優化粗加工 複雜的加工過程變得簡單化
2020-04-01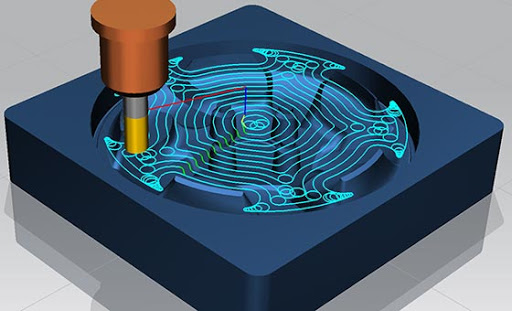
導讀
許多製造商仍依賴過時的機床速度和進給參數,或者堅持以最高速運行立銑刀。然而,他們放棄了相對較新的銑削策略的優勢--優化粗加工--這種策略具有顯著的優勢,包括延長銑刀壽命、改善工件表面光潔度和減少對零件加工的需求。遺憾的是,由於優化粗加工的相對新穎和復雜,許多製造商仍然錯過了優化粗加工的好處。優化粗加工是基於立銑刀的嚙合角及其對銑刀壽命、切屑厚度和工件質量的影響。為了達到真正的粗加工優化,製造商必須選擇他們的機床和軟件能夠在每個銑削路徑中維持的速度和進給量。由於建立銑刀路徑以正確切削工件特徵所涉及的複雜性,最新的CAM軟件在實現良好的結果中起著至關重要的作用。所有這些戰略考慮還取決於選擇合適的銑刀,並配備適當的刃數和塗層,以匹配手頭的銑削應用。如果不考慮其中一個或多個戰略因素,往往會導致銑削效果不佳。
接觸角和切屑厚度
立銑刀與工件的嚙合角或接觸角的變化會影響銑刀、工件和機床。為了延長銑刀壽命和生產出更好的零件,優化粗加工可以確保立銑刀與工件之間的嚙合角一致,同時保證可持續的速度和進給量。更大的嚙合角會增加銑刀和機床本身的負荷,並產生更多的摩擦和熱量,從而影響銑刀壽命和表面光潔度。太厚的切屑會損壞切削刃,而太薄的切屑會磨損切削刃,這兩種情況都會縮短銑刀壽命。當銑刀的切削刃進入和離開工件時,切屑的厚度會不斷變化。隨著嚙合角的增加,進給率必須下降,以確保最大切屑厚度不會達到降低銑刀壽命並最終磨損刀刃的程度。進給率和入口角越高,切屑越厚,反之亦然。
入口角也會影響切削力、銑刀壽命和排屑。
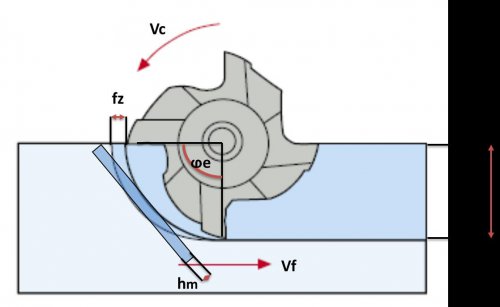
在90度的入口角下,切屑厚度等於進給率,切削力傳遞到機床主軸上,使切削深度超過較少的切削刃,使切削銑刀受力。較小的切入角可以使切削過程更加漸進,減少切削刃上的徑向力,從而提高了銑刀壽命,防止切削深度的切口缺口。較小的進刀角度可以將切削深度分散在較大的切削刃長度上,使切屑變薄,因此在45度的進刀角度下,切屑厚度下降到進刀率的70%,切削力在主軸和工件之間分擔。為了有效地去除金屬,進給率必須保證可工作的切屑厚度。在超合金、鈦和其他材料的工作硬化中,產生過薄切屑的條件也會產生一個影響區,然後銑刀再進入影響區。
平順的切削路徑,或切削參數的穩定性,降低了銑刀的負荷,顯著提高了銑刀的壽命。
