微端銑削中的銑刀磨損 : 材料微觀結構的影響,建模和實驗驗證
2020-06-11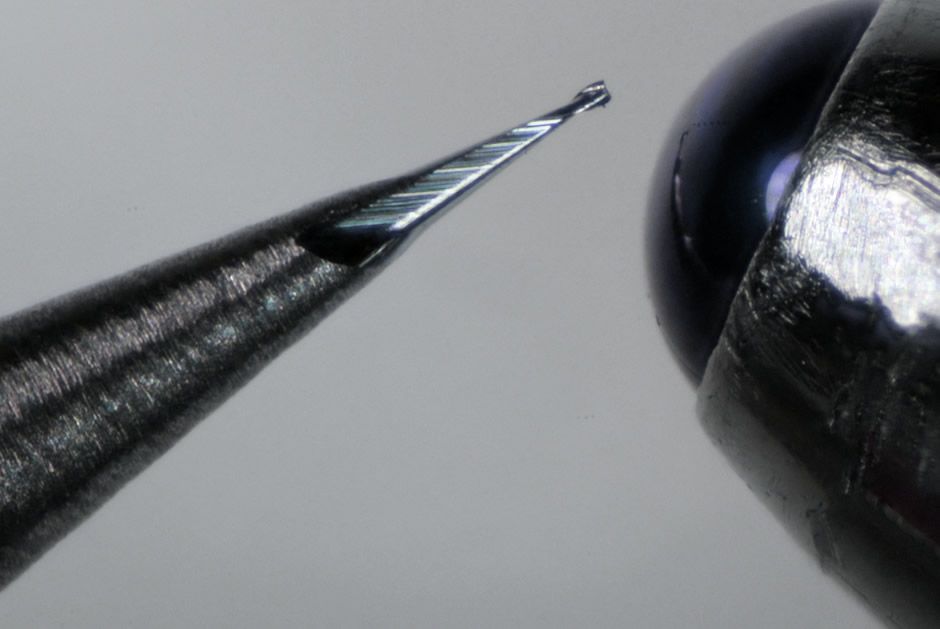
摘要
本文報告了多項材料微尺寸加工中材料微結構對銑刀磨損影響的研究。提出了一種新的通用方法,利用微銑加工對切削刃半徑影響的經驗數據來估計銑刀磨損。實驗獨立研究了鋼材中兩種主要相圖-珠光體和鐵素體在不同切削條件下對銑刀磨損的影響。在此經驗數據的基礎上,建立了兩個回歸模型來估計加工單相鋼和多相鋼時切削刃半徑的增加。為了驗證這些模型,我們將它們應用於預測加工兩種不同多相鋼樣品時的銑刀磨損。結果表明,預估銑刀磨損量與實際的銑刀磨損量之間成正比。
1. 簡介
顯微端面加工是一種被廣泛利用的工藝,可以在微觀尺度上生產複雜的三維特徵,特別是在需要達到嚴格的公差和相對較高的精度時。同時由於工業上對小型化零件的需求越來越大,廣泛的工程材料都可以通過微端銑削加工。與宏觀加工不同,銑刀的刃口半徑與切屑載荷在同一數量級,而兩者與被加工材料的晶粒尺寸相當。因此,在微端銑加工中,必須考慮材料微觀結構對表面粗糙度、切削力和銑刀磨損的影響。在多相材料的情況下,這些尺度效應變得更加明顯,因為它們是由有限數量的相"混合"而成,每一種相都有其獨特的性質,因此在相同的切削條件下具有不同的加工效應。必須對這些影響進行研究,以優化工藝,確定加工窗口、切削條件,從而降低所產生的表面粗糙度,同時延長銑刀壽命。
用於評估任何材料的加工性的主要標準是由此產生的表面粗糙度、切削力和銑刀磨損。此外,銑刀磨損會導致銑刀幾何形狀的變化,特別是切削刃半徑和切削刀具轉角半徑。這可以歸因於微銑中施加的小切屑載荷,導致熱增長和磨損,並因此而顯著增加刀具和工件之間的摩擦。銑刀幾何形狀的這種變化直接影響了表面粗糙度,但刀具磨損最終會影響加工零件的質量和尺寸精度。因此,詳細了解微精加工中的加工機理和銑刀磨損的進展情況,對進一步推進這項技術的發展非常重要。
本文報告在微觀尺度下加工多相材料時建立銑刀磨損模型的新方法,並對其在不同加工條件下的有效性進行了評估。特別是對兩種不同的鋼材-珠光體鋼和鐵素體鋼進行了獨立的實驗,分析了材料對銑刀磨損行為的影響。然後建立經驗模型來評估加工多相樣品時的銑刀磨損情況。
本文首先回顧微加工的現狀,特別是影響銑刀磨損的因素。然後介紹進行加工試驗的實驗設置和實驗設計。接著介紹並討論實驗結果,討論材料對銑刀磨損的影響的重要性。隨後,對建立的兩個回歸模型及其實驗驗證進行了詳述。最後,對提出的方法在加工多相鋼工件時預測銑刀磨損的有效性做出結論。
2. 文獻審查
2.1材料微觀結構影響
僅用運動學參數不能完全解釋微尺度加工中的切削機理。還有其他因素影響會決定基本的切削機理,如與工件材料有關的因素,特別是其異質性、應變硬化、彈性恢復和尺寸效應等。
許多研究者研究材料微結構在微加工過程中的影響。 Furukawa和Moronuki報告了多晶、單晶和非晶材料以及脆性和韌性材料的不同切削機理。有人提出,通過將未變形的切屑厚度增加到給定材料平均晶粒尺寸的10倍,就有可能避免材料微觀結構的負面結晶效應。
Weule等人研究了SAE 1045鋼在精密飛切過程中材料微觀結構的影響。為了使切削銑刀能良好反應到工件上,加工後的材料只有一個相位階段,或者使其微觀組織均勻化,以減小材料的晶粒直徑與切削刃半徑相比。因此,建議在工件微加工前對其進行預熱處理,以使其均勻化。同時,建議採用相對較大的進給率,以提高表面完整性。
Vogler等對單相鐵氧體和珠光體,以及多相鐵進行了一系列的全槽端銑試驗,用兩刃硬質合金端銑進行加工。在加工純鐵氧體和純珠光體時都觀察到了低頻切削力。同時,在加工多相鐵時出現了高頻力,這是由於工件微觀結構的不均勻性造成的,由於這種切削條件的改變,導致震動增加,出現了高度破碎的切屑。
Uhlmann等研究對不同W和Cu比例的燒結鎢銅(WCu)複合材料進行微粉磨的實驗研究,其微觀結構如圖1所示。觀察到表面質量與材料微觀結構的均勻性有很大關係。
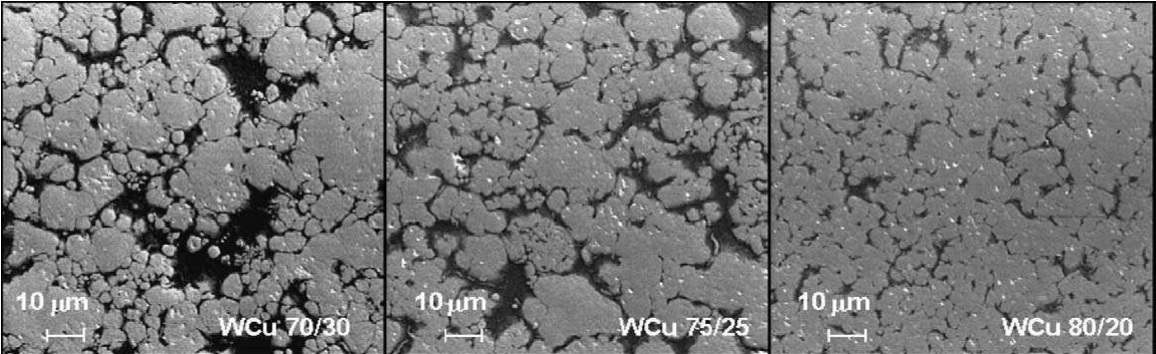
許多研究者研究材料微結構在微加工過程中的影響。 Furukawa和Moronuki報告了多晶、單晶和非晶材料以及脆性和韌性材料的不同切削機理。有人提出,通過將未變形的切屑厚度增加到給定材料平均晶粒尺寸的10倍,就有可能避免材料微觀結構的負面結晶效應。
Weule等人研究了SAE 1045鋼在精密飛切過程中材料微觀結構的影響。為了使切削銑刀能良好反應到工件上,加工後的材料只有一個相位階段,或者使其微觀組織均勻化,以減小材料的晶粒直徑與切削刃半徑相比。因此,建議在工件微加工前對其進行預熱處理,以使其均勻化。同時,建議採用相對較大的進給率,以提高表面完整性。
Vogler等對單相鐵氧體和珠光體,以及多相鐵進行了一系列的全槽端銑試驗,用兩刃硬質合金端銑進行加工。在加工純鐵氧體和純珠光體時都觀察到了低頻切削力。同時,在加工多相鐵時出現了高頻力,這是由於工件微觀結構的不均勻性造成的,由於這種切削條件的改變,導致震動增加,出現了高度破碎的切屑。
Uhlmann等研究對不同W和Cu比例的燒結鎢銅(WCu)複合材料進行微粉磨的實驗研究,其微觀結構如圖1所示。觀察到表面質量與材料微觀結構的均勻性有很大關係。
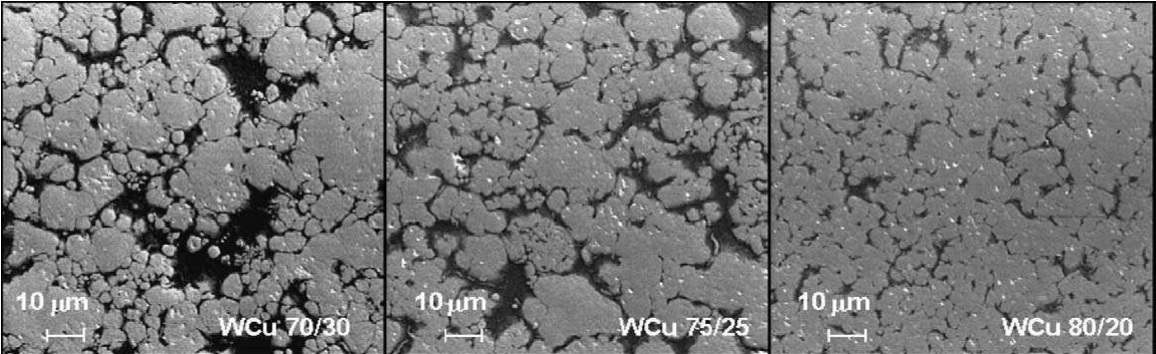
圖1:WCu的微觀結構
