Cutting benefits of ceramic and cermet end mills tools
2020-04-02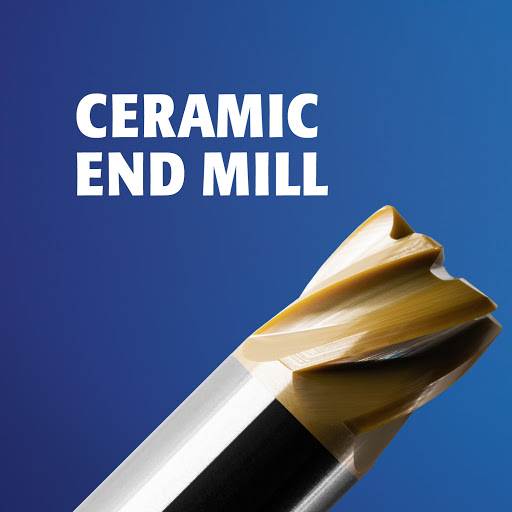
“Everyone’s image of ceramic is a ceramic coffee mug that if you drop it, it shatters,” said Brian Wilshire. “How in the world can you cut metal with it?”
But as technical center manager Wilshire is quite familiar with the metal cutting capabilities of ceramic composite, as well as cermet, tools. The Hendersonville, N.C.-based toolmaker’s offerings include ceramic and cermet inserts for milling and turning. The types of ceramic tool materials include Al2O3, silicon nitride and silicon aluminum oxynitride (SiAlON).
Because SiN and SiAlON are relatively tough ceramics, especially at elevated temperatures, tools made of these materials are best-suited for roughing cast iron and heat-resistant superalloys (HRSAs), Wilshire said. “The Al2O3-based ceramics are still pretty brittle, so those are mainly for hard turning with no interruptions or for finishing cast iron.”
According to Steve Howard, marketing and engineering manager of cutting tools, SiN-based ceramic grades, have twice the fracture toughness of alumina-based ceramics. This level of toughness enables turning and milling cast iron at speeds up to 3,000 sfm.
In addition, SiN-based grades blend the strength of silicon-nitride ceramic with the heat and wear resistance of alumina oxide, Howard said. “SiN-based grades, with SX3 being the newest, feature excellent strength and thermal shock resistance under high temperatures, as well as notching resistance, which are ideal characteristics for high-speed machining of heat-resistant alloys common in aerospace, power generation and oil and gas industries.”
The five grades of black ceramics—alumina with hard carbide added to improve toughness and hardness—have a high-hot hardness and low plasticity to turn steel, chilled or ductile iron rolls and some powdered metals as hard as 62 HRC, Howard said. “Our finest grain structure can perform finishing cuts on steels up to 70 HRC. These ceramics are cost-effective alternatives for applications previously limited to CBNs.”
Like the name implies, cermet combines ceramic elements (such as TiC, TiCN and molybdenum carbide) with metallic binders (such as nickel, as well as molybdenum and cobalt to a lesser degree), Wilshire noted.
Cermet is more brittle than tungsten carbide, so cermet cutting tools are susceptible to chipping and breaking when stressed while taking heavy cuts, he said. As a result, more users consider cermet tools suitable for finishing only at a 0.010" to 0.020" DOC. However, cermet tools that can take a 0.060" to 0.080" DOC in “clean” material.
“If you have interruptions or scale, carbide is still going to be the way to go there,” he said.
Although cermet and ceramic cutting tools have a long history, toolmakers continue to make advancements. One such advancement at creates a gradient in cermet material via a combination of techniques employed during the insert pressing and sintering processes, Wilshire said. “We call those ‘hybrid cermets’ because they offer a hard outer layer and more toughness in the center.”
Combining tough and hard in ceramic inserts. Wilshire explained that the company is able to produce a honeycomb-shaped grain structure in which the hexagon shape that forms the honeycomb is made of tougher ceramic than the harder central core that it surrounds. If the center part develops a crack, the crack will not propagate beyond the shell and cause the insert to break.
“It competes with the whisker material,” he said.
WOTEK does not produce inserts made of whisker-reinforced ceramic but, according to Wilshire, offers a second technology to improve the fracture resistance of ceramic similar to one reinforced with SiC crystals. In the company’s newer SiAlON materials, the grain structure is manipulated to cause some of the grains to become needle-shaped, which functions like whiskers. “During the sintering process, the crystals actually grow,” he said. The structure also includes hard particles for wear resistance.