在較淺的切削深度下,45度的入刀角度可以獲得精細的表面光潔度,限制切削出口處的毛刺的產生,並將切屑從工件上移開,防止切屑污染工件。然而,較高的軸向力會增加工件上的壓力,會使薄壁工件變形,破壞薄弱的夾具或產生振動。
轉速,進給和CAM軟體
可持續的速度和進給,以及一致的嚙合角度,可延長銑刀壽命,並製造出更好的零件。為了實現這些結果,優化的粗加工可以減少切削/跨度寬度,但增加切削深度,以更低的熱量獲得更高的金屬去除率。該策略需要高速的主軸、安全的夾具和機床剛性,使銑刀跳動量保持在0.0004 "或以下。優化的粗加工還需要足夠的CNC加工能力和先進的CAM軟件來處理程序生成和復雜的主軸/切削路徑上的運動所需的大量代碼。
許多車間不顧工件的設計而採用高轉速和高進給率,忽視了機床主軸的最高轉速不適合許多工作。高轉速和高進給率的組合使得優化的粗加工和最佳的切屑負荷幾乎無法維持,從而導致銑刀壽命縮短和零件報廢。在復雜的零件特徵上,這種高速的方法甚至迫使CNC控制裝置降低了機床的進給速度。
其他車間的傳統加工策略是基於銑刀的全直徑嚙合,而不是全長的凹槽,這在銑刀和工件之間形成了一個很大的接觸弧。這種接觸角的增加也會產生摩擦和熱量,從而影響銑刀壽命和表面光潔度。
平滑的切削路徑,無需快速改變方向或切削參數,可減少銑刀的負荷,顯著提高銑刀壽命。除了適當的速度和進給量,優化的粗加工還依賴於強大的、最新的CAM軟件,該軟件具有專門的算法,能夠生成優化的套管銑刀路徑。手工編碼根本無法完成這一任務,但最新的軟件可以從銑刀定義、最大跨度和刀口尺寸中生成優化的粗加工程序。
CAM軟件供應商已經開發出了精細的路徑算法,可以實時控製銑刀嚙合,對簡單和復雜輪廓進行高產、可靠的粗加工。為了縮短切削時間和提高金屬去除率,這些銑刀路徑通常將大的軸向切削深度與小的徑向切削深度、每齒高進給量和高切削速度相結合。
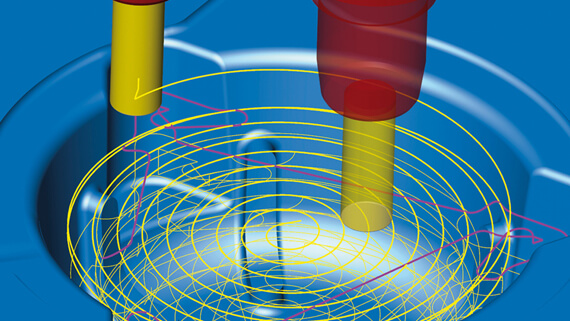
簡單和複雜的零件輪廓
目前的軟件策略依賴於兩種基本的粗銑刀路徑。一種是對凹面或凸面零件特徵應用恆定的進給率和接觸弧,通過不同的步進間隔來實現最大的金屬去除率。 WOTEK方法是改變進給速度和接觸弧度,但保持恆定的步距以產生一致的切屑厚度。在這種方法中,銑刀的嚙合角可以達到80度到140度之間,這取決於CAM軟件。這種高的嚙合角與優化的粗加工方法相反。立銑刀配置必須與零件的複雜程度相匹配,對於簡單的零件要減少凹槽,對於復雜的設計要增加凹槽。具有大切削深度、高進給率和寬徑向步距的高速加工可以在簡單的二維外輪廓上產生優異的效果。然而,這些速度和進給量可能並不適合在具有多層次三維特徵的複雜工件上產生高尺寸輪廓的小而精密的移動。