Popov等人研究了機械和冶金改良的Al 5083合金在銑削微型零件中的薄型特徵時的加工成果。研究顯示,通過對材料微觀結構的細化,可以顯著提高加工後微特徵的表面完整性。例如,通過將平均晶粒尺寸從100-200μm降低到0.6μm,加工特徵的表面粗糙度提高了3倍,同時材料也變得更加各向同性。作者認為,微銑加工產生的微特徵的粗糙度高度依賴於材料晶粒尺寸。
Simoneau等人在普通碳鋼的加工表面觀察到了凹凸不平的表面缺陷。他們將這種現象歸類為工件材料的雙相結構和晶界處應變失配的影響,這是由於較軟的晶粒在被有效切削前吸收了能量。
Wang等人研究了多相材料的物理特性與加工條件之間的相互依賴關係。根據作者提出的公式,最小切屑厚度取決於相位階段性的摩擦係數。因此,摩擦係數高的晶粒可以形成切屑,而對於摩擦係數較低的晶粒,只產生少量毛刺或材料只是被壓縮。
Aramcharoen和Mativenga對支配淬硬銑刀微銑過程的關鍵參數進行了統計分析。特別是對主軸轉速、切削深度、未變形切屑厚度與切削刃半徑之比、潤滑/環境條件對表面光潔度、毛刺形成和銑刀磨損等影響進行了實驗研究。結果表明,表面光潔度和銑刀磨損受加工環境的影響很大,但也指出,對於彈性恢復率較低的硬質和均質材料,當未變形切屑厚度小於切削刃半徑時,表面光潔度最好。
Mian等人通過實驗研究多相材料鐵素體/珠光體AISI 1045鋼在微尺度下加工時的可加工性。作者旨在通過研究加工粗顆粒微結構材料所需的切削條件和策略,提高微加工工藝的可行性。作者發現,銑刀刃口半徑和材料晶粒的大小對產生的表面粗糙度有顯著影響。他們還得出結論,應優化這兩個參數以提高表面質量。特別是,如圖2所示,當切屑載荷小於切削刃半徑時,切削銑刀會迅速磨損,進而導致較高的表面粗糙度。此外,為了減少這種雙相材料加工過程中形成的毛刺,作者建議使用大於平均晶粒尺寸的切屑載荷。
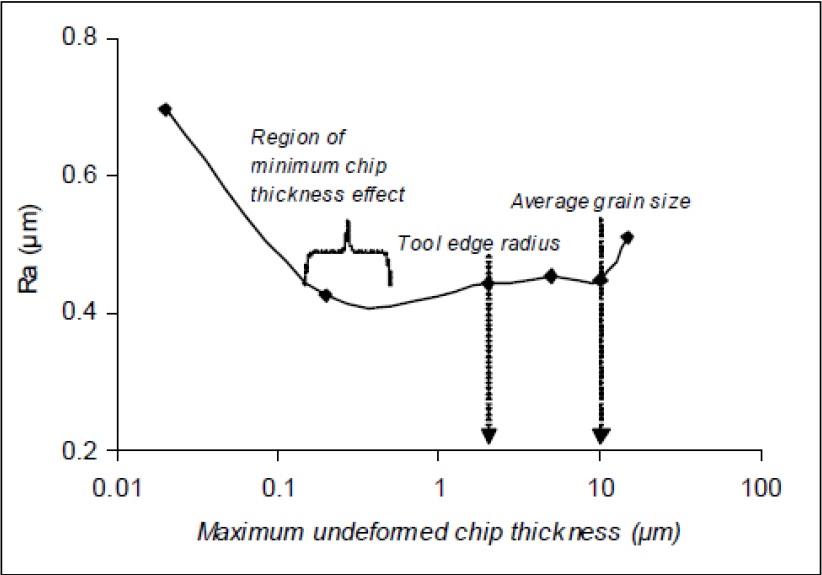
圖2:切削刃半徑對表面粗糙度的影響
在隨後的研究中,Mian等人對兩種不同的鋼件進行了實驗對比研究。一種是以鐵素體鋼為主的AISI 1005,而另一種是平衡良好的鐵素體/珠光體鋼AISI 1045。作者研究了材料微觀結構對一系列切屑載荷下表面光潔度、微觀組織變化、毛刺形成和銑刀磨損的影響。與AISI 1045相比,AISI 1005的加工難度更大。特別是,如圖3a和3b所示,加工AISI 1005時觀察到的毛刺較大。此外,在整個進給率範圍內,在加工表面上發現了更多的毛刺,這與銑刀磨損增加有關。研究顯示,切屑載荷和工件材料對產生的粗糙度都有明顯的影響。然而,表面光潔度對銑刀刃口半徑和切屑載荷比對材料晶粒尺寸更敏感。這反映在兩種材料儘管材料晶粒尺寸不同,但在銑刀刃口半徑附近的切屑載荷下得到的粗糙度值相似。
%20down-milling%20and%20(b)%20up-milling.jpg)
圖3:(a)向下銑削和(b)向上銑削時的毛刺大小
Goo等人進行了微銑試驗,比較了普通聚苯乙烯和碳納米管(CNT)複合聚苯乙烯在大範圍切屑載荷下的切削力、聲射和毛刺形成等方面的加工反應。研究發現,在加工CNT複合聚苯乙烯時,剪切方法更占主導地位,這是因為當普通材料被CNTs強化時,最小切屑厚度減少。
Kota和Ozdoganla研究了粗顆粒鋁的結晶各向異性對不同加工條件下切削力的影響。觀察到在加工不同晶粒尺寸的工件時,切削力發生了顯著的變化,同時也發現平均表面粗糙度取決於特定的晶體取向。具體來說,切削力和表面粗糙度的差異分別可以達到300%和近700%(圖4)。此外,作者還指出,通過增加未切屑厚度和/或降低切削速度,可以降低切削比能量。
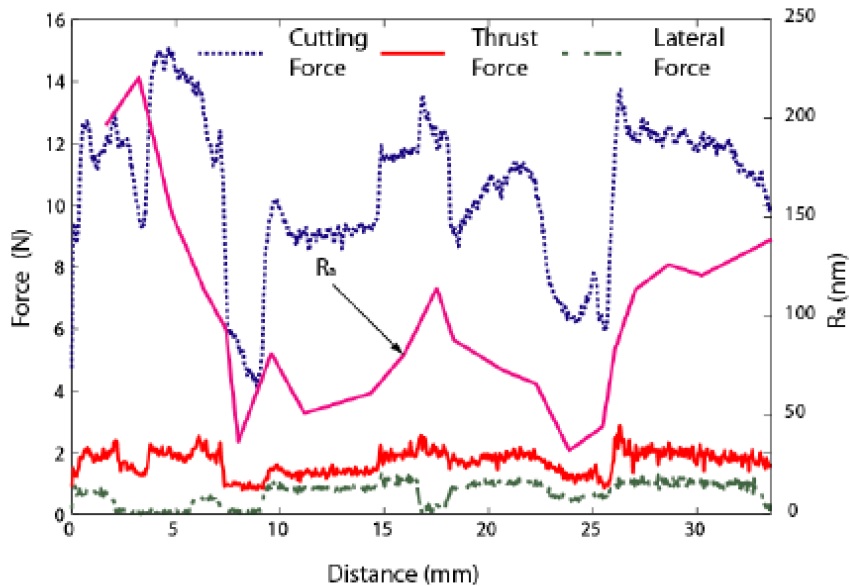
圖4:表面粗糙度和力的變化
所進行的綜述揭示了材料微觀結構是微觀銑削中的一個重要因素,在研究微觀規模加工中的銑刀磨損時,必須考慮這個因素,並建立模型進行預測。
2.2. 切削邊半徑效應
從表面上看,微觀加工和傳統加工在運動學上可以認為是相似的,即它們的材料去除原理。然而,如前所述,微尺度加工和宏觀尺度加工之間存在一些關鍵的差異,這些差異來自於基本物理現象的變化。這些變化主要歸因於尺寸效應,而尺寸效應是微尺度加工中的主導因素。特別是,由於切屑厚度的減小,在尺寸上變得與切削銑刀的切削刃半徑相同,與間歇切削和犁削相關的過渡制度變得更加重要。此外,當切屑厚度低於一個臨界值,稱為最小切屑厚度時,切屑可能不會在每齒切削程中形成;相反,工件材料發生彈性變形。這就導致了較高的切削力、較大的銑刀磨損、微毛刺的形成,繼而影響了表面質量。
最小切屑厚度可以定義為在理想條件下,使用既定切削刃半徑的銑刀從工件表面去除的切屑的最小未變形厚度。在宏觀銑削中,切屑厚度夠大,因此不需要考慮刃口半徑的影響,因此未切削的切屑厚度,而在微觀銑削中變得與銑刀刃口半徑相當。因此,切屑載荷的任何微小變化都會改變加工條件,從正式的切削到犁削甚至磨削,對材料的去除機理產生重大影響。因此,為了消除這種影響,必須在任何加工之前確定最小切屑厚度,從而選擇合適的加工條件。
其他研究者採用分析和實驗的方法研究最小切屑厚度的影響,在此厚度以下既不發生切屑形成,也不發生材料去除。
Ikawa等人通過實驗研究最小切屑厚度效應的意義,通過在電鍍銅的面車過程中採用定義明確的金剛石銑刀,可以形成未變形厚度為納米級的極細切屑,並實現最小切屑厚度為切削刃半徑的1/10。
