Study on the cutting parameters of SCM415, cycloid cutting & machining material, by Taguchi method
2020-04-15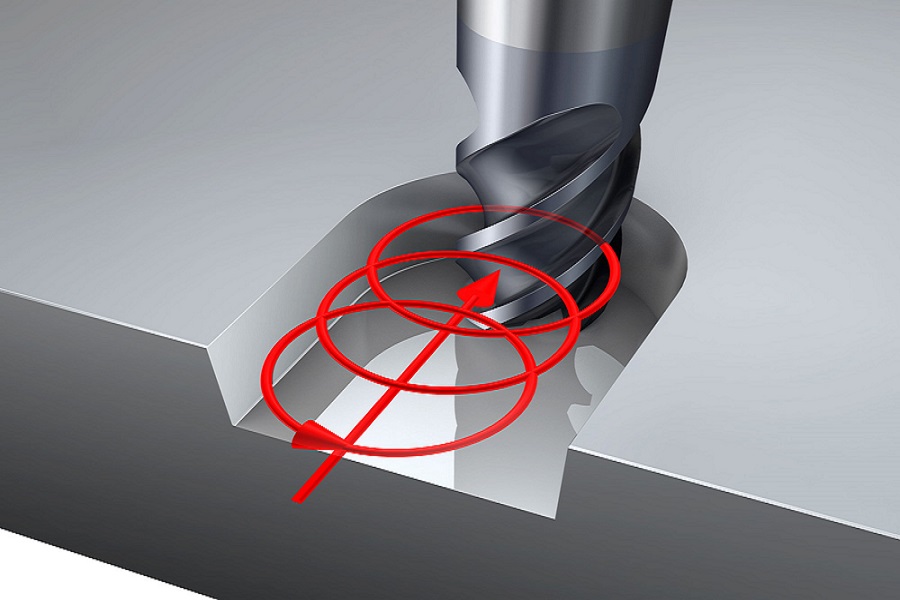
1. Preamble
With the booming development of CNC tools and automatic machines, the related components need to keep up with the process and accuracy. The parts and materials must have high abrasion resistance and high tensile strength, and the main transmission components are ball guide screw set and linear rail set, etc. These two components require a lot of machining. However, in order to reduce the cost of tungsten end mills, the cutting parameters are bound to be lowered and the machining time is increased, this study is to effectively shorten the machining time through the oscillating cutting path and to achieve the best cutting parameters and life of carbide end mills.
SCM415 is a low-carbon Cr-Mo steel in the Japanese JIS specification and AISI specification 4118 with excellent tensile strength. The material contains chromium and molybdenum because of its high hardening energy and its high resistance to tempering softening with less tempering brittleness. In metal cutting operations where the tempering temperature of CrMo steel is higher than that of CrMo steel of the same tensile strength, the question of how to increase the life of the end mill for milling tungsten steel before the application of carburizing heat is an important issue in existing metal cutting operations.
SCM415 is a low-carbon alloyed CrMo steel with good tensile strength and good toughness and elongation compared to pure CrMo or medium-carbon steel, so, it is suitable to be made into screw, bolt, crank shaft and other parts. Since the material is tougher, but the carbon content is only 0.15%, the BUE phenomenon will be generated during the cutting process, which will reduce the life of carbide end mills. How to use the Taguchi method to adjust the cutting parameters of carbide end mills and efficient machining is the focus of this study.
2. Research methodology
In this study, a CNC machining center was used to mill a rectangular cross-sectional square bar of SCM415H material with a two flute carbide end mill of 6mm diameter, using EDGECAM 2015 version to calculate the program path, Fig. 2-2 is an experimental material processing diagram, the two grooves are cut by cycloid cutting path, and the relationship between spindle load, carbide end mills life, chip removal rate, etc. affected by the change of four combination conditions such as rotation speed, feed, depth of cut, and cutting width in material milling processing is explored.
