振動輔助鎢鋼端銑刀微銑削之研究 研究成果報告
2020-06-16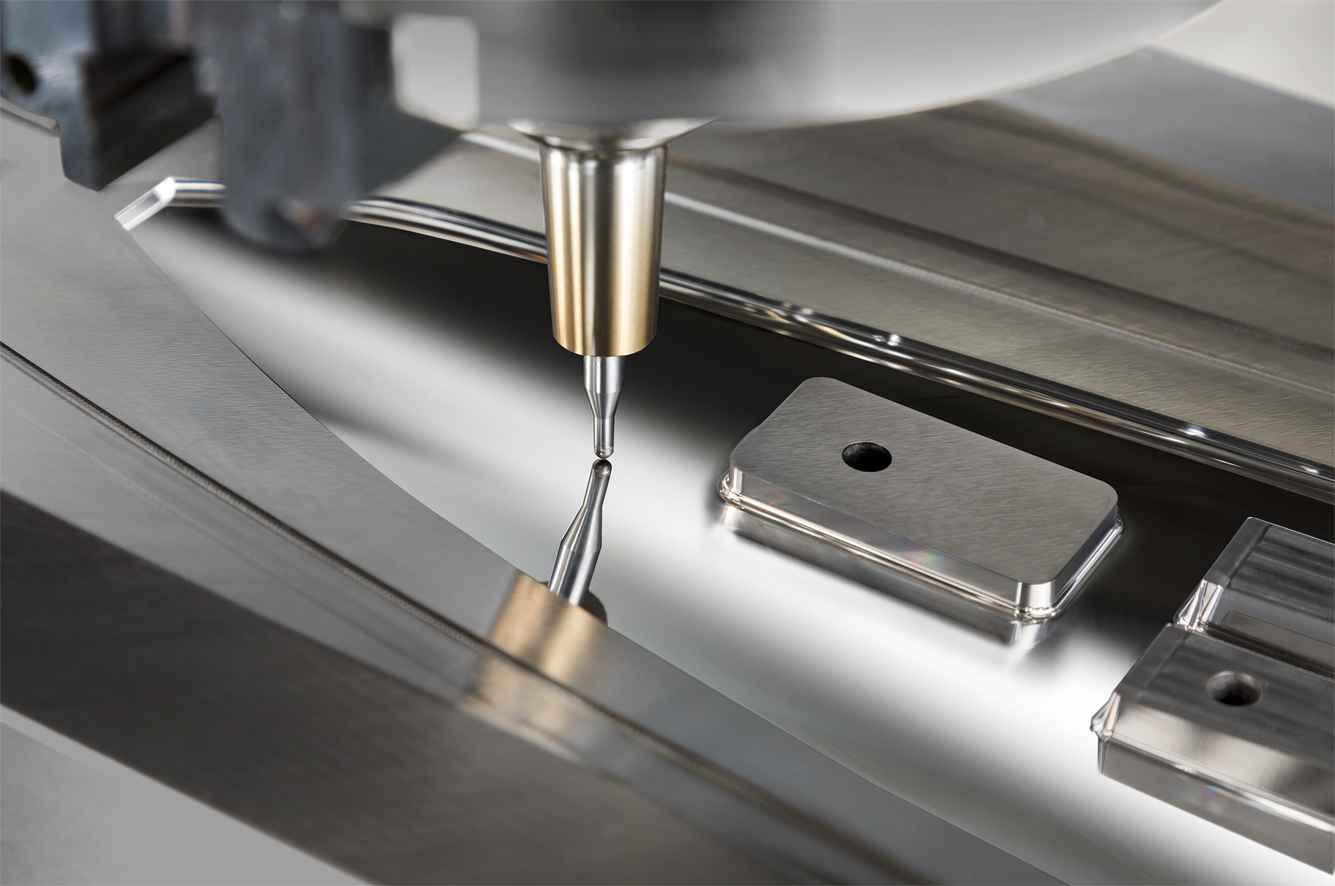
摘要
本研究針對新興科技所需微小化產品之精微加工技術,提出系統性的研究分析,並藉此開發振動輔助銑削應用於微型工具機技術。期能與國際間在前瞻切削領域接軌。振動輔助切削是近年來新興的一種切削加工技術,藉由振動裝置使鎢鋼與工件間產生高頻率、微小振幅的相對運動。與傳統加工相比,具有提升工件表面精度、增加鎢鋼端銑刀壽命等優點。然而過去的振動輔助切削研究,其實驗條件僅針對單一振動頻率與振幅,對於振動輔助切削技術之機制並不甚了解。目前所知,為導入振動輔助加工技術,的確對切削加工有助益。但是否有任何加工條件的限制則一無所知。因此將此一技術應用於精微加工上仍有其困難。
本研究主要是以振動輔助加工應用於微銑刀(直徑 0.6 mm)的銑削加工為研究方向。在不同加工參數(切削速度與進給)組合下,探討微型銑刀在傳統銑削與振動輔助銑削下之鎢鋼端銑刀磨耗、工件表面精度及毛邊之差異。實驗結果指出,當振動速度大於切削速度三倍時,可明顯延長鎢鋼端銑刀壽命。在本研究的實驗條件範圍內,振動輔助切削相對於傳統切削,工件表面精度在進給 4 μm/rev、切削速度 3.39 m/min 的加工條件中為提升最多的 43.51 %。而振動輔助切削的導入,亦有抑制毛邊生成的作用。在振動輔助切削加入微量潤滑(MQL)可有效改善振動輔助切削因摩擦增加導致切削力過大鎢鋼端銑刀斷裂的情形,在提升工件表面精度及抑制毛邊生成皆有很好的表現。
一、前言
切削加工在機械製造領域中,一直扮演相當重要的角色。隨著科技的進步,產品微小化不僅是近年來的趨勢,也是現在許多產品的訴求。如現在極熱門的微機電系統( MEMS),其各機械元件體積就必須非常微小,且成品通常在高精度的要求下完成。加工微小零件時,不但因工件體積微小加工不易,也因為工件強度往往很弱,加工稍有不慎或是加工時切削力過大便會損壞工件本身。如果碰上航空材料、電子與光學元件…等,這些新的材料和形狀複雜的精密零件,讓切削加工面臨一連串的問題。
