使用TiAlN塗層硬質合金立銑刀對不銹鋼進行微加工
2020-06-22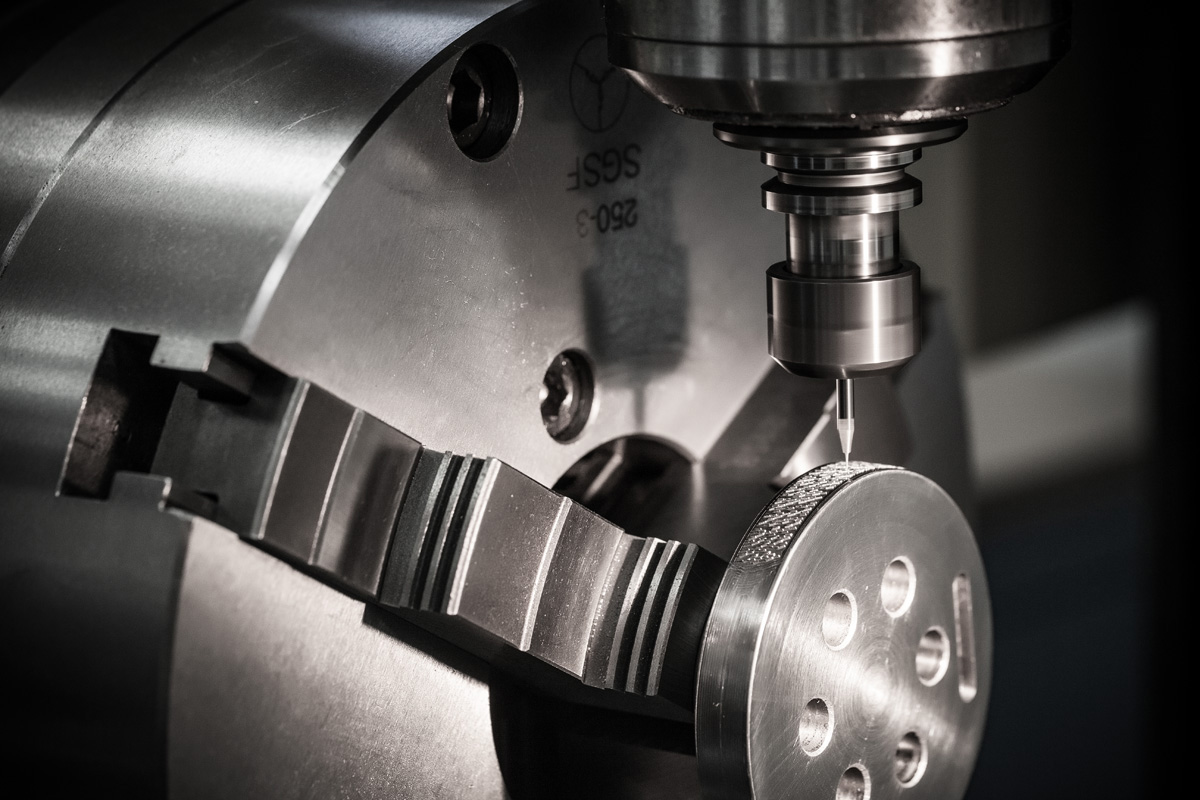
摘要
微溝槽加工用於引入化學反應、傳質和/或熱交換器的一些功能微器件。通常採用微銑工藝,利用微端銑刀機械的切削掉工件材料,以精確的切削溝槽。雖然一些已發表的研究已經揭示了微加工參數對切削尺寸和工藝性能的一些影響,但很少有人對微溝槽加工中的切削表面質量和材料去除率進行討論。因此,本研究旨在研究加工參數對這兩方面的影響。選取AISI 304不銹鋼作為工作材料,採用TiAlN塗層碳化鎢端銑加工。進行了一組實驗,在不同的進給速度和切削深度下對工件進行切削。槽寬、槽深、表面粗糙度、毛刺高度和材料去除率被認為是本研究的過程響應。同時進行了多目標優化,以確定一個能優化平衡切削表面質量和材料去除率的加工條件。結果發現,進給率為30 mm/min、切削深度為2μm的相關條件是促進微溝槽加工質量好、加工率高的合適條件。本研究提出的結論可以拓寬對工藝行為的認識,為工藝優化提供相關指導。
1. 簡介
在醫療設備、機器人、汽車零部件、航天和能源等各種應用中,對微型設備和微型部件的需求已經出現。其中一個例子是製造微溝槽,用於微反應器中輸入化學物質和引入化學反應。由於微反應器的性能取決於微溝槽的特性,因此,為了最大限度地提高反應器的效率,必須對溝槽的幾何尺寸,包括形狀和表面處理進行特殊製造。微機械加工工藝使用切削工具銑床切削掉工件材料,是製造微溝槽以及基體中其他微特徵的典型方法。
切槽的質量在很大程度上取決於端銑的幾何形狀和加工條件。在微加工過程中,尺寸效應是一個重要的問題,造成與宏觀加工過程不同的切削力學和端銑-工件相互作用。因此,微加工操作所設定的最佳條件不一定與宏觀加工條件相同。因此,有很多研究都在研究微加工參數對切削力學、端銑-工件相互作用和獲得的切削特徵質量的影響。Biermann和Steiner研究了奧氏體不銹鋼微加工中銑刀幾何形狀、切削速度和每齒進給量對毛刺高度的影響,他們發現在採用上銑切銑削策略時,使用高切削速度和高每齒進給量可以促進毛刺高度。Kiswanto等人也發現,在1100鋁的微小加工中,使用高進給率和淺切深可以引導毛刺形成方向。毛刺不僅沿切削溝槽的頂邊形成,而且在溝槽的底面也有毛刺。
