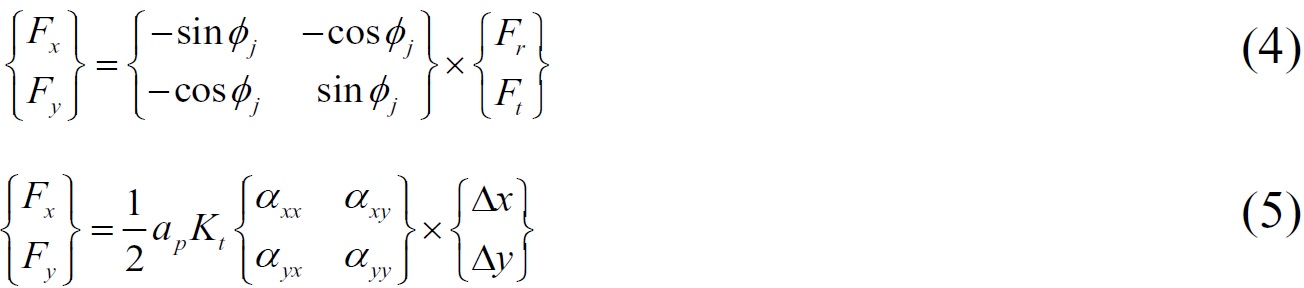
其中 αxx, αxy, αyx, αyy 是隨時間變化的動態銑削力係數。
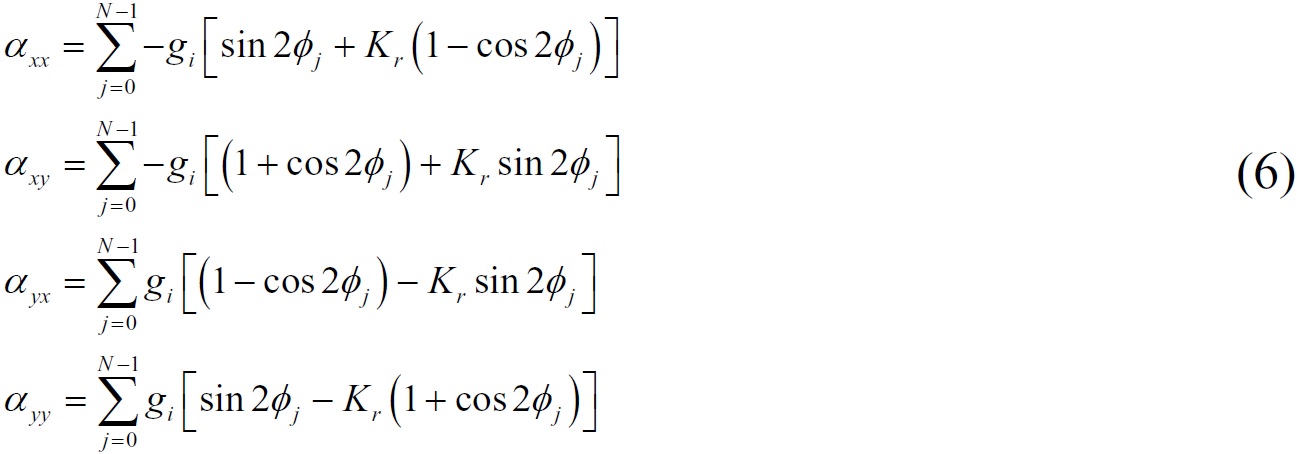
動態銑削力係數隨時間和棱角速度的變化而發生變化,因此在時域中可以用矩陣形式來表示,如式(6)所示。


其中,切削力係數 Kr 和 Kt 為常數。所有的切削力單位在 x、y 方向上進行分解並相加。切削力之和用矩陣形式表示,如表(4)所示。
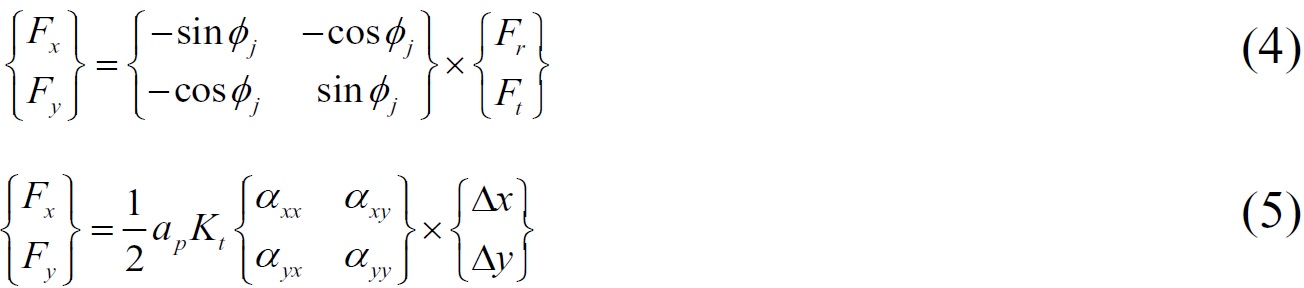
其中 αxx, αxy, αyx, αyy 是隨時間變化的動態銑削力係數。
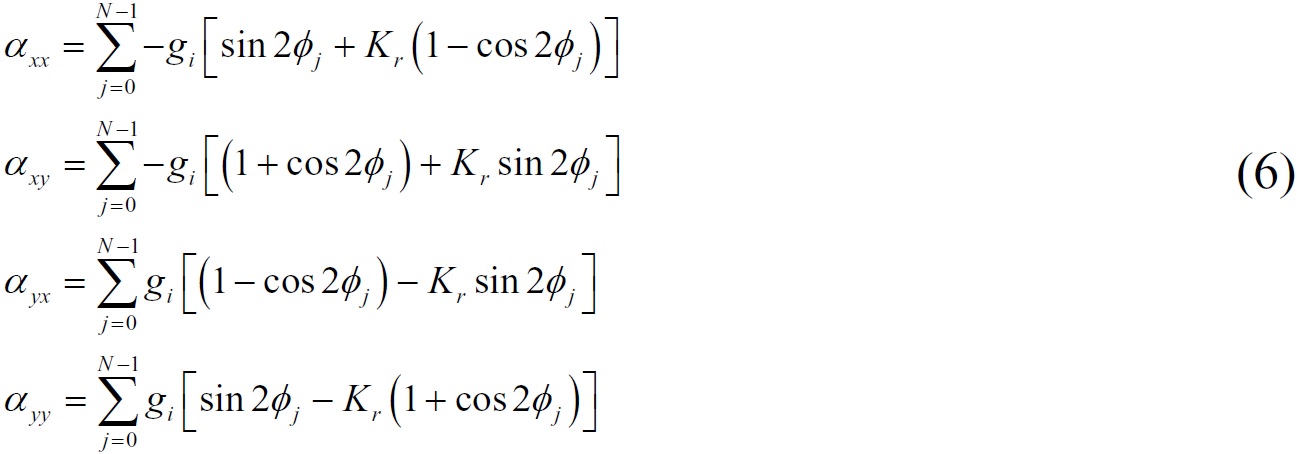
動態銑削力係數隨時間和棱角速度的變化而發生變化,因此在時域中可以用矩陣形式來表示,如式(6)所示。

2.3. 穩定切削的極限軸向深度
在切削週期 T 中產生的動態位移如式(8)所示。

