Vibration-assisted Carbide End Milling Research Results Report
2020-06-16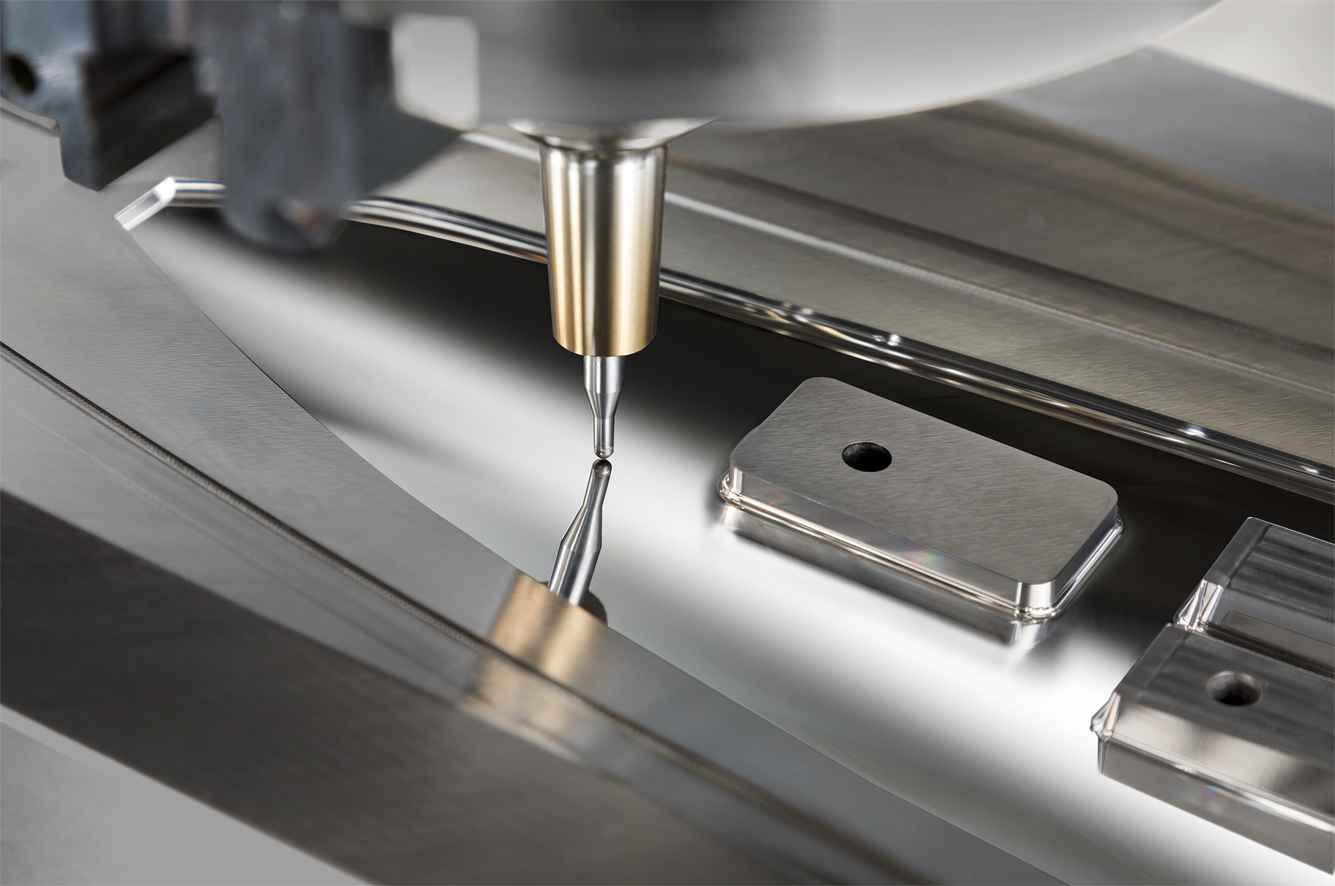
Abstract
This study presents a systematic analysis of the microfabrication technology for the development of vibrations for the miniaturized products required by emerging technologies. Auxiliary milling is applied to micromachine technology. It is expected to be in line with the international advanced cutting field. Vibration-assisted cutting is an emerging cutting and processing technology in recent years. Relative motion of amplitude. Compared with conventional machining, it has the advantages of improving the surface accuracy of workpiece and increasing the life of carbide end mills, etc. However, in the past, the experimental conditions only focus on a single vibration frequency and amplitude. In the past, however, the experimental conditions of vibration-assisted cutting only focused on a single vibration frequency and amplitude. The mechanism of vibration-assisted machining is not well understood. At present, it is known that the introduction of vibration-assisted machining technology is indeed beneficial to cutting. However, it is not known whether there are any limitations to the processing conditions. Therefore, it is still difficult to apply this technology to micromachining.