當切削刀具受到大量端銑的磨損時,這種底部毛刺更為明顯。這又導致切削刃陷入工件材料而不是切削作用,從而形成沿切面的大毛刺。雖然具有正耙角和大螺旋角的切削刀具可以減少毛刺的形成,但由於切削刃的薄弱,端銑容易被磨損。除了端銑刀的幾何形狀外,Biermann等人還考慮了不同塗層材料在AISI 304不銹鋼微粉加工中的切削刀具性能進行了比較。每個直徑為1mm的端銑刀都使用單層CrN、TiN、AlCrN、AlTiN和TiAlN塗層,他們的調查顯示,TiAlN、AlCrN和AlTiN塗層的端銑刀可以表現出比其他刀具更高的耐磨性。Dumkum等人的研究中也提出了類似的塗層材料建議,TiAlN塗層的WC端銑刀可以提供高硬度和對WC基體的良好附著力。上述文獻報導的最小溝槽寬度為0.2mm,而更微小的溝槽目前在製造中的需求量很大,因為它可以進一步提高微器件的整體性能,如改善微反應器的化學反應。
此外,關於微溝槽加工中的切削表面質量和材料去除率的討論還很少。預計在獲得的質量和切削率之間會有一個權衡,但這種關係在其他地方還沒有明確提出。本文通過實驗研究了不銹鋼微加工製作微溝槽的方法。擬研究主要加工參數對被切溝槽的尺寸和表面粗糙度的影響,以使人們對該工藝有進一步的了解。還確定了平衡切削質量和工件去除率的最佳加工條件,以獲得可接受的切削特徵和最大可能的切削率。透過本研究,對加工參數的影響認識將得到進一步的提升,研究結果將為不銹鋼或其他類似金屬的微加工中的工藝優化提供重要的指導。
2. 材料和方法
本研究以304級不銹鋼為工件樣品,在金屬板上切削出尺寸100×100μm的10mm長微溝槽。由於TiAlN塗層的碳化鎢平頭銑刀(WOTEK)硬度高,且TiAlN鍍膜在WC基體上的附著力良好,可以使其具有較高的抗磨損能力,延長端銑壽命,因此選擇了TiAlN塗層的碳化鎢平頭銑刀(WOTEK)作為刀具。刀具直徑(D)為100μm,有兩個螺旋角為30度的槽。從立銑刀製造商那裡得到的推薦切削條件是主軸轉速(N)為40000rpm,進給率(vf)為40mm/min,切削深度(d)為1μm。每齒進給量(f)可以用以下方法計算:

其中n是刃數或槽數。關於這個推薦條件,計算出的每齒進給量為0.5μm/刃。由於本研究中使用的數控機床的最高主軸轉速只能達到35000轉/分,為了保持0.5μm/刃的相同進給量,不得不將進給率降低到35mm/min。此外,推薦的切削深度只有1μm,因此需要100次銑削才能做出100μm深的通道,如圖1所示。為了減少一半的加工時間,本研究還測試了2μm的切削深度。應用較深的切削深度,應採用小於35mm/min的進給率,以避免端銑失敗。因此,本研究考察了20、30和40mm/min的進給率。實驗按照全因素實驗設計進行,每個條件的重複次數為2次,以滿足統計學置信區間的要求,因此,試驗總數為12次。將不銹鋼板放在數控機床的真空台上,壓力為-60 kPa,如圖2所示。
%20Schematics%20of%20milling%20path%20for%20making%20a%20100-%CE%BCm%20deep%20micro-channel%3B%20(b)%20Micrograph%20of%20100-%CE%BCm%20flat%20end%20mill%20used%20in%20this%20study_.jpg)
圖1. (a)製作100μm深微通道的銑削路徑示意圖;(b)本研究中使用的100μm平端銑的顯微圖
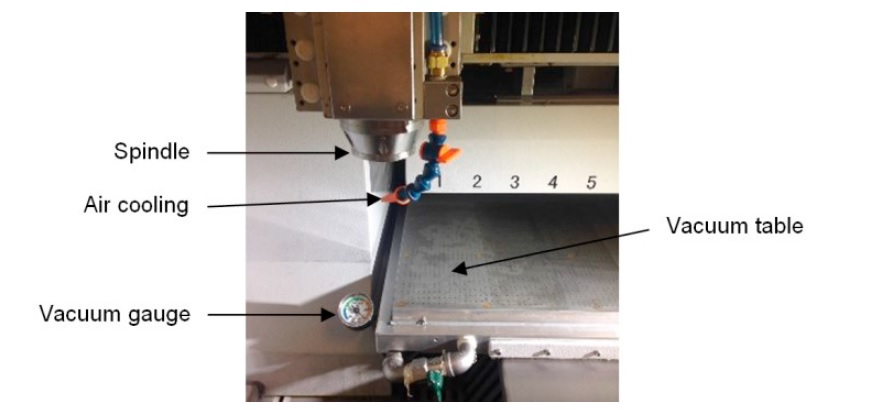
圖2. 帶有真空工作台的數控機床
使用共聚焦顯微鏡(HRM-300,Huvitz)觀察和測量每個切削樣品的溝槽寬度、深度和毛刺高度,使用輪廓儀(SV-3000,日本三豐公司)量化溝槽底面的平均粗糙度(Ra)。本研究還考慮了工藝的材料去除率(MRR),可以用以下方法計算。

其中,D、vf、d和n分別為端銑直徑、進給率、切削深度和槽數。關於式(2),本研究中所核算的加工條件的MRR列於表1。
表1.各加工條件的材料去除率(mm3 /min)

3. 結果和討論
圖3(a)和(b)分別顯示了進給速度和切削深度對溝槽平均寬度和深度的影響。切削溝槽的顯微圖也見表2。根據結果,溝槽寬度略大於端銑直徑,平均誤差為6.4μm。在進給速度為20和30mm/min時,溝槽寬度變化不明顯。但在40mm/min的進給率下發現了明顯的相互作用,即較深的切削深度引入了較窄的溝槽,反之亦然。採用高進給率基本上會造成大量材料被去除,切削區域變形較大。