高速加工之最適化進給率探討
2020-04-24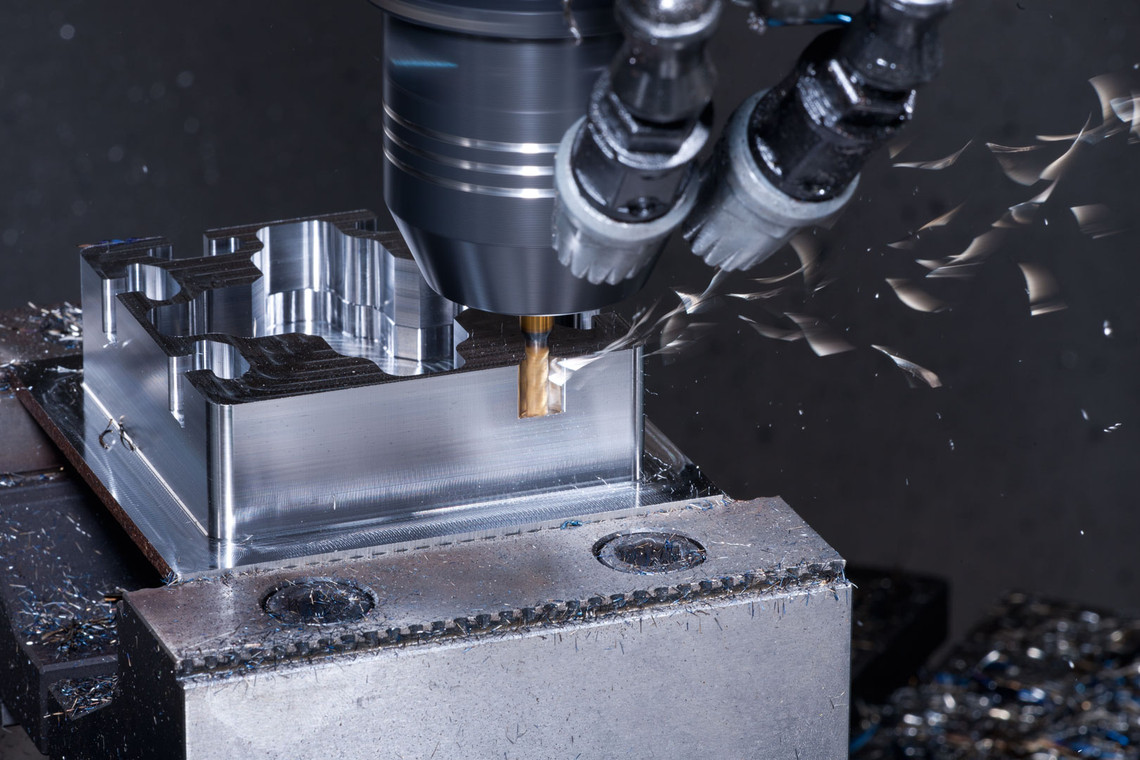
摘要
傳統 NC 加工是以固定的進給率進行材料的移除,由於所移除的體積及刀具的受力並非固定,因此銑刀容易因劇烈的負載而撓曲,影響加工精度與品質。本文先以逆向位移法來進行中加工與精加工的刀具路徑規劃,接著再分別對中加工與精加工提出不同的進給率調整的方法;中加工時藉由切削力與進給率的數學關係來調整進給率,使切削力量維持在適合的範圍內,刀具承受的負載不致於變化太大,而精加工時,以等體積移除率的觀念,藉由曲面的曲率來估計各個加工點體積,藉以改善固定進給率進行 NC加工所產生的缺點,以最適化其加工進給率。
壹、前言
NC 加工一般可分為粗加工(rough machining)、中加工(semi-roughing)及精加工(finish machining),其中粗加工大多使用等高加工,以直線式及輪廓式的刀具路徑,快速的移除工件胚料,形成成品雛型,因而產生階梯狀的餘料,如圖 1 所示,這些餘料將導致中加工的刀具切削 負荷變化太大,而產生刀具斷裂或切削不足的現象。經過中加工的修整後,精加工所要切削的 餘料大多均勻的被覆於模型上,如圖 2 所示,假如我們用傳統的想法將進給率固定,此時會遇 到因曲線中的曲率不同,而造成每一個 CL 點的移除體積都不同,產生的切削力也不同。而目 前文獻上對切削力維持在合理範圍內的方法大致可以區分為下列幾種:
1. 以刀具路徑來避免切削力過大:
例如切削路徑轉則處附近進行以圓滑路徑取代直角路 徑並補上插補路徑使切削力降低,如圖 3 所示[1]。另由擺線加工路徑,銑削溝槽,一 般傳統加工溝槽時,都以銑刀直徑為溝槽寬度直接銑削,此時切削力非常大,目前有 些軟體以擺線路徑去加工溝槽,使切削力下降[2]。
2. 以曲線技術來取代傳統的線性方法:
依靠曲線加工路徑中每個加工點的曲率不同,以 等體積移除率的觀念推導出控制器的即時插值器(Real-time Interpolator)的值,經過以 曲線技術計算後,如圖 4 所示。每個位置參數所對應的曲率不同,因而產生的進給率 也不同 [3~6]。此方法非常適用於精加工,而加工路徑是平滑的曲線型態時。本文有別於以上的方法,採用真實切削加工的體積移除率配合切削力的觀念,調整進給率,因此切削力會維持在一個合理的範圍內。文中分別對中加工、精加工提出兩種不同的自動調整進給率的方法,使加工過程中,切削力不至變動太激烈。當刀具移除材料體積較多時,則降低進給率,使切削力隨之降低,刀具承受的負載不至太大,加工精度與加工品質會較佳;相反的,當刀具移除材料體積較少時,則可提高進給率,以增加加工效率。
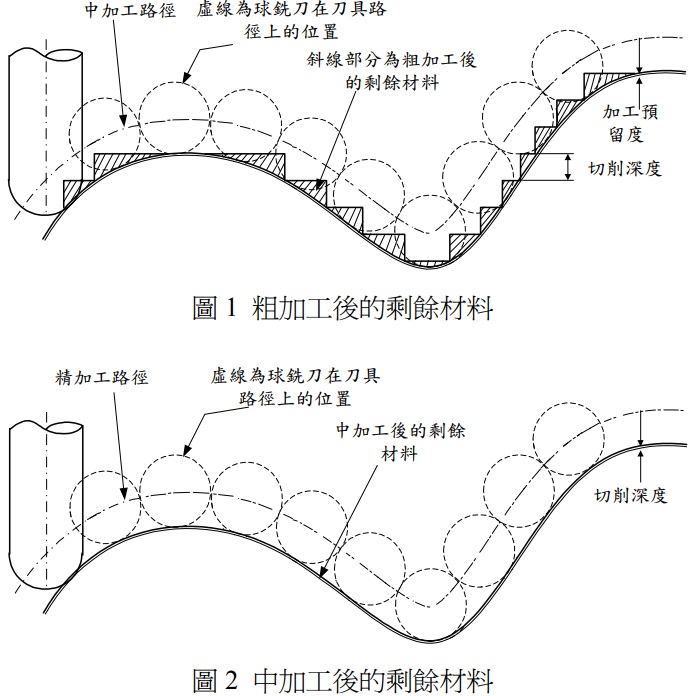
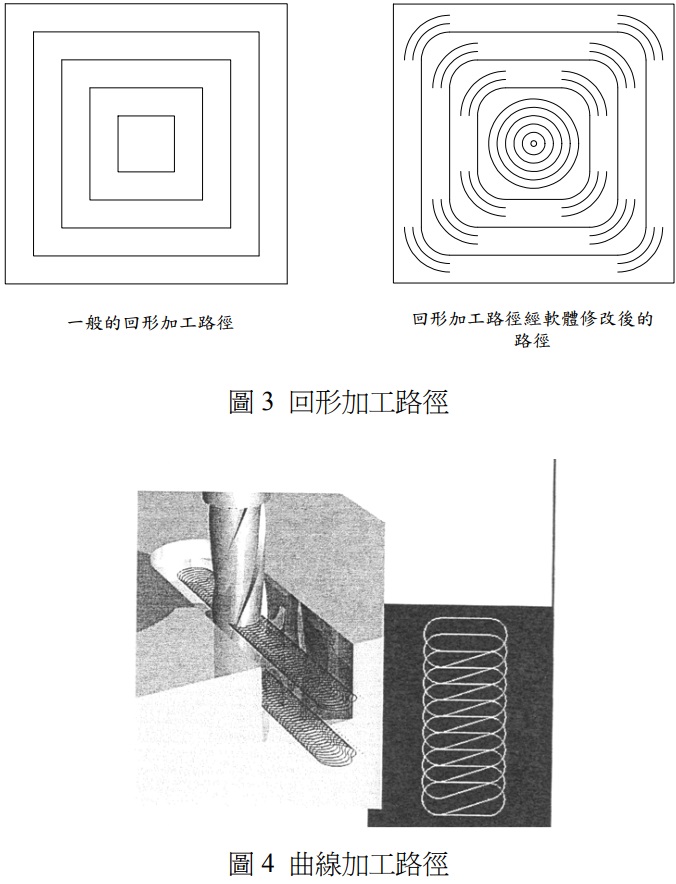