振動輔助切削是近年來新興的一種切削加工技術,藉由振動裝置使鎢鋼端銑刀與工件間產生高頻率、微小振幅的相對運動。與傳統加工相比,具有提升工件表面精度、增加鎢鋼端銑刀壽命等優點。然而過去的振動輔助切削研究,對於振動輔助切削技術之機制並不甚了解。目前所知為導入振動輔助加工技術,的確對切削加工有助益。但是否有任何加工條件的限制則一無所知。因此將此一技術應用於精微加工上仍有其困難。
二、研究目的
機械式微切削加工(micro-machining),乃是使用次厘米(sub-millimeter)的微型鎢鋼端銑刀(Micro carbide end mill)來做元件細微尺寸的加工。另外,微小元件之產品,其加工之尺寸精度的優劣,乃是工業界之第一考量,因此,若能有效的應用微切削加工製程,製造出高精度的產品,可謂一重要之研究目標。加工微小零件時,不但因工件體積微小加工不易,也因為工件強度往往很弱,加工稍有不慎或是加工時切削力過大便會損壞工件本身。如果碰上航空材料、電子與光學元件…等,這些新的材料和形狀複雜的精密零件,讓切削加工面臨一連串的問題。這些難加工技術問題已漸漸不是傳統加工方法所能勝任,因此超音波加工(Ultrasonic machining)、放電加工(EDM)及雷射加工(Laser machining )等非傳統加工方法就被應用於切削加工上。縱然衍生出許多加工成型方法,但以鎢鋼端銑刀作切削仍普遍。如何改善傳統加工當前的問題,譬如:減少毛邊、降低切削力等,導入振動輔助切削(Vibration -assisted machining)技術,是個很好的選擇。其良好的加工精度、有效降低切削力,對於減少毛邊的生成也有助益。但是目前為止,振動輔助切削應用於微銑削的文獻探討,比起其他加工方法如車削、鑽削等相當有限,對於加工參數和加工結果的關係尚未有明確定論,因此值得進一步研究與探討對振動輔助切削應用於微銑削加工的影響,也是本研究之目的。
