Efficient milling of cobalt, chromium, molybdenum(CoCrMo) and titanium alloy hip joints for medical prosthetic implant parts
2020-03-23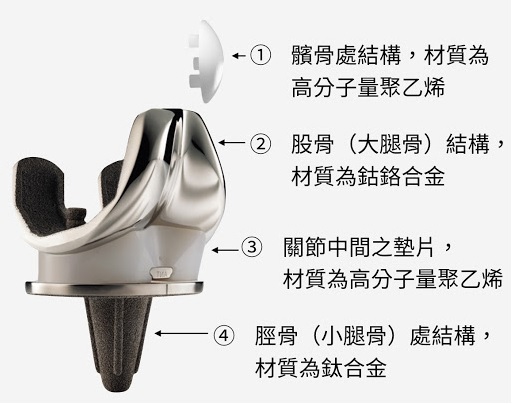
The world's science, technology and economy are constantly developing rapidly. On the other hand, the aging trend of economically developed countries has intensified, and the population of some developing regions and countries is still growing. In this situation, the demand for the medical equipment industry will inevitably increase steadily.
In the past, most of the advanced medical equipment companies were concentrated in developed countries such as Europe, the United States, and Japan. At present, this trend is transferring to Taiwan and Asia.
In the past, most of the advanced medical equipment companies were concentrated in developed countries such as Europe, the United States, and Japan. At present, this trend is transferring to Taiwan and Asia.
In addition to a variety of modern inspection, diagnosis and treatment equipment, medical equipment. It also includes a variety of surgical instruments are implanted into the human body, the functionally restored spine, artificial joints, prosthetics, dental parts and corresponding pads, screws, and other auxiliary equipment and living equipment. Among them, parts that require precision cutting are mostly implanted into the human body and parts for surgery. Because the materials used for these parts must be considered for their adaptability to blood, allergies to the human body, their corrosion resistance, durability, and their own weight should be as light as possible. Therefore, it is necessary to select some advanced materials such as titanium alloy, cobalt chromium molybdenum(CoCrMo) alloy, stainless steel, etc., and UHMWPE (high molecular weight polyethylene), zirconium and alumina ceramics, special resins and other materials. Composite materials such as CFRP (carbon fiber) and GFRP (glass fiber) are also available. With the continuous development of new materials, more and more advanced and suitable materials will be used for medical parts and equipment.
All the various materials, titanium alloy (Ti-6AL-4V) has good adaptability to the human body and is the most widely used. However, titanium has a low thermal transmittance, it is difficult to discharge the high heat generated during milling, and the cutting tool is easily damaged. Cobalt-chromium-molybdenum alloy (HRc40-45) has strong wear resistance, long reorganization, and it is more difficult to process than titanium alloy. Austenite and precipitation hardening are the two most used types of stainless steel. They are mostly used for small parts, such as connecting sheet metal and screws. Focusing on difficult-to-machine materials and complex part shapes, it is not easy to achieve efficient machining. In addition to optimizing the tool material to achieve efficient machining, it is also important to give highly performance of CNC machine tools. The following focuses on the prosthetic parts of hip, knee, spine, dentistry, etc., as well as the processing methods of various bone sheet metal, connection screws and advanced end mill tools currently used.
The main parts of the hip joint prosthesis are shown in Figure 1. The structure is modeled on the human hip joint. As shown in the figure, the stem of the prosthesis is inserted into the femoral bone marrow cavity, and the relative rotation between the head and the surface between the joint acetabulum and the metal cup of the prosthesis is used to realize the femoral Flexion and movement. Prosthetic femoral stem materials can be used; titanium alloy, cobalt chromium molybdenum alloy, ultra-low carbon stainless steel and so on. The inner and outer metal cups can be made of titanium alloy, ultra-low carbon stainless steel, etc. The acetabular material is made of non-toxic ultra-high molecular polyethylene. Titanium alloy blanks are mostly manufactured by thermostatic pressure processing. Cobalt-chromium-molybdenum alloy material is manufactured by casting. Stainless steel blanks are manufactured by forging.
However, the finished products need to be precision milling. The advanced tools of WOTEK end mills can smoothly achieving its precision cutting. The turning surfaces of the above parts, including the inner and outer cylindrical surfaces, conical surfaces, and spherical surfaces, by using turn milling.
However, the finished products need to be precision milling. The advanced tools of WOTEK end mills can smoothly achieving its precision cutting. The turning surfaces of the above parts, including the inner and outer cylindrical surfaces, conical surfaces, and spherical surfaces, by using turn milling.
The base of the turning tool needs special hard alloy with good thermal conductivity, its surface is coated with AlTiN coating, the chip breaker structure of a turning tool should make it easy to generate and remove chips. The chip breakers have a large rake angle and a curved cutting edge. They are most suitable for cutting titanium and heat-resistant alloys. Material, high quality surface. Spherical surface turning in a metal cup is generally difficult, but with this type of insert, the chips and heat can be smoothly discharged despite the constant cutting depth.
Cutting conditions and heat dissipation conditions for drilling difficult-to-machine materials such as titanium alloys are also extremely poor. Holes in prosthetic parts can be processed with solid carbide drills, which are characterized by the main cutting edge being a wave shape, which changes the structure of the negative rake angle near the center in the past, and balances the sharpness and wear resistance of the main cutting edge. The triple flank face of the drill is ground to make the length of the cutting edge "zero", which not only reduces the friction and wear of the flank face, but also reduces the axial force and improves the centering. Therefore, when tooling, it is both sharp and wear-resistant.
