Detailed explanation of seven calibrations end mills methods for CNC machining.
2020-03-26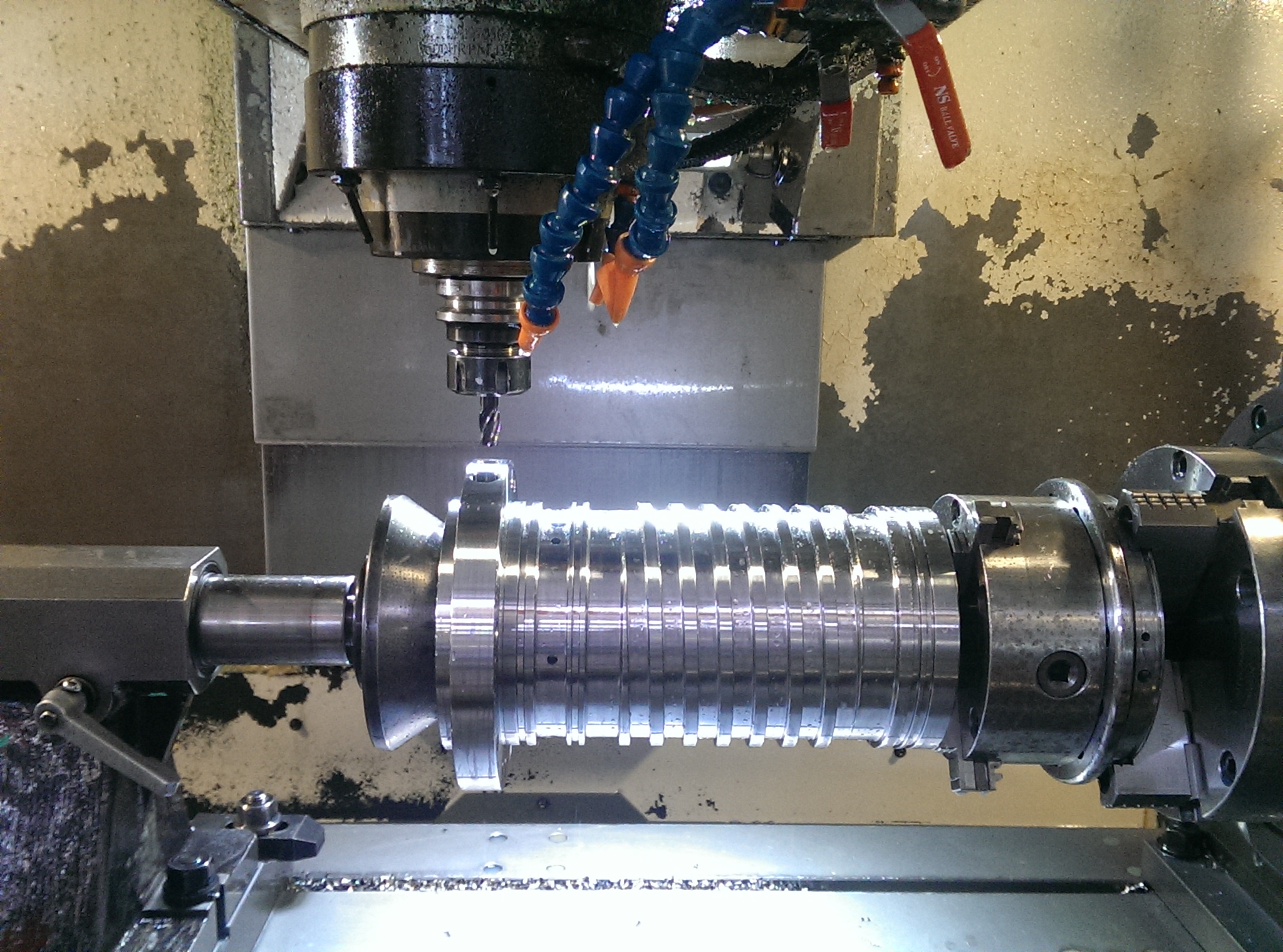
Calibrating the end mill is the main operation and important skill in CNC machining. Under certain conditions, the accuracy of the calibrated end mill can determine the machining accuracy of the part. At the same time, the efficiency of the calibrated milling cutter directly affects the CNC machining efficiency. Knowing the calibration end mill methods is not enough, we need to know the various calibration end mill setting methods of the CNC system, and how these methods are called in the processing program. At the same time, you must know the advantages and disadvantages of various calibration end mill methods, and the use conditions.
