Mastering Cutting Challenges: Solving Common CNC Machining Problems with Selected Tools
2025-04-09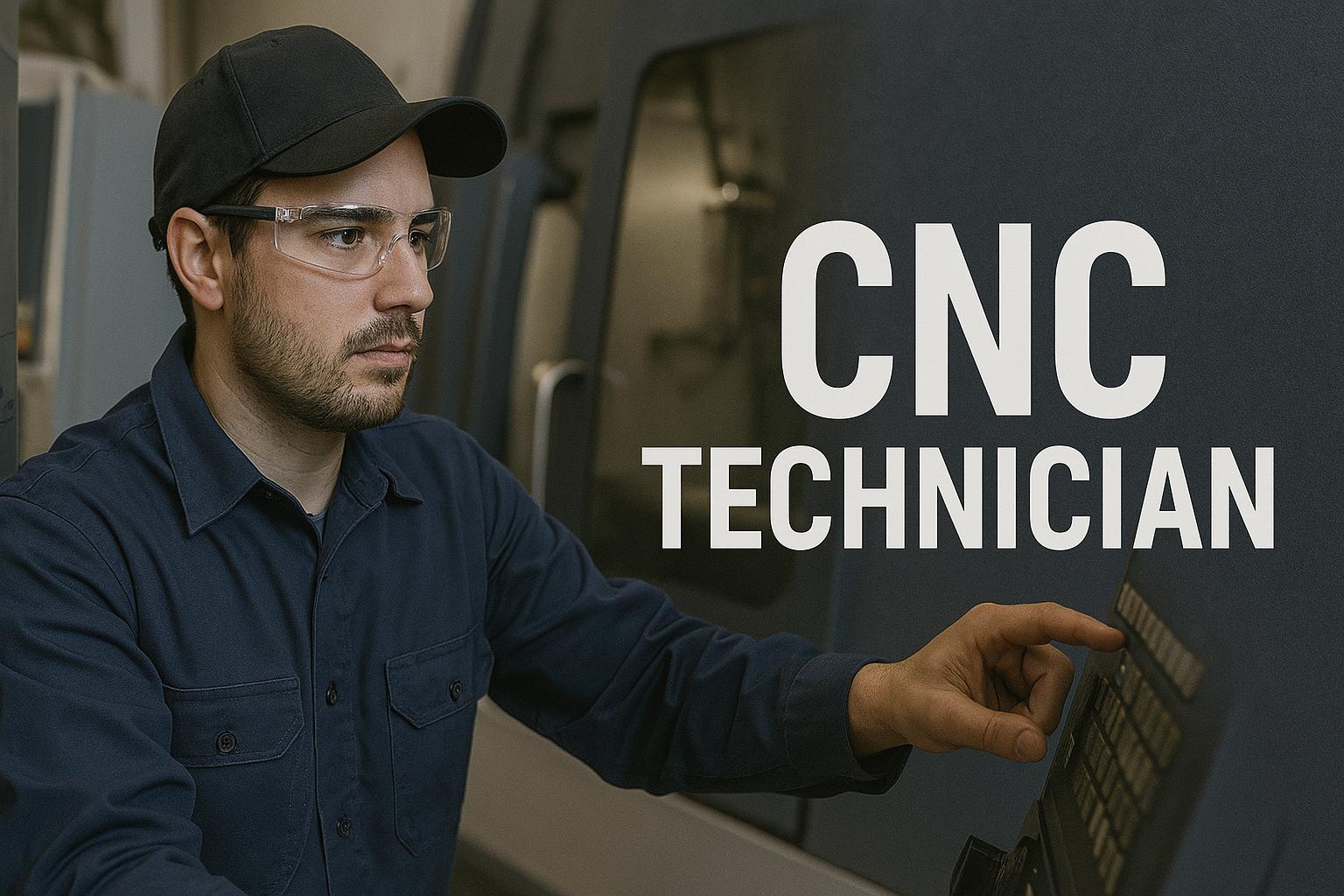
In the realm of precision manufacturing, CNC (Computer Numerical Control) machining technology has become the cornerstone for achieving high-quality, high-efficiency production. While CNC machine tools themselves possess a high degree of sophistication, it is the quietly working cutting tools that ultimately come into direct contact with the workpiece and shape it. The selection and correct use of cutting tools are crucial for ensuring machining quality, precision, and overall efficiency. However, like all complex systems, the CNC machining process is prone to various problems, such as excessively rapid tool wear, rough workpiece surfaces, and poor dimensional accuracy. These issues not only affect the final quality of the product but can also lead to production interruptions and increased costs. This article will delve into common defects in CNC machining, analyze their root causes, and highlight how precise tool selection and optimized operational practices can effectively overcome these challenges.
