優化設計Ti-6Al-4V銑削用立銑刀的有限元分析
2020-06-19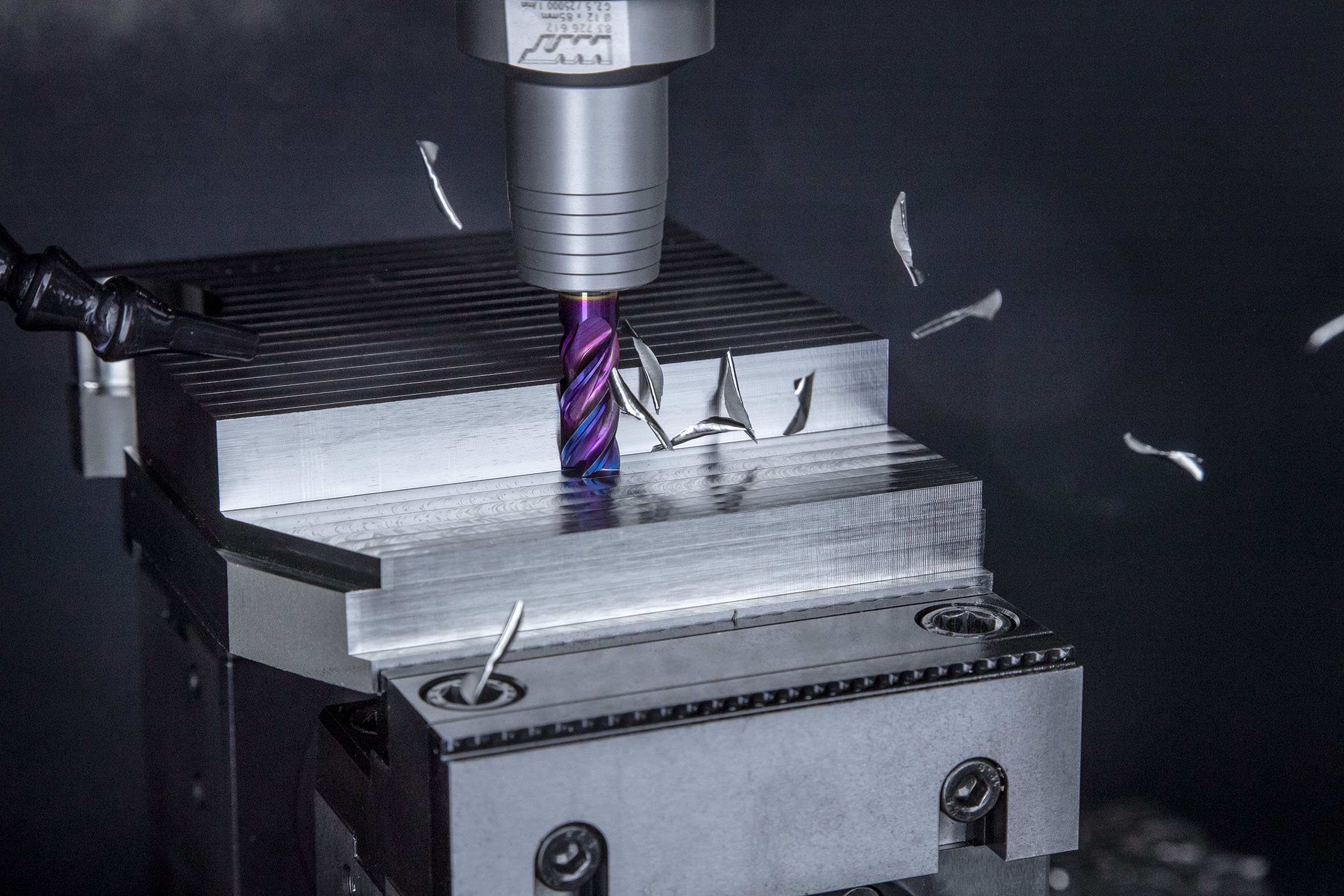
摘要
本文通過驗證銑削鈦合金Ti-6Al-4V的切削刀具力和應力,為優化設計立銑刀進行了有限元分析。最初,根據Lee & Altinas開發的模型,將刀具上的切削刃視為球面/平面上的交點曲線,計算出理論刀具力。考慮到最低的刀具力,採取刀具參數,決定不同尺寸的立銑刀的最佳設計。然後建立立銑刀的三維CAD模型,採用有限元法驗證銑削Ti-6Al-4V的切削力。以Ti-6Al-4V為工件材料,模擬了不同幾何形狀的刀具受力、應力、應變集中度(s)、刀具磨損和溫度。最後,將仿真值和理論值進行比較,驗證了不同尺寸的刀具的優化設計。本方法考慮到斜切削過程中各種參數即軸向力、徑向力和切向力的影響,提高加工表面質量和刀具壽命。介紹了各種模擬測試案例,強調了優化設計立銑刀的方法。
1. 介紹
由於Ti-6Al-4V的幾個固有特性,如低導熱係數、低彈性模量和在高溫下承受不同載荷的能力,現今廣泛應用在汽車、航空航天和生物醫療行業。Ti-6Al-4V的成分和力學性能見表1、2。由於在加工過程中,大部分用於去除材料的機械能都變成了熱能,所以在切削區域會產生高溫。由於這一事實,加工後的切屑很容易黏附在切削刀具上和加工表面上,進而加快的銑刀磨損。對於Ti-6Al-4V來說,由於導熱係數低,此問題會更嚴重,因為切削區域產生的80%的熱量都進入了銑刀。為了避免這個問題,眾所周知,使用切削液。但在高速加工過程中,Ti-6Al-4V的成品表面還是很容易出現損傷。許多研究者試圖採用各種優化方法控制工藝參數和利用不同的切削液來解決這個問題。有的建議使用高硬度的銑刀材料,可以減少熱影響區,提高工件質量、生產率和銑刀壽命。儘管嚐試了很多方法,但在許多加工切削中還是會遇到這個問題,本研究試圖通過採用優化設計合適的立銑刀的方法來解決這個問題,使其產生較小的切削力,提高加工表面質量和銑刀壽命。