Guide to machining Titanium
2020-01-06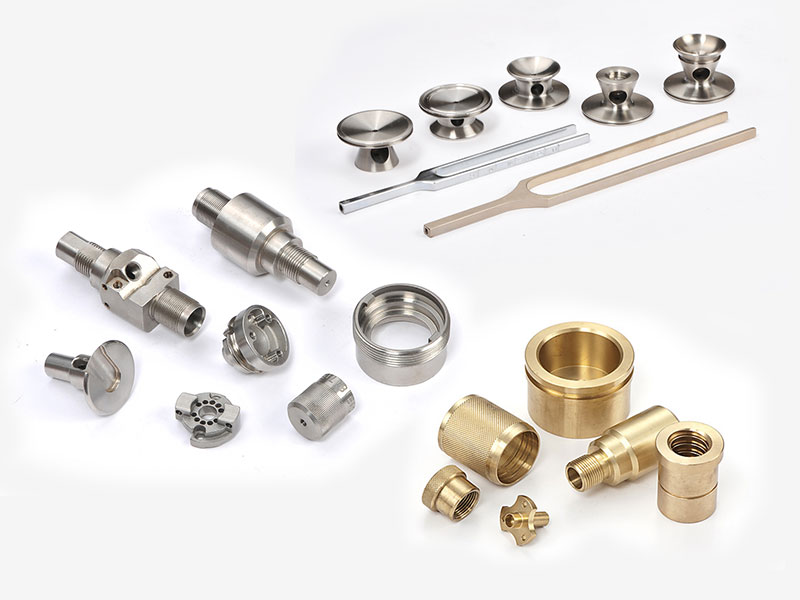
Titanium is widely used in a variety of applications due to its versatility and strength. It has a very high strength-to-weight ratio, weighs about half as much as copper and only slightly more than half of stainless steel. It is much less dense and has high heat and corrosion resistance. It even has several properties for biomedical compatibility, making it great for medical use. Applications within aerospace engineering, military and biomedical fields, among others, use titanium and titanium alloys for their strength and various properties.
Despite its advantages, titanium can be stressful to work with, for both the machine operator and their tools. But with the right approach, you can make the process of machining titanium much less painful.
MACHINING PROCESS FOR TITANIUM
Titanium can be a complicated metal to work with. All of those properties that make it ideal for intense applications make it formidable to work with. Its heat resistance and reactivity can damage your tools, and by extension, your workpiece, if you aren’t careful. You’ll need to consider every aspect of the process when working with titanium.
1. Cutting Tool
Your choice of cutting tool can have a significant impact on the job. As you’ll see, working with titanium involves a lot of high heat, so you’ll need a tool that can stand up to the heat and the hardness of titanium itself. A coated high-speed steel tool is probably your best bet. These tools are made of a combination of tungsten, carbon and vanadium and can maintain hardness up to 600℃. This type of tool can allow you to make deeper cuts and cause fewer shocks within the workpiece, creating less of an opportunity for chipped edges to occur.
2. Tool Coating
Tool coating is another significant way to make your cutting simpler. A coating helps your tool better deal with the high temperatures generated during titanium cutting. For example, a coating can make a carbide tool a reliable option. Zirconium(ZRN) is one coating option that is driven by heat. As the surface heats up, it forms a layer of aluminum oxide, which brings down heat transfer and chemical diffusion between the tool and the workpiece. This coating transfers heat to the chips as the tool generates them.
3. Stable Surface
The titanium also needs to be cut on a very stable surface. This metal can be prone to chattering, or heavy machine vibrations, because of its flexibility and the high forces involved with cutting it. While one option is to reduce power, this could be worse for your machine and the project. Increasing speeds can lead to fire risks with excessive heat. Too much heat can also cause strain hardening, which can make your cutting edges even stronger. This extra strength makes your tools work harder and degrade faster.
Some ways you can increase stability instead include using a larger core-diameter end mill and finding the shortest overhang between the spindle nose and the tooltip. You’ll also want to keep your titanium machining feeds and speeds consistent and keep your tool moving steadily. If it drags in a corner for too long, it can result in more chatter and heat, wearing down the tool.
4. Climb Milling
Climb milling is a useful strategy to keep your chips in check. In conventional milling, which is the traditional method, the chips created from your tool start thin and increase to larger widths. This thin-to-thick approach puts more heat into your piece and increases strain hardening. It also causes more rubbing, which can degrade your tool faster. By using climb milling, the chip width starts high and then decreases, increasing the likelihood of heat transfer to the chip instead of your workpiece. It also creates a cleaner shear and pulls chips behind the cutter, so they don’t get in the way of new cutting.