The objective of this exploratory research is to experimentally investigate the feasibility of superimposing small amplitude vibration of 2μm (frequency = 18 KHz) to micro-tool in milling SKD61 steels. The effects of process parameters on tool wear, surface roughness, and burr formation are studied for both vibrations assisted milling (VAM) and conventional milling (CM). Results indicated that VAM shows a better cutting performance than that of CM in terms of tool life, surface finish, and burr formation. The introduction of minimum quantity lubrication (MQL) in VAM can improve tool life because MQL can reduce the friction between the tool and workpiece.
I. Preamble
Cutting has always played an important role in the field of machine manufacturing. With the advancement of technology, precision workpieces miniaturization are not only a recent trend, but also the demand of many precision workpieces. For example, MEMS (Micro-Electro-Mechanical Systems), which is extremely popular these days, the size of the mechanical components must be very small and the finished workpieces are usually very small at high cost. It is not only difficult to machining small parts because of their size, but also because of the workpiece is lack of strength. Excessive cutting force during machining can damage the workpiece itself. In the case of aerospace materials, electronic and optical components, etc., these new materials and precision parts with complex shapes make machining a difficult task and series of questions.
Vibration-assisted cutting is one of the newest cutting and processing technologies in recent years, which generates high frequency between the carbide end mill and the workpiece by vibration device. It has the advantage of relative motion with small amplitude. Compared with conventional machining, it has the advantages of improving the surface accuracy of workpiece and increasing the life of carbide end mills, etc. However, the mechanism of vibration-assisted cutting was not well understood in the past research. At present, it is known that the introduction of vibration-assisted machining technology is beneficial to the cutting process. However, it is not known whether there are any limitations of processing conditions. Therefore, it is still difficult to apply this technology to micromachining.
II. Objectives of the study
Micro-machining is the use of sub-centimetre (sub-millimetre) machining. Micro carbide end mill for the millimeter. In addition, the precision of dimensional processing of micro components is the first priority of the industry. In addition, the quality of the dimensional accuracy of the micro devices is the first consideration of the industry. One of the most important research objectives is to apply the micromachining process to produce high-precision products. The micro-machining process is not only difficult due to the small size of the workpiece, but also due to the workpiece is lack of strength. Excessive cutting force during machining can damage the workpiece itself. In the case of aerospace materials, electronic and optical components, etc., these new materials and precision parts with complex shapes makes difficult task for machining. A series of problems have arisen from the use of ultrasonic technology. These difficult technical problems are becoming more and more difficult to solve by conventional methods. Therefore, non-traditional machining methods such as ultrasonic machining, electro discharge machining (EDM), and laser machining are used for cutting. The unconventional machining methods such as the tungsten carbide end mill and the tungsten carbide cutter are used for chip-cutting. Even though many machining methods have been developed, it is still common to use carbide end mills for cutting. How to improve the current problems of traditional machining, such as reducing burrs and cutting force, and introducing vibration assisted machining (VAM) Vibration-assisted machining is a very good choice. It has good machining accuracy, effective reduction of cutting force, and help to reduce the generation of burrs. However, so far, the literature on vibration-assisted machining applied to micro-milling is quite limited compared to other machining methods such as turning and drilling. The relationship between machining parameters and machining results has not yet been clearly established, and it is therefore worthwhile to have further study and explore the relationship between vibration-assisted cutting and the machining results. The impact of cutting on micro milling applications is also the purpose of this study.
