微型銑削中的銑刀磨損測量協議
2020-05-11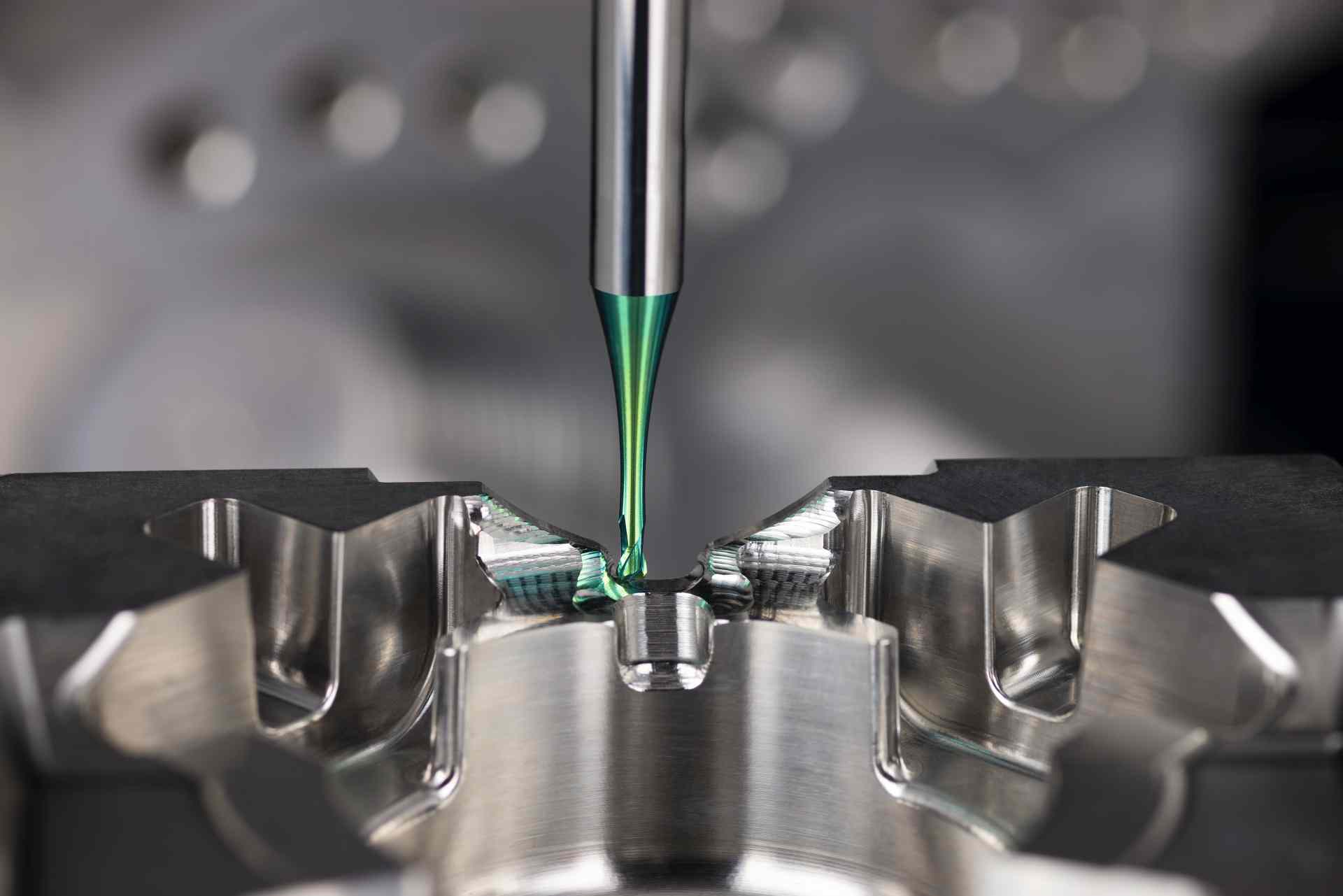
重點
•已開發出用於測量微細銑削中銑刀磨損的新協議。
•協議》考慮了銑刀的側面和耙面的磨損,以提供銑刀磨損的完整情況。
•銑刀已經成功的使用協議進行測量,產生典型的銑刀磨損曲線。
•新協議克服了用標準的微型工具評估宏觀協議時的局限性。
摘要
微型銑削可以快速地生產出小而精密的零件,用於機電、航空航天和醫療領域。由於其尺寸小,微型銑刀的磨損速度快且不可預知,因此銑刀磨損難以測量,而且對銑刀磨損的理解不足,會導致銑刀更換次數過多,生產效率降低。因此,本文提出了一種新的微型銑刀磨損測量協議,以克服這些問題。在ISO標準中找到的一套嚴格的標準對於微銑的研究是不切實際的。這裡的方法允許在不同材料和情況下進行比較,並詳細說明了實現這一目標必須滿足的某些標準。為了評估該協議的微型工具被用來加工三種材料:黃銅,鈦和哈氏合金 ; 銑削磨損產生的磨損曲線。使用所描述的協議,這些磨損曲線可以與大型銑刀的磨損曲線進行類似的分析。對所加工的槽的輪廓分析提供了關於銑刀磨損的寶貴信息,而直接測量是不可能的。這種新的協議提供了一種分析和報告微型端銑刀磨損的新方法,可以在不同的加工條件下和/或銑削不同的材料時進行比較,這是現有的加工標準所不能提供的。這些信息可用於工業應用,延長銑刀壽命並提高加工效率。
切削用語
Xcomp Total sliding distance 總滑動距離
Cing Number of incomplete circles 未完成的圈數
Ccomp Number of complete circles 完成的圈數
Nrev Number of revolutions 轉速
Dcap Engage tool diameter 已嚙合銑刀直徑
Xi Sliding distance of incomplete circle 不完整圓的滑動距離
Fcut Cutting frequency 切削頻率
N Spindle speed 主軸轉速
Zc Number of teeth 切削刃數
Fc Cutting force 切削力
T Cutting time 切削時間
Fz Feed rate 進給
Vc Cutting speed 切削速度
Cing Number of incomplete circles 未完成的圈數
Ccomp Number of complete circles 完成的圈數
Nrev Number of revolutions 轉速
Dcap Engage tool diameter 已嚙合銑刀直徑
Xi Sliding distance of incomplete circle 不完整圓的滑動距離
Fcut Cutting frequency 切削頻率
N Spindle speed 主軸轉速
Zc Number of teeth 切削刃數
Fc Cutting force 切削力
T Cutting time 切削時間
Fz Feed rate 進給
Vc Cutting speed 切削速度
1. 導言
隨著工程設備的日益小型化,微銑加工已經成為製造小型零件的最受歡迎的工藝之一,因為它能夠快速生產出高完整性的零件。它被廣泛應用於醫療和航空領域,以及鐘錶製造、光學和電子、微模製造等小型化機械元件普遍存在的領域。其中一些領域只需要加工銅和黃銅合金等較軟的材料即可。然而,醫療和航空航天工業卻使用鈦和高性能超合金等材料。
這些工具通常難以使用宏觀尺寸的工具進行加工,但在微銑加工中卻更加複雜,因為毛刺和晶體的不規則性會導致工具斷裂。對微型銑刀的磨損研究是非常重要的,因為在此類行業中,達到高質量的表面光潔度是非常重要的,可能是為了美觀,也可能是由於表面光潔度較差的成品(如有活動部件的地方)會影響部件的功能。
此外,銑刀磨損後會導致毛刺增加,導致切削力急劇增加。同時,用傳統的方法很難從微型零件上去除毛刺。針對不同的微銑工況開發出銑刀磨損曲線,可以預測銑刀的壽命,從而使銑刀在保持良好的表面光潔度的同時,能夠最大限度地延長銑刀的使用時間。從而最大限度地提高了生產效率,降低了成本。從歷史上看,關於微型銑刀磨損的研究都是將銑刀磨損與切削距離或切削時間進行對比。測量銑刀相對於工件移動的切削距離或切削時間(即銑刀嚙合時),沒有考慮到不同材料的不同進給速度和速度,不能用於比較不同材料之間的銑刀壽命。因此,用每個齒的滑動距離來衡量銑刀的磨損情況(如本文第3節正式描述)。
此外,在審查的文獻中,對微型銑刀磨損的研究並不一致,因為用於測量銑刀磨損的指標不盡相同:邊緣半徑、側面磨損和銑刀半徑減小是最常見的。為了更好地規範微型銑刀的磨損研究,了解微型銑刀的磨損情況,這裡規定了測量微型銑刀的協議。因此,這裡提出的工作目的是提出一個測量微銑刀磨損的協議,克服了現有方法主要用於宏觀銑刀的問題。
2. 背景和最先進的技術
2.1. 微型銑削
微加工可以被定義為使用具有幾何定義的切削刃的機械工具來製造尺寸在微米級的特徵
。
微加工可以被認為是微加工的一個分支,與所有的微加工一樣,微加工產生的結果與傳統的銑削有很大的不同。這有幾個原因,首先是相對而言,從工件材料的角度看,銑刀會顯得比較鈍。如果切削深度比切削刃半徑小得多,銑刀很可能會沿工件表面磨擦而不是切削,從而使工件表面被燒毀。

微加工可以被認為是微加工的一個分支,與所有的微加工一樣,微加工產生的結果與傳統的銑削有很大的不同。這有幾個原因,首先是相對而言,從工件材料的角度看,銑刀會顯得比較鈍。如果切削深度比切削刃半徑小得多,銑刀很可能會沿工件表面磨擦而不是切削,從而使工件表面被燒毀。