本文考慮端銑(鎢鋼球刀&平刀)加工Ti-6Al-4V,計算了加工過程中的各種切削刀具力。之後,根據切削力,考慮到Ti-6Al-4V作為工件材料,進行了有限元分析,優化設計了立銑刀。為了更好的理解這個問題,提供了簡單的回顧,在廣泛領域,銑削Ti-6Al-4V的研究工作。
表1. Ti-6Al-4V的組成(wt.%)
%20of%20Ti-6Al-4V.jpg)
表2. Ti-6Al-4V在室溫下的機械性能

相關名詞
Ft, Fr, Fa / 切向、徑向和軸向力
Sz / 每刃進給,mm
s / 進給量(mm/分鐘)
Rpm / 主軸轉速
As / 切屑厚度平均值(mm)
Zs / 同時參與加工的每刃數量
Pz / 切向力(N)
Px / 軸向力(N)
Py / 徑向力(N)
P / 總切削力(N)
Ks / 切削力比(Kgf/mm2)
Sz / 每刃進給,mm
s / 進給量(mm/分鐘)
Rpm / 主軸轉速
As / 切屑厚度平均值(mm)
Zs / 同時參與加工的每刃數量
Pz / 切向力(N)
Px / 軸向力(N)
Py / 徑向力(N)
P / 總切削力(N)
Ks / 切削力比(Kgf/mm2)
2. 審查文獻
Lee和Altintas應用球端銑刀銑削過程的幾何學和運動學,準確預測了切向、徑向和軸向的切削力。他們建立了一個模型,並從一組在不同切削速度和進給量下進行的正交切削試驗中測量了基本切削參數、屈服剪切應力、耙面平均摩擦係數和剪切角。Ahmad Yasir等人提出了一種最小質量潤滑(MQL)的方法,並證明MQL對於銑刀壽命、表面粗糙度和一定切削速度下是有效用的。他們提到,在較高的切削速度下,MQL的效果較差,因為需要較高的壓力來確保霧狀顆粒滲透到切削區域。Puneet Tandon et.al從形狀實現的角度提出了一種切削端銑的幾何模型。