At the same time, a double-curvature spiral groove is made to smooth the chip removal. In order to particularly enhance the heat dissipation and cooling effect, a triangular coolant hole developed with a special TRI-Cooling scheme is made in the drill bit to make the coolant discharge speed high Increased, cutting heat can be quickly eliminated, the drill bit processing efficiency and life are greatly improved, and when the inner spherical surface is drilled, the burr is reduced and the drilling quality is improved. V2B, P6B ball nose end mills can still be used for inner spherical processing. Its base material is ultra-fine particle cemented carbide, the surface coating is high hardness and super wear resistance. (Al, Ti, Si) N single-phase nano-coating formed by zirconium technology, the hardness is as high as HV3700, and the oxidation starting temperature is 1300º. Good heat resistance. The coefficient of friction against high-hard steel at 800ºC is only 0.48. Greatly improve the abrasion resistance, resistance to defects, damage and other abnormal damage resistance, so that the processing quality is high and stable.
The taper holes on the spherical parts of the prosthesis can be replaced by helical milling with the combination of rotation and revolution by the helical milling type end mills with unequal helix angle vibration reduction; ① drilling first ② then turning The way that the tool rough and finishes the taper hole is turned (Figure 3), so that the process can be concentrated, the processing quality is reliable, and the man-hour is reduced, and the tool cost is reduced. The reasonable use of the above tools can ensure the smooth completion of the processing of the hip joint prosthesis surface.
The taper holes on the spherical parts of the prosthesis can be replaced by helical milling with the combination of rotation and revolution by the helical milling type end mills with unequal helix angle vibration reduction; ① drilling first ② then turning The way that the tool rough and finishes the taper hole is turned (Figure 3), so that the process can be concentrated, the processing quality is reliable, and the man-hour is reduced, and the tool cost is reduced. The reasonable use of the above tools can ensure the smooth completion of the processing of the hip joint prosthesis surface.
The complex outer surface of the knee joint can be processed with ball nose end mills, whose spiral grooves are spaced at different intervals, so the vibration resistance is good, and the quality of the processed surface is high. Its specially designed cutting edge structure shape (Figure 4) improves chip discharge performance. It uses materials by using wear-resistant and damage resistant, and has a long life. The cutting speed of cobalt chromium molybdenum alloy can reach 100m / min, and the feed rate can reach 3200mm / min. The disc with handles under the knee joint has a concave cavity on the upper plane, which can be used as a ball nose end mills for processing taper holes in the hip joint. Vibration reduction end mill machining. The holes there can also be machined with drills.
The bone plate is mostly used in the repair of fractures. It has a variety of shapes and a large amount of materials. The materials are titanium alloy (Ti-6Al-4V) and stainless steel. The main machining surfaces are profile, holes and chamfers. The surface processing can be described in this article. The substrate is an ultrafine carbide, and (Al, Ti, Si) N coating deposited by zirconium technology. End mill with good heat resistance, abrasion resistance and good cutting edge resistance. The complex machining methods of holes and chamfers in the past are: ① hole processing ② inner diameter forming processing ③ chamfering processing. At present, WOTEK uses the end mill to perform spiral hole milling at one time, which greatly improves the efficiency and processing quality.
Spinal implants are also made of titanium alloy, cobalt chromium molybdenum alloy, and stainless steel. The plane and curved surface should be processed with excellent vibration-resistant end mills. WOTEK's outstanding end mill (diameter 4 mm) is used in CNC compound machining center at a speed of 2400 rpm, feed speed; 380 mm / min. end mill’s back cutting(ap): 16 mm; End mill in the radial direction cutting(ae): 0.2 mm. Machining titanium alloy parts has achieved satisfactory results.
In addition to the above prosthetic parts, there are a large number of various types of screws, and the socket materials are using titanium alloys and stainless steel. Particularly difficult to machine are the deep and small holes (around Φ2) in these screws. The aspect ratio of the holes reaches nearly 30. In the past, gun drilling was used, although the rotation speed was high, but the feed rate was very low. WOTEK adopted an overall tungsten steel ultra-long drill bit, which can increase the feed rate by 4 times compared to gun drills, thereby greatly improving processing efficiency and shortening The processing time also extends the life of the drill. The minimum diameter of the integrated drill is from Φ0.5. In addition, the Torx groove of the screw head can be machined with a small diameter 4-edge long-neck end mill specially developed for this machining.
Factories specializing in processing implanted prosthetic parts and surgical instruments titanium alloys, cobalt chromium molybdenum alloys, and stainless steel parts often produce hundreds of thousands of small parts, many are turned milling. In order to meet this requirement, WOTEK has developed an advanced series of high-aluminum-coated end mills. Generally, the amount of aluminum increases, and aluminum will gather together into a soft phase. High-aluminum-coated end mills can avoid this disadvantage and form a uniform high-hardness. Phase, its hardness reaches HV3000, and has highly thermal stability. Using it as a coating for turning inserts, not only the flank face is resistant to mechanical wear, but also the rake face is resistant to crater wear, anti-adhesion damage, and combined with titanium alloy processing The specially developed hard alloy substrate with high strength and good thermal conductivity has solved many problems such as machining quality, efficiency, and life of small turning tools. For the blanks of some stainless steel and titanium alloy surgical instruments, a large margin is often left. In order to improve the efficiency of milling and roughing of such parts, the radial force can be reduced, and the main deflection angle is small. The feed end mill has a cutting speed of 120 m / min and a feed rate of 2100 mm / min.
Medical implant parts should be suitable for different three-dimensional spatial shapes of different implant sites, so individual requirements are outstanding. Entering the era of Industry 4.0, a distinct competitive characteristic is that whoever can best meet the customer's personalized requirements as quickly as possible will win. Therefore, the future direction is that advanced cutting tools, combined with intelligent manufacturing, and 3D printing additive manufacturing can achieve continuous victory.