Kim提出了一個圓邊切削模型來模擬正交加工中的切削力,該模型考慮了切削刃半徑和沿銑刀間隙面的彈性恢復的影響。特別是考慮了工件彈性恢復引起的銑刀間隙面的法向應力和摩擦應力。此外,還研究了圓刃上的摩擦應力和法向應力,以及負耙角對切削幾何的影響。用該模型得到的結果與Lucca等人報告的實驗結果進行了比較,既驗證了該模型,也評估了用該模型比傳統的刃口切削模型更精確地預測切削力的可行性。
Yuan等人對鋁合金金剛石車削中最小切屑厚度對表面的影響進行了實驗研究。結果顯示,使用較大的切削刃半徑導致表面較粗糙,這與最小切屑厚度效應有關。此外,確定最小切屑厚度在切削刃半徑的20-40%範圍內。
另一實驗,Weule等人研究最小切屑厚度對產生的粗糙度影響。用基於激光的地形測量裝置對SAE1045微切削的表面進行了檢測,得到的鋸齒狀輪廓是最小切屑厚度的影響。同時,通過實驗確定最小切屑厚度為銑刀切削刃半徑的0.293。
Kim等人為了研究黃銅微銑中最小切屑厚度對切屑形成過程的影響,進行實驗。實驗採用從0.188μm到6μm的進給率範圍,用635μm直徑的銑刀進行。作者指出,在切屑負荷很小的情況下,切屑可能不會在每次銑刀切削時形成。此外,與其中一次銑刀切削的材料體積相比,形成的切屑體積比預期的要大,這與切削刃半徑和施加的切屑載荷大小相當是可以解釋的。得出的結論是,除非切屑載荷達到一定值,特別是最小切屑厚度,否則不會形成切屑。
Kim等人建立了微銑過程中切屑形成的綜合模型,以評估微加工過程中刀翼面旁的犁削和材料彈性恢復的影響。研究發現,在微銑過程中,由於最小切屑厚度的影響,犁削對切削力的貢獻很大,特別是在每齒進給量較低時。
Vogler等人採用有限元(FE)模型測定了微尺度加工時鋼工件中鐵素體和珠光體相位的最小切屑厚度。採用2~7μm的不同刃口半徑和0.1~3μm的切屑厚度範圍來估計最小切屑厚度與銑刀刃口半徑的比值,發現珠光體和鐵素體的最小切屑厚度分別在0.14~0.25和0.29~0.43之間。
Lai等人研究了無氧高導銅(OFHC)微加工中的尺寸效應。採用考慮材料特性和切削刃半徑的FE模型,模擬微尺度下的正交加工。發現加工銅時,最小切屑厚度為2 μm切削刃半徑的0.25。同時,由於最小切屑厚度效應和累積切屑厚度的影響,在極低進給率下,比切削能量的增加與主導犁削制度得到了解釋。
Biermann和Kahnis還研究了微銑中切削刃半徑的影響。透過耐磨蝕水沖式擴大銑刀的切削刃半徑,從而達到一定範圍的切削刃半徑。研究顯示,使用較大的切削刃半徑會降低表面質量和增加切削力,但同時也會降低銑刀磨耗。此外,研究顯示,在未變形切屑厚度較低的情況下,切削力比和表面粗糙度增加,並且由於犁削作用,毛刺形成量明顯增加。
從所進行的綜述中可以看出,微加工過程對切削刃半徑狀態有很大的依賴性,特別是它的增加會改變加工條件,從切削到犁削/磨削,從而導致更高的切削力和不均勻的表面生成。所以,銑刀磨損量在切削刃半徑方面的進展,顯示微觀尺度的基本切削條件,應進行研究,以便加強認知不同工藝參數對微加工的影響。
最小切屑厚度可以定義為在理想條件下,使用既定切削刃半徑的銑刀從工件表面去除的切屑的最小未變形厚度。在宏觀銑削中,切屑厚度夠大,因此不需要考慮刃口半徑的影響,因此未切削的切屑厚度,而在微觀銑削中變得與銑刀刃口半徑相當。因此,切屑載荷的任何微小變化都會改變加工條件,從正式的切削到犁削甚至磨削,對材料的去除機理產生重大影響。因此,為了消除這種影響,必須在任何加工之前確定最小切屑厚度,從而選擇合適的加工條件。
其他研究者採用分析和實驗的方法研究最小切屑厚度的影響,在此厚度以下既不發生切屑形成,也不發生材料去除。
Ikawa等人通過實驗研究最小切屑厚度效應的意義,通過在電鍍銅的面車過程中採用定義明確的金剛石銑刀,可以形成未變形厚度為納米級的極細切屑,並實現最小切屑厚度為切削刃半徑的1/10。
Kim提出了一個圓邊切削模型來模擬正交加工中的切削力,該模型考慮了切削刃半徑和沿銑刀間隙面的彈性恢復的影響。特別是考慮了工件彈性恢復引起的銑刀間隙面的法向應力和摩擦應力。此外,還研究了圓刃上的摩擦應力和法向應力,以及負耙角對切削幾何的影響。用該模型得到的結果與Lucca等人報告的實驗結果進行了比較,既驗證了該模型,也評估了用該模型比傳統的刃口切削模型更精確地預測切削力的可行性。
Yuan等人對鋁合金金剛石車削中最小切屑厚度對表面的影響進行了實驗研究。結果顯示,使用較大的切削刃半徑導致表面較粗糙,這與最小切屑厚度效應有關。此外,確定最小切屑厚度在切削刃半徑的20-40%範圍內。
另一實驗,Weule等人研究最小切屑厚度對產生的粗糙度影響。用基於激光的地形測量裝置對SAE1045微切削的表面進行了檢測,得到的鋸齒狀輪廓是最小切屑厚度的影響。同時,通過實驗確定最小切屑厚度為銑刀切削刃半徑的0.293。
Kim等人為了研究黃銅微銑中最小切屑厚度對切屑形成過程的影響,進行實驗。實驗採用從0.188μm到6μm的進給率範圍,用635μm直徑的銑刀進行。作者指出,在切屑負荷很小的情況下,切屑可能不會在每次銑刀切削時形成。此外,與其中一次銑刀切削的材料體積相比,形成的切屑體積比預期的要大,這與切削刃半徑和施加的切屑載荷大小相當是可以解釋的。得出的結論是,除非切屑載荷達到一定值,特別是最小切屑厚度,否則不會形成切屑。
Kim等人建立了微銑過程中切屑形成的綜合模型,以評估微加工過程中刀翼面旁的犁削和材料彈性恢復的影響。研究發現,在微銑過程中,由於最小切屑厚度的影響,犁削對切削力的貢獻很大,特別是在每齒進給量較低時。