The whisker-reinforced ceramics, having introduced the uncoated grade in 1985, said Jan Anderson, global director of the TechTeam and marketing for the Saegertown, Pa., toolmaker. Later introduced the coated whisker-reinforced ceramic, which has a different substrate and a nanostructured coating.
“There are a lot of applications where whisker-reinforced ceramics are still—by far—the best solution,” Anderson said.
A more recent development is phase-toughened ceramic. It is a thermally stable, whisker- and particulate-toughened SiN with almost twice the strength of any other commercially available ceramic too.
In theory, all ceramic tools remove metal by raising the temperature in the cutting zone to a level that causes the material to plasticize, which makes it easier to machine, Anderson said. Without plasticization, tool edge chipping and top and flank slicing can occur.
According to Anderson, the phase-toughened ceramic’s high strength enables tool to efficiently cut without the need for full plasticization to occur. This ability is beneficial when turning a large and heavy or imbalanced part that’s not practical to spin at high speed. For instance, when machining an imbalanced part made of Inconel 718 with a hardness of 46 to 48 HRC, the low-end cutting speed needed for ceramics to plasticize the material is about 550 to 600 sfm. In contrast, an insert can run at 350 to 400 sfm whereas a carbide tool would reach only 150 to 180 sfm.
The latest advanced composite material for effectively machining HRSAs since the introduction of whisker ceramics. The material’s unique physical characteristics provide exceptional tool life, impart fine surface finishes and enable cutting speeds up to 1,600 sfm.
Ceramic cutting tools are just for roughing, according to Benkóczy. Because of the severe tool wear ceramic tools experience, such as chipping of the cutting edge and a significant reduction in the tool radius, they can continue to perform roughing but are not suitable for finishing.
“The finishing we do with carbide, and the roughing we do with ceramic,” he said.
That choice of cutting tool materials is particularly prevalent in the aerospace industry, such as when machining an HRSA engine part, because the production process is usually certified and cannot be easily changed, Benkóczy said.
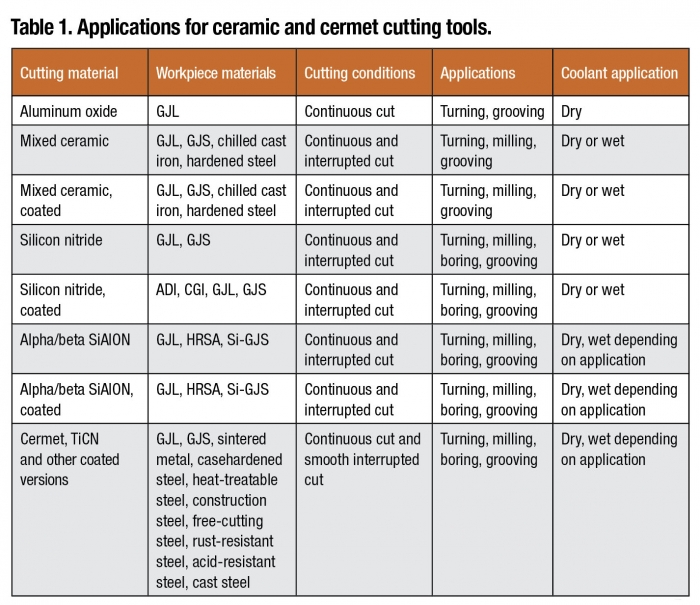
“Certification costs are immense for aerospace engines,” he said. “If an engine is being started from scratch or when a new line is added or something major changes, then, of course, it’s an open box and new ideas can be put in.”
Anderson concurred that Federal Aviation Administration regulations and certifications may prevent anything but carbide tools from being used for an aerospace finishing application but emphasized that ceramic tools are not just for roughing. The traditional mind-set sees ceramics as highly effective for roughing when there are no interruptions and the setup is stable.
“There’s a lot of history that we’re constantly working to change the mind-set about,” he said, adding that aerospace parts manufacturers are realizing that ceramic tools can impart fine surface finishes and are more than acceptable for finishing HRSA engine parts.