CNC machining center machine for milling Cr-Mo steel bar before the experiment, for cutting Cr-Mo steel bar to propose the experimental plan, and according to the experimental plan, planning the experimental step flow as shown in Figure 2-1, first of all, select the carbide end mills material, and set the spindle speed, feed rate per cutting edge, depth of cut, cutting width and other four cutting parameters, measurement of the abdominal wear of the tool after actual cutting and analysis by the Taguchi method to obtain the best cutting conditions, then the cutting process is carried out to optimize the parameters of the cutting tungsten end mills and to compare the effect of conventional groove milling and cycloid milling on the cutting results.
The Taniguchi method design uses four factors, three horizontal research and analysis, respectively, for the same material in the rotation speed, feed per flute, single cutting depth, cutting width and other four factors, the design of the parameters of the conditions is based on the processing parameters proposed to be used in the industry of the carbide end mills with the basis of the cutting theory of cycloid milling for the limit machining experiment to obtain the cutting parameters of cycloid milling for data design, the horizontal preparation of the cutting conditions as shown in Table 2-1, according to the Taniguchi method experimental straight table three horizontal straight table ??9(34) as Table 2-2 experimental planning configuration table.
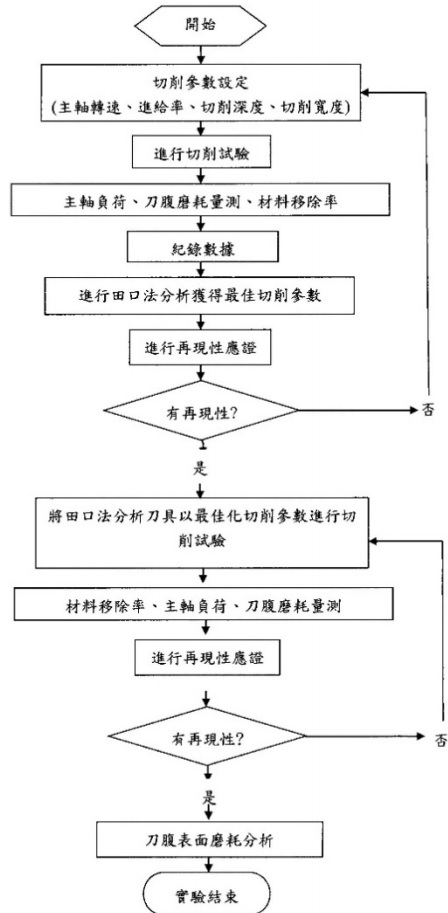
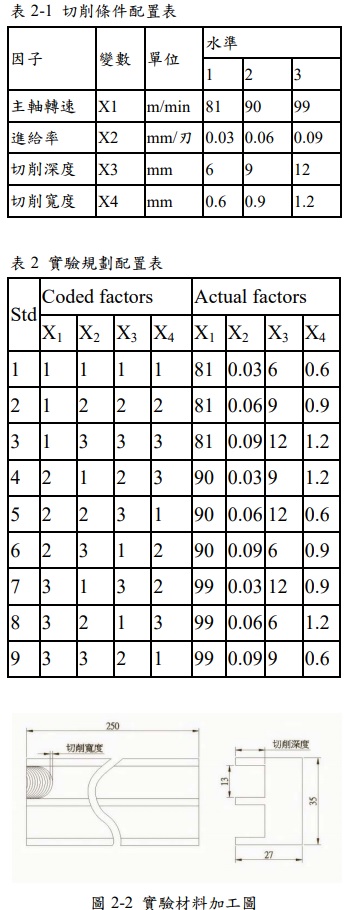
3. Research objectives
The most important cost of metal cutting is the cutting time and the life of the carbide end mill, cutting time is the material removal rate is the desired value, while the carbide end mill life is the curve and the carbide end mill wear speed analysis, this experiment will simplify the carbide end mills and the work pieces, mainly to make the most effective carbide end mills life improvement and shorten the cutting time by comparing the same cutting data with conventional machining, in order to achieve the goal of reducing production costs.