Vogler等人採用有限元(FE)模型測定了微尺度加工時鋼工件中鐵素體和珠光體相位的最小切屑厚度。採用2~7μm的不同刃口半徑和0.1~3μm的切屑厚度範圍來估計最小切屑厚度與銑刀刃口半徑的比值,發現珠光體和鐵素體的最小切屑厚度分別在0.14~0.25和0.29~0.43之間。
Lai等人研究了無氧高導銅(OFHC)微加工中的尺寸效應。採用考慮材料特性和切削刃半徑的FE模型,模擬微尺度下的正交加工。發現加工銅時,最小切屑厚度為2 μm切削刃半徑的0.25。同時,由於最小切屑厚度效應和累積切屑厚度的影響,在極低進給率下,比切削能量的增加與主導犁削制度得到了解釋。
Biermann和Kahnis還研究了微銑中切削刃半徑的影響。透過耐磨蝕水沖式擴大銑刀的切削刃半徑,從而達到一定範圍的切削刃半徑。研究顯示,使用較大的切削刃半徑會降低表面質量和增加切削力,但同時也會降低銑刀磨耗。此外,研究顯示,在未變形切屑厚度較低的情況下,切削力比和表面粗糙度增加,並且由於犁削作用,毛刺形成量明顯增加。
從所進行的綜述中可以看出,微加工過程對切削刃半徑狀態有很大的依賴性,特別是它的增加會改變加工條件,從切削到犁削/磨削,從而導致更高的切削力和不均勻的表面生成。所以,銑刀磨損量在切削刃半徑方面的進展,顯示微觀尺度的基本切削條件,應進行研究,以便加強認知不同工藝參數對微加工的影響。
2.3. 微加工中的銑刀磨損
銑刀磨損的研究多在宏觀尺度上進行,僅有少數針對微觀尺度加工的研究。這是由於現有檢測方法的局限性和經驗審查的困難。
Tansel等人實驗研究在軟材料和極硬工件,特別是鋁和鋼的加工過程中,微銑加工中銑刀磨損(使用量)和切削力之間的關係。採用反向傳播型人工神經網絡(ANN)建立模型來評估銑刀磨損,而不是檢測作者在先前研究中所調查的預失效階段。作者得出的結論是,在鋁的情況下,切削力的變化隨著銑刀的使用成比例的增加,這是因為切削刀具的形狀在切削中發生了變化;切削刃逐漸失去了其鋒利性和有效性。ANN模型能夠識別出軟材料加工過程中銑刀磨損和切削力之間的依賴關係。然而,在加工鋼(NAK 55)工件時,銑刀磨損與切削力之間的關係與鋁的響應有很大的不同。因此,所提出的ANN只能用於識別加工NAK 55工件時的預失效階段。
Bao和Tansel透過衡量銑刀同時旋轉和前進時切削刃軌跡對切屑厚度的影響,建立了微銑削中切削力的模型。所提出的模型比Tlusty和Macneil提出的宏觀尺度模型更精確地預測了切削力,特別是當每齒進給量與銑刀半徑之比大於0.1時。然而,這只是第一次測試,之後還開發了更全面的模型,以考慮銑刀跳動和銑刀磨損的影響,可用於在線監測切削刀具的狀況。
Malekian等人透過實驗研究微端銑中切削條件對銑刀磨損的影響,並提出了一種監測方法,該方法依賴於採用加速度計、力和聲發射傳感器獲得的感覺數據。採用神經模糊法將這些數據結合起來,研究銑刀的狀態,特別是確定銑刀是否有足夠的鋒利度可以繼續正常加工。為了驗證所提出的監測方法,使用直徑500μm的平面微端銑刀進行切削試驗,同時使用光學顯微鏡檢查切削刀具的轉角半徑。據作者介紹,所提出的方法可用於在線監測微端銑刀的狀況,從而在銑刀達到故障前狀態時發出警告。但要強調的是,在本研究中僅監測了銑刀轉角半徑的狀況,以估計銑刀的磨損情況,而沒有監測切削刃半徑,因為切削刃半徑對表面光潔度和切削力影響較大。
Lia等人提出了一種回歸模型來評估銑刀磨損。銑刀半徑的平均減小量作為材料去除量和切削速度的函數來判斷銑刀狀態。由於測量微小徑銑刀困難,測量加工區的寬度來間接判斷銑刀磨損。本研究採用銑刀磨損的回歸模型對基於加工軌跡的表面生成模型進行標定,從而預測其對表面粗糙度變化的影響。研究表明,銑刀磨損對所得表面粗糙度的影響是顯著的;對於某些工況,粗糙度隨著銑刀磨損的增加而增加數倍,因此在建立微端面加工影響模型時,應考慮銑刀磨損對加工表面的影響。但是,本研究沒有考慮由於磨損而引起的銑刀幾何形狀變化的影響,如切削刃半徑的增大。
Jun等人透過實驗研究應用不同進給率的切削和犁削加工條件對銑刀磨損的影響。同時,作者還引入了一個新的參數來量化微端銑過程中的銑刀磨損。特別是將切削刃半徑的增加,表示為Δre,定義為一個新的磨損參數,採用以下公式計算。

Tansel等人實驗研究在軟材料和極硬工件,特別是鋁和鋼的加工過程中,微銑加工中銑刀磨損(使用量)和切削力之間的關係。採用反向傳播型人工神經網絡(ANN)建立模型來評估銑刀磨損,而不是檢測作者在先前研究中所調查的預失效階段。作者得出的結論是,在鋁的情況下,切削力的變化隨著銑刀的使用成比例的增加,這是因為切削刀具的形狀在切削中發生了變化;切削刃逐漸失去了其鋒利性和有效性。ANN模型能夠識別出軟材料加工過程中銑刀磨損和切削力之間的依賴關係。然而,在加工鋼(NAK 55)工件時,銑刀磨損與切削力之間的關係與鋁的響應有很大的不同。因此,所提出的ANN只能用於識別加工NAK 55工件時的預失效階段。
Bao和Tansel透過衡量銑刀同時旋轉和前進時切削刃軌跡對切屑厚度的影響,建立了微銑削中切削力的模型。所提出的模型比Tlusty和Macneil提出的宏觀尺度模型更精確地預測了切削力,特別是當每齒進給量與銑刀半徑之比大於0.1時。然而,這只是第一次測試,之後還開發了更全面的模型,以考慮銑刀跳動和銑刀磨損的影響,可用於在線監測切削刀具的狀況。
