Learn more about CNC vertical and CNC horizontal milling machines
2020-03-05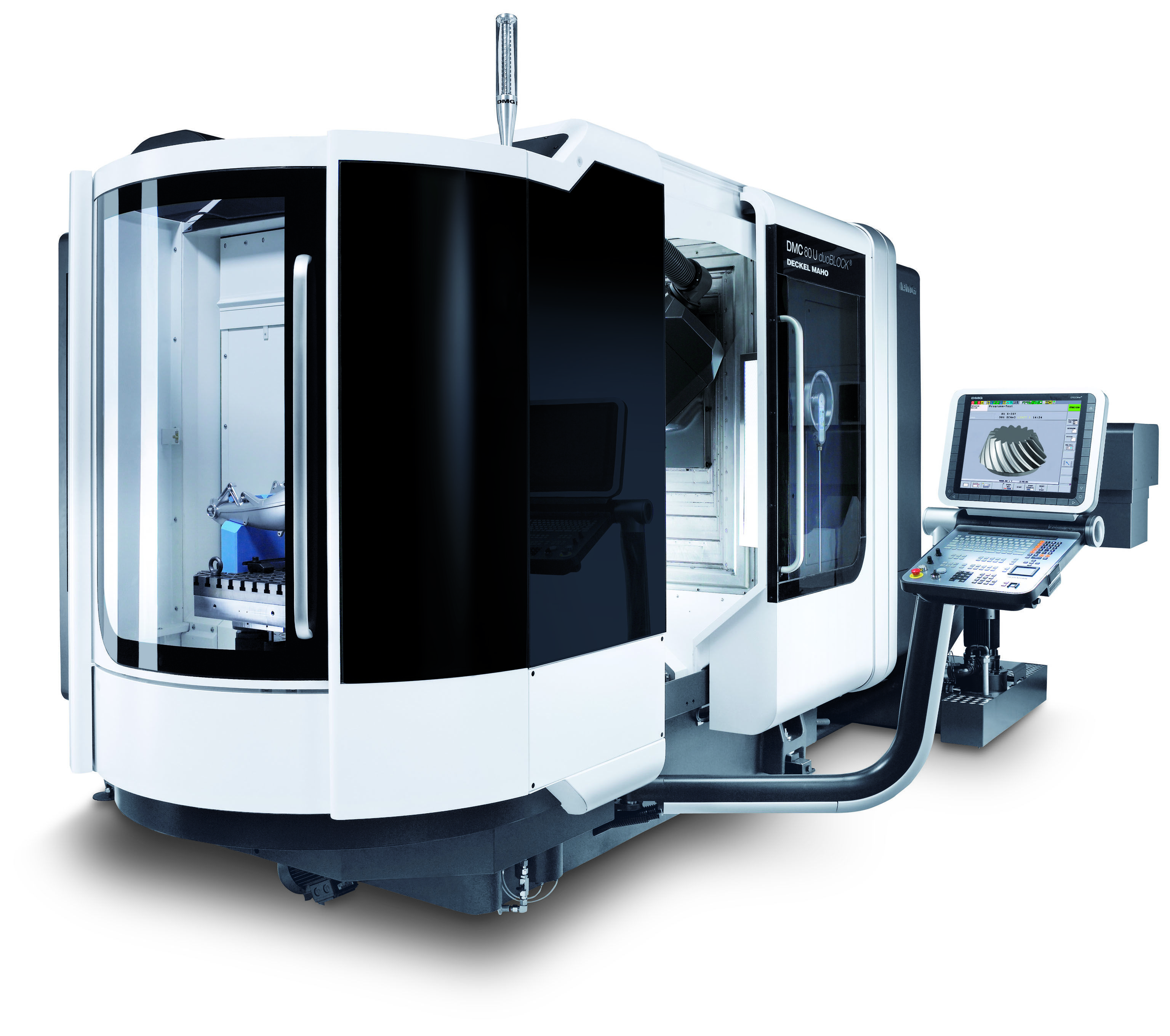
For CNC machines operators who are considering the use of milling machines, a basic configuration-related question that must be clarified is: choose vertical or horizontal milling? The answer depends on the nature of the business, especially the type and amount of work to be performed on the production line, as well as costs, staff capabilities, and the facility itself. Considering all these factors will help make informed decisions.
CNC Vertical milling machine
In vertical milling machines, the axis is oriented vertically. The end mills are fixed in the spindle and rotates around the axis. Usually, the same effect can be achieved by extending the spindle or raising or lowering the table, which can be used for cutting and milling. There are two types of vertical milling machines, bed milling machines and turret milling machines.