當採用40mm/min的進給率和較小的切削深度(1μm)時,發生在端磨邊緣的切削載荷在性能極限範圍內,在此範圍內,排屑仍能很好地進行而不發生堵塞。相反,使用高進給率和大切削深度的組合可能會導致切屑堵塞,甚至材料碎片在切削邊緣上的黏附。這樣的特性導致在加工過程中切削作用不當,切屑脫落不良。因而使切削刀具的耙角變為較負的值,然後使加工機理由切削作用轉化為驟進作用。根據這種效應,預計結果會出現窄切槽。
%20Average%20width%20and%20(b)%20depth%20of%20micro-channels%20obtained%20under%20the%20different%20machining%20conditions_.jpg)
圖3. 在不同加工條件下獲得的微溝槽的平均寬度和深度(a)和(b)深度
表2. 不同進給率和切削深度下,微銑削工藝造成的切削溝槽表面形態
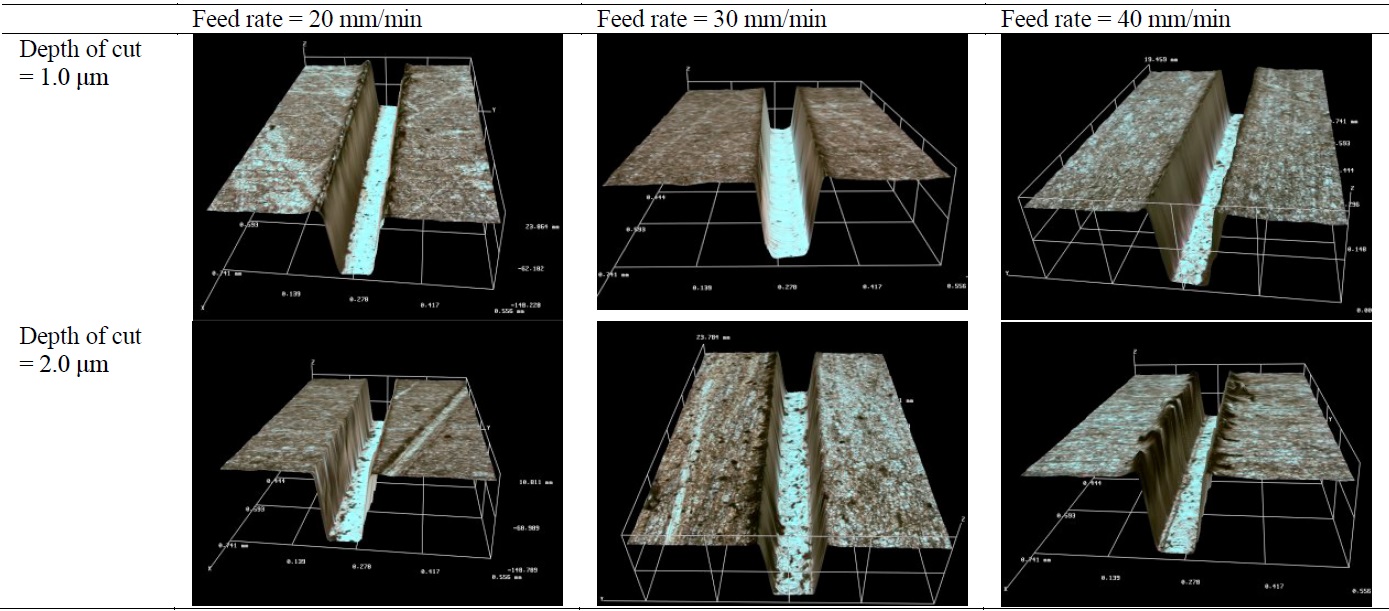
如圖3(b)所示,不同的切削深度所引起的溝槽深度並不明顯。在本研究中測試的所有進給值中,發現所有切削溝槽的深度都比所需的100μm的深度深了約25%。雖然在開始每次實驗運行之前,都仔細測量和設置了端銑位置和端銑長度補償,但本研究中使用的不銹鋼板並不是完全平整的,金屬板的微小變形可能是造成這種切削深度偏差的原因。使用30-mm/min的進給速度可以提供接近所需的溝槽深度,而不管應用的切削深度如何。這一發現也與立銑刀製造商推薦的進給量相吻合,進給率為35mm/min或每刃進給量為0.5μm/刃可以提供良好的切削效果。由於在30mm/min的進給率下,切削深度對槽寬和深度的影響不是很明顯,因此,每道2μm的進給深度適用於獲得良好的切削效果,加工時間比製造商推薦的條件減少了50%。
%20Average%20burr%20height%20and%20(b)%20bottom%20surface%20roughness%20of%20micro-channels%20obtained%20under%20the%20different%20machining%20conditions.jpg)
圖4. (a)在不同加工條件下獲得的微槽的平均毛刺高度和(b)底面粗糙度