Malekian等人透過實驗研究微端銑中切削條件對銑刀磨損的影響,並提出了一種監測方法,該方法依賴於採用加速度計、力和聲發射傳感器獲得的感覺數據。採用神經模糊法將這些數據結合起來,研究銑刀的狀態,特別是確定銑刀是否有足夠的鋒利度可以繼續正常加工。為了驗證所提出的監測方法,使用直徑500μm的平面微端銑刀進行切削試驗,同時使用光學顯微鏡檢查切削刀具的轉角半徑。據作者介紹,所提出的方法可用於在線監測微端銑刀的狀況,從而在銑刀達到故障前狀態時發出警告。但要強調的是,在本研究中僅監測了銑刀轉角半徑的狀況,以估計銑刀的磨損情況,而沒有監測切削刃半徑,因為切削刃半徑對表面光潔度和切削力影響較大。
Lia等人提出了一種回歸模型來評估銑刀磨損。銑刀半徑的平均減小量作為材料去除量和切削速度的函數來判斷銑刀狀態。由於測量微小徑銑刀困難,測量加工區的寬度來間接判斷銑刀磨損。本研究採用銑刀磨損的回歸模型對基於加工軌跡的表面生成模型進行標定,從而預測其對表面粗糙度變化的影響。研究表明,銑刀磨損對所得表面粗糙度的影響是顯著的;對於某些工況,粗糙度隨著銑刀磨損的增加而增加數倍,因此在建立微端面加工影響模型時,應考慮銑刀磨損對加工表面的影響。但是,本研究沒有考慮由於磨損而引起的銑刀幾何形狀變化的影響,如切削刃半徑的增大。
Jun等人透過實驗研究應用不同進給率的切削和犁削加工條件對銑刀磨損的影響。同時,作者還引入了一個新的參數來量化微端銑過程中的銑刀磨損。特別是將切削刃半徑的增加,表示為Δre,定義為一個新的磨損參數,採用以下公式計算。

其中re1和re2分别為第一和第二槽的切削刃半径,而下標w或n則表示磨損的銑刀和新的銑刀。
確定應用進給率和磨損機制之間的依賴性,通過改變進給率可以避免"環狀切削"磨損的增加和最小切屑厚度效應。作者強調,透過選擇適當的加工方法,可以保持有利的加工條件。特別是在不增加切削刃半徑的情況下,可以保持最小切屑厚度以上的正常切削,銑刀磨損以平坦為主。但值得注意的是,銑刀磨損參數只在加工試驗前後進行了評估。
儘管在該領域發表的文章數量有限,但可以得出結論:微精加工中的銑刀磨損是影響加工性能的重要因素,同時也是一個具有挑戰性的研究問題,需要解決。特別是透過了解切削條件對銑刀磨損機理的影響,可以提高加工性能。此外,為了進行這樣的研究,有必要尋找新的方法,如實驗設置,來表徵和監測銑刀磨損。
3. 實驗設置和實驗設計
本節介紹了用於研究微端銑削過程中銑刀磨損的實驗設置。特別概述了在試驗中遵循的基本程序,並解釋了試驗中使用的材料、銑刀和切削參數的原理。
之所以選擇切削刃半徑和刀槽輪廓的變化來量化銑刀磨損,是因為它們在模擬微端銑削過程和預測由此產生的表面粗糙度方面具有較高的重要性。為了研究這兩個銑刀參數對機床的影響,設計並實現了一種新的實驗裝置,如圖5所示。它可以使試驗過程中保持切削條件不變,因為不需要拆下銑刀進行離線檢查。
實驗研究微端銑削中銑刀磨損的程序包括以下步驟。首先,在去除一定體積的材料後,使用Delta GT-7810A超聲波清洗機對銑刀進行清洗,時間為30秒。然後,使用Blum NANO激光系統,P87.0634,測量不同高度的銑刀公稱直徑,從而判斷每次試驗後的銑刀原型。接著,採用500X光學放大倍率的Dino-lite數字顯微鏡對銑刀底部進行成像,如圖5所示。為了檢查三個刀槽的切削刃半徑,採用Dino-Capture 2.0軟件的測量功能,如圖6所示。此外,使用Keyence VHX-2000數字顯微鏡對Dino-lite顯微鏡的測量結果進行驗證,從而判斷其在微觀尺度上準確評價銑刀磨損進展的能力。
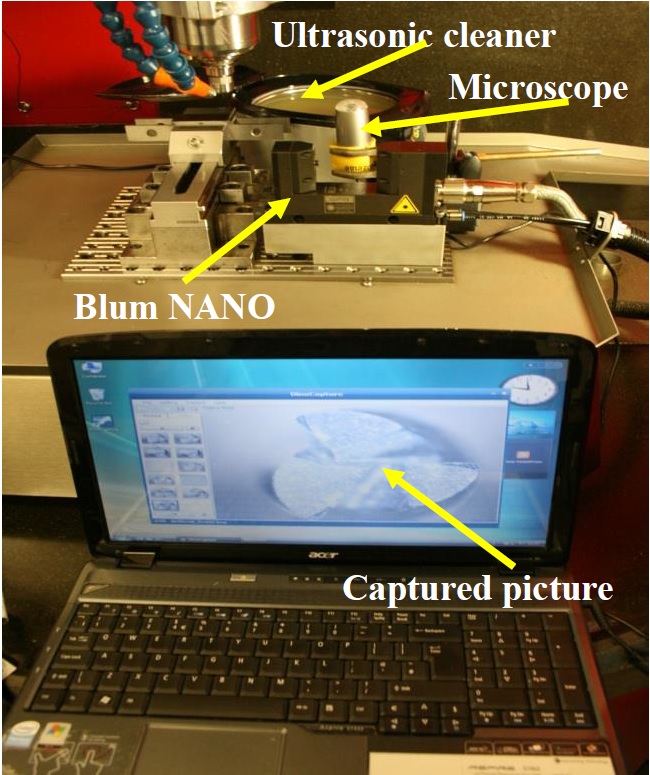
圖5:實驗設置
為了研究材料微觀結構對銑刀磨損演化的影響,由於SAE 01高碳鋼(0.85-1.05%C)和SAE 101低碳鋼(0.08-0.13%C)分別具有純珠光體和純鐵素體的微觀結構,因此本研究的第一部分採用了兩種不同的材料。在不同的切削條件下,通過實驗研究了各相對銑刀磨損行為的影響。特別是通過在微加工中心Kern HSPC 2216上進行開槽試驗,研究了銑刀磨損方面的可加工性。在這些加工試驗中,利用了塗有TiAlN的細顆粒碳化鎢800μm直徑端銑刀。在進行切削試驗之前,使用光學顯微鏡對每個銑刀進行成像,從而測量切削刃的半徑,如圖7所示。對於試驗中使用的銑刀,它們的範圍是2~5μm。通過改變每齒的進給率來控制未變形的切屑厚度,從而達到平均切削刃半徑附近的數值,以獲得預期的最佳表面粗糙度,特別是應用了4和8μm/齒的進給率。試驗中使用的其他切削參數有兩級切削速度,分別為20000和5000轉/分,分別相當於50和12.5米/分鐘,還有一個軸向切削深度,即30μm。
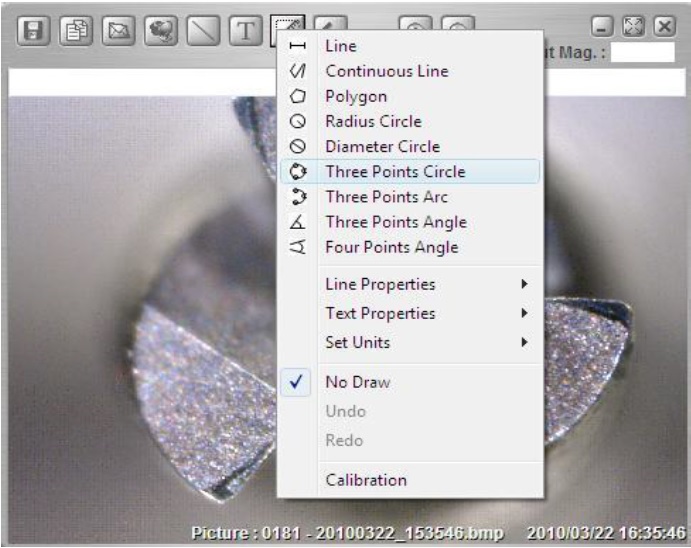
圖6:Dino-Capture 2.0軟件的測量功能
%20a%20new%20tool%2C%20(b)%20a%20worn%20tool%20and%20(c)%20and%20(d)%20severely%20worn%20tools%3B%20where%2C%20r%20denotes%20radius%2C%20C%20is%20the%20circumference%20and%20A%20is%20area.jpg)
圖7:微切削中銑刀磨損的演變(a)新銑刀,(b)磨損的銑刀,(c)和(d)嚴重磨損的銑刀;其中,r表示半徑,C表示圓周,A表示面積
4. 結果和討論
4.1 測量不確定度
