Machinability of Cobalt-based and Cobalt Chromium Molybdenum Alloys - A Review
2020-05-13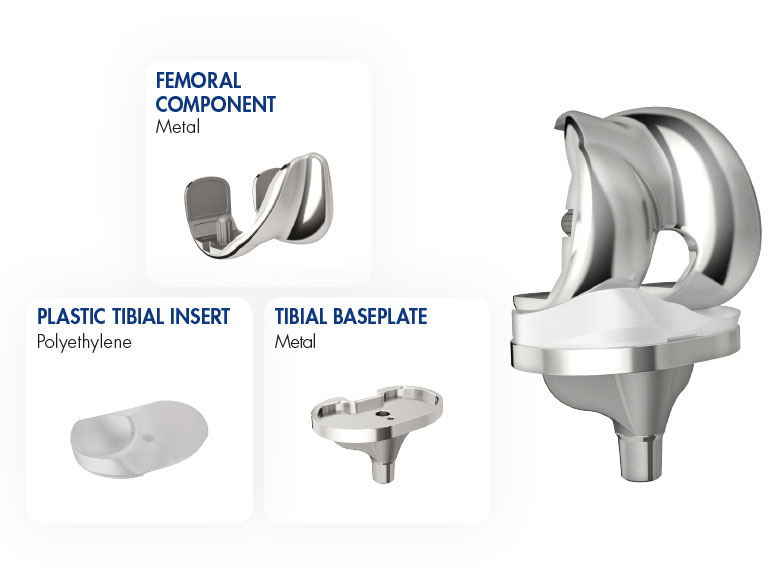
Abstract
Cobalt chrome molybdenum alloy is considered as one of the advanced materials which is widely gaining popularity in various engineering and medical applications. However, it is categorized as difficult to machine material due to its unique combination of properties which include high strength, toughness, wear resistance and low thermal conductivity. These properties tend to hinder the machinability of this alloy which results in rapid tool wear and shorter tool life. This paper presents a general review of the materials’ characteristics and properties together with their machinability assessment under various machining conditions. The trend of machining and future researches on cobalt-based and cobalt chromium molybdenum alloys are also discussed adequately.
1. Introduction
Cobalt chromium alloy is acknowledged as an attractive material in the application of many engineering fields such as aero-engine, nuclear, biomedical and gas turbine. It is mainly attributed to its excellent characteristics such as corrosion resistance, wear resistance, high creep resistance, heat resistance and good biocompatibility. In biomedical application, cobalt chromium is widely consumed in the manufacture of orthopedic implants, especially for implants of heavy-loaded joints, such as knee and hip due to its excellent wear and corrosion resistance. Figure 1 shows the various applications of cobalt based alloys in various engineering and medical products. The presence of molybdenum in the composition of cobalt alloys reduces the grain size thus enhances the strengthening of solid solution and subsequently improves the mechanical properties of these alloys. Besides, chromium (Cr) particles will form as a protective oxide layer on the surface to provide better corrosion resistance in the body environment. In machining aspect, since these alloys maintain their strength and hardness at elevated temperatures, hence machining remains difficult to perform. Low thermal conductivity, high strain hardening, high hardness at elevated temperature and high wear resistance are the reasons for the poor machinability rating of cobalt chromium molybdenum alloys. This paper discusses on the past researches in the machining of cobalt chromium molybdenum alloys.

Figure 1: Applications of cobalt base alloys in engineering and medical products
2. Classification of Cobalt Chromium Molybdenum alloys
Cobalt-based alloys were first introduced by E. Hayes as cobalt chromium or “Stellites” at the beginning of the twentieth century. The primary structures of cobalt base alloys depend on the carbide form in the Co matrix and the grain boundaries to increase the mechanical strength. The comparison of mechanicals properties between cobalt chromium molybdenum alloys and titanium are showed in Table 1. Cobalt chromium molybdenum alloys are normally manufactured by casting process (Co-Cr-Mo alloy (F75), wrought and forged process (Co-Cr-W-Ni alloy (F90), Co-Ni-Cr-Mo alloy (F562), Co-Ni-Cr-Mo-W-Fe alloy (F563) and powder metallurgy technique. As a result, the components that are produced from casting processes exhibit better creep strength and toughness meanwhile components that are produced from wrought and forged process have higher strength, and enhanced fatigue and fracture resistance. Moreover, powder metallurgy technique is adopted when producing complicated and near-net-shaped products. The cast-able CoCrMo alloy has been widely used for many decades in dentistry field and recently, it is also used in making artificial joints. The wrought CoNiCrMo alloy is relatively new, now utilized in the fabrication of stems of prostheses for heavy-loaded joints such as knee and hip. According to American Standards for Testing and Materials (ASTM), there are four types of CoCr alloys which are recommended for surgical implant applications, they are: (1) cast CoCrMo alloy (F75), (2) wrought CoCrWNi alloy (F90), (3) wrought CoNiCrMo alloy (F562), and (4) wrought CoNiCrMoWFe alloy (F563).
