切削工具中的陶瓷材料
2020-03-10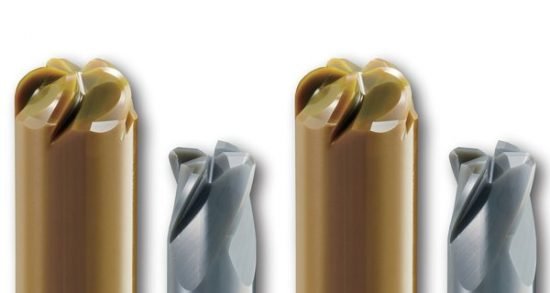
傳統的切削工具大多由鋼和鐵製成,但是陶瓷切削工具近年來發展迅速。在某些領域,陶瓷切削刀具比其他切削刀具具有很多優勢。
陶瓷具有許多切削工具所需的特性,例如高強度和良好的導熱性。陶瓷切削工具的發展曾經由於製造陶瓷的高成本和困難而受到阻礙。由於材料工程的改進和復合材料的出現,成本和製造難度都得以解決。
近年來,陶瓷刀具的市場份額增加了,這表明陶瓷切削刀具的發展狀況良好。
通過對許多加工方法的比較和評估,最終選擇壓模和燒結作為製造陶瓷切削刀具是最合適的方法。
切削工具中可以使用很多潛在的陶瓷材料,其中大多數是氧化鋁或二氧化矽基底。複合材料也以較低的成本和高性能引起了人們的廣泛關注。
陶瓷具有許多切削工具所需的特性,例如高強度和良好的導熱性。陶瓷切削工具的發展曾經由於製造陶瓷的高成本和困難而受到阻礙。由於材料工程的改進和復合材料的出現,成本和製造難度都得以解決。
近年來,陶瓷刀具的市場份額增加了,這表明陶瓷切削刀具的發展狀況良好。
通過對許多加工方法的比較和評估,最終選擇壓模和燒結作為製造陶瓷切削刀具是最合適的方法。
切削工具中可以使用很多潛在的陶瓷材料,其中大多數是氧化鋁或二氧化矽基底。複合材料也以較低的成本和高性能引起了人們的廣泛關注。
切削工具
切削工具旨在分離材料。它們可以分為不同的類別,每種類別都有其自己的特性和對所用材料的要求。切削工具最常用的材料是鋼和鐵。但是,隨著材料科學和工程學的發展,陶瓷切削刀具發揮著越來越重要的作用。
陶瓷通常非常堅硬,耐熱並且與鋼的反應性很小,而這對切削工具至關重要。因此,它們可以以高切削速度使用而不會變形和溶解。然而,陶瓷具有其自身的缺點,即它們缺乏韌性並且對機械或熱衝擊敏感,這限制了在切削區域中使用陶瓷材料。
人類使用陶瓷切削工具已有100多年的歷史了。切削對像從非常柔軟的物質(黃油)到極硬的東西(鋼)不等。在早期,這些陶瓷工具的主要成分是氧化鋁。然而,氧化鋁材料的韌性低並且被玻璃相軟化,這是其應用受到限制的原因。在科學家的努力下,材料科學和技術得到了極大的發展,從而大大改善了陶瓷的性能。通過提高純度,它們變得更堅硬,添加一些添加劑後脆性降低,而通過增強劑則變得更堅韌。用於切削工具的第一種陶瓷材料是氧化鋁。還生產了多種其他陶瓷,專門用於切削工具的製造。有三類可用,即純氧化物陶瓷,混合氧化物加碳化物或氮化物和氮化矽基材料。晶鬚增強的陶瓷材料,在高溫下具有高韌性和硬度,推動了陶瓷刀具的發展。
金屬陶瓷可轉位銑刀選擇材料時,應考慮許多面向。在工具材料的設計中考慮了以下三個面向。首先,表面應具有最高的導熱性,有利於消散切削熱。其次,表面層的熱膨脹係數應該是所有材料層中最低的,以便在製造過程中在表面層中形成殘餘壓縮應力,這可以部分抵消由外部載荷引起的應力。最後,最大值的馮米斯應力值應該是最低的,以保證壓坯的結構完整性。
陶瓷的性能不是材料選擇的唯一因素,經濟因素在考慮材料方面也起著重要作用。陶瓷行業的主要重點之一是如何降低原始成本,而未來的發展最重要的方向必須是降低成本,需要新的原材料和方法來實現這一目標。
未來,隨著材料科學技術的發展,將有更多的方法用於陶瓷的改進。鍍層技術的完善和複合材料的發展將促進陶瓷在切削工業中的應用。CMC(陶瓷基複合材料)被認為是將來用於切削工具的最受歡迎的材料之一。
市場現狀