銑刀磨損測量是手動進行的,因此在進行測量時存在一定的不確定性。因此,使用軟件允許的最大放大倍數來檢查銑刀,從而將測量的不確定性降到最低。此外,測量是在去除材料的相對較大的增量後進行的,因此可以清楚地看到銑刀磨損的進展情況。然而,仍然有必要評估與用於檢測切削刃半徑的程序相關的測量不確定度,”re”。所有的測量都是以相同的放大倍數進行的,因此假設所有測量中檢測半徑的不確定度來源是相同的。因此,用於計算標準不確定度u的公式是:
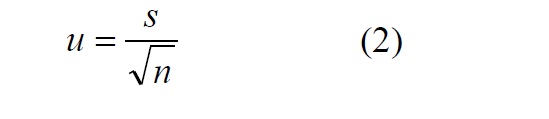
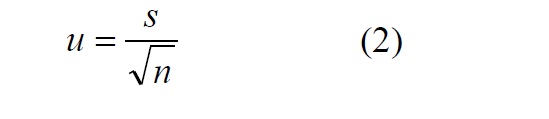
其中s是估計的標準差,n是集合中的測量次數。
為了進行這一評估,對三個不同的切削刃半徑分別進行了五次測量:兩個極端,最低值和最高值,中間為平均值。圖8顯示了測量結果。對於平均值為2.00μm、10.65μm和20.41μm的切削半徑,估計的標準偏差s分別為0.265μm、0.158μm和0.112μm,而標準測量不確定度分別為0.12μm、0.07μm和0.05μm。正如預期的那樣,測量不確定度取決於半徑標稱尺寸。它被確定為最大的測量不確定度是0.12μm,對於2μm的切削刃半徑,普遍認為是本研究可以接受的。因此,對於每個切削刃,所有的測量都進行了五次,並在使用改編後的公式1計算三個切削刃的邊緣半徑的增加,Δre之前使用平均值換算。
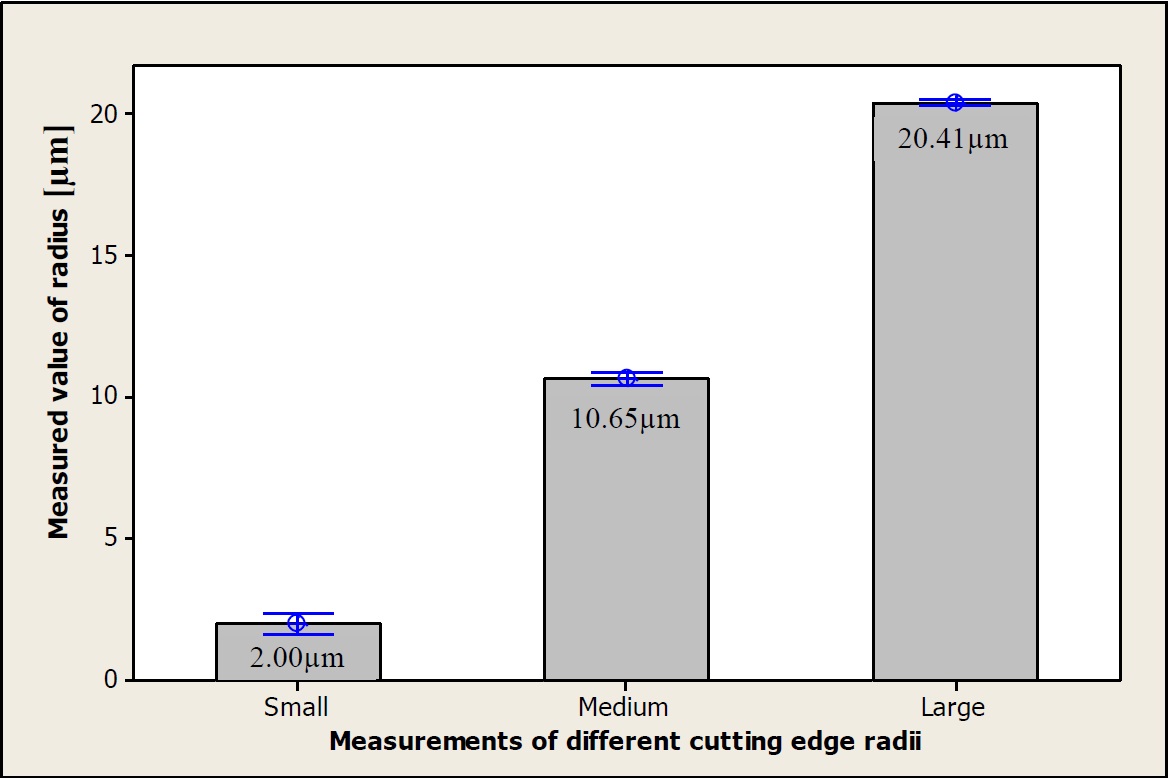
圖8:在三種不同的切削刃半徑下進行的五次測量結果
4.2 銑刀磨損
用顯微鏡拍攝的圖像被用來評估去除一定體積的材料後,切削刃半徑的磨損情況。圖9和圖10分別顯示了珠光體和鐵氧體樣品的邊緣半徑隨歸一化材料去除量MRn(去除量除以切削深度)的增加而變化的情況。
對於珠光體,當應用切削速度Vc和進給率Fz的最低設置時,銑刀表現出最高的磨損,而在最高設置時測得的磨損最低,如圖9所示。值得強調的是,銑刀磨損與施加的進給率和速度之間的關係與宏觀加工中的關係相反,但與Filiz等人報告的結果一致,這種低進給率下銑刀磨損的增加可以歸因於在加工過程中占主導地位的犁削制度。特別是,珠光體在這種設置下的加工響應受到其較大的彈性恢復的影響,導致銑刀上施加的力較大,因而由於銑刀與工件之間的摩擦力較大,磨損較大。由於銑刀/工件的嚙合時間較長,在低切削速度下,最小切屑厚度效應變得顯著。此外,不難看出,銑刀的磨損,特別是Δre,高度依賴於所使用的切削速度。
與鐵素體相反,見圖10,當對切削速度和進給率進行不同設置時,Δre僅有很小的變化。但是,銑刀磨損隨材料去除量的增加而線性增加的現象更為明顯。鐵素體在犁削制度下的回彈率比珠光體低,但儘管如此,在相同的切削條件下,仍觀察到較高的銑刀磨損。這種現象可以用這兩種相位的機械性能差異來解釋。鐵素體相位的特點是具有較高的韌性,特別是當合金中含有少量的錳時,這有助於材料在銑刀上的"加工累積"。因此,與珠光體在相同條件下的反應相比,犁削可能是主要的加工機制,而不是切削。這種機制占主導地位,並導致銑刀邊緣施加更高的切削力,因此銑刀的磨損更嚴重。同時,珠光體更"脆",容易產生較低的最小切屑厚度、較短的切屑形成時間和有利的銑刀邊緣冷卻條件。
%20workpiece.jpg)
對於珠光體,當應用切削速度Vc和進給率Fz的最低設置時,銑刀表現出最高的磨損,而在最高設置時測得的磨損最低,如圖9所示。值得強調的是,銑刀磨損與施加的進給率和速度之間的關係與宏觀加工中的關係相反,但與Filiz等人報告的結果一致,這種低進給率下銑刀磨損的增加可以歸因於在加工過程中占主導地位的犁削制度。特別是,珠光體在這種設置下的加工響應受到其較大的彈性恢復的影響,導致銑刀上施加的力較大,因而由於銑刀與工件之間的摩擦力較大,磨損較大。由於銑刀/工件的嚙合時間較長,在低切削速度下,最小切屑厚度效應變得顯著。此外,不難看出,銑刀的磨損,特別是Δre,高度依賴於所使用的切削速度。
與鐵素體相反,見圖10,當對切削速度和進給率進行不同設置時,Δre僅有很小的變化。但是,銑刀磨損隨材料去除量的增加而線性增加的現象更為明顯。鐵素體在犁削制度下的回彈率比珠光體低,但儘管如此,在相同的切削條件下,仍觀察到較高的銑刀磨損。這種現象可以用這兩種相位的機械性能差異來解釋。鐵素體相位的特點是具有較高的韌性,特別是當合金中含有少量的錳時,這有助於材料在銑刀上的"加工累積"。因此,與珠光體在相同條件下的反應相比,犁削可能是主要的加工機制,而不是切削。這種機制占主導地位,並導致銑刀邊緣施加更高的切削力,因此銑刀的磨損更嚴重。同時,珠光體更"脆",容易產生較低的最小切屑厚度、較短的切屑形成時間和有利的銑刀邊緣冷卻條件。
%20workpiece.jpg)
圖9:珠光體(SAE 01)工件切削刃半徑的平均增加量
%20workpiece.jpg)
圖10:鐵素體(SAE 101)工件切削刃半徑的平均增加量
測量不同高度下的標稱銑刀半徑,圖11和圖12分別提供了珠光體和鐵素體的典型打印實例。黑色箭頭表示由於銑刀磨損導致公稱銑刀半徑減小。影響這些測量結果的因素有銑刀跑偏和震動,加工過程中的熱伸長,也有一些切屑由於清潔時間不夠而未去除。因此,這可以解釋其實際尺寸和名義上尺寸之間的差異,作為半徑為400μm的新銑刀。如製造商所述,用於進行這些測量的Blum NANO激光系統的重複性被認為是±1μm。