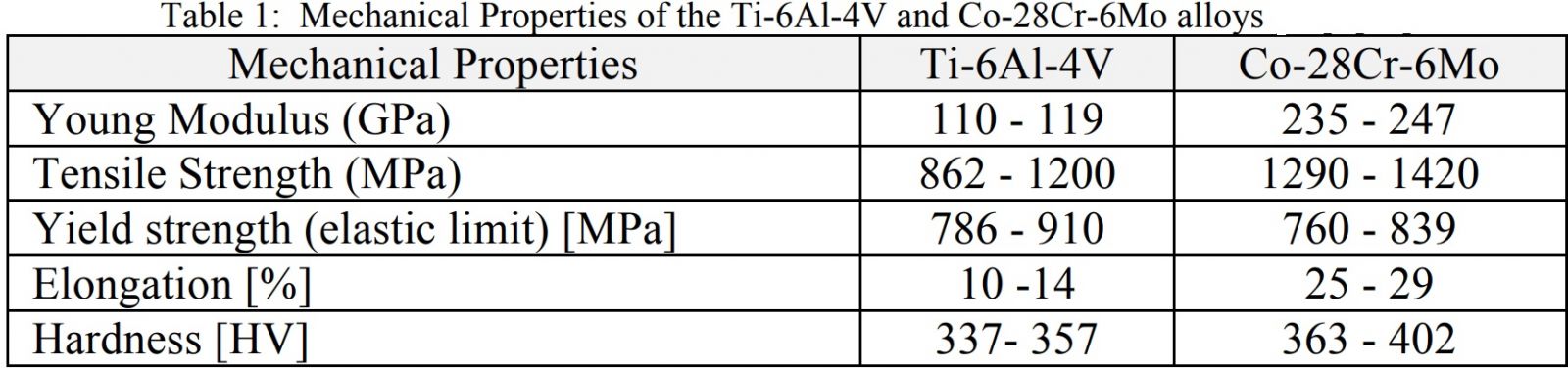
Table 1: Mechanical Properties of the Ti-6Al-4V and Co-28Cr-6Mo alloys
3. Machinability of Cobalt Chromium Molybdenum alloys
Usually, the term machinability can be defined as how easy a material can be machined or cut to a desired shape with respect to the tooling and process conditions with consideration on the surface finish and tool life. For cobalt chromium molybdenum based alloys as shown in Figure 2, the machinability properties are equivalent to other advanced materials such as nickel alloys and titanium alloys which are categorized under difficult to cut materials because of their unique combination of features such as high strength, toughness, high wear resistance and poor thermal conductivity. Figure 3 shows the polar diagram of Difficult-to-Cut Rating (DTCR) or machinability rating of CoCrMo alloys. The polar diagram displays the comparison of material properties of difficult-to-cut materials with reference to free machining steel or medium carbon steel (0.45%C). The impact of high hardness of CrCoMo alloys increases the deformation resistance which leads to an increase in the cutting force and cutting resistance as well. Usually, machining of high hardness materials such as cobalt chromium molybdenum alloys results in many undesirable problems, which is often associated with short tool life of cutting tools and poor surface quality due to heat generation and plastic deformation. The low thermal conductivity of the CoCrMo alloys tend to increase the tool wear of the cutting tool due to the large heat that is transmitted into the cutting edge during the cutting process. Minimizing the cutting speed, feed rates, depth of cut and at the same time using a sharp cutting edge tool during machining reduce the high cutting temperature at the cutting zone. The reduction of the cutting feed provides an additional effect on reducing the mechanical load on the cutting tool. In addition to the above parameters, some other factors also influence the level of machinability rating of CoCrMo alloys such as tool geometry, cutting tool materials, cutting conditions, material conditions and the type of cooling and coolants used. Several recommendations were proposed by Ezugwu when machining difficult-to-cut high temperature materials, which include, using a positive rake angle tool to minimize the work hardening of the machined surface and built-up-edge by shearing the chip away from the work piece. Furthermore, the sharp cutting edge is able to improve the surface quality by preventing build-up of materials during machining. At the same time, tooling and machines should be purely secured to avoid chatter and vibration which have significant effect on the surface finish and tool fracture.
