Analysis Report on Difficult-to-Machine Materials and Mainstream Applications
2024-11-08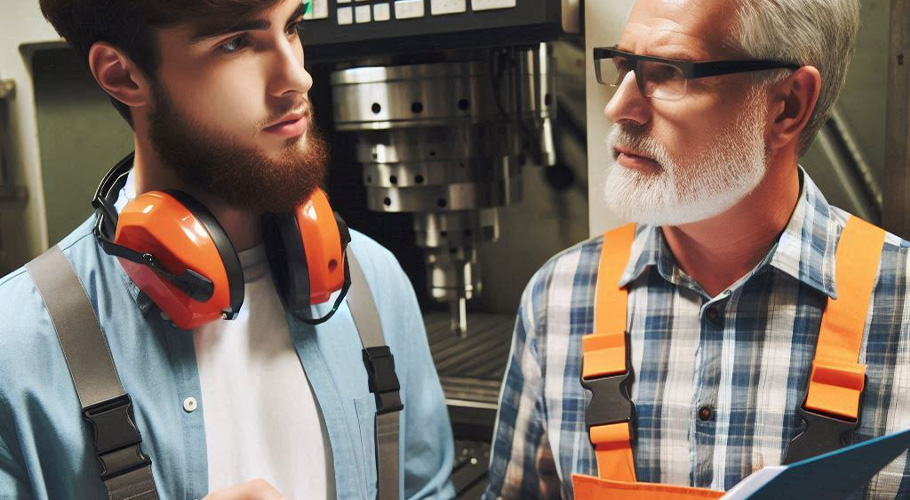
Analysis Report on Difficult-to-Machine Materials and Mainstream Applications
I. High-Difficulty Machining Materials
1. Nickel-based Superalloys
- Representative Materials: Inconel 718, Waspaloy, Hastelloy
- Machining Difficulties:
- High temperature strength
- Severe work hardening
- Poor thermal conductivity
- High tool adhesion tendency
- Main Applications: Aircraft engines, Gas turbines
2. Titanium Alloys
- Representative Materials: Ti-6Al-4V, Ti-5553
- Machining Difficulties:
- High specific strength
- Low elastic modulus
- High chemical reactivity
- Poor thermal conductivity
- Main Applications: Aerospace, Medical implants
3. High-Temperature Steel Alloys
- Representative Materials: H13, D2, M42
- Machining Difficulties:
- High hardness
- High toughness
- High cutting temperatures
- Main Applications: Mold manufacturing, Tool making
4. Composite Materials
- Representative Materials: Carbon Fiber Composites (CFRP), Glass Fiber Composites
- Machining Difficulties:
- Anisotropic properties
- Risk of delamination
- Fiber breakage issues
- Main Applications: Aerospace, Automotive industry
II. Current Mainstream Materials
1. Medical Field
- Cobalt-Chromium-Molybdenum Alloys
- Good biocompatibility
- High corrosion resistance
- Mainly used for artificial joints
- Medical Titanium Alloys
- Lightweight
- Excellent biocompatibility
- Used for implants
2. Aerospace Field
- High-Strength Aluminum Alloys
- 7075, 2024 series
- Light weight, high strength
- Used for airframe structures
- High-Temperature Alloys
- PM-X series
- Heat resistant, fatigue resistant
- Used for engine components
3. Mold Industry
- Pre-hardened Mold Steel
- NAK80, 718H
- Good machinability
- Used for plastic molds
- Powder Metallurgy Tool Steel
- ASP23, M4
- Good wear resistance
- Used for precision stamping dies
4. New Energy Industry
- High Conductivity Copper Alloys
- Good electrical conductivity
- Excellent heat dissipation
- Used for power batteries
- Rare Earth Permanent Magnetic Materials
- Excellent magnetic properties
- Difficult to machine
- Used in motor manufacturing
III. Future Development Trends
1. Lightweight Materials
- Aluminum-lithium alloys
- Magnesium alloys
- High-strength composites
2. Special Functional Materials
- Shape memory alloys
- High-temperature superconductors
- Smart materials
3. Eco-friendly New Materials
- Biodegradable materials
- Recycled materials
- Low-carbon materials
IV. Machining Recommendations
1. General Machining Strategies
- Select appropriate tool materials and coatings
- Optimize cutting parameters
- Implement efficient cooling technology
- Plan reasonable machining paths
2. Special Processing Measures
- Ultrasonic-assisted machining
- Cryogenic machining technology
- High-pressure cooling technology
- Dry machining technology
V. Conclusion
Currently, difficult-to-machine materials mainly include:
- Heat-resistant alloys
- Titanium alloys
- High-hardness steels
- Composite materials
- Special functional materials
The application of these materials is becoming increasingly widespread, requiring continuous optimization of machining processes and development of new processing technologies.