其中 G(iωc) 為銑削系統包括刀具和工件的傳遞函數矩陣,即頻率響應函數。由式(7)可得公式(9)。 (9)可以通過將式(8)放入式(7)中得到。

由特徵方程可以得到系統的穩定性,並用行列式表示。

在顫振頻率 ωc 時,可以得到切削極限深度 Aplim 和相應的主軸轉速 N ,在顫振頻率 ωc 時,切割力係數、切入角、切入角、離去角和頻率響應函數均可得到。
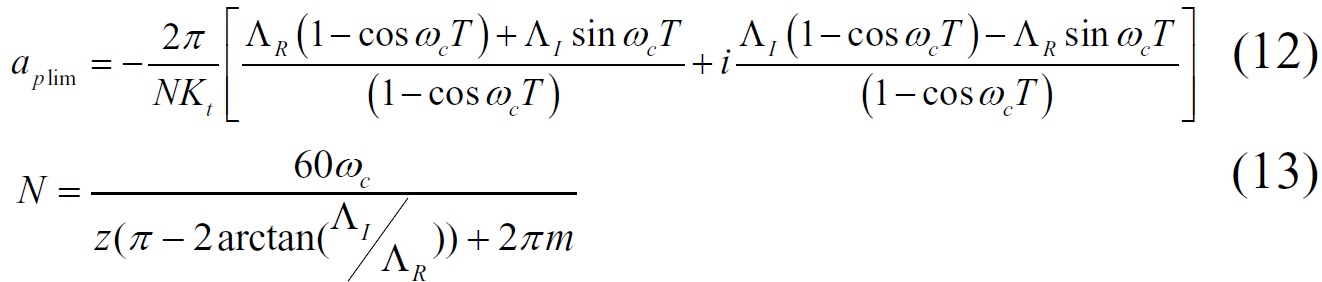
在實際切削過程中, aplim 必須是實數,所以公式(11)的虛數部分為零,則

在穩定切削的臨界條件下的極限軸向深度的表達式,可以通過將方程(16)放入方程(12)的實數部分得到。
.jpg)

其中 G(iωc) 為銑削系統包括刀具和工件的傳遞函數矩陣,即頻率響應函數。由式(7)可得公式(9)。 (9)可以通過將式(8)放入式(7)中得到。

由特徵方程可以得到系統的穩定性,並用行列式表示。

在顫振頻率 ωc 時,可以得到切削極限深度 Aplim 和相應的主軸轉速 N ,在顫振頻率 ωc 時,切割力係數、切入角、切入角、離去角和頻率響應函數均可得到。