貳、加工路徑規劃
在精加工前,我們必須先移除粗切削所產生的階梯狀外型的剩餘體積,如圖 5 (a)所示,其 切削路徑是沿著曲面的表面保持一定的精加工預留量做曲面的切削,接著作中加工,如圖 5 (b) 所示,最後再進行一道精加工,以得到完整的模型,如圖 5 (c)所示。
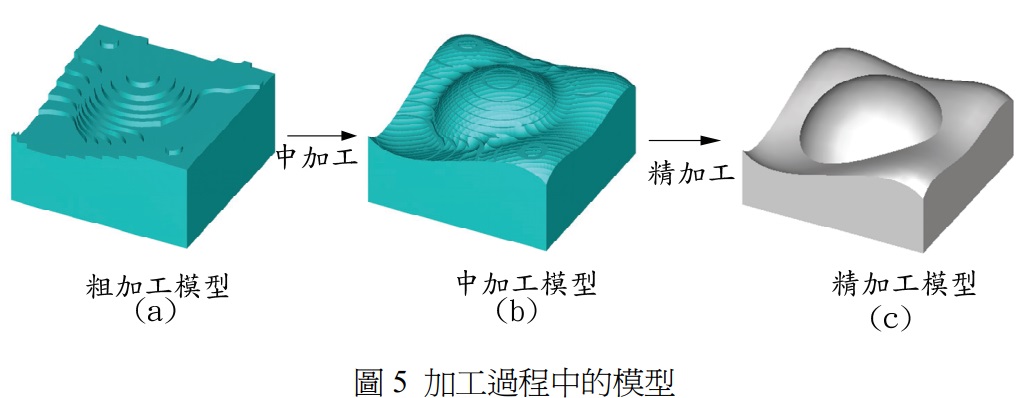
本論文刀具路徑規劃所採取的方法是以逆向位移法和通過點曲線來產生刀具路徑,配合步 進長度(Step length)及刀具間距(Step over)來求得適當的 CL 點,其詳細的步驟如下:
1. 以逆向位移法求刀具路徑。
2. 以刀具步進長度求適當的 CL 點位置。
3. 由刀具間距值配合 Z-map 方法求下一條刀具路徑。
2-1 逆向位移法
本研究是採用以逆向位移的方法來產生刀具路徑的控制點,如圖 6 所示,首先將刀具逆轉 並保持刀具中心落於曲面上,當刀具沿著曲面前進時,刀具輪廓所形成之最外圍的軌跡即位移 曲面。實際切削時,刀具中心保持在位移曲面上,沿著位移曲面切削,即可得到所要的曲面形 狀。以半徑為 R 之球形銑刀為例,若{ x(m), y(n), z(m, n) }表示目前的模型上 CC 點的座標,則 在此位置的位移曲面高度 z’(m, n)可由下式求得[7]。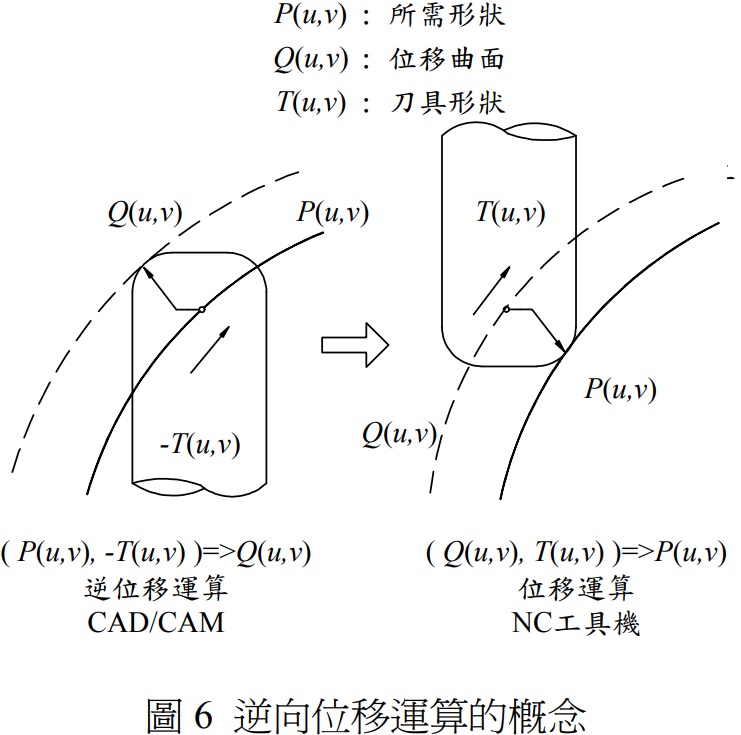
%E5%BC%8F.jpg)
(1)式表示刀具的中心位置為刀具投影面積範圍內“各格子點所在的曲面高度與刀具曲面高度的和”的最大值,式中 h(i,j,m,n:R)表示格子點位置(i,j)上的刀具曲面高度。 當得到格子點位置後,再以通過點曲線把所有同一列的格子點連成一條新曲線,圖 7 所示,此曲線即為刀具路徑。
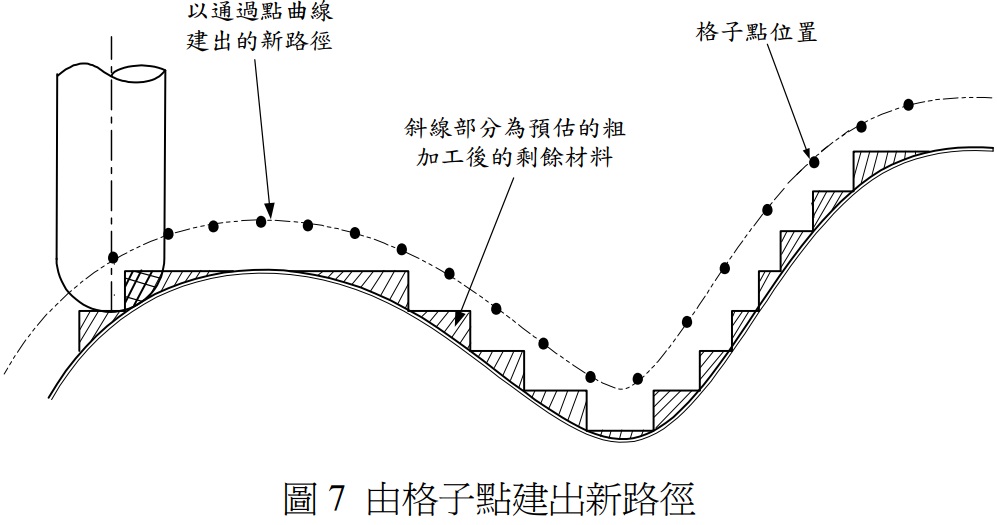
2-2 刀具路徑之步進長度
NC 加工中,刀具大部份是以直線方式作切削,若加工點數較少,則加工後的曲面會較粗糙,若加工點較多,則加工後工件的表面會較平滑,但相對所花在前置規劃的時間會比較久。所以為了在工件表面粗糙度及前置規劃時間取得平衡點,一般是尋找一組直線線段來逼近曲線並使得最大弦偏差量(Chordal deviation)小於所給定的加工裕度(Tolerance),如圖 8 所示。這種演算法 可以避免在曲面較平的地方會造成取點過多的現象,如圖 9 所示。求取最大弦偏差量的方法,依據曲面的外觀特徵可分為如下兩種狀況: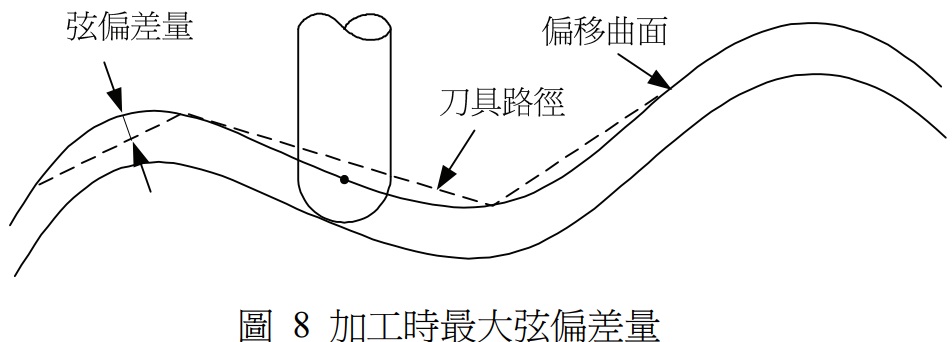
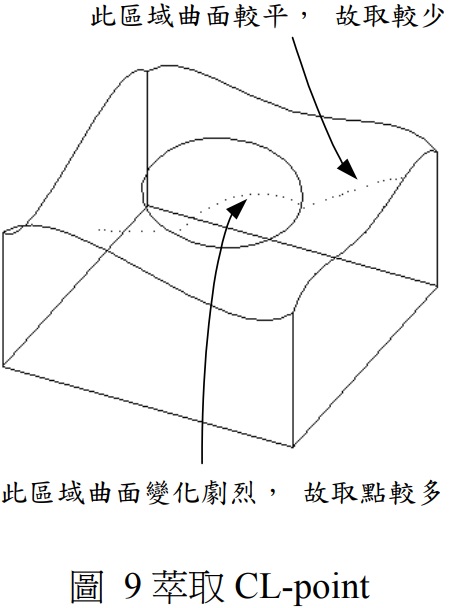
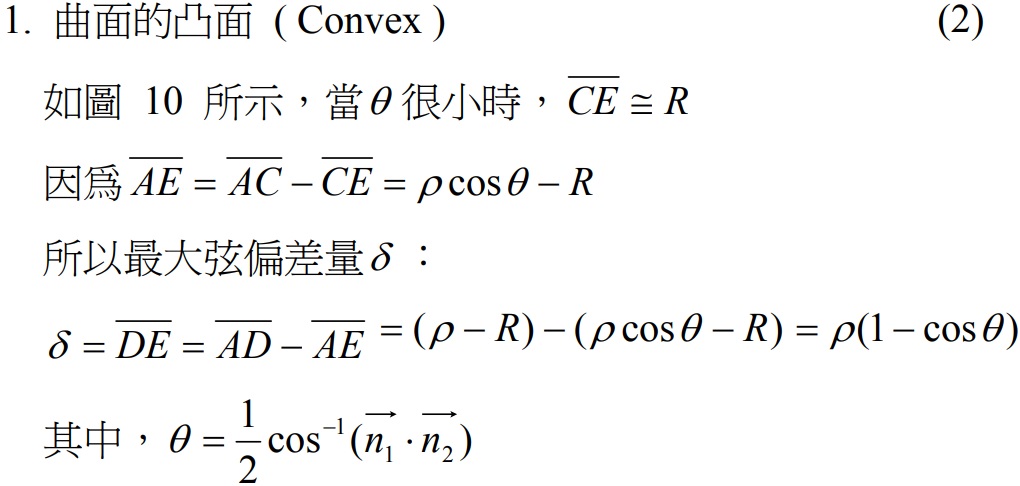
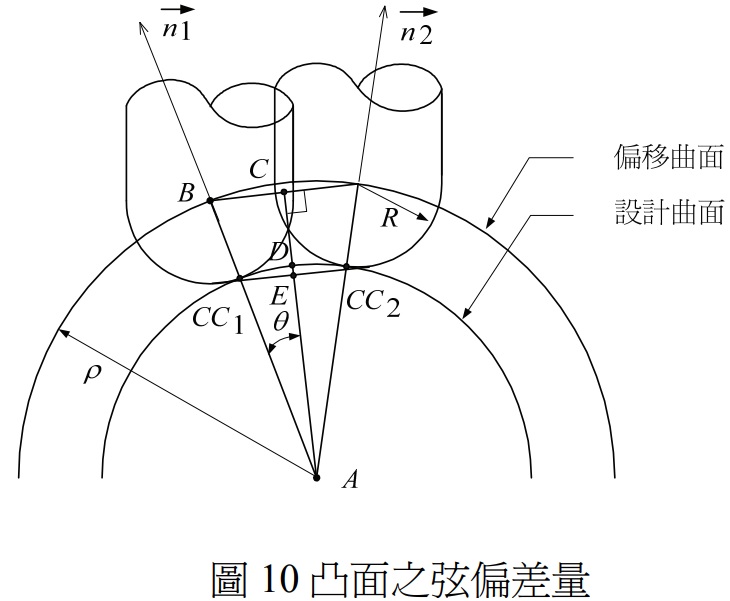
