陶瓷和金屬陶瓷立銑刀的切削優勢
2020-04-02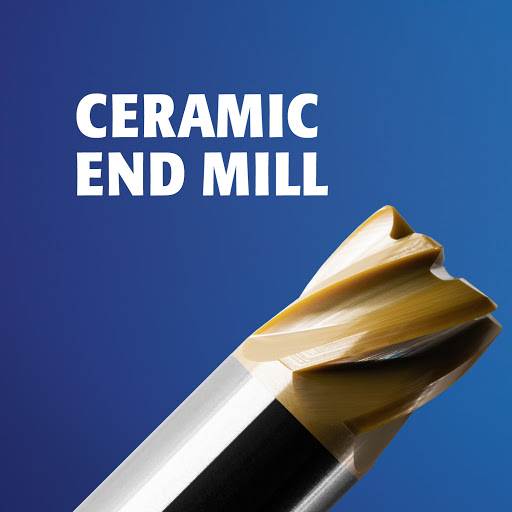
"每個人對陶瓷的印像都是一個陶瓷咖啡杯,只要它摔下來,它就會碎掉。"布萊恩-威爾希爾說。 "你怎麼能用它來切削金屬呢?"
但作為技術中心經理,Wilshire對陶瓷複合切削切削銑刀以及銑刀的金屬切削能力相當熟悉。這家總部位於北卡羅來納州亨德森維爾的銑刀製造商提供的產品包括用於銑削和車削的陶瓷和楔形刀片。陶瓷銑刀材料的類型包括Al2O3、氮化矽和矽鋁氧化氮化物(SiAlON)。
Wilshire說,由於SiN和SiAlON是相對堅硬的陶瓷,特別是在高溫下,由這些材料製成的銑刀最適合粗加工鑄鐵和耐熱超合金(HRSA)。 "基於Al2O3的陶瓷仍然相當脆,所以主要用於無中斷的硬車削或精加工鑄鐵。"
據切削銑刀市場和工程經理Steve Howard說,SiN陶瓷牌號的斷裂韌性是氧化鋁基陶瓷的兩倍。這樣的韌性水平使得車削和銑削鑄鐵的速度可以達到3,000 sfm。
此外,SiN基牌號融合了氮化矽陶瓷的強度和氧化鋁的耐熱性和耐磨性,Howard說。 "以SiN為基礎的牌號,其中SX3是最新的牌號,在高溫下具有優異的強度和抗熱震性能,以及抗切口性能,是航空航天、發電和油氣工業中常見的耐熱合金高速加工的理想特性。"
Howard說,這五種牌號的黑色陶瓷--添加了硬質碳化物的氧化鋁以提高韌性和硬度--具有高熱硬度和低塑性,可使鋼、冷軋或球墨鑄鐵輥和一些粉末狀金屬的硬度達到62HRC。 "我們最好的晶粒結構可以對高達70 HRC的鋼進行精加工切削。這些陶瓷是以前僅限於CBNs的應用中具有成本效益的替代品。"
Wilshire指出,正如其名稱所暗示的那樣,金屬陶瓷將陶瓷元素(如TiC、TiCN和碳化鉬)與金屬粘結劑(如鎳,以及鉬和鈷(程度較低))結合在一起。
他說,金屬陶瓷比碳化鎢更脆,因此,金屬陶瓷切削銑刀在承受重切削時受力時容易發生崩裂和斷裂。因此,更多的用戶認為金屬陶瓷銑刀只適合在0.010“至0.020” DOC下進行精加工。然而,在“純粹”材料中,能承受0.060“至0.080” DOC的咬合銑刀。
他說:“如果出現中斷或結垢,硬質合金仍是解決問題的根本。”
儘管金屬陶瓷和陶瓷切削銑刀的歷史悠久,但切削銑刀製造商仍在不斷進步。威爾夏說,通過鑲件壓制和燒結過程中採用的多種技術在金屬陶瓷材料中產生了梯度。“我們稱這些為“混合金屬陶瓷”,是因為它們提供了堅硬的外層,且具有更高的韌性。”
