Carbide End Mills Wear and Countermeasures
2020-04-13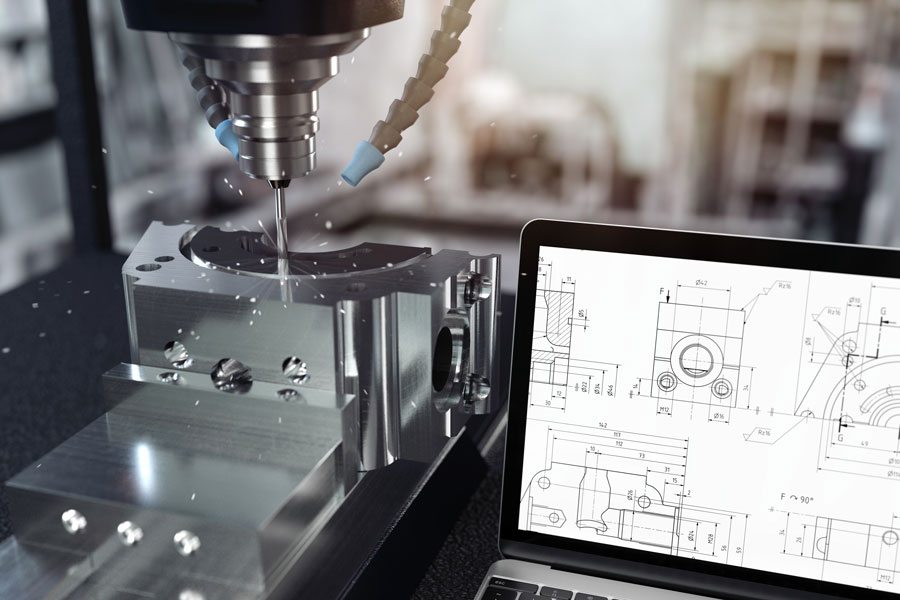
Carbide end mill is one of the most fundamental propositions in cutting operations. Defining and understanding carbide end mill wear can help cutting tools manufacturers and users extend the life of carbide end mill. In addition, today's end mills coating technology, including the use of new alloying elements, provides an effective means of further extending the life of end mills, while significantly increasing productivity.
In metal cutting operations, the heat and friction generated is an expression of energy. The heat and friction generated by the high surface load and the high speed of the chip sliding along the front face of the carbide end mills puts the end mills in an extremely challenging machining environment.
The magnitude of the cutting rate tends to fluctuate up and down, depending mainly on the different machining conditions (e.g. presence of hard components in the workpiece material, or interrupted cutting). Therefore, in order to maintain its strength at high cutting temperatures, some basic characteristics of carbide end mills are required, including excellent toughness, wear resistance and high hardness.
Although the cutting temperature at the carbide end mill/workpiece interface is a key factor in determining the wear rate of almost all carbide end mill material, it can be difficult to determine the parameter values required to calculate the cutting temperature. However, the measurement results of the cutting test can provide the basis for some empirical approaches.
It can usually be assumed that the energy generated in cutting is converted into heat, and usually 80% of this heat is carried away by the chips (this proportion varies depending on several factors - especially the speed of cutting). The remaining 20% of the heat is transferred to the end mills. Even when cutting less hard steel parts, the temperature of the end mill can exceed 550°C, which is the maximum temperature that HSS can withstand without reducing its hardness. When cutting hardened steel with a polycrystalline cubic boron nitride (PCBN) carbide tools, the temperature of the carbide end mills and chips will typically exceed 1000°C.
Carbide end mills wear usually includes the following types: ① back cutting edge wear; ② marking wear; ③ crescent wear; ④ cutting edge wear; ⑤ chipped cutting edge; ⑥ cutting edge cracked; ⑦ catastrophic failure.
There is no universally accepted standard definition of the life of a carbide end mill, which usually depends on the different workpiece and material of the carbide end mill, as well as the different cutting processes. One way to quantitatively analyze the end-of-life point of a carbide end mill is to set an acceptable maximum post cutter wear limit (expressed in VB or VBmax). The life of a carbide end mill can be expressed by the Taylor formula for the expected life of a carbide end mill, namely
VcTn=C
A more common form of the formula is
VcTn×Dxfy=C
Where Vc is the cutting speed; T is the life of the carbide end mills; D is the depth of cut; f is the feed rate; x and y are determined by experiment; n and C are constants determined by experiment or published technical data, which represent the characteristics of the tungsten cutter material, workpiece and feed rate.