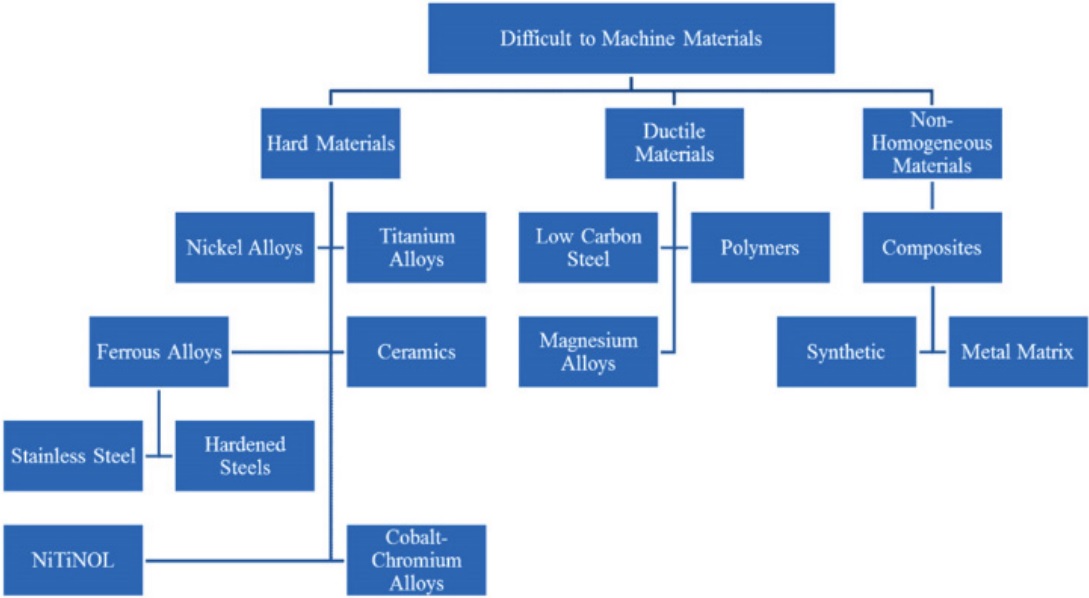
Figure 2: Categories of difficult-to-machine materials
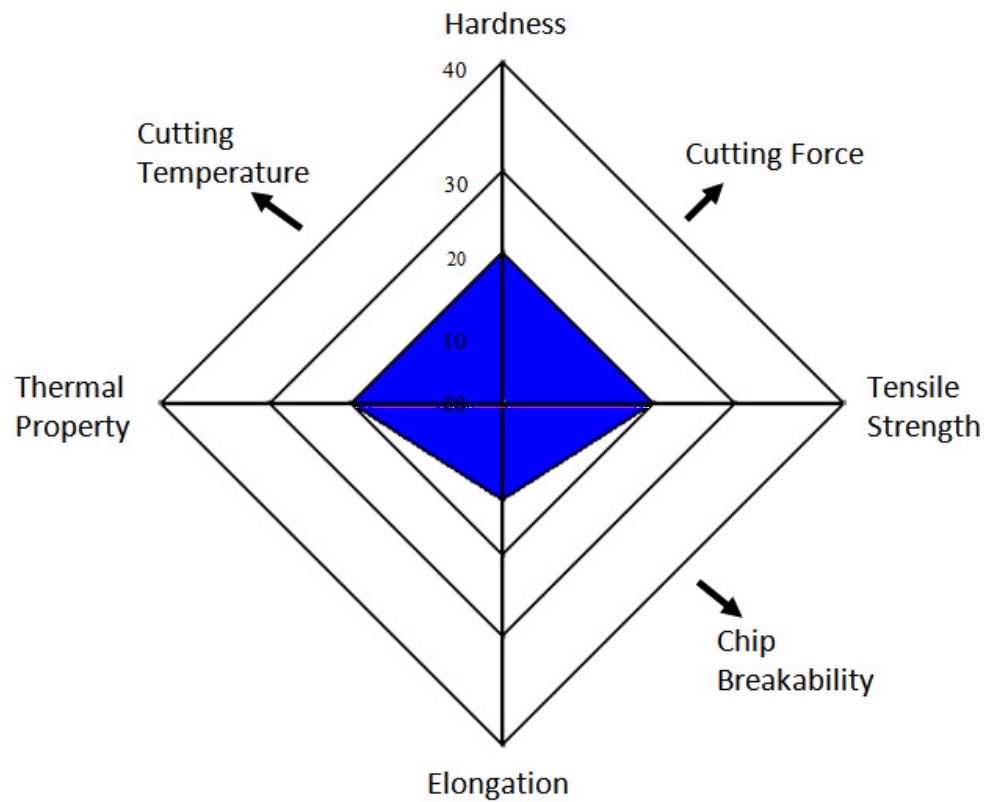
Figure 3: Material properties of CoCrMo alloys
4. Research in machining of cobalt base and CoCrMo alloys
Research on machining of cobalt-based alloy has begun a long time ago when it was widely used in manufacturing and aerospace industries. Back then, all the researches were focused on improving the material properties such as hardness, toughness, strength, wear resistance, corrosion resistance and high temperature resistance. Based on the material properties, cobalt chromium molybdenum alloy is an improved material from the cobalt family that is used for various biomedical applications. As reported by the previous researchers, research on machining these materials, especially cobalt chromium molybdenum alloys is still limited compared to titanium, stainless steel and inconel. Usually cobalt chromium molybdenum alloys are processed by non-traditional machining techniques such as electrical discharge machining (EDM), laser beam machine (LBM) and traditional machining techniques such as turning, milling and grinding machining process. The research gap on machining of Co based and CoCrMo alloys since 2006 until 2015 is shown graphically in Figure 4. Within those years, facing and turning were the dominant operations investigated by various researchers for cobalt-based whereby at the same time optimum cutting conditions were established until the year 2013 whereby CoCrMo alloy was introduced. This alloy is regards as one of the highly potential metallic biomaterials to replace cobalt based alloys due to the presence of large amount of Ni, which is a high-risk element that could cause allergic reaction in human body. CoCrMo alloy is expected to be used for implants and medical devices that are fabricated using machining operation, especially for the required surface finish and dimensional accuracy.