結合堅硬和堅硬的陶瓷刀片。威爾希爾(Wilshire)解釋說,該公司能夠生產出蜂窩狀的晶粒結構,其中形成蜂窩的六邊形形狀由比其所包圍的中心硬核更堅硬的陶瓷製成。如果中心部分出現裂紋,裂紋將不會擴展到殼體之外,也不會導致嵌件斷裂。
他說:“晶須材料與之相互競爭。”
WOTEK不生產晶須增強陶瓷製成的刀片,但據威爾希爾說,它提供了第二種技術來改善陶瓷的抗斷裂性能,類似於用SiC晶體增強的陶瓷。在該公司較新的SiAlON材料中,對晶粒結構進行了處理,以使某些晶粒變為針狀,其功能類似於晶須。他說:“在燒結過程中,晶體實際上會生長。” 該結構還包括用於耐磨的硬顆粒。
另一方面,晶須增強陶瓷於1985年推出了無鍍層等級,TechTeam的全球總監兼賓夕法尼亞州Saegertown的市場行銷總監Jan Anderson說。隨後帶鍍層的晶須增強陶瓷問世,後者俱有不同的基材和納米結構鍍層。
“到目前為止,在許多應用中,晶須增強陶瓷仍然是最佳解決方案,”安德森說。
最新發展是其相韌化陶瓷,它是一種熱穩定,晶須和顆粒增韌的SiN,其強度幾乎是市售陶瓷切削銑刀的兩倍。
從理論上來講,所有陶瓷切削銑刀都會通過將切削區域中的溫度升高到可塑化的水平來去除金屬,從而使加工變得更加容易,Anderson說。如果不進行塑化,則可能會發生刀刃碎裂以及頂部和側面的切片。
根據安德森(Anderson)的說法,相韌化陶瓷的高強度切削銑刀能夠有效地切削,而無需進行完全塑化。當轉動大而重或不平衡的零件時,此功能非常有用,但不適合高轉速。例如,當加工硬度為46至48 HRC的Inconel 718製成的不平衡零件時,陶瓷增塑材料所需的低端切削速度約為550至600 sfm。相比之下,刀片的加工速度為350至400 sfm,而硬質合金銑刀僅為150至180 sfm。
自從引入晶須陶瓷以來,代表可有效加工HRSA的最新先進複合材料。該材料獨特的物理特性可延長銑刀壽命,提供出色的表面光潔度,並使切削速度高達1600 sfm。
Benkóczy說,陶瓷切削銑刀僅用於粗加工。由於陶瓷銑刀的嚴重磨損,例如切削刃的崩裂和銑刀半徑的明顯減小,它們可以繼續進行粗加工,但不適合精加工。
他說:“我們用硬質合金銑刀進行精加工,用陶瓷銑刀進行粗加工,”