本研究之目的,擬針對振動輔助應用於微型銑刀的銑削加工作為研究方向。在實驗過程中,藉由導入振動切削機制結合銑削加工,配合不同加工參數(切削速度與進給),觀察及探討微型銑刀在傳統銑削與振動輔助銑削下之鎢鋼端銑刀磨耗、工件表面精度及毛邊之各種可能影響,並探討加入切削液的效果,提出一套有效的加工參數資料庫,期能對精微零件加工的發展有所助益。
三、文獻探討
1. 表面精度方面
Heisel等人作超音波振動輔助加工ECu 57鋼材實驗,以鎢鋼端銑刀直徑5mm深孔鑽削此高延展性材料,探討切削後的表面精度、切屑型態,及比較傳統鑽削和超音波振動輔助鑽削的結果。實驗結果發現,沒加入振動輔助在作深孔加工時,會產生類似緞帶型較寬、較長的連續型切屑。但當導入超音波振動時,明顯的觀察到切屑型態變成螺旋狀短的不連續之切屑。此現象可以更容易幫助切屑的排除,減少切屑堆積使切削力下降,加工後的表面精度也比傳統切削來的好。Chern等人研究高頻振動輔助微細鑽孔,相對於一般將振動裝置設計在主軸上,此篇文獻則是自製底部振動加工平台於工件上導入振動加工技術,勝於前者的優勢在振動裝置設計簡單且花費成本便宜。其實驗結果顯示,加諸在Z軸工件底部高頻振動鑽削有效改善孔壁的表面精度及孔洞的真圓度。Hsu等人在車削Inconel 718這類耐高溫之鎳基超合金,藉由固定頻率20k Hz的振動切削條件,使用田口分析法分析不同轉速、進給量及切深等加工參數,發現振動切削後的加工表面比一般切削來的更加光滑平整。
2. 切削力方面
