Dry cutting and selection of cutting tools with different coating materials
2020-03-17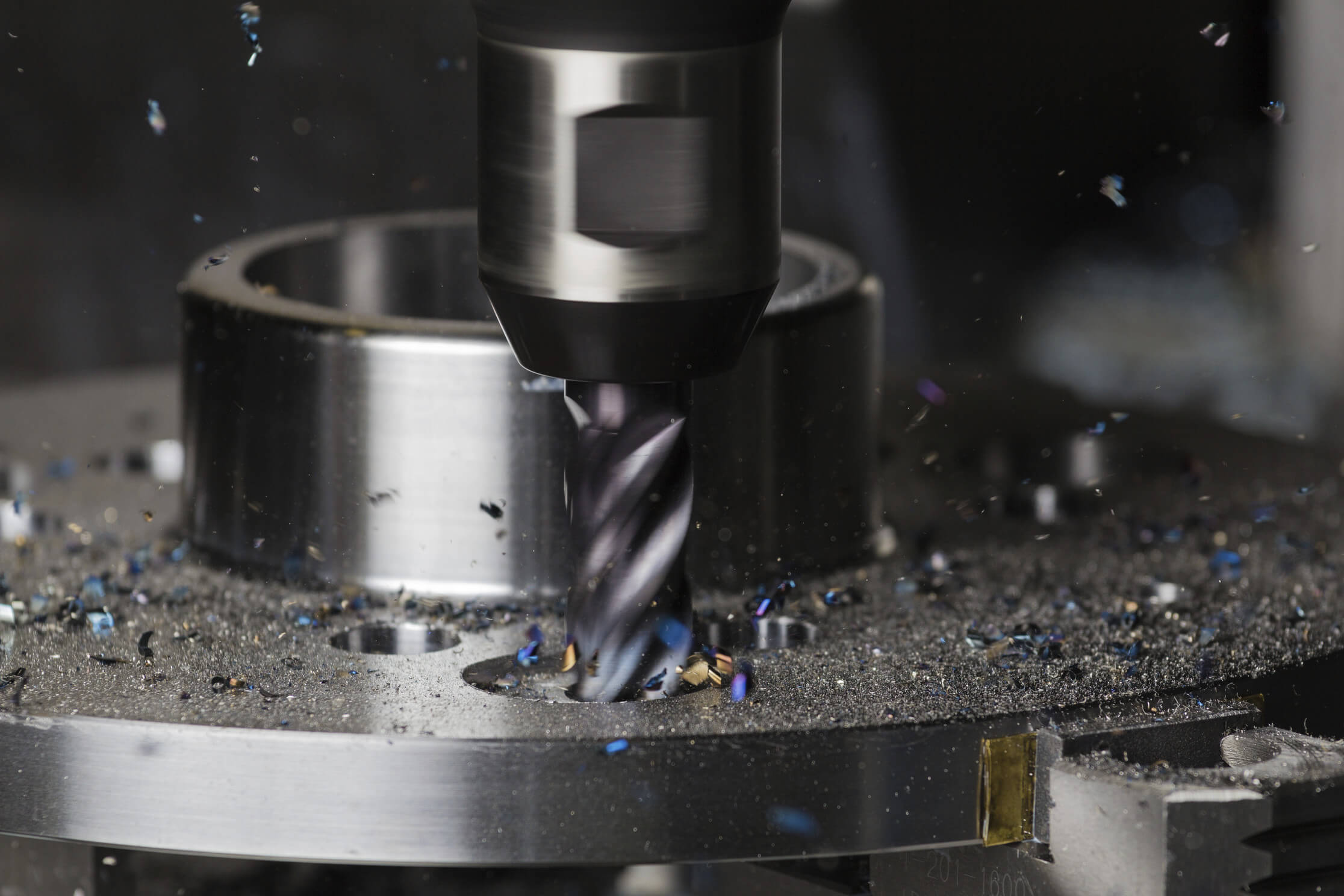
▇Dry cutting is the development direction of milling
Twenty years ago, cutting fluids were very cheap, costs for less than 3% of the most machining processes. No one pays much attention to this. However, it is different now. The proportion of cutting fluid in the production cost of the workshop has risen to 15%, which has to attract great attention from production operators.