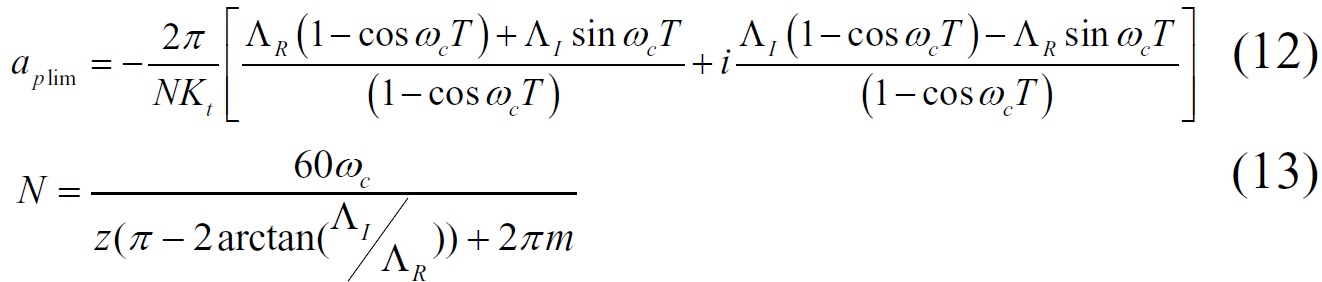
在實際切削過程中, aplim 必須是實數,所以公式(11)的虛數部分為零,則

在穩定切削的臨界條件下的極限軸向深度的表達式,可以通過將方程(16)放入方程(12)的實數部分得到。
.jpg)
3. 實驗和討論
3.1. 模態實驗的設計
通過模態測試儀器對不同剛度條件下的模態參數進行了測量。採用單點激勵和單點輸出,以激勵錘為激勵方式。刀具的動態特性測量結果如圖2所示。
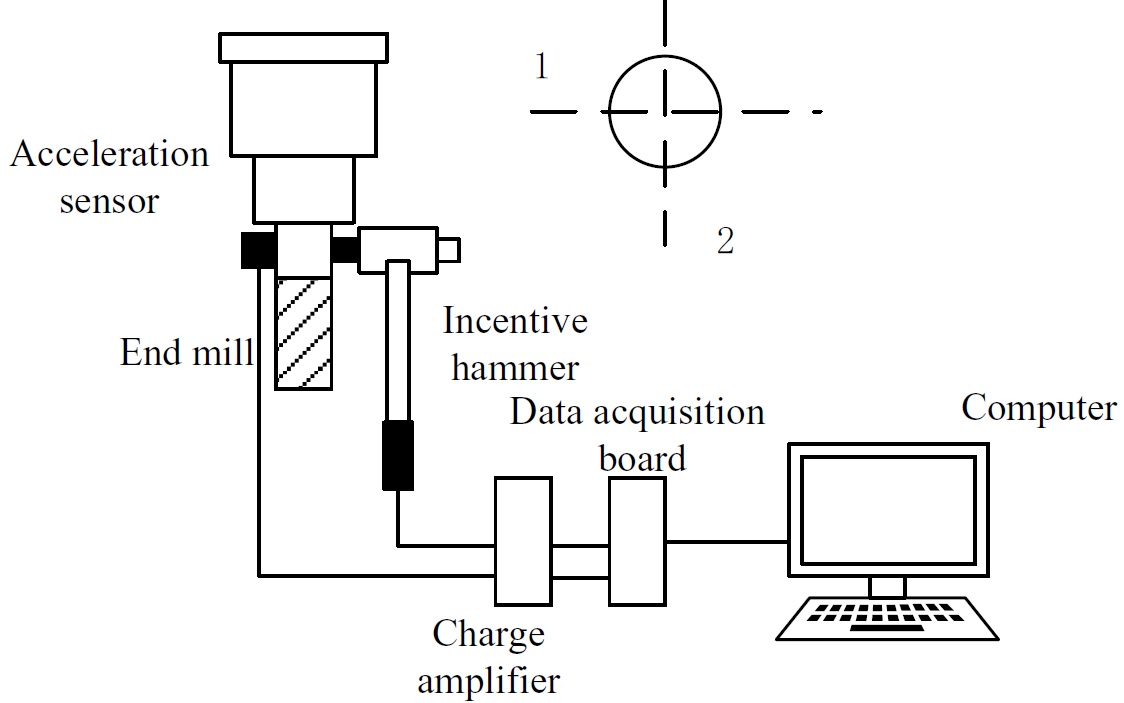
不同刀具剛度條件下的模態實驗如表1所示。模態實驗採用硬質合金立銑刀。刀具長度為112mm,最大裝夾長度為50mm,衝擊點與底邊之間的高度為52mm。利用銑削系統動態模型,採用兩個自由度的銑削系統動態模型,對刀具在x、y兩個方向上的動態特性進行了測量。
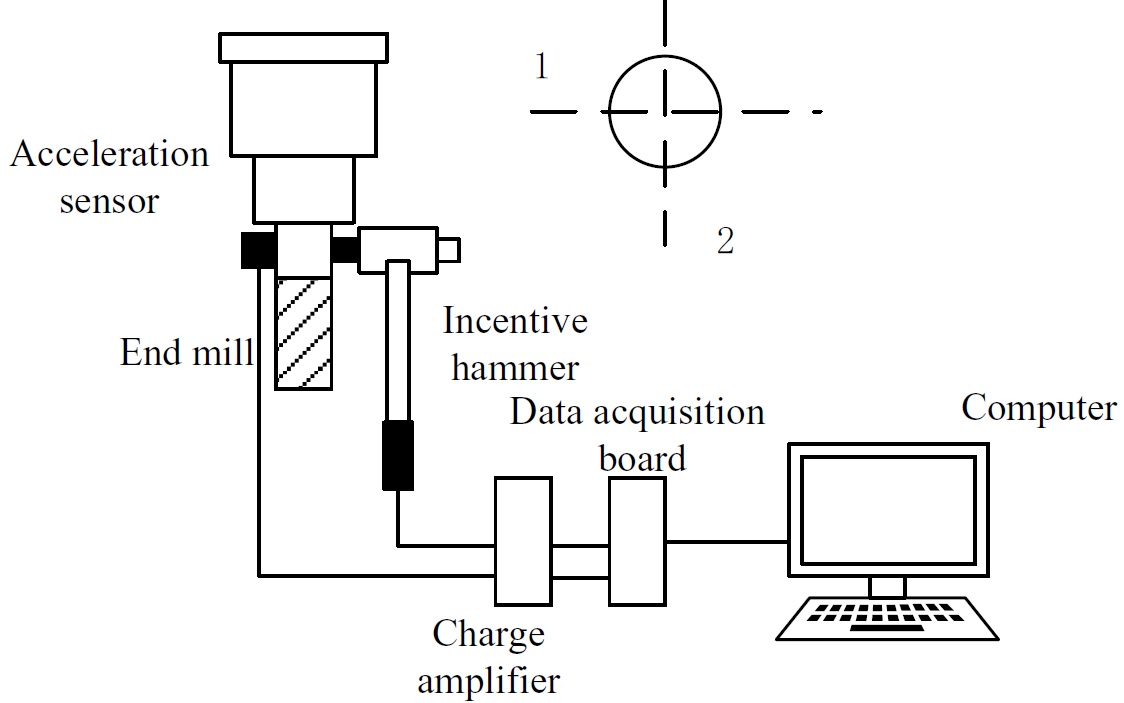