切削銑刀刃和鍍層
除了正確的CAM軟件和機床功能外,優化粗加工還需要選擇好的切削銑刀,通常是帶有外徑偏心和可變分度的立銑刀。較低的刃口數可以實現較高的跨距,而較高的刃口數可以實現更高的進給率。材料的具體進給速度和徑向跳動量決定了刃口數,最優化的粗加工操作是使用5到9個刃口的銑刀。銑刀直徑應測量切削長度/切削深度的一半;超過這一點,軸向切削壓力會導致銑刀偏移,妨礙良好的切屑形成。深度軸向切削需要使用斷屑器,缺口切削刃可以防止切屑纏繞在銑刀或零件特徵上,造成銑刀或零件特徵的損壞。
銑刀設計有賴於幾何形狀、材料和塗層的結合。為了提高銑刀的壽命和性能,現代切削銑刀採用氣相沉積塗層,通過昇華工藝,使材料直接從固態轉化為氣態,而不發生液化。這些塗層通常由鈦和氮氣與鋁、矽或其他元素組成。
為了獲得最佳的銑削效果,車間需要選擇與工件材料兼容的塗層銑刀。像WOTEK End mills這樣的響應式切削銑刀供應商將直接與個人客戶合作,以確保正確選擇銑刀。
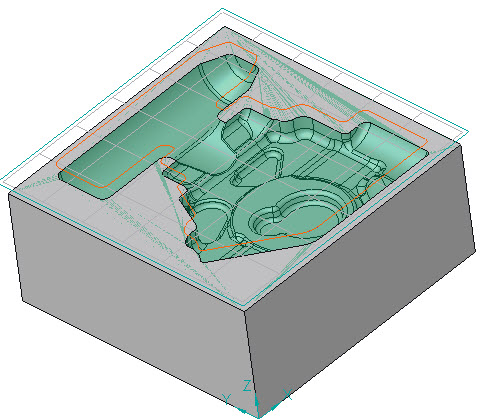
6個常見的優化粗加工錯誤方法
優化粗加工比傳統的方法快三到四倍,並使切削銑刀在鈦合金中的使用壽命長達八小時,而不是只有30分鐘。具有直棱柱狀壁的零件設計,需要較長的軸向切削深度,並且可以嚙合銑刀上的所有凹槽,是優化粗加工的理想選擇。在這些情況下,該策略優化了通常具有挑戰性的邊角特徵,並在超合金和各種不銹鋼中實現了高金屬去除率。
然而,為了避免錯誤和不完美的結果,對於不屬於最佳參數範圍的應用,車間應該跳過優化粗加工。例如,在復雜的三維模具型腔中,優化的粗加工可能會產生台階式表面,需要大量的半精加工。在這種情況下,高進給粗加工會產生更好的效果。
1.過大的跨距
隨著凹槽數量的增加,必須減小跨距尺寸,以保持在較高的進給速度下適當的切屑形成和表面光潔度。如果跨距過大,金屬去除量大,銑削會產生更多的熱量,迫使進給率降低。減小跨距尺寸可以提高切削速度,在去除相同數量的材料時,需要更多的工序,但由於進給率的提高,金屬去除率會更高。
2.劣質的刀桿