The purpose of this research is to study the application of vibration-assisted machining to the milling and processing of micro end mill. In the experimental process, by introducing a vibratory cutting mechanism in combination with milling and machining, with different machining parameters (cutting speed and feed). Observe and discuss the wear, surface accuracy and burrs of carbide end mills in conventional milling and vibration-assisted milling with micro-milling tools. The database of machining parameters is expected to be effective for the machining of micro parts. This will help in development.
III. Documentary research
1. Surface accuracy
Heisel et al. conducted an ultrasonic vibration-assisted machining experiment on ECu 57 steel and used a 5-mm deep hole with a solid carbide end mill diameter to drill this highly ductile material. Experimental results show that the deep hole machining without the vibratory assistants produces a wide, long, continuous chip similar to the satin ribbon. However, when ultrasonic vibration is introduced, it is obvious that the chip pattern becomes a spiral of short discontinuous chips. This phenomenon can removal the chip more easily, reduce the chip accumulation and reduce the cutting force, the surface accuracy after machining is also better than the traditional cutting. Chern et al. study high-frequency vibration-assisted micro-drilling. Compared to the usual design of vibrating device on the spindle, this paper presents a home-made bottom vibrating platform to introduce the vibration machining technology into the workpiece. According to the experimental results, high-frequency vibratory drilling on the bottom of the Z-axis workpiece is effective in improving the surface accuracy and roundness of the hole. Hsu et al. were turning Inconel 718, a nickel-based superalloy that is resistant to high temperature, and used a fixed frequency of 20k Hz vibratory cutting conditions to analyze different processing parameters such as speed, feed and depth of cut using Taguchi analysis. It is found that the machined surface after vibration cutting is smoother and flatter than normal cutting.
2. Cutting forces
Nath et al. applied vibration-assisted turning techniques to the machining of low aluminum alloy DF2 material and analyzed the spindle speed individually. The effect of the three-directional component forces (radial, axial and longitudinal forces) on turning. The experimental results show that a feed rate between 0.1 and 0.2 mm/min results in an increase tangent of the three-directional force applied to vibratory turning. The average cutting force is about 50% of that of conventional turning. The high activity of the tool causes a BUE phenomenon, which is caused by the 19k Hz 30μm, it was found from experiments that this method of machining titanium alloy can reduce the cutting temperature, reduce adhesion and the same ultrasonic vibration-assisted turning study, Liu et al. Processing ceramic materials with a frequency of 20k Hz and an amplitude of 15μm effectively reduces the occurrence of BUE and achieves a reduction in cutting force. Moriwaki et al. applied vibration-assisted milling to single crystal diamond tungsten carbide end mills for cutting steel. The experimental measurement results showed that the cutting force of vibration milling was only 1/8 of that of conventional milling. The self-vibrating device is used for drilling and cutting, and the vibration introduction makes it easy to remove chips. The cutting force is reduced by reducing the friction during cutting.
3. Carbide end mills wear out
Liao et al. used TiAlN-coated drills to introduce ultrasonic vibration-assisted machining of nickel-based alloys. In addition, the processing characteristics of this material are investigated from the data of cutting force and wear of carbide end mills (Inconel 718). When comparing the combination of vibratory cutting with non-vibratory cutting, the cutting force of the former is lower than that of the latter, resulting in longer tool life. In Kuo's research, vibrations were also added to improve the situation where the tool broke due to excessive cutting force during tapping, and the threaded teeth were smoother after machining.
Chern et al. used a hand-made vibratory machining platform to introduce vibratory micro milling on aluminum alloy, with a frequency of 500 Hz. and the amplitude and 10 μm vibration conditions, the life of carbide end mills is improved by 22% compared to the life without vibration. Chang et al. used non-plated and nitrided carbide coated carbide end mills to improve the tool life. Titanium (TiN)-coated drill bits are used for ultrasonic vibration-assisted drilling experiments on aluminum alloy. However, the wear of carbide end mills is greater than that of conventional drilling tools.