Decoding Machining Problems: Common CNC Machining Defects and Their Impact
While CNC machining is precise, it can still encounter various defects that affect the quality and functionality of parts.1 Understanding these common problems and their potential consequences is the first step in adopting effective solutions.
Tool Wear: The Inevitable Deterioration
Tool wear is a natural occurrence in CNC machining, but excessive or premature wear can lead to numerous problems.1 Understanding the different types of tool wear and their causes helps us take preventive measures to extend tool life and maintain machining quality.
-
Flank Wear: Refers to the uniform wear that occurs on the flank face of the tool along the cutting edge, usually caused by severe friction and continuous rubbing against the workpiece.1 Low cutting speeds tend to cause abrasive wear, while high cutting speeds generate high temperatures, accelerating diffusion wear.1 Although flank wear is a more desirable form of wear because it is predictable 1, excessive wear can still affect machining accuracy and surface finish.
-
Crater Wear: Refers to the crater-like wear that forms on the rake face of the tool due to high temperatures causing the decomposition of carbide grains and their diffusion into the chips.1 Crater wear is closely related to high cutting speeds and cutting temperatures, which can lead to a decrease in tool strength and even cause subsequent chipping or accelerated flank wear.
-
Chipping: Refers to the fracturing of small pieces from the cutting edge, usually due to mechanical impact, uneven or shock loads, or interrupted cutting on hard surfaces.1 Unstable machine tool setups and inclusions in the workpiece material can also lead to chipping. Chipping directly affects the surface quality of the workpiece and can cause premature tool failure.
-
Built-up Edge (BUE): Refers to the workpiece material adhering to the cutting edge, especially when machining softer materials or at lower temperatures.2 BUE can change the actual geometry of the tool, leading to increased surface roughness and decreased machining accuracy.
-
Thermal Cracking: Refers to the tiny cracks that form on the tool surface perpendicular to the cutting edge, caused by repeated heating and cooling cycles that lead to the expansion and contraction of the tool.2 Interrupted cutting or improper cooling strategies can easily lead to thermal cracking, which can subsequently cause chipping and premature tool failure.
-
Adhesive Wear: Refers to the phenomenon where the tool and workpiece materials weld or adhere to each other at high temperatures, commonly occurring when machining materials with a high tendency for high-temperature adhesion, such as low-carbon steel.2 Adhesive wear can cause material to be torn from the workpiece surface, affecting the surface finish.
-
Abrasive Wear: Refers to the uniform wear of the tool cutting edge caused by the friction of hard particles in the workpiece material or the tool wear land.2 Abrasive wear is more significant when machining hard materials, which can lead to tool dulling and decreased dimensional accuracy.
-
Notch Wear: Refers to the wear that occurs on the cutting edge near the depth-of-cut line, usually caused by hard materials, stainless steel, abrasive workpieces, or work-hardened surfaces.2 Notch wear can cause irregular cutting marks on the workpiece surface.
-
Plastic Deformation: Refers to the softening and deformation of the cutting edge under high temperatures and high cutting forces, commonly occurring when machining work-hardened materials.3 Plastic deformation can cause the tool to lose its original geometry, affecting machining accuracy and surface quality.