另一個問題是,由於其直徑的原因,即使是微粒度的微銑刀,一般來說也具有較低的剛度和較差的抗斷裂能力,因此很難對其進行長時間的研究,因為銑刀在顯著磨損之前就會發生斷裂(甚至進而損失銑刀)。最後,雖然在宏觀尺度上,多晶結構似乎是均勻的,但在微觀尺度上,與銑刀尺寸相比,晶粒尺寸相對較大,因此加工力會有很大的變化。這些效應結合在一起,形成了一種被稱為 "尺寸效應" 的效應。這被定義為"未成形的切屑厚度減小到切削刃半徑以下的水平,或工件材料的晶粒尺寸開始影響工件材料的變形機理、切屑形成和流動的現象",也就是說,傳統的宏觀力學不能用來描述系統,因為簡單地縮小尺度並不能產生一個有代表性的模型。
2.2. 微銑刀的磨損和磨損測量
通常情況下,銑削中的銑刀磨損研究遵循ISO8688-1和ISO8688-2等標準中規定的協議。這些標準確定了應使用何種參數、材料和切削尺寸,通常作為銑刀質量的基準測試。但是,對於微銑刀來說,ISO標準並不適合,因此必須進行適應性試驗。有一些成分可以從ISO標準中套用。其中之一就是用於描述銑刀磨損的術語:這很有用,因為可以將微觀銑刀的磨損與宏觀銑刀的磨損進行比較。
這些ISO標準還確定了臨界磨損(即銑刀的最大可接受磨損)。這是銑刀磨損在銑刀壽命結束時開始迅速增加的要點。
微觀銑刀的磨損通常比宏觀銑刀的磨損描述得較差,使用切削刃半徑和銑刀直徑的測量值描述的銑刀磨損曲線通常不能得到傳統的磨損曲線。Bahrudin等人利用掃描電子顯微鏡(SEM)研究了鈦和H13銑刀鋼0.5-1.5mm的微銑刀的側面磨損行為與切削時間的對比。雖然他們能夠得到一些被研究的銑刀的磨損曲線,但在整個銑刀範圍內的磨損曲線並不一致,而且每個銑刀的磨損只測量了一個齒。由於即使很小的跳動對微型銑刀的齒嚙合度也有非常顯著的影響,因此考慮兩個齒的磨損是非常重要的。他們觀察到,隨著切削時間的推移,表面光潔度不一致,並推斷這表明切削力不一致。然而,他們沒有直接測量切削力。
基於微觀尺度的加工問題,特別是銑刀的磨損和斷裂問題,進行了大量的研究,以研究不同參數對微觀銑刀磨損的影響。切削速度的增加會增加銑刀磨損,這與傳統加工相似。適度的進給速度通常會產生更穩定的切削力,從而降低銑刀磨損(相對於極低或高的進給速度而言),但前提是進給速度不至於導致斷裂。由於微銑刀的邊緣半徑與被加工材料的晶粒大小相當,因此微觀結構是很重要的,彈性較高的材料會導致更多的犁削(而不是剪切)。
切屑的形成與傳統的情況不同:對於每一個齒的進給量較小的情況下,每一次進給都不會出現切屑,相反,會出現燒蝕或磨擦。銑刀過早失效是微加工中的一個常見問題,這給測量磨損帶來了困難:在傳統加工中,銑刀在切削刃斷裂時就會失效,而使用微型銑刀時,由於銑刀的特殊使用方式(例如,切削刃鈍化或損壞,導致力比預期的大),整個軸往往會斷裂。
考慮切削力對更好地了解臨界磨損開始發生的時間點是很有幫助的。特別是,在銑刀磨損研究中還沒有考慮到銑刀磨損時的總切削力變化(幅度)。這一點很重要,因為高的力幅度表明震動過大,會導致銑刀磨損率增加。在這裡進行的第一階段的工作(在2.2節中描述)研究了銑刀磨損時的切削力,因為在宏觀加工中,切削力會隨著銑刀磨損的增加而增多。
迄今為止,使用微刀產生的最詳細的曲線是用銑刀的表面光潔度作為磨損度量,理由是微刀磨損太難測量。這個度量的問題在於,表面粗糙度取決於銑刀的鋒利度,以及是否發生摩擦或燒損。這意味著,如果在特定的階段出現邊緣斷裂,或材料在銑刀上堆積,則發生磨損的機制(如摩擦或剪切程度)會發生變化。因此,表面粗糙度不能等同於銑刀磨損。
Ucun等人觀察到,切削刃半徑並不能充分衡量銑刀的磨損,因為在微型銑刀的使用壽命內,會逐漸形成新的切削刃,因此,儘管切削刃半徑最初隨著銑刀半徑的減小而增大,但隨後又會減小。他們測量了不同切削條件下不同銑刀的直徑減小量,但沒有繪製磨損曲線。Malekian等人用同樣的方法使用各種傳感器在線測量銑刀磨損,同樣的,邊緣半徑也不能描述銑刀磨損的主要位置,儘管它是一個有用的度量標準,可以判斷材料是否發生剪切或彈性變形。
Aramcharoen等人使用了另一個可能的量化銑刀磨損度量標準--側翼磨損,但由於研究的主要目的是評估不同的塗層,因此沒有產生磨損曲線,因此無法評估這一測量方法在產生磨損曲線方面的有用性。Ding等人也將側面磨損與邊緣半徑一起作為直徑為0.1 mm的微型銑刀的磨損度量,但沒有看到明顯的磨損曲線(儘管磨損明顯隨著切削時間的延長而增加),可能是由於銑刀尺寸極小,測量的數量有限。Elkaseer等人模擬了鋼的微觀結構對銑刀磨損的影響,但沒有研究銑刀磨損的演變情況。
Filiz等人研究了一種更有效的方法,即用減小通道寬度作為切削刃半徑的測量方法來研究銅的可加工性,在加工過程中不需要拆卸銑刀進行測量。這類似於測量銑刀半徑,並不能提供關於單個齒或不均勻齒磨損的信息。然而,類似的工藝也適用於微銑加工,因為槽形輪廓可以提供銑刀磨損的信息,而且只要掌握適當的銑刀磨損與槽形輪廓相關的數據,就可以在不拆下銑刀的情況下進行測量。
這些ISO標準還確定了臨界磨損(即銑刀的最大可接受磨損)。這是銑刀磨損在銑刀壽命結束時開始迅速增加的要點。
微觀銑刀的磨損通常比宏觀銑刀的磨損描述得較差,使用切削刃半徑和銑刀直徑的測量值描述的銑刀磨損曲線通常不能得到傳統的磨損曲線。Bahrudin等人利用掃描電子顯微鏡(SEM)研究了鈦和H13銑刀鋼0.5-1.5mm的微銑刀的側面磨損行為與切削時間的對比。雖然他們能夠得到一些被研究的銑刀的磨損曲線,但在整個銑刀範圍內的磨損曲線並不一致,而且每個銑刀的磨損只測量了一個齒。由於即使很小的跳動對微型銑刀的齒嚙合度也有非常顯著的影響,因此考慮兩個齒的磨損是非常重要的。他們觀察到,隨著切削時間的推移,表面光潔度不一致,並推斷這表明切削力不一致。然而,他們沒有直接測量切削力。
基於微觀尺度的加工問題,特別是銑刀的磨損和斷裂問題,進行了大量的研究,以研究不同參數對微觀銑刀磨損的影響。切削速度的增加會增加銑刀磨損,這與傳統加工相似。適度的進給速度通常會產生更穩定的切削力,從而降低銑刀磨損(相對於極低或高的進給速度而言),但前提是進給速度不至於導致斷裂。由於微銑刀的邊緣半徑與被加工材料的晶粒大小相當,因此微觀結構是很重要的,彈性較高的材料會導致更多的犁削(而不是剪切)。