The purpose of calibrating end mill is to establish workpiece coordinate system. Intuitively speaking, calibrating end mill is to establish the position of the workpiece in the machine tool table, in fact, it is to find the coordinates of the calibration milling point in the machine tool coordinate system. For CNC machine, the calibration milling point must be selected before machining. The calibration milling point refers to the starting point of the tool's movement relative to the workpiece when the workpiece is processed by CNC machine tool. The calibration end mill’s point can be set on the workpiece (such as the design datum or positioning datum on the workpiece), or on the fixture or machine tool. If it is set on a certain point on the fixture or machine tool, the point must be related to the workpiece. The positioning datum maintains a dimensional relationship with a certain accuracy.
When calibrating end mill, the point position should coincide with the calibration end mill. The end mill position point refers to the positioning reference point of the tool. For turning tools, the tool position point is the tool tip. The purpose of the calibration end mill is to determine the absolute coordinate value of the calibration end mill point (or the workpiece origin) in the machine tool coordinate system, and to measure the deviation of the tool position. The accuracy of the calibration end mill point directly affects the machining accuracy. In the actual processing of workpieces, the use of one carbide end mill generally can’t meet the processing requirements of the workpiece, and usually multiple carbide end mills are used for processing. When using multiple carbide end mills to process, the tool tip point will have different geometric position after the tool is changed without changing the tool position. This requires different carbide end mills to start machining at different starting positions. Keep the program running. In order to solve this problem, the machine tool CNC system is equipped with a tool geometric position compensation function. With the tool geometric position compensation function, as long as the position deviation of each carbide end mills relative to a pre-selected reference tool is measured in advance and input into the CNC system in the group number specified in the tool parameter correction column of the carbide end mill, using the T command in the machining program, the carbide end mill position deviation can be automatically compensated in the carbide end mill path. The measurement of carbide end mills position deviation also needs to be realized by calibrating the carbide end mills operation.
In CNC processing, the basic methods of calibrating end mills include trial cutting method, calibration milling instrument, calibration end mills and automatic calibration end mills. This article takes CNC milling machine as an example to introduce several commonly used methods for calibrating end mills.
This method is simple and convenient, but will leave cutting marks on the surface of the workpiece, and has less accuracy of the calibration end mills. As shown in Figure 1, a bilateral calibration end mills method is used to take the calibration end mills point (here coincides with the origin of the workpiece coordinate system) at the center of the workpiece surface as an example.
①Install the workpiece on the workbench through the fixture. When clamping, the four sides of the workpiece should be left with the positions of the calibration end mills.
②Start the spindle to rotate at medium speed, move the table and the spindle quickly, and move the carbide end mills to a position close to the left side of the workpiece with a certain safety distance, and then reduce the speed to move to the left side of the workpiece.
③When approaching the workpiece, use fine-tuning operation(usually 0.01mm) to approach it, and let the carbide end mills approach the left side of the workpiece slowly, so that the carbide end mills just touches the left surface of the workpiece (observe, listen to the cutting sound, see the milling marks, looking at the chips, as long as there is a situation, it means that the carbide end mill is in contact with the workpiece), and then retract by 0.01mm. Note down the coordinate value displayed in the machine tool coordinate system at this time, such as -240.500.
④ Retract the carbide end mill in the z direction to the surface of the workpiece, approach the right side of the workpiece in the same way, and note the coordinate value displayed in the machine tool coordinate system at this time, such as -340.500.
⑤The origin of the workpiece coordinate system in the machine tool coordinate system is {-240.500+(-340.500)/2 = -290.500.