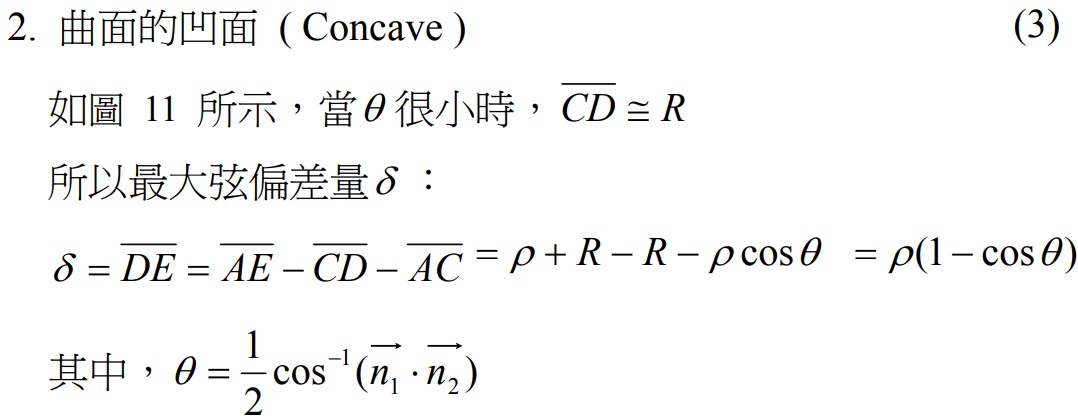
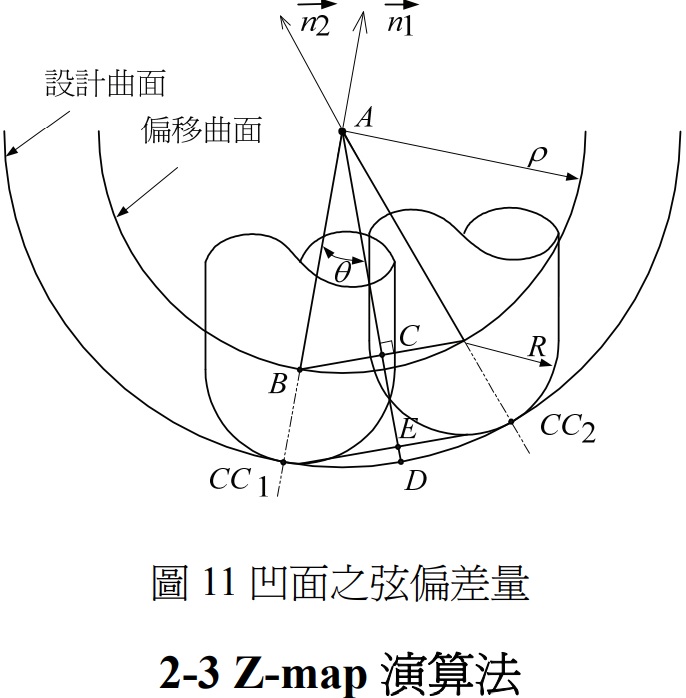
用較大的刀具間距值加工後的工件,在相鄰切削路徑之間會留下一道因切削不足所留下的胚料,稱之為扇型高度(Scallop),故此可藉由較小的刀具間距值之加工,我們可以得到較好的加工表面精度,如圖 12 所示。

本文加工路徑的刀具間距是以格子點為基礎來產生,但由於格子點的疏密直接影響加工誤差及電腦程式所需的記憶體大小,因此本文採用 Z-map 理論[8],產生精確的刀具間距,Z-map 可以解決記憶體問題,因為它是以區域規劃來分配記憶體,其詳細的步驟如下:
1. 在模型面上產生節點資料:
先在模型面上產生一群間格距離一樣的節點資料,如圖 13 及 圖 14 所示。
2. 求位移曲面上的節點:
將節點以逆向位移法,位移到位移曲面上,接下來即可從節點所含的資料,以 Z-map 來計算任意矩形範圍的格子點高度。
3. 以 Z-map 來萃取格子點座標:
以圖 15 為例,欲萃取第 N 列第 I 行至第 M 列第 J 行格子點高度之作法如下:
(a) 尋找格子點範圍邊界的位置:
(b) 檢查 I、M 是否落於點行或點列上,
若是,則把此點行或點列設成 I、M 格子點範圍邊 界的起始位置,若不是,則尋找小於此位置的前一個點行或點列為格子點範圍邊界的起始位置。
(c) 檢查 J、N 是否落於點行或點列上,
若是,則把此點行或點列設成 J、N 格子點範圍邊界的結束位置,若不是,則尋找大於此位置的後一個點行或點列為格子點範圍邊界的結束位置。
(d) 萃取格子點座標:
已知此格子點範圍的邊界後,配合已知的節點座標,可用下列公式找出此範圍內的所有格子點座標。格子點高度 = 節點高度 + 距離 × 斜率 (4) 其中:斜率 = [(格子點所在位置的前一節點高度) - (格子點所在位置的後一節點高 度)] / (兩節點的 XY 平面直線距離) 距離 = 格子數目 × 格子間隔距離 節點高度:格子點所在位置的前一節點的 Z 軸高度 4. 建出新路徑:將 Z-map 後的同一列的格子點以通過點曲線的方式,建出一條新路徑,如 圖 16 及圖 17 所示。
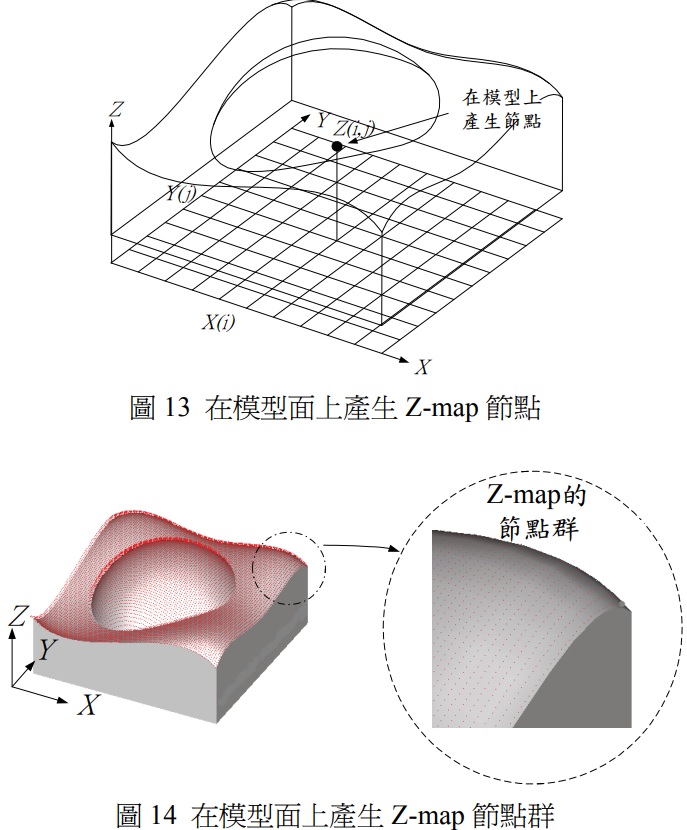
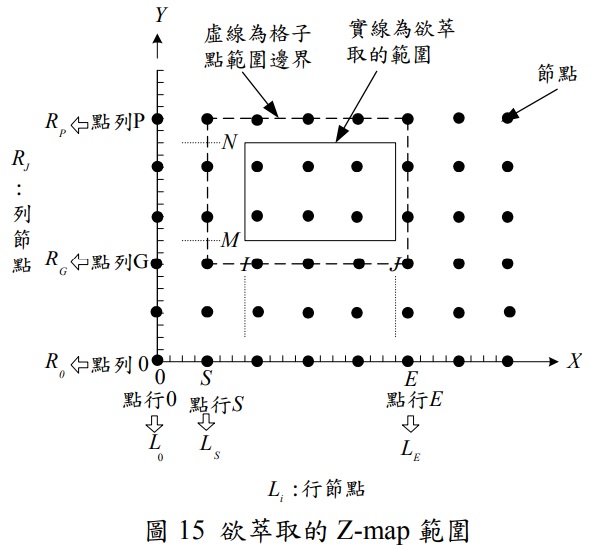
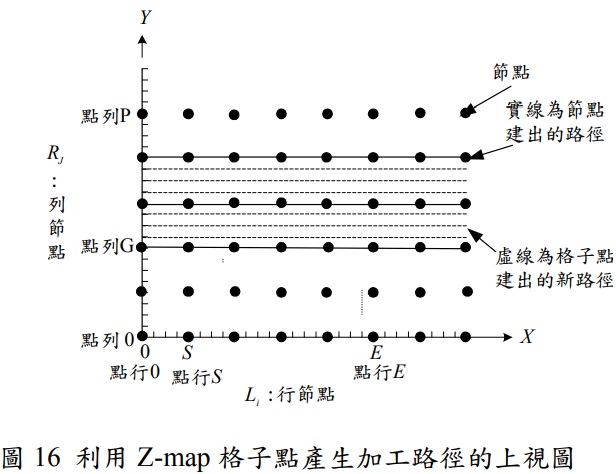
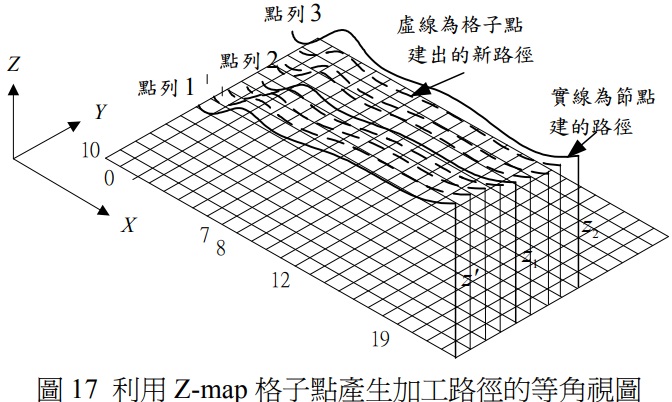
參、加工進給率調整原則