3.1 Cutting abdominal abrasion
Cutting tools abdominal wear is the phenomenon of gradual wear of carbide end mill when the cutting abdominal is in contact with the cutting surface of the workpiece, so the cutting area of the carbide end mill is in front of the cutting edge of the carbide end mill, in particular, discontinuous chips are formed by cutting workpieces, such as milling, because the chips often interfere between the carbide end mills and the machining cutting surface, which may cause greater friction and cutting heat to form the cutting tools abdominal wear, and also because the cutting tools abdominal wear will cause the cutting edge to deform and the gap angle to decrease, resulting in faster wear, which may cause the cutting carbide end mills to chip or even fracture. In this study, abrasion is defined as the abrasion of the cutting tools abdominal when the cutting tools abdominal reaches 0.1mm of abrasion width through the cutting test material. Dr. Taylor derived the correlation equation from the cutting data experiment.V?? = ?? (1)
Where V is the cutting speed, T is the time spent on wear (in minutes), ? is the index (the cutting conditions for the carbide cutter and workpiece material), C is the constant, different materials and cutting conditions will have different values of C and n. The value of C is the cutting speed of the carbide end mill within 1 minute of its life. We know that the faster the cutting speed, the faster the wear level.
3.2 Material removal rate (MRR)
The material removal rate is the volume of cutting material removed per unit of time when the carbide end mill is rotating at N. Therefore, the formula for material removal rate per revolution isMRR = π?avg dfN=dfN (2)
Where ?avg is the average diameter of the carbide end mills, ? the depth of cut, ? the feed rate, ? the speed of rotation, and ? the tangent speed. The actual material removal rate is obtained by multiplying the length of machining by the rectangular area, and the material removal rate in the machining data is mainly expected to be large, the larger the material removal rate, the higher the machining efficiency and shorter the cutting time, which is one of the important indicators of material cutting.
4. Experimental results and discussion
4.1 Experimental results
In this study, the SCM415 Cr-Mo steel square bars were milled with a WOTEK diameter 6mm two flute carbide end mill. Under four different cutting conditions, such as spindle speed, feed rate, cutting depth and cutting width, the standard values are brought into the Taguchi method planning table, and nine sets of values specified in the experimental planning and configuration table are used to conduct experiments, analyze and measure the wear of carbide end mills and material removal rate respectively, analyze the data by Taguchi method, and study and explore the results according to the appearance of the material cut down as follows: According to Table 2-2, set up the experimental data, conduct nine experiments, use the vertex 220 tool microscope to measure and analyze the cutter abdominal wear of the completed end mills, and obtain the relevant data as Table 4-1.The signal-to-noise ratio (S/N) of carbide end mills wear was obtained by Minitab analysis after nine experiments designed by the Taguchi method, as shown in Table 4-2.
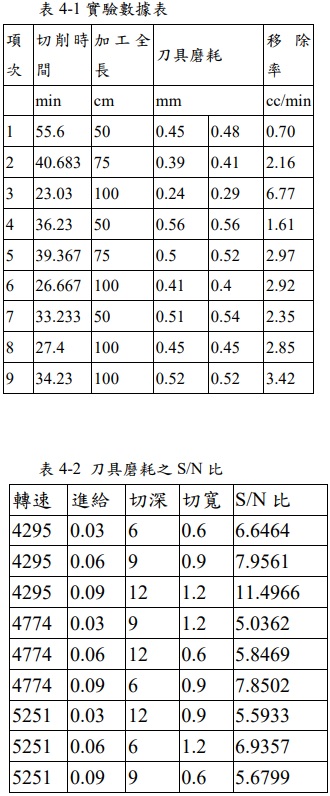
The S/N ratio of carbide end mills wear shows the best S/N ratio of 0.09mm/flute feed at 4295rpm, cut depth 12mm and cut width 1.2mm, while the S/N ratio response of carbide end mills wear among the various factors is most influenced by the rotational speed, which is consistent with the theoretical formula of Taylor's carbide end mills life curve, followed by the feed amount.