建立了立銑刀的數學模型,並以各種雙參數表面斑點來表示刀具的幾何形狀。最後,通過對刀具幾何方程的求解,他們驗證了立銑刀的表面模型。Abbas Fadhel等人預測,進給率對切削力的影響是最主要的,其次是軸向深度、徑向切削深度,然後是切削速度。利用遺傳網絡(GN)對切削力值的準確性進行了實驗驗證,發現其準確性為92%。他們的方法證明了是成功的技術,可以用來預測端銑中產生的縱向切削力。
Dimitrov等人提出了一種驗證切削速度的方法,該方法是對銑刀壽命影響最大的參數。他們進行了實驗,驗證了造成立銑刀壽命減少的主要原因是由於熱負荷的增加和工件材料表面硬化。後期引入的冷卻改造,並透過輔助去除切削區的發熱來降低熱負荷。Nagi Elmagrabi等人透過比較其他切削參數,研究了進給率對表面粗糙度的影響。他們注意到,用PVD硬質合金端銑加工Ti-6Al-4V時,側面磨損、黏附和高速切削時的熱裂紋是最主要的失效模式。Lee等人對高速球端銑刀銑削的振動進行了實驗驗證,指出當高速球端銑刀用於懸臂形薄板時,工件端部振動嚴重,且受刀具方向影響較大。在進行的實驗中,他們發現垂直向上的切削方向和工件下部的切削最穩定。
Pai chi chang和Wang lin提出了一種評價圓柱柄錐度球端銑刀實際工作輪廓質量的模型。工作中,他們將銑刀裝到刀柄的圓柱面上,並採用刀柄的最小圓周圓柱面(MCCS)作為基準軸來分析過程。利用這個概念,他們定義了最小圓周錐面(MCTS)和最小圓周球面(MCS)來計算刀具錐面部分和球端部分的螺旋槽輪廓。 Kuo和Wu提出了一種測量球頭銑刀刃口的數學模型。從刃口的計算數據中,將理論值與測量值進行比較,給出了加工球頭銑刀的精確評價。Engin和Altintas研究了螺旋端銑刀的通用數學模型。