由切削力與進給率的關係可知,我們可以藉著調整進給率的數值,來維持適當的切削力量,且因切削力量與刀具移除材料體積成正比,所以當刀具移除材料體積較多及切削力量較大時,需調降進給率,切削力量便會降低,當刀具移除材料體積較少,且切削力較小時,則調高進給率,因此在加工的過程中刀具承受的負載不致太大。由於中加工與精加工的刀具路徑是由各 CL 點所連接成的,所以加工過程中各 CL 點間刀具所移除的體積及切削力量並不一定。在中加工時我們在調整進給率時,必須算出各 CL 點的體積,並利用切削力與進給率的關係式算出各 CL 點適當的進給率;在精加工中則利用每一點的曲率,配合等體積移除率的觀念,提出調整進給率的演算法則,最後把求得的進給率用 B-Spline 曲線做平滑化處理,以防止相鄰兩點間的進給率變化過大,而產生的機器的振動。
3-1 加工體積的計算
在計算加工進給率之前,我們必須先求出中加工中每一個 CL 點所移除的體積。傳統上,移除體積的計算都以刀具模型與加工胚料模型去做實體的體積布林運算,常常會因為布林運算後,所得到的移除體積幾何複雜,造成電腦計算上非常耗時。因而本論文以積分的概念,以點去代表體積,如圖 18 (a)所示。此方法沒有任何幾何關係,所以在計算時間上可比實體布林運算快上許多。首先我們以一個點代表一個 X、Y 平面的區域面積,如圖 18 (b)所示。因點能在 Z 軸向上下移動,所以一個點又能代表一個柱狀體積,如圖 18 (c)所示,而由無數柱狀體積堆積在一起,則成為一塊胚料,如圖 18 (d)所示,所以一塊胚料可以以無數的點來代表,而移除體積的計算推導過程如下: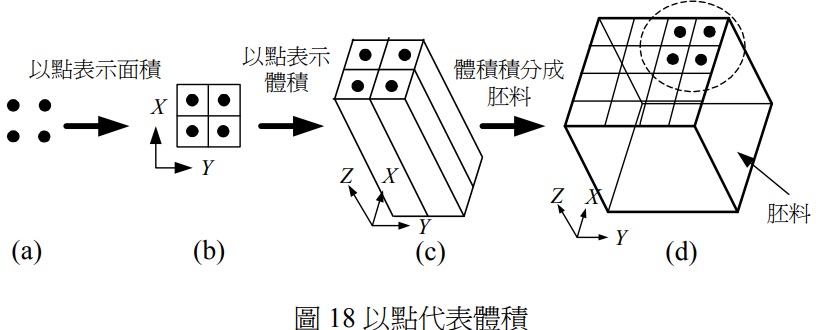
在一個 m ╳ n 的面積中,如圖 19 所示,分別每 s 與 u 間隔給予一個體積節點,所以一個體積節點代表的面積 A 可由下式求得:

加工時體積節點因刀具切削而下降的距離為 h 時,則此移除的體積 V 可由下式求得:

為了使移除體積的運算更加準確,本文配合前文所提過的 Z-map 的方法,把上述的體積節點,分別對 s 與 u 再以 m s 與 ns 等分一次,以求出附近的體積格子點,如圖 20 所示,此時每一個體積格子點所代表的面積 P 可由下式求得:

加工時體積格子點因刀具切削而下降的距離為 hi 時,則每一個體積格子點移除的體積 VS 可由下式求得:

經過 Z-map 的方法,計算所得的移除體積更接近實體的布林運算值。接著在各 CL 點上模擬一把刀具,把此 CL 點的總移除體積算出來,利用所求出的總移除體積依序代入關係式求出中加工路徑上各 CL 點的切削力,以下是我們求移除體積的詳細流程如下:
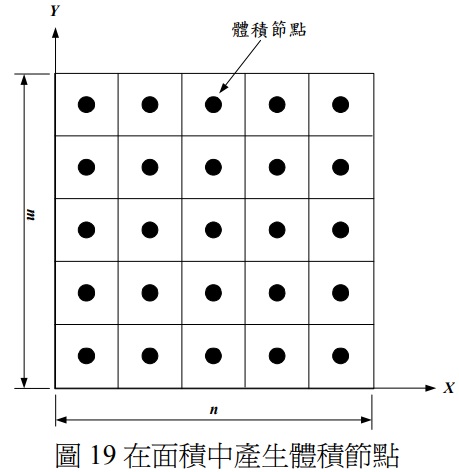
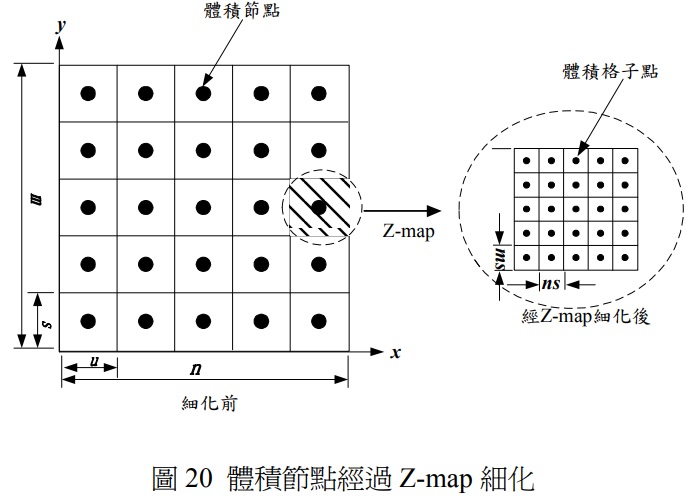
1. 首先計算粗加工後剩餘的胚料體積:
因本文的粗加工是採用等高加工,其刀具路徑有直線式與輪廓式兩種。先以直線式刀具路徑加工出大概外形,再利用輪廓式刀具路徑把邊緣的剩餘體積移除,粗加工後的體積,如圖 21 所示。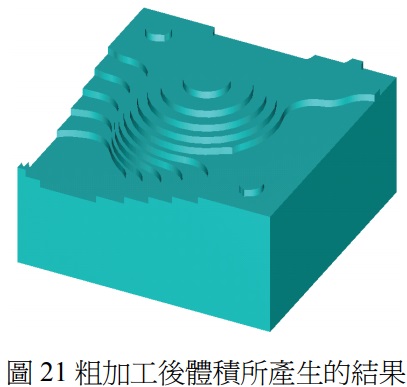
2. CL 點所移除的體積:
接著求 CL 點所移除的體積,如圖 22 所示,在路徑上的各 CL 點上皆模擬一把加工刀具的體積與上述經 Z-map 所得的體積格子點做交集的布林運算,再把這些體積格子點算出的移除體積加起來,就得到此 CL 點所移除的總體積,並將所有 CL 點所移除體積依序帶入進給率的計算公式,以下說明進給率計算公式。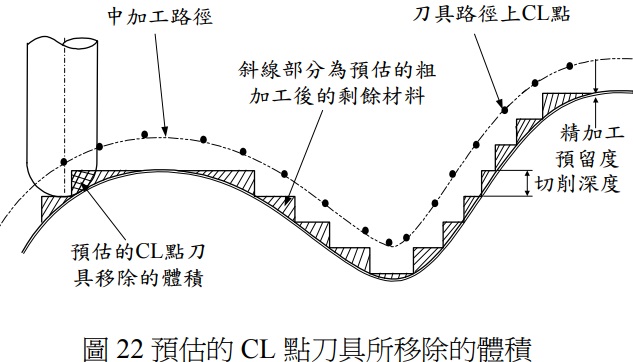
3-2 中加工進給率的計算原則
在切削力學中,切削力與刀具移除材料體積成正比。當刀具移除材料體積較多則切削力較大,我們可以調降進給率,使切削力降低。當刀具移除材料體積較少則切削力較小,我們可以調高進給率,使切削效率較佳。本論文在中加工進給率調整中,是先求出切削力,再以切削力的大小去調整適當的進給率,其中切削力 F 與切屑移除體積 V 及進給率 Vf的關係式,可由切削 力量定律推導出,其推導結果如下: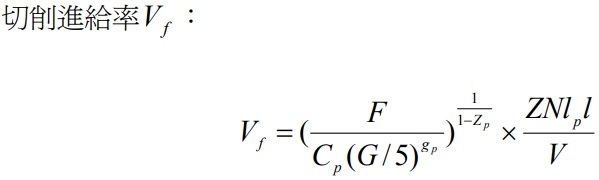
刀具每一齒切削材料所須的切削力 F :
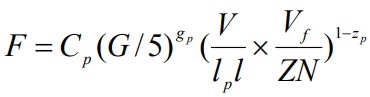
其中
C p :代表切削截面積 = 1mm 2 的切削力量。
G :代表切削形狀(Clip shape),即切削深度與進給的比值。
gp 、 zp :代表切削力量常數。
N :代表主軸轉速,單位為 rpm。
Z :代表刀具齒數。
lp :代表切削路徑長度,單位為 mm。
l :代表切屑長度,單位為 mm。
V :代表切屑移除體積,單位為 mm 3 。
推導出切削力與體積及進給率的關係式後,我們輸入一個固定的進給率,以此固定進給率配合刀具路徑中的各 CL 點所移除體積大小,代入(10)式,可算出在固定進給率下,每個 CL 點 所產生的切削力量,做為後續調整進給率之用。
調整進給率的基本構想是依照加工時所移除的體積及產生切削力量的不同而去改變進給率,使切削力量維持在一合理的範圍。當切削力量太大時,則調降此切削力量 F,將調降後的切削力量,代入(9)式中,可求得調整後的進給率 Vf,如此加工的過程中刀具所承受的負載不會過度負荷,而影響加工品質。
3-3 精加工進給率的計算原則
經過中加工後,所剩餘胚料都均勻的批覆於模型上,此時我們希望對於每一切削點的切削都為等體積的移除率,使得切削力不至於變化太大,產生切削不足或斷刀的現象。以下則列出不同形式之曲面,其精加工進給率之計算原則。
1. 直線路徑的進給率,如圖 23 所示。
刀具切削時,移除的體積 V:
其中 r :代表切削路徑距離參數。
δ:代表切削深度,單位為 mm。
s:代表刀具間隔距離,單位為 mm。