Especially those oily cutting fluids have become a big expense. What's more important is that its emissions pollute the environment, and foreign environmental protection agencies should monitor the treatment of these mixed preparations. Moreover, many countries and regions also classify them as hazardous waste, and if they contain oil and certain alloys, more stringent control measures must be taken.
Further, many high-speed machining processes add cutting fluid to generate fumes. Environmental protection departments also limit the amount of cutting fluid fumes to be released. Occupational safety and employee health management departments are considering a Recommendations of the Advisory Committee. This includes setting a relatively high price policy for cutting fluids. As a result, more and more manufacturers are beginning to use dry cutting to avoid this expense and the troubles associated with cutting fluid handling.
In the past, the metal processing industry has formed a "habit" of using cutting fluids, so the main obstacle to promote dry cutting is this habitual force. They believe that cutting fluids are necessary to obtain a good machining surface and improve tool life. There are also many people who think that wet cutting to dry cutting can be more expensive. In fact, both views are wrong. For most quality machining, dry cutting should be the "standard processing environment". Dry turning and dry milling of hardened materials at high speeds are not only possible, but also more economical.
The key is to know how to choose the right tool, machine and cutting method. Although cutting fluids are still needed in some cases, research shows that due to the great development of tool materials today, the situation is constantly changing. The new cemented carbide grades, especially those coated grades, do not require cutting fluids at high speeds and high temperatures, and have higher cutting efficiency. In fact, for intermittent cutting, the higher the cutting zone temperature, the less suitable it is to use cutting fluids.
The milling case, if the cutting fluid can overcome the centrifugal force caused by a high-speed rotating end mill, then it has evaporated before reaching the cutting area, and its cooling effect is very small. However, the application of cutting fluid tools will cause drastic changes in temperature. The edge flute of end mill will cool down when cutting out from the workpiece, and the temperature will rise again when cutting in. Although similar heating and cooling loops occur during dry cutting, the temperature change is much larger with the addition of cutting fluid. Rapid changes in temperature create stress in the end mills, which can cause cracks.
A similar case occurs in turning. Ex, with uncoated cemented carbide, when the speed is higher than 130m / min, turning middle carbon steel, the cutting edge is cut into the workpiece for less than 40 seconds, and then exposed to the coolant, it can damage from thermal impact is clearly shown. This thermal impact accelerates crater wear and subsequent wear, which greatly reduces tool life. For most turning operations, dry cutting usually increases tool life.
However, this is another case for drilling. Cutting fluid is necessary when drilling because it provides lubrication and flushes chips from the hole. Without cutting fluid, chips may stick in the holes, and the average surface roughness (Ra) may be double that in wet drilling. In this case, the cutting fluid also reduces the required machine torque because the points on the edge of the drill that make contact with the hole wall are lubricated.
Although coated drills can also provide lubrication effects similar to cutting fluids, coatings can also reduce cutting forces and minimize frictional resistance. From the overall effect, it is not yet possible to completely replace cutting fluid. Which type of cutting fluid to use depends on the specific situation. Lubricating cutting fluid is used for low-speed machining of difficult-to-machine materials and higher surface roughness requirements.
The cutting fluid with high cooling capacity can enhance the high-speed machining performance of free-cutting materials, and can be used in situations where there is a tendency to generate chippings or strict dimensional tolerances.
However, the cutting fluid is used to achieve some effects, but it requires a high additional cost and also brings very harmful environmental pollution, which is not worth it. It should be seen that modern cutting tools can withstand higher cutting heat and have the performance required for high-speed cutting. If necessary, compressed air can be used to blow away hot chips from the cutting area to replace the cutting fluid.