切屑的形成與傳統的情況不同:對於每一個齒的進給量較小的情況下,每一次進給都不會出現切屑,相反,會出現燒蝕或磨擦。銑刀過早失效是微加工中的一個常見問題,這給測量磨損帶來了困難:在傳統加工中,銑刀在切削刃斷裂時就會失效,而使用微型銑刀時,由於銑刀的特殊使用方式(例如,切削刃鈍化或損壞,導致力比預期的大),整個軸往往會斷裂。
考慮切削力對更好地了解臨界磨損開始發生的時間點是很有幫助的。特別是,在銑刀磨損研究中還沒有考慮到銑刀磨損時的總切削力變化(幅度)。這一點很重要,因為高的力幅度表明震動過大,會導致銑刀磨損率增加。在這裡進行的第一階段的工作(在2.2節中描述)研究了銑刀磨損時的切削力,因為在宏觀加工中,切削力會隨著銑刀磨損的增加而增多。
迄今為止,使用微刀產生的最詳細的曲線是用銑刀的表面光潔度作為磨損度量,理由是微刀磨損太難測量。這個度量的問題在於,表面粗糙度取決於銑刀的鋒利度,以及是否發生摩擦或燒損。這意味著,如果在特定的階段出現邊緣斷裂,或材料在銑刀上堆積,則發生磨損的機制(如摩擦或剪切程度)會發生變化。因此,表面粗糙度不能等同於銑刀磨損。
Ucun等人觀察到,切削刃半徑並不能充分衡量銑刀的磨損,因為在微型銑刀的使用壽命內,會逐漸形成新的切削刃,因此,儘管切削刃半徑最初隨著銑刀半徑的減小而增大,但隨後又會減小。他們測量了不同切削條件下不同銑刀的直徑減小量,但沒有繪製磨損曲線。Malekian等人用同樣的方法使用各種傳感器在線測量銑刀磨損,同樣的,邊緣半徑也不能描述銑刀磨損的主要位置,儘管它是一個有用的度量標準,可以判斷材料是否發生剪切或彈性變形。
Aramcharoen等人使用了另一個可能的量化銑刀磨損度量標準--側翼磨損,但由於研究的主要目的是評估不同的塗層,因此沒有產生磨損曲線,因此無法評估這一測量方法在產生磨損曲線方面的有用性。Ding等人也將側面磨損與邊緣半徑一起作為直徑為0.1 mm的微型銑刀的磨損度量,但沒有看到明顯的磨損曲線(儘管磨損明顯隨著切削時間的延長而增加),可能是由於銑刀尺寸極小,測量的數量有限。Elkaseer等人模擬了鋼的微觀結構對銑刀磨損的影響,但沒有研究銑刀磨損的演變情況。
Filiz等人研究了一種更有效的方法,即用減小通道寬度作為切削刃半徑的測量方法來研究銅的可加工性,在加工過程中不需要拆卸銑刀進行測量。這類似於測量銑刀半徑,並不能提供關於單個齒或不均勻齒磨損的信息。然而,類似的工藝也適用於微銑加工,因為槽形輪廓可以提供銑刀磨損的信息,而且只要掌握適當的銑刀磨損與槽形輪廓相關的數據,就可以在不拆下銑刀的情況下進行測量。
2.2.1. 需要共同的方法
一些作者已經指出,與宏觀銑削相比,沒有既定的工具測量協議。這導致缺乏現有的數據來比較研究,這使得在工業背景下應用銑刀的過程變得緩慢。如前所述,通常採用側面磨損和直徑,但不是全部採用。 Wang等人研究了在加工TC4合金時,在加工TC4合金的過程中,研究了銑刀和塗層WC端面銑刀的切削性能,銑刀磨損是評估過程的指標之一。他們指出,由於 "在微銑加工中,沒有統一的方法來評估銑刀磨損" ,因此採用微溝槽寬度作為衡量銑刀磨損的指標。這顯然與實際銑刀的測量是無法比擬的,這樣的研究不能與測量銑刀的側面和直徑的研究相聯繫。顯然,要實現這些研究的統一和比較,或將這些研究結合起來,使之對行業有利,唯一的辦法就是確定一個標準的協議。
2.3. 初步研究
在黃銅(CuZn37)上進行了初步試驗,繪製了AlTiN塗層硬質合金銑刀的銑刀磨損與切削距離的對比圖。結果(圖1)顯示,使用SEM可以成功測量銑刀磨損。
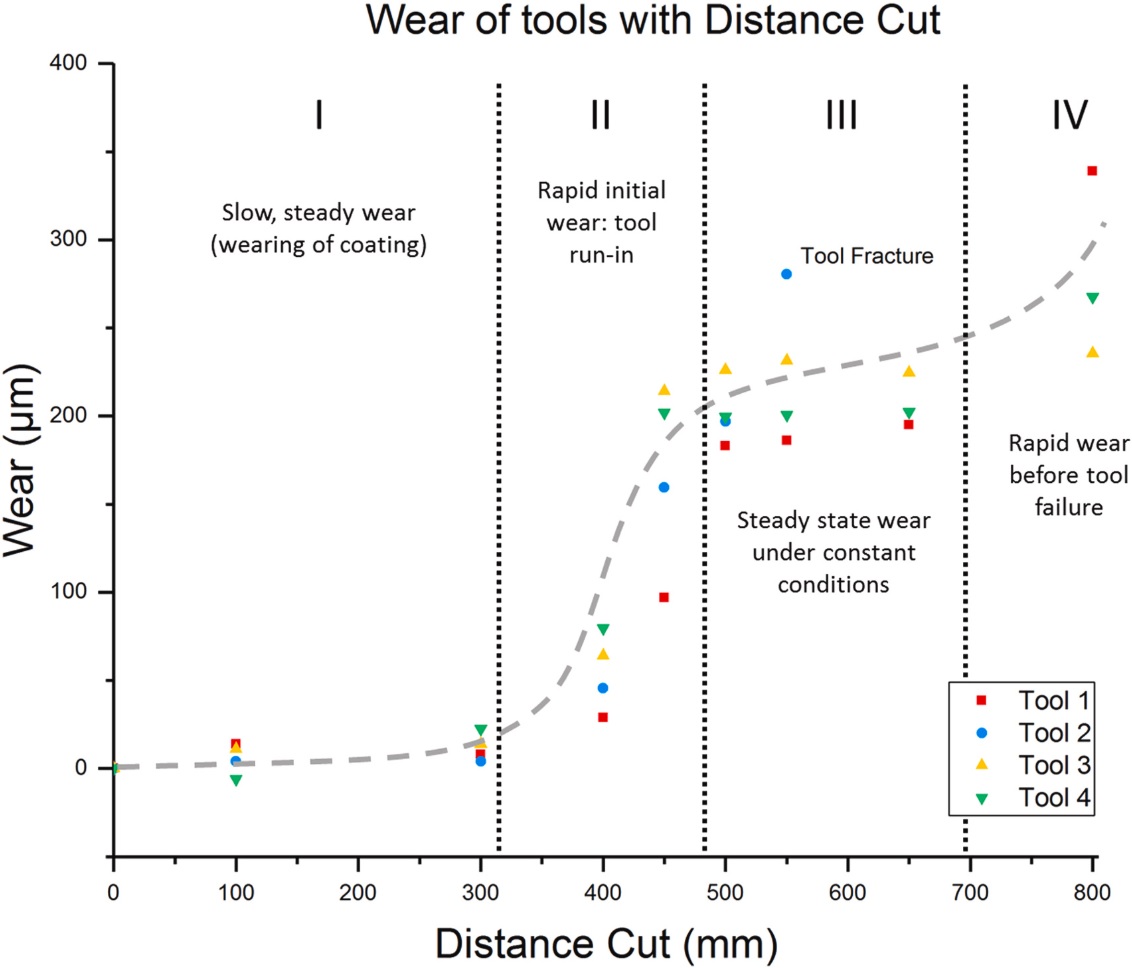
圖1. 0.5 mm微端銑刀切削CuZn38的磨損。磨損量是以總直徑的減少量來表示。
四種銑刀的磨損情況可以按區域進行研究。最初,在I區(至300mm的切削距離),觀察到的磨損很少,這可能是AlTiN塗層被去除的距離。這種塗層,在微銑等高性能應用中被廣泛使用,並且在這之前塗層就被廣泛應用,因為黃銅是一種非常柔軟、易加工的材料,很適合AlTiN塗層。在這之後,銑刀磨損顯示出了通常在宏觀銑刀上看到的磨損曲線特徵。由於銑刀磨損的取樣不足或測量技術不完善,這在以往的微銑刀磨損研究中並不常見。在第二區,銑刀的快速磨損是由於切削刃最初從一個非常尖銳的點開始鈍化。在第三區中,磨損相對緩慢、穩定地增加。最後,在第四區,隨著銑刀的嚴重磨損,磨損加劇。銑刀的斷裂發生在這個階段(除了其中一個銑刀在第三區斷裂外)。使用圖2所示的兩個方向的銑刀的SEM,可以用第3節中詳述的協議來測量銑刀磨損情況(其中使用的術語與ISO標準有關)。在現實中,通常會看到不止一種類型的磨損(見圖3)。需要注意的是,這兩個角度是識別所有磨損類型的最低要求。
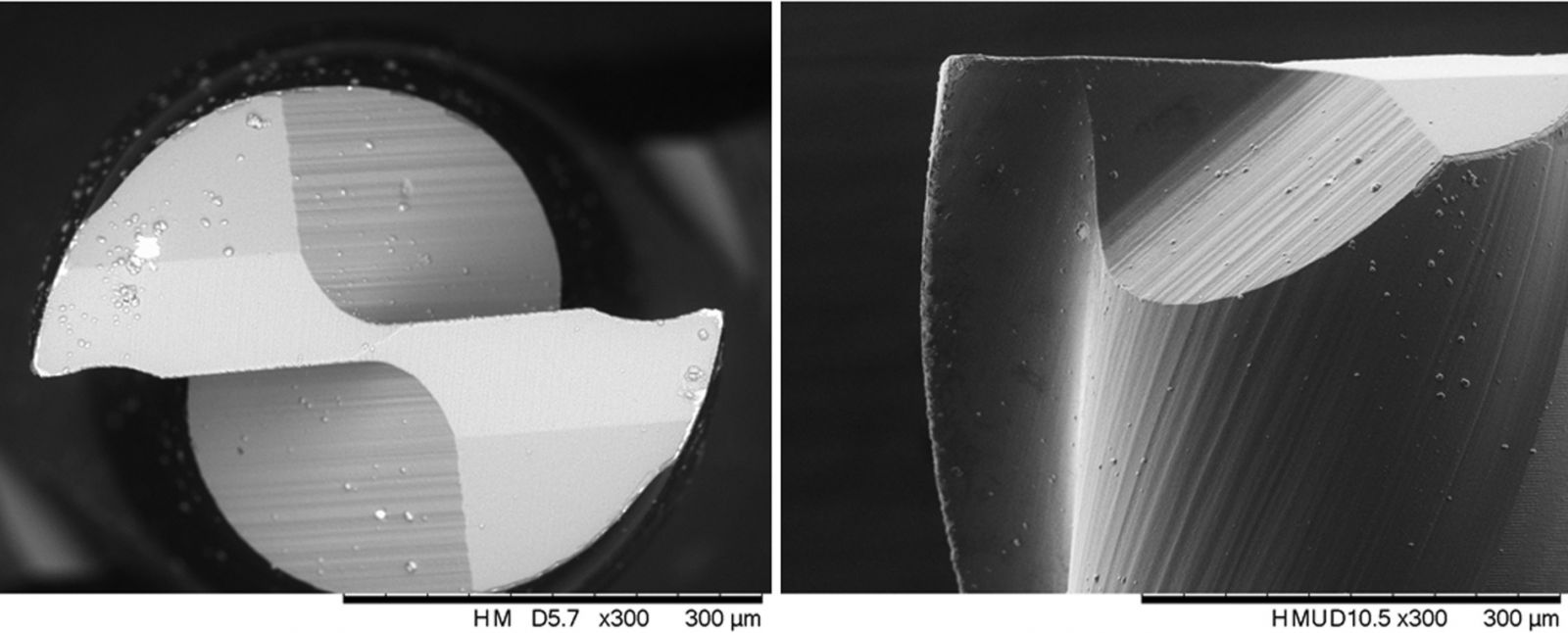
圖2. 測量工具的兩個方向。
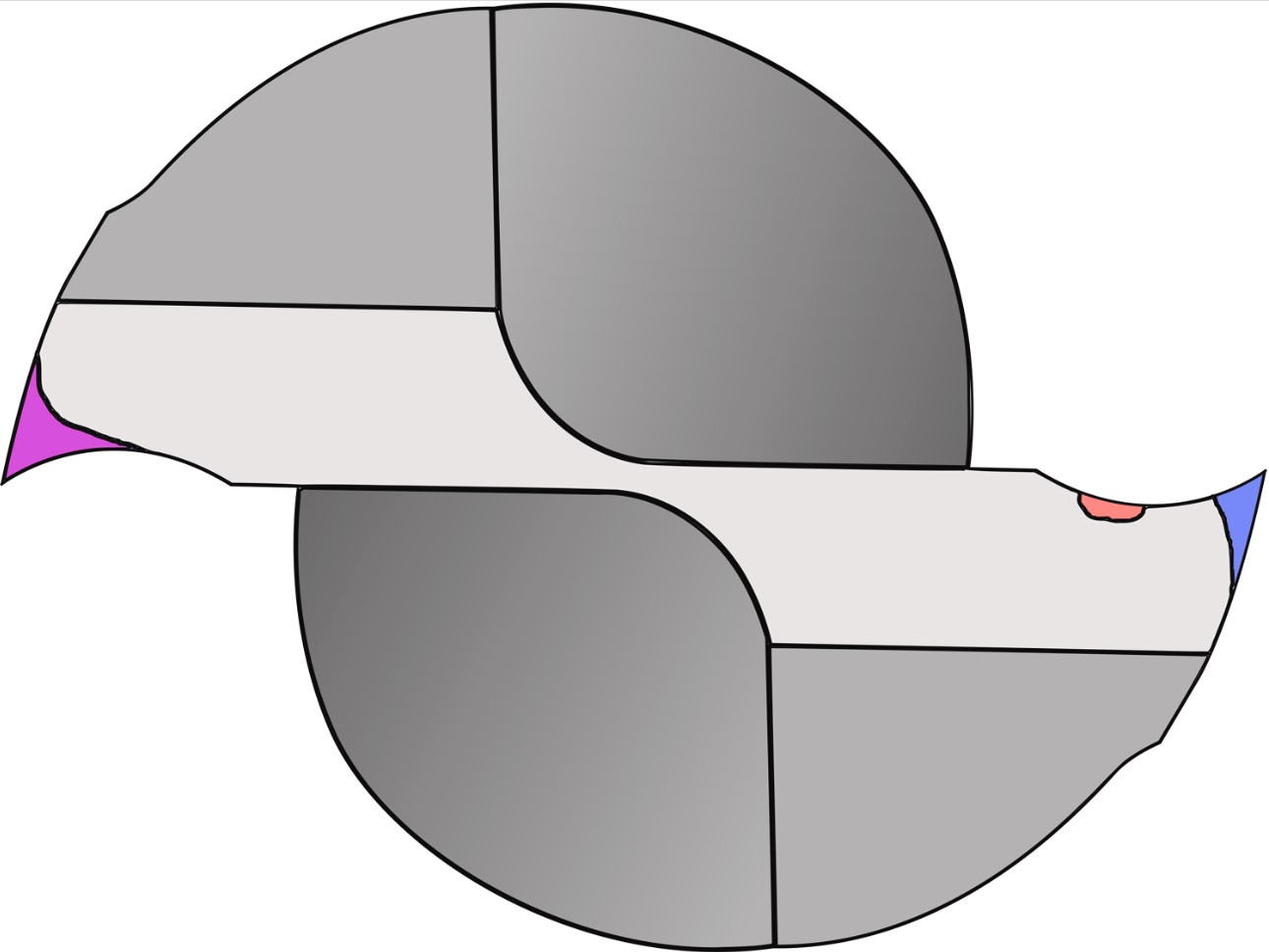
圖3. 一個發生多種類型的磨損的例子 – 其中,VB和KT2為紫色,而CH和KT1為紅色,VB為藍色。
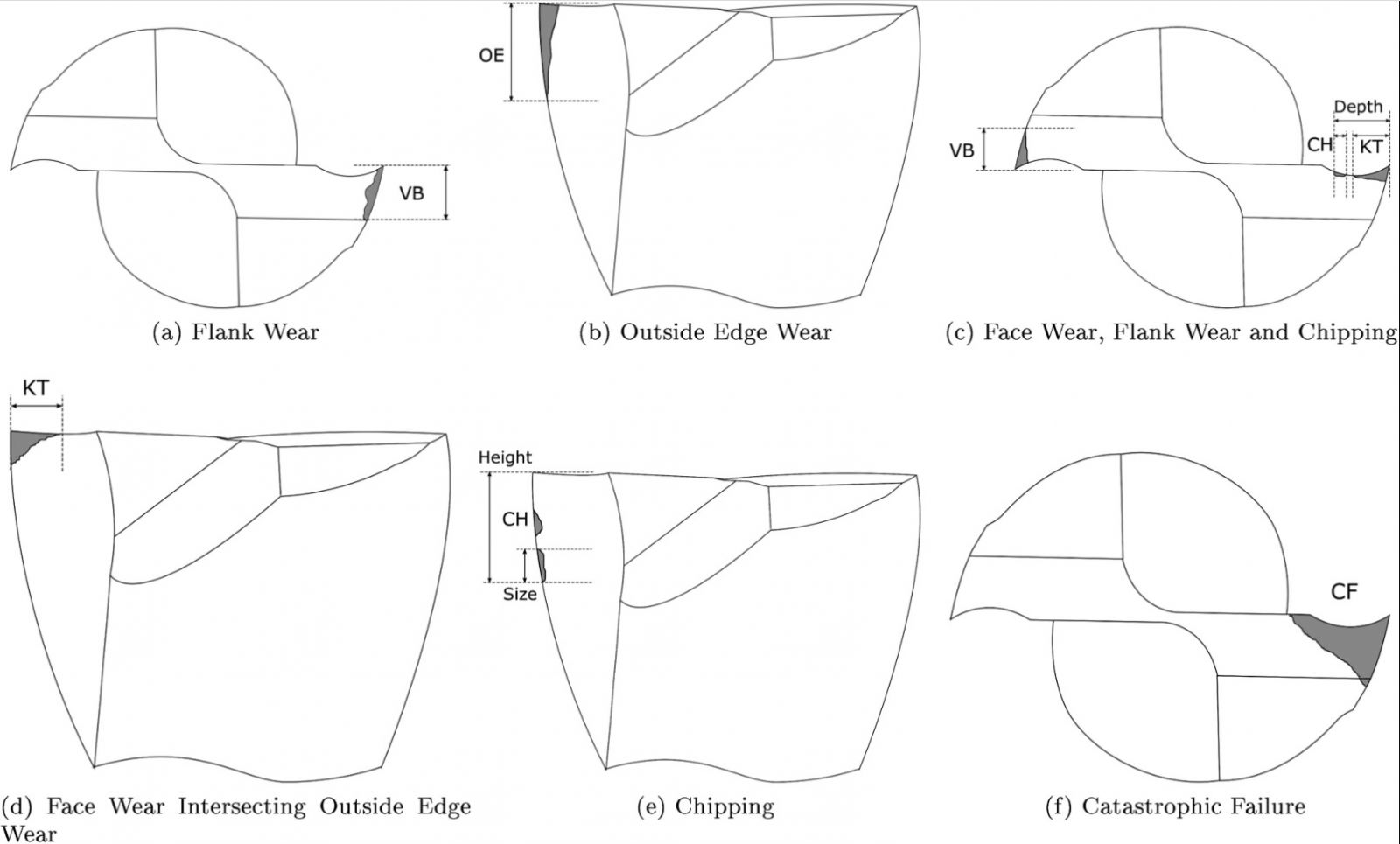
圖4. 磨損的類型--圖示。
初步研究和僅用外徑測量微型銑刀磨損時遇到的障礙,突出表明有必要實現一個標準化的協議,以提供比目前的銑刀半徑更多的資訊。
3. 協議的制定
3.1. 目的
