End mills coating
2020-01-02
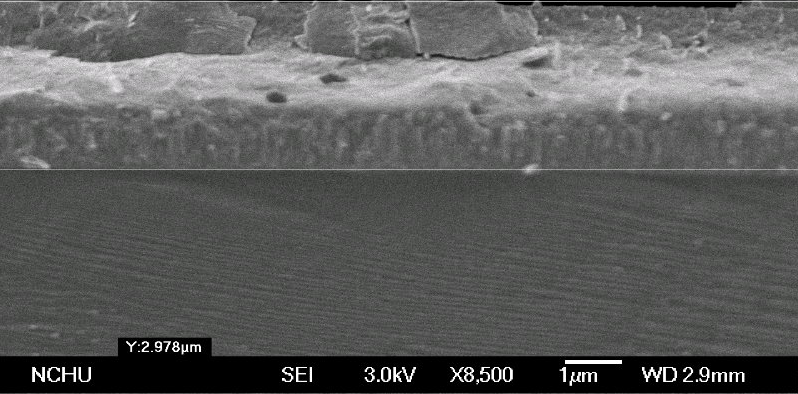
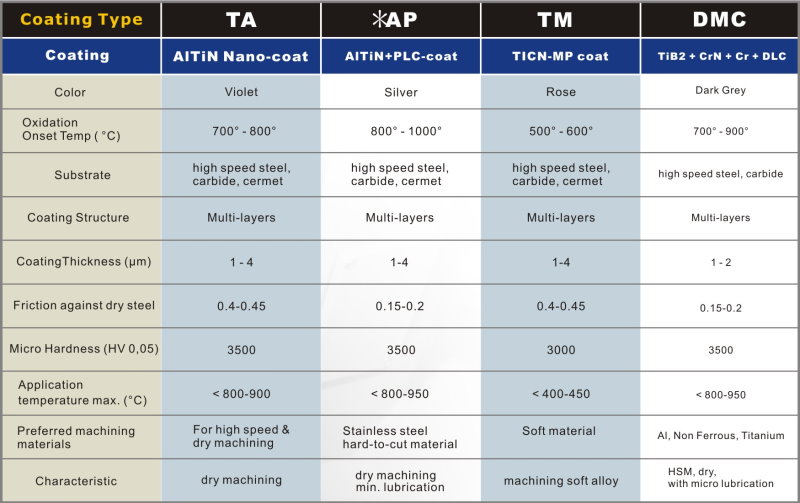
- Coating of Cutter
The coating delivers a variety of benefits to extend tool life, including : - Superior oxidation resistance
High speed machining is always high temperature machining. Coating protects the tool by acting as a thermal barrier. It provides unparalleled performance in high temperature machining.
Lubricity layer for chip removal
High-temperature cutting with coating encourages the formation of a useful outer layer of aluminum oxide. This layer is both hard and slick. While the hardness helps with wear resistance, the slickness lubricates the hot chip to help it slide away without adhesion or heat transfer.
Abrasion resistance
A high performance coating which excellent at machining of abrasive and difficult-to-machine and harden materials such as cast iron, aluminum alloys, tool steels, graphite, titanium alloys and nickel alloys. Its abrasion resistance makes it effective for machining work materials. - Nano TiAlN
The Titanium Aluminum nitride Coating, with purple black in color, is an effective coating for a wide variety of HSM applications.Effective coating for most applications. With benefits of high-temperature & abrasion resistance, extending tool life, and lubricity for chip removal. Great for dry machining and harden materials. Specialized in HSM applications. - DiaCoat / DLC
Diamond like Carbon, tough coating for milling non-ferrous materials. Diamond!|s intrinsic hardness results in long wear characteristics for increasing production Available upon request. - AlTiN + PLC
This coating , with silver color and multi-layers, has superior performance on cutting stainless steel and difficult-to-cut materials. - Coating types
Coating Layer |
TiN | TiCN | CrN | TiALN FUTURA |
TiALN FUTURA-NANO |
TiALN XTREME |
Coating Material |
Titanium Nitride |
Titanium Carbon Nitride |
Chromiun Nitride |
Titanium Aluminum Nitride |
Titanium Aluminum Nitride |
Titanium Aluminum Nitride |
Micro- hardness HV(HV0.05) |
2000 | 3000 | 1800 | 3000 | 3300 | 3500 |
Coefficient Against Steel(Dry) |
0.4 | 0.4 | 0.5 | 0.4 | 0.3~0.35 | 0.4 |
Process Temperature |
450 ℃ 840 ℉ |
450 ℃ 840 ℉ |
400℃ 750 ℉ |
450 ℃ 840 ℉ |
450 ℃ 840℉ |
450 ℃ 840 ℉ |
Max. Working Temperature |
600 ℃ 1100 ℉ |
400 ℃ 750 ℉ |
700℃ 1300 ℉ |
800 ℃ 1470 ℉ |
900 ℃ 1650℉ |
800 ℃ 1470 ℉ |
Coating Color |
Gold | Blue- Gray |
Silver- Gray |
Violet- Gray |
Violet- Gray |
Violet- Gray |
Key Characteristics |
Good general purpose | High hardness, goodwear resistance enhanced toughness |
Good adhesion, good corrosion and oxidation resistance | Good adhesion, good corrosion and oxidation resistance |
Excellent oxidation resistance |
Excellent oxidation resistance |
Primary Applications |
Machining of iron-based materials Metal forming Plastic molding |
For machining difficult-to machine steel alloys and high speed cutting where moderate temp are generated at the cutting edge Metal forming |
Machining copper Metal forming Plastic molding |
A multilayer coating designed for a wide range of carbide, cermet and high speed steel tooling Excellent for machining cast iron,stainless steel,nickel-based high temperature alloys and titanium alloys Designed for high speed and semi-dry or dry machining operations |
The cha-racteristics of FUTURA are maintained and even improved in excellent adhesion, higher hardness, lower residual compressive stress Excellent for machining cast iron,stainless steel,nickel-based high temperature alloysand titanium alloys Designed for high speed andsemi-dry or dry machining operations |
A specialized coating designed specifically for use on carbide end mills for the machining of hardened steel workpieces Designed for high speed and semi-dry or dry machining operations |