有三個主要的切削工具市場。切削工具和可轉位刀片;對銑,車和鑽工具進行了調查,以顯示當前切削工具市場的趨勢。牌號包括硬質合金,陶瓷,金屬陶瓷,CBN / PCBN,金剛石和鋼。產品按國家和最終用途市場進行分析。
消費市場按以下每個地理區域進行了細分:
•中國•美國•德國
•日本•韓國•意大利•法國
•台灣•英國
•巴西•其他歐盟•其他北美自由貿易區
•其他歐洲•其他亞太地區
•其他拉丁美洲•世界其他地區
從上到下的地理區域代表了最大的切削工具市場。據稱,由金屬切削工業和切削工具製造商協會合併而成的美國切削工具學會現在“代表了國內切削工具市場80%”。
切削工具市場將繼續取得長足進步,這將減少工作台時間和更多的加工量,並且切削深度更大,從而提高了生產率和精度。在過去的十年中,切削工具市場急劇增長。這些工具根據應用程序具有非常特殊的作用。現在有特定的硬質合金牌號,鍍層和幾何形狀可以滿足客戶的需求。預計該市場將擴大和增長並達到新的高度。
下面列出了切削工具行業中的大多數最終用戶:
•航空航天
•汽車
•化學加工
•通訊
•施工
•國防/軍事
•電子
•普通加工
•醫學/研究
•石油和天然氣
•造紙工業
•發電
金屬切削工具已經佔領了全球切削市場很長時間了。但是,某些特殊性能使高級陶瓷往往更便宜,壽命更長,應用範圍更大,這成為製造商的競爭優勢。 因此,陶瓷切削工具有望重新佔領切削市場。
預計製造商之間的競爭將白熱化,這將迫使製造商更加努力地工作,以獲得足夠的市場份額。目前三大競爭對手集中在全球範圍內的硬質合金刀具和硬質合金刀片上。
當前使用的材料
下面概述了切削工具行業中使用的四種主要陶瓷成分,每種材料最重要的方面都已特別標示。
賽隆
賽隆是一類基於氮化矽的陶瓷。陶瓷由四種不同的陶瓷粉末組成。二氧化矽(SiO2),氧化鋁(Al2O3)和氮化矽(Si3N4)。第四個成分是氧化釔(Y2O3)或氧化鎂(MgO)。氧化釔用於輔助燒結過程以提高效率。
Sialons的熱膨脹係數非常低,這意味著它們在熱衝擊情況下性能很好。賽隆在800°C至1000°C的溫度下仍能保持其硬度,使其在加工耐熱合金時非常有效。在高速加工淬硬的模具鋼和鑄鐵時,它們也有效。
Sialons的熱膨脹係數非常低,這意味著它們在熱衝擊情況下性能很好。賽隆在800°C至1000°C的溫度下仍能保持其硬度,使其在加工耐熱合金時非常有效。在高速加工淬硬的模具鋼和鑄鐵時,它們也有效。
氧化鋁基陶瓷
這些陶瓷如其名稱所示,但通常會發現少量的氧化鋯(2-5%)。添加的氧化鋯可增加斷裂韌性。
基於Al2O3的陶瓷在800ÌC以上的機械性能有所提高。在此溫度以下,硬質金屬比陶瓷具有更高的強度。
添加碳化鈦或氮化鈦可以使陶瓷的硬度進一步提高30-40%。這些較硬的陶瓷通常用於精加工和較硬的金屬。
(Al2O3 + ZrO2)鹼的另一種常見添加是碳化矽(SiC)晶須,其含量約為25%。晶鬚(Whisker)起到增強結構和增加韌性的作用。這使得陶瓷可以用於高速切削鎳基超級合金。
基於Al2O3的陶瓷在800ÌC以上的機械性能有所提高。在此溫度以下,硬質金屬比陶瓷具有更高的強度。
添加碳化鈦或氮化鈦可以使陶瓷的硬度進一步提高30-40%。這些較硬的陶瓷通常用於精加工和較硬的金屬。
(Al2O3 + ZrO2)鹼的另一種常見添加是碳化矽(SiC)晶須,其含量約為25%。晶鬚(Whisker)起到增強結構和增加韌性的作用。這使得陶瓷可以用於高速切削鎳基超級合金。
氮化矽