Nath等人在應用振動輔助車削技術於低鋁合金DF2材質進行加工研究中,個別分析主軸轉速對車削的三方向分力(徑向力、軸向力和縱向力)之影響。實驗結果顯示,進給率在0.1 - 0.2mm/min之間,導入振動車削之三方向分力的切削力平均約為傳統車削50%。Koshimizu學者,針對鈦合金耐高溫、不易散熱及高溫活性高的特質,使其加工會有積屑刃口(BUE)現象,作者藉由在車刀進給方向產生19k Hz、30μm的微幅振動,從實驗中發現以此方式加工鈦合金可以降低切削溫度,減少了黏附和摩擦,使得切削力平均減少1/2 ~ 1/3。同樣是超音波振動輔助車削研究,Liu等人以頻率20k Hz、振幅15μm加工陶瓷金屬材料,也有效減少BUE的發生,達到切削力降低的效果。Moriwaki 等人將振動輔助銑削方式應用於單晶鑽石鎢鋼端銑刀切削鋼材,實驗量測結果顯示,振動銑削的切削力甚至只有傳統銑削的1/8。Paris等人利用自我振動(self-vibrating)裝置應用在鑽孔切削中,而因為振動的導入使切屑易排除,減少了切削時的摩擦而得到切削力降低的結果。
3. 鎢鋼端銑刀磨耗情形
Liao等人使用氮化鋁鈦(TiAlN)鍍層之鑽刀導入超音波振動輔助加工鎳基合金 (Inconel718),並從切削力與鎢鋼端銑刀磨耗等數據來探討此材料之加工特性。在結合振動切削中與未導入振動比較時,因為前者的切削力較後者低,使鑽刀壽命增長。在Kuo的研究中,也加入振動來改善攻牙時因切削力過大導致斷刀的情形,且加工後螺紋齒更平順。
Chern等人以自製振動加工平台於鋁合金上導入振動微銑削的實驗中,以頻率 500Hz振幅及10 μm的振福條件,鎢鋼端銑刀壽命比未加入振動提升22%。但非一定導入振動輔助加工即對鎢鋼端銑刀壽命呈現正面效果。Chang等人利用無鍍層與氮化鈦(TiN)鍍層之鑽頭於鋁合金上進行超音波振動輔助鑽削實驗,加入振動輔助雖可降低毛邊高度,但是鎢鋼端銑刀磨耗卻皆比傳統鑽孔還大。