Benkóczy說,這種切削切削銑刀材料的選擇在航空航天工業中尤其普遍,例如在加工HRSA發動機零件時,因為生產過程通常是經過認證的,而且不容易更改。
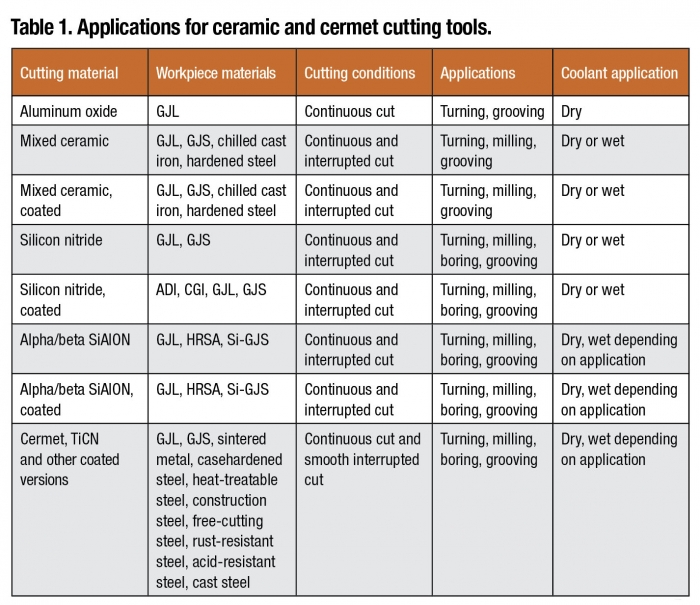
他說:“航空發動機的認證成本龐大。” “如果有其他新航線,新的引擎,或者有新的代碼行或發生了重大變化,當然,這行業在互相激勵下,可以蹦出新的想法。”
安德森同意,聯邦航空管理局的法規和認證可能會阻止硬質合金銑刀被用於航空航天,但他強調陶瓷銑刀不僅用於粗加工。傳統觀念認為,在不間斷且安裝穩定的情況下,陶瓷對於粗加工非常有效。
他說:“歷史案例,我們一直在努力改變人們的觀念。”他補充說,航空零件製造商已經意識到陶瓷切削銑刀可以提供良好的表面光潔度,並且對於HRSA發動機零件的精加工來說是可以接受的。
使用陶瓷切削銑刀銑削時,Benkóczy建議進行乾式加工,以避免切削刃與工件的短暫嚙合過度來回到較長的磨削時間增加切削刃上的熱衝擊。除了不減少銑刀壽命外,乾式加工還避免了必須清理冷卻液可能造成的混亂並將工人暴露於金屬加工液化學品的麻煩。但是,可以使用吹氣清除切削區域的切屑。
他說:“如果運氣不好,您甚至可以提高工件材料的加工硬化性。”
威爾希爾說,在粗加工鑄鐵時使用冷卻液會有所幫助。“許多車間都喜歡使用冷卻液只是為了減少灰塵顆粒。”
當使用陶瓷切削銑刀車削時,Anderson建議使用冷卻液。他說:“如果不這樣做,隨著銑削時間,溫度會不斷升高。高溫銑削,要有一個理想值的均勻高溫。因此,加工轉向處皆使用冷卻液。”
對於金屬陶瓷銑刀,威爾希爾表示,除了乾式加工之外,最小量的潤滑也是一種可行的選擇。“金屬陶瓷具有比碳化物更高的熱硬度,因此它們可以承受更高的溫度。”
貝克說,在空轉時,切削銑刀鍍層可以提供有效的隔熱層,同時增加切削銑刀的硬度並減少磨損。對於陶瓷切削銑刀,“ CVD鍍層是最常見的鍍層,從雙層系統開始,一直到多層系統。最常見的是TiC / TiN或Al 2 O 3層。”
霍華德(Howard)認為陶瓷刀片主要是CVD鍍層的,但是鍍層本身對整體性能的影響有限。
貝克補充說,根據不同的應用,PVD鍍層具有高耐磨性和高附著力,可防止在加工易延展材料時積聚的邊緣和毛刺。“通常,CVD是最好的鍍層方法,它可以延長切削銑刀壽命並提高速度和進給速度。”