刀具切削時間 T (mim):
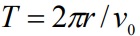
其中 v0:代表直線的切削速度,單位為 mm/min。
由(11)及(12)式,整理出刀具切削的體積移除率 MRR(Material removal rate):
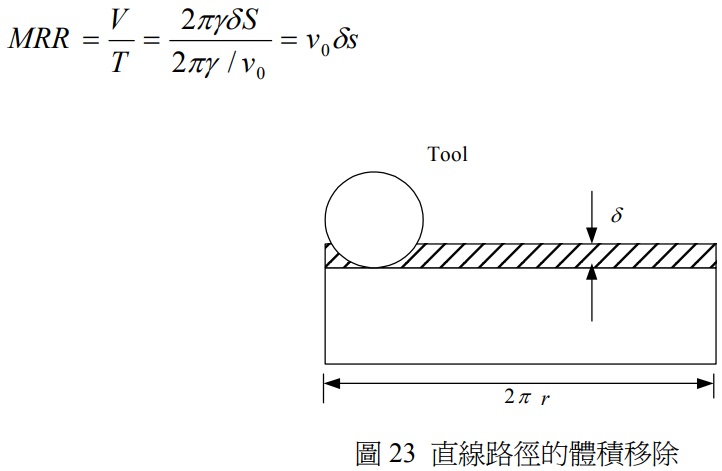
2. 切削曲面為凹面之進給率,如圖 24 所示。
其刀具切削的體積移除率 MRR(mm 3 / mim):
其中 V:移除的體積,單位為 mm 3 。
T:刀具切削時間,單位為 mim。
r :代表切削路徑的曲率半徑。
δ:代表切削深度,單位為 mm。
Rt:代表刀具半徑,單位為 mm。
s :代表刀具間隔距離,單位為 mm。
因此以等體積移除率的觀念,可推導出凹面的切削速度 vf (mm/min)為:
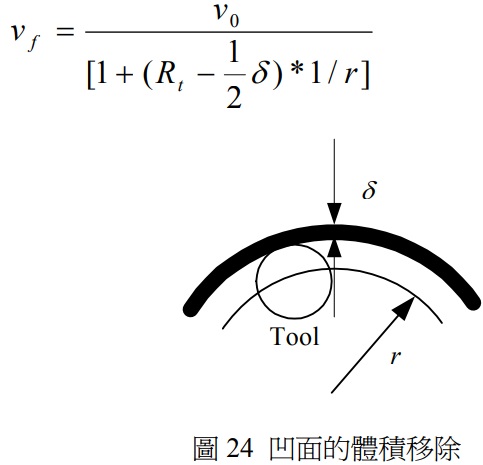
3. 切削曲面為凸面之進給率,如圖 25 所示。
其刀具切削的體積移除率 MRR:
其中 V:移除的體積
T:刀具切削時間
r :代表切削路徑的曲率半徑。
δ:代表切削深度,單位為 mm。
Rt:代表刀具半徑,單位為 mm。
s :代表刀具間隔距離,單位為 mm。
因此以等體積移除率的觀念,可推導出凸面的切削速度 vf (mm/min)為:
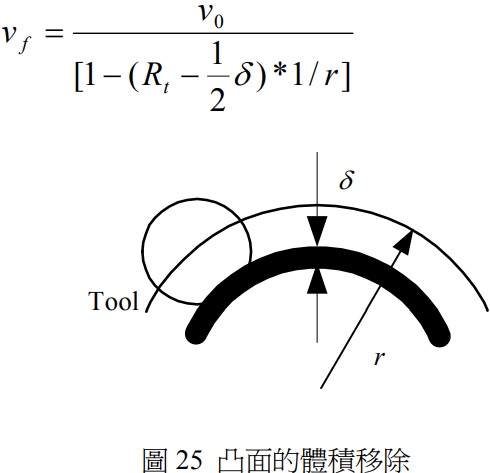
由(15)及(17)式,整理出刀具切削進給率 Vf:
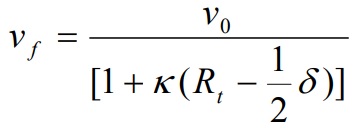
其中 Vf :代表刀具切削進給率,單位為 mm/min。
k :為曲率,當凹狀時k 為 1/r ,當凸狀時k 為 -1/r 。
3-4 進給率的平滑化
在中加工或精加工的進給率,有可能因切削模型的幾何形狀突然變化過大,造成相鄰兩點 的進給率變化過大,產生機器瞬間很大的加減速,造成振動現象,因而本文以 B-Spline 曲線來 平滑此進給率,因 B-Spline 曲線有以下幾個特性,適合去解決振動問題:1. 所設計的曲線會包含於控制多邊形的凸起外殼內,如圖 26 所示。
2. 具有局部控制曲線的特性,即改變一控制點僅會影響到此控制點鄰近的曲線外形,如圖 26 所示。
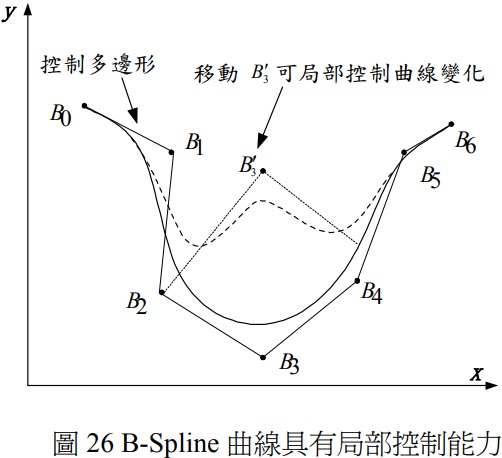
接下來我們將介紹本文如何以 B-Spline 曲線,使進給率達到平滑化的詳細步驟:
1. 求 B-Spline 曲線的控制點:以相鄰兩 CL 點投影在 X、Y 平面的直線距離為 B-Spline 曲線控制點的橫座標,以(9)及(18)式,求出的進給率為 B-Spline 曲線控制點的縱座標。
2. 產生 B-Spline 曲線:由上一步驟所得的控制點拉出一條 B-Spline 曲線,如圖 27 所示。