Chern等人以自製振動加工平台於鋁合金上導入振動微銑削的實驗中,以頻率 500Hz振幅及10 μm的振福條件,鎢鋼端銑刀壽命比未加入振動提升22%。但非一定導入振動輔助加工即對鎢鋼端銑刀壽命呈現正面效果。Chang等人利用無鍍層與氮化鈦(TiN)鍍層之鑽頭於鋁合金上進行超音波振動輔助鑽削實驗,加入振動輔助雖可降低毛邊高度,但是鎢鋼端銑刀磨耗卻皆比傳統鑽孔還大。
4. 毛邊情形
振動輔助鑽削在抑制毛邊生成方面有顯著的成果。Azarhoushang等人以超音波振動鑽削鎳基合金Iconel 738-LC,可以減少出口毛邊的產生。而在Pujana等人研究中,於鑽孔的出洞口甚至發現完全無毛邊情形。
四、研究方法
本研究之主要實驗設備為商用之微超音波加工機,由加工機主軸產生頻率範圍17.5 kHz~30 kHz及振幅大小0~30μm,以達振動切削之目的。超音波加工機系統如圖1所示。所採用之微型銑刀,刀刃長度為1.2mm、刀刃直徑為0.6mm、螺旋角度為35度之雙刃銑刀,其材質為碳化鎢且無鍍層。
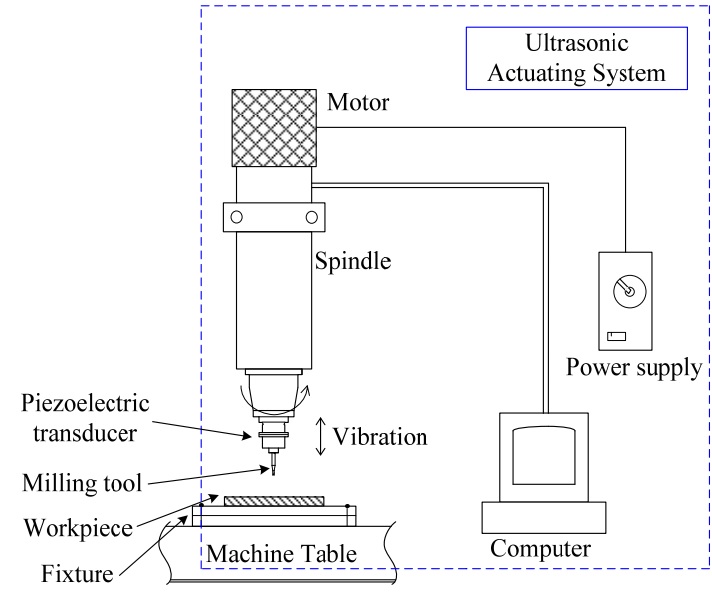
圖1: 超音波加工機系統示意圖
為減少鎢鋼端銑刀磨耗實驗之時間,以槽銑做為傳統銑削加工(CM)與振動輔助銑削(VAM)之比較基準。切削實驗中採固定切削深度 0.2mm,切削長度24mm為切削一次,如圖 2 所示。本研究主要目標為針對傳統切削與振動輔助切削下之加工影響為研究目標。比較在傳統切削與振動輔助切削環境下,不同進給(feed)與切削速度(cutting speed)對鎢鋼端銑刀磨耗、毛邊高度與加工後工件表面精度之影響。為探討振動輔助切削對加工的影響,本研究以固定單一振動切削參數進行實驗,在找到其共振頻率為18 kHz後,量測之振幅為2 μm。
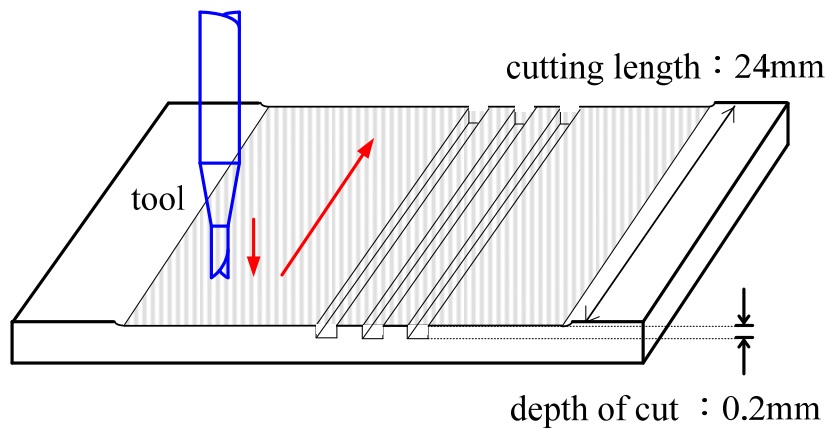
圖2: 切削實驗示意圖
五、結果與討論
1. 振動輔助銑削對鎢鋼端銑刀磨耗之影響