然而,威爾希爾解釋說,切削銑刀材料必須具有足夠的導電性,以使PVD鍍層能夠沉積在其上。例如,Al 2 O 3陶瓷具有足夠的導電性,而SiN陶瓷則不能導電。“因此,我們提供了CVD Al 2 O 3鍍層。”
Wilshire說,在可能的情況下,許多技師會選擇PVD TiN鍍層,因為隨著金色鍍層的磨損,他們可以輕鬆地識別出用過的切削刃。“它的確不能大大提高切削銑刀的使用壽命。”
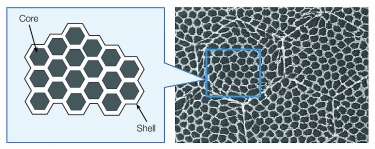
為了延長切削銑刀壽命,WOTEK有PVD鍍層,這是一種基於AlTiN的鍍層,其中包含大量添加劑。深灰色鍍層還具有納米層結構,在每個硬質層之間具有潤滑性,以增強耐磨性並實現更高的切削速度。
由於陶瓷的摩擦係數很低,因此要使鍍層黏附於陶瓷可能是一個挑戰,我們必須發明另一種鍍層。
但是,當優化陶瓷牌號的鍍層,基材,微幾何形狀以及預處理和後處理工藝時,仍可實現令人難以置信的生產率。根據安德森(Anderson)的說法,即使在加工陶瓷領域通常不考慮的金屬時,也可以實現如此高的生產率。“已經證明可以加工PH不銹鋼,其速度是碳化鎢的五到十倍。”
此外,重要的是,技師必須了解用陶瓷加工的最佳方法,以實現刀片的理想性能,霍華德說。這包括編程斜切,更改DOC並減少進給角的進給。
但作為技術中心經理,Wilshire對陶瓷複合切削切削銑刀以及銑刀的金屬切削能力相當熟悉。這家總部位於北卡羅來納州亨德森維爾的銑刀製造商提供的產品包括用於銑削和車削的陶瓷和楔形刀片。陶瓷銑刀材料的類型包括Al2O3、氮化矽和矽鋁氧化氮化物(SiAlON)。
Wilshire說,由於SiN和SiAlON是相對堅硬的陶瓷,特別是在高溫下,由這些材料製成的銑刀最適合粗加工鑄鐵和耐熱超合金(HRSA)。 "基於Al2O3的陶瓷仍然相當脆,所以主要用於無中斷的硬車削或精加工鑄鐵。"
據切削銑刀市場和工程經理Steve Howard說,SiN陶瓷牌號的斷裂韌性是氧化鋁基陶瓷的兩倍。這樣的韌性水平使得車削和銑削鑄鐵的速度可以達到3,000 sfm。
此外,SiN基牌號融合了氮化矽陶瓷的強度和氧化鋁的耐熱性和耐磨性,Howard說。 "以SiN為基礎的牌號,其中SX3是最新的牌號,在高溫下具有優異的強度和抗熱震性能,以及抗切口性能,是航空航天、發電和油氣工業中常見的耐熱合金高速加工的理想特性。"