Chern et al. used a hand-made vibratory machining platform to introduce vibratory micro milling on aluminum alloy, with a frequency of 500 Hz. and the amplitude and 10 μm vibration conditions, the life of carbide end mills is improved by 22% compared to the life without vibration. Chang et al. used non-plated and nitrided carbide coated carbide end mills to improve the tool life. Titanium (TiN)-coated drill bits are used for ultrasonic vibration-assisted drilling experiments on aluminum alloy. However, the wear of carbide end mills is greater than that of conventional drilling tools.
4. Burr situation
Vibration-assisted drilling has shown remarkable results in the suppression of burr formation, and Azarhoushang et al. used ultrasonic vibration drilling of the nickel-based alloy Iconel 738-LC can reduce the generation of exit burrs. In Pujana et al.'s study, the exit hole was found to be completely free of burrs.
IV. Research methodology
The main experimental equipment in this study is a commercial micro-ultrasonic processing machine with a frequency range of 17.5 kHz~17.5 kHz generated by the spindle of the processing machine. 30 kHz and an amplitude of 0~30 μm to achieve the purpose of vibratory cutting. The ultrasonic processing machine system is shown in Figure 1. The micro-milling cutter has a 1.2 mm long cutting edge, 0.6 mm diameter, and 35-degree helix angle. The end mills are made of tungsten carbide and are uncoated.
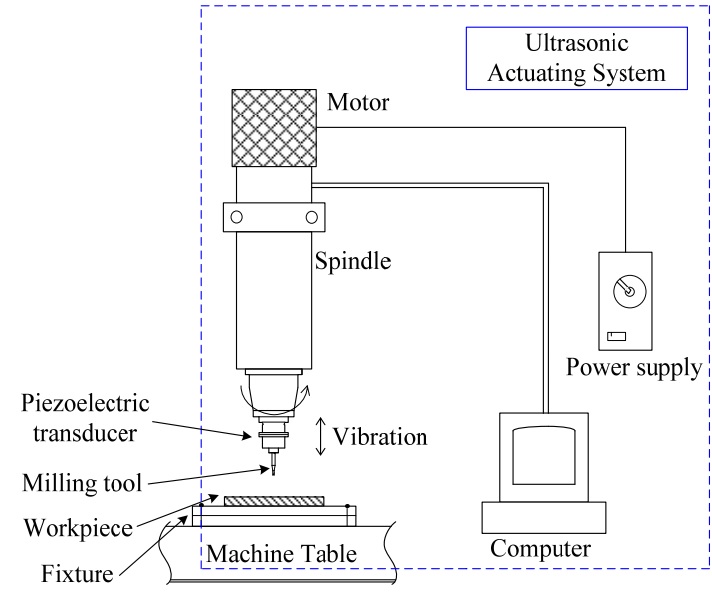
Fig 1: Ultrasonic processing machine system diagram
In order to reduce the wear time of carbide end mills, slot milling is used for conventional milling (CM) and vibration-assisted milling (VAM). The cutting depth is 0.2mm and the cutting length is 24mm. In the cutting experiment, the fixed cutting depth of 0.2mm and the cutting length of 24mm were used for one cut, as shown in Fig. 2. The main objective of this study is to investigate the processing effects of traditional cutting and vibration-assisted cutting. This study compares the effects of different feeds and cutting speeds under traditional cutting and vibration-assisted cutting environments. In this study, we investigate the effect of vibration-assisted cutting on machining, and find the resonance frequency of single vibratory cutting parameter. In order to investigate the effect of vibration-assisted cutting on machining, this study uses a single fixed vibratory cutting parameter and finds the resonance frequency of the parameter. The measured amplitude is 2 μm at 18 kHz.