Various machining methods and modeling techniques were explored by various researchers to optimize the cutting conditions in order to predict the machining performance and achieve higher efficiency. Aykut et al. investigated the effects of machining conditions on tool wear, cutting force and chip morphology by using Design Experimental Method (DOE) approach during symmetric face milling of stellite 6 superalloy when using PVD coated and uncoated carbide tools under dry machining. Their results showed that depth of cut and feed rated significantly influenced the tool wear and cutting force. Variation of chip formation and chip morphology was observed on the chip edge with variation in feed rate. Bagci and Aykut conducted a study on the influence of the cutting conditions on surface roughness using Taguchi method during face milling stellite 6 alloy. Results showed that surface roughness values are significantly influenced by the cutting speed, feed rate and deep of cut. Genetically Optimized Neural Network System (GONNS), Genetic Algorithm (GA), Artificial Neural Networks (ANNs), Response Surface Methodology (RSM) are other modeling techniques that are used to optimize the process parameters in machining operations. Aykut et al. carried out machinability test during symmetric face milling of stellite 6 by using ANN modeling under dry condition using uncoated carbide tool. The cutting force was predicted by ranging the feed rate, cutting speed and depth of cut. Subsequently, Aykut et al. used both models to study the relationship among surface roughness, cutting force and machining parameters. Time and cost constraints are necessary to reduce the manufacturing costs of the end product. Some of these elements were obtained by machining, which are necessary to optimize the machining parameters of these products. Several researchers had conducted experimental study on machining of cobalt-based refractory material to establish the optimal cutting conditions for different cutting parameters. They used several optimization techniques based on RSM method with Sequential Quadratic Programming algorithm and Kriging interpolation for a constrained problem.