陶瓷的密度約為3.2g / cm3,晶粒度約為2-3微米。氮化矽具有良好的耐磨性和切削刃強度以及高的抗熱衝擊性。
Si 3 N 4通常用於提供用於車削和銑削鑄鐵的粗加工等級的領域。
氮化矽的不良溶液磨損性能限制了陶瓷不能用作加工鋼的切削工具。
對熱衝擊的高抵抗力意味著可以在有或沒有冷卻劑的情況下使用陶瓷。可以以這種受控方式在冷卻設備上節省金錢。
Si 3 N 4通常用於提供用於車削和銑削鑄鐵的粗加工等級的領域。
氮化矽的不良溶液磨損性能限制了陶瓷不能用作加工鋼的切削工具。
對熱衝擊的高抵抗力意味著可以在有或沒有冷卻劑的情況下使用陶瓷。可以以這種受控方式在冷卻設備上節省金錢。
立方氮化硼
立方氮化硼是一種合成化合物,在其自然狀態下具有柔軟的六方晶體結構。頓形成立方結構,將其在60kbar的壓力下加熱到1400°C。這對結構的硬度有很大的影響,(大約4000VDH)這類似於鑽石的硬度。
氮化硼碳是多晶的,用於硬質合金受到所採用的切削速度限制的應用中。例子有:
高速鋼,工具鋼,表面硬化鋼,冷硬鑄鐵和人造衛星。
碳氮化硼的硬度僅次於金剛石,因此,氮化硼碳具有出色的耐磨性,並且無需像其他工具那樣在切削工具上更換陶瓷。較硬的金屬也可以提高家工效率,但是氮化碳硼在加工較軟的材料時沒有優勢。
氮化硼碳是多晶的,用於硬質合金受到所採用的切削速度限制的應用中。例子有:
高速鋼,工具鋼,表面硬化鋼,冷硬鑄鐵和人造衛星。
碳氮化硼的硬度僅次於金剛石,因此,氮化硼碳具有出色的耐磨性,並且無需像其他工具那樣在切削工具上更換陶瓷。較硬的金屬也可以提高家工效率,但是氮化碳硼在加工較軟的材料時沒有優勢。
複合材料
通過使用一些尺寸(例如TiC,Co和WC)作為分散相(稱為複合陶瓷),陶瓷的性能得到了顯著改善。類複合陶瓷是Si3N4複合陶瓷,其硬度,彎曲強度和韌性均高於簡單的Si3N4基陶瓷。它還具有更好的耐熱衝擊性。
由於其特殊的性能,它被廣泛地用於加工冷硬鑄鐵輥,並且可以完成粗鑄件的粗加工和精密加工,從而克服了採礦設備中使用的鋼零件的低機械加工硬化性。它的缺點是磨損加工不良。
由於其特殊的性能,它被廣泛地用於加工冷硬鑄鐵輥,並且可以完成粗鑄件的粗加工和精密加工,從而克服了採礦設備中使用的鋼零件的低機械加工硬化性。它的缺點是磨損加工不良。
鍍層材料
鍍層技術在切削刀具的製造中起著非常重要的作用。它用於生產既具有硬質表面又具有高韌性的完美切削刀具。隨著近十年的發展,這項技術使高速切削,硬切削和乾式加工的材料成為可能。
刀具鍍層可分為四種。它們是化學氣相沉積(CVD),低溫化學氣相沉積(PCVD),中溫化學氣相沉積和PVD。
但是,切削刀具應採用不同的鍍層,以滿足對綜合機械性能的要求。因此,應更加註意使鍍層更薄,鍍層溫度更低。
刀具鍍層可分為四種。它們是化學氣相沉積(CVD),低溫化學氣相沉積(PCVD),中溫化學氣相沉積和PVD。
但是,切削刀具應採用不同的鍍層,以滿足對綜合機械性能的要求。因此,應更加註意使鍍層更薄,鍍層溫度更低。
未來的材料
陶瓷刀具的未來取決於刀具超硬度層的發展。陶瓷切削刀具的新鍍層是氮化鈦鋁鍍層。高速使用時,鍍層有助於控制切削工具的溫度。這樣可以加快切削速度,從而提高加工效率。
鍍層還可以延長工具的使用壽命,在某些情況下,它可以使銑刀使用壽命延長數倍。重要的是要注意,鍍層也使工具的成本增加了10%,但鍍層銑刀延長加工時間可相對減少加工成本。