⑥The same can be done for the workpiece coordinate system origin in the machine tool coordinate system.
①Move the carbide end mills quickly over the workpiece.
②Start spindle rotation at medium speed to move the table and spindle quickly so that the carbide end mills moves quickly to a position close to the upper surface of the workpiece at a safe distance, and then reduce the speed to move the carbide end mills edge face close to the upper surface of the workpiece.
③When approaching the workpiece, use the fine-tuning operation (generally 0.01mm) to approach the workpiece, so that the cutting edge of the carbide end mill slowly approaches the surface of the workpiece (note that the cutting edge of the carbide end mill, especially the vertical end mill, is better to cut at the edge of the workpiece, the area of the cutting edge of the cutter touching the surface of the workpiece is less than half circle, try not to make the center hole of the vertical end mill to cut at the surface of the workpiece), so that the cutting edge of the carbide end mill touches the upper surface of the workpiece, then raise the shaft again, remember the z value in the coordinate system of the tool machine, -140.400, then the workpiece coordinate system origin W in the coordinate system of the machine tool coordinate value of -140.400.
This method is similar to the test end mill calibration method, except the spindle doesn’t rotate when calibrating the end mills, and plugs (or standard mandrel or block gauge) is added between the carbide end mill and the workpiece, plugs couldn’t move freely. Because the spindle doesn’t need to be turned for cutting, this method doesn’t leave traces on the surface of the workpiece, but the accuracy of the calibration end mill is less.
The length of the second end mill is not the same as the length of the first end mill, which needs to be zeroed again, but sometimes the zero point is machined off and it is impossible to find the zero point directly, or it is not allowed to damage the machined surface, and some carbide end mills or occasionally it is not good to calibrate the end mills directly.
①When calibrating the first end mill, use the test cut method, the plugging method, etc. After the first end mill is machined, stop the spindle.
②Putting the calibration end mills on the flat surface of the machine tool working table (e.g. large surface of the vise).
③In the hand wheel mode, move the table by hand to the appropriate position, move the spindle downward, use the bottom end of the end mill to calibrate the top of the end mill, turn the dial hands, preferably within one turn, note the axis setter's indication and clear it relative to the coordinate axis.
④Lift the spindle accurately and remove the first end mill.
①Install the second end mill.
②In the hand wheel mode, move the spindle downward and use the bottom end of the end mill to calibrate the position A of the end mill.
③Record the value of z0 (with plus and minus sign) corresponding to the axis coordinate at this time.
④Lift the spindle and remove the calibration end mill.
⑤Add the z1 coordinate data in the original G5 * of the first end mill to z0 (with a sign) to get a new coordinate.
⑥The new coordinates are the actual machine tool coordinates of the second end mill corresponding to the origin workpiece. The remaining end mills are calibrated in the same way as the second end mill.
Note: If several tools use the same G5*, then step 5), 6) instead, save z0 in the length parameter of the second end mill, and use the second end mill to correct G43H02 for the tool length when machining.
①Install the workpiece through the clamp on the machine tool table and replace it with the top one.
②Move the table and spindle quickly so the tip moves close to the top of the workpiece, find the center point of the workpiece drawing line, and reduce the speed movement so the tip is closing to it.
③Use the fine adjustment operation, let the tip slowly approach the center of the workpiece line until the tip is aligned with the center of the workpiece line, and write down the x, y coordinates in the machine coordinate system.
(2) Remove the tip, install the end mill, and use other calibration methods such as test cutting, plugging, etc. to get the Z-axis coordinate value.
Attach the mounting rod of the scale to the toolholder, or stick the magnetic seat of the scale onto the spindle socket, move the table so that the center line of the spindle (i.e. the center of the carbide end mill) is roughly moved to the center of the workpiece, adjust the length and angle of the telescopic rod on the magnetic seat so that the contacts of the scale touch the circumference of the workpiece, (the pointer rotates about 0.1mm) and slowly turn the spindle by hand so that the contacts of the scale rotate along the circumference of the workpiece, observe the movement of the pointer of the scale, slowly move the shaft and shaft of the table, and after many iterations, the pointer of the scale is basically in the same position when the spindle is turned (when the scale is turned for one circle, the amount movement of the pointer is within the allowed tolerance of the calibration cutter, such as 0.02mm).