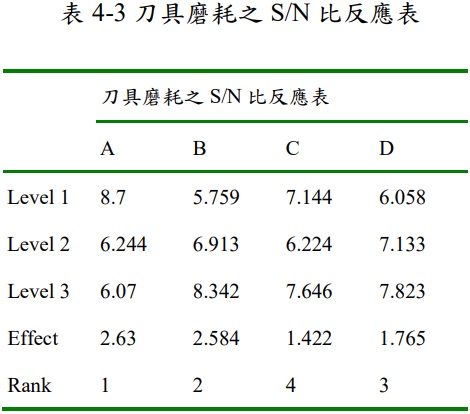
Figure 4-1 shows the S/N ratio main effect plot, indicating the mean value of the calculated S/N ratio for the optimal combination of cutting parameters with a small carbide end mills wear expectation, i.e., a speed of 4295RPM to 0.09mm/cutting depth 12mm cutting width 1.2mm.
Table 4-4 in the carbide end mills wear variation analysis table, to explore the four conditions that affect the cutting carbide end mills wear, the rotational speed influence accounted for 42%, followed by the feed rate accounted for 32.53%, and the first two accounted for nearly three quarters.
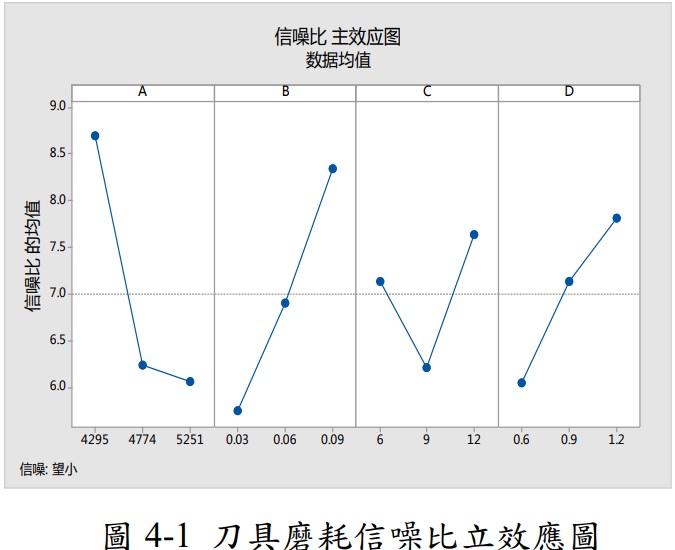
From the material removal rate analysis in Table 4-5, the S/N of the third set of data is the highest in the swing line processing, and the material removal rate is the desired value, the best parameters are 5152 rpm, 0.09mm/blade feed, 12mm cut depth and 1.2mm cut width, as analyzed in the S/N main effect plot against Figure 4-2.
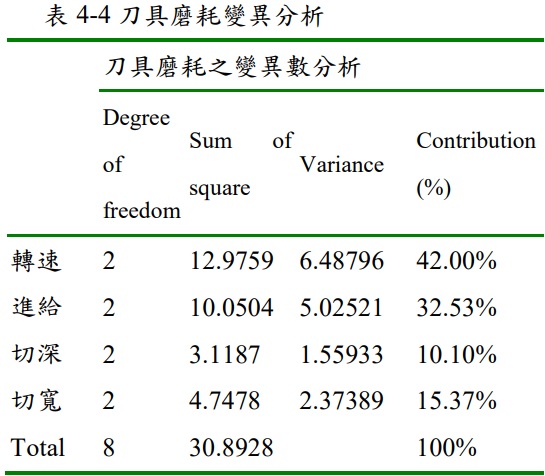
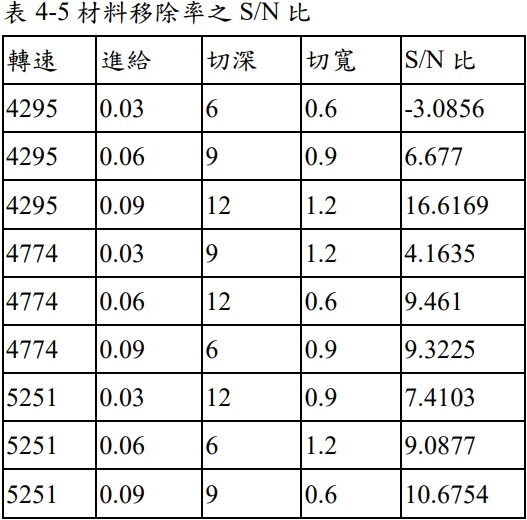
.jpg)
The material removal rate is related to the cutting area and feed, and the permissible feed rate parameter before the carbide end mills breaks is relatively larger per unit of time, but is not necessarily the best and lowest production cost consideration, so the A3B3C3D3 is the best combination parameter for a single object.