The continuous development of optimal carbide end mill substrates, coatings and cutting edge preparation techniques is essential to limit the wear of carbide end mills and to resist high cutting temperatures. These elements, along with the chipbreaker grooves and corner radii used on indexable inserts, determine the suitability of each type of tungsten carbide end mills for different workpieces and cutting operations. The optimal combination of all these elements extends the life of the carbide end mills, making cutting more economical and reliable.
By changing the particle size of carbide in the range of 1-5µm, cutting tools manufacturers can change the substrate properties of carbide end mills. The particle size of the base material plays an important role in the cutting performance and the life of the carbide end mills. The smaller the particle size, the better the abrasion resistance of the carbide end mills. Conversely, the larger the grain size, the better the toughness of the carbide end mills. The fine particle matrix is mainly used for the processing of inserts for aviation grade materials such as titanium alloys, Inconel alloys and other high temperature alloys.
In addition, by increasing the cobalt content of the carbide tungsten end mills material by 6-12%, better toughness can be obtained. Therefore, the requirements of a specific cutting process can be met by adjusting the cobalt content, whether this requirement is toughness or wear resistance.
The performance of carbide end mill substrates can also be enhanced by the formation of cobalt-rich layers close to the outer surface or by the selective addition of other alloying elements (e.g. titanium, tantalum, vanadium, niobium, etc.) in hard alloy materials. The cobalt-rich layer significantly improves the cutting edge strength and thus the performance of roughing and intermittent cutting of carbide end mills.
In addition, five other substrate properties - fracture toughness, lateral fracture strength, compressive strength, hardness and thermal impact resistance - are also considered when selecting a carbide end mill base that matches the workpiece material and machining method. For example, if a carbide end mills exhibits chipping along the cutting edge, a base material with higher fracture toughness should be used. In the case of direct failure or breakage of the cutting edge of a tungsten carbide cutter, a possible solution is to use a base material with a higher lateral fracture strength or higher compressive strength. For higher cutting temperatures (e.g. dry cutting), a harder carbide end mill material should generally be preferred. In applications where thermal cracking of carbide end mills can be observed (most common in milling operations), it is recommended to use a carbide end mills material with better thermal shock resistance.
Optimization of the base material of carbide end mills can improve the cutting performance of carbide end mills. For example, the base material for the insert grade used to process steel parts should be selected from a manufacturer with better resistance to plastic deformation, thus reducing the possibility of micro-cracking in the coating of hard and brittle inserts. By secondary machining the inserts, the surface roughness and microcracks of their coating are reduced, thereby reducing the cutting heat and resulting plastic deformation and microcracks on the insert surface. In addition, a new substrate for machining inserts for cast iron has better heat resistance, which allows machining with higher cutting speeds.
The coating also helps to improve the cutting performance of carbide end mills. Current coating technologies include.
①Titanium Nitride (TiN) Coating: This is a general purpose PVD and CVD coating that improves the hardness and oxidation temperature of carbide end mills.
②Titanium Carbide (TiCN) Coating: By adding carbon to TiN, the hardness and surface finish of the coating is improved.
③Nitro-aluminum titanium (TiAlN) and nitro-aluminum titanium (AlTiN) coatings: the combined application of an alumina (Al2O3) layer with these coatings improves the life of carbide end mills for high temperature cutting. AlTiN coatings are particularly suitable for dry and near-dry cutting and have a higher aluminum content and higher surface hardness than TiAlN coatings with higher titanium content. AlTiN coatings are typically used for high-speed machining.
④Chromium Nitride (CrN) coating: This coating has better anti-adhesion properties and is the preferred solution against pemphigus.
Diamond coating: Diamond coating can significantly improve the cutting performance of carbide end mills for non-ferrous materials, and is very suitable for processing graphite, metal-based composites, high-silicon aluminum alloys and other highly abrasive materials. However, the diamond coating is not suitable for machining steel parts because its chemical reaction with the steel can damage the adhesion of the coating to the substrate.
In recent years, the market share of PVD-coated carbide end mills has expanded and their price is comparable to that of CVD-coated carbide end mills. The thickness of the CVD coating is usually 5-15µm, while the thickness of the PVD coating is about 2-6µm. The CVD coating produces unwelcome pulling stresses when applied to the carbide end mills substrate, while the PVD coating helps to create beneficial compressive stresses on the substrate. Thicker CVD coatings usually significantly reduce the cutting edge strength of carbide end mills. Therefore, the CVD coating cannot be used on carbide end mills that require a very sharp cutting edge.