Common causes of tool wear include improper cutting speeds and feed rates, poor chip evacuation, incorrect helix angles, overly hard workpiece materials, mechanical instability, inclusions in the workpiece, interrupted cutting, inconsistent cooling, material adhesion, abrasion, and thermal stress.1 The consequences of tool wear are multifaceted, including poor material surface finish (rough edges, tool marks, burns) 10, reduced dimensional accuracy 8, increased machining time 8, tool breakage 8, poor surface finish 8, chatter marks 11, material deformation 11, increased cutting forces 7, shortened tool life 10, spindle bearing failure 10, and part rejection.1
Poor Surface Finish: The Compromise Between Aesthetics and Functionality
Poor surface finish is a common problem that can affect the aesthetics and functionality of parts.12 Various factors can lead to surface roughness, producing unwanted textures or irregularities.
-
Chatter Marks: Refer to the wavy or undulating patterns that appear on the workpiece surface, usually caused by excessive vibration of the tool or workpiece.8 Chatter indicates instability in the machining system and may require improvements in workpiece clamping, reduction of tool overhang, optimization of cutting parameters, or inspection of the machine tool condition.
-
Burrs and Sharp Edges: Refer to the excess material left on the workpiece after cutting, commonly found at the edges of drilled holes or around machined grooves.11 Burrs are more common in materials with good plasticity and can be reduced by using sharp tools, optimizing toolpath settings, and employing deburring techniques.
-
Burns: Refer to the discoloration or melting of the workpiece surface due to excessive heat generation.10 Burns are usually caused by incorrect cutting parameters (excessive speed or feed rate), insufficient cooling, or tool dulling, thus requiring appropriate parameter selection and effective coolant use.
-
Dents: Refer to the indentations that appear on the workpiece surface, usually caused by excessive clamping force, especially on softer materials.14 Dents can be prevented by controlling clamping force, using intermediate plates to distribute pressure, or employing softer chucks and fixtures.
-
Varying Surface Finish: Refers to inconsistent smoothness on a single surface, which may be due to chatter, incorrect toolpath strategies (mixing climb and conventional milling), or insufficient coolant.13 Consistent cutting strategies and proper coolant use are crucial for achieving a uniform surface finish.
-
Torn Finish: Refers to a rough, uneven surface finish, which may be caused by the tool pushing material away instead of cutting it, commonly occurring with shallow depths of cut or when machining soft/sticky materials.15 Increasing the depth of cut and ensuring the tool has a good cutting edge can help prevent a torn finish.
-
Faceting: Refers to the surface appearing as flat planes rather than a smooth curve, usually caused by insufficient chord tolerance in CAD/CAM software or the use of low-resolution STL files.16 Proper software settings and correct CAD file formats are essential for achieving smooth curved surfaces.
The causes of poor surface finish are very diverse, including incorrect cutting parameters (speed, feed rate) 8, tool wear 8, improper tool selection 10, insufficient rigidity (workpiece clamping, tool holder, machine tool condition) 12, coolant problems (improper selection, insufficient quantity) 12, material properties (soft/sticky materials) 15, programming errors 8, environmental factors (vibration) 8, chip evacuation problems 18, spindle issues 19, incorrect milling strategies 13, machine tool instability 13, human setup errors 11, excessive spindle speed 20, uncalibrated machine tool or loose parts 21, material warping 21, insufficient clamping force 21, improper number of cutting edges for aluminum 21, incorrect toolpath spacing 22, and CAD file format issues.16 The impact of poor surface finish is significant, as it can reduce friction and wear on moving parts 12, affect aesthetics 12, reduce coating adhesion 12, decrease fatigue strength 12, lower corrosion resistance 12, cause assembly problems 12, and ultimately affect the durability, performance, and appearance of the part.19
Poor Dimensional Accuracy: The Frustration of Deviating from Design
Poor dimensional accuracy is a critical issue that directly affects the functionality and assembly of parts.11 Even minor deviations can lead to serious consequences.