When milling with a ceramic tool, Benkóczy recommends dry machining to avoid increasing the thermal shock on the cutting edge as it transitions back and forth from its brief engagement with the workpiece to a longer airtime. In addition to not decreasing tool life, dry machining avoids having to clean the mess that coolant can create and exposing workers to metalworking fluid chemicals. Pressurized air, however, can be applied to help clear the chips from the cutting zone.
“If you’re unlucky, you may even increase workhardening in the workpiece material,” he said about coolant application.
Applying coolant when roughing cast iron, though, can help, Wilshire said. “A lot of shops like to run coolant just to keep the dust particles down.”
When turning with ceramic tools, Andersson suggests using coolant. “If you don’t,” he said, “as you engage continuously, you will have a continuous increase in temperature. You want to have a high temperature—but a high, even temperature. That’s why you always use coolant when it comes to turning.”
For cermet cutters, Wilshire said minimum quantity lubrication is a viable option in addition to dry machining. “Cermets have a higher hot hardness than carbide, so they can withstand higher temperatures.”
When running dry, a tool coating can provide an effective thermal barrier while increasing a tool’s hardness and reducing wear, said Beck. For ceramic tools, “CVD coatings are the most common coatings, starting from a dual-layer system and going up to a multilayer system. TiC/TiN or Al2O3 layers are the most common.”
Howard concurred that ceramic inserts are primarily CVD-coated, but the coatings themselves have a limited effect on overall performance.
Beck added that, depending on the application, a PVD coating offers a high wear resistance and high adhesion resistance, which prevents built-up edge and burr formation when machining ductile materials. “Generally, CVD is the best method for coating, which enables higher tool life and increased speeds and feeds.”
However, a tool material must have enough conductivity to enable a PVD coating to be deposited on it, Wilshire explained. For example, Al2O3 ceramics are conductive enough, but SiN ceramics are not. “So there we go with the CVD Al2O3 coating.”
When possible, many end users opt for a PVD TiN coating because, as the gold-colored coating wears, they can easily identify a used cutting edge, Wilshire said. “It really doesn’t improve tool life so much.”
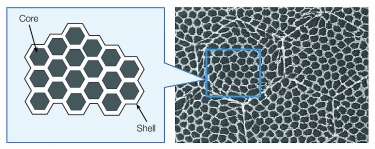
To extend tool life, WOTEK offers its PVD coating. It is an AlTiN-based coating with a plethora of additives to tailor its properties, according to Wilshire. The dark gray coating also has a nanolayer structure with lubricity between each hard layer to enhance wear resistance and enable higher cutting speeds.
Because ceramics have a low coefficient of friction, getting a coating to adhere can be a challenge.
Nonetheless, when the coating, substrate, microgeometry, and pre- and post-treatment processes for a ceramic grade are optimized, incredible productivity occurs. According to Andersson, this high level of productivity is even possible when machining metals that aren’t usually considered in ceramics’ domain. “It has proven that it can machining PH stainless at speeds that are 5 to 10 times higher than that of carbide.”
In addition, it’s important that end users understand the best practice for machining with ceramics to achieve the ideal performance of the insert, Howard said. This includes programming ramping cuts, varying the DOC and reducing the feed going into a corner.
But as technical center manager Wilshire is quite familiar with the metal cutting capabilities of ceramic composite, as well as cermet, tools. The Hendersonville, N.C.-based toolmaker’s offerings include ceramic and cermet inserts for milling and turning. The types of ceramic tool materials include Al2O3, silicon nitride and silicon aluminum oxynitride (SiAlON).
Because SiN and SiAlON are relatively tough ceramics, especially at elevated temperatures, tools made of these materials are best-suited for roughing cast iron and heat-resistant superalloys (HRSAs), Wilshire said. “The Al2O3-based ceramics are still pretty brittle, so those are mainly for hard turning with no interruptions or for finishing cast iron.”
According to Steve Howard, marketing and engineering manager of cutting tools, SiN-based ceramic grades, have twice the fracture toughness of alumina-based ceramics. This level of toughness enables turning and milling cast iron at speeds up to 3,000 sfm.
In addition, SiN-based grades blend the strength of silicon-nitride ceramic with the heat and wear resistance of alumina oxide, Howard said. “SiN-based grades, with SX3 being the newest, feature excellent strength and thermal shock resistance under high temperatures, as well as notching resistance, which are ideal characteristics for high-speed machining of heat-resistant alloys common in aerospace, power generation and oil and gas industries.”