在他們的研究中,端銑的幾何形狀是由參數絡線上的螺旋槽來建模的。然後沿參數螺旋槽的切削刃點的坐標用數學方法表示。最後,他們利用銑削的真實運動學(包括刀具和工件的結構振動)評估了每個切削點的切屑厚度。Johanna Senatore等人利用包絡曲線的曲率半徑計算了銑刀的有效半徑。在他們的工作中,他們通過將包絡曲線的曲率投影到垂直於進給運動方向的平面上,計算出步距和有效半徑。他們建立了一個關係,使平頭鎢鋼端銑刀的步距大於球頭鎢鋼端銑刀的步距的角度區間。Engin和Altintas也提出了一個插入式銑刀的通用數學模型。該模型通過從刀體坐標系中定義其中心,允許在刀體上以數學方式確定不同刀片的間距。刀片通過圍繞刀體的三個軸旋轉來確定其方向。刀片的幾何形狀由其邊緣尺寸和形狀在局部坐標系中單獨定義。曹慶元和趙軍提出了一種新的考慮傾角的球端精銑的力係數識別實驗方法。
根據不同的傾角,對起始和退出的徑向浸入角進行了建模。工作中,他們分析了切削元件在球端銑刀刃上的位置是影響切向、徑向和軸向切削力係數的唯一因素。自20世紀50年代初,Shaw及其合作者和Boston等人對鈦合金或Ti-6Al-4V合金加工過程中切屑的力學進行了開創性的研究,注意到加工Ti6Al-4V時,由於鈦合金的導熱係數低,約為鋼的1/6,因此產生的熱量有很大一部分(約80%)傳導到了端銑刀中,無法隨快速流動的切屑排出。同時端銑刀刀尖的高應力和高溫相結合,促進了端銑刀的磨損,增加了生產成本。W Konig和Ezugwu &Wang研究了鈦合金加工中突出的失效模式。他們注意到Ti6Al-4V中的失效模式有缺口、凹坑磨損、側翼磨損、崩裂和災難性失效,這些失效模式是由高溫、高壓、化學反應性和分段切屑的形成引起的。另外Ezugwu &Wang報導,碳化鎢和PCD是加工Ti-6Al-4V的最佳端銑材料。他們報告說,這是由於在端銑刀和切屑之間形成了穩定的TiC反應層。