3. 計算經 B-Spline 曲線平滑化後的進給率:以控制點畫一條鉛垂線,此鉛垂線必與 B-Spline 曲線產生一交點,此交點的縱座標值,即為經 B-Spline 曲線平滑化後的進給率,如圖 27 所示。
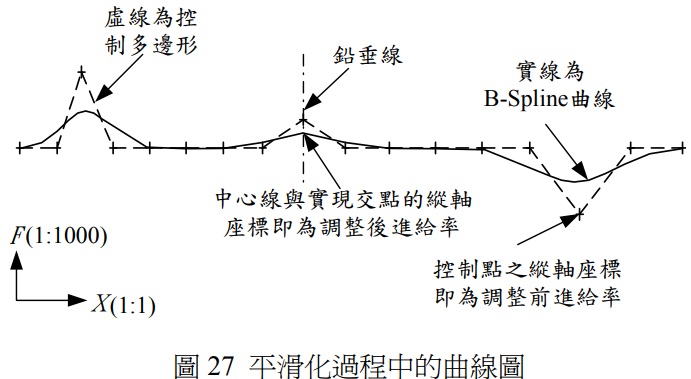
肆、系統功能之執行與實例驗證
本研究採用由 ACIS geometric kernel 為核心程式,產生 3D 實體模型的工件胚料,並以 Visual C++ 程式語言,透過體積布林運算求出各加工點的體積及加工點上的曲率,再利用前文所提出 的中加工及精加工調整進給率的演算法,分別求出調整後進給率的數值,得到進給率後,避免相鄰兩點間的進給率變化過大造成機器震動,將進給率以 B-Spline 曲線作一次平滑化。
4-1 系統之執行流程
本系統執行之詳細流程如下所示:1. 讀取工件胚料的實體模型。
2. 讀取粗加工 NC 加工碼,並將粗加工材料移除。
3. 顯示粗加工後的外形:運用讀入 NC 加工碼把體積移除,將粗加工刀具路徑範圍所產 生的體積與原本胚料做體積布林運算,可算出粗加工後的剩餘體積。 4. 設定中加工的加工參數:包括工件材質、刀具直徑、加工的公差、刀具間距、刀具的 刀刃數、進給率、主軸轉速、刀具安全高度及精加工預留度等。 5. 產生中加工的刀具路徑:以 Z-map 後所產生的格子點,以通過點曲線建出新的曲線, 此曲線即為刀具路徑,配合步進長度及刀具間距來求得適當的中加工 CL 點。
6. 調整中加工的進給率:由每一個 CL 點的刀具形狀去跟模型體積作布林運算,則可得 到每一 CL 點所對應的體積,及各 CL 點的距離,依順序代入調整進給率的演算法, 算出各 CL 點的切削力,依序將切削力代入調整進給率演算法中,去判斷各 CL 點所 適合的進給率,將同一條切削路徑上的進給率用 B-Spline 曲線作平滑化的修正,以防 切削進給率變化過大造成機器震動。
7. 產生中加工的 NC 加工碼。
8. 顯示中加工後的外形:中加工刀具路徑上,在各 CL 點均利用刀具外形的體積與粗加 工後的外形體積做布林運算,便可以算出中加工後的剩餘體積。
9. 產生精加工的刀具路徑:以 Z-map 後所產生的格子點,以通過點曲線建出新的曲線, 此曲線即為刀具路徑,配合步進長度及刀具間距來求得適當的精加工 CL 點。
10. 調整精加工的進給率:由每一個 CL 點找出此 CL 點位於此切削路徑上的曲率,將曲 率依序代入調整進幾率的演算法,算出各 CL 點的切削進給率,將同一條切削路徑上 的進給率用 B-Spline 曲線作平滑化的修正,以防切削進給率變化過大造成機器震動。
11. 產生精加工的 NC 加工碼。