Bruschi et al. investigated the influence of cutting conditions on tool wear, surface integrity and microstructure during semi-finishing turning of CoCrMo alloy using PVD TiALN coated carbide insertunder conventional lubrication conditions. They found that feed rate is the most influenced parameter affecting the cut surface quality and tool wear. Higher feed rate provides higher impact to the tool wear and surface finish and simultaneously reduces the tool life of the cutting tool. Adhesion wear and chipping were the dominant wear operating at the rake and a flank faces when high feed rate is applied. Another study by Song et al. was performed to evaluate the best method in turning CoCrMo alloy using elliptical vibration cutting and ordinary cutting without tool vibration in order to to assess the roughness and hardness of the finishing surface, as well as the tool wear. Results showed that elliptical vibration cutting performed better against the ordinary cutting in terms of reducing the micro chipping, tool wear and work hardening which resulted in better mirror finishing.
H. Shao et al. studied on the machinability of stellite alloys with uncoated and coated carbide tools in dry turning process where cutting conditions were set at cutting speed of 16, 27 and 43m/min, feed rates of 0.20 and 0.25mm/rev, and depth of cut of 0.3mm. Their study showed that the major failure mode of coated tool is uniform flank wear at lower cutting speed. Adhesion, diffusion, chipping and chemical wear were observed at relatively high cutting speed and feed rate. The coated tools outperformed uncoated tools in terms of tool life when machining stellite 12. Pedro Ferreira et al. conducted a study on milling operation of Ti-6Al-4V and Co-28Cr-6Mo alloys to evaluate the effect of cutting speed on cutting temperature and cutting force as well as to determine which material is the most difficult to machine. Results showed that for each cutting speed, the tangential and axial forces (Ft and Fa) are always higher for Co-28Cr-6Mo alloy than Ti-6Al-4V alloy. Bordin et al. presented the experimental results on surface integrity when turning CoCrMo alloy under dry machining for biomedical applications. Outcomes of the study proved that cutting speed and feed rate are the major effect of the surface integrity. The increment of feed rate tends to increase the compressive stresses due to high strain rate, while cutting speed has a reverse effect due to the increment of the cutting temperature.
5. Coolant strategies for machining cobalt-based and CoCrMo alloys
Surface integrity is very important for medical applications, especially for surgical implant and devices. Machining operations generally induce residual stresses through the outer layer of the workpiece machined surface which present potential risks in terms of crack initiation, propagation and affect the tribo-corrosion resistance of surgical implants. Coolant consumption of cutting fluids remains very important and many researchers had studied the effect of coolants on tool wear, cutting temperature and cutting force on surface integrity of machined surface when facing and turning cobalt based alloys. The capability of cutting fluids to remove the heat generated due to friction during machining operation provides better tool life, acceptable surface finish and better dimensional tolerances. As shown in Figure 5, many researchers had used dry machining due to the detrimental effects of cutting fluids such as environmentally harmful, difficulty in disposing, and only recently focused on minimizing the use of cutting fluids in machining CoCrMo alloys. Moreover, dry machining is considered as the best alternative in replacing cutting fluids which eventually reduces the machining cost and ecological hazards. Dry machining is also known to have free pollution, no health threat to operator, low disposal and cleaning cost, no allergy to skin and minimizes the machining cost. Nevertheless, dry machining has its limitation which is mainly due to the high heat generated at the cutting zone as a result of friction and adhesion between the tool and the workpiece. This phenomenon can increase the tool wear and reduce the life of the cutting tool. Karpuschewski et al. investigated the effect of different cooling systems on surface integrity using a ceramic tool during turning of CoCrMo alloys. They reported that the emulsion under full jet cooling and dry machining provide minimum effects on the surface layer of the CoCrMo alloys. Figures 6 summarizes the research gaps on the machining responses when machining cobalt-based and CoCrMo alloys since the past decade. Surface integrity, tool wear and cutting force had been investigated quite extensively by many researchers.