不同刀具剛度條件下的模態實驗如表1所示。模態實驗採用硬質合金立銑刀。刀具長度為112mm,最大裝夾長度為50mm,衝擊點與底邊之間的高度為52mm。利用銑削系統動態模型,採用兩個自由度的銑削系統動態模型,對刀具在x、y兩個方向上的動態特性進行了測量。
表1.不同刀具剛度條件下的模態實驗。不同工具剛度條件下的模態實驗。
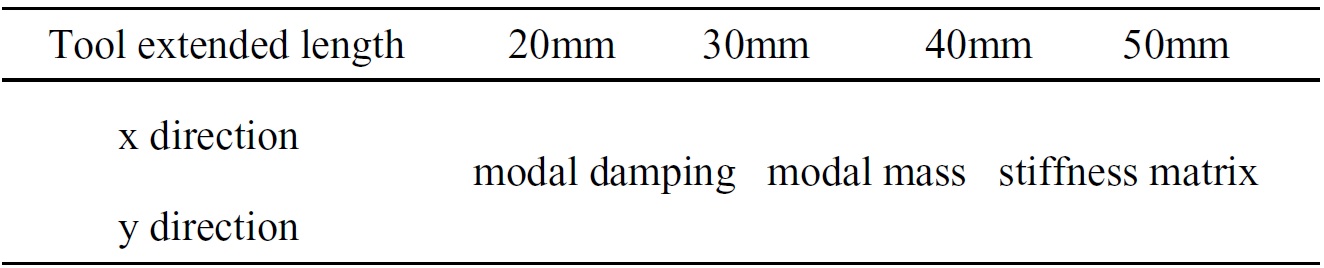
工件的模態實驗如圖3所示。
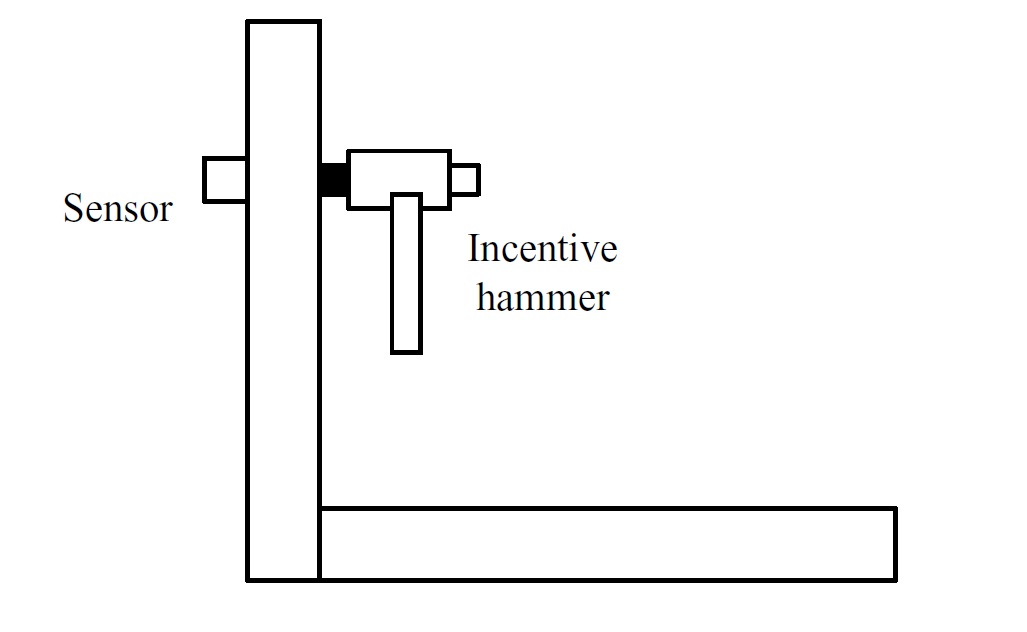
圖3 工件的模態實驗圖
為了研究不同的剛度對工件模態參數的影響,設計了兩個不同的零件。其中,壁板位於工件1的底部側端,稱為 L 型,如圖4所示。工件2的壁板位於底部中部,稱為 T 型,如圖5所示。每個工件的總長度為120mm,初始壁厚為20mm。工件的模態實驗參數如表3所示。
表2. 工件的模態實驗參數

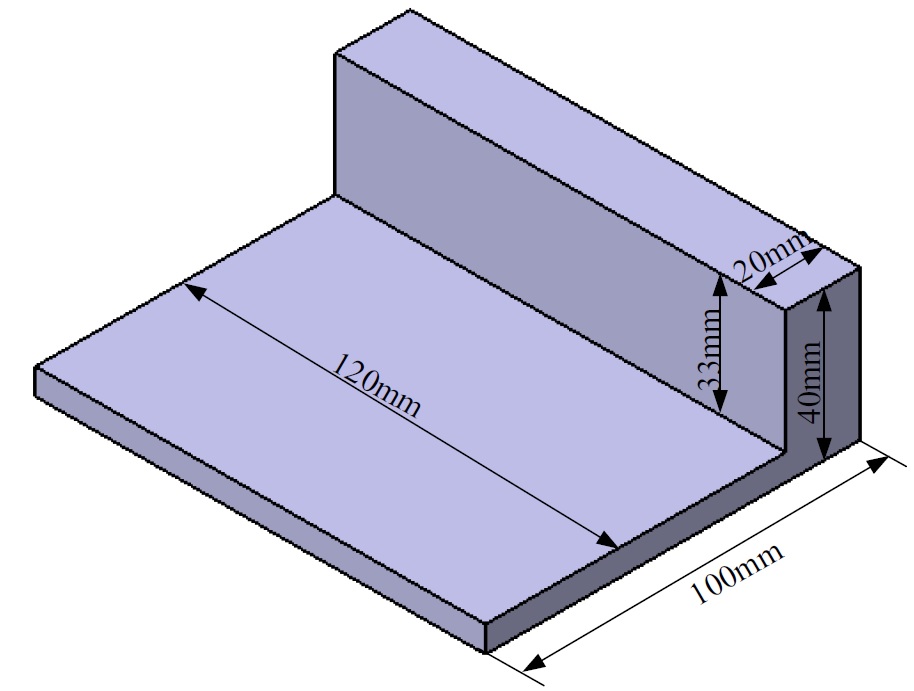
圖4 工件1的模型
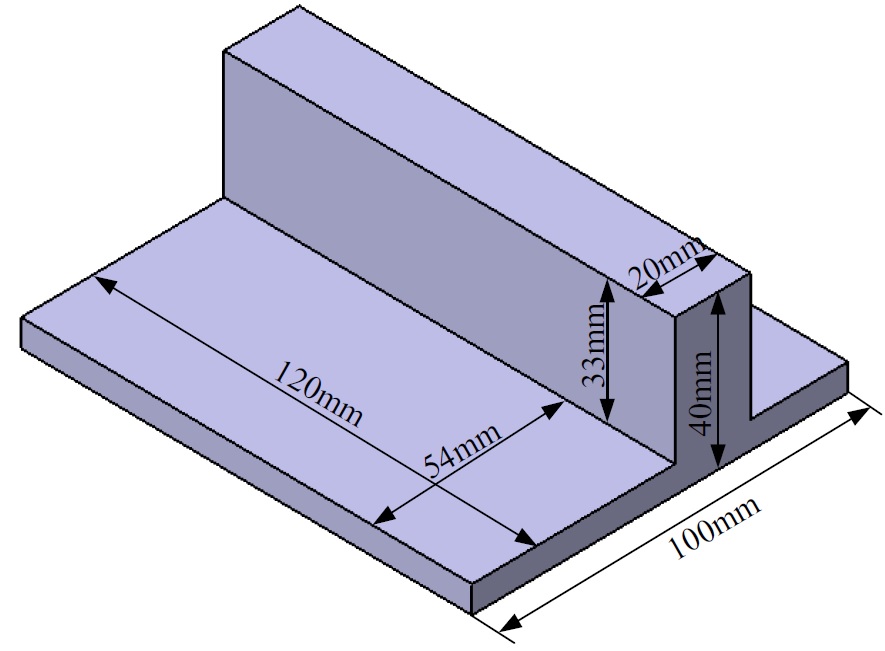
圖5 工件2的模型
模態實驗的現場照片如圖6和圖7所示。