Howard說,這五種牌號的黑色陶瓷--添加了硬質碳化物的氧化鋁以提高韌性和硬度--具有高熱硬度和低塑性,可使鋼、冷軋或球墨鑄鐵輥和一些粉末狀金屬的硬度達到62HRC。 "我們最好的晶粒結構可以對高達70 HRC的鋼進行精加工切削。這些陶瓷是以前僅限於CBNs的應用中具有成本效益的替代品。"
Wilshire指出,正如其名稱所暗示的那樣,金屬陶瓷將陶瓷元素(如TiC、TiCN和碳化鉬)與金屬粘結劑(如鎳,以及鉬和鈷(程度較低))結合在一起。
他說,金屬陶瓷比碳化鎢更脆,因此,金屬陶瓷切削銑刀在承受重切削時受力時容易發生崩裂和斷裂。因此,更多的用戶認為金屬陶瓷銑刀只適合在0.010“至0.020” DOC下進行精加工。然而,在“純粹”材料中,能承受0.060“至0.080” DOC的咬合銑刀。
他說:“如果出現中斷或結垢,硬質合金仍是解決問題的根本。”
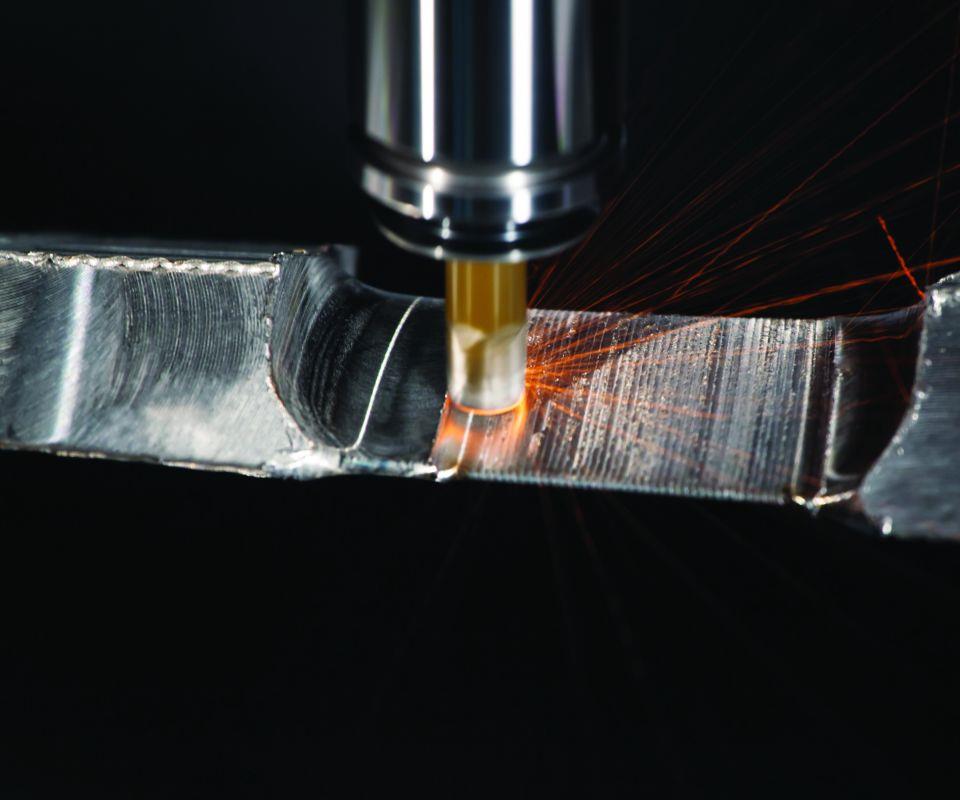
技術發展
儘管金屬陶瓷和陶瓷切削銑刀的歷史悠久,但切削銑刀製造商仍在不斷進步。威爾夏說,通過鑲件壓制和燒結過程中採用的多種技術在金屬陶瓷材料中產生了梯度。“我們稱這些為“混合金屬陶瓷”,是因為它們提供了堅硬的外層,且具有更高的韌性。”
結合堅硬和堅硬的陶瓷刀片。威爾希爾(Wilshire)解釋說,該公司能夠生產出蜂窩狀的晶粒結構,其中形成蜂窩的六邊形形狀由比其所包圍的中心硬核更堅硬的陶瓷製成。如果中心部分出現裂紋,裂紋將不會擴展到殼體之外,也不會導致嵌件斷裂。
他說:“晶須材料與之相互競爭。”
WOTEK不生產晶須增強陶瓷製成的刀片,但據威爾希爾說,它提供了第二種技術來改善陶瓷的抗斷裂性能,類似於用SiC晶體增強的陶瓷。在該公司較新的SiAlON材料中,對晶粒結構進行了處理,以使某些晶粒變為針狀,其功能類似於晶須。他說:“在燒結過程中,晶體實際上會生長。” 該結構還包括用於耐磨的硬顆粒。
強化
另一方面,晶須增強陶瓷於1985年推出了無鍍層等級,TechTeam的全球總監兼賓夕法尼亞州Saegertown的市場行銷總監Jan Anderson說。隨後帶鍍層的晶須增強陶瓷問世,後者俱有不同的基材和納米結構鍍層。
“到目前為止,在許多應用中,晶須增強陶瓷仍然是最佳解決方案,”安德森說。
最新發展是其相韌化陶瓷,它是一種熱穩定,晶須和顆粒增韌的SiN,其強度幾乎是市售陶瓷切削銑刀的兩倍。
從理論上來講,所有陶瓷切削銑刀都會通過將切削區域中的溫度升高到可塑化的水平來去除金屬,從而使加工變得更加容易,Anderson說。如果不進行塑化,則可能會發生刀刃碎裂以及頂部和側面的切片。