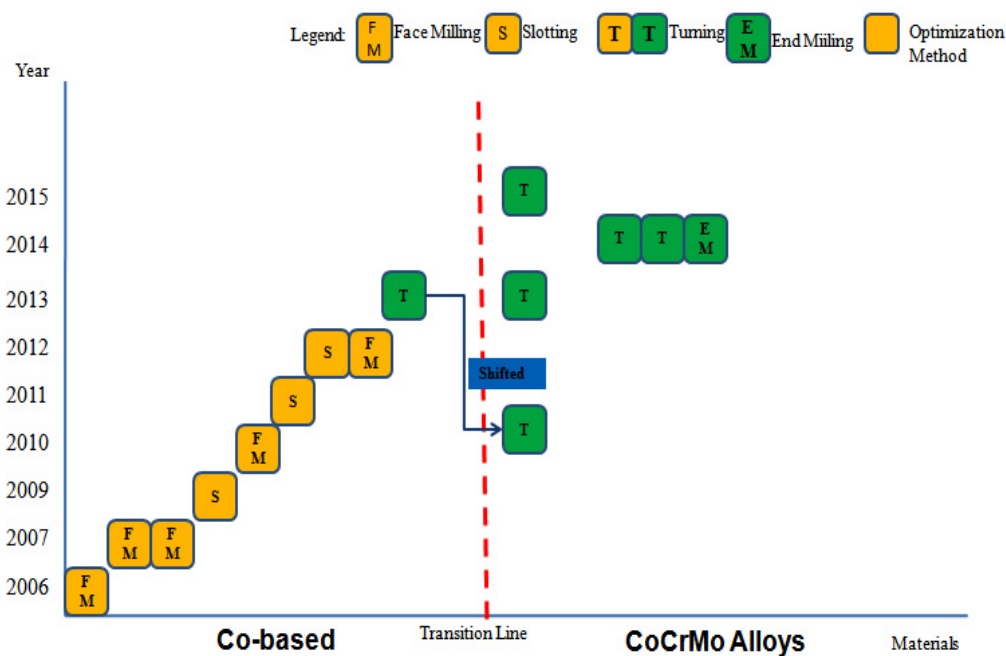
Figure 4: Machining trend for cobalt-based and CoCrMo alloys
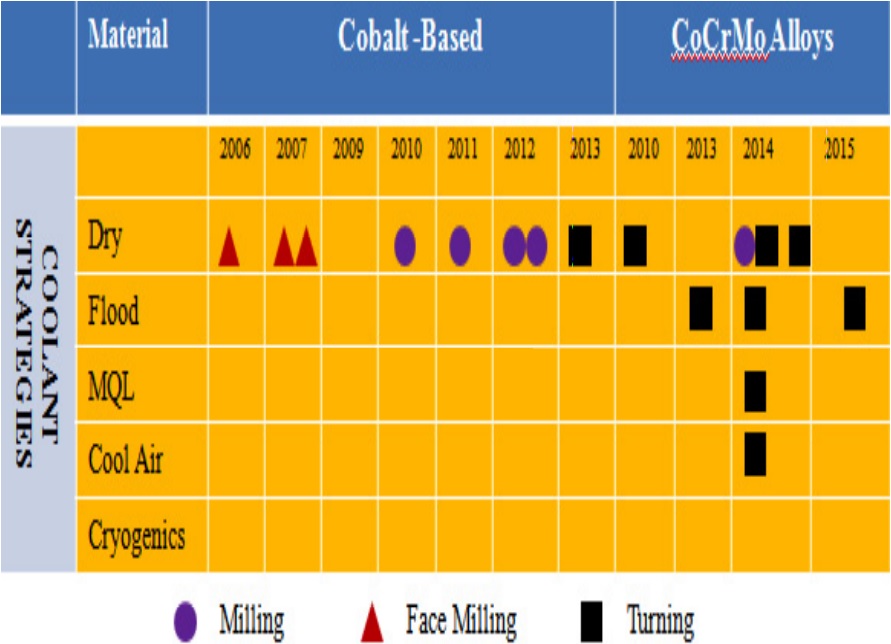
Figure 5: Coolant strategies for cobalt-based and CoCrMo alloys
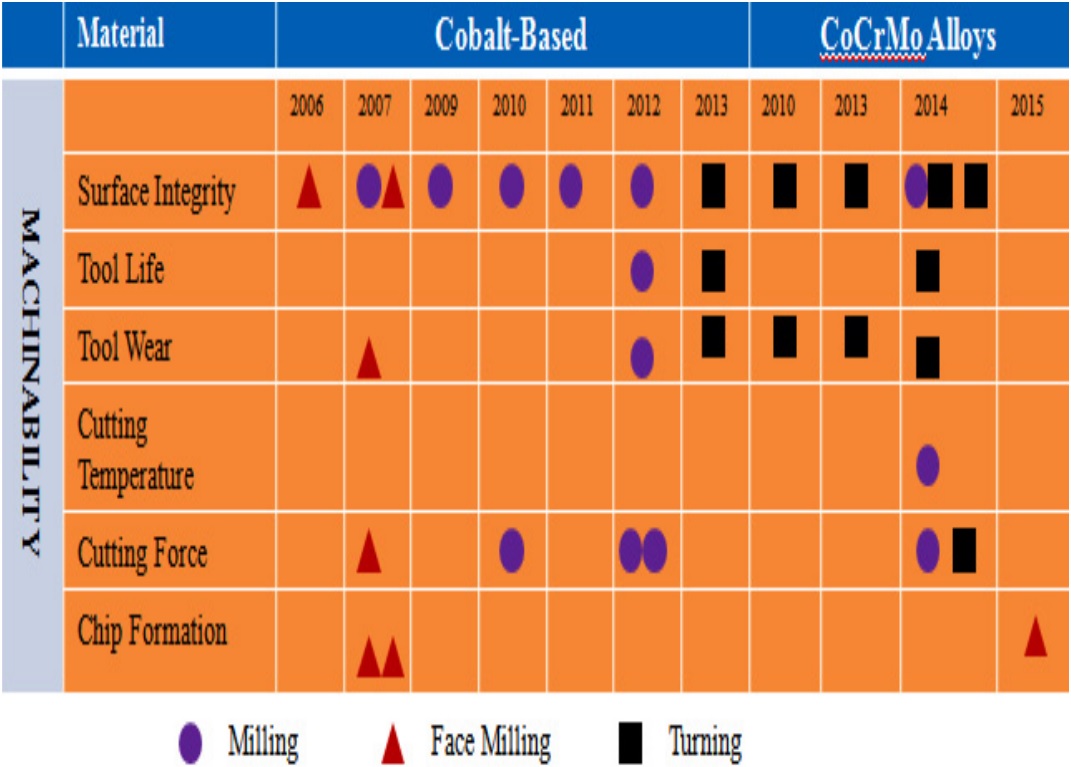
Figure 6: Machinability studies on cobalt- based and CoCrMo alloys
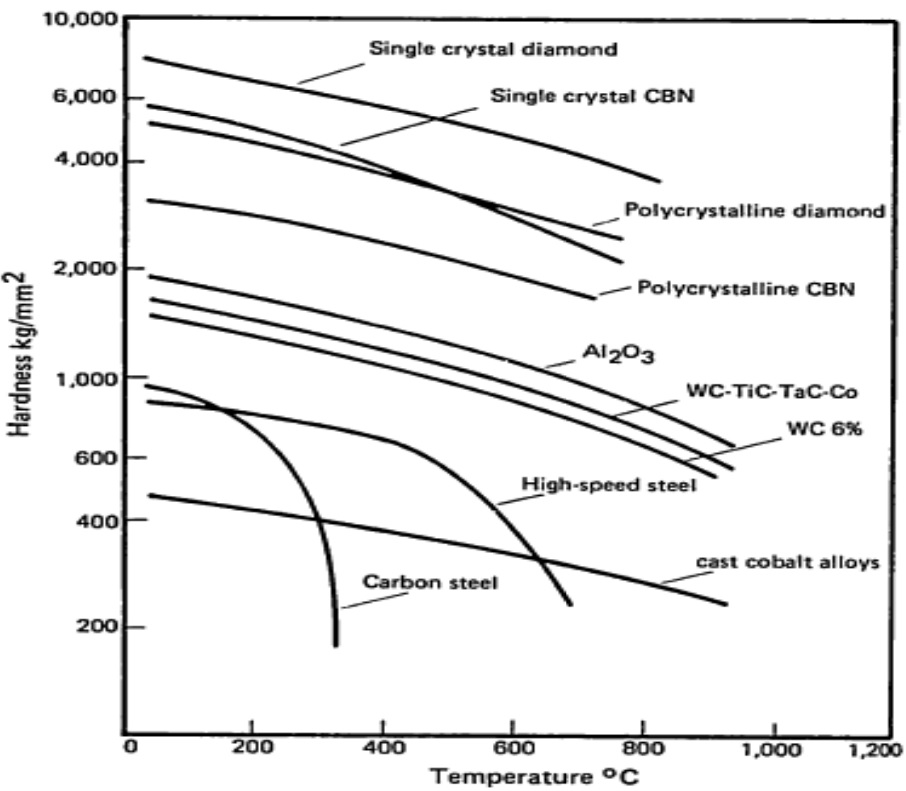
Figure 7: Hot hardness versus temperature for cutting tool materials
6. Tool material for machining cobalt base and CoCrMo alloys
In machining operation, cutting tool material is the most important aspect in the cutting process. The high thermal and mechanical stresses induce at the cutting edge of the tool are major concerns especially during machining of difficult to cut materials such including titanium, nickel and cobalt chromium alloys. To overcome this situation, cutting tools are required to possess these characteristics; high toughness, hot hardness at the elevated temperature, chemical and thermal stability and good thermal shock resistance. In the early development of cutting tools, it is very difficult to find a suitable cutting tool that meets all the above characteristics. Usually, coating is opted as the best solution to provide an uncoated tool with more hardness, toughness and stability at higher temperature. When cutting at a high speed, tool wear becomes a very important factor. Thus, not only the cutting tool should retain the above characteristics, it should also