The traditional method of calibration end mill has the disadvantages of poor safety (such as plugging the ruler to calibrate the end mill, the tip of the end mill will break easily), the production period extends (such as the test cutting needs to be repeated several times), the operators brought about by the large randomness error and so on, has not been able to adapt to the rhythm of CNC machining, also the disadvantage of playing the function of CNC tools. The special calibration end mills have the advantages of high accuracy, high efficiency, good safety and other advantages of calibration end mills, simplifying the tedious work of calibration end mills guaranteed by experience, and ensuring the development of efficient and high precision features of CNC tooling machines.
Ⅰ. The principle of calibration end mill.
The purpose of calibrating end mill is to establish workpiece coordinate system. Intuitively speaking, calibrating end mill is to establish the position of the workpiece in the machine tool table, in fact, it is to find the coordinates of the calibration milling point in the machine tool coordinate system. For CNC machine, the calibration milling point must be selected before machining. The calibration milling point refers to the starting point of the tool's movement relative to the workpiece when the workpiece is processed by CNC machine tool. The calibration end mill’s point can be set on the workpiece (such as the design datum or positioning datum on the workpiece), or on the fixture or machine tool. If it is set on a certain point on the fixture or machine tool, the point must be related to the workpiece. The positioning datum maintains a dimensional relationship with a certain accuracy.
When calibrating end mill, the point position should coincide with the calibration end mill. The end mill position point refers to the positioning reference point of the tool. For turning tools, the tool position point is the tool tip. The purpose of the calibration end mill is to determine the absolute coordinate value of the calibration end mill point (or the workpiece origin) in the machine tool coordinate system, and to measure the deviation of the tool position. The accuracy of the calibration end mill point directly affects the machining accuracy. In the actual processing of workpieces, the use of one carbide end mill generally can’t meet the processing requirements of the workpiece, and usually multiple carbide end mills are used for processing. When using multiple carbide end mills to process, the tool tip point will have different geometric position after the tool is changed without changing the tool position. This requires different carbide end mills to start machining at different starting positions. Keep the program running. In order to solve this problem, the machine tool CNC system is equipped with a tool geometric position compensation function. With the tool geometric position compensation function, as long as the position deviation of each carbide end mills relative to a pre-selected reference tool is measured in advance and input into the CNC system in the group number specified in the tool parameter correction column of the carbide end mill, using the T command in the machining program, the carbide end mill position deviation can be automatically compensated in the carbide end mill path. The measurement of carbide end mills position deviation also needs to be realized by calibrating the carbide end mills operation.
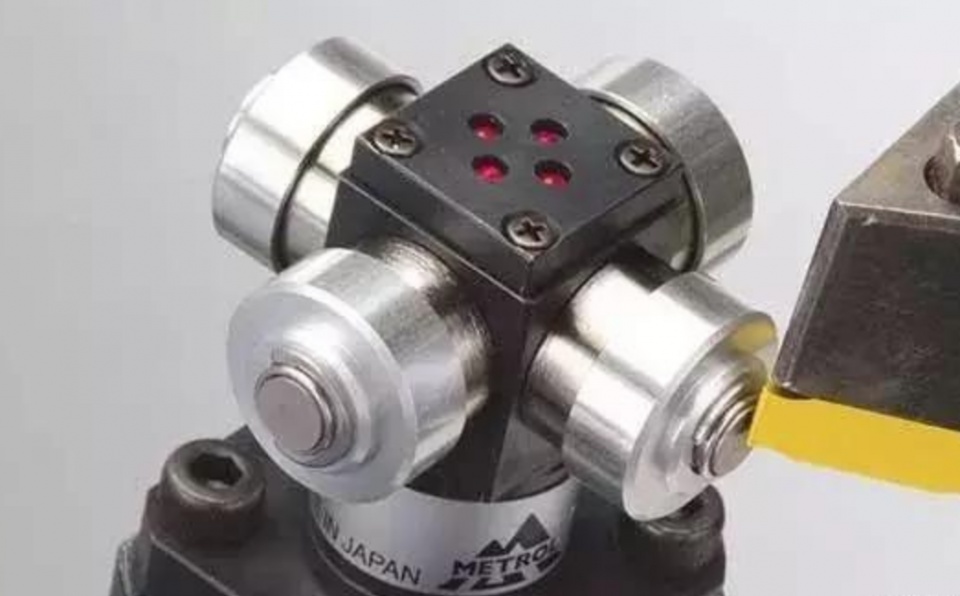
Ⅱ. Method of calibrating end mills
In CNC processing, the basic methods of calibrating end mills include trial cutting method, calibration milling instrument, calibration end mills and automatic calibration end mills. This article takes CNC milling machine as an example to introduce several commonly used methods for calibrating end mills.
