Carbide cutting tools wears faster when milling nickel-based alloys?
2020-01-02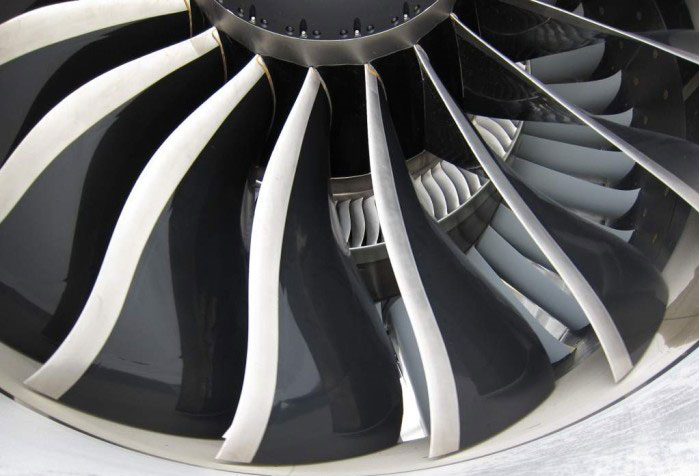
Nickel and chromium are the two main added components in nickel-based alloys. Increasing nickel can increase the toughness of the material. Adding chromium can increase the hardness of the material. Besides, the balance of other components can be used to predict the tool wear. For nickel-based alloys, the cost of the tool is higher, and the cost is 5-10 times that of milling general steel.
Needless to say, when milling nickel-based alloys, heat is the most important factor affecting tool life, because even the best cemented carbide tools are destroyed by excessive cutting heat. Generates extremely high cutting heat, not just a problem encountered when milling nickel alloys. Therefore, when milling these alloys, heat needs to be controlled.
In addition, it is important to understand the amount of heat generated when processing various types of tools (high-speed steel tools, carbide tools or ceramic tools). Many tool damages are also related to other factors, and substandard fixtures and tool holders can shorten tool life. When the clamped work piece is insufficiently rigid and moves during cutting, it may cause the carbide substrate to break. Sometimes small cracks occur along the cutting edge, and sometimes they break from carbide inserts, making it impossible to continue cutting.
Of course, this chipping tool may also be caused by high hardness carbide or overload cutting. At this time, high-speed steel tools should be considered for processing to reduce chipping. Of course, high-speed steel tools can’t withstand the high heat as hard alloys.
Before the machining, the rigidity of the fixture is strengthened, which not only prolongs the tool life, but also improves the surface quality of the work piece and reduces machining errors. Similarly, improper selection of tool holders will also shorten tool life. For example, if an end mill with a shank diameter of 3.175 mm is installed in the milling cutter shank, due to the role of the fastening screw, the fitting gap between the tool and the shank is shifted to one side, and the center of the tool is deviated from the rotation center of the shank, so that the milling cutter The increase in radial runout during work causes the cutting load of each cutter tooth to be uneven. This cutting state is very detrimental to the tool, especially when milling nickel-based alloys and other elements added to the material may be: silicon, manganese, molybdenum, tantalum, tungsten, etc. It is worth noting that tantalum and tungsten are also used to make The main components of cemented carbides can effectively improve the performance of cemented carbides, but the addition of these elements to the work piece material makes it more difficult to make it more difficult to mill.
By using tool holders with improved tool eccentricity, such as hydraulic chucks and hot chucks, the cutting action can be more balanced and stable, reducing tool wear and improving surface quality. When selecting a tool holder, one principle should be followed, that is, the tool holder should be as short as possible. These clamping requirements for tools and work pieces apply to milling any material.
Needless to say, when milling nickel-based alloys, heat is the most important factor affecting tool life, because even the best cemented carbide tools are destroyed by excessive cutting heat. Generates extremely high cutting heat, not just a problem encountered when milling nickel alloys. Therefore, when milling these alloys, heat needs to be controlled.
In addition, it is important to understand the amount of heat generated when processing various types of tools (high-speed steel tools, carbide tools or ceramic tools). Many tool damages are also related to other factors, and substandard fixtures and tool holders can shorten tool life. When the clamped work piece is insufficiently rigid and moves during cutting, it may cause the carbide substrate to break. Sometimes small cracks occur along the cutting edge, and sometimes they break from carbide inserts, making it impossible to continue cutting.
Of course, this chipping tool may also be caused by high hardness carbide or overload cutting. At this time, high-speed steel tools should be considered for processing to reduce chipping. Of course, high-speed steel tools can’t withstand the high heat as hard alloys.
Before the machining, the rigidity of the fixture is strengthened, which not only prolongs the tool life, but also improves the surface quality of the work piece and reduces machining errors. Similarly, improper selection of tool holders will also shorten tool life. For example, if an end mill with a shank diameter of 3.175 mm is installed in the milling cutter shank, due to the role of the fastening screw, the fitting gap between the tool and the shank is shifted to one side, and the center of the tool is deviated from the rotation center of the shank, so that the milling cutter The increase in radial runout during work causes the cutting load of each cutter tooth to be uneven. This cutting state is very detrimental to the tool, especially when milling nickel-based alloys and other elements added to the material may be: silicon, manganese, molybdenum, tantalum, tungsten, etc. It is worth noting that tantalum and tungsten are also used to make The main components of cemented carbides can effectively improve the performance of cemented carbides, but the addition of these elements to the work piece material makes it more difficult to make it more difficult to mill.
By using tool holders with improved tool eccentricity, such as hydraulic chucks and hot chucks, the cutting action can be more balanced and stable, reducing tool wear and improving surface quality. When selecting a tool holder, one principle should be followed, that is, the tool holder should be as short as possible. These clamping requirements for tools and work pieces apply to milling any material.