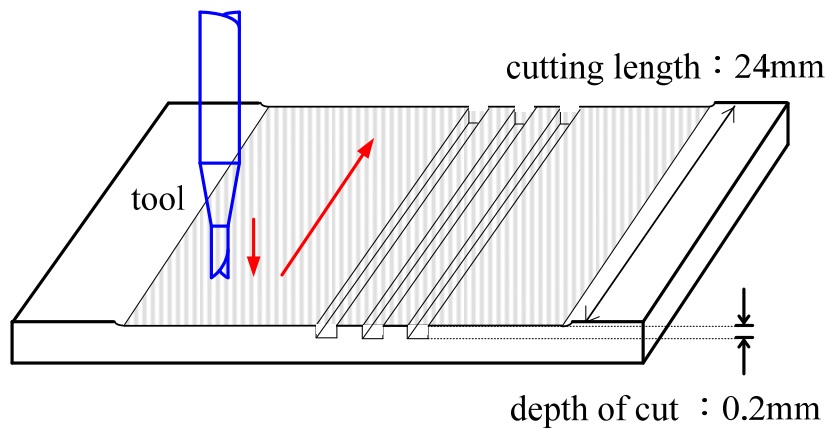
Fig. 2: Schematic diagram of cutting experiment
V. Results and Discussion
1.The effect of vibration-assisted milling on the wear of carbide end mills
A comparison of the wear data of carbide end mills with conventional cutting and vibration-assisted cutting is shown in Fig. 3. After cutting a length of 168 mm with different feeds, vibration-assisted carbide cutting improves the wear of the carbide end mills compared with the traditional cutting, as shown in Fig. 3. 13.81% and 16.30% of the wear of the carbide end mills. As shown in Fig. 3(b), for a feed rate of 4 m/rev, the wear of the carbide end mills with vibration-assisted cutting is not as high as that of the feed rate. Each cut is generally less abrasive than conventional cutting at 2 μm/rev, but after cutting 96 mm and 120 mm. the wear of the carbide end mills decreases more and more after all the cutting is completed. This result has a great impact on the use of carbide end mills, as this experiment shows that the larger the feed of the micro end mills, the greater the wear of the carbide end mills. The smaller the wear of the carbide end mill, the larger the cutting feed, the greater the positive force, which will cause the carbide end mill to fracture easily. The smaller the feed, the carbide end mills will wear out, and the introduction of vibration assist improves this problem.
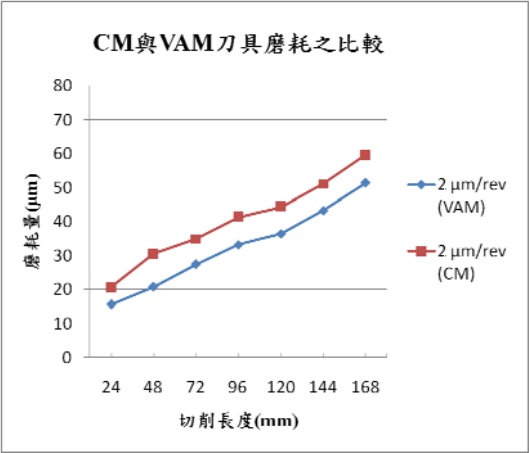
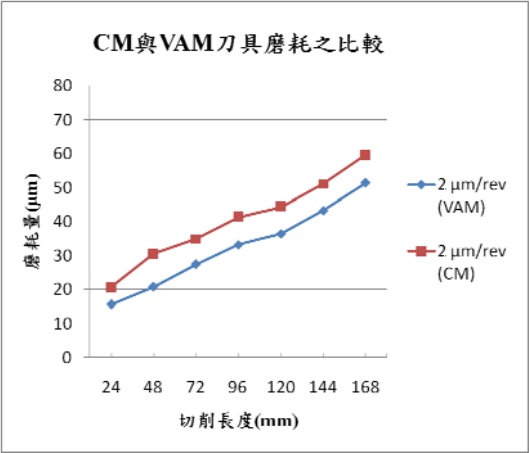
(a) feed of 2 μm/rev
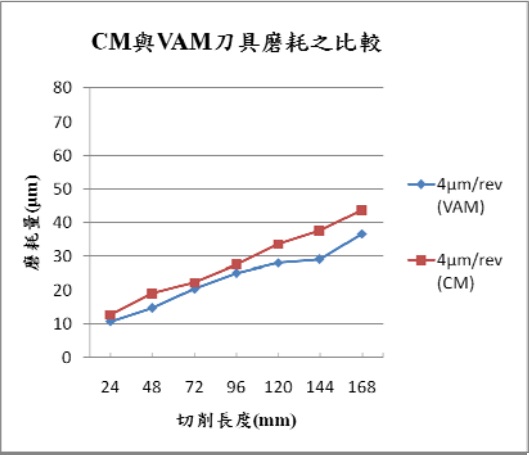
(b) feed of 4 μm/rev