鑑於缺乏對微型銑削銑刀磨損研究的標準化工作,決定建立一個測量銑刀的協議,以幫助今後對傳統工程材料(如鋼等常規工程材料和航空金屬,如鈦和鎳合金)的微型銑削中的磨損進程和基本機制進行研究。從作者的初步實驗和文獻綜述中可以看出,無論是作者的初步實驗還是文獻綜述,都可以直接用光學方法(SEM)觀察到微磨銑刀的磨損情況,給出經典的銑刀磨損曲線。然而,除了研究之間的不一致和如果要進行研究之間的比較,需要標準化之外,銑刀半徑的測量方法也存在一些嚴重的問題,尤其是它沒有考慮到刃的不均勻磨損:例如,如果其中一刃發生災難性的磨損,而另一刃沒有磨損,那麼測量結果將與兩刃的磨損程度相同(見圖3)。由於2.3節中描述的初步工作的結果,確定了需要開發和測試一種更精確的微型銑刀磨損的測量方法,其目的是加工參數和切削材料應該是靈活的,但應該使用標準的報告方法,以便於研究之間的比較。
3.2. 定義
在測量微端銑刀的磨損時,必須定義某些參數,包括切削刃半徑、銑刀半徑和工件表面光潔度,以及類似的磨損機制的定性指標。銑刀半徑是指銑刀耙面的切削刃半徑。銑刀半徑定義為銑刀工作直徑的一半(對於0.5mm的立銑刀來說,是0.25mm)。工件的表面光潔度定義為測得的Ra值,表面紋理定義為測得的Sa值。銑刀磨損的類型以ISO8688為基礎,適用於小型銑刀。這些類型被分為(表1),分別為側翼磨損(VB)、端面磨損(KT)、外緣磨損(OE)切屑(CH)和災難性失效(CF)。通過測量工具與這些類型的磨損的關係,可以在研究之間進行直接比較(表2)。
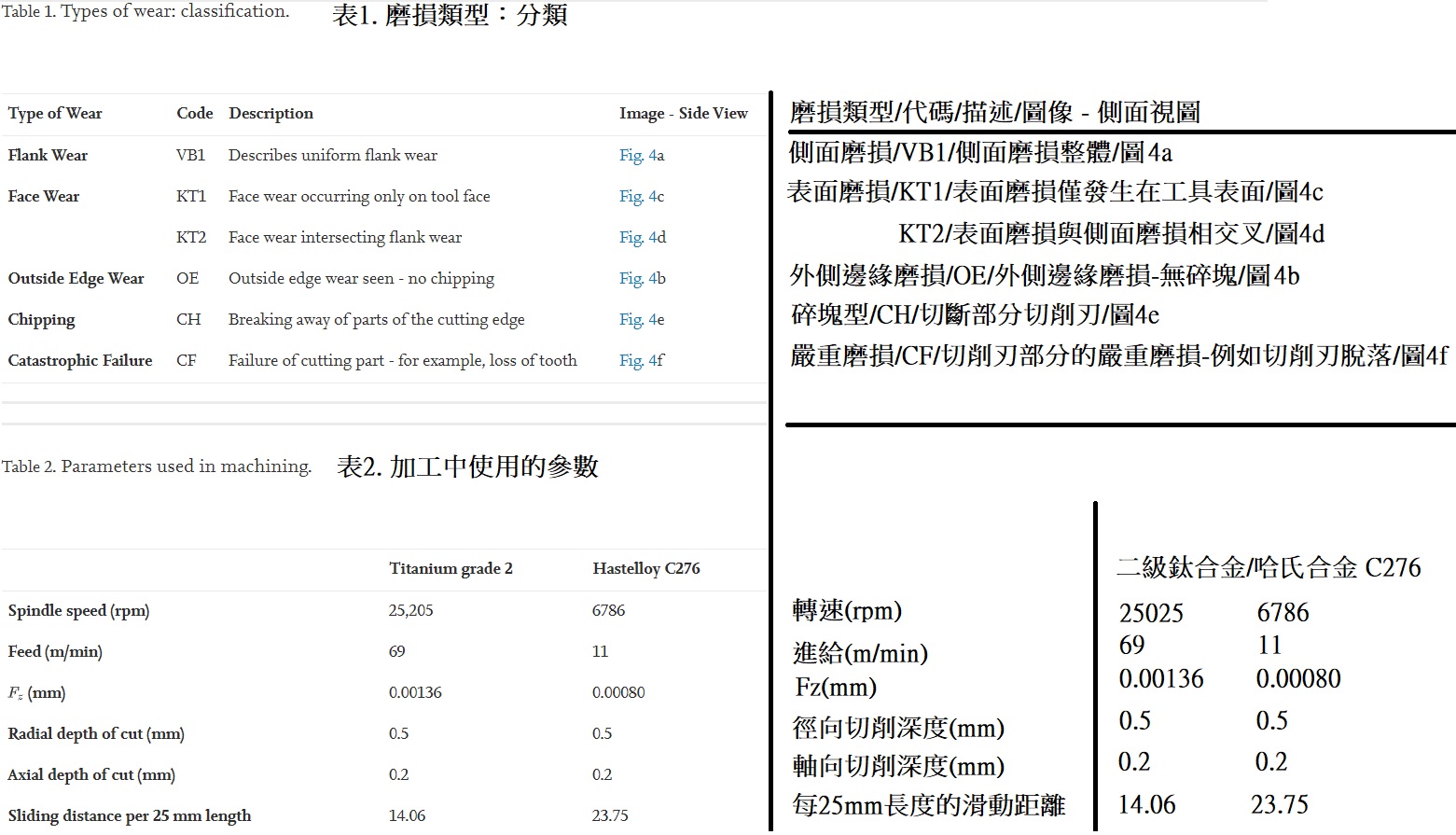
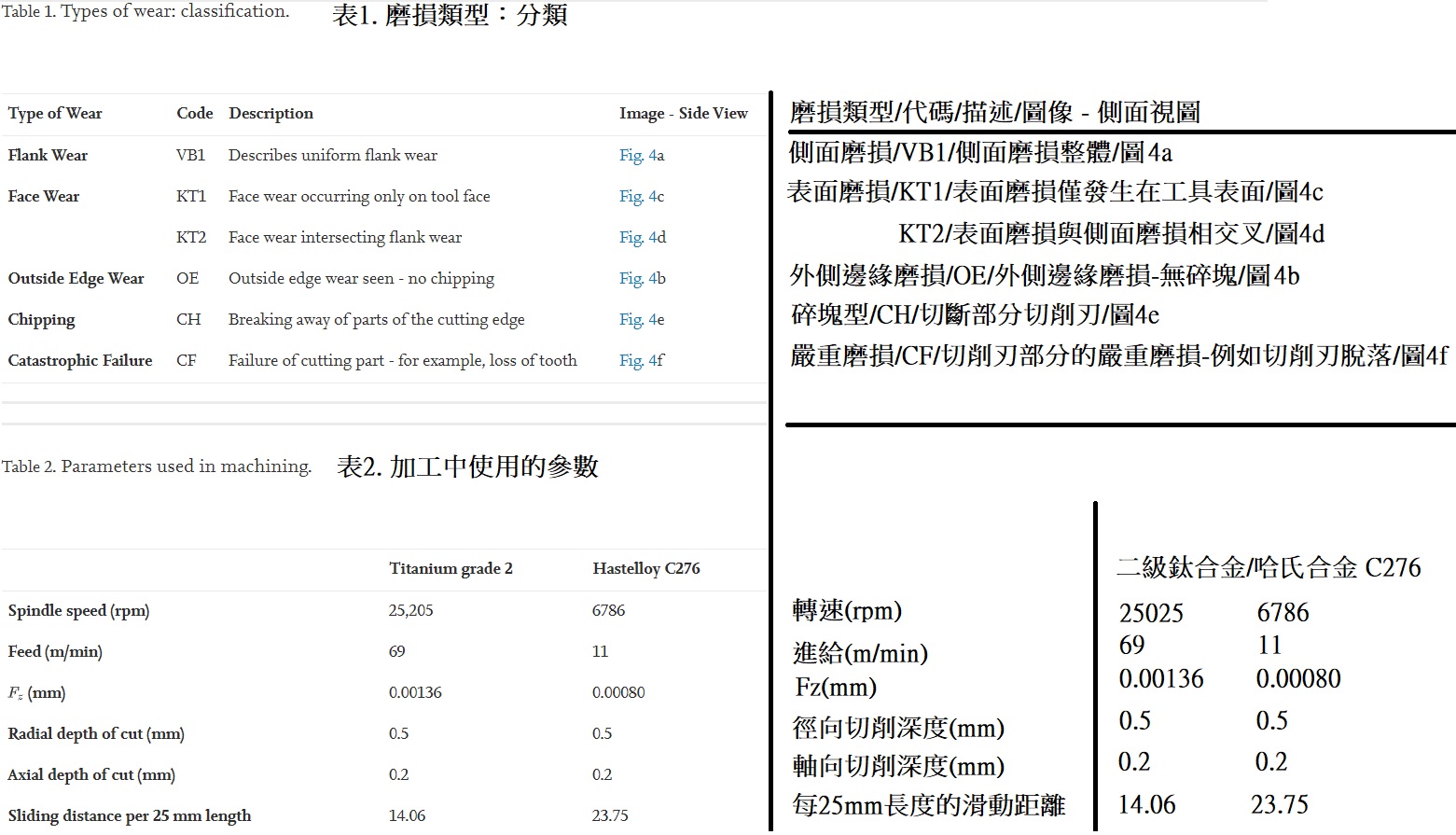
3.3. 材料:用滑動距離作為距離切削的衡量標準。
在第2節回顧的文獻中,微型銑刀的銑刀磨損用切削距離或材料去除率來表示。雖然這種方法對於描述銑刀在給定材料中的使用壽命是有用的,但很難比較不同材料之間的銑刀磨損,因為切削進給和速度的差異導致不同材料的滑動距離明顯不同。銑刀的滑動距離是用以下方法計算出來的。
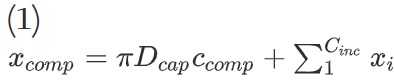
其中,Cinc為不完全圓的數量,由

為完全圓的數量,由Ccomp = nrev - cinc計算,Dcap為嚙合銑刀直徑,
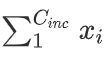
為所有不完全圓的滑動距離之和(圖5)。這種方法在摩擦學意義上比較有用,但也可以比較不同材料的銑刀磨損,即使在不同的切削條件下,也可以比較不同的銑刀磨損。 Xcomp的值是用Matlab程序計算出來的,該程序建立了
。
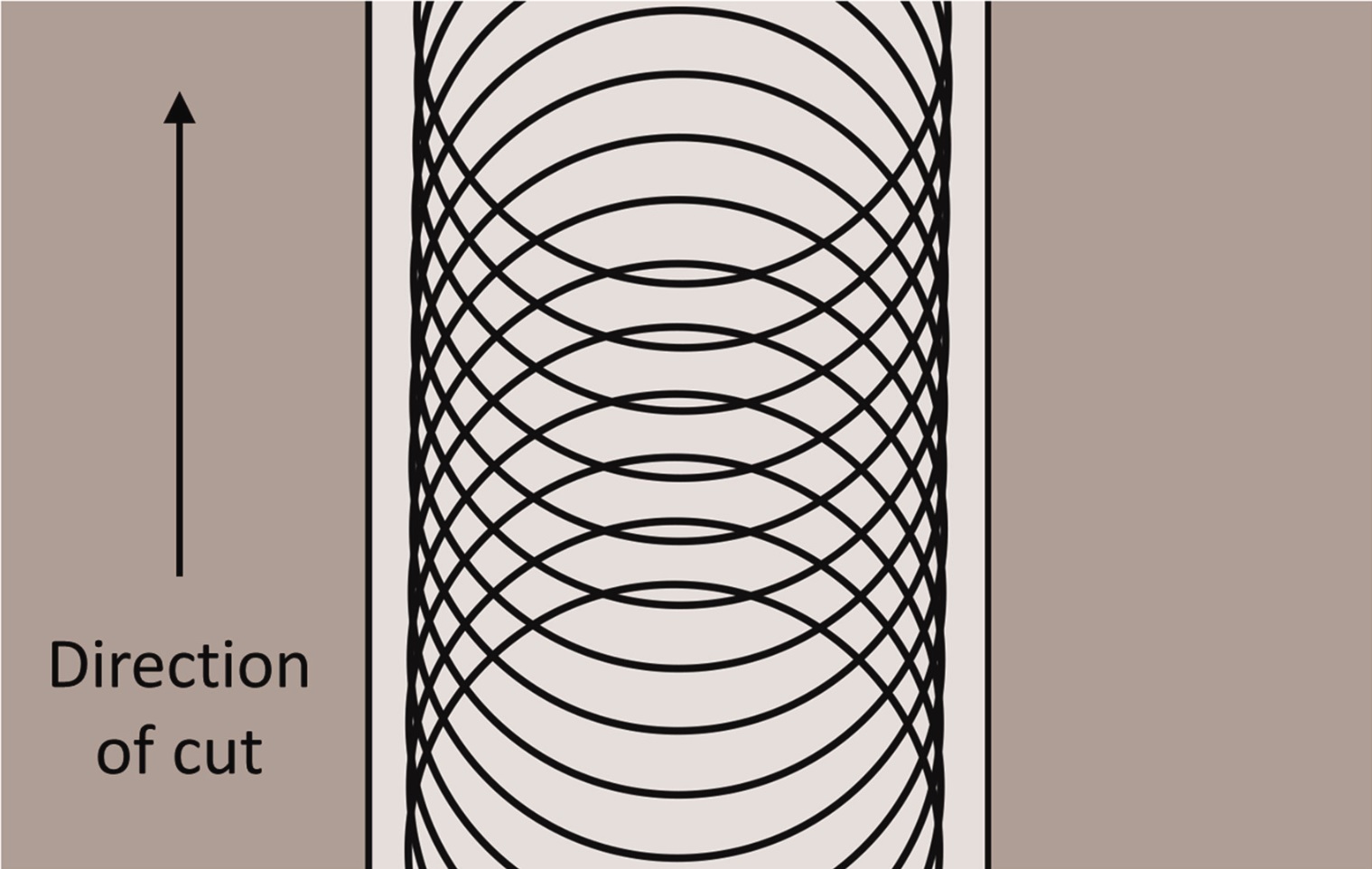
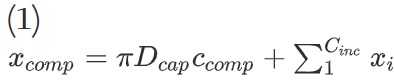
其中,Cinc為不完全圓的數量,由

為完全圓的數量,由Ccomp = nrev - cinc計算,Dcap為嚙合銑刀直徑,
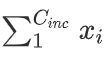
為所有不完全圓的滑動距離之和(圖5)。這種方法在摩擦學意義上比較有用,但也可以比較不同材料的銑刀磨損,即使在不同的切削條件下,也可以比較不同的銑刀磨損。 Xcomp的值是用Matlab程序計算出來的,該程序建立了
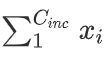
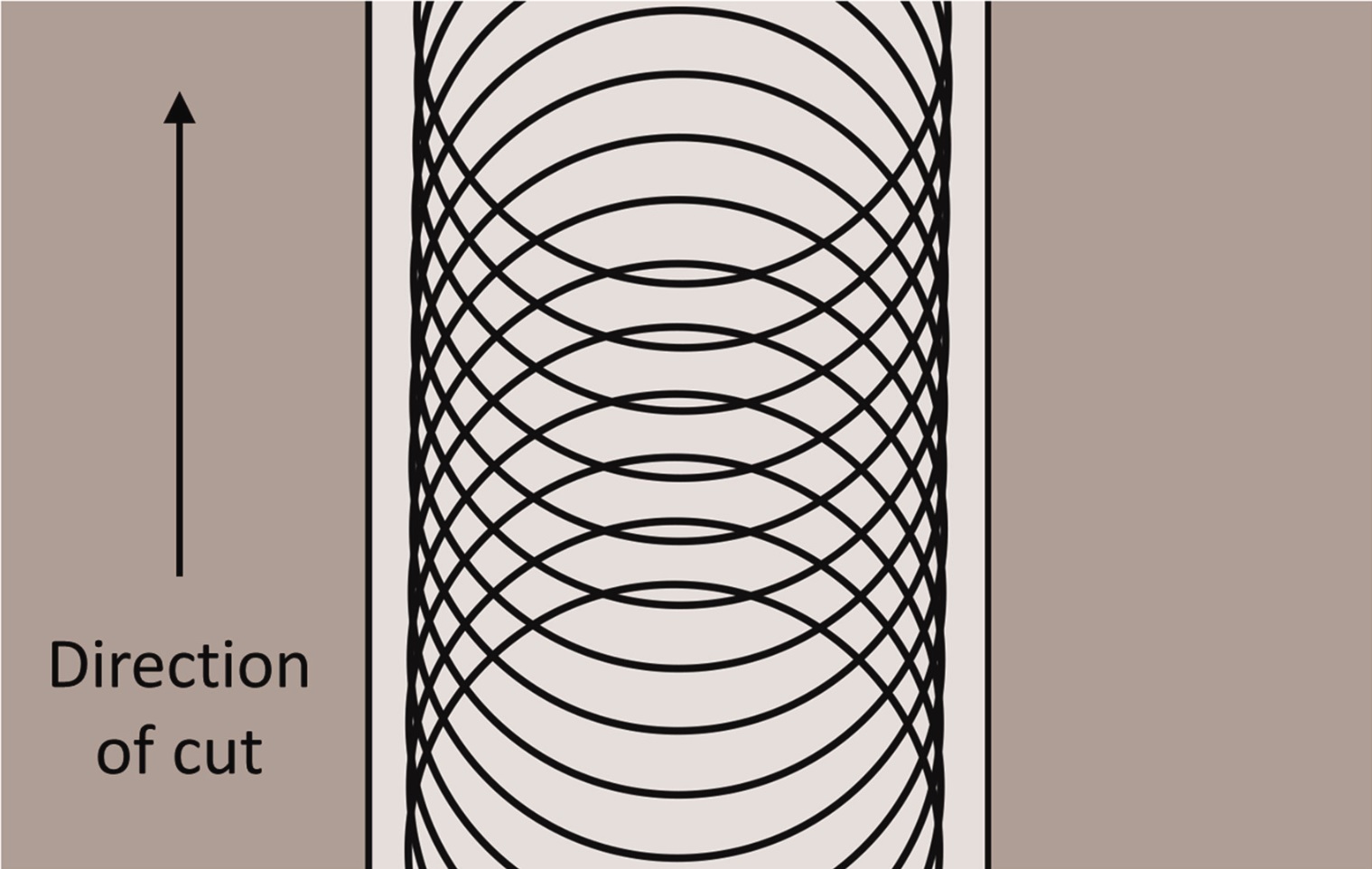
圖5. 銑刀在工件上的起刀和收刀路徑。
與切削距離或切削時間相比,使用滑動距離可以提供更一致的銑刀磨損度量,因為銑刀的工作量取決於主軸速度和進給率。在已知的主軸轉速和進給率的情況下,可以使用換算係數將這些滑動距離與切削距離或切削次數連結起來,從而可以預測不同條件下的銑刀磨損。
3.4. 銑刀和工件準備
在進行磨損測試之前,應先檢查銑刀,以確保達到最低質量標準。對於未塗層的銑刀,可以合理地預期邊緣半徑 < 0.1 μm,而對於塗層銑刀,則可能高達0.2 μm。雖然沒有規定,但在比較工件時,每個工件的晶粒方向應相同,當晶粒尺寸在0.1D(其中D為銑刀直徑)的情況下,應注意確保工件晶粒尺寸相差不超過0.02D 。此外,還應滿足以下關於切削深度和單位去除率的標準。單位去除量被田口法(Taniguchi)定義為每次切削時去除的材料量,有一、二、三等尺寸。這兩個標準結合起來就是
• 邊緣半徑<切割深度和
• 邊緣半徑<單位去除率×10
所有的工件應面對面,以確保垂直於銑刀的平面度,並固定在機床身上,使其表面與Z軸垂直。通常情況下,應使用泛油或霧狀潤滑劑來控制加工溫度,用微型測功機或3組份力傳感器監測其在工件上的壓力,並在加工力時予以深思熟慮。冷卻劑的方法在各比較研究中應保持一致。
• 邊緣半徑<切割深度和
• 邊緣半徑<單位去除率×10
所有的工件應面對面,以確保垂直於銑刀的平面度,並固定在機床身上,使其表面與Z軸垂直。通常情況下,應使用泛油或霧狀潤滑劑來控制加工溫度,用微型測功機或3組份力傳感器監測其在工件上的壓力,並在加工力時予以深思熟慮。冷卻劑的方法在各比較研究中應保持一致。
3.5. 銑刀的測量
微型工具在測試前和測試過程中都應進行測量。測試時需要的基本設備如下。
• 具有散射和反散射電子功能的掃描電子顯微鏡。
• 光學剖面儀(如焦距變化或白光干涉儀)。
• 超聲波浴。
• 丙酮。
• 壓縮空氣源。
• 用於測量工件上潤滑油壓力的力傳感器。
在切削過程中,應測量切削力,以確定潤滑劑壓力和切削力。銑刀應在預定的時間間隔內取出,用SEM測量。在使用SEM測量前,應先用丙酮在超聲波浴中清洗銑刀,然後用壓縮空氣吹乾。銑刀應在兩個方向上進行測量,如圖2所示,可以使用表1中詳述的協議來測量銑刀磨損情況(其中所用術語與ISO標準有關)。通常會看到不止一種類型的磨損(見圖3)。需要注意的是,這兩個角度是確定表中定義的所有磨損類型的最低要求。所有的磨損測量值均以μm為單位。
• 具有散射和反散射電子功能的掃描電子顯微鏡。
• 光學剖面儀(如焦距變化或白光干涉儀)。
• 超聲波浴。
• 丙酮。
• 壓縮空氣源。
• 用於測量工件上潤滑油壓力的力傳感器。