將傳統切削與振動輔助切削的鎢鋼端銑刀磨耗資料做整合比較,如圖3所示。鎢鋼端銑刀在不同進給下切削完168 mm長度後,振動輔助切削比傳統切削各改善了13.81%及16.30%的鎢鋼端銑刀磨耗量。如圖3(b)進給量為4 m/rev的條件下,振動輔助切削之鎢鋼端銑刀磨耗量,雖未像進給為2 μm/rev般每道切削完皆較傳統切削磨耗低,但在切削96 mm以及120 mm後也有慢慢拉開的趨勢,且全部切削完成後之鎢鋼端銑刀磨耗量減少幅度愈來愈大。此結果對鎢鋼端銑刀使用來說有很大的影響,由本實驗結果得知微型銑刀在加工時,進給量愈大則鎢鋼端銑刀磨耗愈小,但切削的進給量愈大,所承受的正向力也愈大,易使鎢鋼端銑刀發生斷裂,而進給量愈小則又有鎢鋼端銑刀容易磨耗的問題,而振動輔助的導入則改善了此問題。
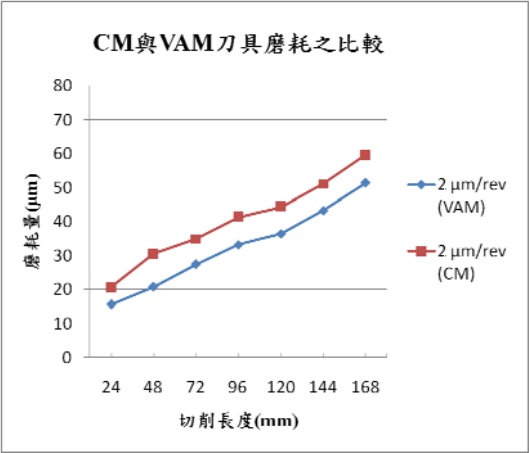
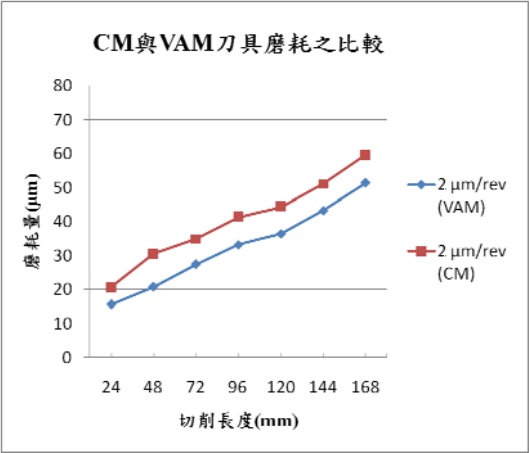
(a) 進給為2 μm/rev
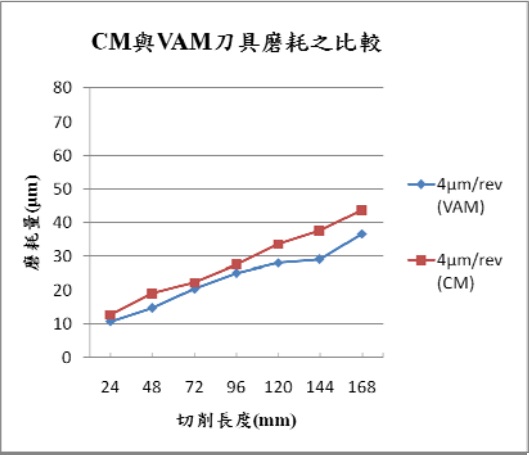
(b) 進給為4 μm/rev
圖3: CM與VAM鎢鋼端銑刀磨耗之比較(固定切削速度為3.39 m/min)
2. 振動輔助銑削對工件表面精度及毛邊之影響
將傳統切削與振動輔助切削之平均粗度值整合比較,如圖4所示。圖4(a)與(b)切削條件為切削速度3.39 m/min,進給2 μm/rev及4 μm/rev,在振動輔助的切削下,平均粗度各改善了36.34 %與43.51 %。圖5為振動輔助切削,經切削實驗後以Nano Focus拍攝的工件底部刀痕輪廓圖。
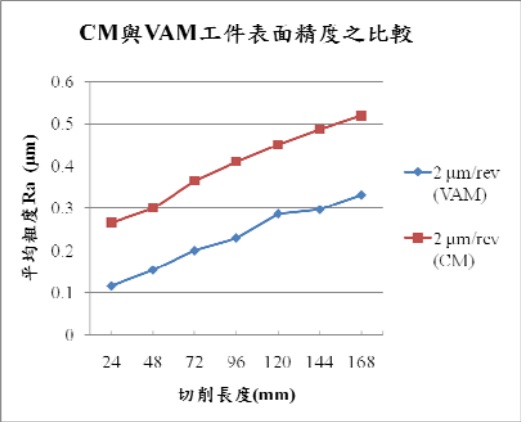
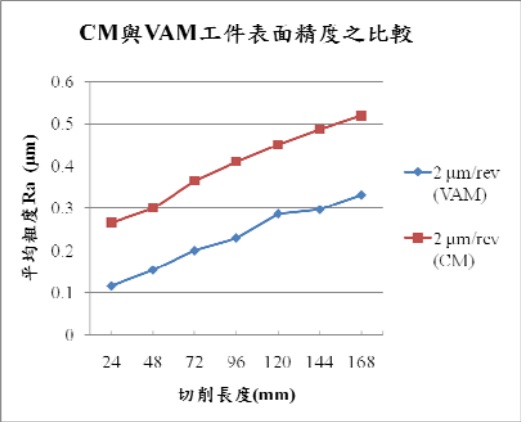