Fig. 3: Comparison of wear between CM and VAM carbide end mills (fixed cutting speed of 3.39 m/min)
2. The effect of vibration-assisted milling on the surface accuracy and burrs of the workpiece
Fig. 4 shows the average roughness value of traditional cutting and vibration-assisted cutting. Fig. 4 (a) and (b) shows the cutting conditions with cutting speed 3.39 m/min, feed 2 μm/rev and 4 μm/rev. m/rev, under the vibration-assisted cutting, the average roughness improved by 36.34 % and 43.51 % respectively. Fig. 5 shows the contour of the tool marks on the bottom of the workpiece taken by Nano Focus after the cutting experiment with vibration-assisted cutting.
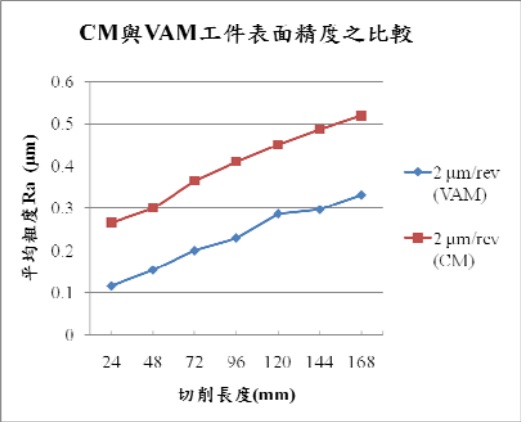
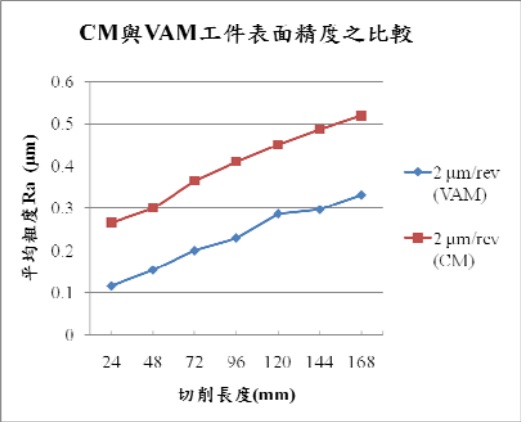
(a) feed of 2 μm/rev
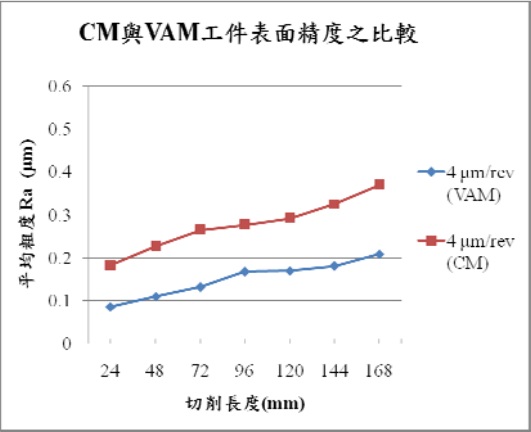
(b) feed of 4 μm/rev
Fig. 4: Comparison of CM and VAM workpiece surface accuracy
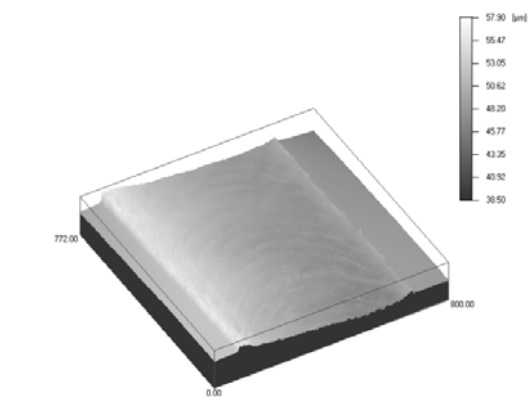
Fig. 5: CM vibration-assisted cutting of the bottom of the workpiece after 168 mm (Nano Focus). (Cutting speed 3.39 m/min, feed 6 μm/rev)
In cutting machining, due to the unique machining method of milling, the burrs generated in the down milling direction are usually larger than those in the up milling direction. In order to compare the effect of different cutting methods (CM and VAM) on the burr formation, we set the cutting speed at 3.39 m/min. After the cutting experiment, the burr height of the down milling end and the up milling end is measured individually and recorded in photos. After the cutting experiment is completed, measure the burr height of the down-milling end and the up-milling end individually, and take photos to record the comparison of the burr height of the down-milling end and the up-milling end of each groove after cutting, as shown in Fig. 6.