在切削過程中,應測量切削力,以確定潤滑劑壓力和切削力。銑刀應在預定的時間間隔內取出,用SEM測量。在使用SEM測量前,應先用丙酮在超聲波浴中清洗銑刀,然後用壓縮空氣吹乾。銑刀應在兩個方向上進行測量,如圖2所示,可以使用表1中詳述的協議來測量銑刀磨損情況(其中所用術語與ISO標準有關)。通常會看到不止一種類型的磨損(見圖3)。需要注意的是,這兩個角度是確定表中定義的所有磨損類型的最低要求。所有的磨損測量值均以μm為單位。
3.6. 槽形的測量
可以使用兩種方法之一來測量已加工的溝槽:或者像圖1中的那樣,拍攝材料的橫截面圖像;或者使用剖面儀來測量溝槽輪廓(圖2)。如果使用後一種方法,必須確保進行去毛刺,因為這將導致測量結果不準確。去毛刺必須小心翼翼地進行,並且要保證槽體不會有進一步的磨損。
測量好後,槽的剖面可以如圖3所示,其中Wbt和Dt分別為槽的理論寬度和深度,Wb和Da分別為槽的基寬和實際深度。如果工件沒有經過適當的平整度處理,槽的深度可能是測量齒面磨損的可靠度低於測量耙面磨損的寬度。
測量好後,槽的剖面可以如圖3所示,其中Wbt和Dt分別為槽的理論寬度和深度,Wb和Da分別為槽的基寬和實際深度。如果工件沒有經過適當的平整度處理,槽的深度可能是測量齒面磨損的可靠度低於測量耙面磨損的寬度。
3.7. 銑刀壽命標準
磨損的銑刀應按照3.5節的規定進行測量。端面磨損不應超過0.2d,因為這被認為是銑刀的災難性故障。為了測量磨損目的,測量端面磨損不超過0.2d,將提供超過實際使用範圍的數據進入銑刀的III區,並確定銑刀壽命標準。
3.8. 測試程序
為了進行磨損測試,槽應按模具供應商或製造商提供的數據規定的深度加工。槽體應從工件外側開始,沿切削的Y方向進行。


圖6. 截面圖。
3.8.1. 機床要求
機床應該是專業的微型加工中心,主軸轉速應能達到50,000轉/分以上(圖7)。
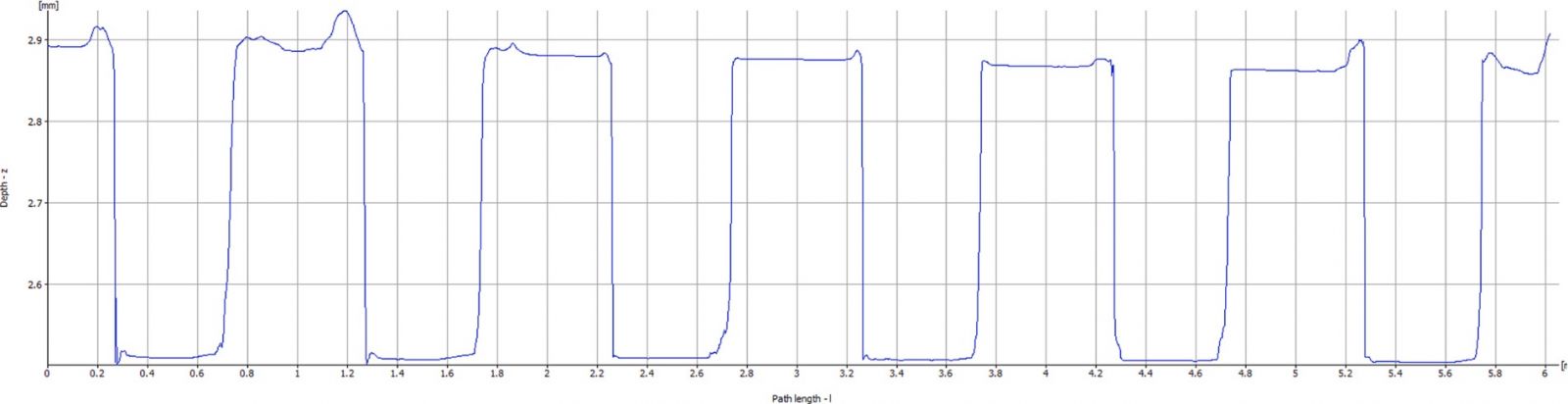
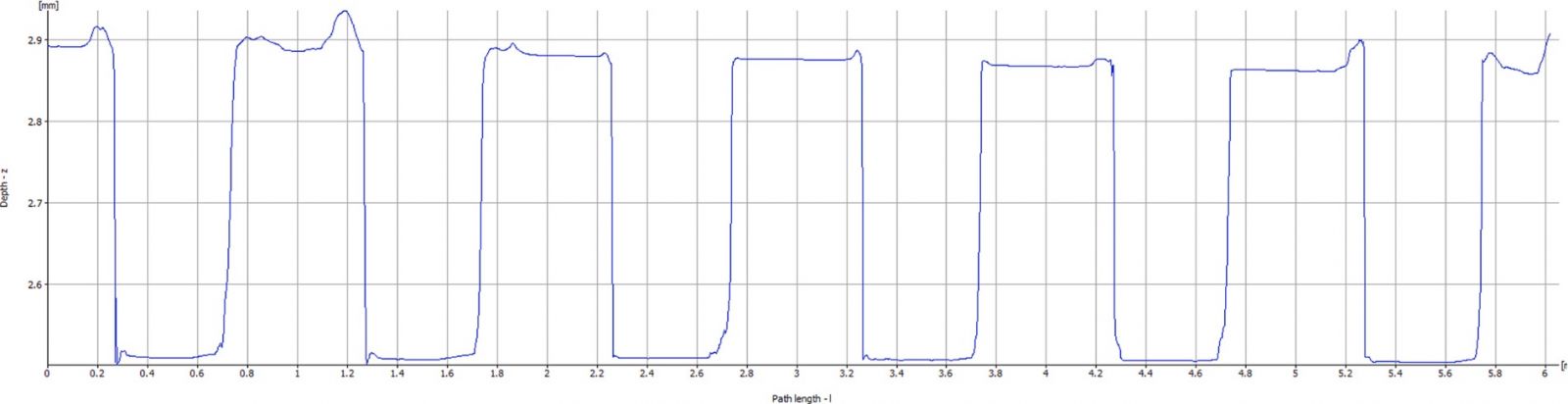
圖7. 使用剖面儀測量的橫截面。
3.8.2. 切削力的測量
在微型銑削應用中,極小的跳動會導致切削刃嚙合誤差和切削刃磨損不均勻。因此,檢查每個切削刃的嚙合力特徵,以確定切削刃的嚙合度是否相等是非常有用的(圖8)。
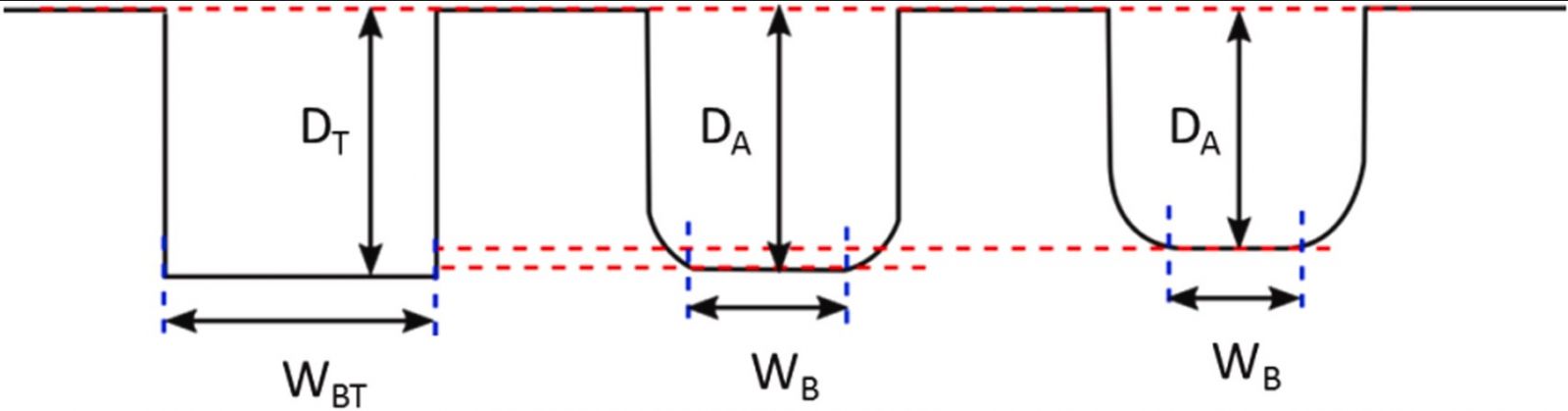
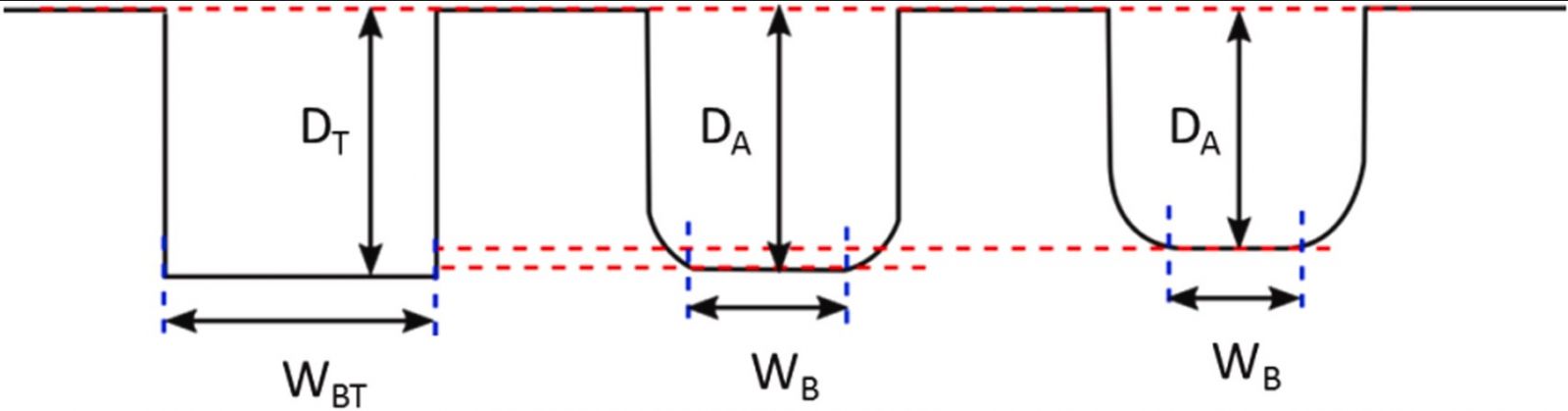
圖8. 槽形測量參數
由於在微型銑削中測量到的切削力很小,所以使用兩種不同的方法來分析切削力,即平均切削力的測量和切削力振幅的測量。前者用於給出進給方向的切削力的總體情況(圖9中用Y表示),並簡單地在規定的切削時間內對信號值進行平均(平均值)。後者略顯複雜,因為它考慮了在指定時間內的切削力範圍。為了準確地做到這一點,必須通過繪製傅立葉係數變換的第二項來計算切削刃的嚙合差異。首先必須計算出第二項傅立葉係數,如公式(2)所示,其中fcut是切削頻率,由fcut=n/60 x Zc計算得出,其中n是主軸轉速,單位為轉/分,Zc是切削刃數。

Fc為切削力,t為切削時間,x為數據點數。利用第二個係數,可以用公式(3)繪製出第二個傅里葉項的實數部分與時間的對比圖。

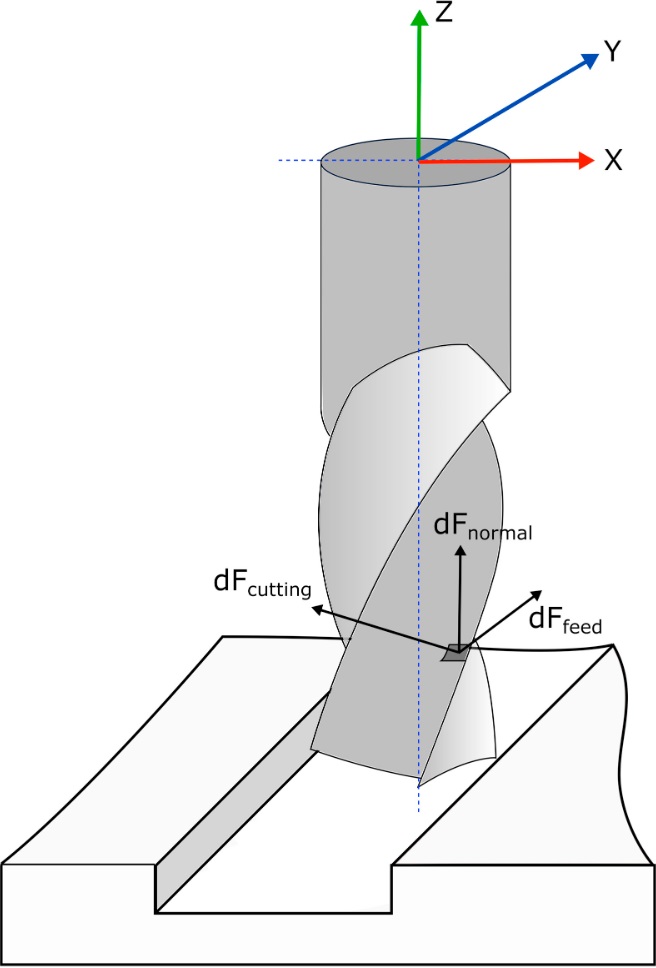
圖9. 對微型立銑刀施加的力。
3.9. 成果報告
在繪製銑刀磨損演變圖時,磨損應以相對於銑刀的原始尺寸(即以μm為單位)的絕對值報告。x軸應使用滑動距離,必要時用第二個軸作為切削距離的轉換係數。圖10中給出了一個例子。銑刀磨損應確定為三個區域之一。
一、快速初始磨損
二、穩態磨損
三、故障前的快速磨損
然後,工具壽命標準可以確定為第二和第三階段之間的交叉點。
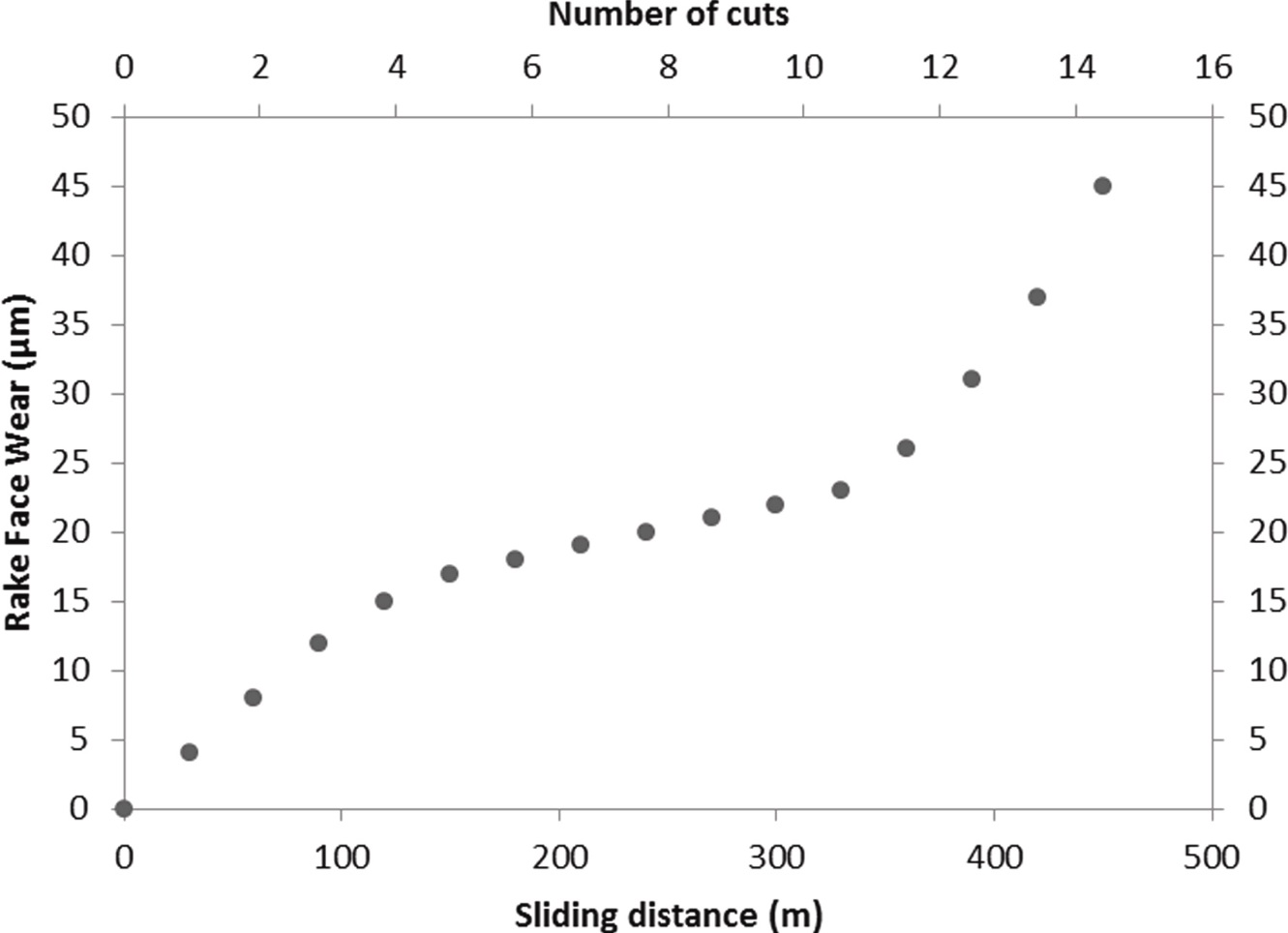
圖10. 報告結果的方式示例。
4. 驗證測試
4.1. 材料和方法
一旦確定了可接受的磨損測試方案,即開始設計加工試驗,以測試該方法的相關性和一致性。使用了三種力學上非常不同的材料:黃銅(CuZn37)、2級鈦和Hastelloy(一種含鋅的鎳鉬合金)。使用三種結構不同的材料意味著可以觀察到各種不同的磨損機制,代表了不同的行業。銑刀的設置和測量見3.4 銑刀和工件準備、3.5 銑刀的測量、3.6 槽形的測量、3.7 銑刀壽命標準、3.8 測試程序。試驗在科恩Evo微型銑床上進行,主軸最大轉速為50,000 RPM。使用的銑刀是WOTEK的0.5 mm的AlTiN塗層碳化鎢立銑刀。銑削了25 mm長的直槽,深度為0.2 mm。工件和銑刀在整個切削過程中,使用合成的Hocut 768連續淹沒工件和銑刀。採用了以下加工參數。
每種材料所使用的不同切削速度和進給率可以通過使用滑動距離作為報告結果的獨立變量來說明。工件被安裝在一個3組份力傳感器(Kistler 9317C)上(圖11),能夠測量三維(x,y,z)與切削過程的主要軸線對齊的切削力。這被連接到國家儀器公司的數據採集系統(DAQ)和。 Kistler軟件用於分析記錄的數據。每次切削完成後,對銑刀進行成像(通過SEM)以測量磨損情況。
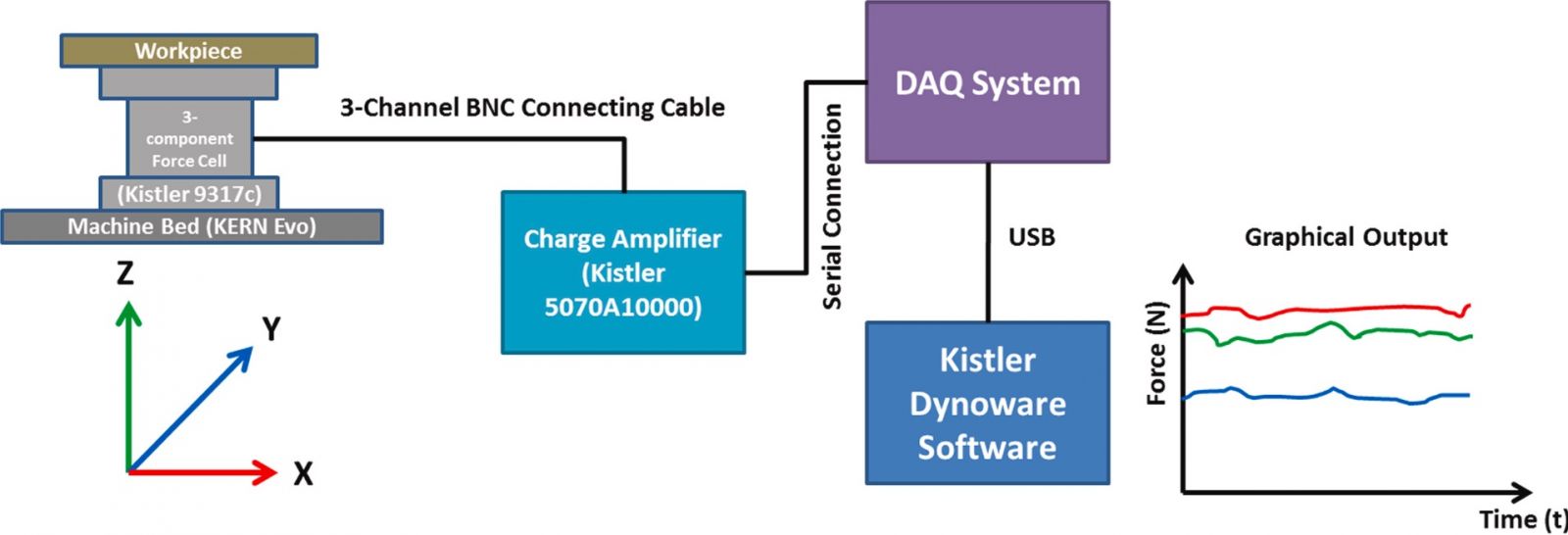
每種材料所使用的不同切削速度和進給率可以通過使用滑動距離作為報告結果的獨立變量來說明。工件被安裝在一個3組份力傳感器(Kistler 9317C)上(圖11),能夠測量三維(x,y,z)與切削過程的主要軸線對齊的切削力。這被連接到國家儀器公司的數據採集系統(DAQ)和。 Kistler軟件用於分析記錄的數據。每次切削完成後,對銑刀進行成像(通過SEM)以測量磨損情況。
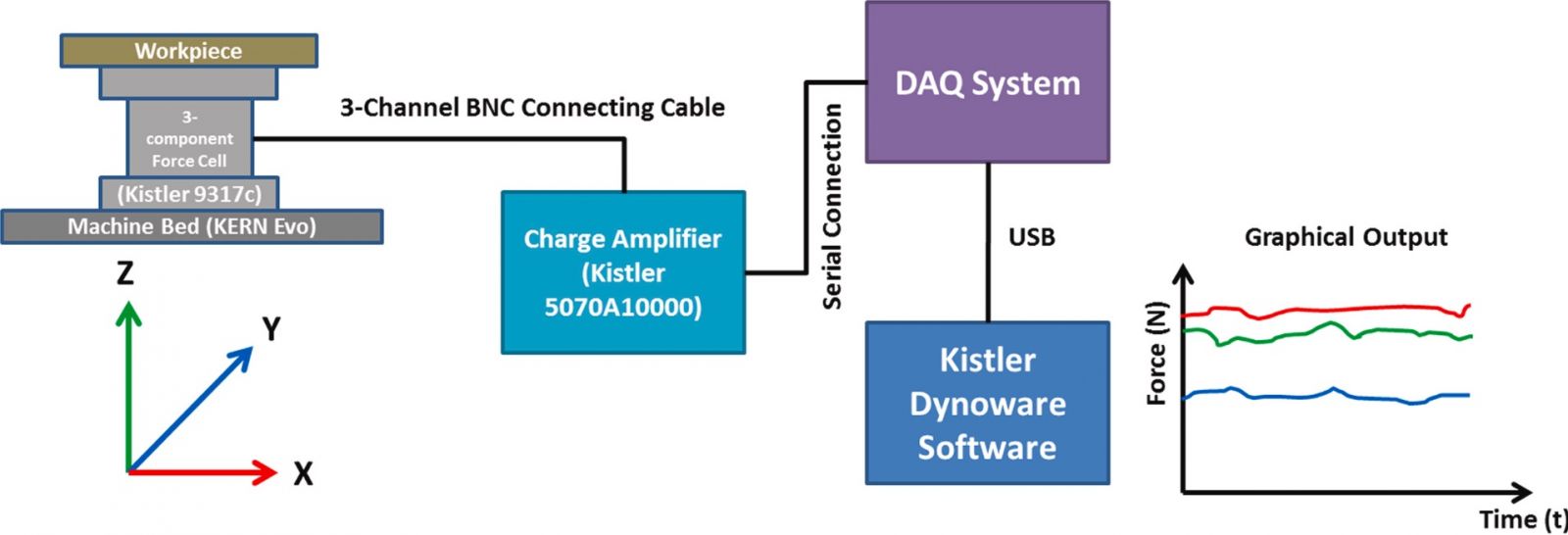
圖11.力測量設置示意圖。