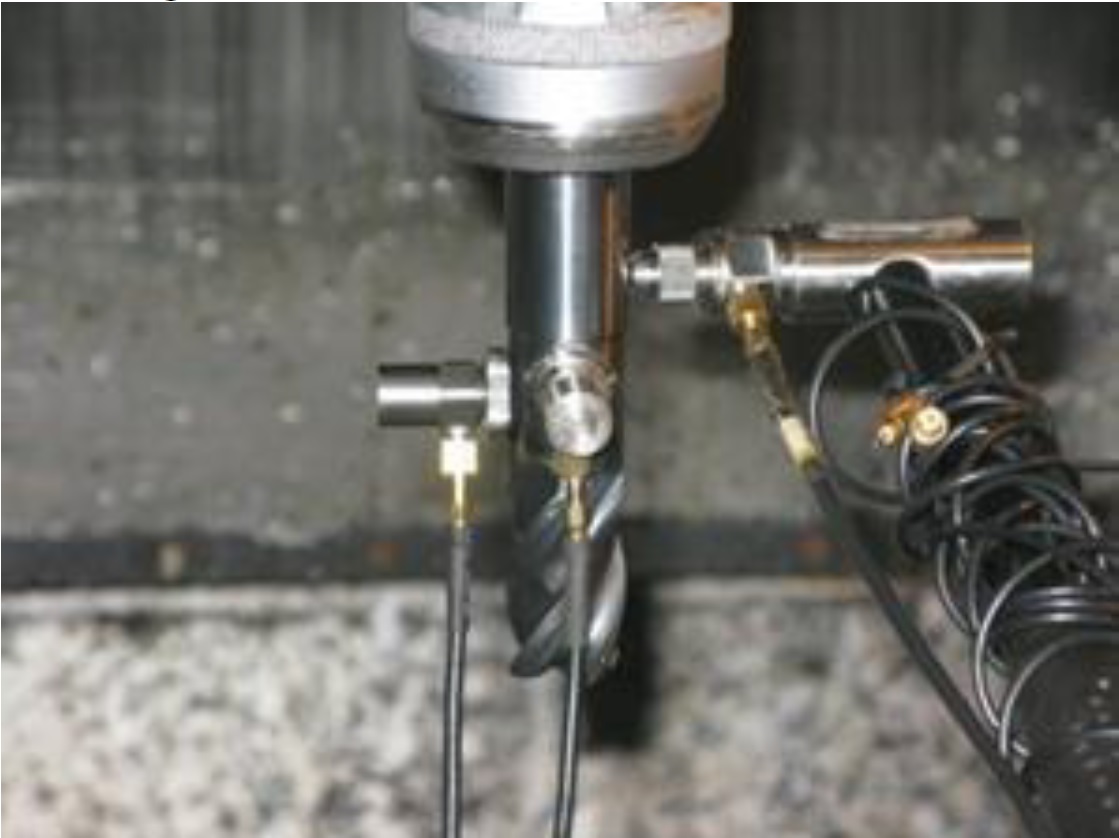
圖6 工具的模態實驗
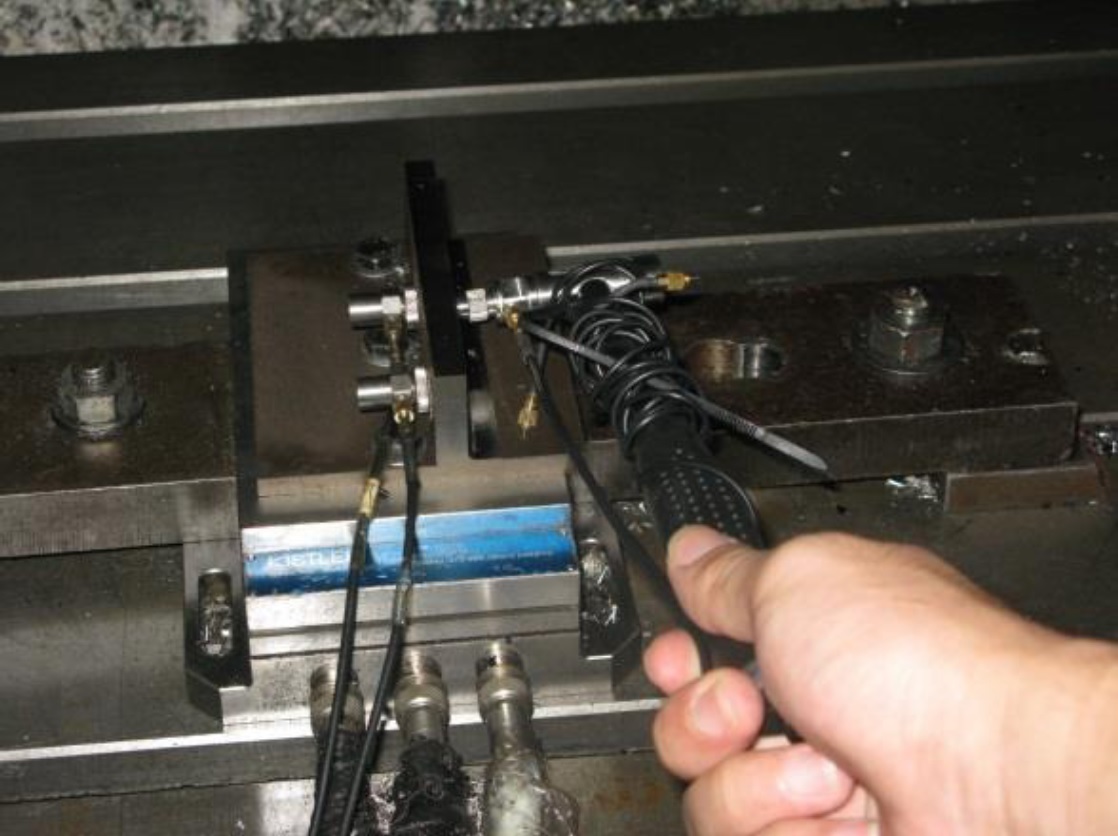
圖7 工件的模態實驗
3.2. 實驗結果和討論
通過不同進給速度的實驗,得到切削力係數,
Ktc=965.79N/mm2,Kte=63.662N/mm。
Krc=-2860.7N/mm2,Kre=55.133N/mm。
由刀具系統和工件系統組成的耦合系統的穩定性,在考慮刀具和工件的剛性時,由兩個子系統的傳遞函數之和決定。而相對位移的絕對值也是兩個子系統的總和。所以,刀具工件的頻率響應函數(FRF)定義為

其中, Gc 和 Gw 分別為刀具和工件的 FRF。在考慮到刀具和工件的剛性的基礎上,繪製了考慮到刀具和工件的剛性的切削穩定性葉片圖。工件1和工件2的切削穩定葉片圖如圖8所示。工件1的壁厚為3mm,刀具延伸長度為72mm。可以看出,工件2的軸向極限深度比工件1大,在同段主軸轉速下,工件2的切削穩定葉數比工件1多。
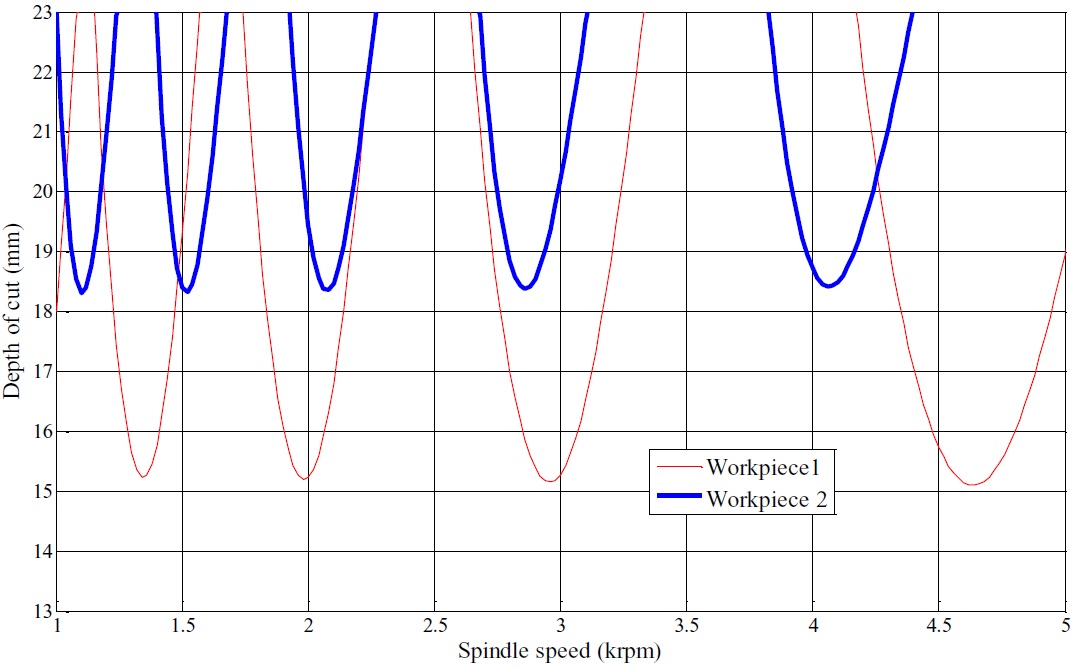
