New strategies for orthopedic CoCrMo parts machining
2020-04-14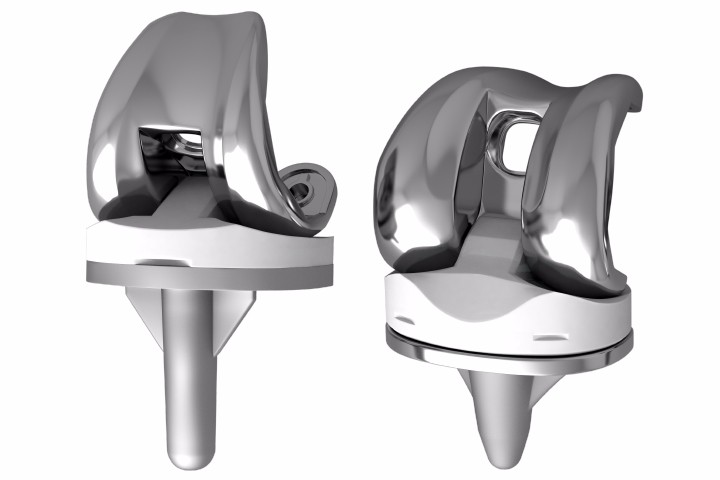
Today, there is an increased demand for orthopedic replacement and rehabilitation devices. Medical parts include artificial joints as well as artificial plates, rods and nails used to repair or reinforce body parts damaged by accidents or illnesses.
With the general increase in human life expectancy, more and more elderly people are suffering from bone and osteoporosis, which has led to a growing demand for orthopedic replacement devices. Global weight gains and obesity trend human skeletal joints are under pressure of diameter. Gradually, most people's lifestyles are changing, from lack of physical exercise to increased participation in sports, further increasing the need for body position swaps. Through the development of emerging economies, it is increasingly predicted by global research institutes that the global orthopedic devices market will grow to a value of 50 billion euros (US$53 billion) by 2024.
Competition drives cutting tool development
In the highly competitive orthopedic parts market, five major suppliers expanded their market share by about 85%, with the other 200 or so companies competing for the remaining share. Part processing methods. Through the application of new materials, the implant becomes stronger, lighter, and can last up to 25 years in the body. In this way, orthopedic devices are part of the entire consumer lifestyle market moving towards personalization; medical device manufacturers are thinking of ways to customize their products to suit patients' needs for physical appearance and other alternatives. Product differentiation has become a key competitive advantage. As a result, machine tool manufacturers seek to develop solutions that enable them to quickly machine complex shaped parts, while cutting tool manufacturers focus on developing cutting tool technologies that offer higher speeds and sizes. Advanced manufacturing technology solutions include 3D printing technology for machining and advanced cooling technology.
Typical parts
Orthopedic instruments include hip and knee joint sites, artificial elbow and fracture joints, incisional rehabilitation instruments, spinal plates and various rehabilitation nails, rods and fasteners. The key requirements for these components are strength, reliability, light weight and biocompatibility.
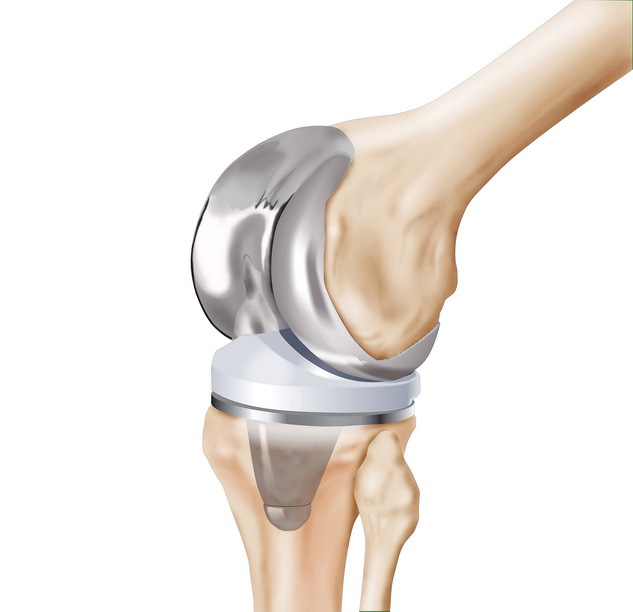
Machining challenges
For bone and knee implants, the most common workpiece material is cobalt chromium, but titanium is growing in use at the same time. Typical cobalt chromium alloys include CoCr28Mo6 and others, while Ti6Al4V titanium alloy is the most commonly used material.