然後,這項工作的結果被用於調查工具的磨損情況,以延長其使用壽命,並確認所述的測試方案。
4.2. 結果--哈氏合金、鈦和黃銅的S曲線觀察結果
4.2.1. Hastelloy(哈氏合金)
圖12顯示了哈氏合金C-276切削後的耙面磨損曲線。遺憾的是,在測量磨損方面的採樣率不理想(每隔21.84 m進行一次磨損測量),今後的研究設計是在較短的滑動距離後測量磨損。對於其中一個牙(牙號沒有物理意義),可以看到以下幾個階段的磨損情況。 一、銑刀磨合時的初始快速磨損(圖中黃色部分顯示為磨損)。二、 穩態磨損(綠色)。穩態磨損(綠色)。三、銑刀失效前的快速磨損(紅色)。銑刀失效前的快速磨損(紅色)。在銑刀壽命結束時,偶爾會出現一個表面上看是零梯度的區域,此時磨損已經超過了切削刃的長度:也就是說,銑刀不再有效地切削。這時,出現摩擦和軸的失效。而另一齒由於銑刀的初始狀態,在這些階段沒有明顯的附著力:這個齒已經被磨圓了。這就更加強調了對銑刀進行初步檢查以確保其達到最低標準的必要性。
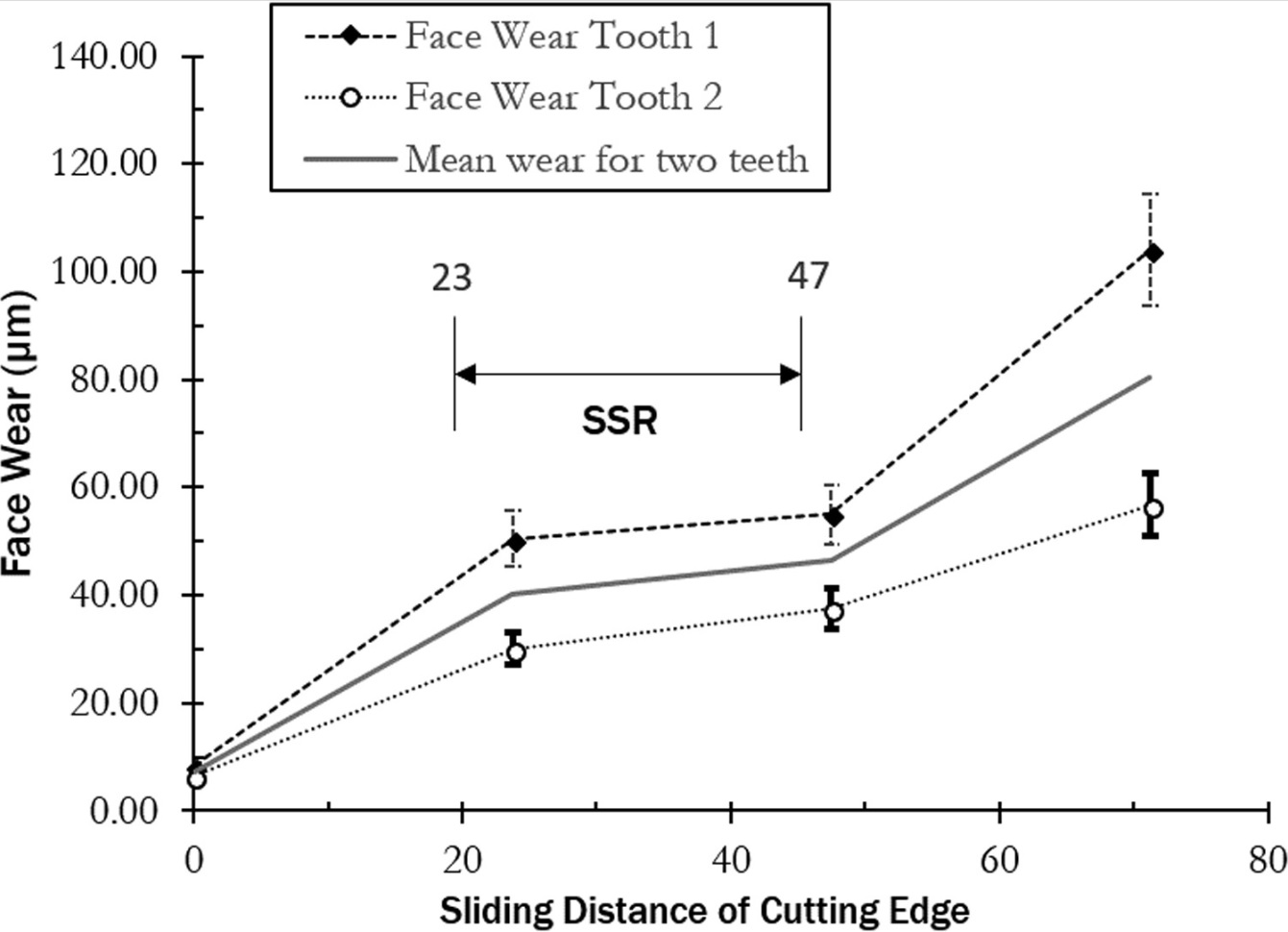
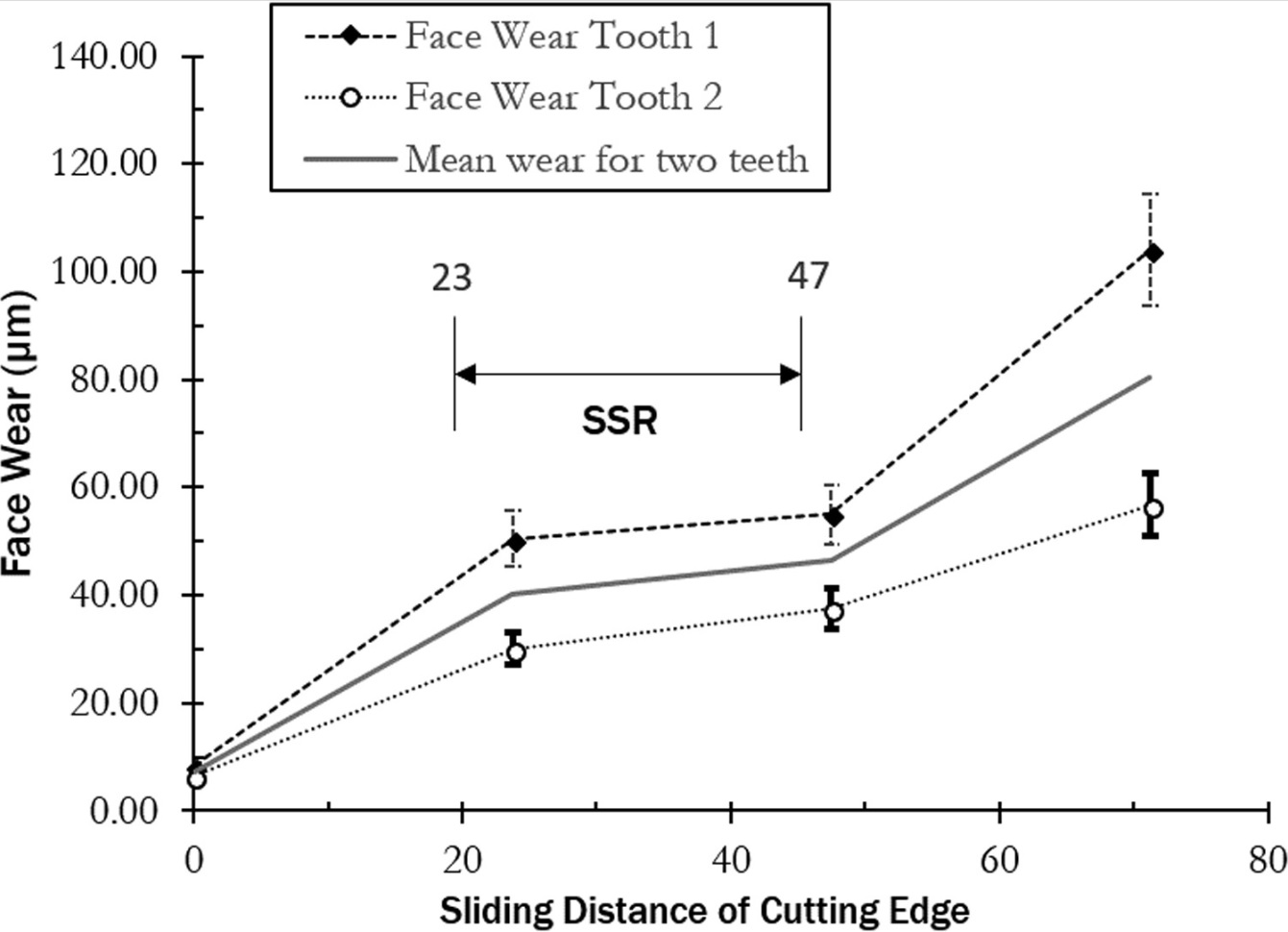
圖12.哈氏合金C-276加工銑刀端面磨損曲線 用於加工哈氏合金C-276的銑刀端面磨損曲線。
其中一個齒的銑刀磨損量比另一個齒的磨損量大。為了理解這一點,我們對銑刀的受力特徵進行了檢查,如圖13所示。從圖13中可以清楚地看出,其中一個齒的嚙合量比另一個齒大,因此切削力較大。這可能有兩個原因:一是第二個齒的初始磨損較大(事實上,這點在切削前的銑刀圖像中得到了驗證);二是銑刀的跑偏導致齒的嚙合不均勻。從現有的維修數據可知,機床主軸有一定的跳動。有報導稱,這種情況在微加工中非常明顯,一般來說,在銑刀較小的情況下,這種類型的行為在微銑中是典型的,有時只有一個齒嚙合。
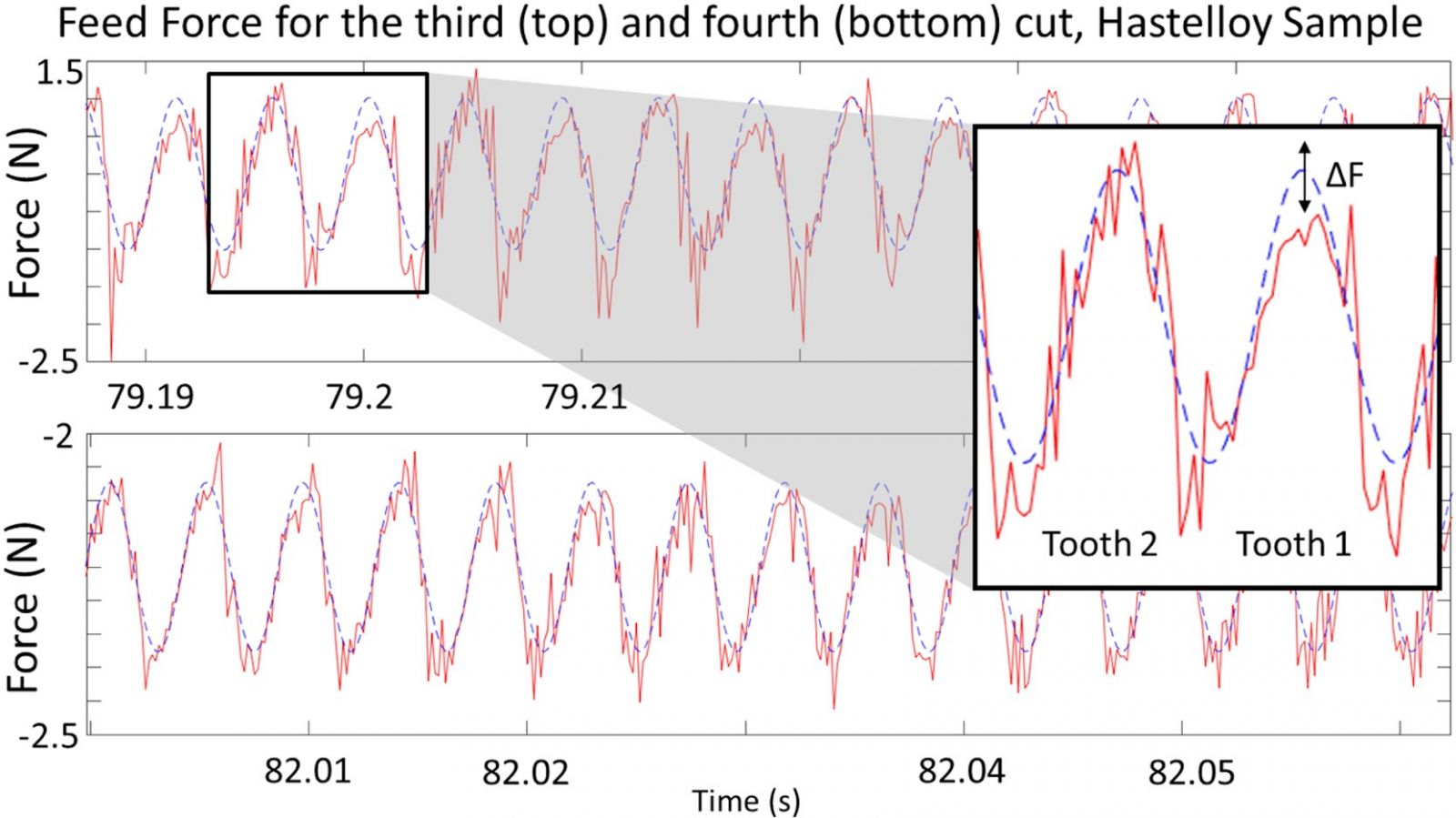
圖13.用於加工哈氏合金C-276的刀具的力特徵。
外部切削刃數據(圖14)顯示,由於測量點太少,再加上測量非常小的銑刀時固有的波動性,因此與傳統的磨損曲線幾乎沒有什麼關係。
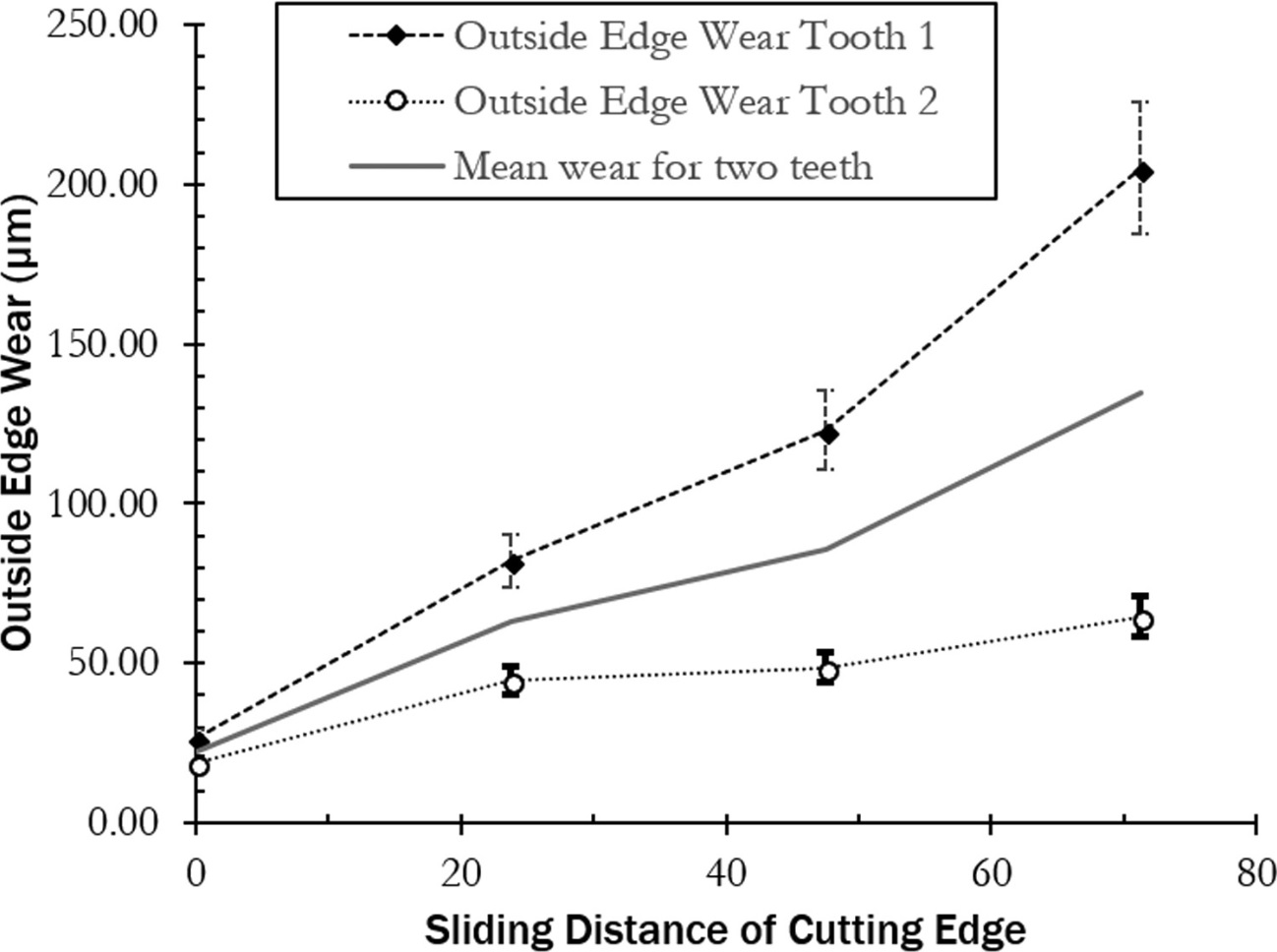
圖14.哈氏合金C-276加工銑刀外刃磨損曲線 用於加工哈氏合金C-276的銑刀外緣磨損曲線。
側面磨損(圖15)顯示出比刀面或外緣磨損更一致的結果,而且在磨損階段上似乎落後於刀面磨損。在這裡,銑刀的初始質量不那麼顯著,因為側翼面與銑刀的前緣相距較遠,而且兩個齒都呈現出經典磨損曲線的前兩個階段。
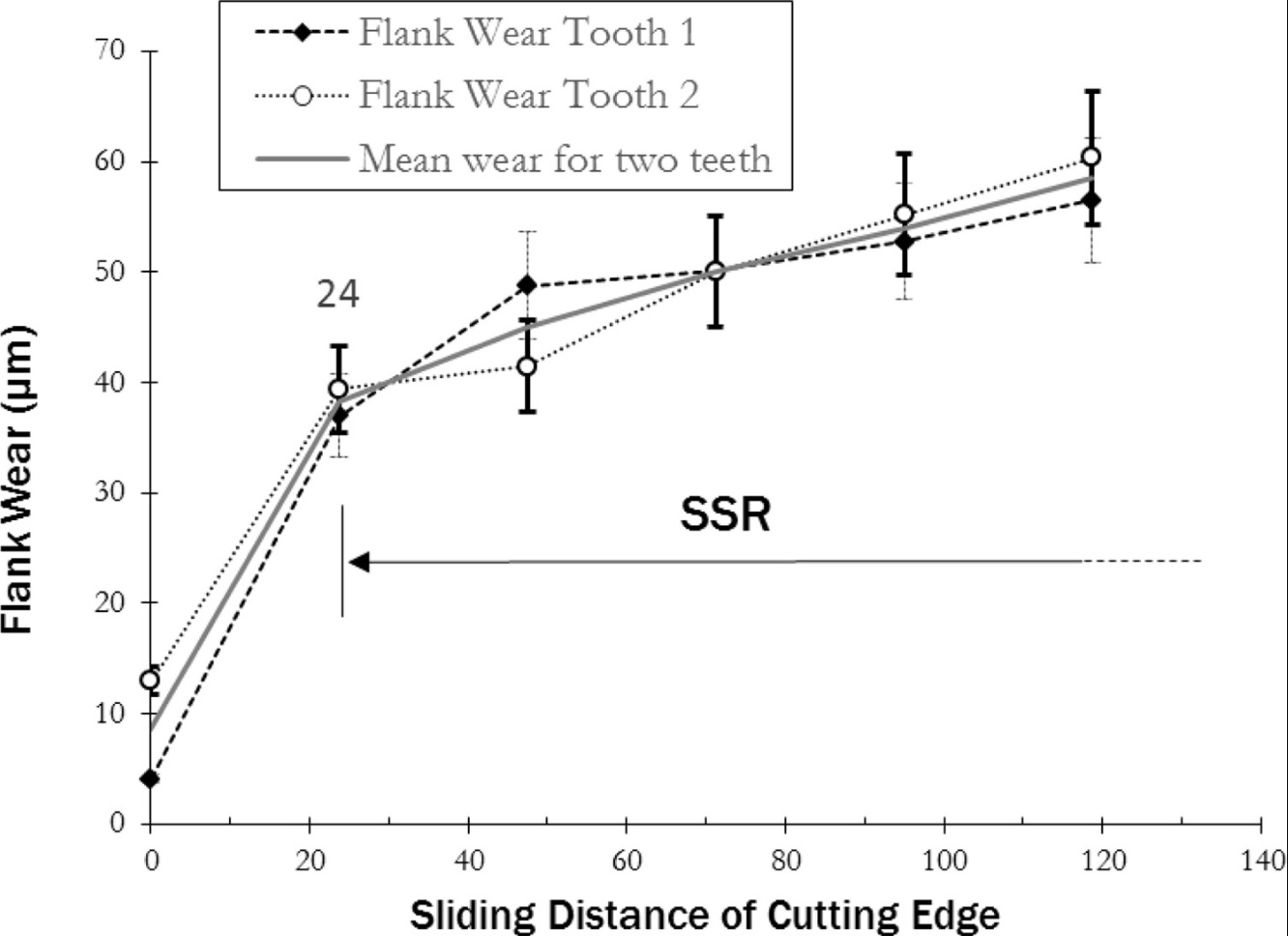
圖15. 用於加工哈氏合金C-276的立銑刀外緣磨損曲線。
4.2.2. 鈦合金
對於用於切削鈦合金的銑刀,耙面磨損曲線(圖16)顯示了一個典型的s曲線,最高約130 µm。磨損在大約35 µm到90 µm之間是穩定的,此後磨損迅速加速--因此,銑刀壽命標準,定義為銑刀開始快速磨損的點,被確定為90 µm或銑刀半徑的8%。
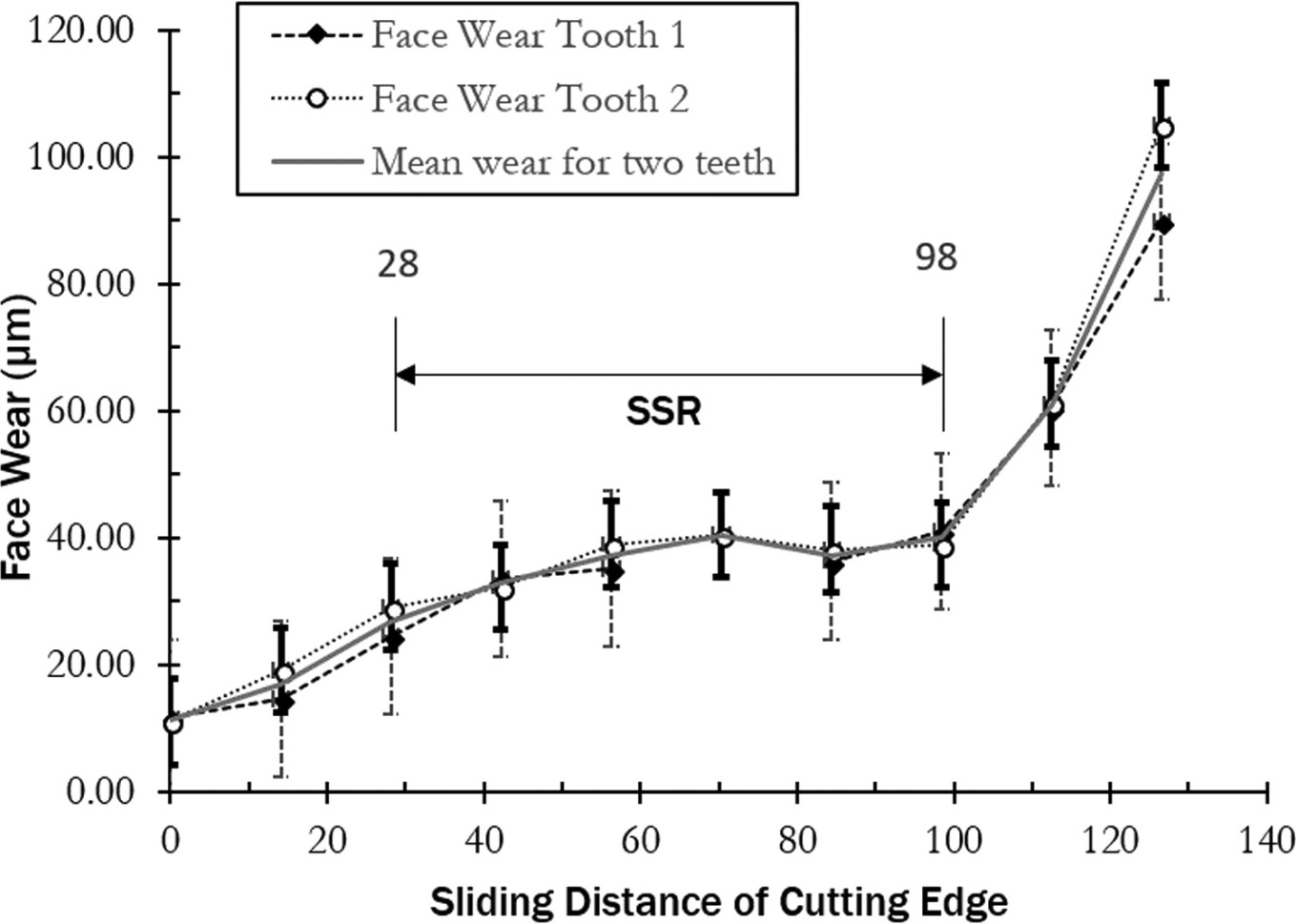
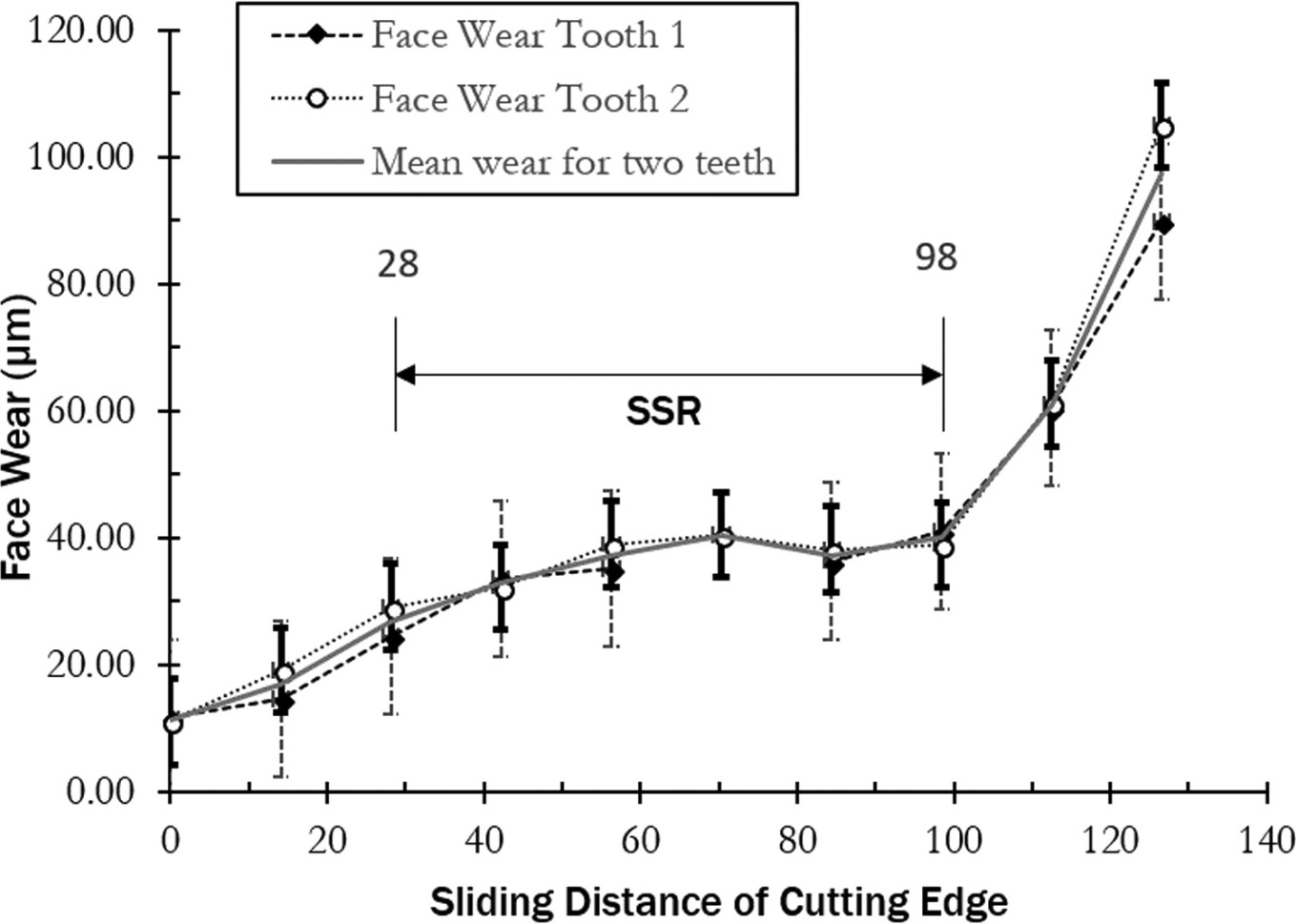
圖16. 用於加工2級鈦合金機床的銑刀端面磨損的銑刀磨損曲線。
磨損100微米後,整個切削刃已被磨掉,銑刀可被視為失效。銑刀軸的斷裂可能會發生,也可能不會發生,這取決於銑刀中心與工件的嚙合度是否達到可以進行切削的程度。
與哈氏合金銑刀一樣,外刃磨損(圖17)沒有顯示出明顯的傳統磨損曲線。由於工件上的切屑作為第三體的作用,磨料磨損會持續超過切削深度。這被潤滑油(冷卻液)排空,但在此過程中會擦過銑刀。磨損似乎在300微米的深度以上達到穩定狀態,這時切屑不再沿著軸向上移動,銑刀和材料之間的接觸很少。雖然外緣磨損不能提供一個清晰的銑刀磨損曲線,但銑刀外緣的磨損可能會影響到銑刀產生良好的表面光潔度,或者說影響到銑刀去除切屑的能力。因此,外緣磨損確實可以提供一些銑刀即將發生故障的跡象。
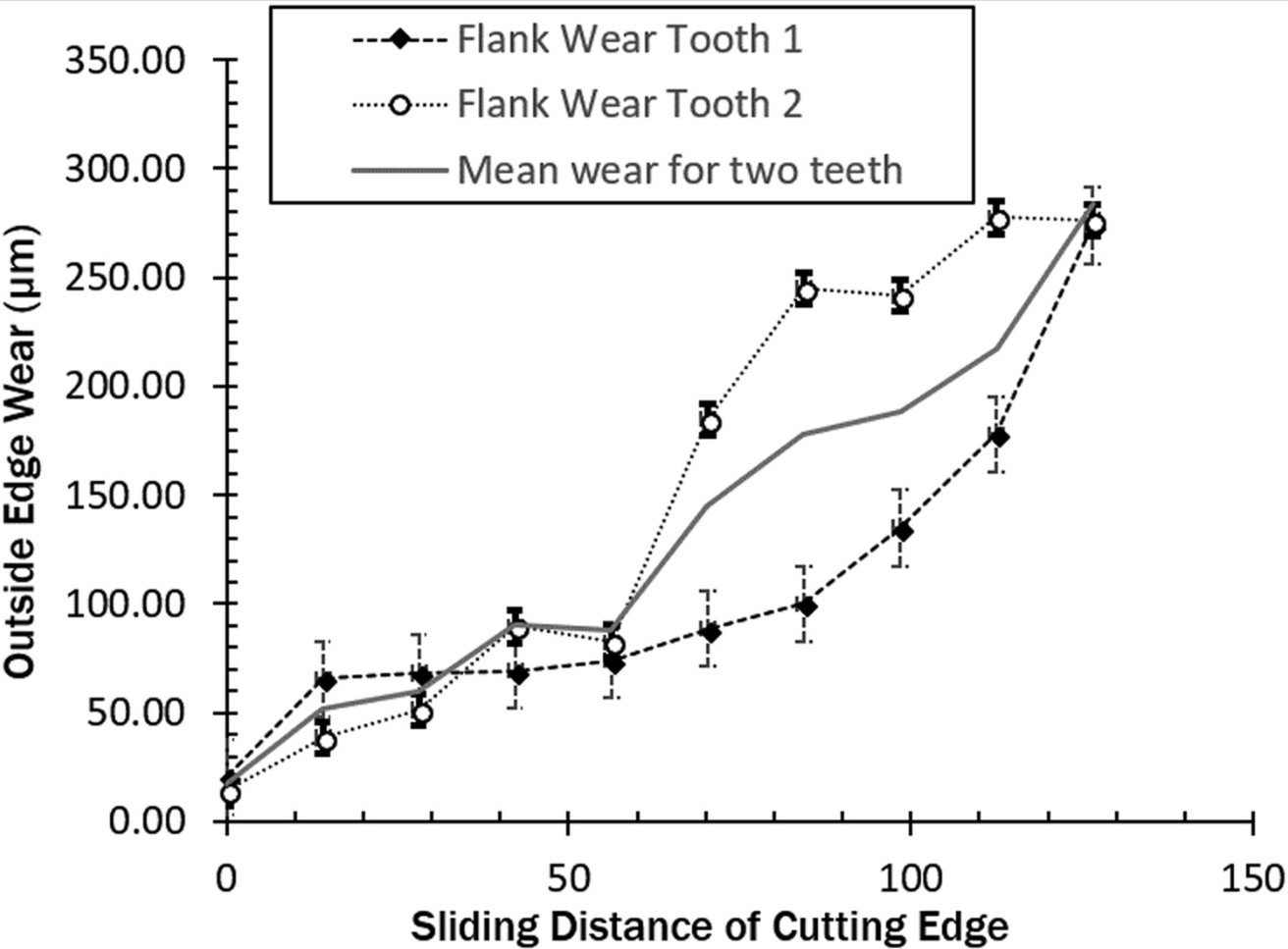
圖17. 用於加工2級鈦合金銑刀的銑刀外緣磨損曲線。
另一方面,側面磨損則顯示出S型曲線,與端面磨損一樣(圖18),唯一明顯的區別在於每個磨損階段達到的點。
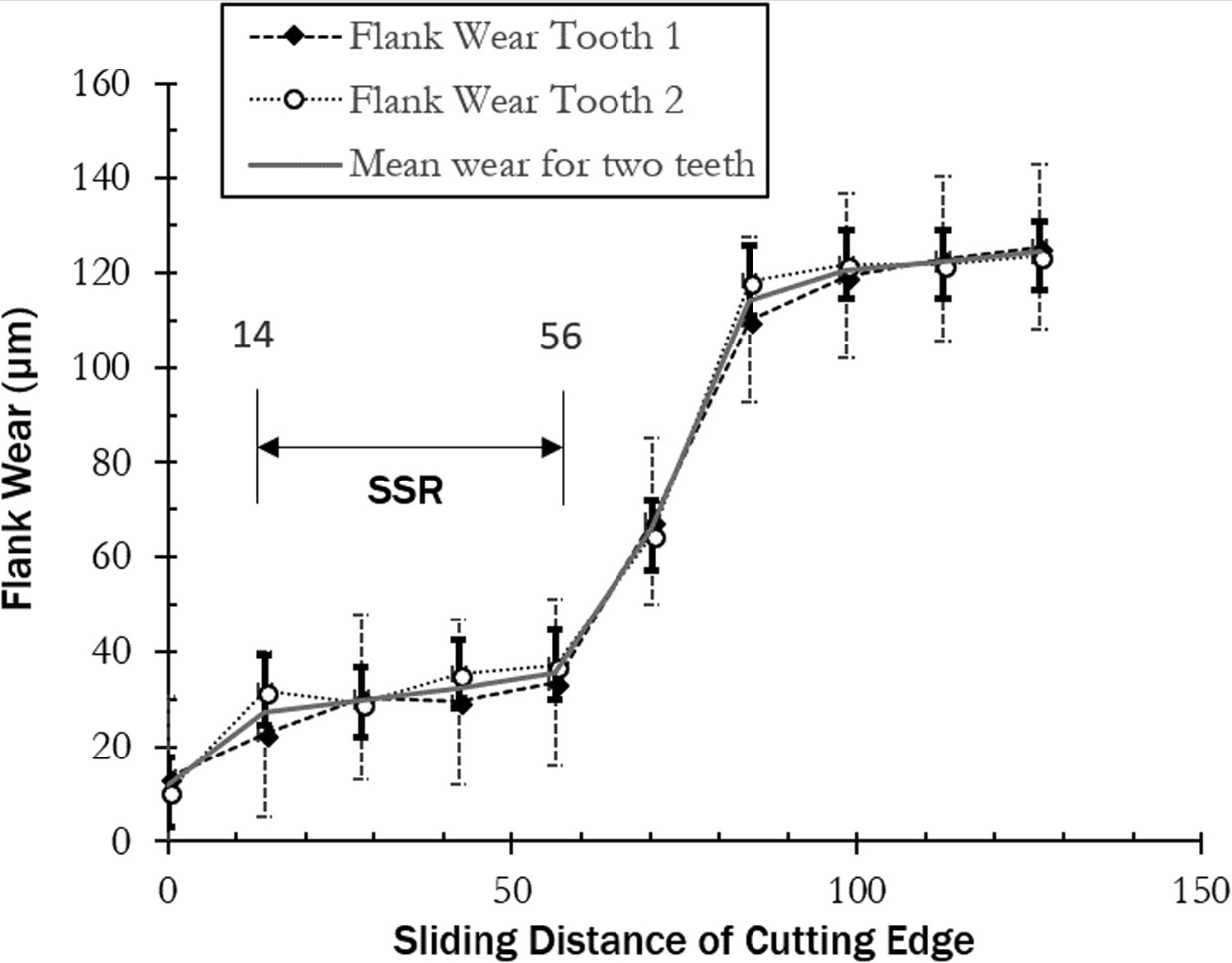
圖18. 用於加工Ti級2號機的立銑機側面磨損曲線。
所得到的銑刀磨損曲線的形狀與傳統的銑刀磨損曲線非常相似--正如Bahrudin等人所指出的那樣--在每種情況下,都可以看到傳統的s曲線。這使得臨界磨損點或銑刀壽命標準被確定為銑刀磨損不可容忍的點。根據工件尺寸公差的要求,實際的銑刀磨損量可能小於此值。
4.2.3. 黃銅
兩種不同類型的銑刀被用於加工黃銅:無塗層的銑刀和有AlTiN塗層的銑刀。基本銑刀為TiB2。至於鈦合金和哈氏合金,可以看到近似於S型曲線的形狀,但未鍍層的銑刀加工時間很短,數據有限。將加工黃銅的TiB2銑刀和塗有AlTiN的銑刀進行比較,可以清楚地看出,塗有AlTiN的銑刀的穩態部分比塗有TiB2的銑刀的長度高出一倍以上。此外,TiB2銑刀的穩態區域的磨損程度較高。其中一個TiB2銑刀在快速磨損之前就已經斷裂了(圖19)。在圖中可以看到耙面磨損,因為塗層黃銅銑刀的磨損曲線來自於2.3節中描述的初步研究,其中只看到了耙面磨損,因此這是唯一可以比較的磨損測量結果。
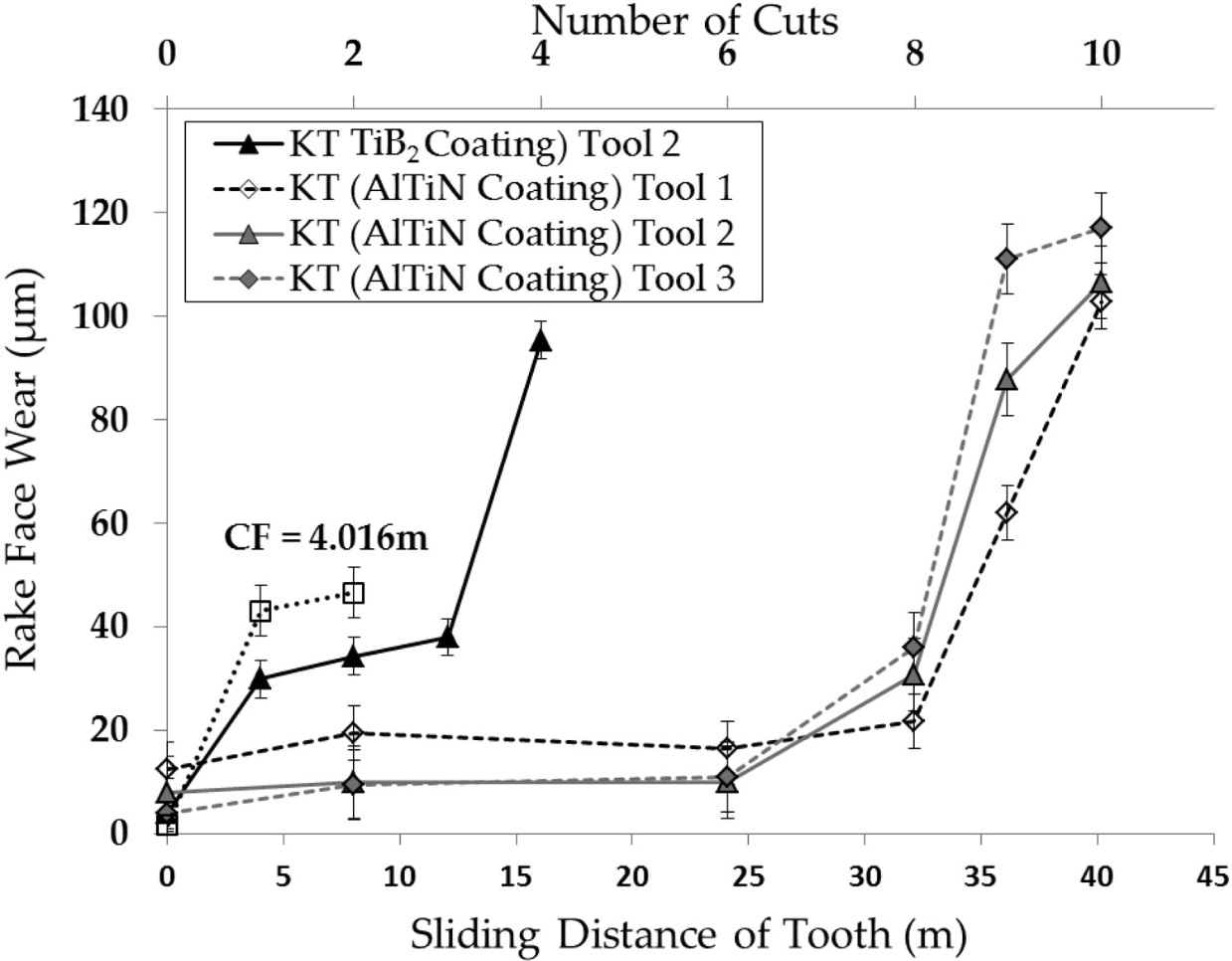
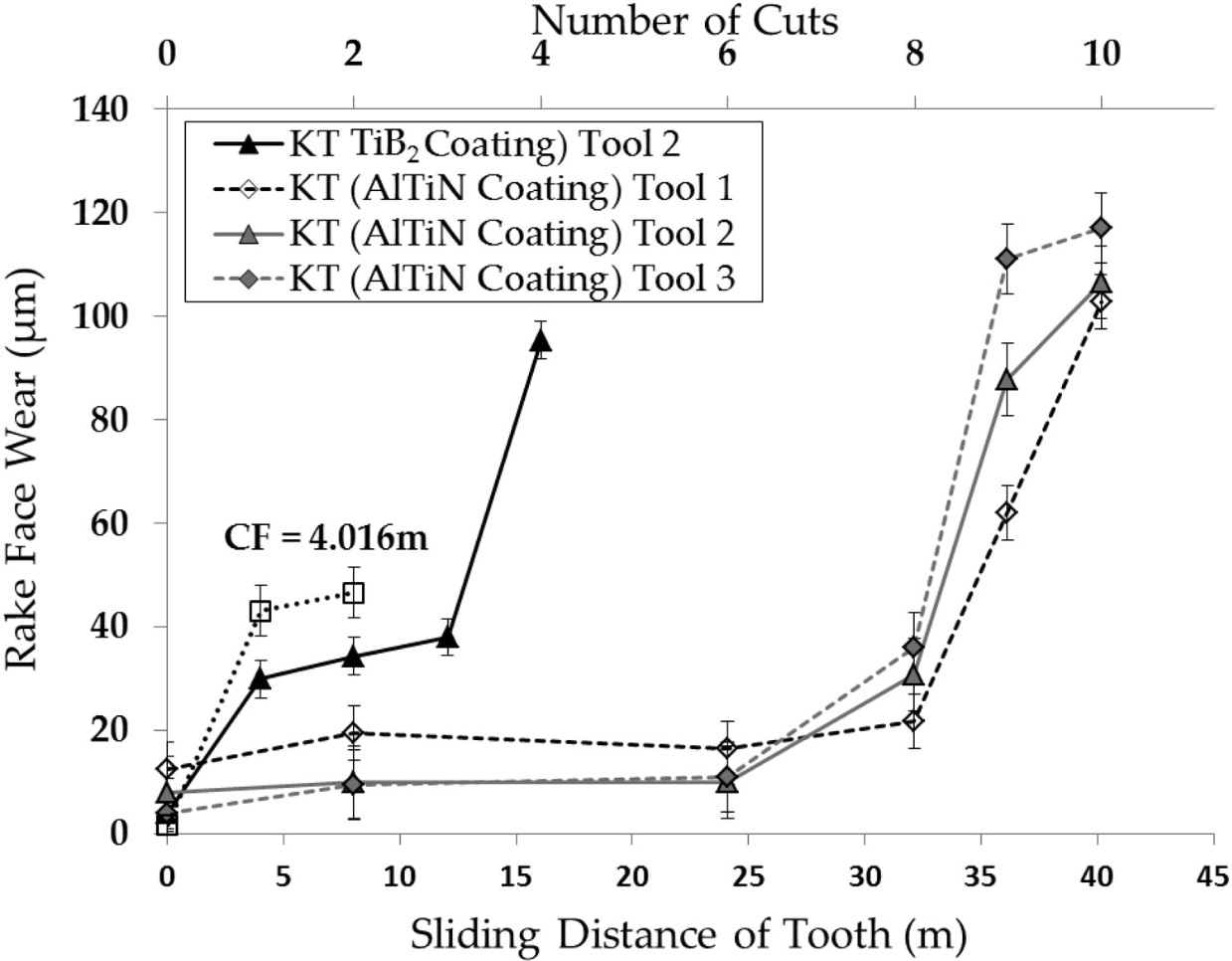
圖19.未塗層和塗層銑刀的耙面磨損 用於加工黃銅的無塗層和塗層銑刀的耙面磨損。 CF表示災難性的銑刀故障。
5. 對協議的反思