加工條件對平均毛刺高度和表面粗糙度的影響如圖4所示。除最低和最高切削載荷兩種條件外,平均毛刺高度約為5.6μm。在進給速度慢、切削深度小的綜合條件下,毛刺高度為55.3μm。採用這種條件,由於未切削的切屑厚度非常小,柱塞效應很可能主導了切削機理。這可能會在端銑與工件接觸處產生較大的塑性變形,金屬流沿通道邊緣向上突出。如圖4(b)所示,端銑刀引起的對工件表面的摩擦作用也會增加切削溝槽的平均表面粗糙度。這種衝撞作用的後果也會導致端銑磨損和切削力的增加。Kiswanto等人也報告了類似的發現,表明鋁材切削中的毛刺形成是通過使用高進給率加上小切削深度引入的。在高進給率和大切削深度條件下,顯著的毛刺也很明顯。切削負荷大,排屑效果差,是造成溝槽內切屑堵塞的原因。這一結果也與Biermann和Steiner的研究一致,指出毛刺高度隨進給率的增加而明顯增加。有些切屑很可能黏附在切槽的底面,有些則傾向於在槽邊擠出毛刺。如表3所示,發現切削屑的黏附會使切削槽的表面形態惡化。Kiswanto等認為這種影響是底部毛刺,其形成與端銑磨損程度成正比。雖然在進給速度為20 mm/min、切削深度為2μm時,可以達到0.428μm的最低表面粗糙度,但發現有許多碎屑附著在切槽的底面。如表3所示,在30-mm/min的進給速度和1-μm的切削深度下,可以獲得較好的表面質量,提供低粗糙度和幾乎沒有底部毛刺。
表3.使用不同進料速度和切削深度形成的微溝槽底面
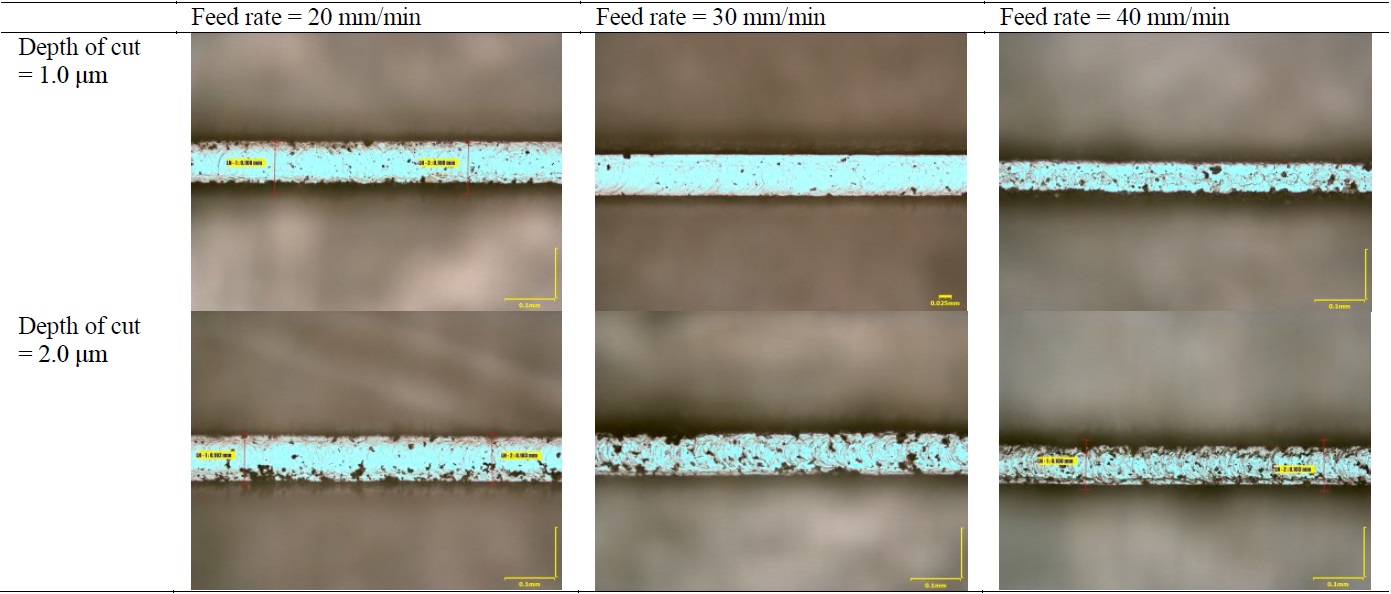
合適的切削條件的選擇受制於個別工藝影響。提供最小尺寸誤差的加工條件不一定與提供最低表面粗糙度的加工條件相同。為了應對各方面的多目標優化,本研究採用了加權平均法,將所有測量數據歸一化,然後定義一個決策因子。第i個條件(y*i)的歸一化響應表示為:

其中yi為第i種情況的測量響應。寬度和深度、毛刺高度和平均表面粗糙度的尺寸誤差被認為是越小越好的情況,而材料去除率(表1)是越大越好。特定條件的所有歸一化值均以相同的加權值1/n取平均值,其中n為工藝響應的數量。因此可以用以下方法計算出第i個切削條件的決定係數(ηi)。