Fig. 6 shows that under vibration-assisted cutting conditions, the burr height of the milling end is lower than that of conventional cutting, and the burr height is reduced by up to 17.46%. The reason for this phenomenon is that when vibration cutting is applied, the relative bottom of the carbide end mill moves downward and also participates in the cutting. As the carbide end mill moves downward, the effective rake angle also vibrates with the vibration. The location keeps changing, also, the angles are larger than the un-vibrated ones, so it will help the flow of chips and suppress the burr effect.
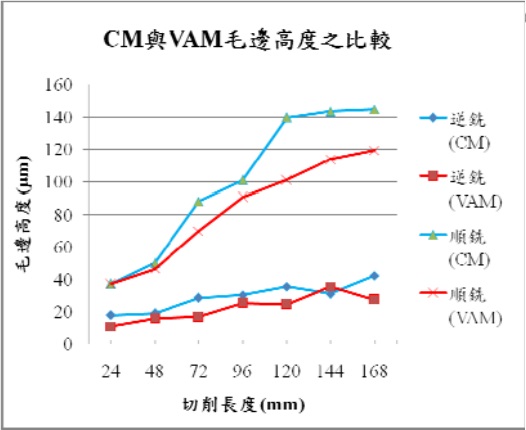
Fig. 6: Comparison of CM and VAM burr height at the down and up end milling
3. Vibration-assisted milling and micro-lubrication compound machining
As shown in Fig. 7, the vibration-assisted machining of carbide end mills with MQL has a significant reduction in wear. It is obvious from the experimental results that there is a significant decrease in the wear of carbide end mills under MQL cutting, both for vibration-assisted machining and MQL cutting. It means that adding MQL can effectively lubricate the cutting area between the solid carbide end mill and the workpiece and reduce the cutting force. In addition, the grinding wear of carbide end mills has been reduced significantly.