優化的粗加工需要高精度的刀架,其規格與硬銑床的規格類似,包括銑刀跳動量低於0.0004"。如果沒有精密的夾具,在優化粗加工的高進給率下,銑削會產生不理想的振動。大多數收縮式夾頭、銑削卡盤、高精度夾頭和精選的立銑刀架都能滿足優化粗加工的精度標準。銑刀、夾頭和環境維護都起著至關重要的作用,因為髒的夾頭孔、環境溫度變化或不穩定的機床基礎會縮短銑刀壽命。
3. 過時的銑床
快速的主軸和機床剛性有助於提供良好的優化粗加工性能。主軸必須產生足夠的轉速,以支持高進給率,而從主軸軸承到滾珠絲槓的機床剛性必須最大限度地減少振動,以實現平滑切削、穩定的銑刀壽命和卓越的零件質量。機床還需要在較新的機床上發現先進的預知能力和處理系統,以及在WOTEK中處理數千行代碼的能力。
4. 程式設計不良
手動編程和為高速側銑設計的軟件無法處理優化粗加工的苛刻機床動作。同樣,僅為複雜的三維高速銑削設計的軟件也可能無法在狹小的邊角處保持連續的嚙合。為了獲得成功,該工藝需要真正適應該工藝的軟件,而不是妥協。
5. 銑削深度不當
切削深度在優化粗加工中起著至關重要的作用,在2xD和銑刀的整個刃口長度下,一次通過的效果最好。較淺的徑向跨度使切削深度更深,而較大的跨度值會產生更多的熱量,需要較淺的切削深度才能達到相同的金屬去除率。大於3xD的切削深度會產生超過銑刀能力的切削壓力,並造成偏移。斷屑器可以將徑向切削壓力降到最低,以減少偏轉的可能性,並協助控制切屑。
6. 不適合的加工參數
機床軟件包含了速度和進給量的默認值,但這些概括性的參數並不能預測任何特定切削銑刀的正確參數。相反,工廠應該向他們的銑刀供應商尋求從細緻的研究和多年的第一手經驗中得出的推薦參數。像WOTEK工具公司這樣的銑刀製造商會針對他們的個性化銑刀設計和特定材料組優化切削數據。此外,他們可以根據客戶的個性化加工方案,對這些參數進行修改建議。
優化粗加工:提高銑刀壽命和工件質量的策略
優化的粗加工在適用的零件和特徵上提供了高效的效果,包括具有長軸向切削深度的凹槽、具有挑戰性的邊角和直壁。這種策略可以顯著改善零件週期時間、表面光潔度、銑刀壽命和機床使用率。花時間了解優化粗加工的車間,可以提高生產率、效率和利潤率,而這些零件都是採用這種策略的最佳選擇。為了達到最佳的效果,車間應利用銑刀供應商的專業知識來調整他們對個別工作的方法。 WOTEK工具公司提供深入的建議,幫助客戶選擇和使用其工具。
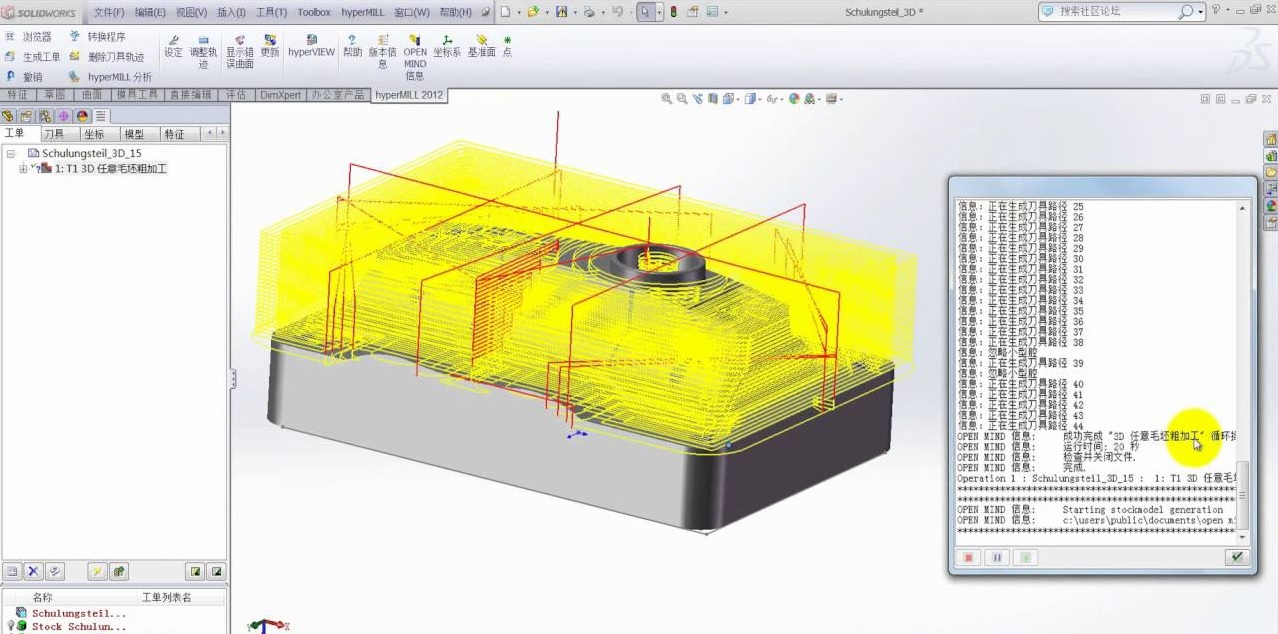