The titanium alloy is light and very strong. It will harden and twist poorly during processing. On a centralized cutting edge and knife surface. High temperatures, large cutting forces and high friction in the chip channel can cause crescent wear and failure of the cutting mill. The material has a minimum modulus of elasticity, which is advantageous in some implantation applications, but the material bounces back from the cutting edge during machining, requiring close attention to the sharpness of the cutting tool.
Coolant Requirements
The materials used in the processing of orthopedic implants often produce excessive velocity and require the use of a coolant. However, the use of conventional coolant is usually extremely restrictive to prevent contamination of parts. After processing, the conventional coolant needs to be cleaned, a time-consuming and costly process. In terms of employee health, safety and handling policies, the coolant itself can cause environmental problems. Another cooling technique uses supercritical carbon dioxide (scCo2) to dry this supercritical scCo2 as a mediator to transport the dried, powerful catheter to the cutting zone.
When CO2 is compressed to 74 bar (1,070 psi) at 31 C, it becomes supercritical when transported to the cutting zone, and although it does not create low temperature material like liquid nitrogen, the supercritical CO2 expands and forms dry ice. In this state, it will fill the container like a gas, but with a density similar to a liquid. As a result, new coolant solutions bring higher cooling efficiency and use existing systems that use high-pressure water/oil, micro-lubrication (MQL), liquid CO2 and liquid nitrogen.
3D printed parts
Another non-traditional manufacturing technique that is becoming increasingly common in the production of orthopedic instruments is 3D printing, a process that uses titanium and cobalt chromium alloy powders to produce complex, near net-formed parts. In the medical industry, selective laser melting (SLM) technology is used to melt the powder and create the parts layer by layer. The process allows medical device manufacturers to customize parts with special contours and dimensions for patients. From there, a uniform and consistent microporous surface can also be produced, thereby accelerating the parts and the body. For finishing, parts produced by 3D printing retain most of the processing characteristics of the metal they are made of. However, such parts may have to undergo post-printing treatment to mitigate uneven stresses created during the process. In addition, part clamping can be a challenge later in the process due to the near net shape and complex contours of the part.
Replacement parts
A total knee replacement usually consists of three basic parts: a contour metal (cobalt chrome or titanium) part called a femoral part, which is attached to the end of the femur (thigh bone). The part, which is fixed to the top of the calf tibia, consists of a short shaft or keel used to support the alignment surface of the protruding edge of the band. The last one is made up of plastic bearing inserts between metal parts that enable free movement of the joint.
Similarly, a hip replacement consists of three main parts: a metal femoral stalk with a femoral cap or head at the top, which is inserted into the top of the femur or hip. Kit. The neo-alinea bearing inserts in the knee joint and the plastic cups in the lumbar joint are usually machined from UHMWPE (ultra-high molecular weight polyethylene).
Combination manufacturing method
Metal alloy parts for orthopedic implants must have an excellent surface finish, both of which are directly aligned to reduce wear on plastic parts while allowing for a 20-year extended life expectancy of the joint. For example, in knee displacement, the femoral component and tibial bracket must be absolutely smooth to protect the plastic bearing inserts from wear and tear.
As a result, the manufacture of orthopedic components often requires grinding after milling operations to achieve a sufficiently fine finish. However, grinding is time consuming and can affect overall manufacturing efficiency and volume. In addition, the grinding process also generates high temperatures and stresses on the base parts, causing dimensional errors in the parts and affecting the strength and performance of the parts.
Often, advanced cutting mills and high-speed milling strategies can improve the grinding process, or in some cases replace it. The purpose of milling is to produce a burr-free profile and an excellent surface finish, and to achieve a specific desired surface quality, dimensional and dimensional accuracy. Since the defined surface shape and structure has been achieved during the milling process, the timing of the post-processing process such as polishing (if any) can be changed alternatively. When it comes to cutting end mills, the same is true for long-lasting, reliable cutting end mills and maximizing tool life and expectations.