CNC Horizontal milling machine
The tool is mounted on the horizontal spindle of the table. Many horizontal milling machines also have a built-in turntable that allows milling at different angles; this is called a universal table. Although end mills and other types of tools used in vertical milling machines can be used in horizontal milling machines, horizontal milling machine spindles are also equipped with end mills, called side and face milling cutters, which have similar cross sections as circular saws, but usually wider and smaller in diameter. Because the mandrel can support the face milling cutters well, and the cross-sectional area of the face milling cutter is larger than that of the end milling cutter, heavy cutting can be performed, thereby increasing the material cutting rate very well.
Angular Juras, Fusion 360 CAM Product Manager, said: "Looking at the general usage across the industry, you will find that most of the machine tools installed are three-axis vertical milling machines. These machines are easy to install and provide technicians with access to the workbench. In addition, if you have a work piece or vice, loading and unloading is easy-you just place the part on the workbench and gravity will put it in place.
Juras states: "The spindle of a horizontal milling machine is horizontal, which means that the surface on which the work piece is mounted is vertical; therefore, the operator is more laborious when loading and unloading. But in addition to being easy or difficult to use, each configuration has its own advantages and disadvantages. "
Advantages and disadvantages of CNC milling machines
Horizontal milling machine has better chip removal rate because of its configuration characteristics, because the gravity can only make chips fall downward. This helps to improve surface finish and extend tool life.
Juras commented: "When machining parts with deep cavities or grooves, all chips generated during milling will fall to one side. If the same part is processed on a vertical milling machine, all chips will stay in place, which may be disadvantageous for tool life and chip flow cutting. " Horizontal machine tools also have a four-axis "monument fixture" function. Juras explained: "The spindle of a horizontal milling machine is oriented horizontally and the table is horizontal; however, it is designed for threaded mounting holes or keyways, and fixtures or bases can be mounted on it. This structure is called a ' monument fixture' '. The tablet-type fixture points in the vertical direction while showing the work piece in the other axis direction. "In this case, the work piece is perpendicular to the spindle. According to Juras, if someone has just set up a machines production, there is a 99% chance that they will start with a basic vertical milling machine because these machines:
• Easy to use
• Easy to get started
• Lower prices
"Usually, vertical milling machines are used in the production," said Juras. "Later, as workload increases, they can add horizontal milling machines if they are suitable for their accessories." He recalled his past experience operating a machine production. He said: "In the beginning, it took us 47 minutes to machining a part. We needed to perform 9 separate operations on a vertical milling machine. Eventually, I purchased a horizontal milling machine, and reduced 9 operations to 2. We finished the part in 22 minutes. "
Juras also talked about his research and development worked at an automaker that uses both vertical and horizontal milling machines, and explained how his work optimizes the configuration of milling machines: "We want to achieve rapid turnaround of components. For each component, we need to ask and answer a series of questions: how speed does it need to be? How many operations are needed to produce a part? What is the availability of the equipment? How many are needed? All these questions determine whether we place the parts on a vertical milling machine or horizontal Milling machines. Usually, during the development phase, it depends on the number of faces to be machined; but vertical milling machines are often easier to load and unload. Things are always good and bad. In the final analysis, everything depends on the clamping and positioning of the work piece. "
Two other factors also make it very attractive to start with a vertical milling machine: the size of the training and the space it takes up. In today's era, manufacturers are in urgent need of finding qualified technicians, and more technicians have experience with vertical milling machines, but scarce with horizontal milling machines. Whether a tool can be fully effective depends on the operator, so in addition to the higher cost of horizontal milling machines (usually three to four times that of vertical milling machines), owners must also consider that they have not used The personnel of such equipment provide the time and capital required for training.
In addition, especially in areas with high rents, smaller vertical milling machines are more advantageous. Juras said: "I have seen some small horizontal milling machines and large vertical milling machines, but that is an isolated phenomenon. Usually, vertical milling machines take up significantly less space than horizontal milling machines.
Final considerations for CNC milling machines
To reiterate the overall advantages of each milling machine configuration:
CNC Vertical milling machine
- Costs are significantly lower. The cost of a vertical milling machine is $ 80,000, while the cost of a horizontal milling machine ranges from $ 250,000 to $ 400,000. Therefore, it is not difficult for us to understand why the number of vertical milling machines purchased by production capacities is much larger than that of horizontal milling machines, and is growing at a rate of 4 times or more per year.
- Easy to use. Easier to see what is milling inside the vertical milling machine
- More mechanics are familiar with this technology
- Smaller size and smaller footprint
CNC Horizontal milling machine
- More complex parts can be produced with fewer operations; spindle uptime can be extended by reducing setup and positioning time for multiple operations
- Greater throughput. One horizontal milling machine can usually complete the workload equivalent to 3 or more vertical milling machines
- Improves chip evacuation, improved work pieces and longer tool life