根據安德森(Anderson)的說法,相韌化陶瓷的高強度切削銑刀能夠有效地切削,而無需進行完全塑化。當轉動大而重或不平衡的零件時,此功能非常有用,但不適合高轉速。例如,當加工硬度為46至48 HRC的Inconel 718製成的不平衡零件時,陶瓷增塑材料所需的低端切削速度約為550至600 sfm。相比之下,刀片的加工速度為350至400 sfm,而硬質合金銑刀僅為150至180 sfm。
自從引入晶須陶瓷以來,代表可有效加工HRSA的最新先進複合材料。該材料獨特的物理特性可延長銑刀壽命,提供出色的表面光潔度,並使切削速度高達1600 sfm。
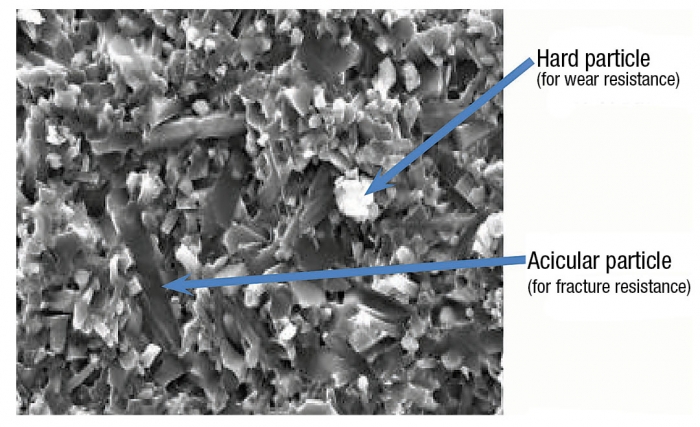
粗加工
Benkóczy說,陶瓷切削銑刀僅用於粗加工。由於陶瓷銑刀的嚴重磨損,例如切削刃的崩裂和銑刀半徑的明顯減小,它們可以繼續進行粗加工,但不適合精加工。
他說:“我們用硬質合金銑刀進行精加工,用陶瓷銑刀進行粗加工,”
Benkóczy說,這種切削切削銑刀材料的選擇在航空航天工業中尤其普遍,例如在加工HRSA發動機零件時,因為生產過程通常是經過認證的,而且不容易更改。
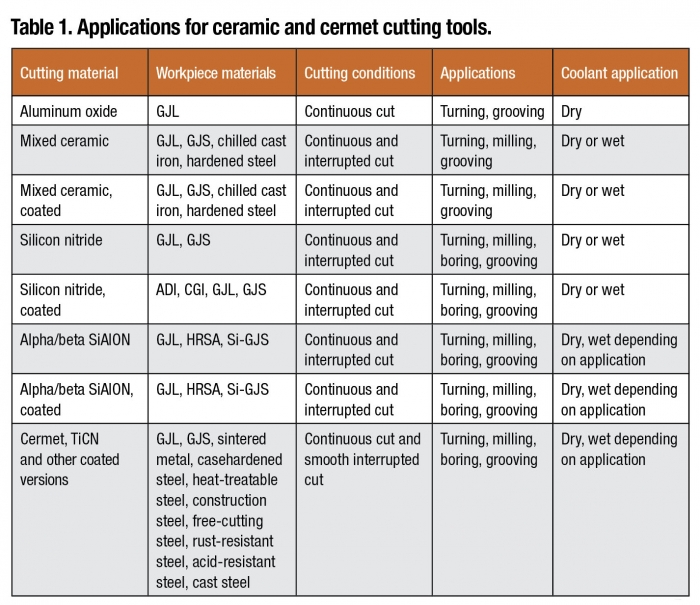
他說:“航空發動機的認證成本龐大。” “如果有其他新航線,新的引擎,或者有新的代碼行或發生了重大變化,當然,這行業在互相激勵下,可以蹦出新的想法。”
安德森同意,聯邦航空管理局的法規和認證可能會阻止硬質合金銑刀被用於航空航天,但他強調陶瓷銑刀不僅用於粗加工。傳統觀念認為,在不間斷且安裝穩定的情況下,陶瓷對於粗加工非常有效。
他說:“歷史案例,我們一直在努力改變人們的觀念。”他補充說,航空零件製造商已經意識到陶瓷切削銑刀可以提供良好的表面光潔度,並且對於HRSA發動機零件的精加工來說是可以接受的。
冷卻和鍍層
使用陶瓷切削銑刀銑削時,Benkóczy建議進行乾式加工,以避免切削刃與工件的短暫嚙合過度來回到較長的磨削時間增加切削刃上的熱衝擊。除了不減少銑刀壽命外,乾式加工還避免了必須清理冷卻液可能造成的混亂並將工人暴露於金屬加工液化學品的麻煩。但是,可以使用吹氣清除切削區域的切屑。
他說:“如果運氣不好,您甚至可以提高工件材料的加工硬化性。”