第4.2節描述了使用第3節中描述的協議獲得的結果。使用所描述的成像方法,可以看到清晰的磨損曲線,包括耙面和側翼磨損。其他的指標,如槽形,已在第2.2節中討論過,未能提供盡可能多的信息。本節將考慮協議的每個部分及其相對的成功,以確定協議中的哪些部分可以被認為是最佳的嚙合工具時的結論。
5.1. 新方法對銑刀直徑的改進
如第2節所討論的,可以用直徑減小來描述銑刀磨損。然而,除了沒有考慮到銑刀幾何形狀和不均勻齒磨損等特徵外,從第4.2節中的銑刀磨損曲線可以看出,側翼磨損和端面磨損會導致不同的極端磨損開始發生的點,甚至外緣磨損雖然不產生曲線,但可以提供銑刀崩裂和即將失效的信息。銑刀的使用壽命應確定為刃部或端面磨損達到第三階段的點,在鈦合金工件的情況下,刃部磨損就是刃部磨損。這不是簡單的直徑測量所能反映的。雖然一旦知道了銑刀壽命標準,測量直徑可能就足夠了,但不能用來確定直徑。由使用這裡描述的協議所產生的數據,可以測量每個齒的磨損情況,這樣可以更清楚地了解銑刀的磨損情況,以更一致的方式,比以前進行的更多。
5.2. 測量槽形輪廓作為加工後銑刀磨損方法的有效性
圖20顯示了使用3.6節中描述的方法觀察到的鈦樣品的銑刀磨損情況。可以看到側面的磨損和耙面的磨損。
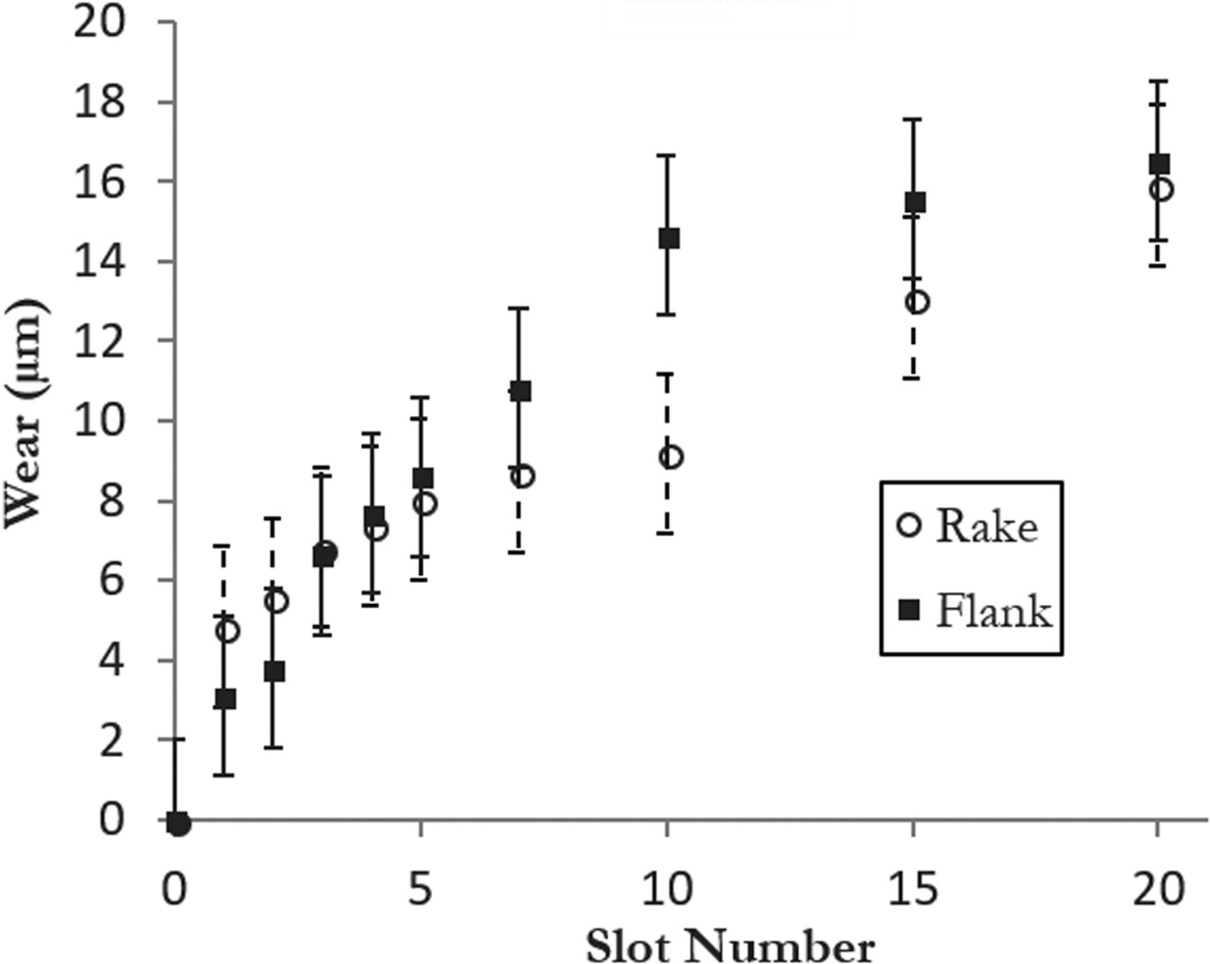
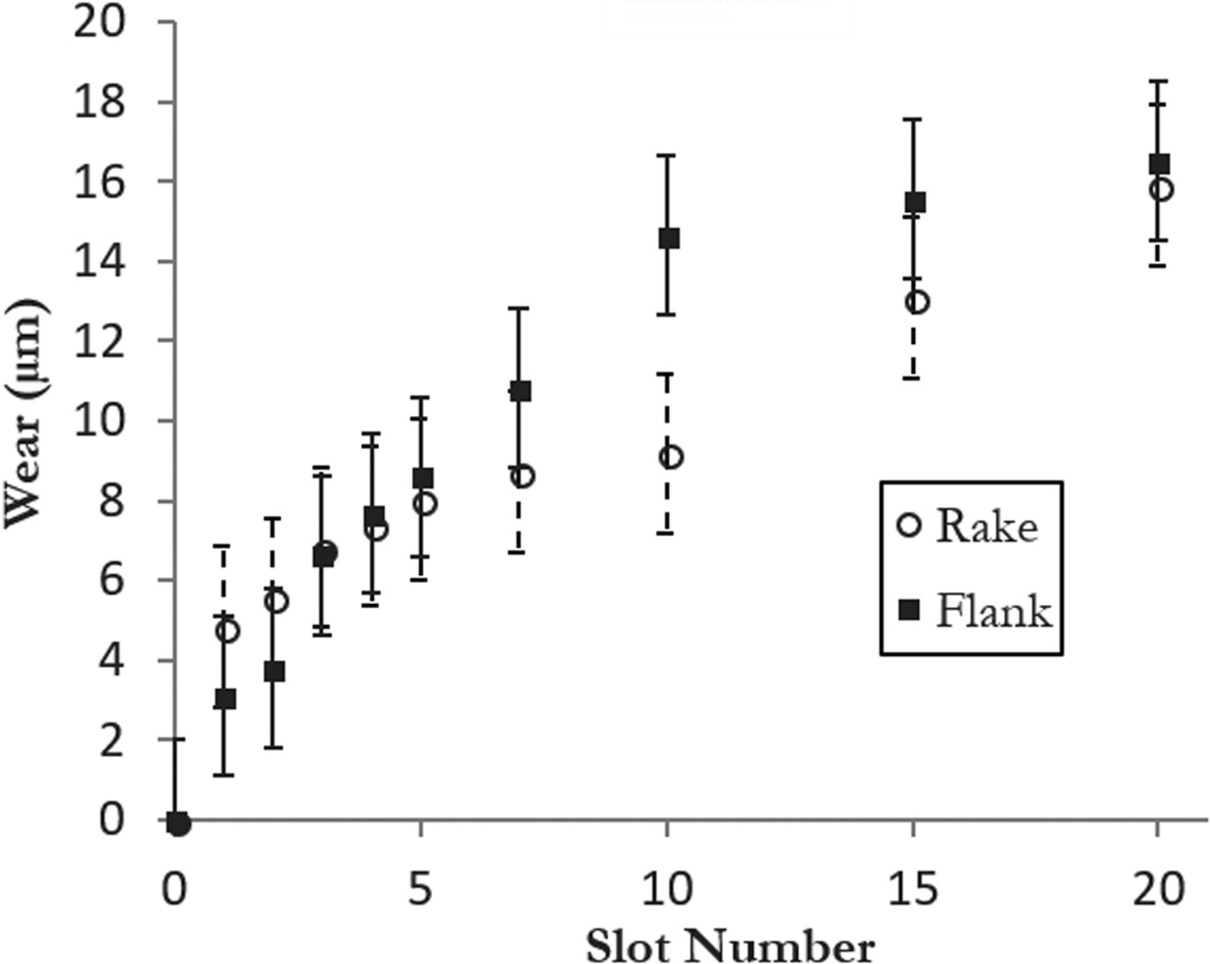
圖20. 使用2級Ti的槽型尺寸測量的銑刀磨損曲線。
這種方法的一個問題是,如果工件在最初的平移階段後被移走,其在夾具中的方向不是完全垂直於銑刀。這導致了Wf和Wr的誤差,如圖中所示。這樣做的結果是無法用這種方法確定銑刀的絕對磨損。但是,仍然可以確定磨損的穩態截面,這表明,經過細化,這種方法可以作為快速分析銑刀磨損的方法。通常情況下,工件角度的誤差會非常小。
此方法不能用在銑刀被拆下的地方,因為銑刀和工件的重新定位會導致系統誤差變大和隨機性,結果變得不可靠。
5.3. 滑動距離與切削距離比較
如第3.3節所述,滑動距離比切削距離或切削時間更適合用來計算銑刀磨損,因為銑刀的工作量取決於主軸轉速(RPM)和進給速度。
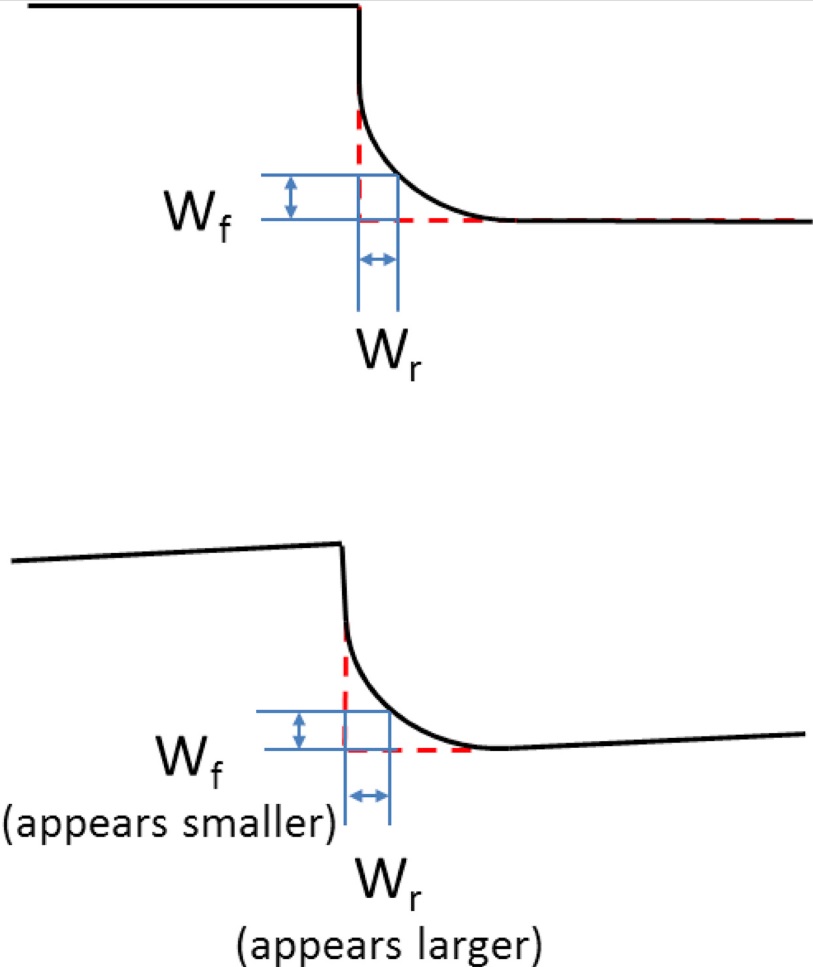
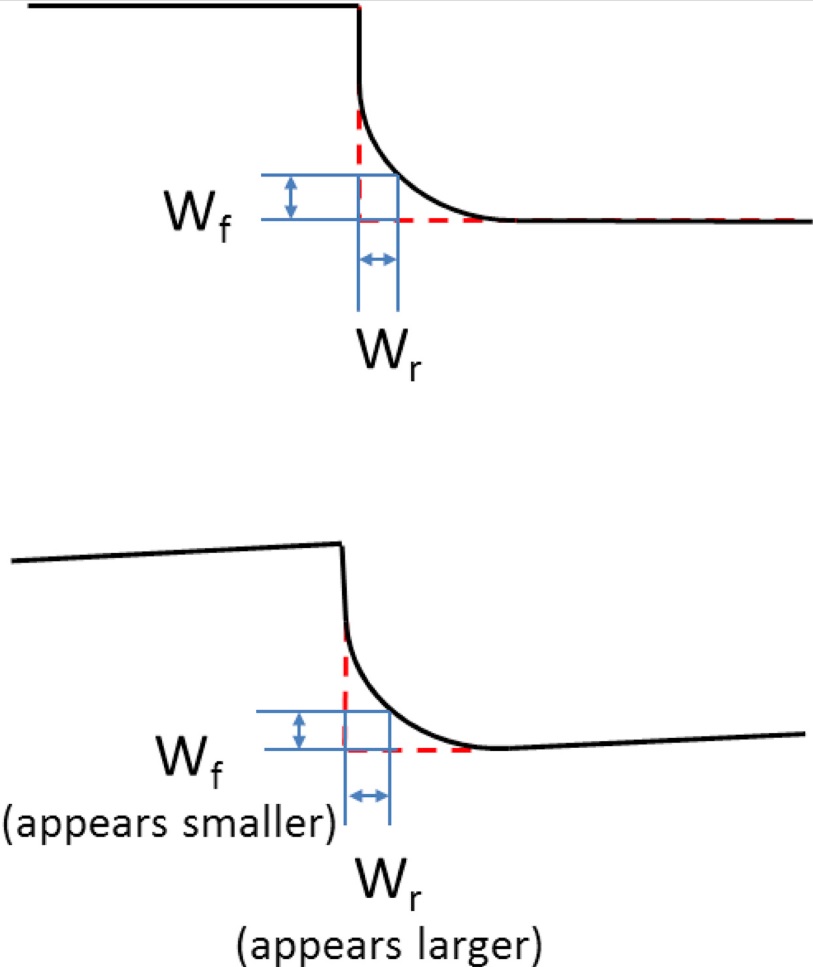
圖21. 測量槽位時可能出現的誤差來源。
如圖22所示,當用切削距離比較鈦和哈氏合金的銑刀磨損情況時,用於切割哈氏合金的銑刀進入第三個磨損階段,與用於切割鈦的銑刀進入穩態磨損階段的切削距離大致相同。這種比較有誤導性,因為切割哈氏合金的銑刀由於哈氏合金的切削阻力比較大,進給率和速度都比較低,所以用滑動距離繪製的圖更有代表性。使用滑動距離可以看出,即使考慮到切割哈氏合金銑刀的單位切削長度的滑動距離較高,這些銑刀的磨損速度也比切割鈦合金的銑刀快得多(圖23)。
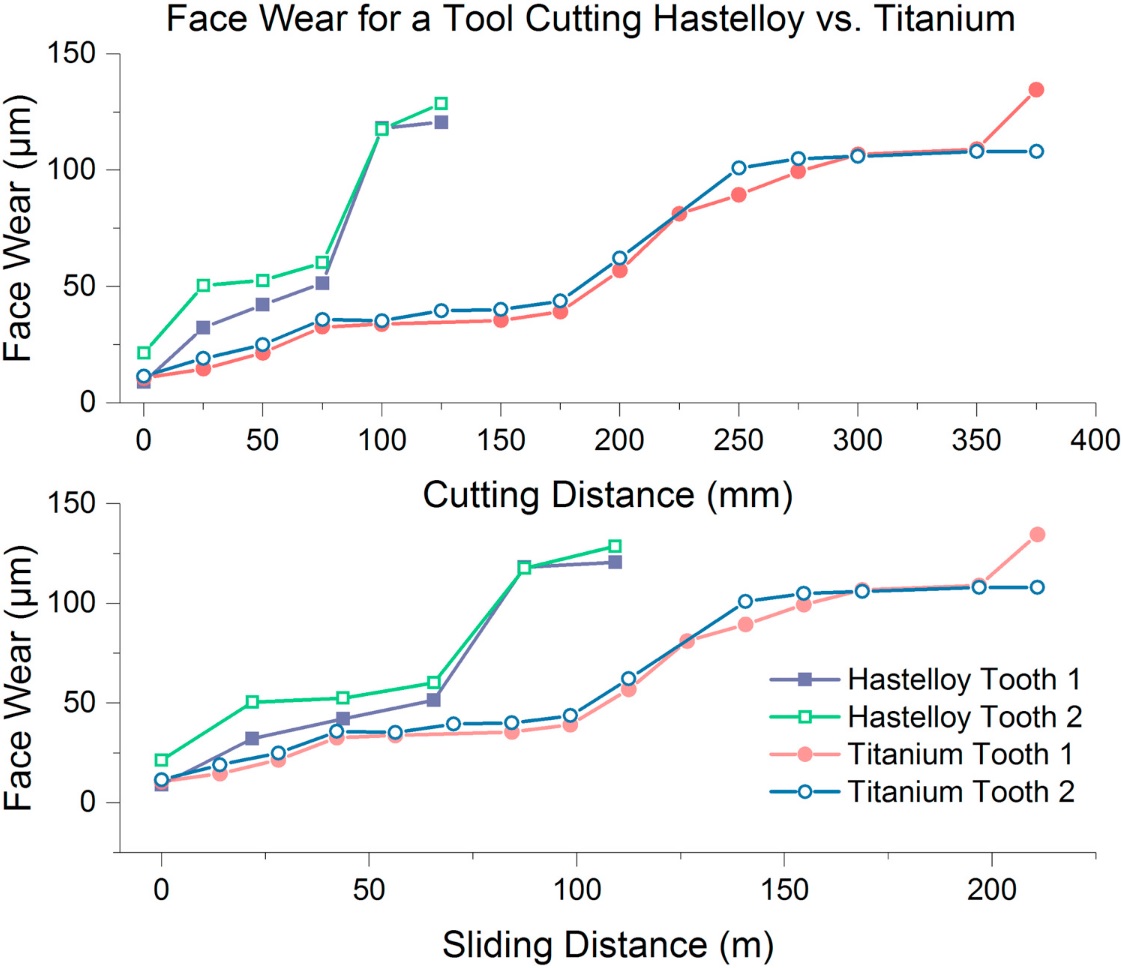
圖22. 測量槽位時可能出現的誤差來源。
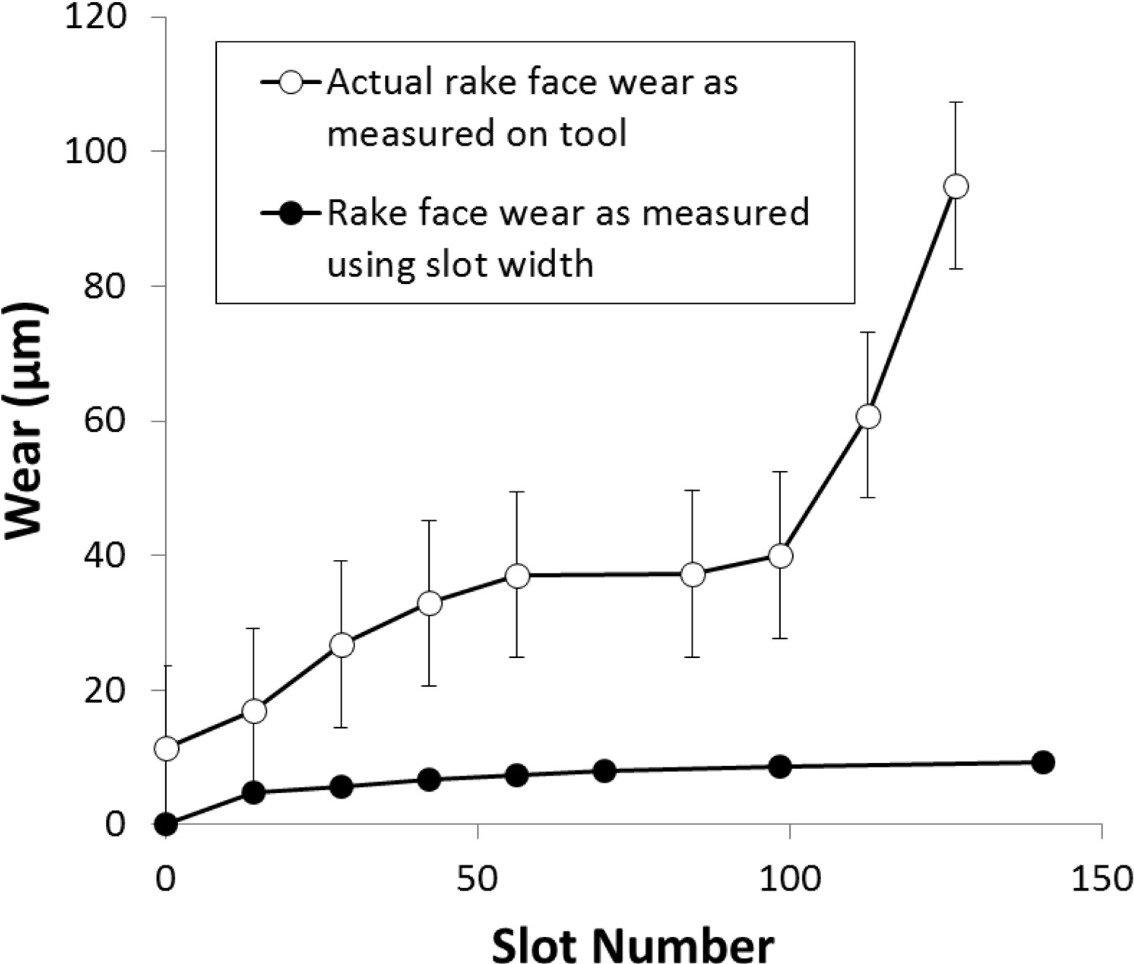
圖23. 測量槽位時可能出現的誤差來源。
5.4. 銑刀直接測量與槽位測量相比
圖為用於切削鈦合金銑刀的槽形測量與銑刀實際測量的比較。從圖中可以看出,對耙面的槽形測量(用3.6節中描述的方法測量)並不能準確描述銑刀的磨損曲線,因此不能得到正確的磨損曲線。這表明一個事實,雖然槽形曲線可以作為一種快速識別磨損發生位置的方法,但要獲得銑刀磨損的詳細信息,需要直接測量。
5.5. 耙面磨損與切削力
耙面磨損與切削力的進給分量比較二者之間的關係。對哈氏合金的這種比較可以從圖24中看到:兩種齒的耙面磨損情況相似,第1階段和第2階段之間的過渡(如第5節所述)發生在滑動距離22米時,銑刀壽命標準發生在滑動距離65米時。
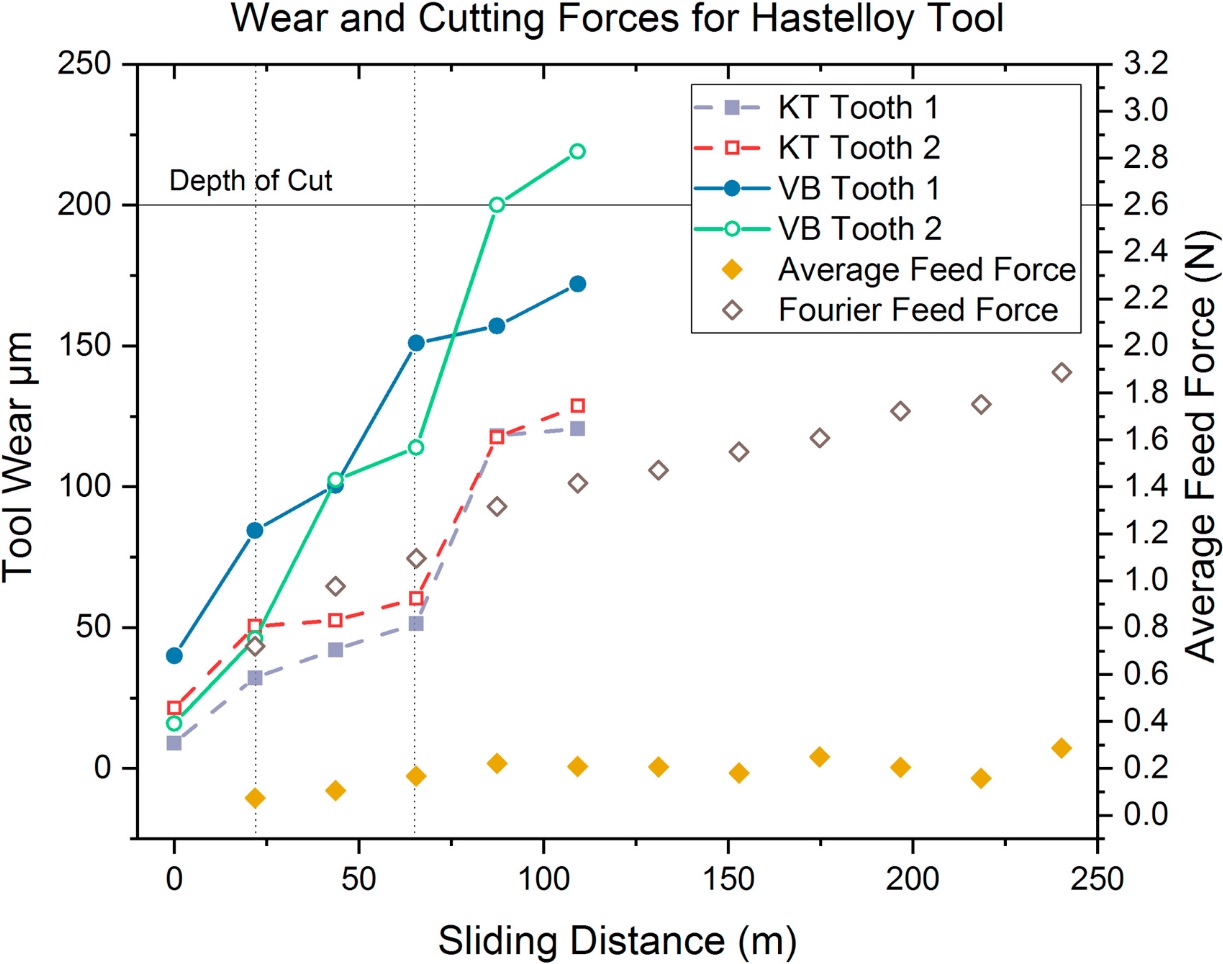
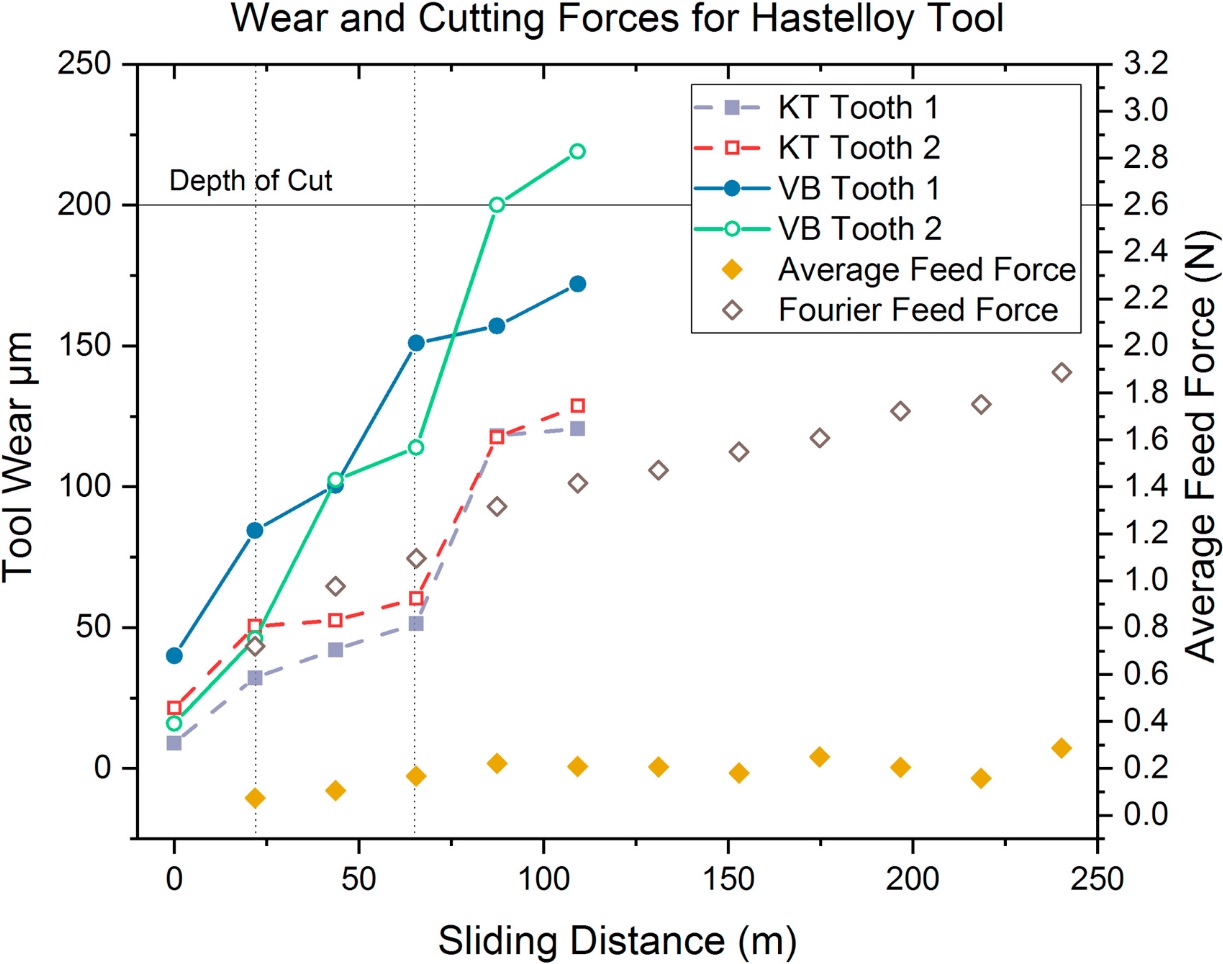
圖24:哈氏合金C-276銑刀的磨損與切削力的關係 圖24. 用於切割哈氏合金C-276的銑刀的磨損與切削力的關係。
從這兩組力數據中可以看出,平均進給力和進給力範圍(銑刀震動)最初都隨著銑刀磨損而增加,但這種增加的速度隨著銑刀磨損而趨於平緩--這與銑刀磨損嚴重到銑刀與工件之間幾乎沒有嚙合的假設是一致的。
與哈氏合金的數據相比,用於切割第一個鈦樣品的銑刀的數據點明顯多了。最初看到的是一個明顯的S曲線(圖25),在滑動距離為42 m時出現穩定狀態磨損,在滑動距離為99 m時出現銑刀壽命標準。平均進給力持續增加,而且有趣的是,即使在銑刀磨損梯度最低時(即第二階段),平均進給力也會隨著滑動距離的增加而線性增加。平均進給力只有在切削結束時,由於缺乏嚙合,銑刀磨損達到峰值時,平均進給力才會達到峰值。力的傅里葉變換也開始呈線性增加,但在穩定狀態區域後,可能是由於銑刀與工件接觸減少,力的傅里葉變換也開始呈線性增加,但在穩定狀態區域後,力的峰值就會下降。
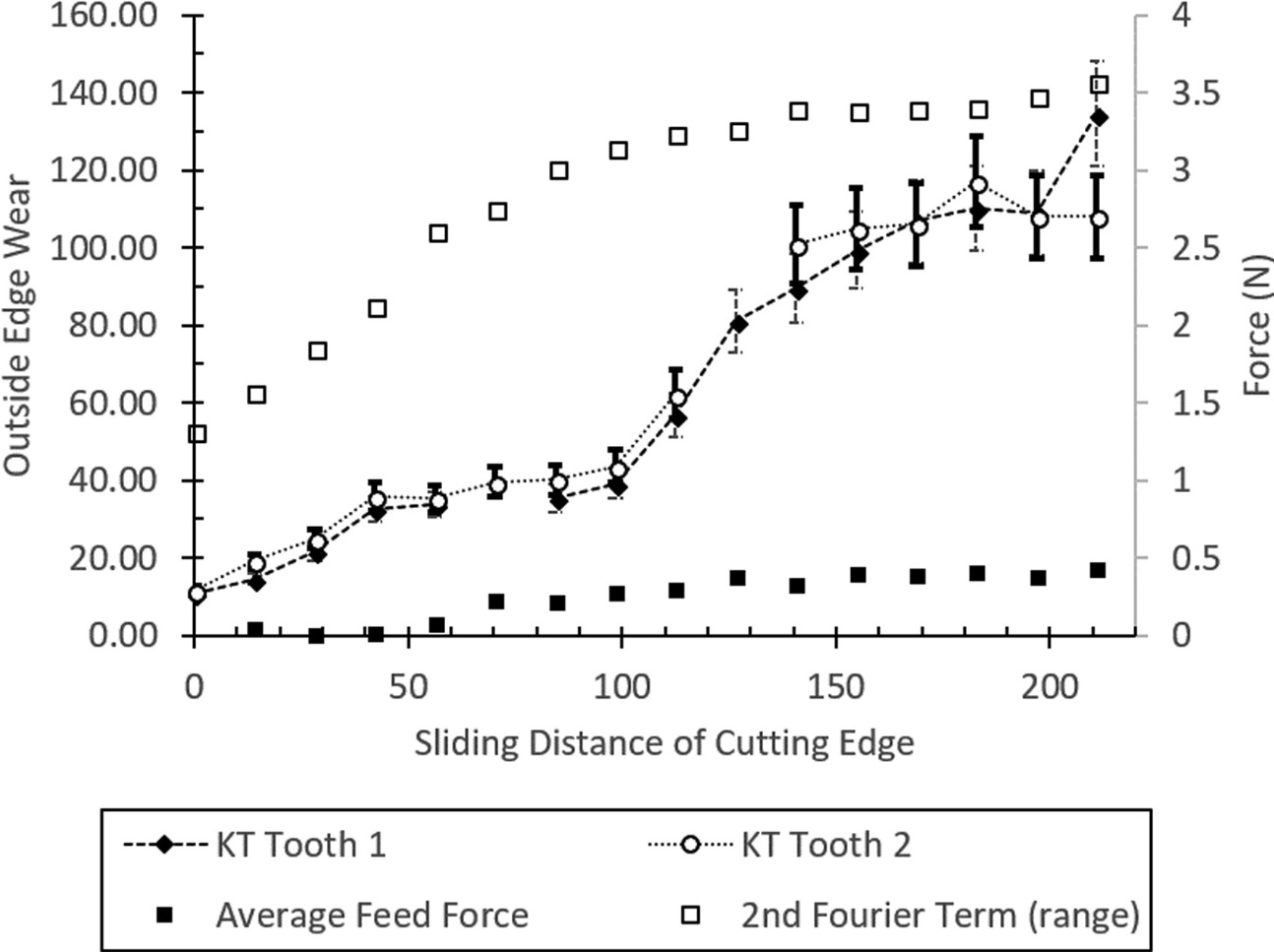
圖25.用於切削2級鈦合金銑刀的磨損與切削力的關係。用於切削2級Ti的銑刀的磨損與切削力的關係。
除了初始刃口圓度對較小的銑刀有更大的意義外,塗層厚度可能更重要:既因為它佔銑刀直徑的比例更大(2μm的厚度代表銑刀直徑的0.4%,而5mm立銑刀的厚度為0.04%),也因為它增加了初始刃口半徑。這裡討論的結果的一致性問題再次表明,在未來的研究中,確保在切削前對銑刀進行仔細檢查的重要性,並加強了對微型銑刀磨損測量標準協議的必要性。
5.6. 切削力特徵----觀察齒的不均勻嚙合情況
對每個切削力特徵進行了調查。齒間的切削力信號的差異程度不同,圖26中給出了一個哈氏合金切削的例子。
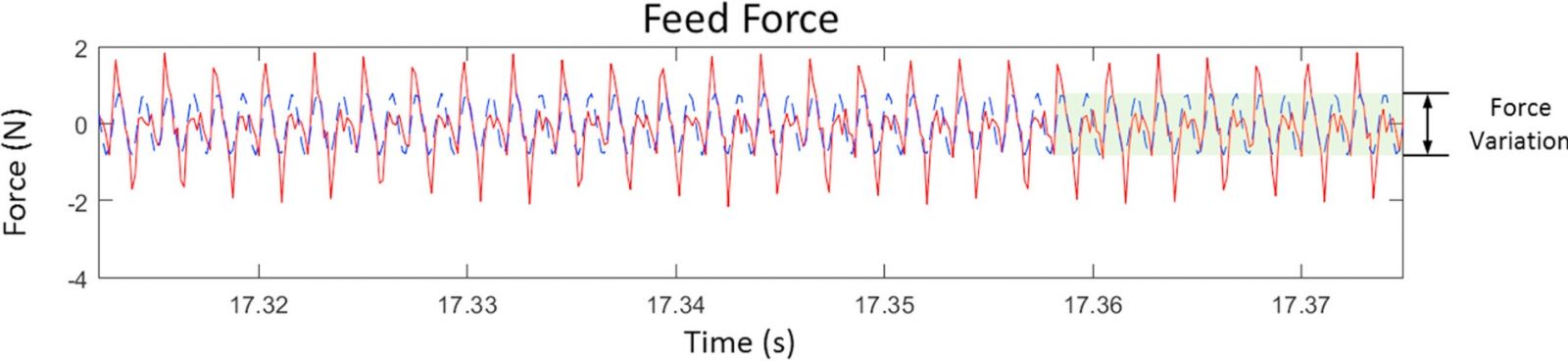