The five grades of black ceramics—alumina with hard carbide added to improve toughness and hardness—have a high-hot hardness and low plasticity to turn steel, chilled or ductile iron rolls and some powdered metals as hard as 62 HRC, Howard said. “Our finest grain structure can perform finishing cuts on steels up to 70 HRC. These ceramics are cost-effective alternatives for applications previously limited to CBNs.”
Like the name implies, cermet combines ceramic elements (such as TiC, TiCN and molybdenum carbide) with metallic binders (such as nickel, as well as molybdenum and cobalt to a lesser degree), Wilshire noted.
Cermet is more brittle than tungsten carbide, so cermet cutting tools are susceptible to chipping and breaking when stressed while taking heavy cuts, he said. As a result, more users consider cermet tools suitable for finishing only at a 0.010" to 0.020" DOC. However, cermet tools that can take a 0.060" to 0.080" DOC in “clean” material.
“If you have interruptions or scale, carbide is still going to be the way to go there,” he said.
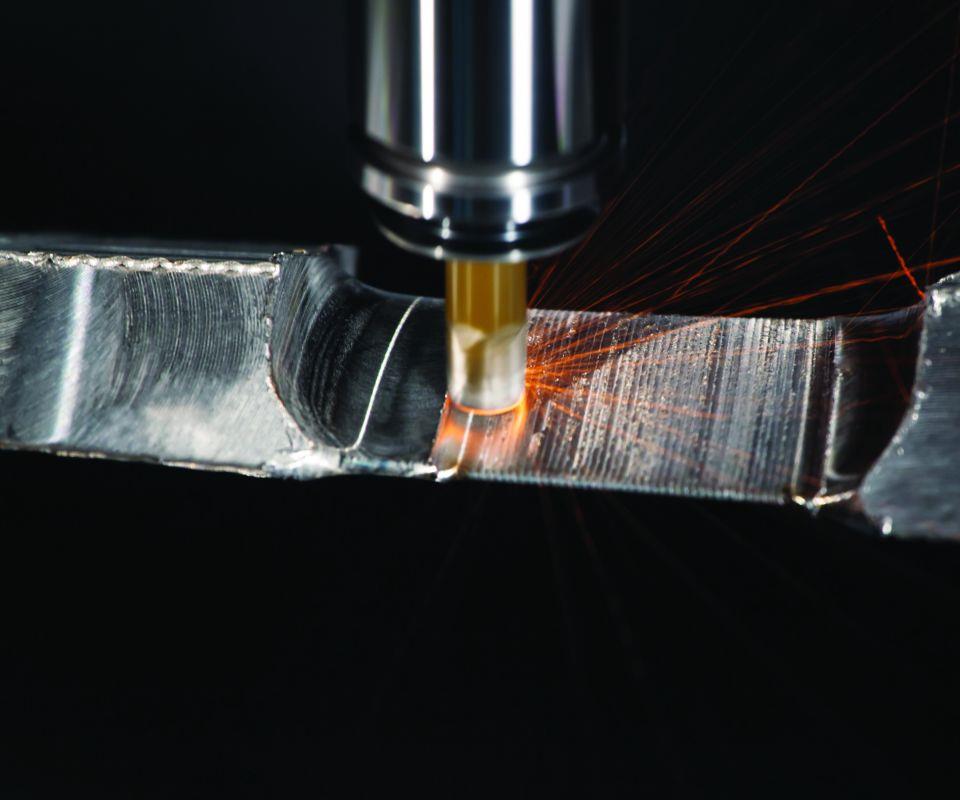
Technical Developments
Although cermet and ceramic cutting tools have a long history, toolmakers continue to make advancements. One such advancement at creates a gradient in cermet material via a combination of techniques employed during the insert pressing and sintering processes, Wilshire said. “We call those ‘hybrid cermets’ because they offer a hard outer layer and more toughness in the center.”
Combining tough and hard in ceramic inserts. Wilshire explained that the company is able to produce a honeycomb-shaped grain structure in which the hexagon shape that forms the honeycomb is made of tougher ceramic than the harder central core that it surrounds. If the center part develops a crack, the crack will not propagate beyond the shell and cause the insert to break.
“It competes with the whisker material,” he said.