1. Trial cutting calibration end mills method.
This method is simple and convenient, but will leave cutting marks on the surface of the workpiece, and has less accuracy of the calibration end mills. As shown in Figure 1, a bilateral calibration end mills method is used to take the calibration end mills point (here coincides with the origin of the workpiece coordinate system) at the center of the workpiece surface as an example.
(1) Calibration end mills in x and y directions.
①Install the workpiece on the workbench through the fixture. When clamping, the four sides of the workpiece should be left with the positions of the calibration end mills.
②Start the spindle to rotate at medium speed, move the table and the spindle quickly, and move the carbide end mills to a position close to the left side of the workpiece with a certain safety distance, and then reduce the speed to move to the left side of the workpiece.
③When approaching the workpiece, use fine-tuning operation(usually 0.01mm) to approach it, and let the carbide end mills approach the left side of the workpiece slowly, so that the carbide end mills just touches the left surface of the workpiece (observe, listen to the cutting sound, see the milling marks, looking at the chips, as long as there is a situation, it means that the carbide end mill is in contact with the workpiece), and then retract by 0.01mm. Note down the coordinate value displayed in the machine tool coordinate system at this time, such as -240.500.
④ Retract the carbide end mill in the z direction to the surface of the workpiece, approach the right side of the workpiece in the same way, and note the coordinate value displayed in the machine tool coordinate system at this time, such as -340.500.
⑤The origin of the workpiece coordinate system in the machine tool coordinate system is {-240.500+(-340.500)/2 = -290.500.
⑥The same can be done for the workpiece coordinate system origin in the machine tool coordinate system.
(2) Z-align the end mills.
①Move the carbide end mills quickly over the workpiece.
②Start spindle rotation at medium speed to move the table and spindle quickly so that the carbide end mills moves quickly to a position close to the upper surface of the workpiece at a safe distance, and then reduce the speed to move the carbide end mills edge face close to the upper surface of the workpiece.
③When approaching the workpiece, use the fine-tuning operation (generally 0.01mm) to approach the workpiece, so that the cutting edge of the carbide end mill slowly approaches the surface of the workpiece (note that the cutting edge of the carbide end mill, especially the vertical end mill, is better to cut at the edge of the workpiece, the area of the cutting edge of the cutter touching the surface of the workpiece is less than half circle, try not to make the center hole of the vertical end mill to cut at the surface of the workpiece), so that the cutting edge of the carbide end mill touches the upper surface of the workpiece, then raise the shaft again, remember the z value in the coordinate system of the tool machine, -140.400, then the workpiece coordinate system origin W in the coordinate system of the machine tool coordinate value of -140.400.
(3) Enter the measured x, y, and z values into the machine's workpiece coordinate system storage address G5* (generally use G54 to G59 codes to store calibration carbide end mills parameters).
(4) Enter the panel input mode (MDI), enter "G5*", press the start button (in auto mode), run G5* to starting.