▇ Selection of tool materials in dry cutting
1. The best coating for high-speed dry cutting is TiaLN.
Today, the important reason that cutting fluids are usually no longer necessary is coating. They alleviate the impact of temperature by suppressing the heat transfer from the cutting area to the cutting tool. The coating acts like a thermal barrier because it has a much lower thermal conductivity than the tool base and workpiece material. Therefore, these tools absorb less heat and can withstand higher cutting temperatures. Whether turning or milling, coated tools allow more efficient cutting parameters without reducing tool life.The coating thickness is between 2 and 18 μm and it plays an important role in tool performance. Thinner coatings are more resistant to temperature changes during impact cutting than thicker coatings because thinner coatings have less stress and are less prone to cracking. During rapid cooling and heating, the thick coating is as easily broken as the glass is heated and cooled very quickly. Dry cutting with thin-coated inserts can extend tool life up to 40%, which is why physical coatings are commonly used to coat round tools and milling inserts. PVD coatings tend to be thinner than chemical coatings and bond more strongly to contours. In addition, PVD coatings can be deposited on cemented carbides at much lower temperatures, so they are commonly used for very sharp cutting edges and large positive rake angle milling and turning tools.
Although the coating material is TiN, it has 80% of all coated tools. However, in the case of high-speed dry cutting, the best PVD coating is TiAlN, which has four times better performance than TiN in continuous high-temperature cutting, such as for high-speed turning. TiAlN coatings also outperform other coatings for tools under high thermal stress conditions. Such as dry milling and deep hole drilling with small diameter holes where cutting fluid is difficult to reach.
TiAlN is harder than TiN at cutting temperature and has thermal stability. The PVD coating takes advantage of its chemical wear resistance. Its hardness is up to 3500 degrees Vickers and its operating temperature is up to 1470 ° F (800 ° C). Materials scientists speculate that these properties can be attributed to amorphous alumina films, which are formed on the chip / tool interface after some aluminum in the coating surface oxidizes at high temperatures.
This study selected ultra-thin multilayer PVD coatings. The coating produced by this deposition process consists of hundreds of layers, each layer being only a few nanometers thick. The deposits of ordinary PVD coatings have only a few micron-thick coatings.
Despite PVD coating has many advantages, CVD coatings are still more popular for processing most ferrous metals. During the CVD process, a relatively high deposition temperature helps to improve the bonding strength, and allows a higher cobalt content in the matrix, so that the edge cutting has good toughness and improves the ability to resist plastic deformation. Since CVD coatings are thicker than PVD coatings, passivation is required at their cutting edges to prevent the coating from peeling, and it can also help improve the tool's wear resistance. Allows feed rates up to 0.035 inch / rev (0.9mm / r).
CVD is the process of depositing a useful layer of alumina on a tool, which known is the most heat-resistant and oxidation-resistant coating. Alumina is a poor conductor that separates the tool from the heat generated by the deformation of the cutting and promotes the heat to the chip. This is an excellent CVD coating material, mainly used for carbide turning tools used in dry cutting. It also protects the substrate during high-speed cutting, and is the best coating against abrasive wear and crater wear.
Coated inserts have a longer tool life and higher stability in dry milling than wet milling. Higher cutting speeds will further increase the cutting temperature. For example, dry cutting of cast iron at a cutting speed of 14000 rpm and a cutting speed of 1575 inches per minute (40m / min) can heat the cutting area in front of the tool to 600 ° to 700 ° C. The metal removal rate is similar to milling aluminum, and the temperature on cast iron is higher than that of conventional tools.
2. Selection of cermet, ceramic, CBN, PCD
The higher cutting speed, the higher wear resistance of the tool material is required, as well as the higher heat hardness. Cermets, cubic boron nitride, and two types of ceramics suitable for fine machining-alumina and silicon nitride (the modern term "ceramic" includes alumina and silicon nitride, unlike the past alumina), their Applications are growing in popularity. Polycrystalline diamond is another tool material used in dry cutting conditions. In all of these materials, they have high heat hardness and abrasion resistance, and greater brittleness.
◆. Cermet
It is an advanced cemented carbide. Cermet can withstand higher cutting temperatures than conventional cemented carbides, but lack the impact resistance than cemented carbides, toughness in semi to heavy machining, and strength at low speeds and large feeds. Under small and constant loads, cermet has similar cutting strengths as conventional cemented carbides. However, it has higher temperature and wear resistance at high cutting speeds, lasts longer, and the surface of the processed workpiece is smoother. When used to process soft and sticky materials, it also has good resistance to chippings and good surface quality.Higher temperature hardness comes from the titanium compound added during the formulation. Cermet is a type of cemented carbide. It contains hard titanium-based compounds (titanium carbide, titanium carbonatite and titanium nitride), and the binder is nickel or nickel molybdenum. Due to the temperature limitation of metal-type adhesives, typical metal-ceramic grades do not have sufficiently high thermosetting properties when the hardness of the processed material exceeds HRC40.