事實證明,在所有切削條件中,切削速度對立銑刀壽命的影響最為突出。隨著切削速度的提高,端銑刀壽命將成倍下降。因此,加工鈦材時,常用的加工方法是以60mm/min的切削速度進行加工。也有報導稱,切削深度對端銑壽命有負面影響。端銑的幾何形狀對端銑壽命也有很大影響。有人提出,100-150的間隙角和高負前角(-100到-150)可以產生顯著的改善。根據文獻綜述,我們決定進行優化設計立銑刀的研究,並進行加工Ti-6Al-4V的FEM分析。為了進行分析,首先計算出理論的立銑刀力,並建立立銑刀的CAD模型。然後利用CAD模型在ANSYS工作台上進行了有限元分析。為了便於理解,本文其餘部分介紹如下。 (i)第3節解釋了對Ti-6Al-4V進行的端銑幾何和受力分析(ii)第4節提供了銑削Ti-6Al-4V的端銑刀的有限元分析的細節(iii)第5節描述了模擬和結果(iv)第6節關於結論和未來工作的範圍。
3. 立銑刀的幾何形狀和力
分析在這項研究中,Altintas和Lee開發的幾何模型已經被考慮用於計算Ti-6Al-4V銑削時的切削力。略作修改以適應本工作的需要,以此複製相同的模型,以便更好的理解。球頭銑刀的詳細幾何形狀如圖1.1-1.3所示。
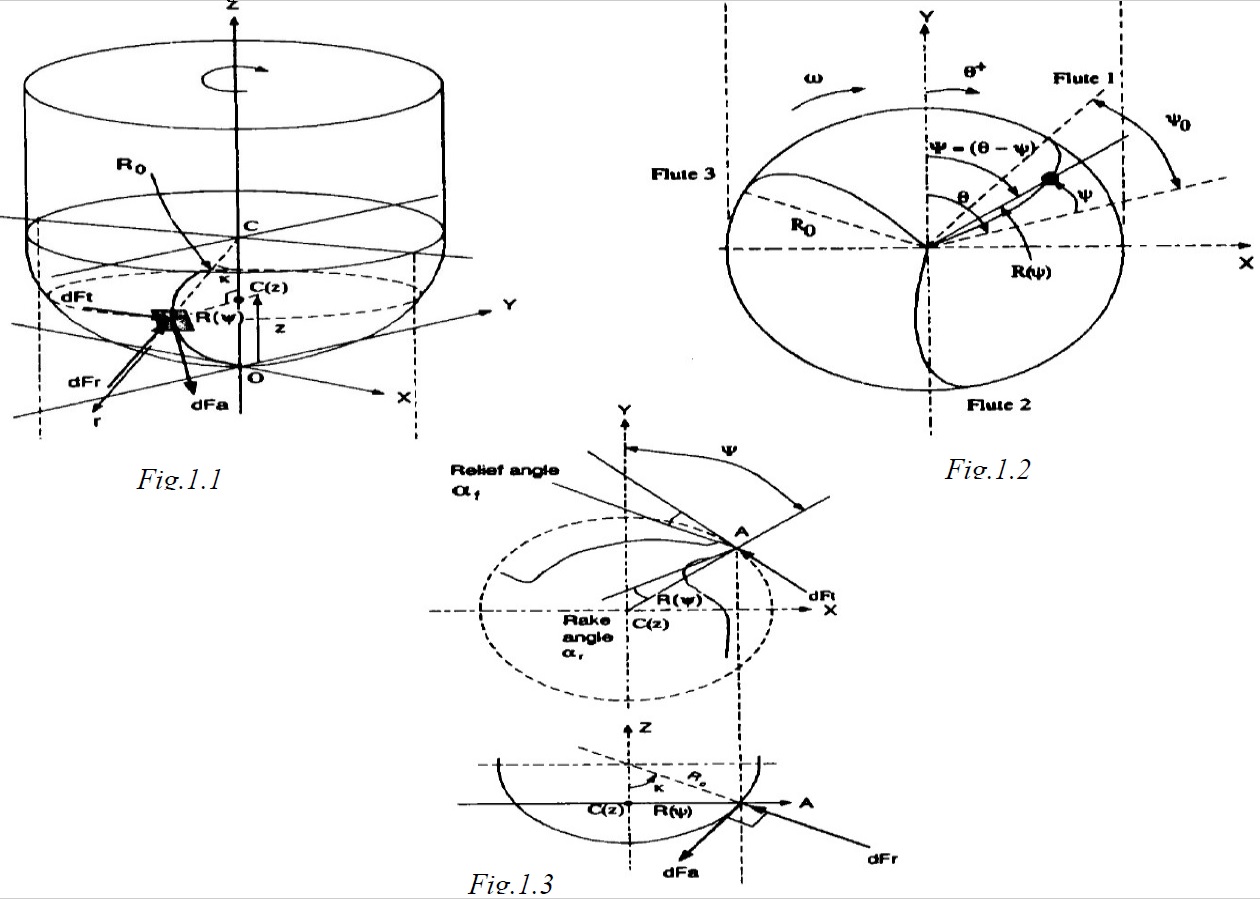
圖1.1-1.3球銑刀的幾何形狀1,2&3
每刃都位於半球銑刀的表面,並以恆定的螺旋引線進行研磨。刀刃在球柄會合邊界處的螺旋角為io。由於x-y平面上的半徑在軸向(z)方向上向刀尖方向減小,對於恆螺旋鉛刀來說,沿切削槽的局部螺旋角i(ψ)是變化的。球部包絡線的表達式為。X2+Y2+(Ro-Z)2=R2......式中(1) 其中Ro為從球體中心測得的球刀半徑。在x-y平面的軸向位置Z處的刀具半徑為R2 (Z) = Z2 + Y2 ......式(2 )而在球尖處為零。圖中球尖點'O'所示的測力計上,局部坐標系的中心與全局坐標系X-Y-Z重合。
3.1 切削力分析