鍍層還可以延長工具的使用壽命,在某些情況下,它可以使銑刀使用壽命延長數倍。重要的是要注意,鍍層也使工具的成本增加了10%,但鍍層銑刀延長加工時間可相對減少加工成本。
可能的加工條件
大多數陶瓷是通過成型和燒結加工的。成形的陶瓷稱為毛坯。陶瓷的成型過程至關重要,因為它會影響燒結產品的性能,例如孔隙率。如今,形成陶瓷毛坯的主要方法包括壓模,滑模鑄造,壓力鑄造和注塑成型。
成型
以上所有方法均始於將陶瓷顆粒與液體或聚合物熔體混合的懸浮液,適當的分散劑以及可能的其他添加劑(例如粘合劑,增塑劑和消泡劑)混合在一起,以便可以分散良好的非團聚陶瓷漿料製作。
模壓可分為許多不同的壓制途徑,例如乾壓,冷等靜壓和熱等靜壓。通過將粉末倒入模具中來製造毛坯,並在一定壓力下形成這些顆粒。乾壓法幾乎與冷等靜壓法相同。考慮到它們的生產率,這兩種方法被廣泛用於陶瓷材料的工業生產中,並且冷等靜壓的發展使得更高密度的毛坯成為可能。
排水澆鑄技術中包括滑模澆鑄和壓力澆鑄,它們涉及固液分離過程以形成緻密的毛坯。兩個鑄件中流動液體的驅動力是外部壓力梯度。壓鑄是一種低壓過濾,其毛坯成型的驅動力是毛細作用。與壓模相比,滑模鑄造速度較慢,但可以獲得複雜的圖形。壓鑄通常用於製造傳統的粘土基陶瓷材料,例如陶器和衛生瓷。壓力過濾是一種改進的滑模鑄造方法,提高了鑄造速度,毛坯具有更高的密度。
壓鑄和鑄造都受到一些遺傳問題的困擾。需要懸浮液的液體流動,並且應力梯度還可能導致生坯的密度不均勻,從而導致袋狀物質。
注射成型是形成較小物體的絕佳方法。將粉末和粘合劑的混合物倒入模具中並形成毛坯。然而,去除可以在較低溫度下燃燒的粘合劑是一個問題,在此過程中容易引起裂紋和缺陷。
還有一種稱為固態自由成型製造(SFF)的技術,通過該技術,我們無需使用模具即可形成陶瓷毛坯。所有過程均由計算機使用在過程之前設計的3D CAD控制。該方法已經用於形成複雜的圖形,但是表面光潔度差。這種方法由於其不成熟的技術尚未得到廣泛使用。
燒結
成型後,毛坯的密度通常約為其理論密度的50%。通過在高達1800°C的溫度下燒結可以實現完全緻密化。
在此過程中,單個粉末顆粒可以獲得足夠的能量以結合在一起,從而實現從存在的孔隙度到壓實階段的轉變。
複合材料加工
複合材料由兩部分組成:基體相和增強相。通常,這兩個部分的組合是通過融合事件實現的,融化後,零件形狀即被設定。
根據熔化事件,複合材料的製備方法可分為四種主要方法:真空袋成型,壓力袋成型,高壓釜成型和樹脂傳遞成型(RTM)。此外,還有其他一些類型的成型,包括壓製成型,拉擠成型,長絲纏繞等。
複合材料還可以根據基體材料分為金屬基複合材料(MMC)和陶瓷基複合材料(CMC)。根據加工過程中金屬基體的溫度,MMC的過程可分為五類:
1)液相工藝
2)固液過程,
3)兩階段(固液)工藝,
4)沉積技術
5)原位處理。
選材及加工路線
然後,干法處理對毛坯的微觀結構和生產率有很大影響。我們必須抱持這種想法,以避免破裂和翹曲的問題。陶瓷零件生產的理想結果是快速乾燥,但是快速乾燥會導致開裂。已經研究出降低的干燥速率導致增加的毛坯密度。功率的大小也會影響陶瓷的燒結性能。如今,非定型粉末由於其特殊的性能(機械,光學,磁和電)而備受關注。可以在明顯降低的溫度下燒結奈米粉末的壓塊,從而降低了燒成成本。在形成奈米級顆粒時,可以獲得高密度陶瓷體。