Common causes of poor dimensional accuracy include machine tool errors (misalignment, spindle runout, backlash) 8, programming errors (incorrect G-code, syntax errors) 8, tool wear (worn or dull tools) 8, machine tool vibration or chatter 8, workpiece instability (insufficient clamping or support) 10, thermal expansion of the workpiece or machine tool components 10, inadequate operator training (errors in machine operation, tool handling, workpiece setup) 8, drive system backlash (loose mechanical components) 23, faulty motors causing inconsistent motion 23, machine tool not placed on a stable foundation or loose mounting bolts 23, incorrect tools or settings (dull tools, incorrectly sized tools, wrong feed rate ratio) 10, power supply issues (insufficient or excessive voltage) 8, chuck and fixture clamping/unclamping problems 10, automatic tool changer problems 10, machine tool overheating 10, wrong CNC machine tool partner 10, environmental factors (dust, extreme temperature changes, humidity) 17, machine tool wear 17, CAD file format issues (e.g., using insufficient resolution STL) 16, chord tolerance in CAM software (approximating curves with line segments) 16, machine tool heating during operation 24, CNC machining position error (swing angle error of the axis) 24, CNC machining system error (impact of multiple components) 24, deformation error caused by external forces (clamping, gravity, friction) 24, backlash 25, incorrect steps per unit setting 31, gantry misalignment 32, bent extrusions or improperly installed guide rail supports 32, bent motor mounting points 33, incorrect rotation radius used by firmware 33, incorrect chain sag compensation 33, incorrect vertical offset distance of the motor 33, mismatched chain lengths 33, and feed rate too fast for interpolation mode.27 The consequences of poor dimensional accuracy include improper fit and function of parts 11, material waste 17, machine tool damage 17, operator safety risks 17, non-conforming or marginally conforming surfaces 28, and part rejection.24
Tool Breakage: Costly Interruptions
Tool breakage is a serious problem that can lead to downtime, scrapped parts, and even damage to the machine tool.34 Understanding the common causes of tool breakage is essential for preventing its occurrence.
Common causes of tool breakage include excessive cutting forces (excessive feed rate, depth of cut, or cutting speed) 6, improper tool selection for the material or operation (insufficient tool strength, incorrect geometry) 8, machining hard materials 8, insufficient tool strength (excessive tool length, excessive overhang) 8, tool wear (dull or worn tools) 8, programming errors (toolpath collisions, incorrect parameters) 8, machine tool vibration or chatter 8, high cutting pressure 8, material inclusions or non-uniformity 1, improper cutting speeds and feed rates 5, poor programming considerations (defining safe zones, inappropriate depth of cut) 23, loose tool holder or unstable workpiece clamping 5, incorrect coating 4, inappropriate depth of cut 4, hot spots on the workpiece 6, built-up edge 3, mechanical instability of the machine tool setup 1, excessive impact loads during operation 5, tool holder problems or loose workpiece clamping 4, and lost steps due to loose connectors.31 The consequences of tool breakage include interruption of the machining process 8, damage to the workpiece and composite materials 8, grooves or scratches on the workpiece 11, production delays 11, catastrophic failure of the tool 7, safety issues 6, and downtime events.6
The Cutting Edge of Solutions: Selecting the Right Tools to Meet Challenges
Selecting the correct cutting tool is the first line of defense against these common problems.35 Choosing the appropriate tool for specific workpiece materials and machining operations is crucial for ensuring machining quality and efficiency.
Material Matters: Selecting Tools Based on Workpiece Material
Different workpiece materials (aluminum, steel, stainless steel, titanium, composites) have unique machining characteristics that require specific tool materials and geometries.8
-
Aluminum: Due to its softness and stickiness, it requires tools with good chip evacuation (fewer flutes, polished flutes), typically made of carbide or high-speed steel. Coatings such as ZrN or DLC help prevent built-up edge.37 Aluminum chips are large and prone to clogging, so tools and coatings specifically designed for aluminum are essential.
-
Steel: Can be machined with various tool materials, including high-speed steel and carbide, depending on hardness and cutting speed requirements.57 Coatings like TiN or TiCN can improve wear resistance.
-
Stainless Steel: Known for its work hardening and poor thermal conductivity, it requires sharp, wear-resistant tools, typically made of carbide or cobalt-containing high-speed steel. Coatings such as AlTiN or nACo are very beneficial. Lower cutting speeds and higher feed rates are generally recommended.58 The properties of stainless steel require tools that can withstand heat and prevent work hardening.