在銑削作業中,切削刀具對工件產生切向力、徑向力和軸向力。在本工作中,為了設計切削刀具,利用MATLAB完成了不同類型切削刀具幾何形狀的不同法線特徵的切削力計算(圖2)。在計算切削力的同時,根據標準手冊數據,採取了切削條件(主軸轉速、進給量、切削深度、平均切屑厚度等)。然後利用這些條件,計算出作用在立銑刀上的切削力即切向、徑向和軸向力。從MATLAB得到的結果如表3和表4所示。它清楚地表明,當主軸轉速提高時,切削力減小,從而使切削溫度值降低,使立銑刀的壽命提高。
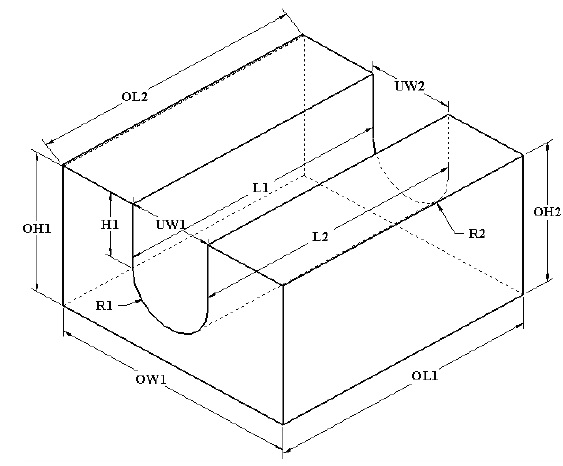
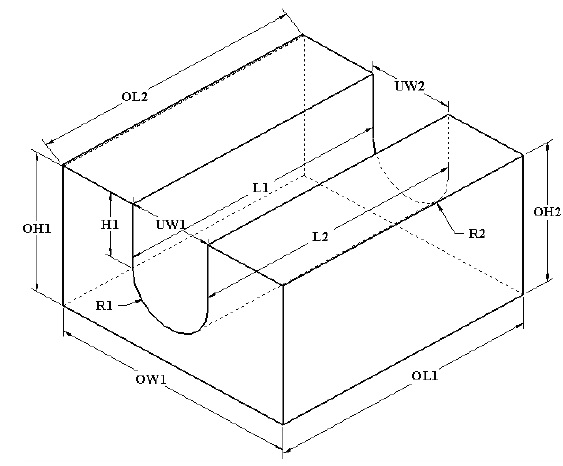
圖2 普通槽形帶弧形底座
表3 切削力的計算
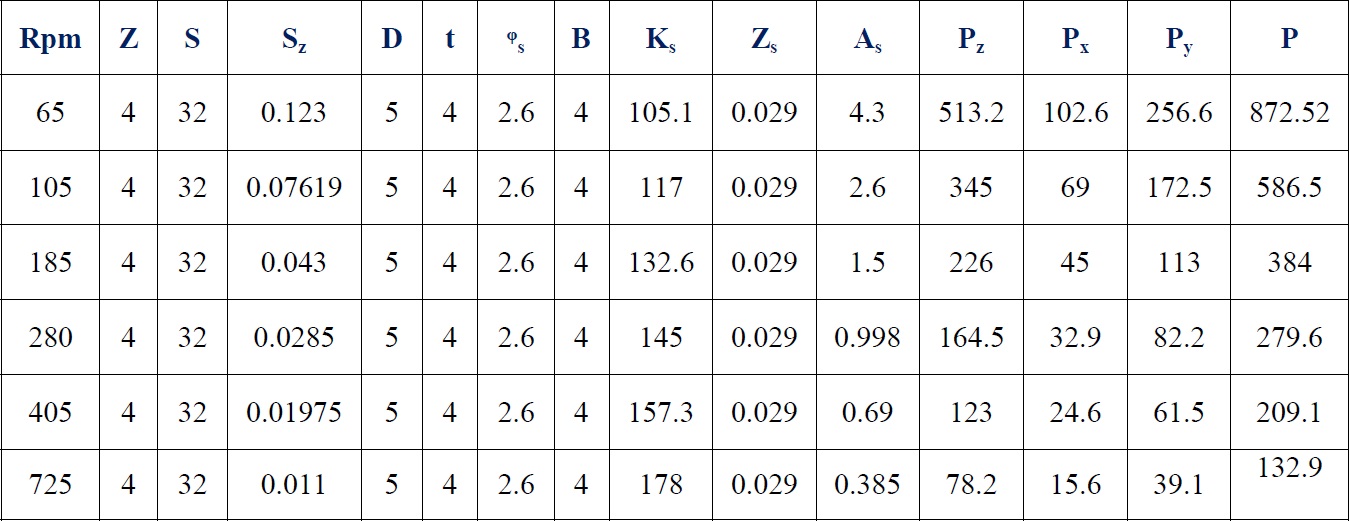
根據結果繪製了圖3.1至3.3所示的曲線圖,它們代表了每齒進給與切削力的關係(圖3.1)、切削力與速度的關係(圖3.2)和速度與功率的關係(圖3.3)。三幅圖表明,隨著進給量的增加,切削力逐漸增大,同樣當速度增大時,切削力也在減小(圖3.2)。這說明如果進給量和速度增加,切削力會增加。在最後一張圖(圖3.3)中,可以理解為切削速度和功率成比例增加。
表4 切削速度和功率的計算方法
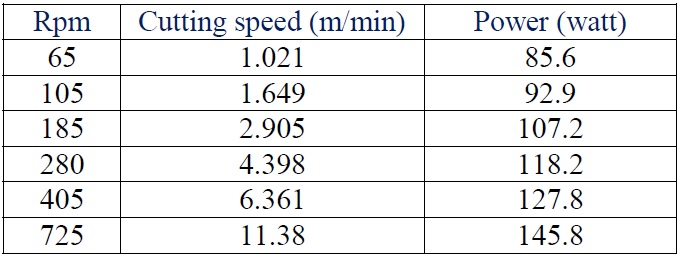
%20Vs%20Force%20(N).jpg)
圖3.1 每齒進給(mm)與切削力(N)的關係圖
%20Vs%20Speed%20(rpm).jpg)
圖3.2 切削力(N)與轉速(rpm)的關係圖
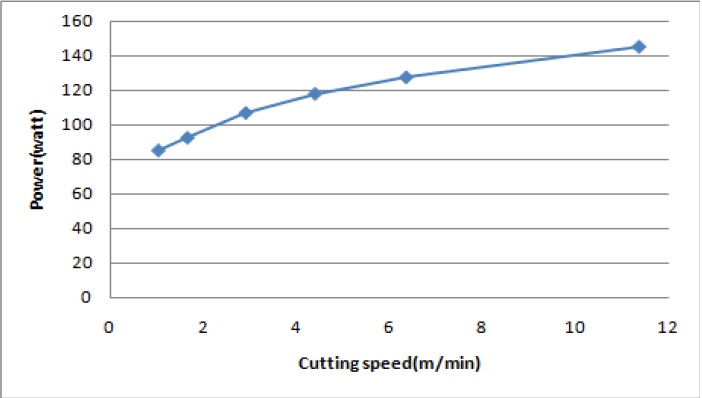
圖3.3 切削速度(mm/分鐘)與功率(瓦特)的關係曲線
4.1 銑削Ti-6Al-4V工件時碳化鎢立銑刀的分析