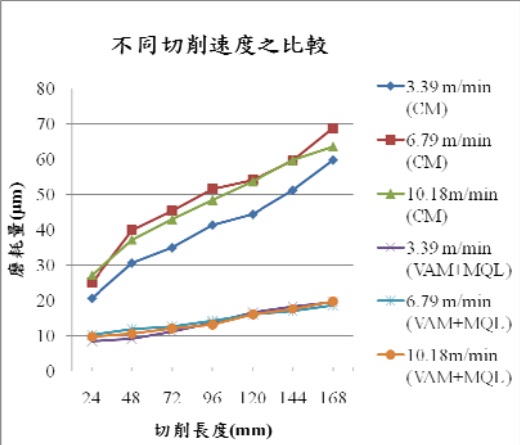
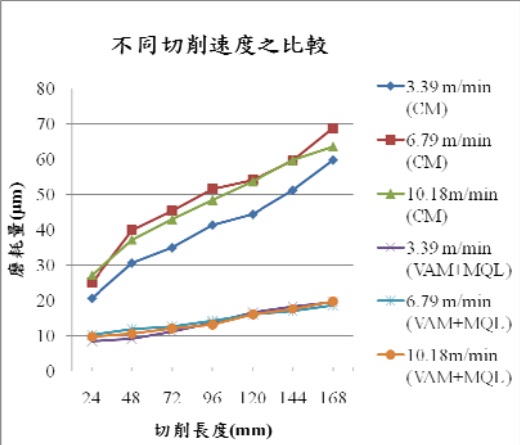
Fig. 7: Comparison of wear of carbide end mills with different cutting speeds (fixed feed of 2 μm/rev)
Vibration-assisted cutting with the introduction of MQL, so that the cutting fluid can reach the machining area more, and the machining part between the carbide end mill and the workpiece. Effective lubrication is provided, and the cutting is carried away. As shown in Figure 8, the addition of MQL to vibration-assisted cutting has a good effect on the burr generation, whether it is on the milling side or the reverse milling side. Milling end burrs. Therefore, adding MQL to vibration assisted cutting can raise the machining quality to a higher level.
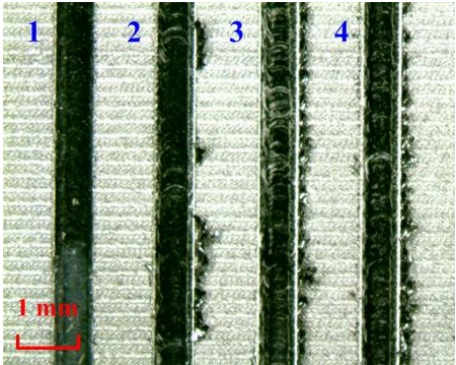
(a) CM Groove burrs
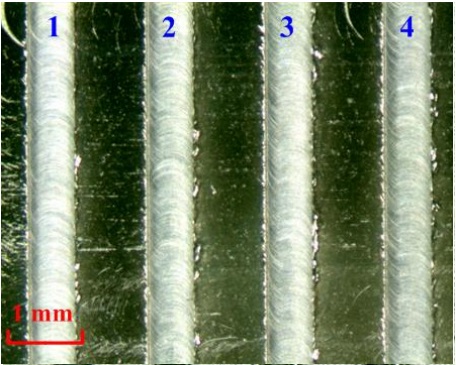
(b) VAM+MQL groove burrs
Fig. 8: Comparison of groove burrs between CM and VAM (cutting speed 3.39m/min, feed 4μm/min. rev)
VI. Conclusion
This study is to investigate the effect of wear on carbide end mills, surface accuracy and burrs on the surface of carbide end mills under conventional milling and vibration-assisted milling. In addition, an effective database of machining parameters can be established for reference by subsequent researchers. With the introduction of vibratory assistance, the wear of carbide end mills with the same cutting conditions is less than that of conventional cutting. The machining conditions of 3.39 m/min and 6 μm/rev feed were the most reduced by 22.64%. The results indicate that when the cutting conditions are three times greater than the cutting speed in vibration speed, it extends the life of the carbide end mills and improves the cutting performance. The results of the experiments on the burrs show that the greater the wear of the carbide end mills, the larger the burrs will be and the larger the burrs of the milling end will be. And the burr size of the down-milling end will usually be larger than up-milling. The vibration-assisted cutting suppresses the formation of burrs and improves the burr height up to 18.6%. The reason for this is that the effective cutting angle of the bottom of the carbide end mill is larger than that of the non-vibrating cutter when vibration cutting is applied. The results also show that the combination of vibration-assisted milling and MQL can effectively improve the situation of excessive cutting force caused by friction when the vibration speed is less than three times of the cutting speed, resulting in the breakage of carbide end mills, it has the advantage of enhancing the life of carbide end mills and also has the effect of greatly improving the surface accuracy of workpieces and suppressing burr formation.