在資料的輸入/輸出方面,先讀入模型工件的幾何資料,接著設定中加工及精加工的加工參 數,包括工件材質、刀具長度、刀具直徑、加工刀具路徑間隔、切削深度、進給率、主軸轉速、 刀具安全高度及加工預留度等,最後產生中加工刀具路徑與精加工刀具路徑,並自動調整適合 加工的進給率及產生 NC 加工碼。
4-2 實例驗證
圖 28 為單一曲面實體模型的加工範例,其操作步驟如下: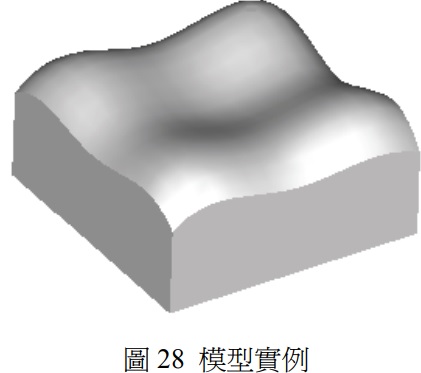
1. 設定加工材料材質及胚料尺寸,工件尺寸範圍為 X:50mm,Y:50mm,Z:30mm,對話框如圖 29 所示。
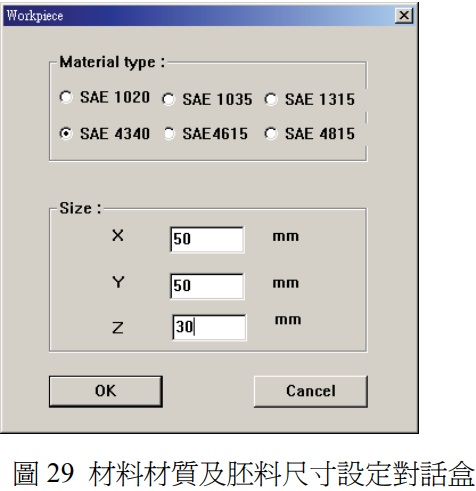
2. 設定中加工的參數,步進長度 0.01mm、刀刃齒數 2、精加工預留度 0.1mm、主軸轉 速 7000rpm、刀具直徑為 3mm、路徑間距 0.2mm、初始進給率 2500 mm/min,對話框如圖 30 所示。
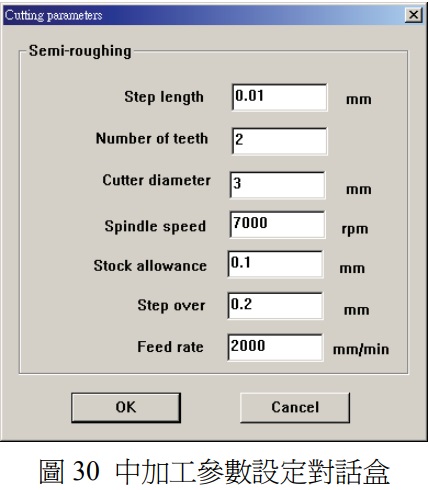
3. 設定精加工的參數,步進長度 0.01mm、主軸轉速 8000 rpm、刀具直徑為 2mm、初始進給率 2000 mm/min、路徑間距 0.1mm,對話框,如圖 31 所示。
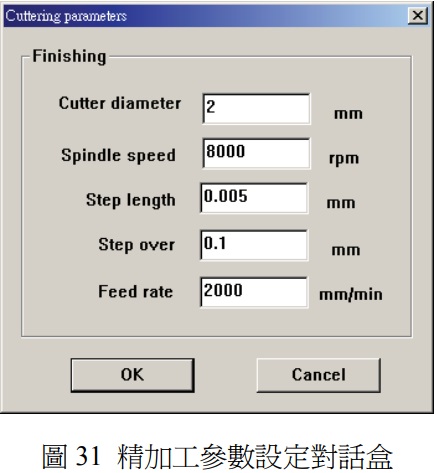
4. 最後產生中加工及精加工的 NC 加工碼,如圖 32 及圖 33 所示。
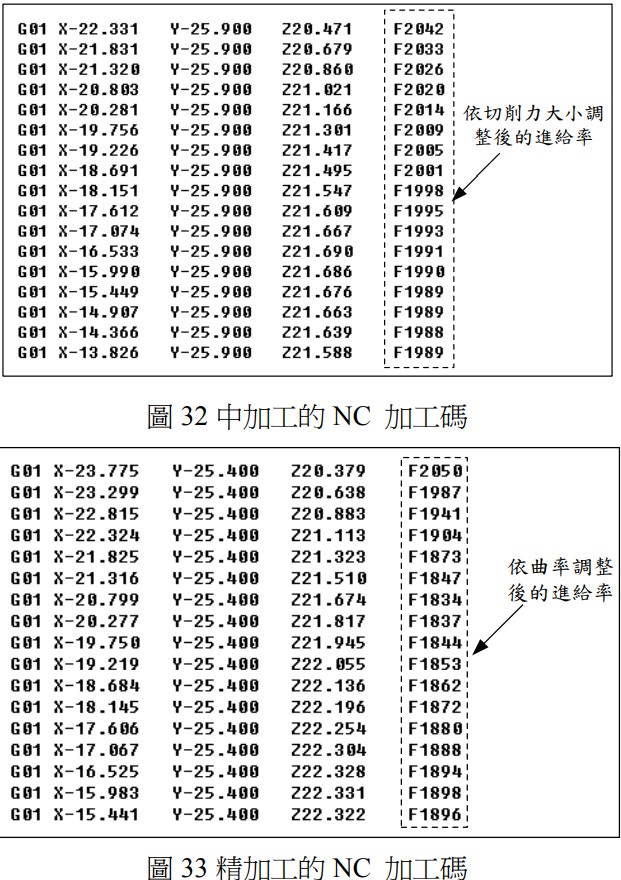
5. 實際加工後的模型,如圖 34 所示。
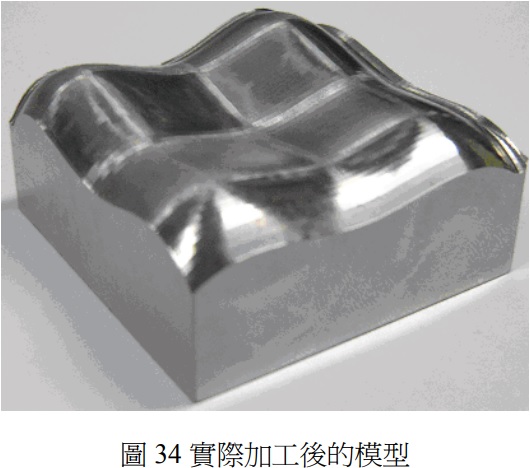
4-3 結果與討論
實驗中發現,中加工進給率調整演算法,特別適用於粗加工路徑中,無插補路徑功能的軟體上。當粗加工無插補路徑功能時,切削曲面斜率小的區域後,所留下的階梯胚料仍過大,若直接以中加工切削時,則刀具將會受到很大的切削力,因而產生振刀現象,目前一些高速加工軟體附有粗加工插補路徑功能,但其加工法仍無法完全使中加工切削力維持在一個合理範圍內,如以本文所提出的中加工進給率調整演算法,以真實切削體積的概念去算出進給率,則刀具所受的切削力會維持在一個合理範圍內,此對加工品質將會有所改善。
伍、結論
本研究提出可調整進給率的演算法來規劃 NC 精加工刀具路徑,並運用 ACIS geometric kernel 來驗證所提的理論。其特色如下:
1. 中加工與精加工時因為可以調整進給率,使刀具承受的負載不致於變化太大,也不會承受 劇烈的受力,所以刀具較一般不易損壞。
2. 加工中當切削刀具移除材料較少時,刀具的進給率可較快,所以可縮短加工時間。
3. 中加工自動調整進給率的方法,非常適合用於粗加工無補差路徑功能的中加工上。
4. 中加工時,採用積分的觀念配合 Z–map 理論,來計算加工體積,比一般使用實體體積布林 的算法快上許多。