Typical application is the machining of femoral parts made of cast cobalt-chromium alloy on 5-axis milling machines using ball-head end mills. High-speed profiling strategies and high-performance end mills eliminate the grinding process. The result is a machining cycle of 11 minutes per part, which is 50% shorter than the previous method. By replacing milling with grinding of the articulated surfaces, the generation of scrap parts is eliminated. The overall carbide end mill is made from a specialized carbide material and a hard polished TiAlSiN coating to ensure excellent metal removal and smooth cutting, resulting in a superior surface finish or minimal polishing time.
Multiple processing operations
The complex contours of orthopedic parts often require the use of several specific special cutting end mills. For example, some osseoids involve seven machining operations, including roughing, bottom roughing, bottom finishing, chamfering, and T-groove root-cutting, which require minimal manual intervention to achieve excellent surface quality and reliable cutter performance, thereby ensuring optimal alignment, lowest cost, and highest quality.
In the past, when completing a wide variety of operations, special cutting mills were required to achieve each desired profile, size and surface finish. Special cutting mills require significant design and development time and expense, and due to their reduced size, their cross-linking times may be extended and their availability limited.
The new approach is to develop and use standardized cutting mills that can be produced efficiently in these applications, and these cutting mills must also retain sufficient size to be used to machine other similar parts in the orthopedic industry.
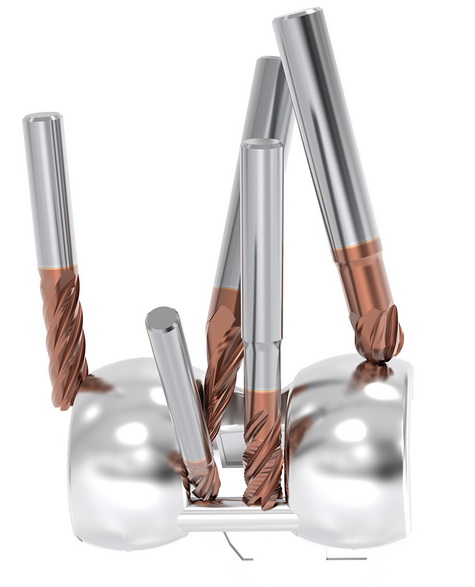
Conclusion
Global demographic and economic growth trends indicate that the demand for complex orthopedic parts will continue to grow. At the same time, consumer expectations and the determination of medical component manufacturers to win the race have combined to drive the development of personalized orthopedic components that can meet the unique needs of different patients. Amazingly, different part sizes can be achieved by using standardized cutting mills that are more flexible and cost effective than the custom cutting mills previously used to produce such parts.
Note: Standardized cutting tools and application support offer many advantages.
Some of the design details of orthopedic instruments differ between manufacturers, but there is also a lot of commonality in the products, as all body structures are essentially the same. Although manufacturers have traditionally used custom cutting mills to machine these parts, there is now a broad and effective common base on which cutting mills can be made to efficiently machine some common components in a variety of materials. And in the past, this required the manufacture of a complete set of custom cutting mills.
WOTEK has carefully analyzed the manufacturing process of medical parts and used more than 10 years of experience in medical parts processing to develop a series of standardized end mills for machining cobalt-chromium alloy orthopedic parts. The goal is to convert specialized cutting end mill solutions to these cutting end mills with performance features that can be used for a wide range of parts and materials.
It eliminates the design, prototyping and testing process of custom cutting mills and therefore saves a lot of time. Since cutting end mills are standard cutting end mills, they are listed in our product catalog and are available worldwide through WOTEK distribution centers. Eventually, these cutting mills began to be produced in large quantities, thus reducing the cost of subcutting mills.
The new range of cutting mills includes 9 different groove types and a total of 39 products. By offering different models, rounded cross-sections and sizes, it is possible to expand the range of products currently relatively available.
These cutting mills are designed to machine specific components common to a variety of orthopedic parts, including knee and hip joints, but are also suitable for machining bone plates, spine parts and other parts. Each of the nine different groove types has a specific function or application area, including roughing, finishing, T-slot root cutting, super finishing of complex profile parts, etc.
For example, WOTEK end mills are designed for roughing and are available in a variety of models with 4, 5 and 6 flutes, allowing for overall roughing and near-net-forming operations. The cutting end mill is a 4-sided tapered ball end mill for 5-axis finishing of precise part details such as boxed components of the femoral condyle.
Standardized cutting mills are made of a tough, hard alloy material (12% cobalt content).