從已經討論過的陶瓷來看,用於該產品的最佳陶瓷將是氧化鋁基陶瓷。它已經在行業中廣泛使用,因此無需進行測試以確保其有效。切削刀具時,熱量迅速增加,有時會產生影響,但是Al2O3的溫度越高,其機械性能越好。添加碳化矽晶須還將進一步提高陶瓷的硬度。這些晶鬚(Whisker)增加了結構的強度並增加了其韌性。因此,切削工具可以以更高的速度使用。我們的陶瓷不僅可以通過晶鬚(Whisker)增強強度,而且還可以通過TiAlN塗層獲得堅固的外殼。這種鍍層具有“高粘結強度,高硬度,耐磨性和高切削速度。
從行業中所有可能的加工條件中,已經確定乾壓將是對公司最有利的條件。
乾壓機最吸引人的特點是生產率因素。它的快速生產率意味著增加產品數量,因此相對降低成本。”富蘭克林說“時間就是金錢”,他是對的。減少生產時間減少了員工的工作時間,減少了機器必須開機的時間,因此減少了生產成本。
乾壓是使用含有0%至4%水分的顆粒狀或噴霧乾燥粉末進行的,這就是乾壓的名稱。使用此過程有一些缺點,這些缺點之一是在該過程中使用高壓,但是這些高壓又不如壓力鑄造中使用的高壓那麼高。如果在成型或壓制之前的所有步驟都受到嚴格控制,則乾壓只能獲得良好的效果。離開模腔的產品處於塑性狀態,如果不小心處理,可能會變形。
對於乾壓而言,可以使用的組合物沒有限制,因為不依賴於主體的可塑性來輔助成形。在正常條件下和監督下,有可能生產出非常好的公差陶瓷。在特殊情況下,如果控制非常緊密,則可以保持比平常更好的公差。
滑模鑄造需要仔細控制,以有利的生產率大量生產,尤其是在將製品鑄造在模具上需要很長時間的情況下。壓力鑄造與滑模鑄造幾乎相同,但是增加了壓力以加快鑄造時間。這種增加的壓力是不合理的,因為它太昂貴了,並且沒有花費足夠的時間進行處理。注塑成型具有一些可能會在產品上出現的缺陷。模具,編織線和微裂紋內的填充可能不完整,所有這些都會對成品產生視覺缺陷。
最後,與其他工藝路線相比,乾壓工藝產生的缺陷數量最少。這是最快的路線,具有很高的生產率,並且可以提供很高的公差。這些是我們選擇乾壓工藝路線的主要原因。
RAC的合理論點
已選定要採用的陶瓷是Al2O3 +(2%Zr)+(20%SiC晶鬚),合法使用此成分沒有問題。但是,使用切削工具的方法必須作為要求專利的專利4,879,277進行審查。“在一種切削金屬的方法中,使切削工具與金屬工件接觸,並且切削工具和金屬工件彼此相對移動,從而通過切削工具從金屬工件上去除金屬,該改進包括使用燒結的具有基本由氧化鋁和2-40%(體積)的碳化矽晶須組成的基體的複合材料切削工具。”如果要以這種方式使用材料,則必須圍繞專利開展一項工作。
RAC可以通過繼續執行此選項來為自己創造競爭優勢,因為它將幫助他們與大多數競爭對手區分開來。選擇的材料是具有極高性能的非常前瞻的材料。許多競爭對手的企業可能不會採用這種材料,並且可能會繼續使用價格更低廉的材料,例如未增強的氧化鋁基陶瓷。RAC將能夠為其客戶提供更快,更高效的切削解決方案。先進的技術可能會吸引新客戶買單,從而擴大市場份額。較硬的切削刃和更快的切削速度也將帶來更高的切削質量,刀具尺寸將更小,因此可以進行更精確的加工。
從先前進行的市場分析中可以明顯看出,切削工具行業正在蓬勃發展。令人鼓舞的是,在過去十年中,市場如此迅猛增長,並且對新切削工具技術的需求也在不斷增長。隨著市場上產品的複雜性不斷發展,對更快,更準確方法的需求將保持不變。
總之,考慮到所涉及的因素,所提出的陶瓷和製造工藝可以預示為RAC的積極一步。在做出決定之前,唯一要解決的問題是有關陶瓷及其方法的專利。一旦解決了這一問題,那麼繼續下一步的決定就很容易了,最終是企業成功的關鍵因素。