WOTEK does not produce inserts made of whisker-reinforced ceramic but, according to Wilshire, offers a second technology to improve the fracture resistance of ceramic similar to one reinforced with SiC crystals. In the company’s newer SiAlON materials, the grain structure is manipulated to cause some of the grains to become needle-shaped, which functions like whiskers. “During the sintering process, the crystals actually grow,” he said. The structure also includes hard particles for wear resistance.
With Reinforcements
The whisker-reinforced ceramics, having introduced the uncoated grade in 1985, said Jan Anderson, global director of the TechTeam and marketing for the Saegertown, Pa., toolmaker. Later introduced the coated whisker-reinforced ceramic, which has a different substrate and a nanostructured coating.
“There are a lot of applications where whisker-reinforced ceramics are still—by far—the best solution,” Anderson said.
A more recent development is phase-toughened ceramic. It is a thermally stable, whisker- and particulate-toughened SiN with almost twice the strength of any other commercially available ceramic too.
In theory, all ceramic tools remove metal by raising the temperature in the cutting zone to a level that causes the material to plasticize, which makes it easier to machine, Anderson said. Without plasticization, tool edge chipping and top and flank slicing can occur.
According to Anderson, the phase-toughened ceramic’s high strength enables tool to efficiently cut without the need for full plasticization to occur. This ability is beneficial when turning a large and heavy or imbalanced part that’s not practical to spin at high speed. For instance, when machining an imbalanced part made of Inconel 718 with a hardness of 46 to 48 HRC, the low-end cutting speed needed for ceramics to plasticize the material is about 550 to 600 sfm. In contrast, an insert can run at 350 to 400 sfm whereas a carbide tool would reach only 150 to 180 sfm.
The latest advanced composite material for effectively machining HRSAs since the introduction of whisker ceramics. The material’s unique physical characteristics provide exceptional tool life, impart fine surface finishes and enable cutting speeds up to 1,600 sfm.
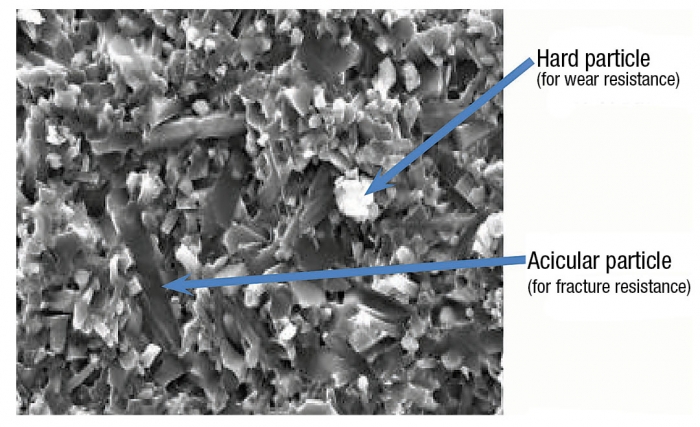
In the Rough
Ceramic cutting tools are just for roughing, according to Benkóczy. Because of the severe tool wear ceramic tools experience, such as chipping of the cutting edge and a significant reduction in the tool radius, they can continue to perform roughing but are not suitable for finishing.
“The finishing we do with carbide, and the roughing we do with ceramic,” he said.
That choice of cutting tool materials is particularly prevalent in the aerospace industry, such as when machining an HRSA engine part, because the production process is usually certified and cannot be easily changed, Benkóczy said.
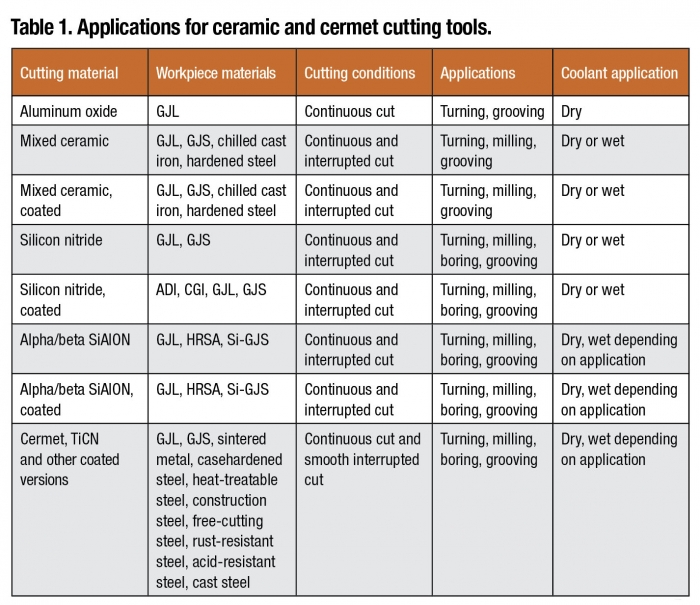
“Certification costs are immense for aerospace engines,” he said. “If an engine is being started from scratch or when a new line is added or something major changes, then, of course, it’s an open box and new ideas can be put in.”