-
Titanium: Difficult to machine due to its high strength, low thermal conductivity, and tendency to adhere. Requires sharp carbide tools with coatings like TiAlN, lower cutting speeds, and the use of copious amounts of coolant at high pressure.78 Titanium's unique properties necessitate tools and techniques focused on managing heat and preventing material adhesion.
-
Composite Materials: Abrasive and prone to delamination, they require specialized tools usually made of carbide or PCD, with specific geometries (e.g., compression tools), and may require waterjet cutting for delicate materials.97 The layered structure and abrasive nature of composite materials demand tools that cut without causing separation or excessive wear.
Choosing the correct tool material is fundamental to preventing premature wear and breakage, and ensuring good surface finishes for different workpiece materials.
Geometry and Design: Matching Tools to Operations
Different tool geometries (number of flutes, helix angle, end type - flat, ball nose, bull nose) are suitable for specific machining operations (roughing, finishing, slotting, drilling, engraving).36
-
Fewer Flutes: Better chip evacuation, suitable for roughing.
-
More Flutes: Better surface finish, suitable for finishing.
-
High Helix Angle: Facilitates chip evacuation and reduces cutting forces, suitable for softer materials like aluminum.
-
Low Helix Angle: Provides higher strength, better for harder materials.
-
Up-Cut: Pulls chips upward away from the workpiece, suitable for thicker materials.
-
Down-Cut: Pushes chips downward, provides a cleaner top surface on thinner materials.
-
Compression: Combines up-cut and down-cut, ideal for laminated materials.
-
Flat End Mill: Versatile, suitable for 2D features, slotting, contouring.
-
Ball Nose End Mill: Used for 3D contouring and curved surfaces.
-
Bull Nose End Mill: Used for roughing and corner rounding.
-
Drill Bit: Used for creating holes (twist drill, center drill, jet drill).
-
Tap: Used for creating internal threads.
-
Thread Mill: Used for creating internal and external threads, suitable for hard materials.
Selecting the correct tool geometry can optimize material removal rates, surface finish, and tool life for specific machining tasks.
Protective Layers: Understanding Tool Coatings
Various tool coatings (TiN, TiCN, AlTiN, DLC, ZrN) offer advantages in improving hardness, wear resistance, heat resistance, and lubricity, which help overcome common machining problems.1
-
TiN (Titanium Nitride): A general-purpose coating that improves hardness and wear resistance.
-
TiCN (Titanium Carbonitride): Offers better wear resistance and higher hardness than TiN.
-
AlTiN (Aluminum Titanium Nitride): Provides excellent high-temperature hardness and oxidation resistance, suitable for high-speed machining and difficult-to-cut materials like stainless steel and titanium.
-
DLC (Diamond-Like Carbon): Offers low friction and high hardness, ideal for non-ferrous materials like aluminum and plastics.
-
ZrN (Zirconium Nitride): Helps prevent aluminum from adhering to the tool.
-
nACo (Nano-composite Coating): Provides superior heat and wear resistance, excellent for stainless steel.
Coatings provide a crucial protective layer that can extend tool life, improve cutting performance, and help prevent issues like built-up edge and excessive wear.
Your company's comprehensive range of tools fully considers these factors, providing optimal solutions for various materials and applications.
Beyond the Basics: Optimizing Parameters and Practices for Success
In addition to selecting the right tools, optimizing cutting parameters and adopting best practices are crucial for avoiding common problems in CNC machining.
The Symphony of Speed and Feed: Setting Cutting Parameters
Correctly setting cutting speed, feed rate, and depth of cut is essential for the workpiece material, tool type, and desired results (surface finish, material removal rate).1
-
Excessive Speed/Feed: Can lead to overheating, tool wear, burns, chatter, tool breakage.
-
Insufficient Speed/Feed: May cause friction, work hardening (especially in stainless steel), increased machining time, poor chip formation.
Emphasize the use of online calculators, material-specific guidelines, and iterative adjustments based on monitoring machine performance (vibration, sound, temperature) and cutting quality. Optimized cutting parameters are essential for balancing material removal rate, tool life, surface finish, and accuracy, as well as preventing common machining defects.