The material removal rate was found to be 5.55cc/min per unit time and the carbide end mills wear increased to 0.76mm in the confirmation experiment.
Table 4-7 Analysis of the variation of the material removal rate of the main influence of the condition of the feed accounted for 59.08%, the feed rate is the product of the speed, feed per edge and the number of edges, the depth of cutting is the secondary influence of the condition, and these two even accounted for 84.25%, the data show that the material processing time is short, should be combined in the feed and depth of cutting to obtain the best parameters.
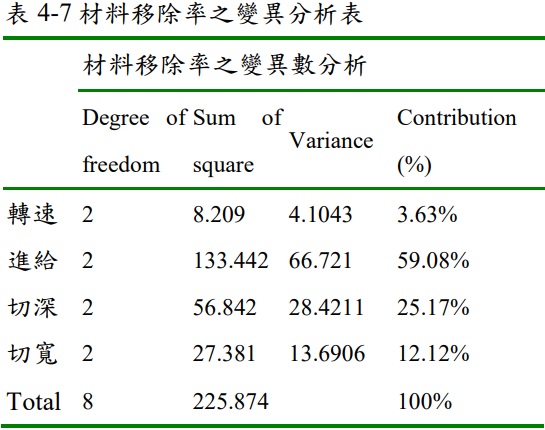
The difference in carbide end mills wear is seen in the tool microscope and compared with the results of the analysis, Figure 4-3 (a) shows the condition of the carbide end mills before machining, Figure 4-3 (b), (e), (h) all have the phenomenon of BUE, the main cause is the friction on the cutting surface of the workpiece due to the slow feed rate.
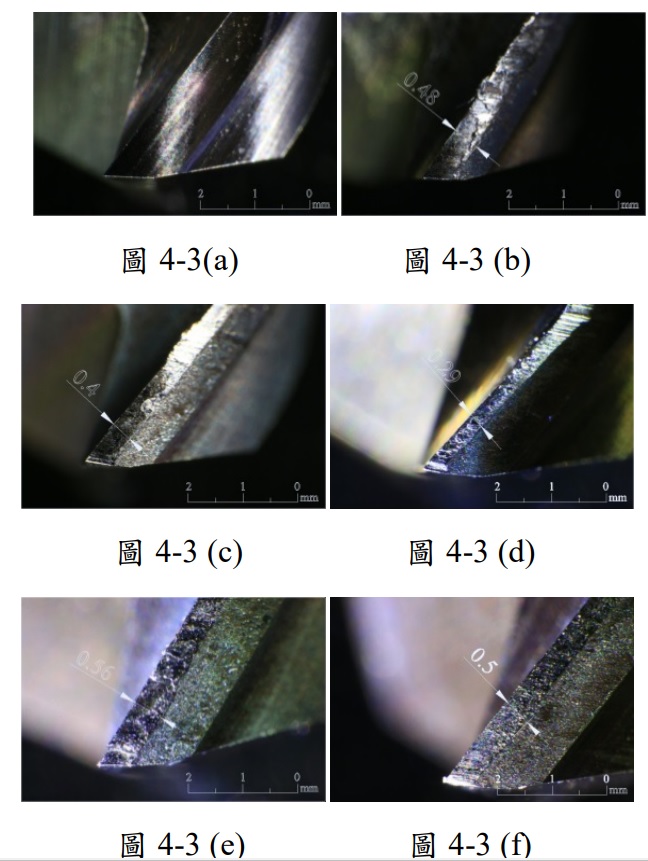
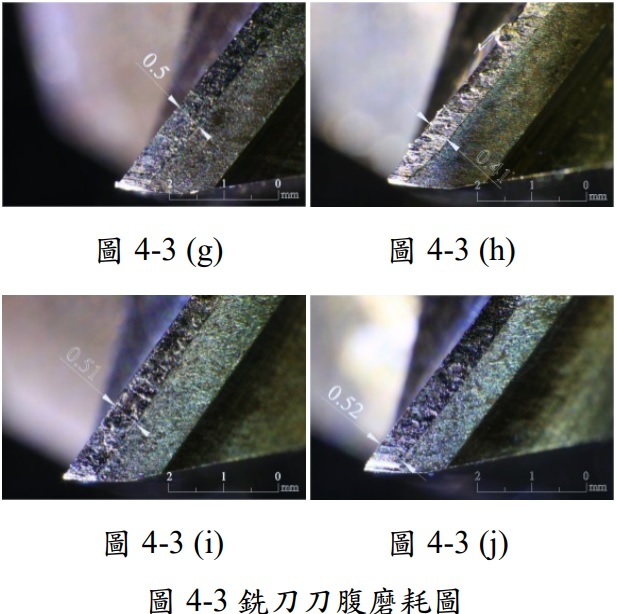
4.2 Discussion
Nine data analyses were made in this research laboratory, and the Taniguchi method was used to analyze the optimal data, after three failed data tests, the cutting parameters are constantly corrected by calculations, and the tested material tungsten carbide cutter is corrected again if the experimental data is incorrect. It also includes the question of measurement until the last test analyzes the optimized data and then does a complete confirmation of the optimized parameter experiment to complete this study of the experimental data.
5. Conclusion
CNC milling machine has been introduced to Taiwan for more than thirty years, only within the last ten years, because of the high labor and machining costs, in order to reduce the total cost of production, and then try to shorten the machining time, improve the quality and efficiency, the cycloid cutting and tools have the advantage of introduction, but due to the relative complexity of its programming and calculation, and the lack of domestic CAM software development, so