The use of new alloying elements in the coating process can improve the adhesion and coating performance. WOTEK coating technology also reduces friction, thereby reducing energy consumption in the process and increasing resistance to phytoma.
The WOTEK coating process reduces micro-cracks on the cutting tool surface caused by different shrinkage rates when the cutting tool is cooled after CVD coating. Likewise, the process eliminates harmful droplets on the coating surface during PVD coating, resulting in a smoother coating surface, lower cutting temperature during machining, longer life, better chip flow, and higher cutting speeds.
Another example is WOTEK's coating technology. The technology allows a TiAlN PVD coating to be deposited over a medium temperature CVD Al2O3 coating. This composite coating has excellent abrasion and chipping resistance and is well suited for a wide range of insert grades used for high speed cutting of cast iron, with expected cutting speeds up to 650-1200 sfm or more (depending on the type of workpiece material and processing conditions).
In many cases, the preparation of the cutting edge (or edge passivation) has become a watershed in determining machining success. Passivation process parameters are determined according to specific process requirements. For example, the cutting edges used for high-speed finishing steel parts have different requirements for edge passivation than those used for roughing. Edge passivation can be applied to the cutting edges of almost any type of carbon or alloy steel, while its application to the cutting edges of stainless steel and special alloy materials is limited. The passivation can be as small as 0.007mm or as large as 0.05mm, and to enhance the cutting edge in harsh machining conditions, tiny T-bands can be formed by passivating the edge.
In general, inserts used for continuous turning and milling of most steel and cast iron require a greater degree of edge passivation. The amount of passivation depends on the hard alloy number and the type of coating (CVD or PCD coating). For heavily interrupted cutting inserts, heavy passivation of the edges or machining of T-bands has become a prerequisite. Depending on the type of coating, the passivation can be close to 0.05mm.
In contrast, carbide end mills for machining stainless steel and high-temperature alloys are prone to the formation of scabbards and therefore require a sharp cutting edge that can only be slightly passivated (down to 0.01mm), and even smaller passivation amounts can be customized. Similarly, carbide end mills for machining aluminum alloys require a sharp cutting edge.
For example, WOTEK manufactures a variety of carbide end mills with a spiral cutting edge, which has a profile formed around a cylindrical face that moves evenly along an axis. One of the advantages of this spiral-edge design, which approximates a helix, is a smoother cutting motion. Unlike the straight edge, the spiral cutting edge mimics the motion of a spiral fluted end mill. The cutting edge enters the cut gradually in a "spiral" motion, rather than all at once, which reduces chatter and results in a better finish on the surface.
In addition, the spiral cutting edge can withstand greater cutting rates and obtain a higher rate of metal removal, while also reducing stress. Another advantage of the spiral cutting edge is that it extends the life of the carbide end mills due to the reduced cutting pressure and cutting heat acting on the carbide end mills.
Understanding the mechanism of carbide end mills wear and using new technologies to improve the life and machining efficiency of carbide end mills. In today's market, where companies are not only competing locally, but also globally, it is important to take advantage of their full competitive advantage.
Carbide End Mills Wear Principle
In metal cutting operations, the heat and friction generated is an expression of energy. The heat and friction generated by the high surface load and the high speed of the chip sliding along the front face of the carbide end mills puts the end mills in an extremely challenging machining environment.
The magnitude of the cutting rate tends to fluctuate up and down, depending mainly on the different machining conditions (e.g. presence of hard components in the workpiece material, or interrupted cutting). Therefore, in order to maintain its strength at high cutting temperatures, some basic characteristics of carbide end mills are required, including excellent toughness, wear resistance and high hardness.
Although the cutting temperature at the carbide end mill/workpiece interface is a key factor in determining the wear rate of almost all carbide end mill material, it can be difficult to determine the parameter values required to calculate the cutting temperature. However, the measurement results of the cutting test can provide the basis for some empirical approaches.
It can usually be assumed that the energy generated in cutting is converted into heat, and usually 80% of this heat is carried away by the chips (this proportion varies depending on several factors - especially the speed of cutting). The remaining 20% of the heat is transferred to the end mills. Even when cutting less hard steel parts, the temperature of the end mill can exceed 550°C, which is the maximum temperature that HSS can withstand without reducing its hardness. When cutting hardened steel with a polycrystalline cubic boron nitride (PCBN) carbide tools, the temperature of the carbide end mills and chips will typically exceed 1000°C.