在相同的切削條件下,比較在珠光體和鐵氧體工件上獲得的結果,如圖11所示,與鐵氧體的結果相比,圖12所示,在加工珠光體時,銑刀的公稱半徑磨損較小。特別是,珠光體和鐵氧體工件的公稱銑刀直徑分別減少了12μm和28μm。這些結果與另一個磨損參數--切削刃半徑一致,與鐵素體相比,珠光體的加工表現出較少的磨損。同樣,這種現象可以歸因於這兩種相的機械性能,如前所述。
.jpg)
圖11:珠光體不同高度的銑刀半徑測量(SAE 01)
.jpg)
圖12:鐵氧體(SAE 101)在不同高度下的銑刀半徑測量
5. 基於回歸的建模
.
ANNs被認為是一種比基於回歸模型更好的工具磨損建模方法。然而,為了創建此種ANNs,需要大量的數據集來訓練和測試模型。這是一個主要的限制因素,因為需要相對較多的昂貴的切削銑刀,通常每個加工實驗設置都需要一個切削銑刀。所以,在這項研究中,實驗只在每種材料的兩種切削速度、兩種進給率和七種去除率下進行。嘗試使用70%到100%的可用經驗數據來訓練ANN,然而由於數據集相對較小,模型在訓練和測試階段的表現都很差。因此,在本實驗研究中選擇了回歸建模的方法來研究加工多相材料時切削刃半徑的增加。
採用兩個回歸模型來分析珠光體和鐵素體的銑刀磨損量Δre,p和Δre,f分別是切削速度、Vc、每齒進給率Fz和歸一化材料去除量MRn的函數,根據加工SAE 01和SAE 1010樣品得到的實驗數據,採用Minitab 15軟件生成模型。
對於珠光體,考慮到圖9中觀察到的銑刀磨損趨勢,採用指數模型,即公式3,以達到最佳擬合效果。

ANNs被認為是一種比基於回歸模型更好的工具磨損建模方法。然而,為了創建此種ANNs,需要大量的數據集來訓練和測試模型。這是一個主要的限制因素,因為需要相對較多的昂貴的切削銑刀,通常每個加工實驗設置都需要一個切削銑刀。所以,在這項研究中,實驗只在每種材料的兩種切削速度、兩種進給率和七種去除率下進行。嘗試使用70%到100%的可用經驗數據來訓練ANN,然而由於數據集相對較小,模型在訓練和測試階段的表現都很差。因此,在本實驗研究中選擇了回歸建模的方法來研究加工多相材料時切削刃半徑的增加。
採用兩個回歸模型來分析珠光體和鐵素體的銑刀磨損量Δre,p和Δre,f分別是切削速度、Vc、每齒進給率Fz和歸一化材料去除量MRn的函數,根據加工SAE 01和SAE 1010樣品得到的實驗數據,採用Minitab 15軟件生成模型。
對於珠光體,考慮到圖9中觀察到的銑刀磨損趨勢,採用指數模型,即公式3,以達到最佳擬合效果。

然後,應用對數變換將式3轉換為式4所示的線性分析形式。

應用最小二乘法估計技術計算係數,從而建立一個回歸模型來估計微尺度加工珠光體鋼時的銑刀磨損。
對於鐵素體,由於銑刀磨損趨勢非常接近線性,見圖10,因此採用了線性回歸模型。再一次採用最小二乘法估計技術來確定係數,從而建立擬議的回歸模型。
為珠光體和鐵素體相建立的模型分別在式5和式6中得出。

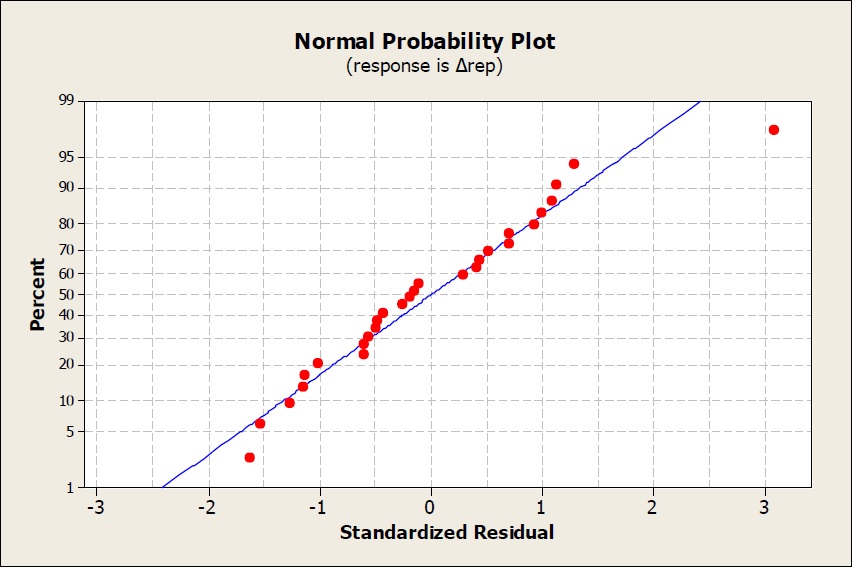
圖13:珠光體磨損模型的正態概率圖
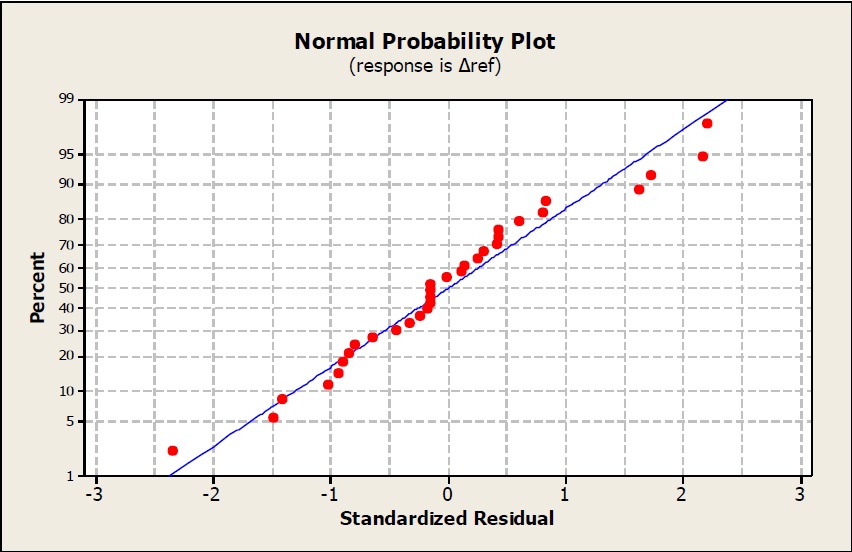
圖14:鐵氧體磨損模型的正態概率圖
根據得到的兩個模型的確定係數R-Sq,珠光體和鐵素體的平均磨損量Δre,p和Δre,f的預測精度分別在91.2%和97.0%以內。另外,圖13和圖14所示的珠光體和鐵素體模型的正態概率圖表明,在分析中將影響銑刀磨損的大部分因素納入考量。
6. 實驗驗證
第二系列實驗的目的是證明所提出的方法的有效性,並驗證所開發的回歸模型。在不同的條件下對所提出的模型進行了評估,並將銑刀磨損的預測值與測量結果進行了比較。所提出的模型用於評估加工兩種不同的雙相鋼樣品時的銑刀磨損,即AISI 1040(0.37-0.44%C)和AISI 8620(0.18-0.23%C)碳鋼,其微觀組織中鐵素體和珠光體的比例不同。加工試驗,特別是開槽試驗,採用直徑為800μm的銑刀進行,切削條件與第一組實驗試驗的條件相似,特別是進給率為6μm/齒,切削速度為25m/min,切削深度為30μm。
圖15a和15b分別顯示了AISI 1040和AISI 8620鋼樣的顯微組織。可以清楚地看到兩種相,深色的是珠光體,而明亮的相是鐵素體。對這兩個樣品的顯微照片進行拍攝,以創建其金相顯微結構圖,然後計算其中珠光體和鐵素體的百分比。對於AISI 1040鋼來說,珠光體和鐵素體之間有很好的平衡,分別為48%和52%,而對於AISI 8620樣品來說,鐵素體相占主導地位,為68%。在相同的切削條件下,與AISI 1040樣品相比,鐵素體含量較高,其最小切屑厚度高於珠光體,預計銑削中會使用更多的犁削而不是切削。由於銑刀與工件之間的摩擦力顯著增加,這種犁削機制增加了施加在切削刃上的力,進而導致溫度升高,磨損加劇。
%20AISI%201040%20and%20(b)%20AISI%208620%20steels.jpg)
圖15:(a)AISI 1040和(b)AISI 8620鋼的光學顯微結構圖
根據這些數據,可以解釋這兩個不同相的影響,並使用公式4和公式5來估計銑刀磨損。同樣的方法也可以應用於其他多相材料。特別是,雙相材料的銑刀磨損模型可以定義為:

其中:Δre為雙相材料的銑刀磨損量;Δre,p和Δre,f分別為珠光體和鐵素體的銑刀磨損量;Rp和Rf為這兩相在雙相材料中的百分比。
圖16顯示了在加工直徑為800μm的AISI 1040工件時,採用25m/min的切削速度,每齒6μm的進給率和30μm的切削深度,所表現出的預測和實際銑刀磨損的比較。實驗結果與預測磨損的線性趨勢線不同,實驗結果具有非線性趨勢線;估計的銑刀磨損與實際磨損的差異平均為14.7%。