各方面都同樣滿足的最佳條件,其決定因素最多。如圖5所示,最大ηi為0.739,屬於進給速度30-mm/min、切削深度2μm的切削條件。在此條件下,可以得到107和117.9μm的槽寬和槽深,平均表面粗糙度為0.644μm,毛刺高度僅為5.07μm。切削一條10mm長的溝槽,總加工時間約為17分鐘。圖6為銑刀切削溝槽後的顯微照片,表明切削刃處有崩刃的跡象。此外,在切削刀具的側面,切削碎屑與端銑表面的黏連,稱為堆積刃,很明顯。這可能是由於端銑刀-切屑界面的動線狀況不佳,使切屑不能有效地從刀具上脫落。雖然提高切削速度或主軸轉速可以合理地減少切屑堆積的刃口,改善切削面質量,但預計磨損率高,毛刺形成明顯。這可能會導致切削表面質量差,並縮短鎢鋼銑刀的使用壽命。由於本研究中使用的數控機床是以最高轉速運行,因此可以進一步研究切削速度在這一特殊微加工過程中的影響,以拓寬對工藝行為的理解,並確定今後更好的切削條件。
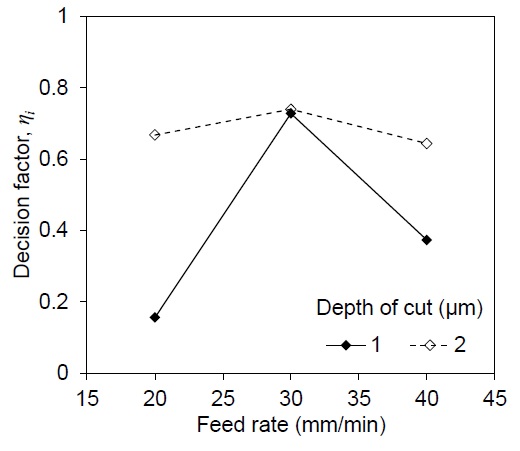
圖5.進給率、切削深度與決定因素的關係
%20Rake%20face%2C%20(b%2Ce)%20side%20view%20and%20(c%2Cf)%20end%20view%20of%20new%20and%20used%20cutting%20tools%20after%20machining%20a%2010-mm%20long%20channel.jpg)
圖6. (a,d)耙面,(b,e)側視圖和(c,f)新舊刀具加工10mm長槽後的端視圖
4. 結論
在AISI 304不銹鋼板上加工了一條尺寸為100×100μm的微通道。本研究對進給速度和切削深度對溝槽尺寸、表面粗糙度、毛刺高度和材料去除率的影響進行了實驗研究和分析。進給率大於30mm/min時,特別是切削深度為1μm時,進給率的增加擴大了溝槽的寬度和深度。雖然使用2μm的切削深度可以使1μm深度的材料去除率增加一倍,但發現毛刺高度和平均表面粗糙度顯著增加,這些反過來又惡化了切削通道的質量。應用與加權平均法相關的多響應優化來確定一個合適的加工條件。這可以使本研究中考慮的各方面都得到平衡折衷讓步。透過使用30mm/min的進給率和2μm的切削深度,平均尺寸誤差為12.45%,毛刺高度為5.07μm,表面粗糙度為0.644μm,材料去除率為0.00942 mm3 /min。本研究的意義可以使人們對微加工行為有更好的認知,同時也為不銹鋼或其他類似金屬微加工中的切削質量和材料去除率的工藝優化提供指導。