(a) 進給為2 μm/rev
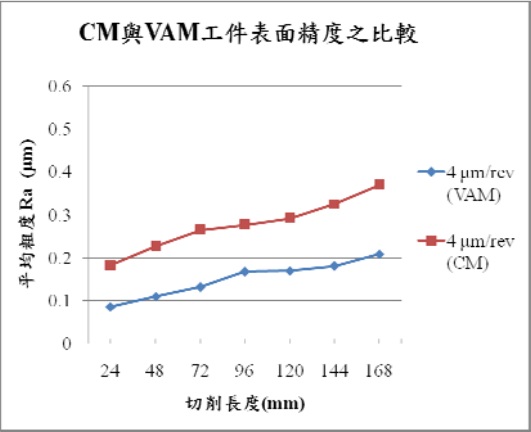
(b) 進給為4 μm/rev
圖4: CM與VAM工件表面精度之比較
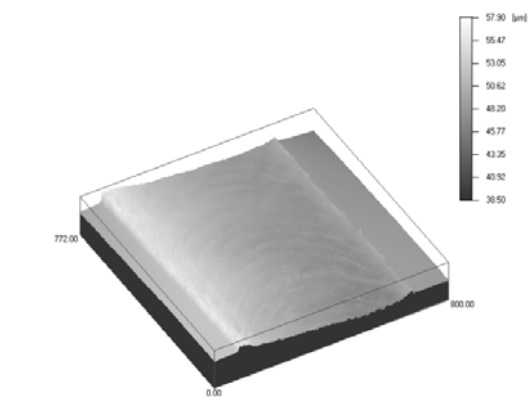
圖5: CM 振動輔助切削168 mm後工件底部刀痕輪廓(Nano Focus)(切削速度 3.39 m/min、進給6 μm/rev)
在切削加工中,因為銑削獨特的加工方式,順銑方向所產生的毛邊通常皆大於逆銑端毛邊。為比較不同切削加工方式(CM與VAM)對毛邊生成之影響,在切削速度3.39 m/min,進給4 μm/rev下進行實驗。待工件切削實驗完成後,個別量測順銑端與逆銑端之毛邊高度,並拍照記錄,其切削後每道溝槽順、逆銑端毛邊高度之比較,如圖6所示。由圖6可看出振動輔助切削條件下,順銑端毛邊高度皆低於傳統切削,毛邊高度減少達 17.46 %。造成此現象的原因為當有加入振動切削時,相對的鎢鋼端銑刀底部在向下移動的時候也會參與切削。隨著鎢鋼端銑刀向下移動,有效傾角(effective rake angle)也隨著振動位置不同一直改變,但角度大小皆比未加振動的大,因此會幫助切屑的流動,而達到抑制毛邊的效果。
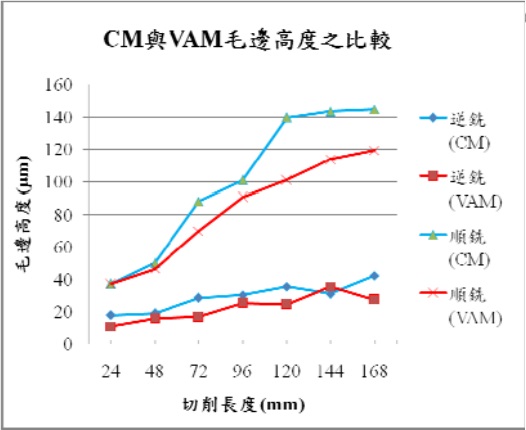
圖6: CM與VAM順、逆銑端毛邊高度之比較
3. 振動輔助銑削與微量潤滑複合式加工
如圖7所示。從實驗結果可明顯看到,振動輔助加工在使用MQL切削下,鎢鋼端銑刀磨耗量有顯著的下降,皆未超過20 μm。表示加入MQL能有效潤滑鎢鋼端銑刀與工件間的切削區域,切削力得以減少,鎢鋼端銑刀磨耗也大幅下降。
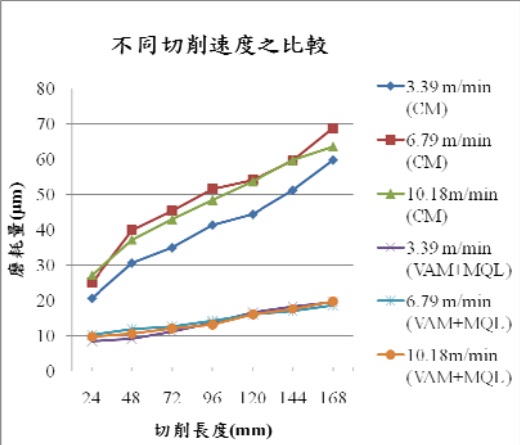
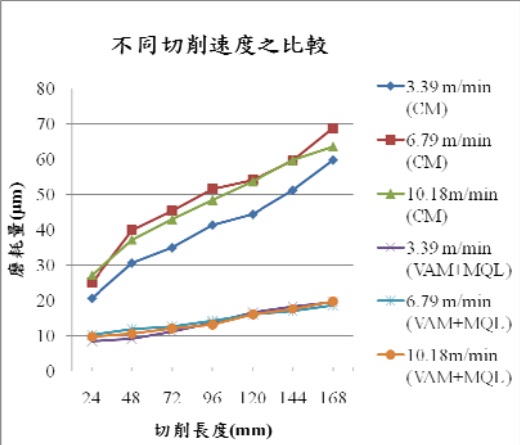