圖17是在與AISI 1040相同的切削條件下加工AISI 8620樣品時的預測和實驗結果的比較。從該圖可以看出,其趨勢與加工AISI 1040鋼時觀察到的趨勢相似(圖16)。同樣,預測結果和實驗結果之間也有差異,但同樣比較低,在16.4%以內。因此,可以得出結論,這些結果支持使用所提出的方法和創建的模型來預測加工雙相鋼時的銑刀磨損。
研究兩種材料的實驗結果(圖16和圖17),不難看出,在相同的切削條件下,AISI 8620工件與AISI 1040工件相比,加工時產生的銑刀磨損較高。這是預料之中的,主要是由於AISI 8620微觀結構中鐵素體的比例較高。此外,模型準確預測了兩種情況下的磨損。因此,可以說材料微觀結構對銑刀磨損的影響是顯著的,考慮到這點,可以建立模型,準確預測加工多相材料時的銑刀磨損。
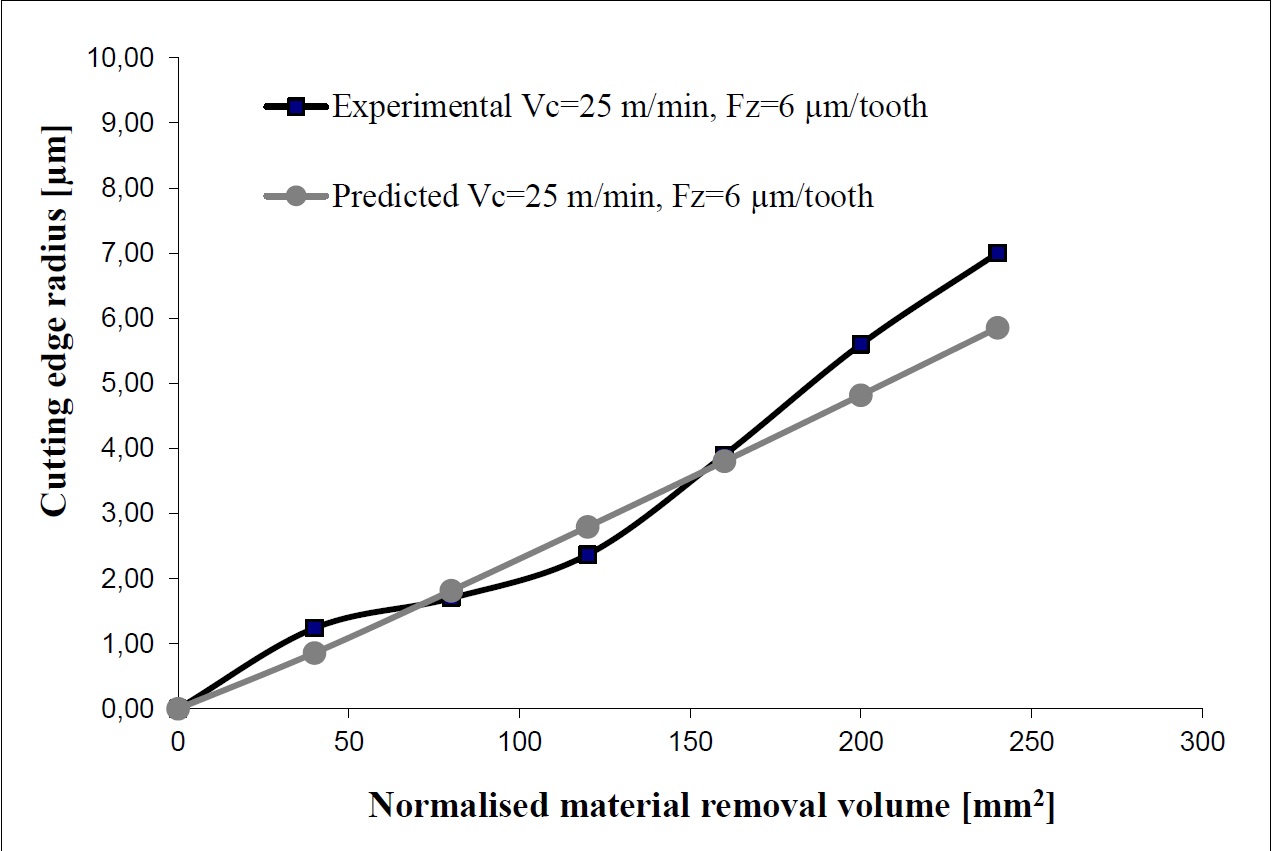
圖16:當使用800μm直徑的銑刀和30μm的切削深度加工AISI 1040工件時,實驗和估計的銑刀磨損比較
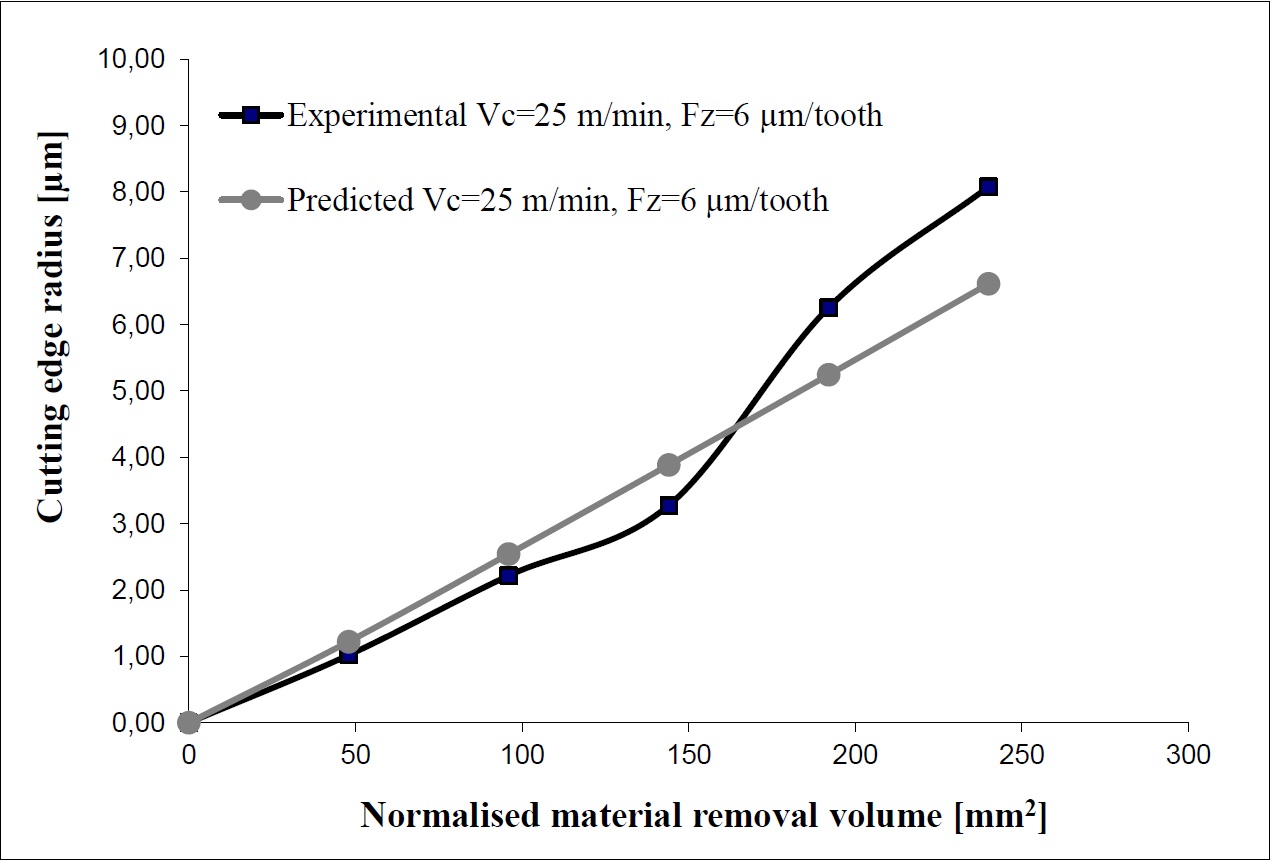
圖17:用直徑800μm的銑刀和30μm的切削深度加工AISI 8620工件時,實驗和估計的銑刀磨損比較
考慮到所有試驗的結果,很明顯,所提出的方法可以用來模擬加工雙相材料時的銑刀磨損行為。可以說,透過增加對珠光體和鐵素體樣品進行的試驗次數,以產生用於創建模型的數據集,可以減少預測和試驗結果之間的差異。此外,銑刀同時與一個以上的相位接觸可能是造成觀察到的差異的另一個原因。
同樣的方法也可以用於預測加工多相材料時的銑刀磨損,特別是透過對其微觀結構中存在的所有相進行類似的實驗試驗,從而模擬它們對銑刀磨損的影響。另外,應該注意的是,以這種方式建立的回歸模型可以很容易地進行改進,以考慮任何新的實驗數據,從而提高其預測能力。值得強調的是,雖然研究了切削刃半徑和名義上銑刀半徑這兩個不同的參數,以量化微尺度加工後的銑刀磨損,但該模型只考慮了前者,並沒有考慮名義上銑刀半徑所得到的結果。
7. 結論
本文研究了微端銑中影響銑刀磨損的各種因素,並對其影響進行了討論。特別關注了材料微結構對銑刀磨損的影響。切削刃半徑和刀槽輪廓的平均值被用來評估銑刀磨損。設計並實施了一個新的實驗裝置來確定這兩個銑刀參數,然後在珠光體鋼和鐵素體鋼上進行了一系列實驗來研究銑刀磨損。此外,還討論了在分析槽型時影響測量不確定度的因素。然後,提出了兩個經驗模型來估計銑刀磨損,特別是切削刃半徑的增加,當各別加工珠光體和鐵素體鋼時。然後,這兩個模型被應用於預測加工主要由這兩種相組成但比例不同的雙相鋼工件時的銑刀磨損。
為了證明這種通用方法的可行性,同時為了驗證模型,在不同的條件下對所提出的方法進行了評估,通過加工兩種不同的雙相鋼樣品,AISI 1040和AISI 8620,使用的銑刀與最初的實驗試驗中使用的銑刀相似。結果顯示,估計的銑刀磨損量與實際的銑刀磨損量有較好的一致性,AISI 1040和AISI 8620的平均誤差分別為14.7%和16.4%。
此外,還可以得出以下結論。
Ø對於珠光體來說,所表現出的磨損過高與應用的進給率和速度之間存在著反比關係。這是由於規模效應造成的,因為結果與宏觀規模加工中的典型結果相反。因此,必須專門針對微尺度加工優化切削參數。
Ø與鐵氧體相反,切削速度和進給率的增加導致切削刃半徑的小幅增加。此外,隨著材料去除量的增加,銑刀磨損的線性增加更為明顯。
Ø在相同的切削條件下,加工鐵素體比加工珠光體時,觀察到較高的銑刀磨損。這種影響可以用這兩種相的機械性能差異來解釋。
Ø在相同的切削條件下,與AISI 1040鋼相比,加工AISI 8620時有較高的銑刀磨損。這主要是由於AISI 8620微觀結構中鐵素體的比例較高。因此,材料中各相的具體加工反應可以用來預測加工多相材料時的銑刀磨損情況。
Ø單相加工實驗的數量有限,造成了預測和實驗結果之間的差異,但這也可以歸因於另外兩個因素。特別是,模型中沒有考慮到評估銑刀磨損時的測量不確定性,也沒有考慮到銑刀同時與一個以上相位的嚙合。
最後,應該指出的是,當有新的實驗數據出現時,應用這種方法建立的銑刀磨損模型可以很容易地更新和完善,從而提高其預測能力。
致謝
此報告的研究得到了FP7項目"微系統製造融合技術(COTECH)"、"小型系列金屬零件高性能生產線(HYPROLINE)"和"多尺度表面結構柔性壓縮注塑平台(IMPRESS)"以及FP7 EUMINAFAB基礎設施計劃的部分資助。
作者要感謝埃及文化局(ECB)為Elkaseer博士提供的資金支持。
Keyence UK和卡迪夫大學機械與製造工程研究所的E.Brousseau博士的支持表示感謝。
相關名詞
Fz, 每齒進給率[μm/齒]
MRn, 歸一化材料清除量,材料清除量/切割深度
n, 每組銑刀磨損測量中的測量次數
re, 銑刀的切削刃半徑
re1, n 新銑刀第一齒槽的切削刃半徑
re1, w 磨損銑刀第一齒槽的切削刃半徑
re2, 新銑刀第二槽的切削刃半徑為n
re2, w磨損銑刀第二槽的切削刃半徑
Rf, 為雙相鋼中鐵素體的百分比
Rp, 為雙相鋼中珠光體的百分比
s, 銑刀磨損測量的估計標準偏差
u, 銑刀磨損測量的標準不確定度
Vc, 切割速度[m/min]
Δ, 雙相鋼的銑刀磨損情況
Δre,f, 鐵素體鋼的銑刀磨損情況
Δre,p, 珠光體鋼的銑刀磨損情況