Drilling processes quality of drill and end mills
2020-03-03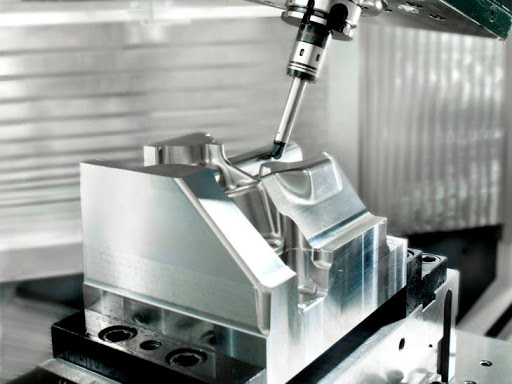
Drilling with twist drill is one of the commonly used operations in metal machining. In this paper, a comparison of the drilling force and the drilled hole quality by using twist drill and end mill in hole drilling were been investigated. To indicate the appropriate selection of twist drill or end mill for hole drilling is the aim of this study. The diameters of twist drills and end mills used for drilling experiments include 6, 8, 10, and 12 mm. The cutting tool commonly used high-speed steel (HSS) material twist drill and end mill, the end mill contains 2-flute and 4-flute, the workpiece been machined is AL6061-T6 aluminum in present experiments. Use the same drilling speed in all drilling experiments and three feeds (mm/tooth) in each tool diameter. Seventy-two experiments were carried out including drilling with or without a previously drilled hole ( 3) in present study. A dynamometer of Kistler 9272 was used to measure the torques, pressures, and the lateral forces during drilling. And then use the micrometer and the surface gage to measure the accuracy of diameter and the surface roughness of the drilled hole respectively for each experiment.
The results show that the torques using twist drills are all slightly larger than that of using end mills. As for comparison of drilling pressure, the pressure forces by twist drills without a previously drilled hole are evidently larger than that of drilling by end mills, and the percentage of the pressure force difference between twist drill and end mill will increases as the tool diameter decreases. The results explain the chisel edge effect of the twist drill. On the side of lateral force, the twist drill has a suitable point angle at tool tip which can effectively stabilize drilling tool and prevent causing vibration during drilling. Therefore the measured lateral forces of twist drills reveal evidently smaller than that of end mills. Because the end mill during drilling can not suppress the tool run out vibration, the diameter accuracy of drilled hole is all relatively poor with respect to that of drilling by twist drill and the error increases as the tool feed increases. In the quality of surface roughness, the results show the twist drill has a stable acceptable surface roughness for both drilling with or without a previously drilled hole. For end mill, more excellent surface roughness can be obtained in small feed conditions than that of twist drill, but it is speedy worsened by increasing end mill feed conditions. In summary, the end mill has better stiffness and smaller torque and pressure force during drilling than twist drill and can generate an excellent surface roughness with small feed conditions. In addition, use end mill can make a hole with flat bottom. Therefore the end mill is appropriate for making a shallow hole like counterboring operations.
The results show that the torques using twist drills are all slightly larger than that of using end mills. As for comparison of drilling pressure, the pressure forces by twist drills without a previously drilled hole are evidently larger than that of drilling by end mills, and the percentage of the pressure force difference between twist drill and end mill will increases as the tool diameter decreases. The results explain the chisel edge effect of the twist drill. On the side of lateral force, the twist drill has a suitable point angle at tool tip which can effectively stabilize drilling tool and prevent causing vibration during drilling. Therefore the measured lateral forces of twist drills reveal evidently smaller than that of end mills. Because the end mill during drilling can not suppress the tool run out vibration, the diameter accuracy of drilled hole is all relatively poor with respect to that of drilling by twist drill and the error increases as the tool feed increases. In the quality of surface roughness, the results show the twist drill has a stable acceptable surface roughness for both drilling with or without a previously drilled hole. For end mill, more excellent surface roughness can be obtained in small feed conditions than that of twist drill, but it is speedy worsened by increasing end mill feed conditions. In summary, the end mill has better stiffness and smaller torque and pressure force during drilling than twist drill and can generate an excellent surface roughness with small feed conditions. In addition, use end mill can make a hole with flat bottom. Therefore the end mill is appropriate for making a shallow hole like counterboring operations.