圖7: 不同切削速度鎢鋼端銑刀磨耗量之比較(固定進給2 μm/rev)
振動輔助切削在MQL導入下,使切削液更能到達加工區域,對鎢鋼端銑刀與工件之間的加工部位進行有效的潤滑,並且有帶走切削功能。如圖8所示,振動輔助切削加入MQL,其毛邊生成方面有很好的抑制效果,不管是順銑端或是逆銑端毛邊。因此振動輔助切削上加入MQL,可使加工品質更提升一個層次。
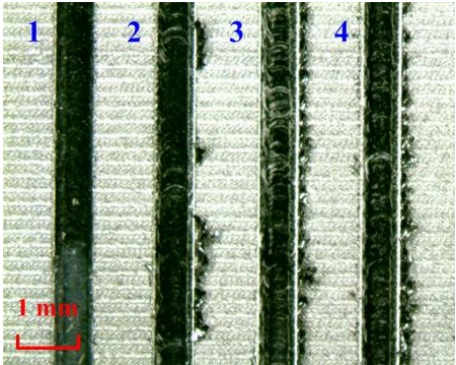
(a) CM溝槽毛邊
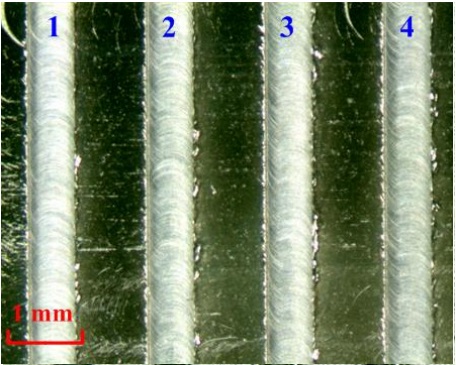
(b) VAM+MQL溝槽毛邊
圖8: CM與VAM溝槽毛邊比較(切削速度 3.39m/min、進給 4μm/rev)
六、結論
本研究為探討微型銑刀在傳統銑削與振動輔助銑削下之鎢鋼端銑刀磨耗、工件表面精度及毛邊之影響,並建立一套有效的加工參數資料庫,以供後續研究人員作為參考。在振動輔助的導入下,相同切削條件之鎢鋼端銑刀磨耗量皆比傳統切削來的小,其中以切削速度3.39 m/min、進給6 μm/rev的加工條件為減少最多的22.64 %。研究結果指出當切削條件在振動速度大於切削速度三倍時,可延長鎢鋼端銑刀壽命,並改善切削性能。在探討毛邊的實驗結果得知,當鎢鋼端銑刀磨耗愈大,其毛邊愈大,且順銑端的毛邊大小通常會大於逆銑端的毛邊。而加入振動輔助切削則可抑制毛邊的生成,在不同的切削條件下,毛邊高度改善最多可達18.6%。其原因為當有加入振動切削時,鎢鋼端銑刀底部有效切削角的角度比未加振動大,因此會幫助切屑的流動,而達到降低毛邊高度的效果。研究結果也指出振動輔助銑削與MQL的複合式加工能有效改善振動輔助切削在振動速度小於切削速度三倍時,因摩擦增加導致切削力過大鎢鋼端銑刀斷裂的情形,具有提升鎢鋼端銑刀壽命之優點,也有大幅提升工件表面精度及抑制毛邊生成的效果。