Carbide End Mills Wear and Life Span
Carbide end mills wear usually includes the following types: ① back cutting edge wear; ② marking wear; ③ crescent wear; ④ cutting edge wear; ⑤ chipped cutting edge; ⑥ cutting edge cracked; ⑦ catastrophic failure.
There is no universally accepted standard definition of the life of a carbide end mill, which usually depends on the different workpiece and material of the carbide end mill, as well as the different cutting processes. One way to quantitatively analyze the end-of-life point of a carbide end mill is to set an acceptable maximum post cutter wear limit (expressed in VB or VBmax). The life of a carbide end mill can be expressed by the Taylor formula for the expected life of a carbide end mill, namely
VcTn=C
A more common form of the formula is
VcTn×Dxfy=C
Where Vc is the cutting speed; T is the life of the carbide end mills; D is the depth of cut; f is the feed rate; x and y are determined by experiment; n and C are constants determined by experiment or published technical data, which represent the characteristics of the tungsten cutter material, workpiece and feed rate.
The continuous development of optimal carbide end mill substrates, coatings and cutting edge preparation techniques is essential to limit the wear of carbide end mills and to resist high cutting temperatures. These elements, along with the chipbreaker grooves and corner radii used on indexable inserts, determine the suitability of each type of tungsten carbide end mills for different workpieces and cutting operations. The optimal combination of all these elements extends the life of the carbide end mills, making cutting more economical and reliable.
Alteration of Carbide End Mills Base
By changing the particle size of carbide in the range of 1-5µm, cutting tools manufacturers can change the substrate properties of carbide end mills. The particle size of the base material plays an important role in the cutting performance and the life of the carbide end mills. The smaller the particle size, the better the abrasion resistance of the carbide end mills. Conversely, the larger the grain size, the better the toughness of the carbide end mills. The fine particle matrix is mainly used for the processing of inserts for aviation grade materials such as titanium alloys, Inconel alloys and other high temperature alloys.
In addition, by increasing the cobalt content of the carbide tungsten end mills material by 6-12%, better toughness can be obtained. Therefore, the requirements of a specific cutting process can be met by adjusting the cobalt content, whether this requirement is toughness or wear resistance.
The performance of carbide end mill substrates can also be enhanced by the formation of cobalt-rich layers close to the outer surface or by the selective addition of other alloying elements (e.g. titanium, tantalum, vanadium, niobium, etc.) in hard alloy materials. The cobalt-rich layer significantly improves the cutting edge strength and thus the performance of roughing and intermittent cutting of carbide end mills.
In addition, five other substrate properties - fracture toughness, lateral fracture strength, compressive strength, hardness and thermal impact resistance - are also considered when selecting a carbide end mill base that matches the workpiece material and machining method. For example, if a carbide end mills exhibits chipping along the cutting edge, a base material with higher fracture toughness should be used. In the case of direct failure or breakage of the cutting edge of a tungsten carbide cutter, a possible solution is to use a base material with a higher lateral fracture strength or higher compressive strength. For higher cutting temperatures (e.g. dry cutting), a harder carbide end mill material should generally be preferred. In applications where thermal cracking of carbide end mills can be observed (most common in milling operations), it is recommended to use a carbide end mills material with better thermal shock resistance.
Optimization of the base material of carbide end mills can improve the cutting performance of carbide end mills. For example, the base material for the insert grade used to process steel parts should be selected from a manufacturer with better resistance to plastic deformation, thus reducing the possibility of micro-cracking in the coating of hard and brittle inserts. By secondary machining the inserts, the surface roughness and microcracks of their coating are reduced, thereby reducing the cutting heat and resulting plastic deformation and microcracks on the insert surface. In addition, a new substrate for machining inserts for cast iron has better heat resistance, which allows machining with higher cutting speeds.
Choose the right coating
The coating also helps to improve the cutting performance of carbide end mills. Current coating technologies include.
①Titanium Nitride (TiN) Coating: This is a general purpose PVD and CVD coating that improves the hardness and oxidation temperature of carbide end mills.
②Titanium Carbide (TiCN) Coating: By adding carbon to TiN, the hardness and surface finish of the coating is improved.