根據分析結果,決定利用得到的數值優化設計立銑刀,進行仿真。使用Autodesk inventor軟件創建CAD模型,並與一個矩形塊(被視為工件)組裝,並導入到ANSYS工作台。在ANSYS工作台中考慮了瞬態結構分析,因為這類型的分析是用來確定結構在任何一般時間依賴性載荷作用下的動態迴響。然後將材料屬性添加到CAD模型中。附上端銑刀和工件的CAD模型後,輸入與零件幾何形狀、坐標系和參考溫度有關的設置。然後對其進行網格化處理,如圖4所示,並在接觸面上採用較高的網格密度進行模擬,使接觸應力分佈更平滑。
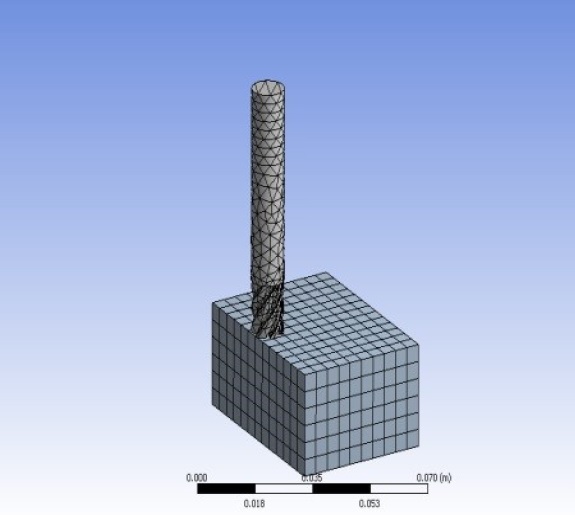
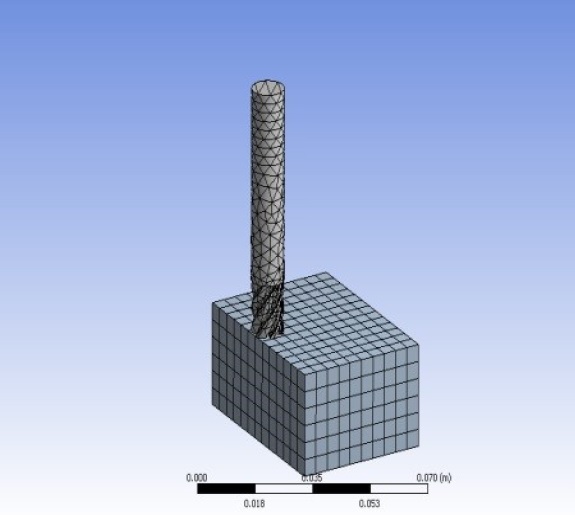
圖4. 端銑刀與工件的嚙合
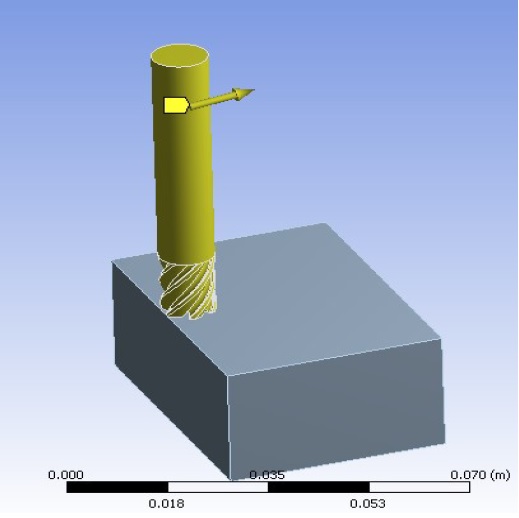
圖5. 將所有設置應用於立銑刀
4.2 分析設置
分析設置包括許多尋找應力分析的選項。階段性控制用於控制瞬態分析中的時間階段大小。它們用於執行兩個不同的功能,如定義階段和為每個階段指定分析設置。所有這些細節都從表5-7中給出。圖5是應用所有必要設置後的零件螢幕截圖。
表5 分析設置詳情
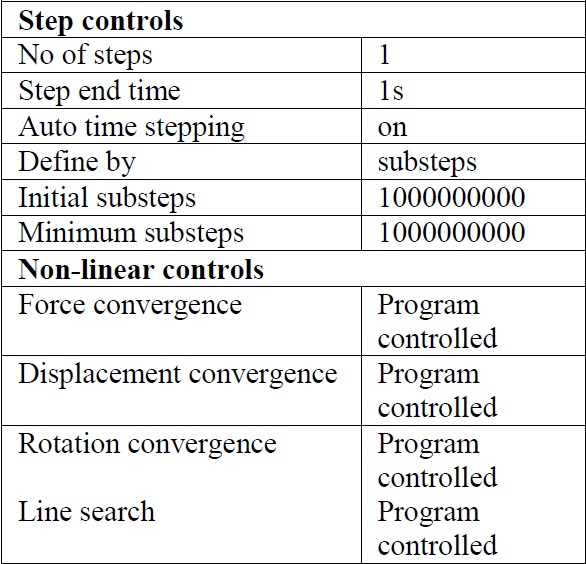
表6 旋轉速度詳情
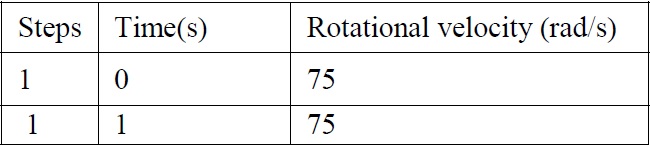
表7 速度詳情
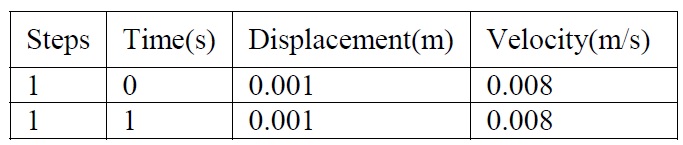
5. 模擬和結果
本工作採用ANSYS工作台軟件對Ti-6Al-4V工件上的硬質合金端銑刀進行動態分析仿真。仿真結果見表8。圖6和圖7為目前條件下進行的瞬態結構分析。此外,還對3種銑削操作即槽銑、孔銑和階梯銑削進行了仿真分析,並繪製了各種圖形。由於篇幅限制,只介紹了Fig.8-10中的幾張圖。圖8表示端銑的應力隨時間的推移而逐漸增大。在機械加工中,時間段是主要的標準,因為它將影響立銑刀的壽命,進而影響工件的質量。同時,加工過程中作用在立銑刀上的應力也會影響立銑刀的壽命。特別是在銑削加工中,立銑刀所做的工作必須在時間內完成,以優化應力,因為時間和應力都是相互關聯的。