Cermet are more sensitive to fracture and feed stress than coated and uncoated cemented carbides. Therefore, it is used on high precision workpieces and high surface quality requirements. The ideal machining process is to cut those continuous surfaces.
When turning carbon steel, the upper limit of feed rate is usually 0.025 inches / revolution (0.635 mm / r). General-purpose milling can be performed at high spindle speeds and semi feed rates. If these conditions establish, cermet can maintain sharp cutting edges for a long time during large production. If cermet is used at traditional cutting speeds and feed rates, they can improve tool life and surface quality, as well as productivity, compared to carbide cutting tools. For cutting alloy steel, the increase is 20%. For cutting carbon, 50% for steel, stainless steel and soft iron.
◆. Ceramic
Ceramic tools are similar to cermets in that they are more chemically stable than cemented carbide and can be machined at high cutting speeds for longer periods. Pure alumina can withstand very high temperatures, but its strength and toughness are very low. If the working conditions are not good, it will break easily.In order to reduce the susceptibility of ceramics to crushing, when trying to improve its toughness and impact resistance, zirconia or a mixture of titanium carbide and titanium nitride was added. Despite the addition of these additives, the toughness of ceramics is much lower than that of cemented carbide.
Another method to increase the toughness of alumina ceramics is to add crystalline texture or silicon carbide whiskers to the material. Through these special averages, the whiskers are only 1 nanometer in diameter and 20 micrometers long and very strong. Toughness, strength and thermal shock resistance. In composition, whiskers can be as high as 30%.
Like alumina, silicon nitride has higher thermal stiffness than cemented carbide. It also has better resistance to high temperature and mechanical impact. Compared with alumina ceramics, it has less chemical stability when processing steel. However, gray cast iron can be processed with silicon nitride ceramics at a speed of 1450 feet per minute (442m / min) or higher.
Although machining with ceramic cutting tools can be very efficient, the application must be specific. For example, ceramic tools can’t be used for machining aluminum, but are particularly suitable for gray cast iron, ductile cast iron, hardened steel and some unhardened steels, heat-resistant alloys. However, for these materials, the successful application depends on the preparation of the cutting edge appearance before the cutting, the stability of the machine and equipment, and the selection of the best processing parameters.
◆. CBN
CBN is a high hardness material. It is usually used to process materials with hardness higher than RC48. It has excellent high temperature hardness-up to 2000 ° C, although it’s much more brittle than cemented carbide, worse heat resistance and chemical resistance than ceramic. But it has higher impact strength and crushing resistance than ceramic cutting tools. For cutting hardened metals, the machine rigidity can be slightly worse. Beside, some special CBN tools can withstand the chip load of high rate roughing, the impact of intermittent cutting, and the wear and cutting heat during finishing.For highly demanding parts, the equipment should be appropriately adjusted to increase the rigidity of the machine and equipment. The blunt edge should be large enough to prevent micro-scale spalling and a certain thickness of CBN layer on the tool base, which can make the tool work under high speed, heavy load and severe intermittent load. These characteristics make CBN the tool material of choice for roughing hardened steel and pearlite gray cast iron.
The tool with a thin layer of CBN is relatively fragile, but it is a better tool material for machining hardened ferroalloys. CBN has low thermal conductivity and high compressive strength, and can withstand the cutting heat generated by high cutting speed and negative rake angle. Due to the higher temperature in the cutting zone, the workpiece material is softened, which helps the formation of chips. Negative geometric angles strengthen the tool, stabilize the cutting edge, improve tool life, and allow machining at shallow depths of less than 0.010 inches (0.254mm).
In the case of dry-turning hardened workpieces, CBN tools can be used to replace the grinding process because they can produce a surface quality of less than 16 micro inches (0.4 μm) and can control accuracy of ± 0.0005 inches (0.0127 mm).
CBN tools are ideal for hard turning and high-speed milling. For this application, ceramics and CBN are overlapping. Therefore, a cost-benefit analysis is necessary to determine which material will provide the best results.