③Nitro-aluminum titanium (TiAlN) and nitro-aluminum titanium (AlTiN) coatings: the combined application of an alumina (Al2O3) layer with these coatings improves the life of carbide end mills for high temperature cutting. AlTiN coatings are particularly suitable for dry and near-dry cutting and have a higher aluminum content and higher surface hardness than TiAlN coatings with higher titanium content. AlTiN coatings are typically used for high-speed machining.
④Chromium Nitride (CrN) coating: This coating has better anti-adhesion properties and is the preferred solution against pemphigus.
Diamond coating: Diamond coating can significantly improve the cutting performance of carbide end mills for non-ferrous materials, and is very suitable for processing graphite, metal-based composites, high-silicon aluminum alloys and other highly abrasive materials. However, the diamond coating is not suitable for machining steel parts because its chemical reaction with the steel can damage the adhesion of the coating to the substrate.
In recent years, the market share of PVD-coated carbide end mills has expanded and their price is comparable to that of CVD-coated carbide end mills. The thickness of the CVD coating is usually 5-15µm, while the thickness of the PVD coating is about 2-6µm. The CVD coating produces unwelcome pulling stresses when applied to the carbide end mills substrate, while the PVD coating helps to create beneficial compressive stresses on the substrate. Thicker CVD coatings usually significantly reduce the cutting edge strength of carbide end mills. Therefore, the CVD coating cannot be used on carbide end mills that require a very sharp cutting edge.
The use of new alloying elements in the coating process can improve the adhesion and coating performance. WOTEK coating technology also reduces friction, thereby reducing energy consumption in the process and increasing resistance to phytoma.
The WOTEK coating process reduces micro-cracks on the cutting tool surface caused by different shrinkage rates when the cutting tool is cooled after CVD coating. Likewise, the process eliminates harmful droplets on the coating surface during PVD coating, resulting in a smoother coating surface, lower cutting temperature during machining, longer life, better chip flow, and higher cutting speeds.
Another example is WOTEK's coating technology. The technology allows a TiAlN PVD coating to be deposited over a medium temperature CVD Al2O3 coating. This composite coating has excellent abrasion and chipping resistance and is well suited for a wide range of insert grades used for high speed cutting of cast iron, with expected cutting speeds up to 650-1200 sfm or more (depending on the type of workpiece material and processing conditions).
Preparation of The Cutting Flute
In many cases, the preparation of the cutting edge (or edge passivation) has become a watershed in determining machining success. Passivation process parameters are determined according to specific process requirements. For example, the cutting edges used for high-speed finishing steel parts have different requirements for edge passivation than those used for roughing. Edge passivation can be applied to the cutting edges of almost any type of carbon or alloy steel, while its application to the cutting edges of stainless steel and special alloy materials is limited. The passivation can be as small as 0.007mm or as large as 0.05mm, and to enhance the cutting edge in harsh machining conditions, tiny T-bands can be formed by passivating the edge.
In general, inserts used for continuous turning and milling of most steel and cast iron require a greater degree of edge passivation. The amount of passivation depends on the hard alloy number and the type of coating (CVD or PCD coating). For heavily interrupted cutting inserts, heavy passivation of the edges or machining of T-bands has become a prerequisite. Depending on the type of coating, the passivation can be close to 0.05mm.
In contrast, carbide end mills for machining stainless steel and high-temperature alloys are prone to the formation of scabbards and therefore require a sharp cutting edge that can only be slightly passivated (down to 0.01mm), and even smaller passivation amounts can be customized. Similarly, carbide end mills for machining aluminum alloys require a sharp cutting edge.
For example, WOTEK manufactures a variety of carbide end mills with a spiral cutting edge, which has a profile formed around a cylindrical face that moves evenly along an axis. One of the advantages of this spiral-edge design, which approximates a helix, is a smoother cutting motion. Unlike the straight edge, the spiral cutting edge mimics the motion of a spiral fluted end mill. The cutting edge enters the cut gradually in a "spiral" motion, rather than all at once, which reduces chatter and results in a better finish on the surface.
In addition, the spiral cutting edge can withstand greater cutting rates and obtain a higher rate of metal removal, while also reducing stress. Another advantage of the spiral cutting edge is that it extends the life of the carbide end mills due to the reduced cutting pressure and cutting heat acting on the carbide end mills.
Understanding the mechanism of carbide end mills wear and using new technologies to improve the life and machining efficiency of carbide end mills. In today's market, where companies are not only competing locally, but also globally, it is important to take advantage of their full competitive advantage.