這一點已經得到了正確的實現,在圖9中顯示了應力和應變之間的關係(應力隨著應變的增加而增加)。最後,圖10表示應力與時間段的關係。它清楚地表明,每當立銑刀使用量增加時,立銑刀上的應力就會增加。根據分析和繪製的圖表,可以看出以下幾點。
1. 優化設計的立銑刀上觀察到的應力較小。
2. 與現有文獻中的數值相比,立銑刀上的切削力有所減小。
3. 根據新的優化設計,立銑刀的壽命(使用量)得到提高。
4. 根據計算出的切削力,觀察到了Ti-6Al-4V銑削時的立銑刀壽命。
5. 模擬值和計算值比較接近,可以作為進一步研究的潛在方向。
表8 加工條件和馮米斯應力
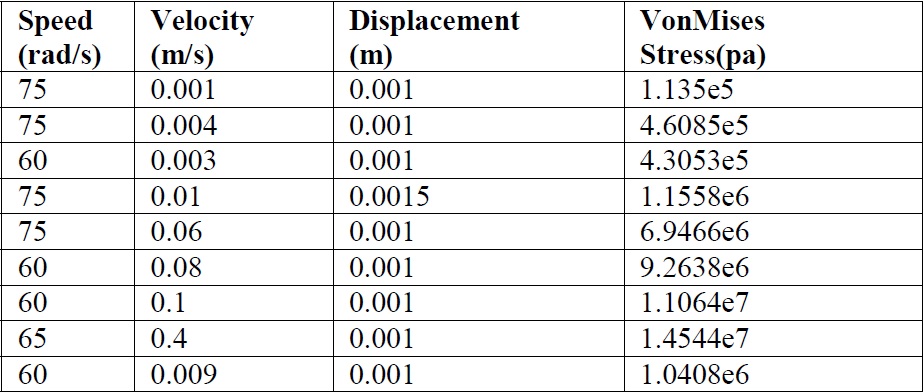
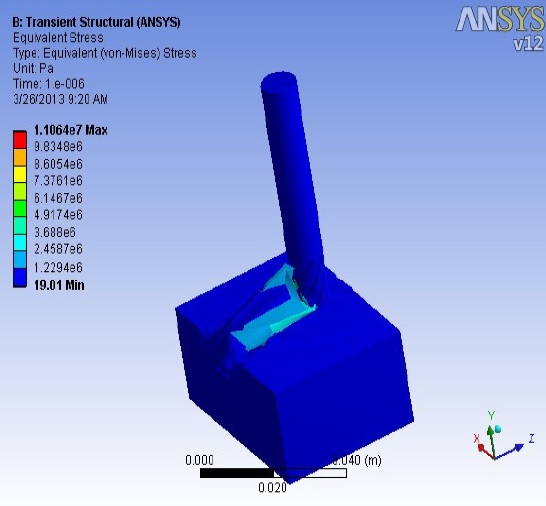
圖6 當量應力-1
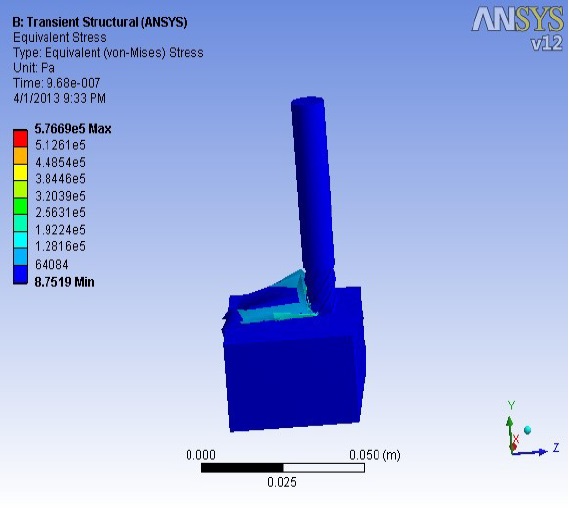
圖7 當量應力-2
%20vs_%20minimum%20and%20maximum%20Stress%20(pa).jpg)
圖8 時間(s)與最小和最大應力(pa)的關係
%20vs_%20Strain%20during%20end%20mill%20tool%20analysis.jpg)
圖9 端銑刀分析過程中,應力(pa)與應變的關係
6. 結論和今後的工作範圍
本文利用立銑刀幾何方程提出了一種在銑削Ti-6Al-4V時計算立銑刀切削力的方法。考慮了銑床的標準切削條件,合併計算了切削速度、切削力、功率,以提高立銑刀的性能。利用Autodesk Inventor開發了包括刀片在內的立銑刀優化設計,並利用ANSYS進行了仿真。得到的結果表明,預測力和模擬力比較接近。根據這些觀察結果,決定開展進一步的工作,在考慮適當的加工參數的情況下,對銑削Ti-6Al-4V時的端銑的動態應力和力進行實驗驗證。