possess high resistance to wear. The high temperature at the cutting zone can cause most of the cutting tool to lose their hot hardness, which can shorten the tool life and at the same time, increase the wear rate. Therefore, the machined material, cutting tool material, cutting conditions, tool wear and cooling medium are the influencing factors which affect the level of the temperature generated at the cutting area. Figure 7 shows the effect of the temperature on the hardness of several types of cutting tool materials. Machining of hard to cut materials such as cobalt chromium alloys always result in the difficulty of selecting the appropriate cutting tools. Failure to select the correct type of cutting tool material may jeapordize the machining performance of the cutting tool as a result of rapid flank wear, notch wear, edge chipping, crater wear, plastic deformation and tool failure. There are several cutting tool materials that were used by previous researchers in machining the family of cobalt superalloys material. These include uncoated carbide tools, PVD coated tools such as TiN/TiCN/Ti, TiN, TiN/TiCN/TiAN, TiN/TiCN, AlTiN, TiAlN, TiSiC and CVD coated tools including TiN/TiCN/Al2O3, TiCN/Al2O3/TiN.
7. Conclusion
As presented in this article, it can be concluded that cobalt-based and CoCrMo alloys are gaining popularity in the aerospace and medical applications due to their excellent mechanical properties such as corrosion resistance, wears resistance, high creep resistance, high hardness, heat resistance and excellent biocompatibility. Machining these materials faced many challenges and complications, mainly caused by their high strength, toughness, high wear resistance and poor thermal conductivity. Based on huge applications of cobalt-based and CoCrMo alloys, more studies need to be conducted especially in the conventional machining processes to overcome the problems of poor machinability of these materials. Future machining researches are summarized in Figure 5 and Figure 6 to improve the performance of cutting tools and machinability of cobalt-based and CoCrMo alloys. Carbide tools remain the most popular tool materials by many researchers as compared to others tool materials such as HSS, ceramic and CBN. New coolant strategies such as cryogenic, cool air, high pressure coolant and MQL with nanoparticles are among the future potential research topics in machining these alloys. Studies on cutting temperature, chip formation, surface integrity, residual stresses and wear mechanisms are still lacking and provide great opportunity for future research especially when using high speed machining.
Acknowledgement
This work was supported by the Basic Science Research Program of the NRF funded by the Ministry of Education of Republic of Korea (2016R1D1A3B03934974), and Research Management Centre of Universiti Teknologi Malaysia through the RUG funding.