it is always behind the advanced countries in Europe and America, the processing parameters of cycloid milling is also little research and development, now the cutting parameters completely stay on the traditional processing parameters, the processing time of the cycloid cutting can be shortened to 12 times as much, and also because the cutting heat during processing is only 5% of the traditional processing, can effectively increase the life of carbide end mills, under the current situation of a gradual shortage of raw materials, is a very effective energy saving method.
The optimisation of the cycloid cutting parameters studied in this study has verified that the cutting resistance of the cycloid cutting can be 15 times higher than that of the original data by using the programming method of cycloid machining for the same machining material, with the original recommended cutting speed of 930RPM and a feed of 0.03mm/edge.
According to this study, it is inferred that with the use of carbide end mills for roughing SCM415 material with cycloid cutting and milling, the carbide end mills can have a speed reference of 81M/min and a feed of 0.015 times the carbide end mill diameter per flute with a depth of cut up to 2 times the diameter and a width of cut of 0.2 times the diameter. This study also shows that it is not advisable to use too low a feed rate for cutting because of the grinding effect. The results of this experiment show that the main factor affecting the wear factor of carbide end mill is the speed, the best parameter for carbide end mill wear is 4295rpm, feed 0.09mm/flute, cutting depth 12mm, cutting width 1.2mm, the main factor affecting material removal is the feed, the best parameter is 5251rpm, feed 0.09mm/flute, cutting depth 12mm, cutting width 1.2mm.
The most effective mode of machining is the cycloid machining. The rapid development of Taiwan's industry and the shortening of delivery time, it has greatly influenced and helped Taiwan's component machining industry to go global and keep pace with the advanced countries in China and Europe and America in both quality and quantity.