Anderson concurred that Federal Aviation Administration regulations and certifications may prevent anything but carbide tools from being used for an aerospace finishing application but emphasized that ceramic tools are not just for roughing. The traditional mind-set sees ceramics as highly effective for roughing when there are no interruptions and the setup is stable.
“There’s a lot of history that we’re constantly working to change the mind-set about,” he said, adding that aerospace parts manufacturers are realizing that ceramic tools can impart fine surface finishes and are more than acceptable for finishing HRSA engine parts.
Cool and Coated
When milling with a ceramic tool, Benkóczy recommends dry machining to avoid increasing the thermal shock on the cutting edge as it transitions back and forth from its brief engagement with the workpiece to a longer airtime. In addition to not decreasing tool life, dry machining avoids having to clean the mess that coolant can create and exposing workers to metalworking fluid chemicals. Pressurized air, however, can be applied to help clear the chips from the cutting zone.
“If you’re unlucky, you may even increase workhardening in the workpiece material,” he said about coolant application.
Applying coolant when roughing cast iron, though, can help, Wilshire said. “A lot of shops like to run coolant just to keep the dust particles down.”
When turning with ceramic tools, Andersson suggests using coolant. “If you don’t,” he said, “as you engage continuously, you will have a continuous increase in temperature. You want to have a high temperature—but a high, even temperature. That’s why you always use coolant when it comes to turning.”
For cermet cutters, Wilshire said minimum quantity lubrication is a viable option in addition to dry machining. “Cermets have a higher hot hardness than carbide, so they can withstand higher temperatures.”
When running dry, a tool coating can provide an effective thermal barrier while increasing a tool’s hardness and reducing wear, said Beck. For ceramic tools, “CVD coatings are the most common coatings, starting from a dual-layer system and going up to a multilayer system. TiC/TiN or Al2O3 layers are the most common.”
Howard concurred that ceramic inserts are primarily CVD-coated, but the coatings themselves have a limited effect on overall performance.
Beck added that, depending on the application, a PVD coating offers a high wear resistance and high adhesion resistance, which prevents built-up edge and burr formation when machining ductile materials. “Generally, CVD is the best method for coating, which enables higher tool life and increased speeds and feeds.”
However, a tool material must have enough conductivity to enable a PVD coating to be deposited on it, Wilshire explained. For example, Al2O3 ceramics are conductive enough, but SiN ceramics are not. “So there we go with the CVD Al2O3 coating.”
When possible, many end users opt for a PVD TiN coating because, as the gold-colored coating wears, they can easily identify a used cutting edge, Wilshire said. “It really doesn’t improve tool life so much.”
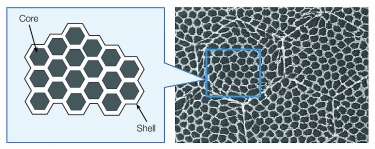
To extend tool life, WOTEK offers its PVD coating. It is an AlTiN-based coating with a plethora of additives to tailor its properties, according to Wilshire. The dark gray coating also has a nanolayer structure with lubricity between each hard layer to enhance wear resistance and enable higher cutting speeds.
Because ceramics have a low coefficient of friction, getting a coating to adhere can be a challenge.
Nonetheless, when the coating, substrate, microgeometry, and pre- and post-treatment processes for a ceramic grade are optimized, incredible productivity occurs. According to Andersson, this high level of productivity is even possible when machining metals that aren’t usually considered in ceramics’ domain. “It has proven that it can machining PH stainless at speeds that are 5 to 10 times higher than that of carbide.”
In addition, it’s important that end users understand the best practice for machining with ceramics to achieve the ideal performance of the insert, Howard said. This includes programming ramping cuts, varying the DOC and reducing the feed going into a corner.