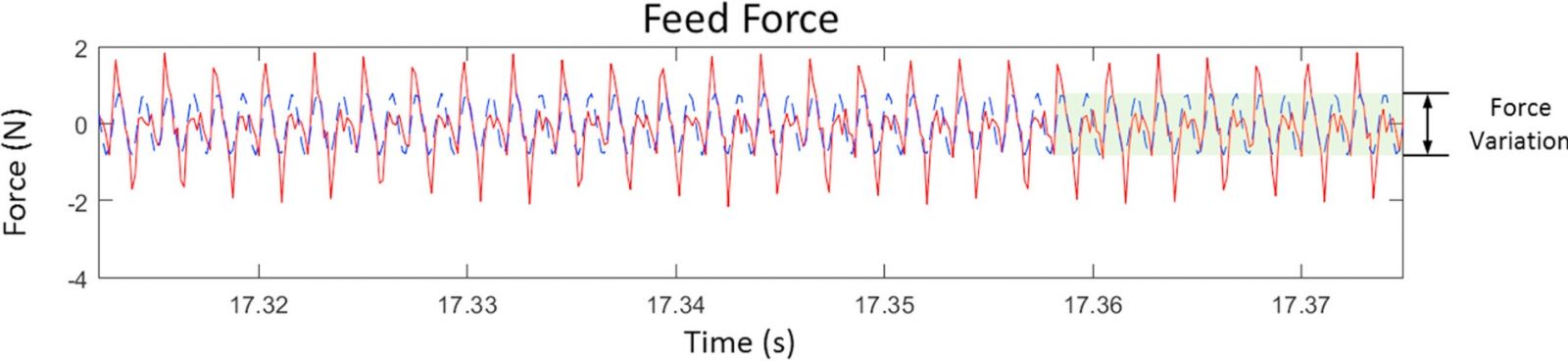
圖26.利用傅里葉數列的第二項進行擬合。使用傅里葉數列的第二項進行的擬合。
未經分析的銑刀受力特徵表明,刃的磨損嚙合往往比宏觀銑刀更不均勻。這種情況以前也曾見過。 Mativenga和Hon報告的嚙合力差不超過30%。同樣地,Kim和Jeon觀察到,8、12和14mm立銑刀切削Al6061-T6鋁合金時,在50N範圍內的力差約為10N(小於20%),但在微加工中,力的大小要小得多。此外,銑刀的跳動對於較小的銑刀意義更大,如圖27所示。如前所述,由跳動引起的齒的不均勻嚙合會導致每個齒的磨損程度與微銑加工時不同。這導致了兩刃的受力特徵會有明顯的差異。在每個刃的磨損曲線非常相似的情況下,預計每個刃的受力特徵也是相似的。
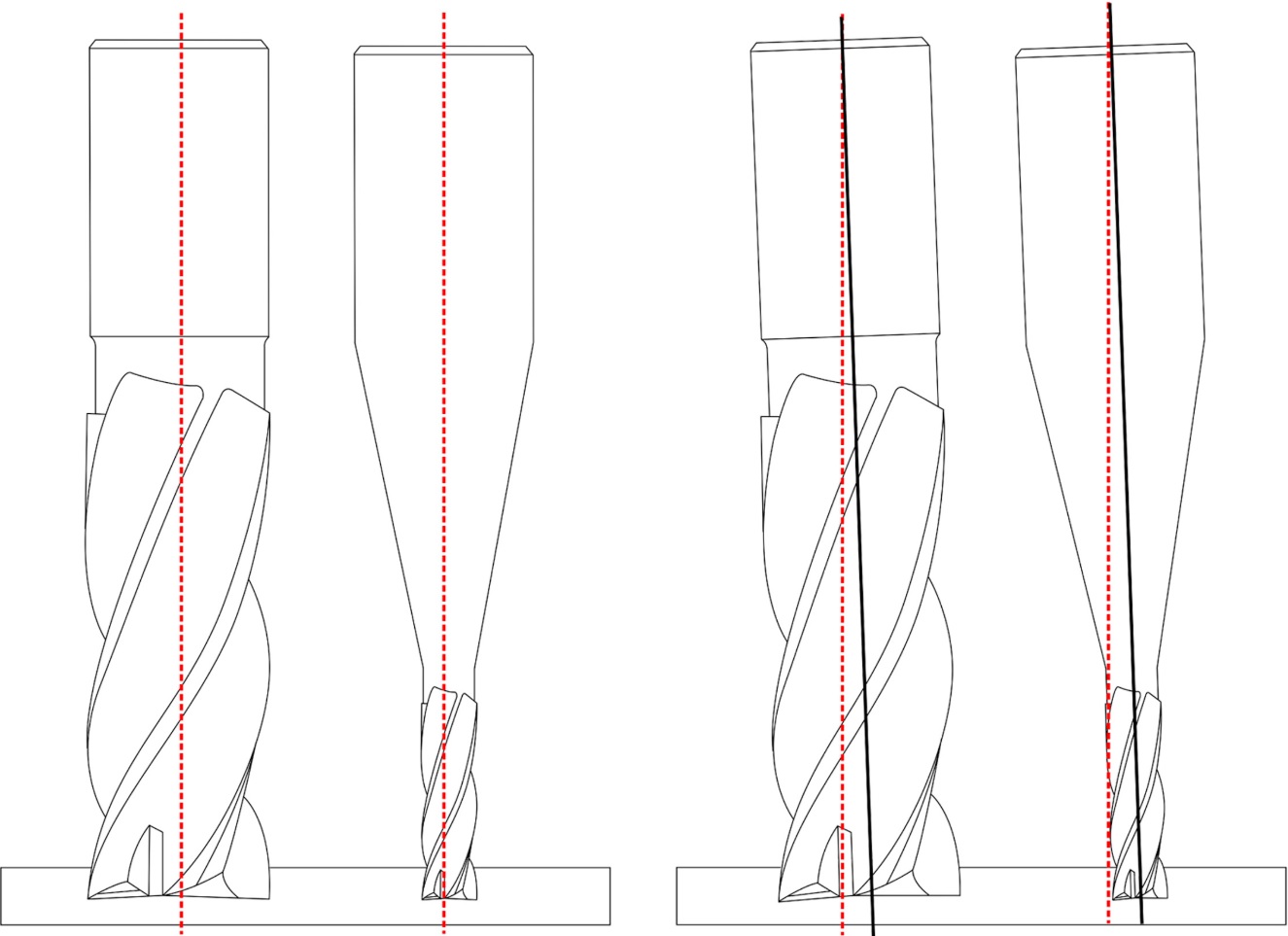
圖27. 對於較小的工具,跳動的影響被放大了。
5.7. 銑刀破損機制
微銑加工中的一個主要考慮因素是工件晶粒相對於銑刀的相對尺寸。圖28顯示了哈氏合金的晶粒尺寸(近似比例)。許多晶粒的尺寸在10米左右,是銑刀直徑的2%。這種結構在銑刀上顯得不均勻,因此,切削力在不同的通道上會有很大的變化。這就導致了銑刀不時地突然斷裂,而不是宏觀銑削時的平滑、均勻磨損。為了進一步了解銑刀斷裂的機理,觀察銑刀磨損過程中產生的切屑是非常有用的(圖29)。
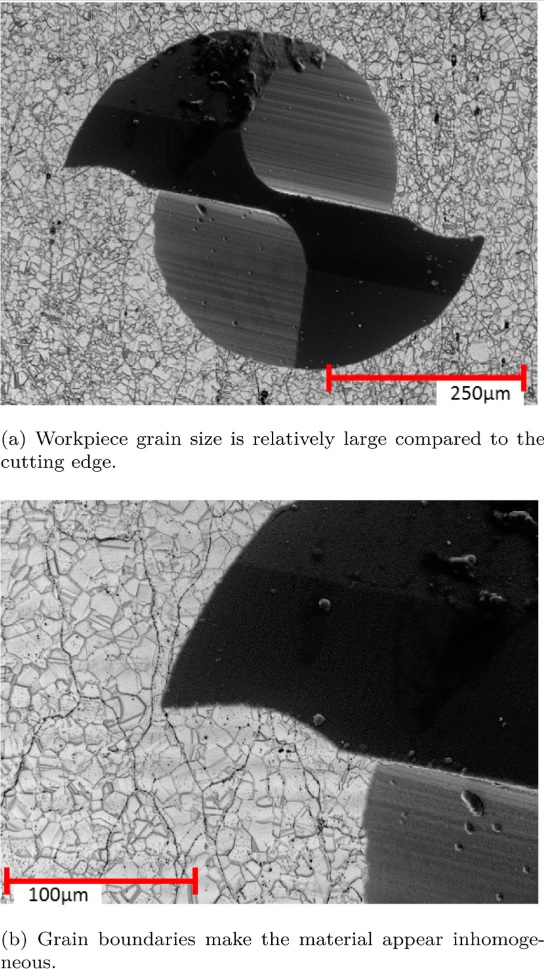
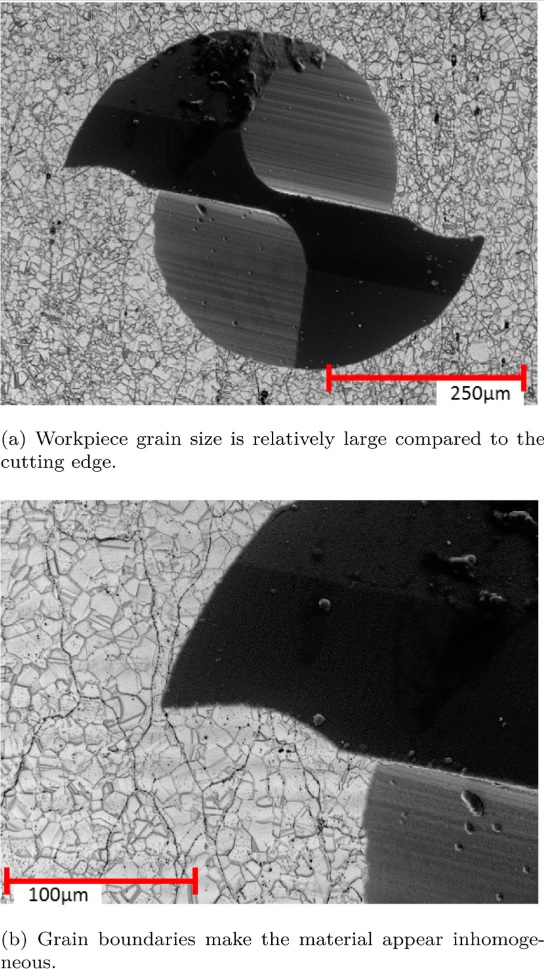
圖28. 晶粒尺寸與銑刀尺寸的關係。
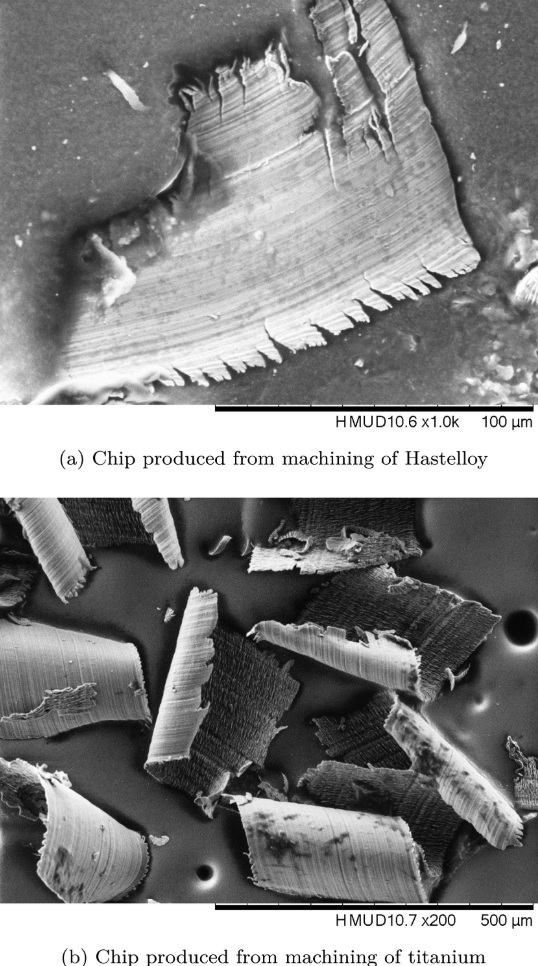
圖29. 加工中生產的切屑。
由於切屑的尺寸非常小(一般來說,切屑的長和寬都不超過200微米),所以收集和研究起來非常困難。然而,我們直接從工件上收集了一些每種材料的切屑的例子。對於鈦合金和哈氏合金,我們看到了圖22所示的鋸齒型切屑。這兩種切屑的例子如圖21所示。切屑的形成是指剪切力強的區域,然後是相對不變形的區域。這是因為加工溫度過高,而在切割鈦合金和鎳合金時,加工溫度不能迅速消散,這是常見的現象。由於材料的不規則流動以及熱疲勞導致切削刃磨損,從而導致崩裂和開裂。其結果可能會導致銑刀最終的災難性故障(圖30)。
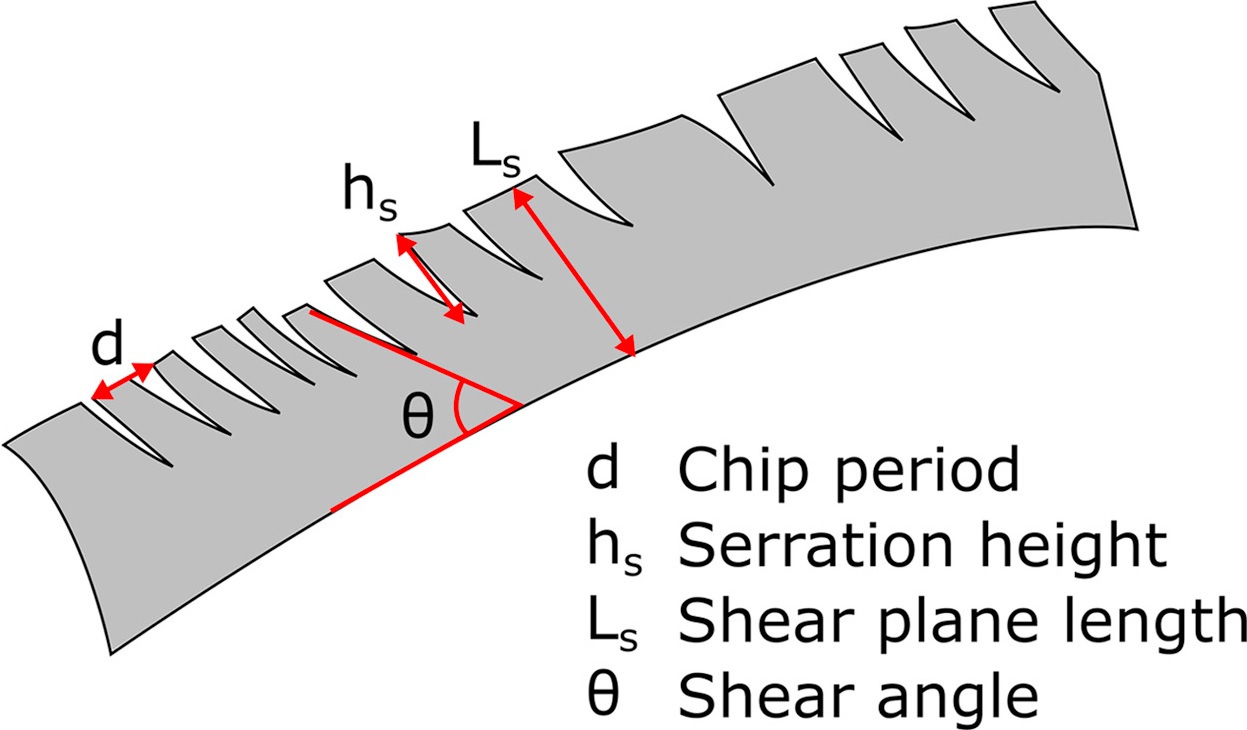
5.8. 考慮替代性塗層:通過塗層延長工具壽命的早期調查
在圖6中,用AlTiN塗層的銑刀用於加工黃銅(圖19),顯示出AlTiN塗層銑刀磨損曲線的穩態區域顯著延長。此外,這些銑刀的穩定狀態發生在較低的磨損水平。後者的結果以前也有報導,但曲線的延長是顯著的,因為它表明銑刀的壽命更長。其中一個TiB2銑刀的早期斷裂很可能是由於硬質合金材料的不完善或黃銅中的毛刺或較大的晶體所產生的過大的切削力造成的,這也提醒我們在微觀尺度上測量銑刀的難度和預檢的重要性。這一結果表明,即使對於黃銅等較軟的金屬,塗層銑刀也能顯著提高銑刀壽命。在一定程度上,這與切削刃半徑有關--塗覆的塗層增加了銑刀的切削刃半徑,而這一切削刃半徑降低了銑刀的應力。這種對銑刀壽命的延長是值得進一步研究的。
6. 結論
考慮到在比較微型立銑刀磨損研究時遇到的困難,提出了一個測量、描述和報告亞毫米級立銑刀磨損的協議。其目的是提供一種方法,以便對不同銑刀幾何形狀和材料之間的研究進行合理的比較。標準化將使現有研究成為可能,而對不同銑刀的磨損曲線進行表徵則可直接應用於生產中,以提高加工效率。
在驗證性磨損試驗中得到的結果表明,所提出的磨損測量方案可以繪製出亞毫米級微端銑刀的磨損曲線,有以下幾點值得注意。
一. 使用所建議的協議,可以確定磨損的階段性,如與宏觀立銑刀一樣,這樣銑刀的磨損不允許超出穩態區域。
二. 外部邊緣磨損在研究微端銑刀的磨損時提供的信息很少,因為在加工過程中,切屑滑過這些邊緣的磨損影響很大。結合端面磨損和側翼磨損可以提供更多的一致數據。
三. 通過使用SEM技術(包括背散射電子技術)對銑刀進行檢查,並對切屑進行檢查,可以了解正在發生的磨損機理,這在設計微型立銑刀的塗層時非常有用。
四. 由於主軸跳動導致銑刀的齒部磨損不均勻,即使在銑刀磨損曲線相對較早的時候也會出現單齒失效的現象,這是很常見的。這再次凸顯了與微觀銑削相比,盡量減少這種情況的重要性。
五. 與切削距離或切削時間相比,滑動距離是報告微型立銑刀磨損的一個更合適的衡量標準,因為它考慮了切削速度和進給率。
六. 雖然分析工件中的通道和特徵作為銑刀磨損測量的方法有一定的空間,由於一次測量而不是多次拆卸銑刀,會大大加快測量時間,但這種方法只能提供事後的銑刀信息,而且需要非常嚴格的加工才能發揮作用。因此,它在繪製磨損曲線方面的可靠性不如直接測量銑刀的方法。
根據第2節中回顧的文獻,對大型微型立銑刀的塗層還有很大的進一步研究空間,因為許多銑刀公司提供標準的塗層和未塗層的微型立銑刀,但對微型立銑刀塗層的研究明顯少於大型立銑刀。儘管塗層有其缺點(例如,增加切削刃半徑),但這裡有機會顯著延長銑刀壽命。
由於測試的銑刀直徑為500μm,進一步的工作應該研究這個協議的尺寸限制,並建立新的方法,在這個協議是不再合適的地方。
鳴謝
作者希望感謝謝菲爾德大學先進製造研究中心的DTCurtis在構思這項工作之前對銑刀磨損問題的討論做出的貢獻;感謝英國EPSRC工程和物理科學研究理事會對這項工作的資金支持(EP/L016257/1)。
由於測試的銑刀直徑為500μm,進一步的工作應該研究這個協議的尺寸限制,並建立新的方法,在這個協議是不再合適的地方。
鳴謝
作者希望感謝謝菲爾德大學先進製造研究中心的DTCurtis在構思這項工作之前對銑刀磨損問題的討論做出的貢獻;感謝英國EPSRC工程和物理科學研究理事會對這項工作的資金支持(EP/L016257/1)。