威爾希爾說,在粗加工鑄鐵時使用冷卻液會有所幫助。“許多車間都喜歡使用冷卻液只是為了減少灰塵顆粒。”
當使用陶瓷切削銑刀車削時,Anderson建議使用冷卻液。他說:“如果不這樣做,隨著銑削時間,溫度會不斷升高。高溫銑削,要有一個理想值的均勻高溫。因此,加工轉向處皆使用冷卻液。”
對於金屬陶瓷銑刀,威爾希爾表示,除了乾式加工之外,最小量的潤滑也是一種可行的選擇。“金屬陶瓷具有比碳化物更高的熱硬度,因此它們可以承受更高的溫度。”
貝克說,在空轉時,切削銑刀鍍層可以提供有效的隔熱層,同時增加切削銑刀的硬度並減少磨損。對於陶瓷切削銑刀,“ CVD鍍層是最常見的鍍層,從雙層系統開始,一直到多層系統。最常見的是TiC / TiN或Al 2 O 3層。”
霍華德(Howard)認為陶瓷刀片主要是CVD鍍層的,但是鍍層本身對整體性能的影響有限。
貝克補充說,根據不同的應用,PVD鍍層具有高耐磨性和高附著力,可防止在加工易延展材料時積聚的邊緣和毛刺。“通常,CVD是最好的鍍層方法,它可以延長切削銑刀壽命並提高速度和進給速度。”
然而,威爾希爾解釋說,切削銑刀材料必須具有足夠的導電性,以使PVD鍍層能夠沉積在其上。例如,Al 2 O 3陶瓷具有足夠的導電性,而SiN陶瓷則不能導電。“因此,我們提供了CVD Al 2 O 3鍍層。”
Wilshire說,在可能的情況下,許多技師會選擇PVD TiN鍍層,因為隨著金色鍍層的磨損,他們可以輕鬆地識別出用過的切削刃。“它的確不能大大提高切削銑刀的使用壽命。”
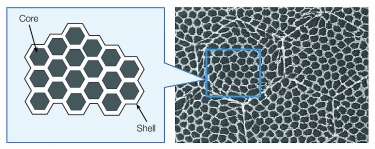
為了延長切削銑刀壽命,WOTEK有PVD鍍層,這是一種基於AlTiN的鍍層,其中包含大量添加劑。深灰色鍍層還具有納米層結構,在每個硬質層之間具有潤滑性,以增強耐磨性並實現更高的切削速度。
由於陶瓷的摩擦係數很低,因此要使鍍層黏附於陶瓷可能是一個挑戰,我們必須發明另一種鍍層。
但是,當優化陶瓷牌號的鍍層,基材,微幾何形狀以及預處理和後處理工藝時,仍可實現令人難以置信的生產率。根據安德森(Anderson)的說法,即使在加工陶瓷領域通常不考慮的金屬時,也可以實現如此高的生產率。“已經證明可以加工PH不銹鋼,其速度是碳化鎢的五到十倍。”
此外,重要的是,技師必須了解用陶瓷加工的最佳方法,以實現刀片的理想性能,霍華德說。這包括編程斜切,更改DOC並減少進給角的進給。