Ktc=965.79N/mm2,Kte=63.662N/mm。
Krc=-2860.7N/mm2,Kre=55.133N/mm。
由刀具系統和工件系統組成的耦合系統的穩定性,在考慮刀具和工件的剛性時,由兩個子系統的傳遞函數之和決定。而相對位移的絕對值也是兩個子系統的總和。所以,刀具工件的頻率響應函數(FRF)定義為

其中, Gc 和 Gw 分別為刀具和工件的 FRF。在考慮到刀具和工件的剛性的基礎上,繪製了考慮到刀具和工件的剛性的切削穩定性葉片圖。工件1和工件2的切削穩定葉片圖如圖8所示。工件1的壁厚為3mm,刀具延伸長度為72mm。可以看出,工件2的軸向極限深度比工件1大,在同段主軸轉速下,工件2的切削穩定葉數比工件1多。
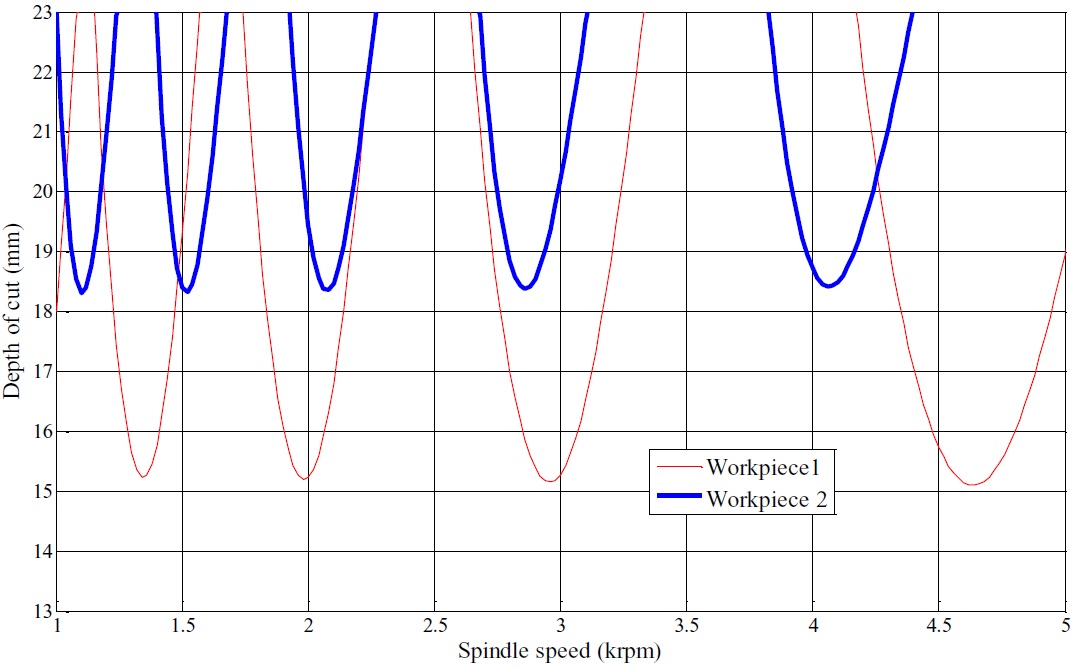
圖8 考慮到刀具和工件的剛性的切削穩定性葉片圖
銑削實驗是為了驗證切削穩定葉圖的準確性。兩工件的切削深度分別為15mm和18mm。壁厚為3mm,刀具延伸長度為72mm,其他切削參數為vc=120m/min,fz=0.05mm/z,ae=0.5mm。