(5) Checking the calibration end mill is correct or not.
2. Plugs, standard mandrels, block gauge calibration end mills method.
This method is similar to the test end mill calibration method, except the spindle doesn’t rotate when calibrating the end mills, and plugs (or standard mandrel or block gauge) is added between the carbide end mill and the workpiece, plugs couldn’t move freely. Because the spindle doesn’t need to be turned for cutting, this method doesn’t leave traces on the surface of the workpiece, but the accuracy of the calibration end mill is less.
3. Use edge finder, eccentric bar, shaft setter and other tools to calibrate end mills method.
The procedure is similar to using the test cut calibration method, except that the carbide end mills are replaced with edge finders or eccentric bars. This is the most common method. High efficiency and guaranteed calibration of end mills accuracy. The z-axis setter is generally used to transfer (indirectly) the calibration milling method.
4. Transfer (indirect) calibration of end mills method.
The length of the second end mill is not the same as the length of the first end mill, which needs to be zeroed again, but sometimes the zero point is machined off and it is impossible to find the zero point directly, or it is not allowed to damage the machined surface, and some carbide end mills or occasionally it is not good to calibrate the end mills directly.
(1) Calibration the first end mill.
①When calibrating the first end mill, use the test cut method, the plugging method, etc. After the first end mill is machined, stop the spindle.
②Putting the calibration end mills on the flat surface of the machine tool working table (e.g. large surface of the vise).
③In the hand wheel mode, move the table by hand to the appropriate position, move the spindle downward, use the bottom end of the end mill to calibrate the top of the end mill, turn the dial hands, preferably within one turn, note the axis setter's indication and clear it relative to the coordinate axis.
④Lift the spindle accurately and remove the first end mill.
(2) Calibration the second end mill.
①Install the second end mill.
②In the hand wheel mode, move the spindle downward and use the bottom end of the end mill to calibrate the position A of the end mill.
③Record the value of z0 (with plus and minus sign) corresponding to the axis coordinate at this time.
④Lift the spindle and remove the calibration end mill.
⑤Add the z1 coordinate data in the original G5 * of the first end mill to z0 (with a sign) to get a new coordinate.
⑥The new coordinates are the actual machine tool coordinates of the second end mill corresponding to the origin workpiece. The remaining end mills are calibrated in the same way as the second end mill.
Note: If several tools use the same G5*, then step 5), 6) instead, save z0 in the length parameter of the second end mill, and use the second end mill to correct G43H02 for the tool length when machining.
5. Top end mills calibration method.
(1) X, Y directional calibration end mills.
①Install the workpiece through the clamp on the machine tool table and replace it with the top one.
②Move the table and spindle quickly so the tip moves close to the top of the workpiece, find the center point of the workpiece drawing line, and reduce the speed movement so the tip is closing to it.
③Use the fine adjustment operation, let the tip slowly approach the center of the workpiece line until the tip is aligned with the center of the workpiece line, and write down the x, y coordinates in the machine coordinate system.
(2) Remove the tip, install the end mill, and use other calibration methods such as test cutting, plugging, etc. to get the Z-axis coordinate value.
6. Percentile (or millimeter) calibration cutter method (generally used for calibration cutters for round workpieces)
(1) X, Y directional alignment end mills.
Attach the mounting rod of the scale to the toolholder, or stick the magnetic seat of the scale onto the spindle socket, move the table so that the center line of the spindle (i.e. the center of the carbide end mill) is roughly moved to the center of the workpiece, adjust the length and angle of the telescopic rod on the magnetic seat so that the contacts of the scale touch the circumference of the workpiece, (the pointer rotates about 0.1mm) and slowly turn the spindle by hand so that the contacts of the scale rotate along the circumference of the workpiece, observe the movement of the pointer of the scale, slowly move the shaft and shaft of the table, and after many iterations, the pointer of the scale is basically in the same position when the spindle is turned (when the scale is turned for one circle, the amount movement of the pointer is within the allowed tolerance of the calibration cutter, such as 0.02mm).