◆. PCD cutting tools
As the hardest tool material, polycrystalline diamond is the most wear-resistant. Its hardness and abrasion resistance result from the lack of azimuth bonding between diamond crystals. This different arrangement of crystal orientations inhibits crack propagation. When cutting, the PCD chip is bonded to the cemented carbide cutting, which can increase its strength and impact resistance, and its tool life is 100 times that of cemented carbide.However, certain properties limit its cutting in many processing operations. One is the affinity of PCD for iron in ferrous metals, which causes chemical reactions. This tool material can only be used to process non-ferrous parts. The second is that PCD cannot withstand high temperatures in the cutting zone exceeding 600 ° C. Therefore, it cannot cut tough, highly ductile materials.
PCD tools are especially for processing non-ferrous metals, especially high-silicon aluminum alloys, which are highly abrasive. These materials cutting with sharp cutting edge and a large positive rake angle, minimizing cutting pressure and chipping.
▇ Enhancement of cutting edge, tool geometry parameters and chip removal
Despite the physical progress and application development in recent years, tools made of cermet, ceramic, CBN and PCD are still much more brittle than cemented carbide and cannot withstand too much pressure. Therefore, tools made of these materials must be combined with design characteristics, to strengthen support and disperse pressure.
This is very important. Ex, in order to change the direction of the grinding force so the force moves from the cutting edge inward to the tool body, the cutting edge must be machined-the edge preparation. There are three types of cutting edge preparation and their size should be appropriate: T-shaped cutters, reinforced, T-shaped cutting reinforced.
◆. T-shaped cutters
It is a chamfer narrow flat surface grinding on the cutting edge to replace the weaker and sharper cutting. An important task for tool technicians is to find the smallest plane width and the angle that can give the cutting edge the appropriate strength and life; because the large width and the angle of the strengthened cutting edge will undoubtedly increase the cutting force.
◆. Reinforcement
Is to round out the sharp edge. Although reinforcement is not as angular and angled as those of T-shaped cutting tools, reinforcement works well for advanced cutting materials used for finishing. These hardened tools should be used for shallow depth of cuts, low speed feeds, and minimalize the cutting pressures.
◆. T-shaped cutting reinforcement
The T-shaped edge band can also be strengthened when the front and back where chamfering is used for chamfering is strengthened. In applications, when tiny spalling occurs (like rough turning steel with a ceramic cutting tools), strengthening can disperse the pressure at these points without making the chamfers larger and strengthening the cutting edge of the tool.In addition to determining the most suitable tool edge for the workpiece, the tool designer must also optimize the tool's geometric angle and chip removal capabilities. Increasing the relief angle reduces the cutting force and pressure on the tool, and also reduces the temperature in the cutting zone. Make the positive rake angle as large as possible, so that cutting forces can be reduced due to better shear. The wide chip flutes help with chip removal, especially for drilling and threading.
The alternative to reduce cutting forces is to cut at high speeds. In order to improve the efficiency, it is better to reduce the large feed rate at a very high spindle speed instead of increasing the feed rate. In addition, today's end mills are much more accurate than they were five years ago, and the mechanical stability and rigidity of milling and turning machines are also higher, thus eliminating possible vibrations. All of this facilitates the application of brittle, harder and wear-resistant tool materials.
Another favorable factor for the application of high temperature resistant tools is the extremely high efficiency of chip formation. For example, when cutting cast iron, the heat makes the material in the cutting area into a plastic body, which reduces the strength of the workpiece material in the cutting area. The result is a three-fold increase in the removal rate of metal compared to ordinary roughing. Because of the high feed rate, the cutting of the metal material by the tool is so fast that a large amount of heat stays in the chip, and there is no time to pass to the workpiece and deform it. Although the cutting temperature is very high, the temperature rise of the workpiece is very small, and the precision of the workpiece is higher than that of the conventional cutting.
Low axial force finishing can also minimize static deformation of workpieces, fixtures and machine tools. Such processes require the use of coarse-tooth milling cutters, low feeds and high cutter speeds. Since the clamping force required to clamp the workpiece is small, the fixture can be simple. For prismatic workpieces, there are wider milling cutter channels.