工件1的表面照片如圖9(a)所示。可以看出,當切削深度為15mm時,表面有輕微的震動痕跡,應該是刀具退刀的痕跡。但當切削深度為18mm時,震動痕跡明顯,聲音刺耳,因此出現顫動。
工件1在ap=15mm和18mm時的切削力譜圖如圖10所示。可以看出,圖10(a)中,震動發生在刀齒通過率的整數倍上。但是,除了圖10(b)中的整數倍以外,其他頻率的震動也發生了。由此可見,在這些頻率上發生了顫動。
%20the%20surface%20photos%20of%20workpiece%201.jpg)
(a) 工件1的表面照片
%20the%20surface%20photos%20of%20workpiece%202.jpg)
(b) 工件2的表面照片
圖9 工件的表面照片
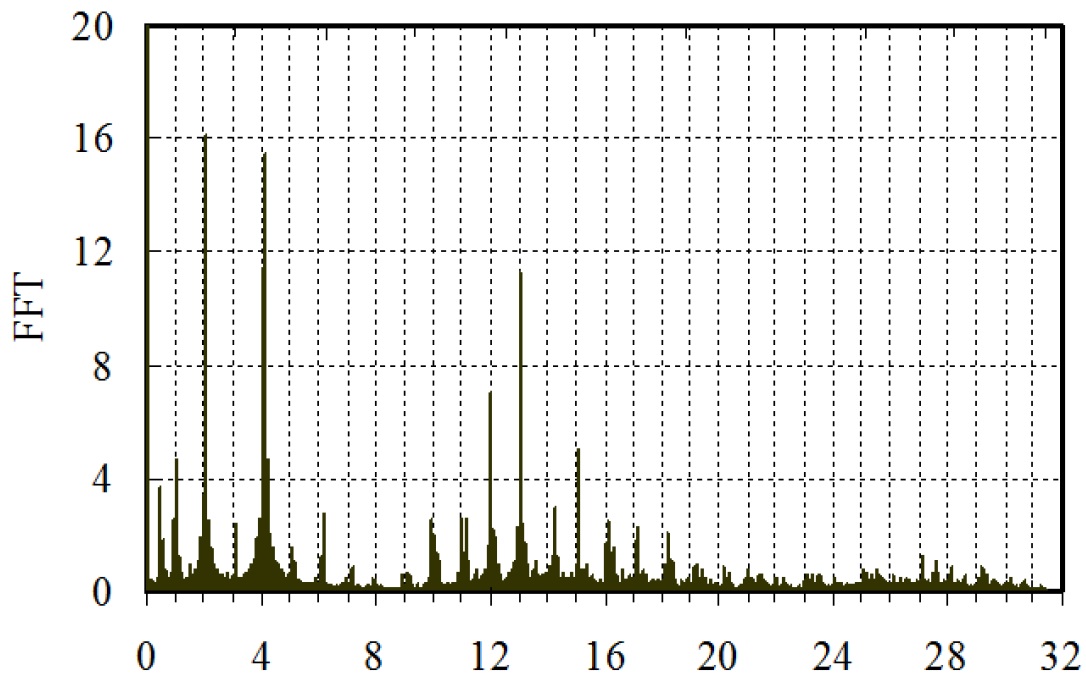
刀齒通過率的整數倍數
(a) ap=15mm
.jpg)
刀齒通過率的整數倍數
(b) ap=18mm
圖10 工件1的切削力譜圖
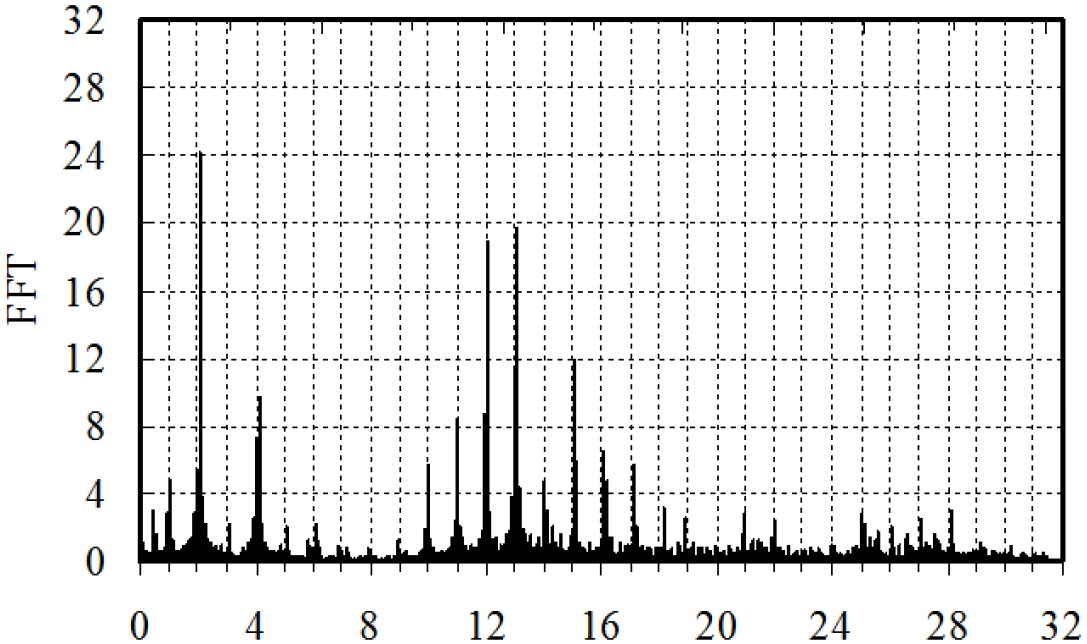