Cooling and Lubrication: Keeping Things Cool and Smooth
Coolants and lubricants play a vital role in CNC machining: dissipating heat, evacuating chips, and reducing friction.1 Different types of coolants (synthetic, semi-synthetic, soluble oil, straight oil) are suitable for different materials and operations.126 Proper coolant delivery methods (flood, mist, through-tool coolant) and concentration are also important. Additionally, alternative cooling methods such as air cooling and minimum quantity lubrication (MQL) are worth considering.126 Proper cooling and lubrication are essential for managing heat, extending tool life, improving surface finish, and promoting effective chip evacuation.
Extending Investment: Tool Maintenance and Regrinding
Briefly introduce the importance of regular tool maintenance (cleaning, inspection, proper storage) for maximizing tool life and performance.136 Introduce the concept of tool regrinding as a cost-effective method to restore tool performance and extend tool life.146 Timely regrinding can prevent more severe tool damage and ensure consistent cutting quality. Proactive tool maintenance and considering tool regrinding can significantly reduce tooling costs and ensure consistent machining quality.
Conclusion: Overcoming Cutting Challenges with Confidence
Common CNC machining problems (tool wear, poor surface finish, poor dimensional accuracy, tool breakage) are prevalent and far-reaching. Understanding the root causes of these problems is the first step in finding effective solutions. Selecting the correct cutting tool suitable for the specific material and application is the primary solution. Furthermore, optimizing cutting parameters and implementing proper machining practices (coolant, lubrication, maintenance) are essential for preventing these issues. Our company offers a range of high-quality cutting tool solutions designed to help you overcome these common challenges and achieve excellent results in your CNC machining operations. We encourage you to explore our product line and feel free to contact our experts for personalized advice and support to help you confidently tackle various cutting challenges.
Type of Tool Wear |
Main Causes |
Possible Consequences |
Flank Wear |
Abrasion at low cutting speeds, diffusion at high cutting speeds |
Reduced machining accuracy, worsened surface finish |
Crater Wear |
High cutting speeds and temperatures |
Reduced tool strength, may lead to chipping or accelerated flank wear |
Chipping |
Mechanical impact, uneven or shock loads, interrupted cutting |
Affects workpiece surface quality, may lead to premature tool failure |
Built-up Edge |
Adhesion of softer materials at lower temperatures |
Increased surface roughness, decreased machining accuracy |
Thermal Cracking |
Repeated heating and cooling cycles |
May cause chipping and premature tool failure |
Adhesive Wear |
Welding or sticking of tool and workpiece materials at high temperatures |
Material tearing from the workpiece surface, affecting surface finish |
Abrasive Wear |
Friction from hard particles in the workpiece material or the tool wear land |
Tool dulling, decreased dimensional accuracy |
Notch Wear |
Hard materials, stainless steel, abrasive workpieces, work-hardened surfaces |
Irregular cutting marks on the workpiece surface |
Plastic Deformation |
Excessive temperature and cutting force |
Tool loses its original geometry, affecting machining accuracy and surface quality |
Workpiece Material |
Recommended Tool Material |
Recommended Coating |
Aluminum |
Carbide, High-Speed Steel |
ZrN, DLC |
Steel |
High-Speed Steel, Carbide |
TiN, TiCN |
Stainless Steel |
Carbide, Cobalt-containing High-Speed Steel |
AlTiN, nACo |
Titanium |
Carbide |
TiAlN |
Composite Materials |
Carbide, PCD |
No specific recommendation |
Machining Operation |
Recommended Number of Flutes |
Recommended Helix Angle |
Recommended End Type |
Roughing |
Fewer |
High |
Flat |
Finishing |
More |
Higher |
Ball Nose |
Slotting |
2-3 |
Medium |
Flat |
Drilling |
2 |
Medium |
Twist Drill |
Tapping |
Specific Tap |
Specific Tap |
Specific Tap |
Thread Milling |
Fewer |
High |
Flat |
Engraving |
Fewer |
Higher |
V-Type |