刀齒通過率的整數倍數
(a) ap=15mm
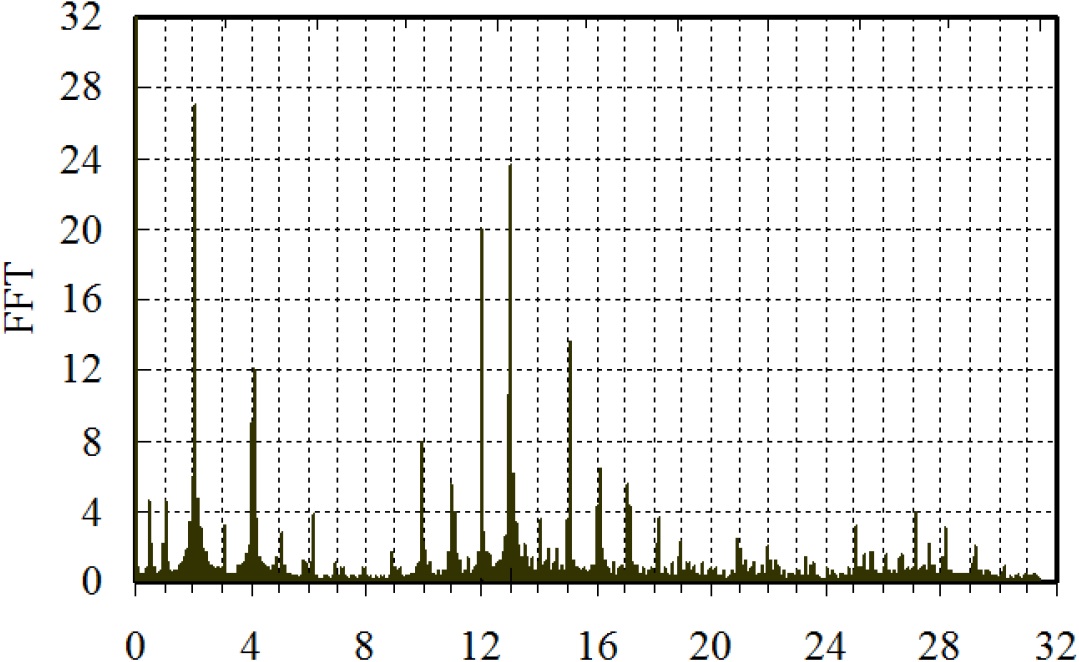
刀齒通過率的整數倍數
(b) ap=18mm
圖11 工件2的切削力譜圖
工件2的表面照片如圖9(b)所示。可以看出,沒有明顯的顫動痕跡。振動痕跡是刀具退刀的痕跡。工件2的ap 15mm和18mm的切削力譜圖如圖11所示。可以看出,所有的振動都發生在刀齒通過率的整數倍上。說明沒有發生顫動,這與工件2的表面現像是一致的。
4. 結論
(1)考慮到刀具和工件的剛度特性,建立了鈦合金薄壁零件的銑削動態模型。並建立了銑削系統的切削力模型。
(2)繪製了考慮刀具和工件剛度的切削穩定性葉狀圖。並從結果中可以看出,不同剛度條件下,切削的軸向極限深度不同。工件2的軸向極限深度比工件1的軸向極限深度大,在同段主軸轉速下,工件2的軸向極限深度比工件1的軸向極限深度多。
(3)切削試驗結果表明,模型是有效的,模型可以準確預測鈦合金薄壁零件加工中的顫動穩定性。
致謝
這項研究得到了國家科技重大項目的資助。編號:2013ZX04001 - 021)。